記事公開日:2023.07.28
最終更新日:2024.06.04
製造業の原価改善3ステップとは?原価低減の方法を紹介!
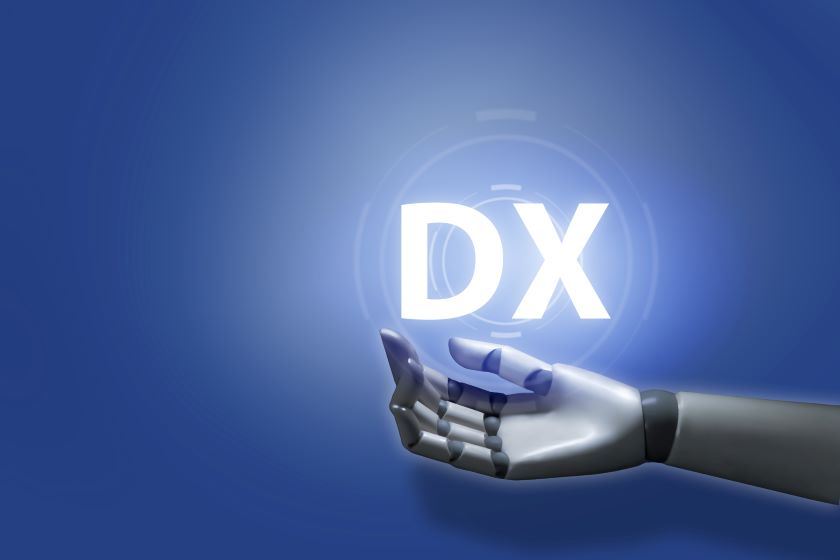
いつも当コラムをご愛読いただきありがとうございます。
原価管理は、適切に利益を上げていくために不可欠な要素の一つです。
近年では、さまざまな原価管理の手法・ツールがありますが、原価管理を行う際には、自社に適した手法や・ツールを選ぶことが重要です。
本記事では、原価管理の最適化“に関する基本的な考え方と、原価改善の 3 ステップを解説します。
1.「原価管理の最適化」に関する基本的な考え方
以下①~⑥は、「原価管理の最適化」に関する基本的な考え方です。
①現状、製品ごとに「市場価格」がある程度決まっており、原材料費高騰分の補うための価格転嫁も難しいため、製品の売価設定については、現場の要望が反映されにくい(売価を上げにくい)状況にある。
②そのため、利益確保のために自社でコントロールできるのは「原価低減」に関するアプローチ。
③「市場価格(売上)」は自社の力だけではコントロールできないが、「原価低減」なら自社の中でコントロール可能である。
④利益を生み出すための「原価低減」に不可欠なデータとして、製品別の原価が必要。
⑤製品別の原価が現状どうなっているかを知らなければ、目の前の仕事と原価の繋がりが見えてこないため、現場改善のしようがない。
⑥製品別の原価が常にオープンになっている状態を作ることで、初めて目の前の仕事と原価の繋がりが見えてくる。
上記①~⑥の考え方をもとに、今回は「原価管理の最適化」のうち、「加工原価の改善」に向けた実際の取り組みのステップをご紹介いたします。
大きくは以下3つのステップに分かれます。
2.「データをもとにした原価改善」の3ステップとは?
Step1)製品別×工程別工数データの“正確な”把握
上図は加工原価把握のためのフォーマット例です。
・縦軸に自社の製品名
・横軸に製品別の工程名(各工程名に段取り工数・加工工数・工賃が紐づく)
を並べています。
ここでのポイントは、各製品の工数について、「段取り時間」と「加工時間」を一纏めにして記録するのではなく、「段取り時間」と「加工時間」をそれぞれ分けて記録することです。
「段取り時間」と「加工時間」を一纏めにして記録してしまうと、後々の加工原価改善に向けた現場改善を実施するにあたって、「段取り工程」と「加工工程」のどちらに問題があるのかを正確に追及することが難しくなり、結果として加工原価の改善が進みません。
一方、「段取り時間」と「加工時間」をそれぞれ分けて記録することで、「段取り工程」と「加工工程」のどちらに問題があるのかを明確に分析することが可能となるため、結果として改善対象となる工程を具体的に突き止めることができます。
ところで、多くの中堅・中小製造業の企業様では、実行加工原価(実際の加工原価)を厳密には把握しきれていません。
「段取り時間」と「加工時間」をそれぞれ正確に分けて記録することが加工原価の改善に向けた最大のポイントですが、多くの中堅・中小製造業の企業様は、「段取り時間」と「加工時間」をそれぞれ正確に分けて記録することを手間に感じる製造現場側からの強い反発がネックとなり、このStep1でつまずきます。
「段取り時間」と「加工時間」をそれぞれ分けて記録することが、巡り巡って加工原価の改善と利益の確保へと繋がり、ひいては工場経営全体にインパクトを与える取り組みであることをいかに製造現場側に理解してもらうか。
この点、Step1をクリアするための最大のポイントとなります。
Step2)製品別の原価・利益データのリストアップ
上図は製品別の原価・利益データのリストアップ例です。
前述のStep1で記録した製品別の加工原価データや製品別の売価データ等を整理した上で、各製品を利益の高い順に並べた後に、
・上側にベスト10
・下側にワースト10
をピックアップしています。
このようにリスト化を進めていくことで、「なんとなく儲かっている」「なんとなく儲かっていない」といった“勘や経験”に依存することなく、実際のデータに基づいて次の現場改善策を打ち出すことが可能となります。
現場の実態に即したデータを活用することで、経営層・現場の工場長・現場作業者の間で共通の改善基準を持つことができます。
「もっと頑張れ」と精神論で改善活動を指示しても現場作業者はなかなか思うように動いてくれませんが、データをもとにした共通の改善基準が見えてくることで、現場作業者も納得感を持ってより精度の高い改善活動を行うことができます。
Step3)加工原価の改善に向けた対策の実行
前述のStep2で「製品別利益ベスト10&ワースト10」を把握することで、優先的にテコ入れが必要な製品が明らかになります。
テコ入れ対象の製品を絞り込んだ後に、
「その製品のどの工程がネックになっているか」
「段取りのしかたに問題があるのか」
「加工工程に問題があるのか」
「担当するヒトのスキルに問題があるのか」
等の観点から、データをもとに過去の現場の状況の振り返りを進めていくことで、その後の加工原価改善に向けて何から手を付けていけばよいかが整理されていきます。
このように、まずは“現場の事実・データ”をもとに現状を正しく把握し、分析を進めていくことで、より精度高くポイントを絞り込みながら改善活動を行うことが可能となります。
敢えて別な表現をするならば、「勘や経験に頼った経営」から「データをもとにした経営」へと会社の体質を変えていくことこそが、「工場の原価改善」の本質であると言っても過言ではないでしょう。
以上、「データをもとにした原価改善」の3ステップとは?
というテーマでお伝えさせていただきました。
【原価管理改善で収益UP】原価管理の方法と成功事例紹介レポート
個別原価を「見える化」で現場からの原価改善!!
最新事例解説レポート!
- 従業員30名金属加工業の原価改善事例!!
- 工程毎の作業時間を可視化する事で現場からの原価改善が促進
- 生産管理、原価管理システムを導入
- 手書き日報からリアルタイム日報に運用を改善
https://www.funaisoken.co.jp/dl-contents/smart-factory__00950
■関連するセミナーのご案内
「多品種少量生産機械加工業の為の原価改善!」 社長セミナー
生産管理&原価管理を徹底見直し!原価率削減!粗利改善!儲け改善!
セミナー詳細・申込はこちらから
https://www.funaisoken.co.jp/seminar/103833
■開催日程
全てオンライン開催となります
以下の日程よりご都合の良い日程をお選び下さい
※内容は全て一緒です
- 2023/10/04 (水) 13:00~15:00
- 2023/10/06 (金) 13:00~15:00
- 2023/10/11 (水) 13:00~15:00
お申し込みはこちらから⇒
https://www.funaisoken.co.jp/seminar/103833
関連コラム
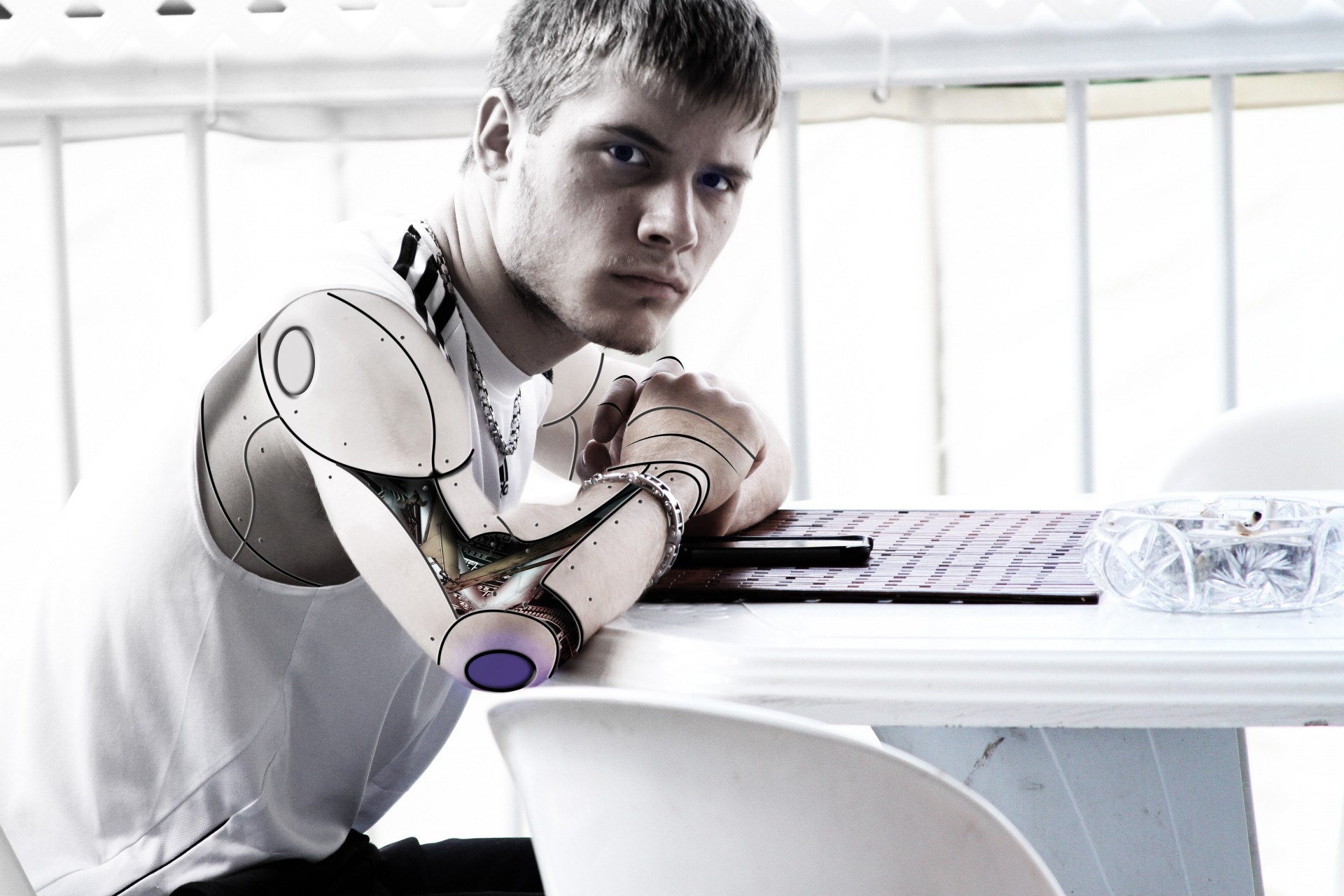
ロボットのティーチングとは?ティーチングの種類と概要を解説
2019.08.27
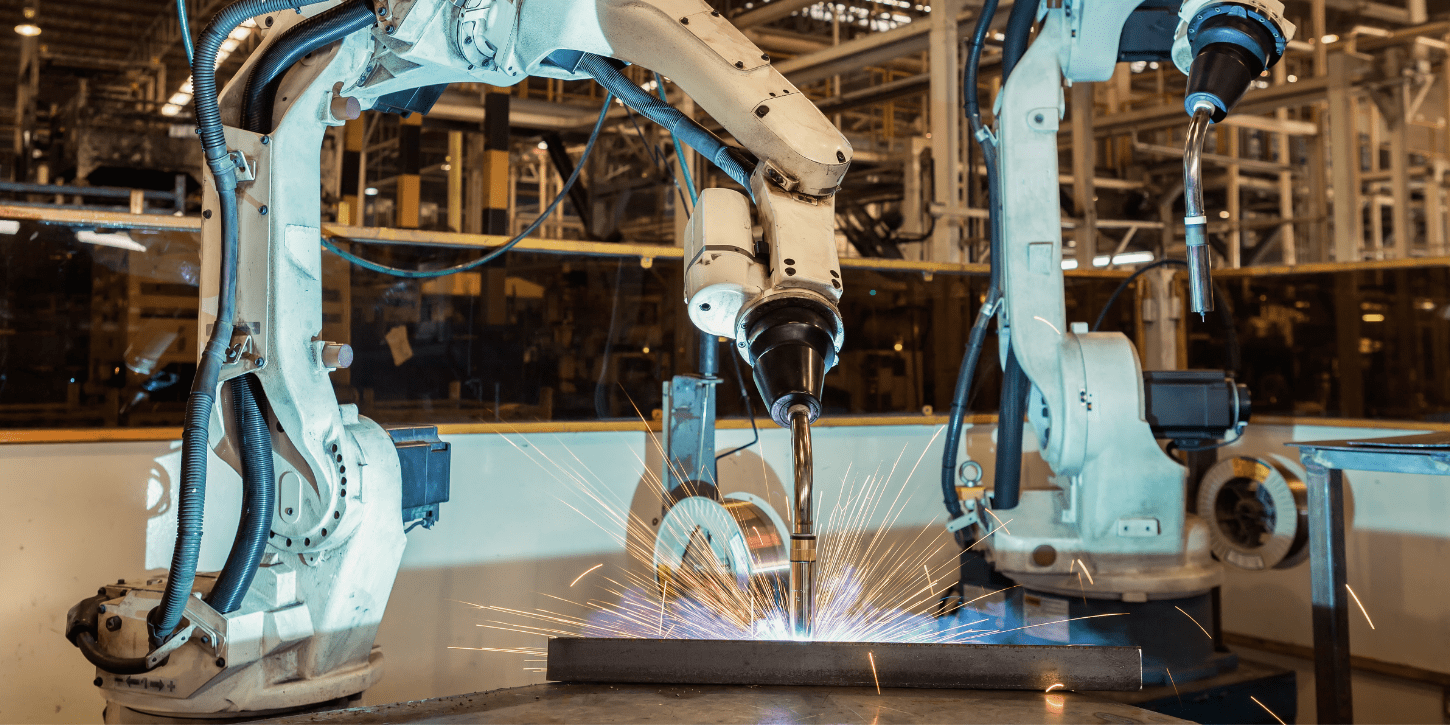
溶接ロボットで行う自動化の方法とは?
2019.08.29
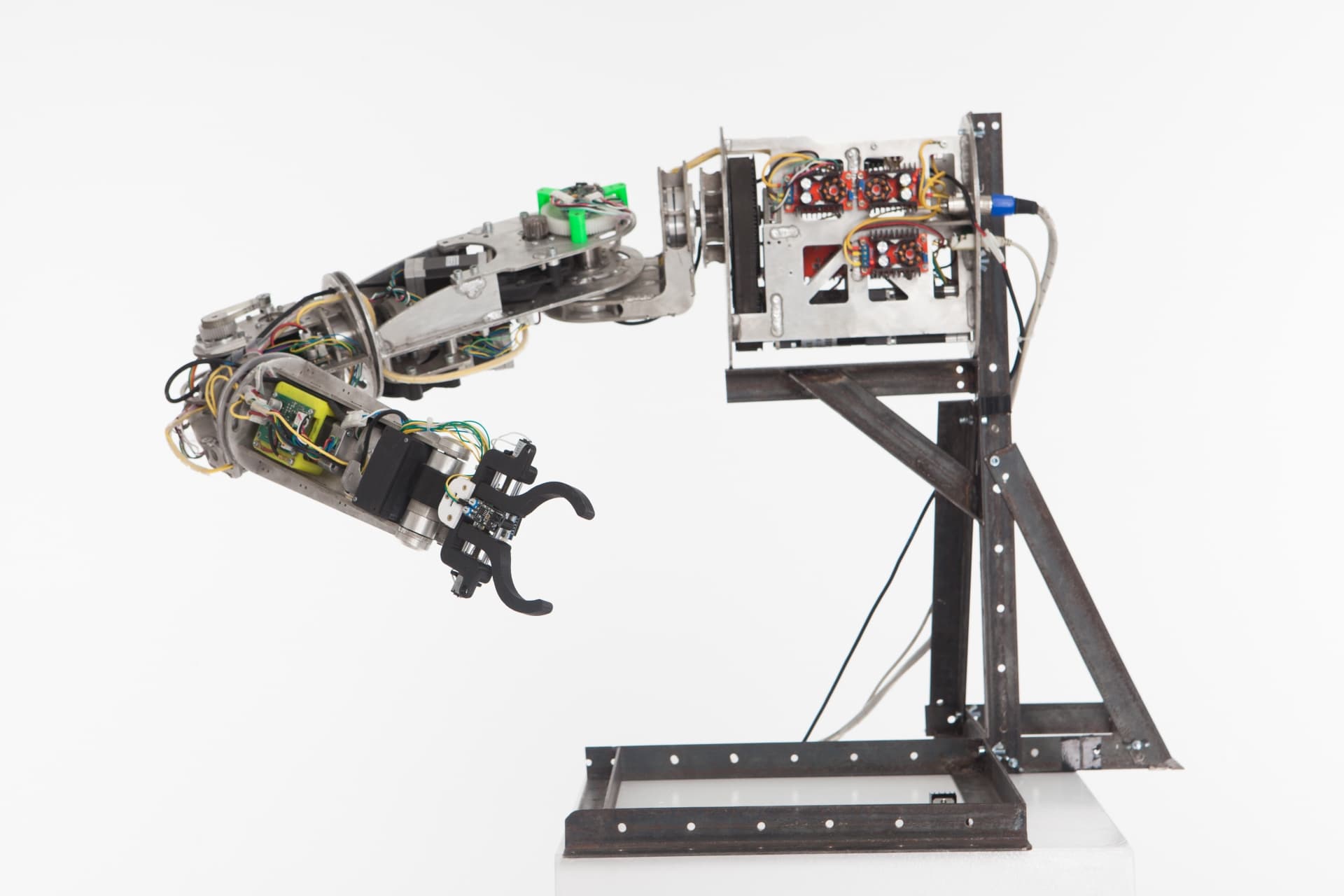
産業用ロボットとは?最新動向からロボットの違いを知る
2019.09.17