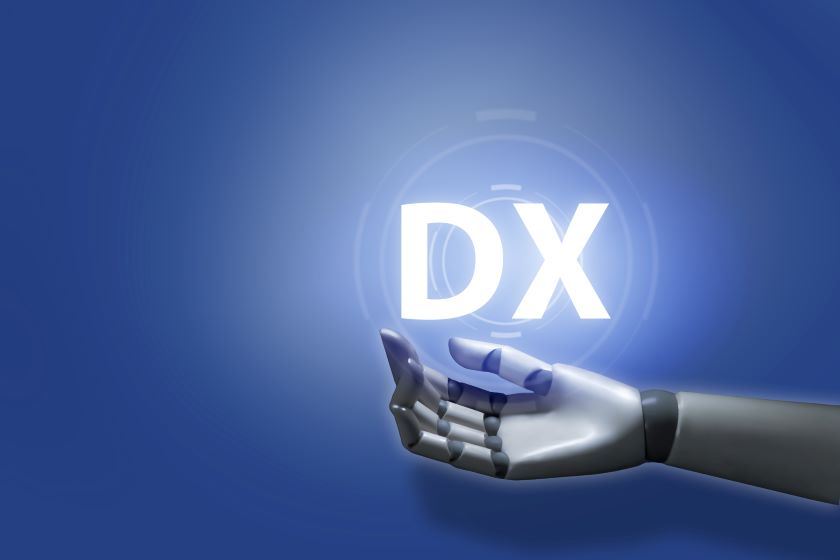
「知らなきゃマズい!?2025年設備投資に使える補助金」
2025.01.06
製造業の経営者様、幹部社員の皆様、あけましておめでとうございます!
船井総合研究所の徳竹です。
「設備投資をしたいけど、費用が…」 「最新設備を導入して生産性を上げたいけど、なかなか踏み切れない…」
そんな悩みをお持ちのあなたへ。
2025年は、補助金を活用して設備投資を加速させる絶好のチャンスです!
1.2025年の補助金はどうなる? 最新情報をキャッチ!
2025年の補助金制度は、大きく以下の5つのポイントを押さえておきましょう。
① 大規模成長投資補助金は2025年も続行!
最低投資額10億円、最大補助上限50億円(補助率1/3)の超大型補助金が来年も出ます! 2027年末までに終える大規模投資を考えている場合は、ぜひご検討ください。
② 中小企業成長加速化補助金の新設!※詳しくは下へスクロール
売上高100億円を目指す企業に向けた設備投資への補助金が新設される見込みです。 大規模成長補助金(最低投資額10億円)は大きすぎて使いづらかったという会社様は要チェックです。
③ 「事業再構築補助金」は「新事業進出補助金(仮称)」へ進化!
事業再構築補助金は、約1500億円残っていた基金を流用する形で新たな補助金へと生まれ変わるようです。 対象事業や補助金額等、これまで事業再構築補助金を使ってしまった、自社では使い勝手が悪かったという会社様も動向を注視していく必要があります。
④ ものづくり補助金は継続も、上限・枠・要件の見直しへ
「最低賃金近傍の事業者に対する支援拡充」と記載があるように、賃上げの流れは来年もさらに加速していくと考えられます。 補助金をうまく活用して、人件費の上昇を上回る成長を遂げていきましょう!
⑤ 省エネやGX系の補助金も過去最高予算
省エネ関係は引き続き出ます!古くなったエアコンや生産設備の入れ替えなどでも使えますので、積極的に活用していきましょう。
2.中小企業必見!「中小企業成長加速化補助金」とは?
中小企業の皆様には、「中小企業成長加速化補助金」がおすすめです。
これは、売上高100億円への飛躍的成長を目指す中小企業を対象とした補助金で、最大5億円(補助率1/2)の補助を受けることができます。
「中小企業成長加速化補助金」の概要
補助対象者:売上高100億円への飛躍的成長を目指す中小企業
補助上限額:5億円(補助率1/2)
補助事業実施期間:交付決定日から24か月以内
補助事業の要件:投資額1億円以上(専門家経費・外注費を除く補助対象経費分)「売上高100億円を目指す宣言」を行っていることその他、賃上げ要件 など
補助対象経費:建物費、機械装置等費、ソフトウェア費、外注費、専門家経費
「売上高100億円を目指す宣言」とは、中小企業が「売上高100億円を超える企業になる」という目標と、そのためのビジョンや取り組みを宣言し、ポータルサイト上で公表するものです。
この宣言を行うことで、以下のメリットがあります。
「宣言」マークの活用による自社PR:「宣言」を行った企業だけ「ロゴマーク」を使用できます。
経営者ネットワークへの参加:地域・業種を超えた経営者ネットワークに参加し、交流や情報交換ができます。
「宣言」取得による補助金等の活用:上記で紹介した「中小企業成長加速化補助金」を含む、様々な補助金の申請が可能になります。
補助金の獲得にはポイントをおさえることが非常に重要です。
なぜなら、補助金の審査をする審査員はこの「ポイント」を重点的に見ているからです。
逆に言うと、いくら素晴らしい投資計画や事業計画を立てても「ポイント」を外してしまうと補助金の採択からは遠ざかってしまいます。
ここからは補助金獲得のポイントと昨年2024年の補助金獲得事例をみていきましょう。
3.補助金獲得のポイントとは? 2024年大型補助金の獲得事例を紹介
「補助金って、申請が難しそう…」 「うちの会社に採択されるか不安…」
そう思われるかもしれません。
確かに、補助金を獲得するためには、事業計画の内容や実現可能性、将来的な成長性などをしっかりとアピールする必要があります。
しかし、ご安心ください。
適切な準備と戦略があれば、多額の補助金を獲得し、大規模な設備投資を実現できる可能性があります。
例えば、2024年には、
鉄骨加工工場新設で約7億円
食品加工工場新設で約41億円
電気部品加工工場新設で約29億円
といった、大型補助金の活用事例が出ています。
4.補助金採択の確立を上げる方法
2月25日(火)、26日(水)、28日(金)に開催される
「【2025年最新】工場新設・設備投資!製造業の補助金セミナー」
では、補助金獲得の秘訣を、わかりやすく解説いたします。
セミナーで得られるもの
2025年最新の補助金制度の情報
採択されるためポイント
工場新設・設備投資の成功事例
DX、自動化、省人化、IoT化など、生産性向上のためのノウハウ
工場新設や設備投資における事業計画・建築計画・設備計画の方法
さらに!
オンライン形式で、PCがあればどこでも受講可能!
視覚的にわかりやすい資料で、理解を深めます!
【参加者限定】セミナー後の個別相談でさらに詳細な情報をGET!
行動を起こすなら今!
補助金には限りがあり、申請が遅れるとチャンスを逃してしまう可能性があります。
準備を今すぐ始めましょう!
皆様のご参加を心よりお待ちしております。
■関連するセミナーのご案内
https://www.funaisoken.co.jp/seminar/124103
【2025年最新】工場新設・設備投資!製造業の補助金セミナー
最大50億円の補助金を活用して工場新設や設備投資する具体的な手法と成功事例
2025年 工場新設・設備投資に使える!補助金活用講座
補助金動向講座「2025年最新版!製造業が使える補助金情報と採択のポイント」
2025年 製造業が使える補助金最新情報!
最大50億円!補助金活用のポイントを解説
製造業が押さえておくべき補助金活用時の考え方
最新補助金情報の超有力な獲得手法!
AI外観検査導入を検討されている方は、ぜひこの機会にセミナーにご参加ください。
お申し込みはこちら
https://www.funaisoken.co.jp/dl-contents/jy-robot_S045
【製造業 ロボット活用・自動化】時流予測レポート2025
工場の自動化・ロボット導入を成功させるための秘訣を凝縮!
本レポートでは、工場の自動化・ロボット活用の現状と将来展望、そして具体的な導入プロセスについて解説しています。
特に、2025年に向けて、製造業が実践すべき工場自動化戦略として、4つのSTEPで進めるロボット活用と、効果最大化のための製品・作業分析を紹介しています。
また、スムーズな工場のロボット導入を実現するための具体的な取組みとして、ROIを考慮した導入計画の重要性を解説し、段階的な導入によるリスク抑制と効果最大化について解説しています。
さらに、具体的な事例を挙げながら、各社の工場自動化・ロボット活用状況や成果を紹介し、読者の皆様にロボット導入のイメージを掴んでいただけるよう工夫しています。
お申し込みはこちら 製造業の経営者様、幹部社員の皆様、あけましておめでとうございます!
船井総合研究所の徳竹です。
「設備投資をしたいけど、費用が…」 「最新設備を導入して生産性を上げたいけど、なかなか踏み切れない…」
そんな悩みをお持ちのあなたへ。
2025年は、補助金を活用して設備投資を加速させる絶好のチャンスです!
1.2025年の補助金はどうなる? 最新情報をキャッチ!
2025年の補助金制度は、大きく以下の5つのポイントを押さえておきましょう。
① 大規模成長投資補助金は2025年も続行!
最低投資額10億円、最大補助上限50億円(補助率1/3)の超大型補助金が来年も出ます! 2027年末までに終える大規模投資を考えている場合は、ぜひご検討ください。
② 中小企業成長加速化補助金の新設!※詳しくは下へスクロール
売上高100億円を目指す企業に向けた設備投資への補助金が新設される見込みです。 大規模成長補助金(最低投資額10億円)は大きすぎて使いづらかったという会社様は要チェックです。
③ 「事業再構築補助金」は「新事業進出補助金(仮称)」へ進化!
事業再構築補助金は、約1500億円残っていた基金を流用する形で新たな補助金へと生まれ変わるようです。 対象事業や補助金額等、これまで事業再構築補助金を使ってしまった、自社では使い勝手が悪かったという会社様も動向を注視していく必要があります。
④ ものづくり補助金は継続も、上限・枠・要件の見直しへ
「最低賃金近傍の事業者に対する支援拡充」と記載があるように、賃上げの流れは来年もさらに加速していくと考えられます。 補助金をうまく活用して、人件費の上昇を上回る成長を遂げていきましょう!
⑤ 省エネやGX系の補助金も過去最高予算
省エネ関係は引き続き出ます!古くなったエアコンや生産設備の入れ替えなどでも使えますので、積極的に活用していきましょう。
2.中小企業必見!「中小企業成長加速化補助金」とは?
中小企業の皆様には、「中小企業成長加速化補助金」がおすすめです。
これは、売上高100億円への飛躍的成長を目指す中小企業を対象とした補助金で、最大5億円(補助率1/2)の補助を受けることができます。
「中小企業成長加速化補助金」の概要
補助対象者:売上高100億円への飛躍的成長を目指す中小企業
補助上限額:5億円(補助率1/2)
補助事業実施期間:交付決定日から24か月以内
補助事業の要件:投資額1億円以上(専門家経費・外注費を除く補助対象経費分)「売上高100億円を目指す宣言」を行っていることその他、賃上げ要件 など
補助対象経費:建物費、機械装置等費、ソフトウェア費、外注費、専門家経費
「売上高100億円を目指す宣言」とは、中小企業が「売上高100億円を超える企業になる」という目標と、そのためのビジョンや取り組みを宣言し、ポータルサイト上で公表するものです。
この宣言を行うことで、以下のメリットがあります。
「宣言」マークの活用による自社PR:「宣言」を行った企業だけ「ロゴマーク」を使用できます。
経営者ネットワークへの参加:地域・業種を超えた経営者ネットワークに参加し、交流や情報交換ができます。
「宣言」取得による補助金等の活用:上記で紹介した「中小企業成長加速化補助金」を含む、様々な補助金の申請が可能になります。
補助金の獲得にはポイントをおさえることが非常に重要です。
なぜなら、補助金の審査をする審査員はこの「ポイント」を重点的に見ているからです。
逆に言うと、いくら素晴らしい投資計画や事業計画を立てても「ポイント」を外してしまうと補助金の採択からは遠ざかってしまいます。
ここからは補助金獲得のポイントと昨年2024年の補助金獲得事例をみていきましょう。
3.補助金獲得のポイントとは? 2024年大型補助金の獲得事例を紹介
「補助金って、申請が難しそう…」 「うちの会社に採択されるか不安…」
そう思われるかもしれません。
確かに、補助金を獲得するためには、事業計画の内容や実現可能性、将来的な成長性などをしっかりとアピールする必要があります。
しかし、ご安心ください。
適切な準備と戦略があれば、多額の補助金を獲得し、大規模な設備投資を実現できる可能性があります。
例えば、2024年には、
鉄骨加工工場新設で約7億円
食品加工工場新設で約41億円
電気部品加工工場新設で約29億円
といった、大型補助金の活用事例が出ています。
4.補助金採択の確立を上げる方法
2月25日(火)、26日(水)、28日(金)に開催される
「【2025年最新】工場新設・設備投資!製造業の補助金セミナー」
では、補助金獲得の秘訣を、わかりやすく解説いたします。
セミナーで得られるもの
2025年最新の補助金制度の情報
採択されるためポイント
工場新設・設備投資の成功事例
DX、自動化、省人化、IoT化など、生産性向上のためのノウハウ
工場新設や設備投資における事業計画・建築計画・設備計画の方法
さらに!
オンライン形式で、PCがあればどこでも受講可能!
視覚的にわかりやすい資料で、理解を深めます!
【参加者限定】セミナー後の個別相談でさらに詳細な情報をGET!
行動を起こすなら今!
補助金には限りがあり、申請が遅れるとチャンスを逃してしまう可能性があります。
準備を今すぐ始めましょう!
皆様のご参加を心よりお待ちしております。
■関連するセミナーのご案内
https://www.funaisoken.co.jp/seminar/124103
【2025年最新】工場新設・設備投資!製造業の補助金セミナー
最大50億円の補助金を活用して工場新設や設備投資する具体的な手法と成功事例
2025年 工場新設・設備投資に使える!補助金活用講座
補助金動向講座「2025年最新版!製造業が使える補助金情報と採択のポイント」
2025年 製造業が使える補助金最新情報!
最大50億円!補助金活用のポイントを解説
製造業が押さえておくべき補助金活用時の考え方
最新補助金情報の超有力な獲得手法!
AI外観検査導入を検討されている方は、ぜひこの機会にセミナーにご参加ください。
お申し込みはこちら
https://www.funaisoken.co.jp/dl-contents/jy-robot_S045
【製造業 ロボット活用・自動化】時流予測レポート2025
工場の自動化・ロボット導入を成功させるための秘訣を凝縮!
本レポートでは、工場の自動化・ロボット活用の現状と将来展望、そして具体的な導入プロセスについて解説しています。
特に、2025年に向けて、製造業が実践すべき工場自動化戦略として、4つのSTEPで進めるロボット活用と、効果最大化のための製品・作業分析を紹介しています。
また、スムーズな工場のロボット導入を実現するための具体的な取組みとして、ROIを考慮した導入計画の重要性を解説し、段階的な導入によるリスク抑制と効果最大化について解説しています。
さらに、具体的な事例を挙げながら、各社の工場自動化・ロボット活用状況や成果を紹介し、読者の皆様にロボット導入のイメージを掴んでいただけるよう工夫しています。
お申し込みはこちら