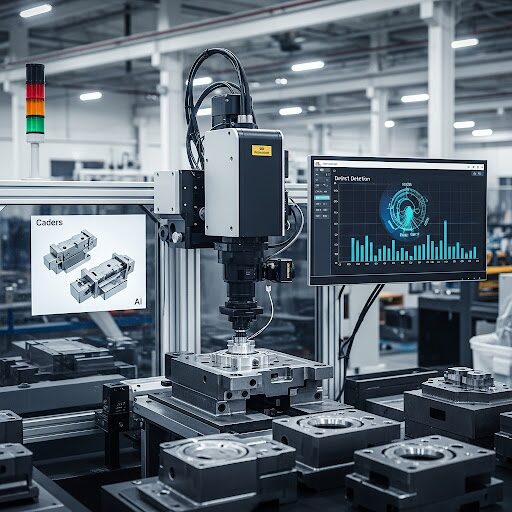
AI外観検査 導入後の安定運用と進化を実現する5つの秘訣
2025.05.23
導入して終わりではない!AI外観検査の価値を持続させる運用ノウハウ。専門コンサルタントが継続的な成果創出のポイントを解説。
このコラムをお勧めしたい方のイメージ
既にAI外観検査システムを導入し、その運用に課題を感じている
AI外観検査の導入効果を持続させ、さらに向上させたいと考えている
AIシステムの運用体制構築や人材育成に関心がある
AIモデルの再学習や精度維持の方法について具体的な情報を求めている
製造プロセスの変化に柔軟に対応できるAI検査システムを目指したい
このコラムの内容
本コラムは、AI外観検査システムを導入されたものの、その後の運用において課題を感じている、あるいはさらなる効果を追求したいと考えている経営者様およびご担当者様に向けて、導入後の安定運用と継続的な改善を実現するための重要なポイントを解説します。AI外観検査は導入がゴールではなく、むしろスタートです。本コラムでは、運用フェーズで直面しがちな問題点を洗い出し、それらに対する具体的な解決策を提示します。特に、AIモデルの精度維持に不可欠な再学習のプロセス、変化する製造環境への対応、そしてこれらを支える運用体制の構築と人材育成の重要性について、株式会社船井総合研究所のコンサルタントが具体的な事例やチェックリストを交えながら、実践的なノウハウを提供します。
このコラムを読むメリット
このコラムをお読みいただくことで、AI外観検査システム導入後の運用における具体的な課題とその解決策を深く理解し、自社システムの価値を最大限に引き出すための道筋を描くことができます。「導入したものの、精度が維持できない」「新しい不良に対応できない」「担当者が不在で困っている」といったお悩みを抱える企業様にとって、本コラムはAI外観検査を真の経営貢献ツールへと進化させるための実践的な指針となるでしょう。AIモデルの継続的な改善方法、効果的なデータ管理、ハードウェアメンテナンスのポイント、そして何よりも重要な社内運用体制の構築と人材育成のノウハウを得ることで、変化に強いAI外観検査システムを確立し、持続的な品質向上と生産性向上を実現するための一助となります。
1. AI外観検査「導入後」によくある課題とは?~現状チェックリスト~
AI外観検査導入後の隠れた問題点
AI外観検査システムは、導入直後は高い検査精度を発揮し、省人化や品質向上に貢献することが期待されます。しかし、時間の経過とともに、あるいは製造環境の変化に伴い、様々な問題が顕在化してくるケースが少なくありません。「導入して終わり」ではなく、むしろ導入後からが本当のスタートと言えるでしょう。
株式会社船井総合研究所のコンサルティング現場でも、以下のようなお悩みをよく伺います。
判定精度の低下: 「導入当初は良かったが、最近不良品の見逃しや良品の誤判定が増えてきた。」
検査時間の長期化: 「処理速度が遅くなり、タクトタイムに影響が出ている。」
費用対効果の悪化: 「期待したほどのコスト削減効果が得られていない。」
新たな不良への未対応: 「新しい種類の不良品に対応できず、結局人手で検査している。」
環境変化への追随困難: 「製品のマイナーチェンジや、照明など検査環境の変化にAIが対応しきれない。」
ブラックボックス化と属人化: 「AIの判定根拠が分からず、トラブル時に対応できない。」「導入時の担当者が異動・退職し、システムの詳細が分かる人間がいない。」
ドキュメント不足: 「導入時の完成図書や運用マニュアルが整備されておらず、現状把握が困難。」
ベンダーとの連携問題: 「導入業者と連絡が取れない、あるいは追加費用を要求される。」
ハードウェアの老朽化・陳腐化: 「予備機材がない、または製造中止で入手困難。」
これらの問題は、AI外観検査システムの価値を著しく損なう可能性があります。まずは、自社の運用状況を客観的に把握することが重要です。
【現状チェックリスト】あなたの会社のAI外観検査は大丈夫?
以下の質問項目について、自社の状況をチェックしてみましょう。
判定精度は導入時と比較して低下していませんか? (Q1)
検査時間(タクトタイム)は遅くなっていませんか? (Q2)
導入時に見込んだ費用対効果は維持されていますか? (Q3)
良品を不良品と誤判定するケースは増えていませんか? (Q4)
不良品を見逃す(流出させる)ケースは発生していませんか? (Q5)
AIの判定スコアが低い(判定に迷っている)場合の対応ルールは明確ですか? (Q6)
照明の変化、カメラの汚れ、製品の材質変更など、検査環境や対象物の変化に適切に対応できていますか? (Q7)
新しい種類の不良が発生した場合、AIに追加学習させる仕組みはありますか? (Q8)
検査画像データとAIの判定結果は適切に保存・管理されていますか? (Q9)
AIの再学習に使用するための教師データ(アノテーション済みデータ)は適切に保存・管理・運用されていますか? (Q10)
AIソフトウェアや関連システムのアップデートは定期的に行っていますか? (Q11)
カメラ、照明、PCなどのハードウェアの定期点検、清掃、必要な部品交換は実施されていますか? (Q12)
AIシステムの監視、メンテナンス、データ管理を行う専任または兼任の担当者は明確ですか? (Q13)
担当者に対するAIやシステム運用に関する教育・トレーニングは実施されていますか? (Q14)
製造部門、品質管理部門、情報システム部門など、関係部署との連携体制は構築されていますか? (Q15)
AIの判定基準、検査プロセス、運用方法などを継続的に見直し、改善する活動は行われていますか? (Q16)
これらの質問の多くに「いいえ」や「不十分」という回答が付くようであれば、運用体制やプロセスに何らかの課題を抱えている可能性が高いと言えます。次章以降で、これらの課題に対する具体的な解決策を詳述します。
2. AIは育て続けるもの!検査精度を維持・向上させる再学習の重要性
AI検査精度の経時変化と再学習の必要性
AI外観検査システムは、導入直後には高い検出率を示すことが一般的です。これは、初期学習データがその時点での製品や不良の傾向に最適化されているためです。しかし、運用を続ける中で、様々な要因によりAIの検出率は徐々に低下していく傾向が見られます。例えば、以下のようなケースです。
新たな不良パターンの出現: 製造プロセスの微妙な変化や原材料のロット差などにより、これまで学習データに含まれていなかった新しい種類の不良が発生することがあります。
製品のマイナーチェンジ: 外観にわずかな変更が加えられた場合、AIがそれを異常と誤認識したり、逆に本来検出 すべき不良を見逃したりする可能性があります。
検査環境の変化: 照明の経年劣化や交換、カメラのレンズの汚れやピントのズレ、周囲の明るさの変化などが、撮像される画像に影響を与え、AIの判断を狂わせることがあります。
これらの要因により、導入時に例えば90%だった検出率が、数ヶ月後には85%に低下するといった事態は珍しくありません。この低下した精度を回復させ、さらに向上させるために不可欠なのが「再学習」です。
再学習のプロセスとポイント
再学習とは、新たな画像データをAIモデルに追加で学習させ、その時点での最適な状態にモデルを更新していく作業です。 具体的には、以下のようなステップで進められます。
課題の特定とデータ収集:
○ 「どのような不良を見逃しているのか?」「どのような良品を誤検出しているのか?」を具体的に把握します。
○ 見逃した不良品や誤検出した良品の画像を収集します。また、新たに出現した不良パターンの画像も積極的に収集します。
アノテーション(教師データ化):
○ 収集した画像に対して、専門の担当者が正確な教師ラベル(例:傷、汚れ、気泡など)を付与します(アノテーション作業)。この教師データの質が、再学習後のAIの精度を大きく左右します。
再学習の実施:
○ 既存の学習データに、新たにアノテーションされた画像データを追加、あるいは一部置き換えるなどして、AIモデルに再学習を実行させます。
評価と検証:
○ 再学習後のAIモデルの精度を、テスト用の画像データセットを用いて評価します。期待する精度に達しているか、特定の不良に対する検出能力が改善されたかなどを確認します。
○ 必要に応じて、アノテーションの見直しや学習パラメータの調整を行い、再度学習と評価を繰り返します。
この再学習サイクルを定期的に、あるいは問題が顕在化したタイミングで実施することにより、AIの検出率を再び95%以上に引き上げることも可能です。
再学習における重要なポイント:
学習データの質: 最も重要なのは、質の高い教師データを用意することです。誤ったラベル付けは、AIの性能をむしろ悪化させる可能性があります。
データのバランス: 特定の不良データばかりに偏らず、様々な種類の不良や良品のデータをバランス良く学習させることが望ましいです。
学習データの履歴管理:いつ、どのようなデータで再学習を行ったのか、その結果どう精度が変化したのか、といった履歴を記録・管理することが重要です。これにより、問題発生時の原因究明や、さらなる改善のための知見が蓄積されます。作成した学習データは安易に消去せず、将来的に再活用できる形で保存しておくべきです。
過学習の防止:新しいデータに過剰に適合しすぎると、未知のデータに対する汎化性能が失われる「過学習」に陥る可能性があります。これを防ぐために、学習データとは別に検証用データを用意し、汎化性能も確認しながら再学習を進める必要があります。
データ解析の活用:単に画像を追加するだけでなく、学習データを統計的に解析し、例えばクラスタリング(類似のデータをグループ化)や因果推論(データから原因と結果の関係を推定)といった手法を用いて、どのデータがAIの精度向上に寄与するのか、あるいは逆に精度を落とす要因となっているのかを分析することも有効です。これにより、より効率的で効果的な再学習が可能になります。
AIは一度作ったら完成ではなく、継続的に「育てていく」という意識を持つことが、AI外観検査を長期的に成功させるための鍵となります。株式会社船井総合研究所では、この再学習プロセスの構築支援や、効果的なデータ活用のコンサルティングも提供しております。
3. 変化への対応力が鍵!AI運用におけるデータ管理とシステム保守
AI外観検査システムを安定して長期間運用し、その価値を持続させるためには、AIモデルの再学習だけでなく、それを支えるデータ管理とシステム・ハードウェアの保守も極めて重要です。これらが疎かになると、せっかく導入したAIシステムが期待通りの性能を発揮できなくなるばかりか、最悪の場合、運用停止に追い込まれる可能性もあります。
データ管理の重要性と実践項目
AI外観検査において「データは資産」です。検査で得られた画像データや判定結果、そして再学習に用いる教師データなどを適切に管理・活用することが、システムの継続的な改善と価値向上に繋がります。
検査画像・結果データの蓄積と活用:
○ AIが検査した全ての画像データと、それに対するAIの判定結果(OK/NG、不良の種類、判定スコアなど)を、日時やロット番号などと紐付けて体系的に保存します。
○ これらの蓄積データは、単に記録として残すだけでなく、将来のAIモデルの再学習や、不良発生傾向の分析、歩留まり改善といった品質改善活動のための貴重な情報源となります。例えば、特定の時期に特定の不良が増加する傾向が見られれば、製造プロセスの見直しに繋げることができます。
教師データの管理と更新:
○ AIの再学習に使用する教師データ(アノテーション済み画像)は、その精度がAIモデルの性能に直結するため、特に厳格な管理が求められます。
○ アノテーションの基準を明確にし、作業者間でのばらつきを抑えることが重要です。
○ 新しい不良の種類が発見された場合や、製品仕様に変更があった場合には、速やかに教師データを更新し、最新の状態に保つ必要があります。
○ 教師データのバージョン管理を行い、いつどのような基準で作成・更新されたものかを追跡できるようにしておくことも、後の検証や改善に役立ちます。
データセキュリティとバックアップ:
○ 検査画像や教師データは、企業の機密情報を含む場合があるため、不正アクセスや情報漏洩を防ぐためのセキュリティ対策を講じる必要があります。
○ また、ハードウェアの故障や災害などによるデータ損失リスクに備え、定期的なバックアップと、必要に応じて遠隔地へのバックアップ体制を構築することも重要です。
システム・ハードウェアの保守ポイント
AI外観検査システムは、AIソフトウェアだけでなく、カメラ、照明、PC、搬送装置など、多くのハードウェアから構成されています。これらの物理的な機器が正常に機能し続けることが、システム全体の安定稼働の前提となります。
定期的な点検と清掃:
○ カメラ: レンズの汚れや傷、ピントのズレ、設置位置のズレなどがないか定期的に確認し、清掃や調整を行います。
○ 照明: 照度の低下やちらつき、ランプ切れなどがないか確認し、必要に応じて清掃や交換を行います。照明環境は撮像品質に大きく影響するため、特に注意が必要です。
○ PC・サーバー: 冷却ファンの清掃、内部の埃除去、ケーブル接続の確認などを定期的に行い、熱暴走や接触不良によるトラブルを未然に防ぎます。
○ 搬送装置: センサーの汚れ、可動部の摩耗や異音などを確認し、清掃やグリスアップ、部品交換を行います。
ソフトウェアアップデート:
○ AIソフトウェア本体だけでなく、OSやデータベース、関連ミドルウェアなどのセキュリティパッチや機能アップデート情報を常に把握し、計画的に適用します。アップデートにより、セキュリティ脆弱性の修正や新機能の利用、性能向上が期待できますが、一方で既存システムとの互換性に問題が生じる可能性もあるため、事前の検証が重要です。
予備部品の確保と老朽化対策:
○ 故障時に迅速に交換できるよう、クリティカルな部品(カメラ、照明、特殊なインターフェースカードなど)については予備品を確保しておくことが望ましいです。
○ 特に海外製の部品や特殊な部品は、納期がかかったり、製造中止になったりするリスクがあるため、早期の調達計画が必要です。
○ システム全体の耐用年数を考慮し、計画的なリプレースやアップグレードの予算化も視野に入れておくべきです。
環境整備:
○ AIシステムが設置されている環境(温度、湿度、粉塵、振動など)が、各機器の推奨動作条件を満たしているか確認し、必要に応じて空調設備の導入や防塵対策などを行います。
これらのデータ管理とシステム・ハードウェア保守を継続的に行うことで、AI外観検査システムは長期にわたり安定した性能を発揮し、企業の生産性向上と品質保証に貢献し続けることができます。
4. AIを使いこなす「人」と「組織」~あるべき運用体制と人材育成~
AI外観検査システムを導入し、その効果を持続的に引き出すためには、優れたAIモデルや最新のハードウェアだけでなく、それを適切に運用・管理し、改善していくための「人」と「組織」の力が不可欠です。どんなに高度なシステムも、それを使いこなし、育てていく体制がなければ宝の持ち腐れになりかねません。
AI外観検査運用に必要な役割と体制
企業の規模や検査対象、システムの複雑さなどによって最適な体制は異なりますが、一般的に以下のような役割と、それらを担うチームや担当者が必要となります。
経営層・システム導入推進部門:
○ 役割: AI導入・運用の全体方針決定、投資判断、プロジェクト全体の管理、関係部署間の調整、導入効果測定とROI評価、運用ルールの策定・周知。
○ ポイント: 経営層がAI活用の重要性を理解し、トップダウンで推進することが成功の鍵です。DX推進部門などがハブとなり、全社的な取り組みをリードします。
AIモデル開発・管理チーム(データサイエンティスト、AIエンジニア):
○ 役割: 検査要件に基づいたAIモデルの選定・開発・トレーニング・評価、精度維持・向上のためのモデルの再学習・チューニング、新しい欠陥種類や製品への対応、アノテーション(教師データ作成)の管理・指導。
○ ポイント: AIの専門知識が求められるため、社内育成が難しい場合は、外部の専門企業やコンサルタントとの連携も有効です。
インフラ・IT運用チーム(IT部門、インフラエンジニア):
○ 役割: AI推論用サーバー、カメラ、ネットワークなどのハードウェア・インフラの構築・保守・管理、AIソフトウェア・関連システムの導入・アップデート・セキュリティ管理、システム全体の安定稼働監視、障害対応。
○ ポイント: 既存のITインフラとの連携や、セキュリティポリシーの遵守が重要となります。
生産・製造現場チーム(現場オペレーター、生産技術者):
○ 役割: 日常的なAI検査システムの操作、検査対象物の投入、検査結果の確認、AIが判定困難としたものや異常検知時の初期対応、現場からのフィードバック(例:新しい欠陥の報告、誤検出の指摘)。
○ ポイント: AIシステムを最も日常的に利用するユーザーであり、AI改善のための重要な情報提供者です。AIへの理解と協力を得ることが不可欠です。
品質管理・品質保証チーム(QA/QC担当者):
○ 役割: 検査基準の設定とAIの判定基準との整合性確認、AIの検査精度(見逃し、過検出)の定期的な評価・監査、AIが判定した不良品や要注意品に対する最終確認・ダブルチェック体制の構築・運用、検査結果データの分析と品質改善活動への活用。
○ ポイント: AIを品質管理プロセスにどう組み込むか、人間による最終確認をどの程度行うかなど、品質保証の観点からAI運用を設計・監督します。
これらの役割を明確にし、各チーム・担当者がスムーズに連携するためのコミュニケーション体制や情報共有の仕組み(定期的な会議、レポートラインの設定など)を構築することが、効果的なAI運用には欠かせません。
AIを使いこなす人材の育成
AI外観検査システムの運用には、AIや画像処理に関する専門知識だけでなく、自社の製品や製造プロセスに関する深い理解も求められます。以下のような視点で、人材育成に取り組むことが重要です。
階層別・役割別教育プログラムの実施:
○ 経営層向け: AI活用の戦略的重要性、投資対効果、成功事例などを学ぶ機会を提供。
○ 管理者向け: AIプロジェクトの進め方、運用体制の構築、リスク管理などを学ぶ。
○ AI担当者向け: AIの基礎知識、機械学習、ディープラーニング、画像処理技術、データ分析手法、アノテーションツール操作などを習得。
○ 現場オペレーター向け: AIシステムの日常操作、簡単なトラブルシューティング、異常発見時の報告手順などを学ぶ。
OJT(On-the-Job Training)とOff-JT(Off-the-Job Training)の組み合わせ:
○ 日常業務を通じたOJTに加え、外部研修やセミナー参加、資格取得支援といったOff-JTも活用し、体系的な知識・スキル習得を促進します。
社内勉強会や情報共有の場の設定:
○ 部門横断的な勉強会や、AI活用の成功事例・失敗事例を共有する場を設け、組織全体のAIリテラシー向上を図ります。
外部専門家の活用とナレッジトランスファー:
○ 初期段階では、外部のコンサルタントや専門ベンダーの支援を受けながら運用を進め、その過程で社内にノウハウを蓄積していくことも有効な手段です。
AIを真に「使いこなす」ためには、特定の担当者だけでなく、組織全体としてAIに対する理解を深め、変化に柔軟に対応できる学習する組織文化を醸成していくことが求められます。
5. AI外観検査の価値を持続させるために経営者がすべきこと
本コラムでは、AI外観検査システム導入後の運用における課題、検査精度を維持・向上させるための再学習の重要性、データ管理とシステム保守のポイント、そしてこれらを支える運用体制と人材育成について解説してまいりました。
繰り返しになりますが、AI外観検査は「導入して終わり」のシステムではありません。むしろ、導入後からが本当のスタートであり、その価値を持続させ、さらに高めていくためには、経営層のリーダーシップのもと、組織全体で継続的な改善活動に取り組むことが不可欠です。
運用後に起こりうる様々な問題(精度の低下、新たな不良への未対応、属人化など)を予見し、それらに対する解決策をあらかじめ準備しておくこと。 そして、AIモデルは定期的な再学習によって「育て続ける」ものであるという認識を持つこと。 これが、AI外観検査運用成功の根幹と言えるでしょう。
株式会社船井総合研究所は、AI外観検査の導入支援に留まらず、導入後の運用コンサルティングにも力を入れています。以下のような取り組みを通じて、お客様のAIシステム価値最大化をご支援いたします。
AI運用状況の診断と課題抽出: 現状の運用プロセスや体制を客観的に評価し、改善点を明確にします。
再学習プロセスの構築支援: 効果的なデータ収集・アノテーション方法から、再学習のタイミングや評価指標の設定まで、具体的な運用フローを設計します。
データ管理・活用戦略の策定: 蓄積された検査データを分析し、品質改善や生産性向上に繋げるための施策を提案します。
運用体制構築と人材育成プログラムの提供: お客様の組織体制やリソースに合わせた最適な運用体制の構築を支援し、必要なスキルセットを持つ人材の育成をサポートします。
定期的なフォローアップと改善提案: 導入後も継続的に関与し、市場や技術の変化に対応した改善提案を行います。
このコラムを読んだ後に取るべき行動
AI外観検査システムを導入済みで、本コラムで触れたような課題に直面している、あるいはこれから直面する可能性を感じていらっしゃる経営者様、ご担当者様は、ぜひ一度、現状の運用状況を見直すことから始めてみてください。
そして、もし自社だけでの解決が難しいと感じられたり、より専門的な知見を求められたりする場合には、どうぞお気軽に株式会社船井総合研究所までご相談ください。
私どもは、お客様のAI外観検査システムが真の競争力となり、持続的な企業成長に貢献できるよう、伴走型のコンサルティングを通じて全力でサポートさせていただきます。まずは、貴社の現状の課題や目指す姿をお聞かせください。最適な解決策を共に考え、実行していくことが、私たちの使命です。
お問い合わせはこちら
https://www.funaisoken.co.jp/solution/maker_smartfactory_703_S045 導入して終わりではない!AI外観検査の価値を持続させる運用ノウハウ。専門コンサルタントが継続的な成果創出のポイントを解説。
このコラムをお勧めしたい方のイメージ
既にAI外観検査システムを導入し、その運用に課題を感じている
AI外観検査の導入効果を持続させ、さらに向上させたいと考えている
AIシステムの運用体制構築や人材育成に関心がある
AIモデルの再学習や精度維持の方法について具体的な情報を求めている
製造プロセスの変化に柔軟に対応できるAI検査システムを目指したい
このコラムの内容
本コラムは、AI外観検査システムを導入されたものの、その後の運用において課題を感じている、あるいはさらなる効果を追求したいと考えている経営者様およびご担当者様に向けて、導入後の安定運用と継続的な改善を実現するための重要なポイントを解説します。AI外観検査は導入がゴールではなく、むしろスタートです。本コラムでは、運用フェーズで直面しがちな問題点を洗い出し、それらに対する具体的な解決策を提示します。特に、AIモデルの精度維持に不可欠な再学習のプロセス、変化する製造環境への対応、そしてこれらを支える運用体制の構築と人材育成の重要性について、株式会社船井総合研究所のコンサルタントが具体的な事例やチェックリストを交えながら、実践的なノウハウを提供します。
このコラムを読むメリット
このコラムをお読みいただくことで、AI外観検査システム導入後の運用における具体的な課題とその解決策を深く理解し、自社システムの価値を最大限に引き出すための道筋を描くことができます。「導入したものの、精度が維持できない」「新しい不良に対応できない」「担当者が不在で困っている」といったお悩みを抱える企業様にとって、本コラムはAI外観検査を真の経営貢献ツールへと進化させるための実践的な指針となるでしょう。AIモデルの継続的な改善方法、効果的なデータ管理、ハードウェアメンテナンスのポイント、そして何よりも重要な社内運用体制の構築と人材育成のノウハウを得ることで、変化に強いAI外観検査システムを確立し、持続的な品質向上と生産性向上を実現するための一助となります。
1. AI外観検査「導入後」によくある課題とは?~現状チェックリスト~
AI外観検査導入後の隠れた問題点
AI外観検査システムは、導入直後は高い検査精度を発揮し、省人化や品質向上に貢献することが期待されます。しかし、時間の経過とともに、あるいは製造環境の変化に伴い、様々な問題が顕在化してくるケースが少なくありません。「導入して終わり」ではなく、むしろ導入後からが本当のスタートと言えるでしょう。
株式会社船井総合研究所のコンサルティング現場でも、以下のようなお悩みをよく伺います。
判定精度の低下: 「導入当初は良かったが、最近不良品の見逃しや良品の誤判定が増えてきた。」
検査時間の長期化: 「処理速度が遅くなり、タクトタイムに影響が出ている。」
費用対効果の悪化: 「期待したほどのコスト削減効果が得られていない。」
新たな不良への未対応: 「新しい種類の不良品に対応できず、結局人手で検査している。」
環境変化への追随困難: 「製品のマイナーチェンジや、照明など検査環境の変化にAIが対応しきれない。」
ブラックボックス化と属人化: 「AIの判定根拠が分からず、トラブル時に対応できない。」「導入時の担当者が異動・退職し、システムの詳細が分かる人間がいない。」
ドキュメント不足: 「導入時の完成図書や運用マニュアルが整備されておらず、現状把握が困難。」
ベンダーとの連携問題: 「導入業者と連絡が取れない、あるいは追加費用を要求される。」
ハードウェアの老朽化・陳腐化: 「予備機材がない、または製造中止で入手困難。」
これらの問題は、AI外観検査システムの価値を著しく損なう可能性があります。まずは、自社の運用状況を客観的に把握することが重要です。
【現状チェックリスト】あなたの会社のAI外観検査は大丈夫?
以下の質問項目について、自社の状況をチェックしてみましょう。
判定精度は導入時と比較して低下していませんか? (Q1)
検査時間(タクトタイム)は遅くなっていませんか? (Q2)
導入時に見込んだ費用対効果は維持されていますか? (Q3)
良品を不良品と誤判定するケースは増えていませんか? (Q4)
不良品を見逃す(流出させる)ケースは発生していませんか? (Q5)
AIの判定スコアが低い(判定に迷っている)場合の対応ルールは明確ですか? (Q6)
照明の変化、カメラの汚れ、製品の材質変更など、検査環境や対象物の変化に適切に対応できていますか? (Q7)
新しい種類の不良が発生した場合、AIに追加学習させる仕組みはありますか? (Q8)
検査画像データとAIの判定結果は適切に保存・管理されていますか? (Q9)
AIの再学習に使用するための教師データ(アノテーション済みデータ)は適切に保存・管理・運用されていますか? (Q10)
AIソフトウェアや関連システムのアップデートは定期的に行っていますか? (Q11)
カメラ、照明、PCなどのハードウェアの定期点検、清掃、必要な部品交換は実施されていますか? (Q12)
AIシステムの監視、メンテナンス、データ管理を行う専任または兼任の担当者は明確ですか? (Q13)
担当者に対するAIやシステム運用に関する教育・トレーニングは実施されていますか? (Q14)
製造部門、品質管理部門、情報システム部門など、関係部署との連携体制は構築されていますか? (Q15)
AIの判定基準、検査プロセス、運用方法などを継続的に見直し、改善する活動は行われていますか? (Q16)
これらの質問の多くに「いいえ」や「不十分」という回答が付くようであれば、運用体制やプロセスに何らかの課題を抱えている可能性が高いと言えます。次章以降で、これらの課題に対する具体的な解決策を詳述します。
2. AIは育て続けるもの!検査精度を維持・向上させる再学習の重要性
AI検査精度の経時変化と再学習の必要性
AI外観検査システムは、導入直後には高い検出率を示すことが一般的です。これは、初期学習データがその時点での製品や不良の傾向に最適化されているためです。しかし、運用を続ける中で、様々な要因によりAIの検出率は徐々に低下していく傾向が見られます。例えば、以下のようなケースです。
新たな不良パターンの出現: 製造プロセスの微妙な変化や原材料のロット差などにより、これまで学習データに含まれていなかった新しい種類の不良が発生することがあります。
製品のマイナーチェンジ: 外観にわずかな変更が加えられた場合、AIがそれを異常と誤認識したり、逆に本来検出 すべき不良を見逃したりする可能性があります。
検査環境の変化: 照明の経年劣化や交換、カメラのレンズの汚れやピントのズレ、周囲の明るさの変化などが、撮像される画像に影響を与え、AIの判断を狂わせることがあります。
これらの要因により、導入時に例えば90%だった検出率が、数ヶ月後には85%に低下するといった事態は珍しくありません。この低下した精度を回復させ、さらに向上させるために不可欠なのが「再学習」です。
再学習のプロセスとポイント
再学習とは、新たな画像データをAIモデルに追加で学習させ、その時点での最適な状態にモデルを更新していく作業です。 具体的には、以下のようなステップで進められます。
課題の特定とデータ収集:
○ 「どのような不良を見逃しているのか?」「どのような良品を誤検出しているのか?」を具体的に把握します。
○ 見逃した不良品や誤検出した良品の画像を収集します。また、新たに出現した不良パターンの画像も積極的に収集します。
アノテーション(教師データ化):
○ 収集した画像に対して、専門の担当者が正確な教師ラベル(例:傷、汚れ、気泡など)を付与します(アノテーション作業)。この教師データの質が、再学習後のAIの精度を大きく左右します。
再学習の実施:
○ 既存の学習データに、新たにアノテーションされた画像データを追加、あるいは一部置き換えるなどして、AIモデルに再学習を実行させます。
評価と検証:
○ 再学習後のAIモデルの精度を、テスト用の画像データセットを用いて評価します。期待する精度に達しているか、特定の不良に対する検出能力が改善されたかなどを確認します。
○ 必要に応じて、アノテーションの見直しや学習パラメータの調整を行い、再度学習と評価を繰り返します。
この再学習サイクルを定期的に、あるいは問題が顕在化したタイミングで実施することにより、AIの検出率を再び95%以上に引き上げることも可能です。
再学習における重要なポイント:
学習データの質: 最も重要なのは、質の高い教師データを用意することです。誤ったラベル付けは、AIの性能をむしろ悪化させる可能性があります。
データのバランス: 特定の不良データばかりに偏らず、様々な種類の不良や良品のデータをバランス良く学習させることが望ましいです。
学習データの履歴管理:いつ、どのようなデータで再学習を行ったのか、その結果どう精度が変化したのか、といった履歴を記録・管理することが重要です。これにより、問題発生時の原因究明や、さらなる改善のための知見が蓄積されます。作成した学習データは安易に消去せず、将来的に再活用できる形で保存しておくべきです。
過学習の防止:新しいデータに過剰に適合しすぎると、未知のデータに対する汎化性能が失われる「過学習」に陥る可能性があります。これを防ぐために、学習データとは別に検証用データを用意し、汎化性能も確認しながら再学習を進める必要があります。
データ解析の活用:単に画像を追加するだけでなく、学習データを統計的に解析し、例えばクラスタリング(類似のデータをグループ化)や因果推論(データから原因と結果の関係を推定)といった手法を用いて、どのデータがAIの精度向上に寄与するのか、あるいは逆に精度を落とす要因となっているのかを分析することも有効です。これにより、より効率的で効果的な再学習が可能になります。
AIは一度作ったら完成ではなく、継続的に「育てていく」という意識を持つことが、AI外観検査を長期的に成功させるための鍵となります。株式会社船井総合研究所では、この再学習プロセスの構築支援や、効果的なデータ活用のコンサルティングも提供しております。
3. 変化への対応力が鍵!AI運用におけるデータ管理とシステム保守
AI外観検査システムを安定して長期間運用し、その価値を持続させるためには、AIモデルの再学習だけでなく、それを支えるデータ管理とシステム・ハードウェアの保守も極めて重要です。これらが疎かになると、せっかく導入したAIシステムが期待通りの性能を発揮できなくなるばかりか、最悪の場合、運用停止に追い込まれる可能性もあります。
データ管理の重要性と実践項目
AI外観検査において「データは資産」です。検査で得られた画像データや判定結果、そして再学習に用いる教師データなどを適切に管理・活用することが、システムの継続的な改善と価値向上に繋がります。
検査画像・結果データの蓄積と活用:
○ AIが検査した全ての画像データと、それに対するAIの判定結果(OK/NG、不良の種類、判定スコアなど)を、日時やロット番号などと紐付けて体系的に保存します。
○ これらの蓄積データは、単に記録として残すだけでなく、将来のAIモデルの再学習や、不良発生傾向の分析、歩留まり改善といった品質改善活動のための貴重な情報源となります。例えば、特定の時期に特定の不良が増加する傾向が見られれば、製造プロセスの見直しに繋げることができます。
教師データの管理と更新:
○ AIの再学習に使用する教師データ(アノテーション済み画像)は、その精度がAIモデルの性能に直結するため、特に厳格な管理が求められます。
○ アノテーションの基準を明確にし、作業者間でのばらつきを抑えることが重要です。
○ 新しい不良の種類が発見された場合や、製品仕様に変更があった場合には、速やかに教師データを更新し、最新の状態に保つ必要があります。
○ 教師データのバージョン管理を行い、いつどのような基準で作成・更新されたものかを追跡できるようにしておくことも、後の検証や改善に役立ちます。
データセキュリティとバックアップ:
○ 検査画像や教師データは、企業の機密情報を含む場合があるため、不正アクセスや情報漏洩を防ぐためのセキュリティ対策を講じる必要があります。
○ また、ハードウェアの故障や災害などによるデータ損失リスクに備え、定期的なバックアップと、必要に応じて遠隔地へのバックアップ体制を構築することも重要です。
システム・ハードウェアの保守ポイント
AI外観検査システムは、AIソフトウェアだけでなく、カメラ、照明、PC、搬送装置など、多くのハードウェアから構成されています。これらの物理的な機器が正常に機能し続けることが、システム全体の安定稼働の前提となります。
定期的な点検と清掃:
○ カメラ: レンズの汚れや傷、ピントのズレ、設置位置のズレなどがないか定期的に確認し、清掃や調整を行います。
○ 照明: 照度の低下やちらつき、ランプ切れなどがないか確認し、必要に応じて清掃や交換を行います。照明環境は撮像品質に大きく影響するため、特に注意が必要です。
○ PC・サーバー: 冷却ファンの清掃、内部の埃除去、ケーブル接続の確認などを定期的に行い、熱暴走や接触不良によるトラブルを未然に防ぎます。
○ 搬送装置: センサーの汚れ、可動部の摩耗や異音などを確認し、清掃やグリスアップ、部品交換を行います。
ソフトウェアアップデート:
○ AIソフトウェア本体だけでなく、OSやデータベース、関連ミドルウェアなどのセキュリティパッチや機能アップデート情報を常に把握し、計画的に適用します。アップデートにより、セキュリティ脆弱性の修正や新機能の利用、性能向上が期待できますが、一方で既存システムとの互換性に問題が生じる可能性もあるため、事前の検証が重要です。
予備部品の確保と老朽化対策:
○ 故障時に迅速に交換できるよう、クリティカルな部品(カメラ、照明、特殊なインターフェースカードなど)については予備品を確保しておくことが望ましいです。
○ 特に海外製の部品や特殊な部品は、納期がかかったり、製造中止になったりするリスクがあるため、早期の調達計画が必要です。
○ システム全体の耐用年数を考慮し、計画的なリプレースやアップグレードの予算化も視野に入れておくべきです。
環境整備:
○ AIシステムが設置されている環境(温度、湿度、粉塵、振動など)が、各機器の推奨動作条件を満たしているか確認し、必要に応じて空調設備の導入や防塵対策などを行います。
これらのデータ管理とシステム・ハードウェア保守を継続的に行うことで、AI外観検査システムは長期にわたり安定した性能を発揮し、企業の生産性向上と品質保証に貢献し続けることができます。
4. AIを使いこなす「人」と「組織」~あるべき運用体制と人材育成~
AI外観検査システムを導入し、その効果を持続的に引き出すためには、優れたAIモデルや最新のハードウェアだけでなく、それを適切に運用・管理し、改善していくための「人」と「組織」の力が不可欠です。どんなに高度なシステムも、それを使いこなし、育てていく体制がなければ宝の持ち腐れになりかねません。
AI外観検査運用に必要な役割と体制
企業の規模や検査対象、システムの複雑さなどによって最適な体制は異なりますが、一般的に以下のような役割と、それらを担うチームや担当者が必要となります。
経営層・システム導入推進部門:
○ 役割: AI導入・運用の全体方針決定、投資判断、プロジェクト全体の管理、関係部署間の調整、導入効果測定とROI評価、運用ルールの策定・周知。
○ ポイント: 経営層がAI活用の重要性を理解し、トップダウンで推進することが成功の鍵です。DX推進部門などがハブとなり、全社的な取り組みをリードします。
AIモデル開発・管理チーム(データサイエンティスト、AIエンジニア):
○ 役割: 検査要件に基づいたAIモデルの選定・開発・トレーニング・評価、精度維持・向上のためのモデルの再学習・チューニング、新しい欠陥種類や製品への対応、アノテーション(教師データ作成)の管理・指導。
○ ポイント: AIの専門知識が求められるため、社内育成が難しい場合は、外部の専門企業やコンサルタントとの連携も有効です。
インフラ・IT運用チーム(IT部門、インフラエンジニア):
○ 役割: AI推論用サーバー、カメラ、ネットワークなどのハードウェア・インフラの構築・保守・管理、AIソフトウェア・関連システムの導入・アップデート・セキュリティ管理、システム全体の安定稼働監視、障害対応。
○ ポイント: 既存のITインフラとの連携や、セキュリティポリシーの遵守が重要となります。
生産・製造現場チーム(現場オペレーター、生産技術者):
○ 役割: 日常的なAI検査システムの操作、検査対象物の投入、検査結果の確認、AIが判定困難としたものや異常検知時の初期対応、現場からのフィードバック(例:新しい欠陥の報告、誤検出の指摘)。
○ ポイント: AIシステムを最も日常的に利用するユーザーであり、AI改善のための重要な情報提供者です。AIへの理解と協力を得ることが不可欠です。
品質管理・品質保証チーム(QA/QC担当者):
○ 役割: 検査基準の設定とAIの判定基準との整合性確認、AIの検査精度(見逃し、過検出)の定期的な評価・監査、AIが判定した不良品や要注意品に対する最終確認・ダブルチェック体制の構築・運用、検査結果データの分析と品質改善活動への活用。
○ ポイント: AIを品質管理プロセスにどう組み込むか、人間による最終確認をどの程度行うかなど、品質保証の観点からAI運用を設計・監督します。
これらの役割を明確にし、各チーム・担当者がスムーズに連携するためのコミュニケーション体制や情報共有の仕組み(定期的な会議、レポートラインの設定など)を構築することが、効果的なAI運用には欠かせません。
AIを使いこなす人材の育成
AI外観検査システムの運用には、AIや画像処理に関する専門知識だけでなく、自社の製品や製造プロセスに関する深い理解も求められます。以下のような視点で、人材育成に取り組むことが重要です。
階層別・役割別教育プログラムの実施:
○ 経営層向け: AI活用の戦略的重要性、投資対効果、成功事例などを学ぶ機会を提供。
○ 管理者向け: AIプロジェクトの進め方、運用体制の構築、リスク管理などを学ぶ。
○ AI担当者向け: AIの基礎知識、機械学習、ディープラーニング、画像処理技術、データ分析手法、アノテーションツール操作などを習得。
○ 現場オペレーター向け: AIシステムの日常操作、簡単なトラブルシューティング、異常発見時の報告手順などを学ぶ。
OJT(On-the-Job Training)とOff-JT(Off-the-Job Training)の組み合わせ:
○ 日常業務を通じたOJTに加え、外部研修やセミナー参加、資格取得支援といったOff-JTも活用し、体系的な知識・スキル習得を促進します。
社内勉強会や情報共有の場の設定:
○ 部門横断的な勉強会や、AI活用の成功事例・失敗事例を共有する場を設け、組織全体のAIリテラシー向上を図ります。
外部専門家の活用とナレッジトランスファー:
○ 初期段階では、外部のコンサルタントや専門ベンダーの支援を受けながら運用を進め、その過程で社内にノウハウを蓄積していくことも有効な手段です。
AIを真に「使いこなす」ためには、特定の担当者だけでなく、組織全体としてAIに対する理解を深め、変化に柔軟に対応できる学習する組織文化を醸成していくことが求められます。
5. AI外観検査の価値を持続させるために経営者がすべきこと
本コラムでは、AI外観検査システム導入後の運用における課題、検査精度を維持・向上させるための再学習の重要性、データ管理とシステム保守のポイント、そしてこれらを支える運用体制と人材育成について解説してまいりました。
繰り返しになりますが、AI外観検査は「導入して終わり」のシステムではありません。むしろ、導入後からが本当のスタートであり、その価値を持続させ、さらに高めていくためには、経営層のリーダーシップのもと、組織全体で継続的な改善活動に取り組むことが不可欠です。
運用後に起こりうる様々な問題(精度の低下、新たな不良への未対応、属人化など)を予見し、それらに対する解決策をあらかじめ準備しておくこと。 そして、AIモデルは定期的な再学習によって「育て続ける」ものであるという認識を持つこと。 これが、AI外観検査運用成功の根幹と言えるでしょう。
株式会社船井総合研究所は、AI外観検査の導入支援に留まらず、導入後の運用コンサルティングにも力を入れています。以下のような取り組みを通じて、お客様のAIシステム価値最大化をご支援いたします。
AI運用状況の診断と課題抽出: 現状の運用プロセスや体制を客観的に評価し、改善点を明確にします。
再学習プロセスの構築支援: 効果的なデータ収集・アノテーション方法から、再学習のタイミングや評価指標の設定まで、具体的な運用フローを設計します。
データ管理・活用戦略の策定: 蓄積された検査データを分析し、品質改善や生産性向上に繋げるための施策を提案します。
運用体制構築と人材育成プログラムの提供: お客様の組織体制やリソースに合わせた最適な運用体制の構築を支援し、必要なスキルセットを持つ人材の育成をサポートします。
定期的なフォローアップと改善提案: 導入後も継続的に関与し、市場や技術の変化に対応した改善提案を行います。
このコラムを読んだ後に取るべき行動
AI外観検査システムを導入済みで、本コラムで触れたような課題に直面している、あるいはこれから直面する可能性を感じていらっしゃる経営者様、ご担当者様は、ぜひ一度、現状の運用状況を見直すことから始めてみてください。
そして、もし自社だけでの解決が難しいと感じられたり、より専門的な知見を求められたりする場合には、どうぞお気軽に株式会社船井総合研究所までご相談ください。
私どもは、お客様のAI外観検査システムが真の競争力となり、持続的な企業成長に貢献できるよう、伴走型のコンサルティングを通じて全力でサポートさせていただきます。まずは、貴社の現状の課題や目指す姿をお聞かせください。最適な解決策を共に考え、実行していくことが、私たちの使命です。
お問い合わせはこちら
https://www.funaisoken.co.jp/solution/maker_smartfactory_703_S045