記事公開日:2020.07.14
最終更新日:2023.01.20
AI搭載ロボットコントローラーによるロボット制御の事例と解説
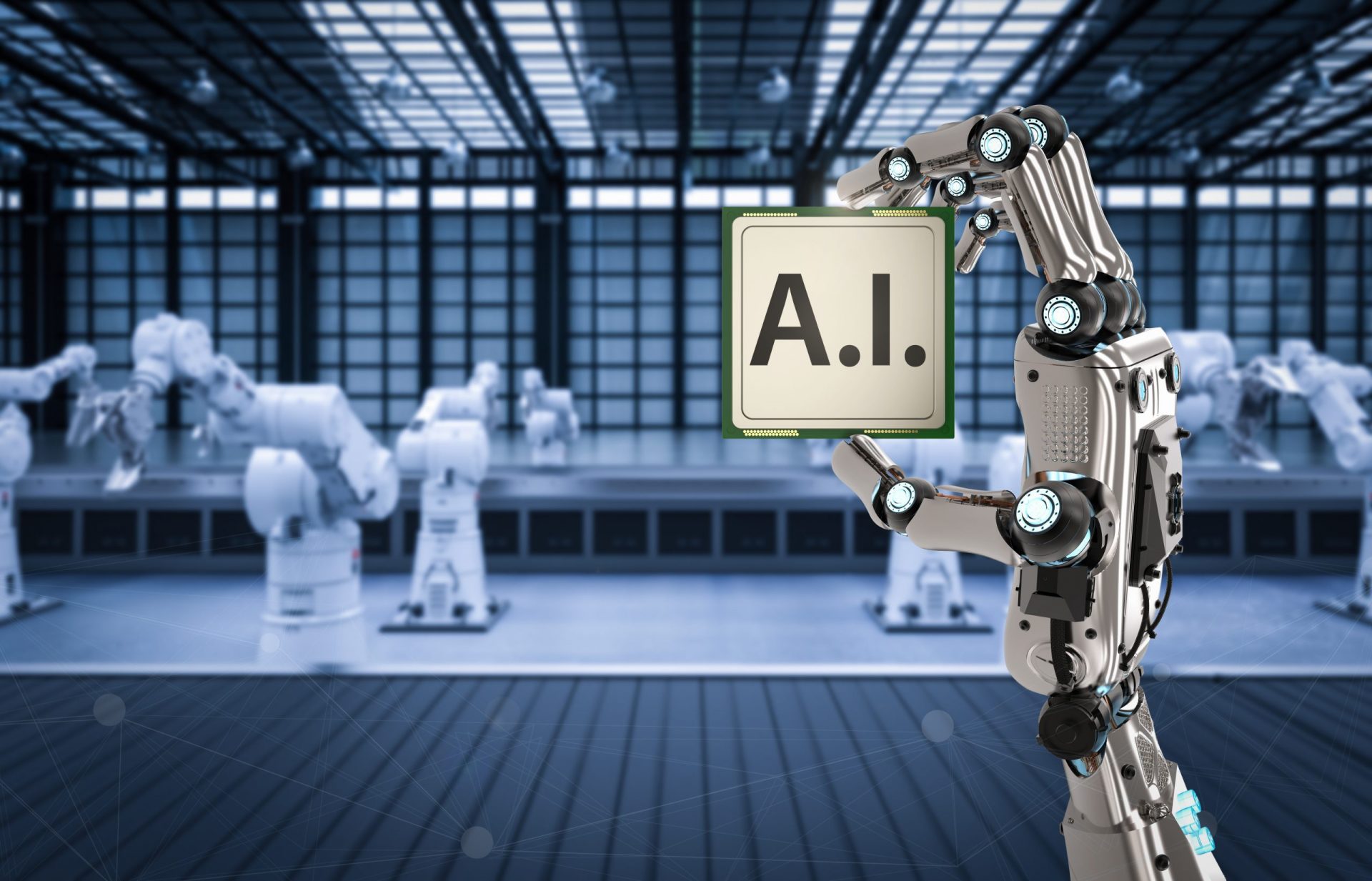
近年、AIを搭載したロボットコントローラーの需要が高まっています。
今回はその「AI搭載ロボットコントローラー」について事例を交えて解説します。
1.ロボットティーチングの現状と課題
ロボットを動かすために必要な作業が「ティーチング」です。
ティーチング作業は非常に複雑、かつ専門知識を要する作業であり、専門のロボットプログラマーが行うのが一般的です。
ロボットを動かすにはペンダント(操作パネル)を使います。
このペンダントでティーチングの修正や動作確認を行っていくのですが、一般的に使用されているペンダントの画面はプログラムが羅列された文字だらけの画面であり非常に複雑です。
このプログラム画面からロボットの動きを想像するのは容易ではありません。そのため工場の現場レベルでティーチングを行うことはほぼ不可能なのが現状となっています。
2.AI搭載ロボットコントローラーによる制御とは
そのような背景で近年注目されているのが「AI搭載ロボットコントローラー」です。
通常のロボットコントローラーと比較すると、大きく3つのメリットがあります。
①ティーチング作業が簡単
②生産性向上
③操作性、メンテナンス性の向上
まず、一番のメリットはティーチング作業が圧倒的に簡単であることです。ワークのピンキング位置、ワークの置き位置、を指定するだけで後はAIが自動で判断してロボットの軌跡を生成します。
この時、あらかじめ登録した障害物との干渉を回避しつつ最適な動きをAIが自動で生成してくれます。
次に生産性向上です。
従来のティーチング作業では人間のような滑らかな動きをロボットで表現することは困難でした。
しかし、AI搭載ロボットコントローラーでは先にも記載した通り、AIが最適な動きを自動で生成します。
それにより、従来のような何点ものティーチングポイントを経由する動きと比べるとサイクルタイムが大幅に改善されます。
最後に、メンテナンス性・操作性の向上です。
通常のコントローラーではロボットメーカーごとにコントローラーが異なるため違うメーカーのロボットを導入する度に新しい操作方法を覚える必要がありました。
近年開発されているAI搭載ロボットコントローラーの中には、メーカーを選ばずどんなメーカーのロボットも直接制御できる物もあります。
それにより、操作も覚えやすく、メンテナンス方法も統一されるので操作ミスによるトラブルや「チョコ停」時の復旧時間短縮にも繋がり、結果として生産性も向上します。
3.事例と解説
では、具体的にどのような場面において導入されているのでしょうか。
事例を交えて解説していきます。
・事例①自動車部品バラ積みピッキング
コンテナのような深い箱に無作為に投入されているシャフトやギヤのようなワークを3Dビジョンシステムと組み合わせてピッキングし次工程(例えばバリ取り装置など)にワークセットするシステムが実装されています。この場合における圧倒的なメリットはやはり「バラ積みピッキング」が可能となったことです。
本来であればピッキングするワークは治具等を用いて綺麗に整列して並べて置く必要がありました。
3DビジョンとAIを組み合わせることで、箱の中にある様々なワークの姿勢を判断し、最適な掴み位置を自動で判断してピッキングします。
さらに、箱の底付近のワークをピッキングする際にはロボットと箱の干渉が懸念されますが、それも干渉の無い姿勢をAIが判断して最適な姿勢と軌跡で動きます。ピッキング後の動作もまるで人間が物を手で運ぶようにスムーズな動きを実現し、従来のティーチングによる動きと比べるとサイクルタイムが大幅に減少しています。
人間が行う場合と変わらないスピードで(むしろ、より速く)ロボットが無人で作業を続ける、これを2台、3台と展開していくことにより3名で作業していた工程が2名に、2名で作業していた工程が1名に、1名が付きっ切りだった工程が無人に、と工場の省人化が進んでいきます。
事例②物流倉庫における多品種ケースの荷下ろし作業
物流倉庫において、毎日大量に納品される商品をパレットから仕分け用のコンベアに載せ替える作業があり、これまでは全て手作業で行ってきました。しかし、高さのある積み荷や、時には20kg近いケースもあり作業員の負担となっていました。
この場合においてロボット化の問題となるのが、ランダムにケースが積まれている場合です。
従来のロボットコントローラーではランダムに積まれているケースをロボットで取ろうとした場合には、一つ一つ品種登録し、様々なパターンをプログラムし、と膨大な時間と費用がかかってしまいます。
そのように工数をかけてもあらかじめ設定したパターン以外ではロボットは動けません。要するに現実的には実現不可能となります。
そこで採用されたのがAI搭載ロボットコントローラーと3Dビジョンシステムを組み合わせたデパレタイズ(荷下ろし)システムです。事例①と同様に、AIと3Dビジョンを組み合わせることでランダムに積み重ねられたケースの荷下ろしが可能となりました。
このように、作業員に負荷の高い作業をロボットに行わせ、手の空いた作業員にはより付加価値の高い作業にシフトしてもらうというのもロボット化の目指すべきところです。
4.まとめ
いかかがでしたでしょうか?
ロボット導入による省人化=従業員数を減らす、ではありません。
その空いた工数を、AI・ロボットの管理メンテナンス人員として育てる、新たなAI・ロボットシステムを作っていく未来ある人材(人財)として育てる。さらにそのような分野の採用を強化し会社を育てる。
中小製造業の目指すべきAI、ロボット導入の本質はそこにあるのかもしれません。
「AIとロボット、なんか難しそう、、」
「どうせ大手じゃなきゃ導入できないんでしょ、、」
「うちは中小で資金力が無いから、、」
そう思われた方もいらっしゃるかもしれません。が、そんなことはありません。
Withコロナ時代における企業の優位性を確保するため、優秀な人材(人財)を確保するため、最先端のAI搭載ロボットコントローラーの導入を検討してみてはいかがでしょうか?
ーーーーーーーーーーーーーーーーーーーーーーーーーーーーーーーーーー
自動化・ロボット化事例集 vol.2
本事例集は、全国の先進的な工場が取り組む「自動化・ロボット化」の事例をまとめたものとなります。
これから自動化・ロボット化に取組もうと考える皆さまに、
「工場にロボット・IoTを導入する」ための具体的なノウハウを、
事例を通して知っていただくことを目的に作成しました。
※こちらの事例集は、導入を検討している工場の担当者様限定となっております。
同業他社、メーカーや商社、SI事業者の方にはご送付をお断わりさせていただいております。
ーーーーーーーーーーーーーーーーーーーーーーーーーーーーーーーーーー
https://smart-factory.funaisoken.co.jp/download/automation-robotization-examples-02/
関連コラム
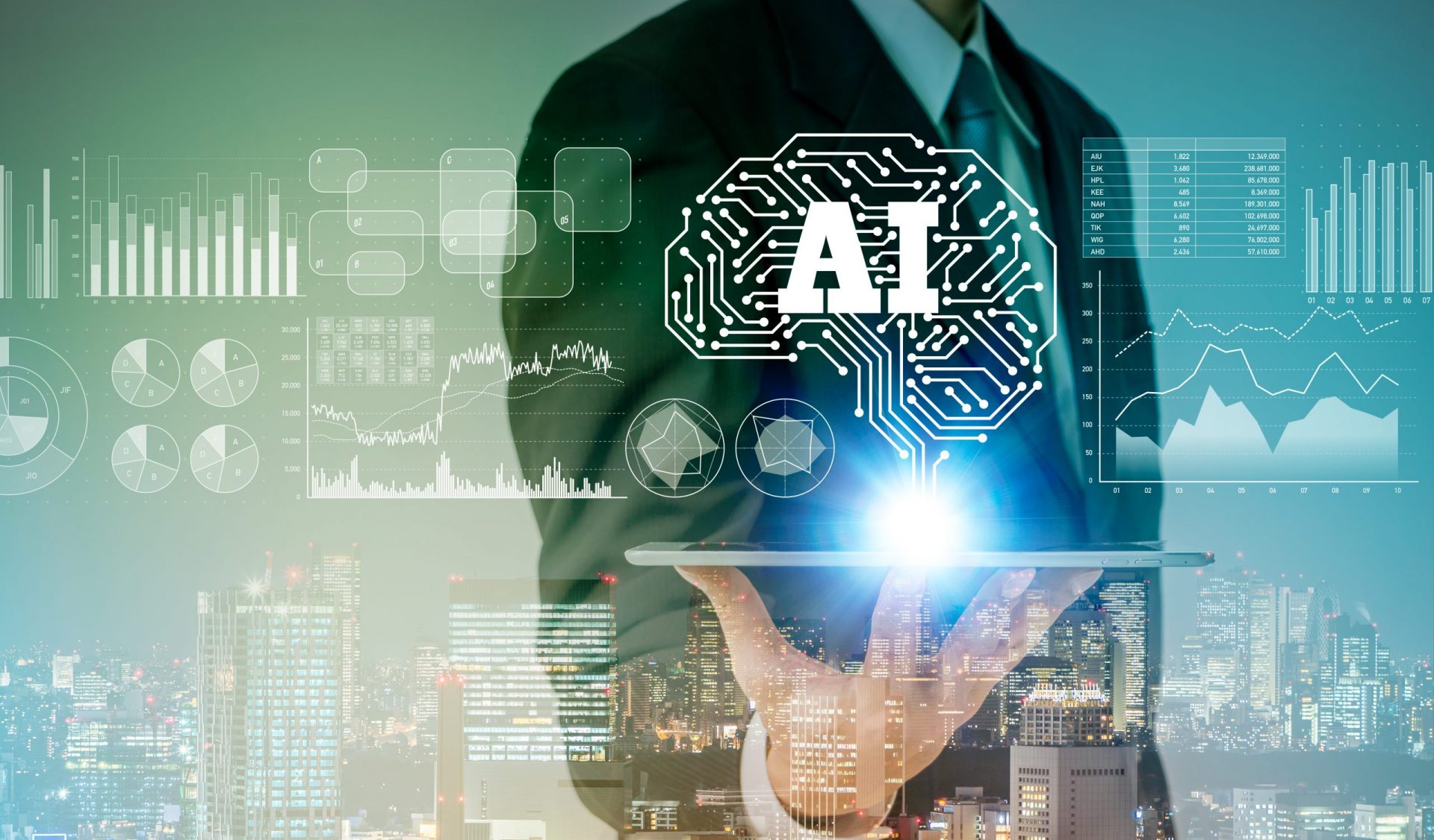
中堅・中小製造業におけるAI導入の目的とは?
2020.11.24
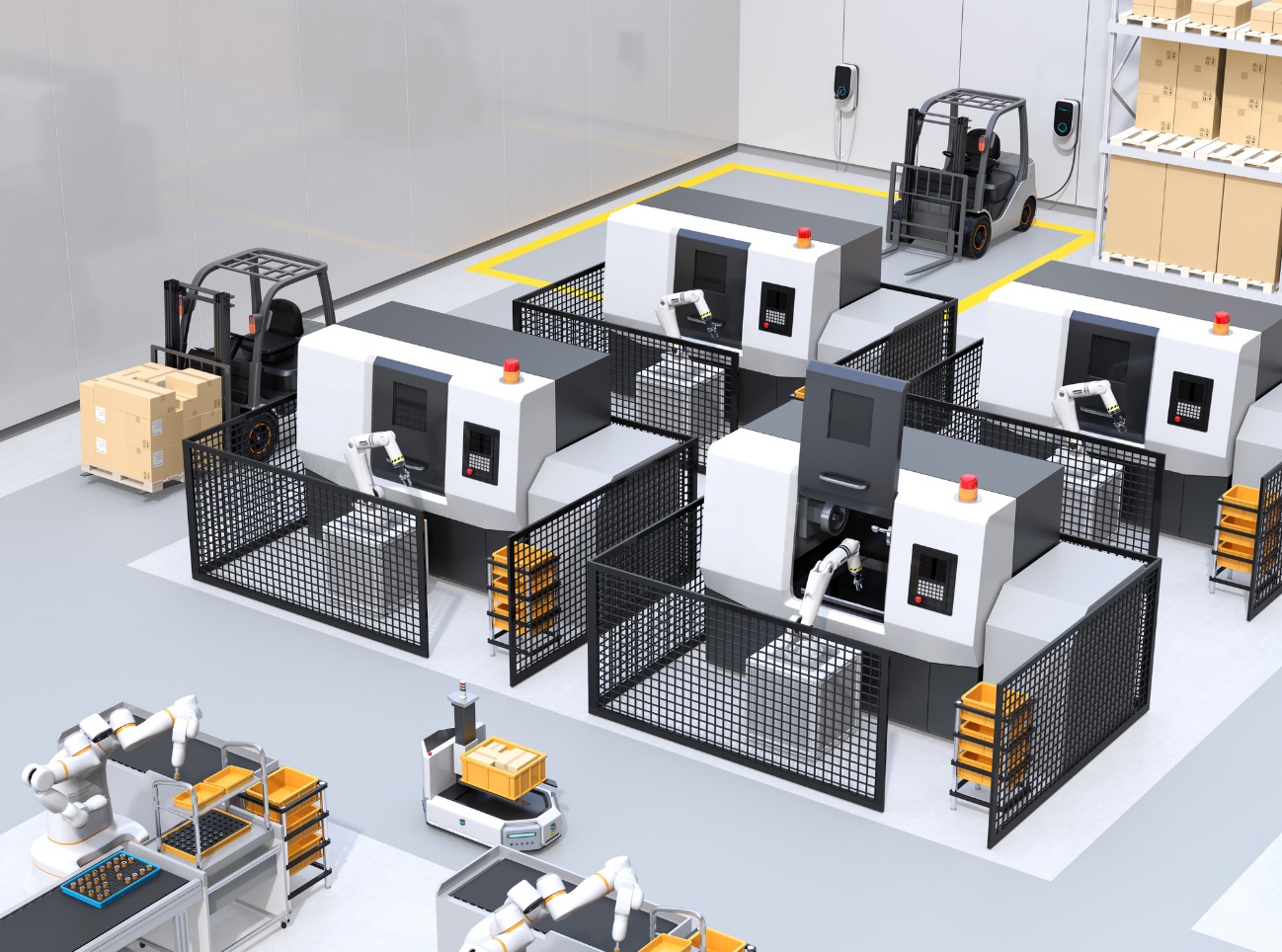
機械加工業における協働ロボットの活用方法
2021.07.19
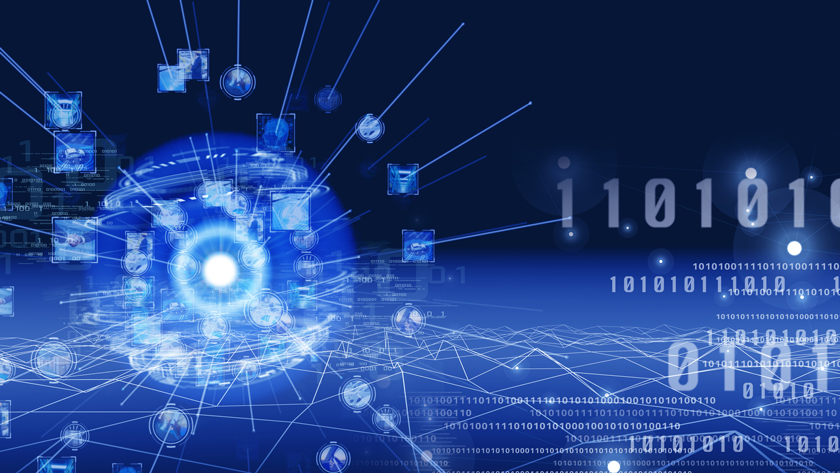
基幹系システムからAIサービスまで広がる「ノーコード/ローコード開発」
2022.02.15