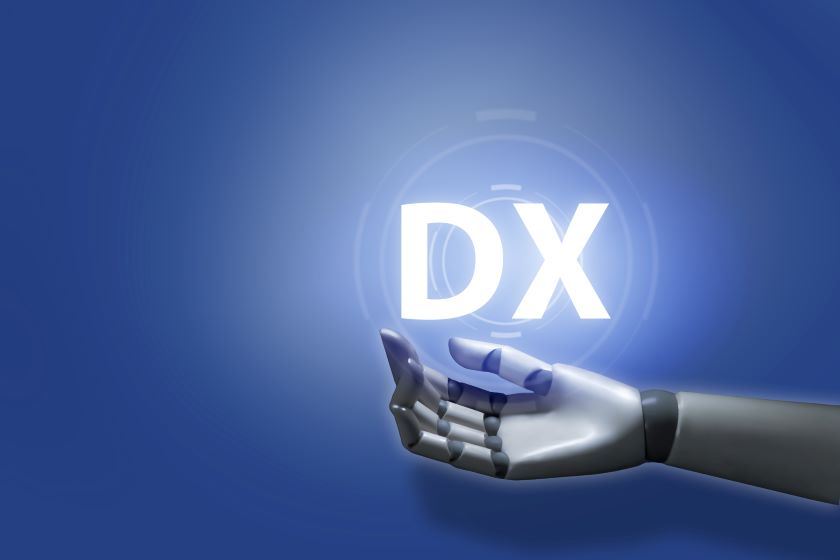
人型ロボットって実際どうなの?
2025.06.19
Teslaや、BMWなどの工場で活用されている、人型ロボット。
人型ロボットって実際のところどうなの?
内容まとめて教えてよ!
というお声を先週2回もいただきましたので、調べさせていただきました。
私自身、人型ロボットの本格活用はまだまだ先だろう、と思っていましたが、調べてみると日本の製造現場でも使われる日が来るかもしれない、と感じました。
本コラムでは、人型ロボットとは、従来のロボットとの違い、人型ロボットの価格について解説いたします。
人型ロボットについて学ぶ前に、協働ロボットの理解は進んでおりますでしょうか?
人型ロボットの前に、協働ロボットで何ができるのか知りたい!
どんなロボットが出ているのか知りたい!
多品種少量生産において、協働ロボットをどのように使えば良いか知りたい!
という方向けに、7月開催の「徹底比較!協働ロボット【実機体験】セミナー」をご紹介いたします。(詳細は本コラム下部を参照)
協働ロボット活用事例のご紹介から、メーカー各社の比較、本体価格100万円以下の協働ロボットのご紹介、協働ロボット実機体験など、盛りだくさんの2時間となっております。是非ご検討ください。
1.人型ロボットとは
“人型ロボットとは何か“、を理解するために、まずは人型ロボットが稼働している動画をご覧ください。
動画:BMWにおける活用事例
(引用:igure Status Update - BMW Full Use Case)
人型ロボット(ヒューマノイドロボット)は、人間の身体構造を模倣して設計されたロボットです。頭部、胴体、両腕、両脚を持ち、人間と同様の基本的な動作が可能な設計となっています。従来のSF映画に登場するような夢の技術から、現実の産業応用へと急速に進化を遂げています。
近年、AI技術の飛躍的な発展により、人型ロボットは単なる機械的な動作を行うだけでなく、環境を認識し、判断し、学習する能力を獲得しました。特に大規模言語モデル(LLM)との統合により、自然言語による指示理解や複雑なタスクの実行が可能になり、産業界からの注目度が急激に高まっています。
現在、Tesla、Boston Dynamics、Honda、トヨタなど、世界の主要企業が人型ロボットの開発に巨額の投資を行っており、2024年から2025年にかけて商用化が本格的に始まろうとしています。2025年6月現在は、まだ活用方法を模索している段階と言えますが、そう遠くない未来、日本の製造現場においても活用されるかもしれません。
2.人型ロボットと、産業用ロボット & 協働ロボットとの違い
人型ロボットと、従来のロボットの違いは以下の2点です。
①ティーチング不要(!?) - 自然言語で指示を解釈し、稼働できる点
従来の産業用ロボットは、事前にプログラミングされた動作を正確に繰り返すことに特化していました。新しい作業を行わせるためには、専門的な知識を持つエンジニアがティーチングペンダントを使用して、細かい動作を一つ一つプログラムする必要がありました。
しかし、人型ロボットは根本的に異なるアプローチを採用しています。AI技術、特に自然言語処理能力により、「その箱をA棚に運んで」「製品を検査してXX不良があれば取り除いて」といった日常的な言葉での指示を理解し、実行することができます。これにより、専門的なプログラミング知識を持たない現場作業者でも、ロボットに新しい作業を教えることが可能になります。どこまで内容を理解し、動作できるのか疑問が残りますが、Alexaなどの存在を鑑みると、そこまで飛躍的な話でもないでしょう。
②ロボットに合わせて、生産体制を整備する必要がないこと
産業用ロボットの導入には、多くの場合、生産ラインの大幅な改修が必要でした。ロボットアームの可動範囲に合わせてワークステーションを設計し直し、安全柵を設置し、専用の治具や設備を準備する必要がありました。
人型ロボットの最大の利点は、既存の人間用に設計された作業環境をそのまま活用できることです。人間と同じ身体構造を持つため、既存の工具、設備、作業台をそのまま使用でき、大規模な設備投資や生産ライン変更を必要としません。また、人間の作業者と同じ空間で協働することも可能で、柔軟な生産体制の構築が実現できます。
ロボット導入でよくある課題が、“作業スペースの制限”です。人型ロボットは安全柵もなく、スペースも比較的取らないため、活用の幅が大きく広がりそうです。
3.人型ロボットの価格
現在発表されている人型ロボットの価格帯は、メーカーや機能により大きく異なります。主要どころの価格を以下に記載します。
i) Tesla Optimus:約200万円〜300万円(予想価格) Teslaのイーロン・マスクCEOは、量産時には20,000ドル(約300万円)以下での提供を目指すと発表しています。
ii)Boston Dynamics Atlas:価格未公表(研究開発段階) 商用版の具体的な価格は未発表ですが、従来の同社製品から推測すると1000万円以上になると予想されます。
iii) 中国系メーカー各社:100万円〜500万円 UBTech、Agility Roboticsなどが比較的低価格での市場参入を図っています。
思ったより安いですね。その辺の協働ロボットよりも安いかも...
4.まとめ
人型ロボットは、従来の産業用ロボットとは根本的に異なる新しいカテゴリーの技術です。AI技術の進歩により、自然言語での指示理解、既存環境での即座の稼働、専門知識不要の運用が可能になりました。
価格面でも、量産効果により人間の労働者と競合できるレベルまで下がってきており、特に人手不足が深刻な製造業、物流業、サービス業での導入が加速すると予想されます。
今後5年間で、人型ロボットは工場の生産ライン、倉庫作業、清掃業務、介護支援など、様々な分野で人間と協働する光景が当たり前になるでしょう。企業は今から人型ロボット導入の準備を進め、新しい労働力革命に備える必要があります。
ただし、技術的な課題もまだ残されており、安全性の確保、メンテナンス体制の整備、従業員の再教育など、導入に向けた総合的な検討が重要になります。人型ロボットは単なる技術革新ではなく、働き方そのものを変革する可能性を秘めた画期的な存在なのです。
徹底比較!協働ロボット【実機体験】セミナー
https://www.funaisoken.co.jp/seminar/129957
Teslaや、BMWなどの工場で活用されている、人型ロボット。
人型ロボットって実際のところどうなの?
内容まとめて教えてよ!
というお声を先週2回もいただきましたので、調べさせていただきました。
私自身、人型ロボットの本格活用はまだまだ先だろう、と思っていましたが、調べてみると日本の製造現場でも使われる日が来るかもしれない、と感じました。
本コラムでは、人型ロボットとは、従来のロボットとの違い、人型ロボットの価格について解説いたします。
人型ロボットについて学ぶ前に、協働ロボットの理解は進んでおりますでしょうか?
人型ロボットの前に、協働ロボットで何ができるのか知りたい!
どんなロボットが出ているのか知りたい!
多品種少量生産において、協働ロボットをどのように使えば良いか知りたい!
という方向けに、7月開催の「徹底比較!協働ロボット【実機体験】セミナー」をご紹介いたします。(詳細は本コラム下部を参照)
協働ロボット活用事例のご紹介から、メーカー各社の比較、本体価格100万円以下の協働ロボットのご紹介、協働ロボット実機体験など、盛りだくさんの2時間となっております。是非ご検討ください。
1.人型ロボットとは
“人型ロボットとは何か“、を理解するために、まずは人型ロボットが稼働している動画をご覧ください。
動画:BMWにおける活用事例
(引用:igure Status Update - BMW Full Use Case)
人型ロボット(ヒューマノイドロボット)は、人間の身体構造を模倣して設計されたロボットです。頭部、胴体、両腕、両脚を持ち、人間と同様の基本的な動作が可能な設計となっています。従来のSF映画に登場するような夢の技術から、現実の産業応用へと急速に進化を遂げています。
近年、AI技術の飛躍的な発展により、人型ロボットは単なる機械的な動作を行うだけでなく、環境を認識し、判断し、学習する能力を獲得しました。特に大規模言語モデル(LLM)との統合により、自然言語による指示理解や複雑なタスクの実行が可能になり、産業界からの注目度が急激に高まっています。
現在、Tesla、Boston Dynamics、Honda、トヨタなど、世界の主要企業が人型ロボットの開発に巨額の投資を行っており、2024年から2025年にかけて商用化が本格的に始まろうとしています。2025年6月現在は、まだ活用方法を模索している段階と言えますが、そう遠くない未来、日本の製造現場においても活用されるかもしれません。
2.人型ロボットと、産業用ロボット & 協働ロボットとの違い
人型ロボットと、従来のロボットの違いは以下の2点です。
①ティーチング不要(!?) - 自然言語で指示を解釈し、稼働できる点
従来の産業用ロボットは、事前にプログラミングされた動作を正確に繰り返すことに特化していました。新しい作業を行わせるためには、専門的な知識を持つエンジニアがティーチングペンダントを使用して、細かい動作を一つ一つプログラムする必要がありました。
しかし、人型ロボットは根本的に異なるアプローチを採用しています。AI技術、特に自然言語処理能力により、「その箱をA棚に運んで」「製品を検査してXX不良があれば取り除いて」といった日常的な言葉での指示を理解し、実行することができます。これにより、専門的なプログラミング知識を持たない現場作業者でも、ロボットに新しい作業を教えることが可能になります。どこまで内容を理解し、動作できるのか疑問が残りますが、Alexaなどの存在を鑑みると、そこまで飛躍的な話でもないでしょう。
②ロボットに合わせて、生産体制を整備する必要がないこと
産業用ロボットの導入には、多くの場合、生産ラインの大幅な改修が必要でした。ロボットアームの可動範囲に合わせてワークステーションを設計し直し、安全柵を設置し、専用の治具や設備を準備する必要がありました。
人型ロボットの最大の利点は、既存の人間用に設計された作業環境をそのまま活用できることです。人間と同じ身体構造を持つため、既存の工具、設備、作業台をそのまま使用でき、大規模な設備投資や生産ライン変更を必要としません。また、人間の作業者と同じ空間で協働することも可能で、柔軟な生産体制の構築が実現できます。
ロボット導入でよくある課題が、“作業スペースの制限”です。人型ロボットは安全柵もなく、スペースも比較的取らないため、活用の幅が大きく広がりそうです。
3.人型ロボットの価格
現在発表されている人型ロボットの価格帯は、メーカーや機能により大きく異なります。主要どころの価格を以下に記載します。
i) Tesla Optimus:約200万円〜300万円(予想価格) Teslaのイーロン・マスクCEOは、量産時には20,000ドル(約300万円)以下での提供を目指すと発表しています。
ii)Boston Dynamics Atlas:価格未公表(研究開発段階) 商用版の具体的な価格は未発表ですが、従来の同社製品から推測すると1000万円以上になると予想されます。
iii) 中国系メーカー各社:100万円〜500万円 UBTech、Agility Roboticsなどが比較的低価格での市場参入を図っています。
思ったより安いですね。その辺の協働ロボットよりも安いかも...
4.まとめ
人型ロボットは、従来の産業用ロボットとは根本的に異なる新しいカテゴリーの技術です。AI技術の進歩により、自然言語での指示理解、既存環境での即座の稼働、専門知識不要の運用が可能になりました。
価格面でも、量産効果により人間の労働者と競合できるレベルまで下がってきており、特に人手不足が深刻な製造業、物流業、サービス業での導入が加速すると予想されます。
今後5年間で、人型ロボットは工場の生産ライン、倉庫作業、清掃業務、介護支援など、様々な分野で人間と協働する光景が当たり前になるでしょう。企業は今から人型ロボット導入の準備を進め、新しい労働力革命に備える必要があります。
ただし、技術的な課題もまだ残されており、安全性の確保、メンテナンス体制の整備、従業員の再教育など、導入に向けた総合的な検討が重要になります。人型ロボットは単なる技術革新ではなく、働き方そのものを変革する可能性を秘めた画期的な存在なのです。
徹底比較!協働ロボット【実機体験】セミナー
https://www.funaisoken.co.jp/seminar/129957