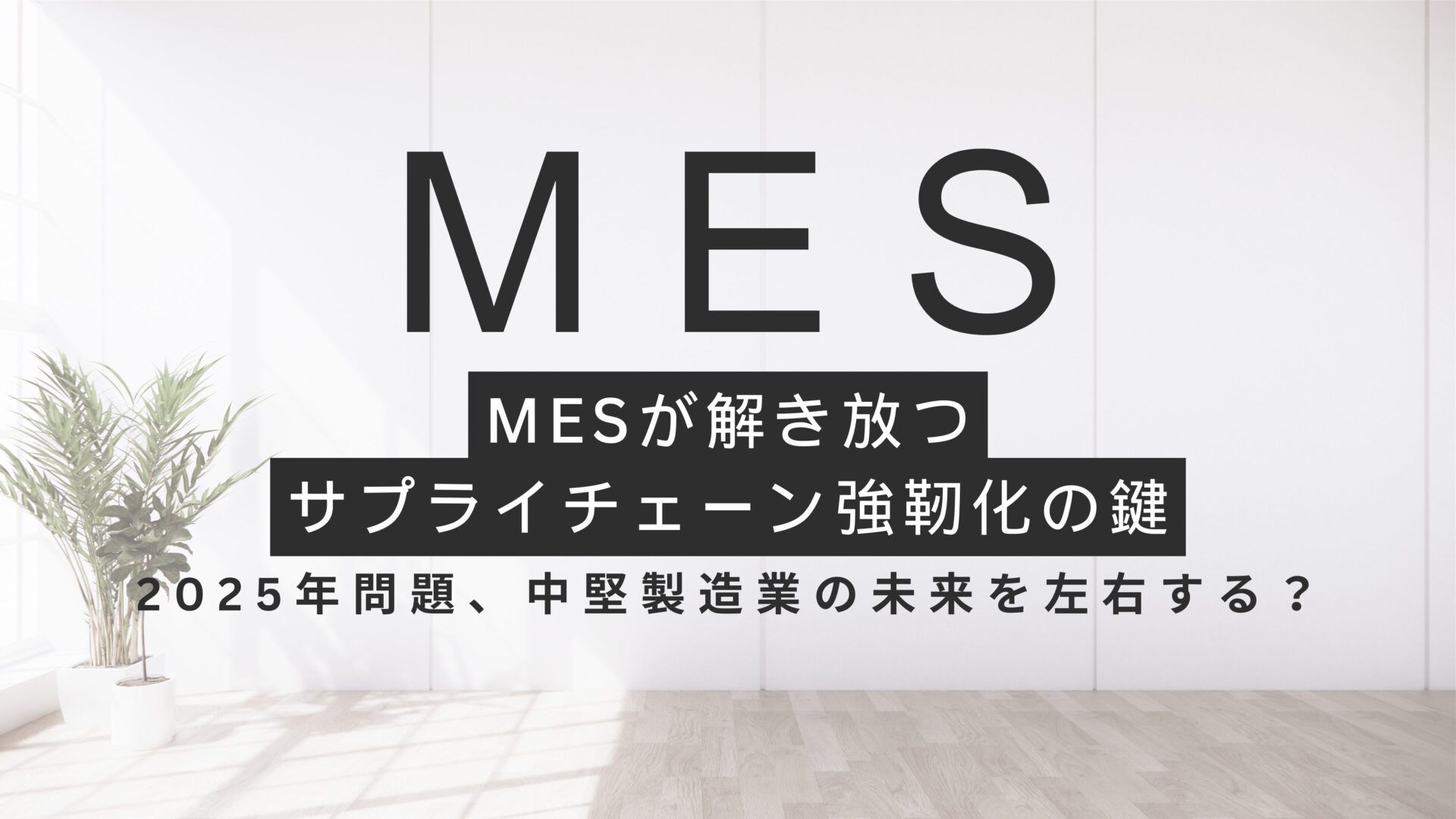
2025年問題、中堅製造業の未来を左右する?MESが解き放つサプライチェーン強靭化の鍵
2025.06.24
刻一刻と迫る「2025年問題」。
少子高齢化による労働力人口の減少、熟練技術者の大量引退は、中堅製造業にとって喫緊の課題です。単なる人手不足では片付けられない、生産性の低下、技術継承の断絶、そしてサプライチェーン全体の脆弱化…この大きな波を前に、貴社はどのような手を打つべきでしょうか?
本記事では、この喫緊の課題に対し、MES(製造実行システム)がいかに強力な解決策となり、貴社のサプライチェーンを盤石なものにするかを徹底解説します。
2025年問題が中堅製造業に突きつける「3つの壁」
人材の壁: 熟練技術者の引退によるノウハウの喪失、若手人材の確保難。
生産性の壁: 人手不足による生産ラインの維持困難、生産計画の最適化の停滞。
サプライチェーンの壁: 国内の生産体制の変化、海外リスクの増大に対する脆弱性。
これらの壁は、貴社の事業継続性、ひいては競争力そのものを脅かしかねません。しかし、MESを導入することで、これらの課題に先手を打つことが可能です。
MESが「2025年問題」を解決する具体的アプローチ
MESは、製造現場のあらゆる情報をリアルタイムで収集・分析・可視化するシステムです。これにより、2025年問題がもたらす課題を以下のように解決します。
人手不足・技術継承の課題解消:
作業手順の標準化とデジタル化: 熟練工の「勘と経験」をデータとして蓄積し、誰でも高品質な作業ができるよう標準化。新人教育の効率化にも貢献します。
リアルタイム進捗管理: 現場の状況を「見える化」し、少人数でも効率的な生産管理を実現。
自動化・省力化の推進: MESと連携することで、ロボットや自動機の導入をスムーズにし、人手に頼る部分を削減。
サプライチェーン強靭化への貢献:
生産計画の最適化: 需要予測や在庫状況、設備稼働率などに基づき、最適な生産計画を自動立案。突発的な事態にも柔軟に対応できます。
品質トレーサビリティの確保:
製品の製造履歴、使用部品、検査結果などを詳細に記録し、万一の際に迅速な原因究明と対応が可能に。サプライヤーとの連携強化にも繋がります。
リアルタイムな情報共有: サプライヤーや顧客との間で生産進捗や在庫情報をリアルタイムで共有し、サプライチェーン全体の透明性と連携を強化します。
これらのアプローチは、絵に描いた餅ではありません。現に、今回のセミナーで登壇されるデンソーウェーブ様をはじめ、多くの中堅企業がMESとIoTの連携によって成果を上げています。こうした具体的な事例から学ぶことは、貴社のDX推進の大きなヒントとなるでしょう。
中堅製造業が今すぐ取るべき行動:MES導入の成功の鍵
MES導入は、貴社の未来を拓く戦略的な投資です。成功のためには、以下のポイントが重要です。
現状課題の明確化: 貴社が抱える具体的な2025年問題に関連する課題を特定します。
目的の明確化: MES導入によって何を達成したいのか、具体的な目標を設定します。
スモールスタート: まずは一部の工程やラインに導入し、効果を検証しながら段階的に拡大します。
ベンダー選定: 貴社の業種・規模に合ったMESを提供し、導入から運用まで手厚いサポートを受けられるベンダーを選びましょう。
▼関連記事「製造業 生産性向上支援(IoT・自動化)」
https://www.funaisoken.co.jp/solution/dc-highmix-lowvolume_706_S045
まとめ:未来を掴む、MESという選択肢
2025年問題は、中堅製造業にとって大きな試練であると同時に、DXを推進し、新たな競争力を獲得する絶好の機会でもあります。MESを導入することで、人手不足の解消、技術継承、そしてサプライチェーンの強靭化という3つの課題を一挙に解決し、持続可能な成長を実現できます。
今こそ、未来を見据えた賢い投資を行い、貴社の生産体制を盤石なものにしませんか?
▼参考記事「【第3回】『勘と経験頼み』から脱却!データが語る、製造現場の隠れた課題と改善策 ~MES導入で見える化する、生産性向上の次の一手~」
https://smart-factory.funaisoken.co.jp/250604-4/
貴社の課題解決のヒントがここに。MES活用の最前線を学びませんか?
本記事で解説したMESによるサプライチェーン強靭化。その具体的な実践方法と成功の秘訣を、業界の第一線で活躍する企業の事例から直接学べる絶好の機会をご用意しました。
「中堅製造業のためのMES活用&事例紹介セミナー」では、デンソーウェーブ様にご登壇いただき、IoT活用による驚異の生産性向上事例を詳しくご紹介いただきます。
「人手不足やコスト増に、今すぐ具体的な対策を打ちたい」
「他社の成功事例から、自社に合ったDXの進め方を学びたい」
このようにお考えの経営者様、現場責任者様は、ぜひご参加ください。貴社の未来を切り拓く、実践的なヒントがここにあります。
▼セミナー申し込みはこちらから
https://www.funaisoken.co.jp/seminar/130320
【このような方にオススメ】
・従業員数200~2000名の変革期を迎える中堅製造業の方
・現在、現場の人手不足や原材料費の高騰などに悩んでおり、MESやIoTを活用した具体的な改善策を探している方
・社内のシステム導入・運用を担当されており、製造現場のIT化やIoT連携に関心のある方
・IoTやDXに関心があり、デンソーウェーブ様の先進的な事例から学びたいと考えている方
・工場の生産性向上、自動化、省人化に関心があり、具体的な技術や導入事例を知りたい方
・近年の製品多様化に伴い、管理が複雑化していく中で必要なシステム活用を知りたいと考えている従業員数200名以上の製造業の方
【本セミナーで学べるポイント】
・従業員200~2000名の製造業におけるMES活用の重要性が学べる!
~市場動向を踏まえ、なぜ今中堅製造業がMESに取り組むべきなのか、具体的なメリットや実現できる姿を理解できます。~
・IoT連携による製造現場の革新事例が学べる!
~デンソーウェーブ様にご登壇いただき、IoTをどのように生産性向上や現場の可視化を実現できるのか、具体的な事例を通して学ぶことができます。~
・人手不足・コスト増の課題解決のヒントが学べる!
~MESやIoTの導入によって、どのように省人化を進め、コストを削減できるのか、具体的な取り組みや効果について理解を深めることができます。~
・自社に適したMES導入への第一歩が学べる!
~中堅製造業がMES導入を検討する上で重要なポイントや、成功のためのステップ、注意点などを把握することができます。~ 刻一刻と迫る「2025年問題」。
少子高齢化による労働力人口の減少、熟練技術者の大量引退は、中堅製造業にとって喫緊の課題です。単なる人手不足では片付けられない、生産性の低下、技術継承の断絶、そしてサプライチェーン全体の脆弱化…この大きな波を前に、貴社はどのような手を打つべきでしょうか?
本記事では、この喫緊の課題に対し、MES(製造実行システム)がいかに強力な解決策となり、貴社のサプライチェーンを盤石なものにするかを徹底解説します。
2025年問題が中堅製造業に突きつける「3つの壁」
人材の壁: 熟練技術者の引退によるノウハウの喪失、若手人材の確保難。
生産性の壁: 人手不足による生産ラインの維持困難、生産計画の最適化の停滞。
サプライチェーンの壁: 国内の生産体制の変化、海外リスクの増大に対する脆弱性。
これらの壁は、貴社の事業継続性、ひいては競争力そのものを脅かしかねません。しかし、MESを導入することで、これらの課題に先手を打つことが可能です。
MESが「2025年問題」を解決する具体的アプローチ
MESは、製造現場のあらゆる情報をリアルタイムで収集・分析・可視化するシステムです。これにより、2025年問題がもたらす課題を以下のように解決します。
人手不足・技術継承の課題解消:
作業手順の標準化とデジタル化: 熟練工の「勘と経験」をデータとして蓄積し、誰でも高品質な作業ができるよう標準化。新人教育の効率化にも貢献します。
リアルタイム進捗管理: 現場の状況を「見える化」し、少人数でも効率的な生産管理を実現。
自動化・省力化の推進: MESと連携することで、ロボットや自動機の導入をスムーズにし、人手に頼る部分を削減。
サプライチェーン強靭化への貢献:
生産計画の最適化: 需要予測や在庫状況、設備稼働率などに基づき、最適な生産計画を自動立案。突発的な事態にも柔軟に対応できます。
品質トレーサビリティの確保:
製品の製造履歴、使用部品、検査結果などを詳細に記録し、万一の際に迅速な原因究明と対応が可能に。サプライヤーとの連携強化にも繋がります。
リアルタイムな情報共有: サプライヤーや顧客との間で生産進捗や在庫情報をリアルタイムで共有し、サプライチェーン全体の透明性と連携を強化します。
これらのアプローチは、絵に描いた餅ではありません。現に、今回のセミナーで登壇されるデンソーウェーブ様をはじめ、多くの中堅企業がMESとIoTの連携によって成果を上げています。こうした具体的な事例から学ぶことは、貴社のDX推進の大きなヒントとなるでしょう。
中堅製造業が今すぐ取るべき行動:MES導入の成功の鍵
MES導入は、貴社の未来を拓く戦略的な投資です。成功のためには、以下のポイントが重要です。
現状課題の明確化: 貴社が抱える具体的な2025年問題に関連する課題を特定します。
目的の明確化: MES導入によって何を達成したいのか、具体的な目標を設定します。
スモールスタート: まずは一部の工程やラインに導入し、効果を検証しながら段階的に拡大します。
ベンダー選定: 貴社の業種・規模に合ったMESを提供し、導入から運用まで手厚いサポートを受けられるベンダーを選びましょう。
▼関連記事「製造業 生産性向上支援(IoT・自動化)」
https://www.funaisoken.co.jp/solution/dc-highmix-lowvolume_706_S045
まとめ:未来を掴む、MESという選択肢
2025年問題は、中堅製造業にとって大きな試練であると同時に、DXを推進し、新たな競争力を獲得する絶好の機会でもあります。MESを導入することで、人手不足の解消、技術継承、そしてサプライチェーンの強靭化という3つの課題を一挙に解決し、持続可能な成長を実現できます。
今こそ、未来を見据えた賢い投資を行い、貴社の生産体制を盤石なものにしませんか?
▼参考記事「【第3回】『勘と経験頼み』から脱却!データが語る、製造現場の隠れた課題と改善策 ~MES導入で見える化する、生産性向上の次の一手~」
https://smart-factory.funaisoken.co.jp/250604-4/
貴社の課題解決のヒントがここに。MES活用の最前線を学びませんか?
本記事で解説したMESによるサプライチェーン強靭化。その具体的な実践方法と成功の秘訣を、業界の第一線で活躍する企業の事例から直接学べる絶好の機会をご用意しました。
「中堅製造業のためのMES活用&事例紹介セミナー」では、デンソーウェーブ様にご登壇いただき、IoT活用による驚異の生産性向上事例を詳しくご紹介いただきます。
「人手不足やコスト増に、今すぐ具体的な対策を打ちたい」
「他社の成功事例から、自社に合ったDXの進め方を学びたい」
このようにお考えの経営者様、現場責任者様は、ぜひご参加ください。貴社の未来を切り拓く、実践的なヒントがここにあります。
▼セミナー申し込みはこちらから
https://www.funaisoken.co.jp/seminar/130320
【このような方にオススメ】
・従業員数200~2000名の変革期を迎える中堅製造業の方
・現在、現場の人手不足や原材料費の高騰などに悩んでおり、MESやIoTを活用した具体的な改善策を探している方
・社内のシステム導入・運用を担当されており、製造現場のIT化やIoT連携に関心のある方
・IoTやDXに関心があり、デンソーウェーブ様の先進的な事例から学びたいと考えている方
・工場の生産性向上、自動化、省人化に関心があり、具体的な技術や導入事例を知りたい方
・近年の製品多様化に伴い、管理が複雑化していく中で必要なシステム活用を知りたいと考えている従業員数200名以上の製造業の方
【本セミナーで学べるポイント】
・従業員200~2000名の製造業におけるMES活用の重要性が学べる!
~市場動向を踏まえ、なぜ今中堅製造業がMESに取り組むべきなのか、具体的なメリットや実現できる姿を理解できます。~
・IoT連携による製造現場の革新事例が学べる!
~デンソーウェーブ様にご登壇いただき、IoTをどのように生産性向上や現場の可視化を実現できるのか、具体的な事例を通して学ぶことができます。~
・人手不足・コスト増の課題解決のヒントが学べる!
~MESやIoTの導入によって、どのように省人化を進め、コストを削減できるのか、具体的な取り組みや効果について理解を深めることができます。~
・自社に適したMES導入への第一歩が学べる!
~中堅製造業がMES導入を検討する上で重要なポイントや、成功のためのステップ、注意点などを把握することができます。~