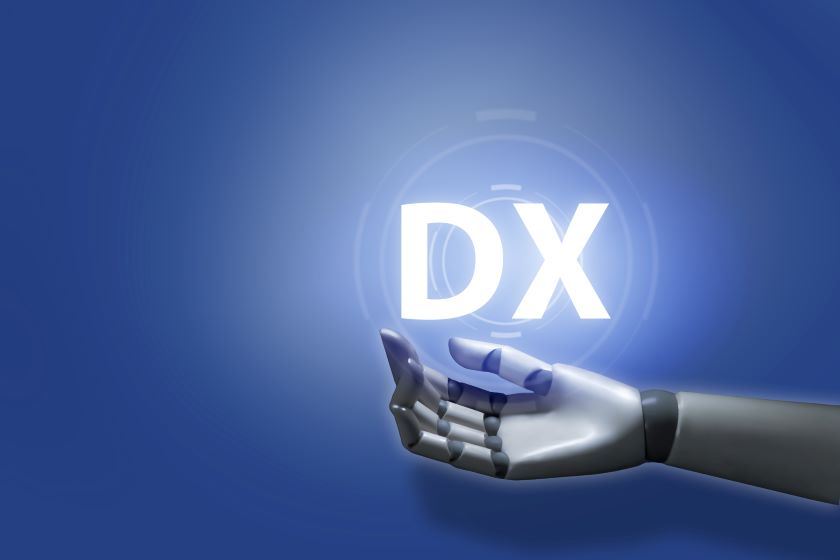
ロボットシステムインテグレーターが確度の高い新規案件を獲得する手法
2025.01.08
1. ロボットシステムインテグレーターの新規案件獲得における現状
近年、製造業をはじめとした様々な業界で人手不足が深刻化しており、その解決策としてロボットシステムの導入が注目されています。ロボットシステムの導入は、生産性向上や品質安定、労働環境改善などの効果が期待できる一方で、導入には専門的な知識や技術が必要となります。そのため、ロボットシステムの設計・構築から導入、運用・保守までを一括して請け負う「ロボットシステムインテグレーター(ロボットSIer)」の役割が重要となっています。
しかし、ロボットSIer業界は、いくつかの課題を抱えています。
SIer間の格差の拡大: ロボットSIerは増加傾向にあり、顧客の獲得競争が激化しています。しかし、その一方で、一部のSIerに仕事が集中し、忙しい企業と暇な企業の格差が広がっているのが現状です。これは、大企業や実績のあるSIerに顧客が集中しやすいためです。
提案依頼から受注までの低い確率: ユーザーからの提案依頼が来た際に、概要構想の作成や見積もり作成をしても受注に至る確率は必ずしも高くありません。多くの場合、複数社から提案を受け、比較検討されるため、価格や技術力だけでなく、提案内容や対応力など、総合的な評価で判断されます。そのため、概要構想作成から見積もり提出までのフェーズがネック工程となり、生産性低下の原因となっています。
Webマーケティングの難しさ: 一部のSIerは積極的なWebマーケティングを行っていますが、キーエンスのような企業出身のマーケターが担っているケースが多く、高度なノウハウを必要とします。他のSIerがWebマーケティングでロボットシステムインテグレーターとしての新規案件を獲得するには、ニッチなテーマなどに注力する必要がありますが、そのようなニッチなテーマでは、多くの新規案件を獲得するのは難しいのが現状です。
顧客のニーズが多様化・複雑化している中で、顧客の課題を的確に捉え、最適なシステムを提案することが求められています。
2. ロボットシステムインテグレーターが求められる提案内容
ロボットSIerは、単にロボットを販売するのではなく、顧客の課題を解決するためのコンサルティングを行う必要があります。そのため、顧客の業務内容や課題を深く理解し、最適なロボットシステムを提案することが重要となります。
近年では、特にコンサルティング営業が求められています。これは、顧客のニーズを丁寧にヒアリングし、現状の課題や将来的な展望を踏まえた上で、最適なロボットシステムを提案する営業手法です。
コンサルティング営業を行う上で、以下の様な提案内容が求められます。
顧客のニーズに合わせたロボットシステムの設計・構築: 顧客の業務内容や課題を深く理解し、最適なロボットを選定し、周辺機器やシステムとの連携を含めた設計・構築を行います。・単にロボットを導入するだけでなく、作業効率や安全性、運用コストなどを考慮した提案が重要です。・顧客の要望をヒアリングするだけでなく、現場の状況を把握し、潜在的な課題を抽出する能力も必要となります。
既存システムとの連携を考慮したシステム提案: 多くの場合、ロボットシステムは既存の生産ラインやシステムと連携して稼働する必要があります。・既存システムとの互換性やデータ連携などを考慮し、スムーズな導入と運用を実現する提案が求められます。
ロボット導入による効果の明確化(ROIの提示など): ロボットシステム導入による費用対効果を明確に示すことが重要です。導入コストだけでなく、人件費削減、生産性向上、品質向上など、具体的な効果を数値化し、投資対効果(ROI)を算出することで、顧客の投資判断を支援します。
顧客にあった補助金の活用も情報提供: ロボットシステム導入には、国や地方自治体による補助金制度が利用できる場合があります。・顧客の状況に合わせて、適切な補助金制度の情報を提供することで、導入コストの削減を支援します。
上記のような提案を行うためには、ロボット技術に関する専門知識だけでなく、幅広い知識やスキルが必要となります。既存のロボットシステムインテグレーターの人材では、これらのすべてを持ち合わせていることは非常に少ないのが現状です。そのため、必要に応じて、外部のコンサルタントや専門家などのリソースを活用することも重要です。
3. 確度の高い新規案件を獲得する手法
では、ロボットSIerはどのようにして新規案件を獲得すれば良いのでしょうか。確度の高い新規案件を獲得するための手法をいくつかご紹介します。が、これらは一般的に考えられる内容であり、すでに取り組みをされているロボットSIerが多いでしょう。
3-1. 専門性を高め、差別化を図る
ロボットSIerは増加傾向にあり、競争が激化しています。そのため、他のSIerとの差別化を図ることが重要です。 特定の業界や工程に特化したり、独自の技術やノウハウを開発したりすることで、専門性を高め、顧客に選ばれるSIerを目指しましょう。
3-2. WebサイトやSNSを活用した情報発信
WebサイトやSNSを活用し、自社の強みや実績を発信することで、顧客にアプローチする手法です。 Webサイトでは、導入事例や実績、保有技術などを掲載し、自社の強みをアピールします。また、SNSでは、最新の技術情報や業界動向などを発信することで、顧客との接点を増やし、見込み顧客を獲得することができます。
3-3. 顧客との関係構築を重視する
既存顧客との関係を強化することで、紹介やリピート受注に繋げることが重要です。顧客満足度を高めるためには、導入後のサポート体制を充実させたり、定期的な訪問や連絡を行うなど、継続的な関係構築を心掛けましょう。
3-4. 展示会やセミナーへの積極的な参加
展示会やセミナーに参加することで、新規顧客との接点を増やすことができます。 自社の技術やサービスをアピールすることで、見込み顧客を獲得することができます。また、他の企業との交流を通して、ビジネスチャンスを広げることも期待できます。
3-5. 提案資料の作成
顧客に提出する提案資料は、分かりやすく、説得力のある内容にする必要があります。 提案資料には、以下の内容を盛り込むようにしましょう。
顧客の課題に対する解決策
導入するロボットシステムの概要
導入による効果(ROIなど)
導入スケジュール
費用
会社概要
3-6. 営業担当者の育成
顧客との信頼関係を構築し、ニーズを的確に捉えることができる営業担当者を育成することが重要です。 ロボットシステムに関する専門知識やコミュニケーション能力を向上させるための研修などを実施することで、営業担当者のスキルアップを図りましょう。
以上が一般的な取り組むべき内容です。では、一般的ではなく、効果的な取り組みとはなんでしょうか?
ロボットSIerが抱える課題を解決する、専門家との協業
これまで見てきたように、ロボットSIerは、高度な専門知識やコンサルティング能力、多岐にわたる提案内容が求められると同時に、新規顧客の獲得、受注率の向上など、多くの課題を抱えています。
これらの課題を解決し、確度の高い新規案件を獲得するためには、船井総合研究所との協業が有効です。
船井総合研究所は、長年のコンサルティング実績を持つ、日本有数の経営コンサルティング会社です。特に、製造業や中小企業の支援に強みを持ち、ロボットシステム導入に関する豊富な知見とノウハウを有しています。
船井総合研究所のコンサルタントは、まさに前述した「ロボットシステムインテグレーターが求められる提案内容」を網羅しており、顧客の課題を的確に捉え、最適なロボットシステム導入を支援することができます。
具体的には、以下の様な協業が考えられます。
船井総研との協業セミナーの開催: 船井総合研究所が集客した顧客に対し、貴社と共同でセミナーを開催することで、見込み顧客へアプローチできます。船井総合研究所が集客する顧客は、ロボットシステム導入に高い関心を持つ企業が多いため、非常に確度の高い新規案件獲得に繋がります。
船井総研によるDX・補助金勉強会の開催: 貴社社員向けに、船井総合研究所のコンサルタントがDXや補助金に関する勉強会を実施いたします。ロボットシステム導入支援に必要な知識やノウハウを習得することで、提案力の強化、コンサルティング営業力の向上に繋がり、受注率向上に貢献します。
船井総合研究所との協業は、貴社の営業力強化、新規顧客獲得、そして事業成長に大きく貢献すると確信しております。
協業セミナー、DX・補助金勉強会に関するお問い合わせは、以下までご連絡ください。 1. ロボットシステムインテグレーターの新規案件獲得における現状
近年、製造業をはじめとした様々な業界で人手不足が深刻化しており、その解決策としてロボットシステムの導入が注目されています。ロボットシステムの導入は、生産性向上や品質安定、労働環境改善などの効果が期待できる一方で、導入には専門的な知識や技術が必要となります。そのため、ロボットシステムの設計・構築から導入、運用・保守までを一括して請け負う「ロボットシステムインテグレーター(ロボットSIer)」の役割が重要となっています。
しかし、ロボットSIer業界は、いくつかの課題を抱えています。
SIer間の格差の拡大: ロボットSIerは増加傾向にあり、顧客の獲得競争が激化しています。しかし、その一方で、一部のSIerに仕事が集中し、忙しい企業と暇な企業の格差が広がっているのが現状です。これは、大企業や実績のあるSIerに顧客が集中しやすいためです。
提案依頼から受注までの低い確率: ユーザーからの提案依頼が来た際に、概要構想の作成や見積もり作成をしても受注に至る確率は必ずしも高くありません。多くの場合、複数社から提案を受け、比較検討されるため、価格や技術力だけでなく、提案内容や対応力など、総合的な評価で判断されます。そのため、概要構想作成から見積もり提出までのフェーズがネック工程となり、生産性低下の原因となっています。
Webマーケティングの難しさ: 一部のSIerは積極的なWebマーケティングを行っていますが、キーエンスのような企業出身のマーケターが担っているケースが多く、高度なノウハウを必要とします。他のSIerがWebマーケティングでロボットシステムインテグレーターとしての新規案件を獲得するには、ニッチなテーマなどに注力する必要がありますが、そのようなニッチなテーマでは、多くの新規案件を獲得するのは難しいのが現状です。
顧客のニーズが多様化・複雑化している中で、顧客の課題を的確に捉え、最適なシステムを提案することが求められています。
2. ロボットシステムインテグレーターが求められる提案内容
ロボットSIerは、単にロボットを販売するのではなく、顧客の課題を解決するためのコンサルティングを行う必要があります。そのため、顧客の業務内容や課題を深く理解し、最適なロボットシステムを提案することが重要となります。
近年では、特にコンサルティング営業が求められています。これは、顧客のニーズを丁寧にヒアリングし、現状の課題や将来的な展望を踏まえた上で、最適なロボットシステムを提案する営業手法です。
コンサルティング営業を行う上で、以下の様な提案内容が求められます。
顧客のニーズに合わせたロボットシステムの設計・構築: 顧客の業務内容や課題を深く理解し、最適なロボットを選定し、周辺機器やシステムとの連携を含めた設計・構築を行います。・単にロボットを導入するだけでなく、作業効率や安全性、運用コストなどを考慮した提案が重要です。・顧客の要望をヒアリングするだけでなく、現場の状況を把握し、潜在的な課題を抽出する能力も必要となります。
既存システムとの連携を考慮したシステム提案: 多くの場合、ロボットシステムは既存の生産ラインやシステムと連携して稼働する必要があります。・既存システムとの互換性やデータ連携などを考慮し、スムーズな導入と運用を実現する提案が求められます。
ロボット導入による効果の明確化(ROIの提示など): ロボットシステム導入による費用対効果を明確に示すことが重要です。導入コストだけでなく、人件費削減、生産性向上、品質向上など、具体的な効果を数値化し、投資対効果(ROI)を算出することで、顧客の投資判断を支援します。
顧客にあった補助金の活用も情報提供: ロボットシステム導入には、国や地方自治体による補助金制度が利用できる場合があります。・顧客の状況に合わせて、適切な補助金制度の情報を提供することで、導入コストの削減を支援します。
上記のような提案を行うためには、ロボット技術に関する専門知識だけでなく、幅広い知識やスキルが必要となります。既存のロボットシステムインテグレーターの人材では、これらのすべてを持ち合わせていることは非常に少ないのが現状です。そのため、必要に応じて、外部のコンサルタントや専門家などのリソースを活用することも重要です。
3. 確度の高い新規案件を獲得する手法
では、ロボットSIerはどのようにして新規案件を獲得すれば良いのでしょうか。確度の高い新規案件を獲得するための手法をいくつかご紹介します。が、これらは一般的に考えられる内容であり、すでに取り組みをされているロボットSIerが多いでしょう。
3-1. 専門性を高め、差別化を図る
ロボットSIerは増加傾向にあり、競争が激化しています。そのため、他のSIerとの差別化を図ることが重要です。 特定の業界や工程に特化したり、独自の技術やノウハウを開発したりすることで、専門性を高め、顧客に選ばれるSIerを目指しましょう。
3-2. WebサイトやSNSを活用した情報発信
WebサイトやSNSを活用し、自社の強みや実績を発信することで、顧客にアプローチする手法です。 Webサイトでは、導入事例や実績、保有技術などを掲載し、自社の強みをアピールします。また、SNSでは、最新の技術情報や業界動向などを発信することで、顧客との接点を増やし、見込み顧客を獲得することができます。
3-3. 顧客との関係構築を重視する
既存顧客との関係を強化することで、紹介やリピート受注に繋げることが重要です。顧客満足度を高めるためには、導入後のサポート体制を充実させたり、定期的な訪問や連絡を行うなど、継続的な関係構築を心掛けましょう。
3-4. 展示会やセミナーへの積極的な参加
展示会やセミナーに参加することで、新規顧客との接点を増やすことができます。 自社の技術やサービスをアピールすることで、見込み顧客を獲得することができます。また、他の企業との交流を通して、ビジネスチャンスを広げることも期待できます。
3-5. 提案資料の作成
顧客に提出する提案資料は、分かりやすく、説得力のある内容にする必要があります。 提案資料には、以下の内容を盛り込むようにしましょう。
顧客の課題に対する解決策
導入するロボットシステムの概要
導入による効果(ROIなど)
導入スケジュール
費用
会社概要
3-6. 営業担当者の育成
顧客との信頼関係を構築し、ニーズを的確に捉えることができる営業担当者を育成することが重要です。 ロボットシステムに関する専門知識やコミュニケーション能力を向上させるための研修などを実施することで、営業担当者のスキルアップを図りましょう。
以上が一般的な取り組むべき内容です。では、一般的ではなく、効果的な取り組みとはなんでしょうか?
ロボットSIerが抱える課題を解決する、専門家との協業
これまで見てきたように、ロボットSIerは、高度な専門知識やコンサルティング能力、多岐にわたる提案内容が求められると同時に、新規顧客の獲得、受注率の向上など、多くの課題を抱えています。
これらの課題を解決し、確度の高い新規案件を獲得するためには、船井総合研究所との協業が有効です。
船井総合研究所は、長年のコンサルティング実績を持つ、日本有数の経営コンサルティング会社です。特に、製造業や中小企業の支援に強みを持ち、ロボットシステム導入に関する豊富な知見とノウハウを有しています。
船井総合研究所のコンサルタントは、まさに前述した「ロボットシステムインテグレーターが求められる提案内容」を網羅しており、顧客の課題を的確に捉え、最適なロボットシステム導入を支援することができます。
具体的には、以下の様な協業が考えられます。
船井総研との協業セミナーの開催: 船井総合研究所が集客した顧客に対し、貴社と共同でセミナーを開催することで、見込み顧客へアプローチできます。船井総合研究所が集客する顧客は、ロボットシステム導入に高い関心を持つ企業が多いため、非常に確度の高い新規案件獲得に繋がります。
船井総研によるDX・補助金勉強会の開催: 貴社社員向けに、船井総合研究所のコンサルタントがDXや補助金に関する勉強会を実施いたします。ロボットシステム導入支援に必要な知識やノウハウを習得することで、提案力の強化、コンサルティング営業力の向上に繋がり、受注率向上に貢献します。
船井総合研究所との協業は、貴社の営業力強化、新規顧客獲得、そして事業成長に大きく貢献すると確信しております。
協業セミナー、DX・補助金勉強会に関するお問い合わせは、以下までご連絡ください。