記事公開日:2024.07.22
最終更新日:2025.03.31
製造業DXとは?メリットや成功事例6選、成功のポイントを一挙解説!
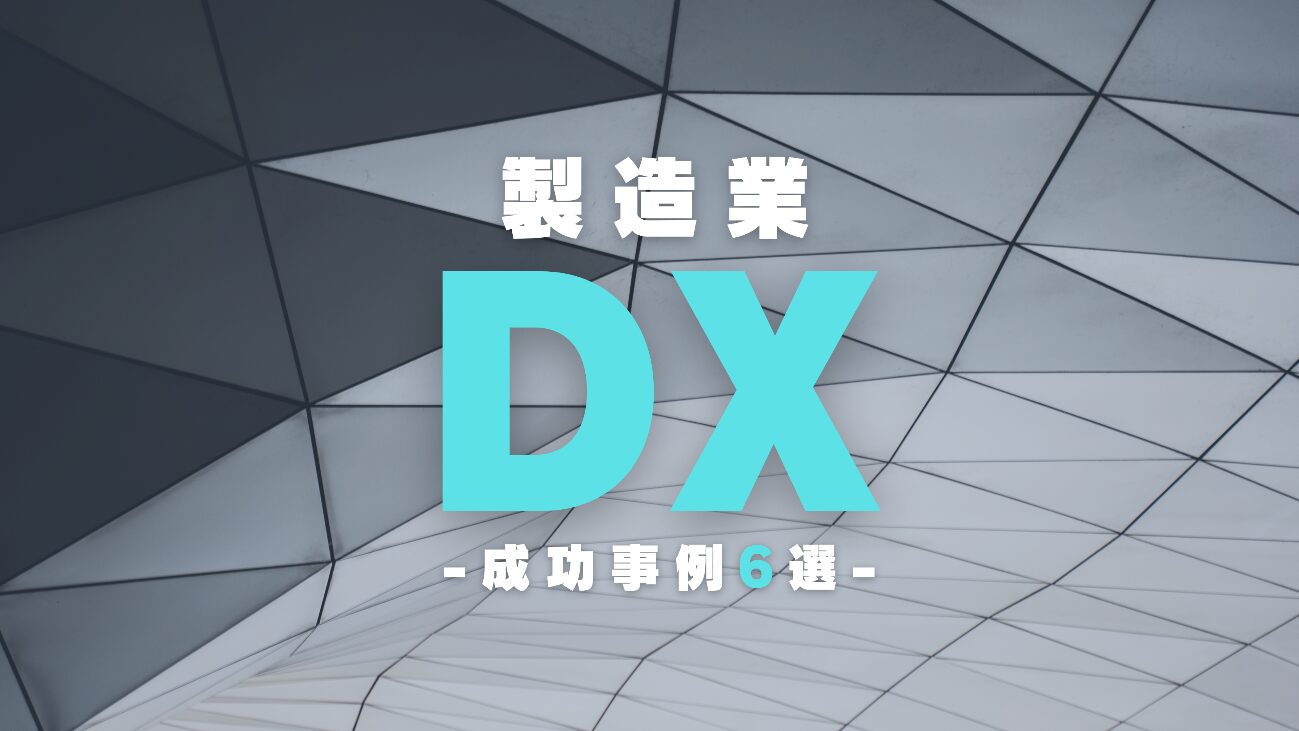
製造業を取り巻く環境は、かつてないスピードで変動しています。インターネットおよびデジタル化の波は、もはや無視できない潮流となり、企業の競争力を左右する重要な要素となっています。そんな中、注目を集めるのが「デジタルトランスフォーメーション(DX)」です。
「DXって、結局何をすればいいの?」
「うちの工場でも、本当に効果があるの?」
「コストばかりかかって、何も変わらないんじゃないか?」
そんな疑問や不安を抱えている方も多いのではないでしょうか。もちろん多大な労力が必要ですが、DXは決して遠い世界の出来事ではありません。日々の業務効率化から、可視化による品質向上、さらにはコミュニケーションの変革まで、その効果は多岐にわたります。
この記事では、DXの基礎から、実際の成功事例、そして導入時の課題と解決策まで、あなたの工場がDXを成功させるための羅針盤となる情報を提供します。他社の失敗事例も踏まえ、業務改善につなげられるようなノウハウもご紹介していきます。
1.製造業におけるDX
近年、製造業界でもデジタルトランスフォーメーション(DX)が注目されています。DXとは、具体的にどういったものを指すのでしょうか?
1-1.そもそもDXとは
そもそも、DXの定義はなんでしょうか?媒体によってさまざまな表現がなされていますが、「世界最先端デジタル国家創造宣言・官民データ活用推進基本計画」(2020年)には、以下のように示されています。
「Digital Transformation(デジタルトランスフォーメーション):
企業が外部エコシステム(顧客、市場)の劇的な変化に対応しつつ、内部エコシステム(組織、文化、従業員)の変革を牽引しながら、第3のプラットフォーム(クラウド、モビリティ、ビッグデータ/アナリティクス、ソーシャル技術)を利用して、新しい製品やサービス、新しいビジネスモデルを通して、ネットとリアルの両面での顧客エクスペリエンスの変革を図ることで価値を創出し、競争上の優位性を確立すること」
また、経済産業省の資料には、わかりやすく以下のように記載されています。
「そもそもDX(デジタルトランスフォーメーション)とは何か:
デジタル技術やツールを導入すること自体ではなく、データやデジタル技術を使って、顧客目線で新たな価値を創出していくこと。
また、そのためにビジネスモデルや企業文化等の変革に取り組むことが重要となる。」
これらをまとめると、DXとは、「ICTの技術を使って、顧客目線で新たな価値を創出し、競争上の優位性を確立すること」だと言えます。
全社横断的な変革を実現し、且つお客様に価値を提供して初めてDXを“実現できている”ということができます。DXは、デジタル技術を活用して事業モデルや業務プロセス、組織文化、従業員の意識をイノベーションすることが求められます。
よく言われることですが、単にITシステムを導入するだけではDXとはいえません。例えば、RFIDタグを活用して日報の手書き作業をなくしたとしても、DXとはいえません。状況が可視化され、生産性は上がりますが、業務プロセスのなかの部分的な業務効率化にとどまっているためです。この場合はDXではなくデジタイゼーション (アナログ・物理データのデジタルデータ化)といいます。
1-2.DXが必要とされる背景
インターネットおよびデジタル化の発展により、製造業においても経済成長のスピードについていくためにはDXは欠かせないものです。詳しく解説します。
◆デジタル化されていないと、すべてにおいて時間がかかり競争力が低下する
現代では、デジタル技術やデータを活用し、業務や判断がよりスピーディーに行われるようになってきており、年々そのスピードは上がっています。物事をKKD(勘、経験、度胸)に頼って判断していくことは、(判断は早い場合もありますが、)属人的でもあり、正確性にもかけてしまいます。データや事実に基づいた分析・改善をおこなっていくことで、よりムダのない、より成功確率の高い判断をしていくことが求められています。DXを実現できていない企業では、DXを実現してデータ活用をおこなっている企業と比較して、すべての面において大きな差が生まれ、競争力が低下するというのは明らかです。
◆新人・若手の確保が難しくなる
Paperlogic社の調査によると、2021年2月25日の段階で2021年の新卒社員の43.1%が、企業のDX推進具合を企業選考の基準としていたことが分かりました。DX推進具合を企業選考の基準とした理由としては「DXに限らず、今後必要になってくる事を積極的に取り入れる会社かどうか見極めるポイントになると考えたから」「社会情勢に応じて、柔軟な対応ができる企業に勤めたいと思っていたから」などが挙げられていました。より社会の変化に敏感になっている学生や若手社員にとって、DXへの姿勢は「この先やっていけるか」を判断する大変重要な要素になるということが分かります。
◆脱炭素の実現やサプライチェーン強靭化に対応していないと競争力が低下する
他社から「製造品あたりのCO2排出量を教えてほしい」と要求された場合、どのように答えますか?
近年では、自社だけでなく、発注先会社の製造過程におけるCO2排出量なども考慮していく気運が高まっています。その中にあって、上記のような質問に答えるには、営業や、製造工程において使用する電力量、化石燃料使用量、メタン排出量etc..など、さまざまな製造データを収集し、統合する必要があります。
また、サプライチェーンについても同様のことが言えます。各社が持つ在庫情報や消費者ニーズを把握し、全体最適化していく気運が高まっています。同じように、他社から「製造品の発注数・受注数・在庫数データを共有してほしい」と要求された場合、どのように答えますか?
上記のような質問に答えるには、在庫情報や消費者ニーズの情報をデータに落とし込む必要があります。中長期的なSCM (サプライチェーンマネジメント)の観点からみれば、ERPやCRMを活用していない企業は競争力が低下することが懸念されています。
カーボンニュートラルの実現も、SCMの最適化も、どちらも自社でデータを収集し、データを活用できる社内環境が整備されていなければならず、これは簡単にできることではありませんが、近い将来対応していかなければならないテーマです。
1-3.日本のDXの現状
では、日本の製造業においてDXの推進状況はどのようになっているのでしょうか?
調査では、日本企業のDXの取り組みはゆっくりではあるものの順調に増加し、成果が出ている企業の割合も増加傾向にあります。一方で、DXの取り組みをデジタイゼーション、デジタライゼーション、デジタルトランスフォーメーションの3段階に分類すると、各段階における具体的な取り組み項目別の成果については、その割合に大きな変化は見られず、特にデジタルトランスフォーメーション段階での成果は、他の段階に比べて道半ばであるとしています。
日本企業のDXの取り組みについては、2021年度から年々増加傾向で、今回調査時点では7割強がDXに取り組んでおり、2022年度調査の米国に並びつつあると説明。DXに取り組んでいる企業の割合は、2021年度の55.8%から73.7%に増加し、着実にDXが企業に浸透していると分析しています。
(引用:DX動向2024)
DXの取り組みにおいて、設定した目的に対する成果が出ているかという質問では、「成果が出ている」と回答した企業の割合は、2022年度調査の58.0%から2023年度調査は64.3%に増加しており、成果が出ている企業が増加しています。
一方で、2022年度の米国調査では、9割程度の企業が「成果が出ている」と回答しており、DXの取り組みは米国並みに進みつつある中で、成果創出につながっていない企業もあると考えられるとしています。
2.DX成功事例6選
国内には、アナログ的な手法から脱却してDXに成功した工場は多数存在します。ここでは成功事例を6つ紹介します。
2-1.DX成功事例①:J社 基幹システム刷新
J社では、基幹システム刷新と業務改革によって、DXの推進をおこなっています。
業種 | 鋳造・機械加工・表面処理業 |
---|---|
DX化効果 | 300万円/年のコスト削減/作業時間の短縮 |
J社では、生産管理・会計管理・在庫管理・原価管理などのそれぞれの管理項目において、それぞれ別のシステムを用いて管理をおこなっていましたが、基幹システムの刷新に際し、さまざまな管理項目の一元化をおこないました。
その際に、現状業務フローの把握⇒フローの見直しをおこない、パッケージシステムに業務を合わせることで、全社横断的に2重/3重入力の排除、属人化の排除を実現しました。近年では、年間300万円のコスト削減に成功しています。
2-2.DX成功事例②:S社 協働ロボット活用
S 社では、これまで手作業だった作業に協働ロボットを使うことによって、加工機へのワーク投入作業の自動化に成功しました。
業種 | 樹脂切削加工品製造 |
---|---|
デジタライゼーション化効果 | 年間工数1200時間削減 |
投資金額 | 500万円 |
S社の成功事例の特徴は、SIer なしでロボット導入を行った点です。
ロボット導入のネックになりがちな費用として、SIer 費用があげられます。 (S社でロボット導入を検討した際は、ロボット本体代金のほかに SIer 費用が 1000 万円近く見積もられていました。)
S社では、自社で内製化することで、SIer 費用を押さえながらロボット活用を行うことに成功しました。
内製化の利点は、自動化品種の追加や、製造ラインの変更に比較的容易に対応できることです。ロボット立ち上げ時に、技術的な開発部分を SIer に任せてしまうと、新たに品種追加を行う際はさらに SIer に費用を払わなくてはなりません。内製化は時間も工数もかかりますが、中長期的に見れば経営効果は高いでしょう。
また、この会社様は従業員数 10 名以下の会社様のため、1 日数時間だけ単純作業を自動化するだけでも、高い自動化効果を発揮することができます。従業員数が少なくなればなるほど捻出される時間の価値が高まるため、ロボット活用は事業規模が小さい会社様ほど効果を発揮できるといえます。
⇒関連記事:工場の自動化 (ファクトリーオートメーション) とは?成功事例5選やメリット、実現までの流れを一挙解説!
2-3.DX成功事例③:S社 AI外観検査
S社では、これまで目視で行われていた樹脂成形製品の目視検査をAI外観検査で自動化に成功しました。
業種 | 樹脂成型品製造 |
---|---|
デジタライゼーション化効果 | 検査人員2名削減・1400万円/年のコスト削減 |
投資金額 | 4300万円 |
S社の成功事例の特徴は、製品自体を回転させながら撮像をおこない、AIに不良品判定を行わせている点です。
S社では、通常では検査が難しい透明の円筒形製品検査の自動化に取り組みました。製品自体を回転させ、且つ撮像した製品画像をAIで処理することで、不良品判定の自動化を成功させました。
明確な金額は記載しませんが、S社も補助金を活用することで投資費用を抑えています。
⇒関連記事:AI外観検査とは?従来の画像検査との違い、導入のメリットや注意点とは?
2-4.DX成功事例④:A社 自動バリ取りロボット
A 社ではロボットを使うことによって、工数がかかっていたバリ取り作業の自動化に成功しました。業種と自動化効果、投資金額は以下のようになっています。
業種 | セラミック製品製造 |
---|---|
自動化効果 | 年間工数 1019 時間削減・生産性 167%増 |
投資金額 | 1800 万円+6 軸ロボット費用 |
A 社の成功事例の特徴は、画像認識によりバリ取りパスを自動で生成している点です。自動生成されたパスに沿ってロボットが動作するため、品種ごとにティーチングプログラムを作成する必要がなく、超多品種少量生産に対応することができます。
本来ロボットを稼働させる際は、ティーチングと呼ばれるロボットのプログラムを人が作成する必要があります。そのためロボットでさまざまな製品の加工をおこなおうとすると、その数だけティーチングをおこなう必要があります。
A 社では、画像認識による自動プログラム作成を採用しているため、作業員が治具に製品を置けば、ロボットが自動でバリ取りをおこなってくれます。
⇒関連記事:自社の業務に合わせた自動化で、少ない人員でも生産増に対応することができました-アスザック株式会社 様
2-5.DX成功事例⑤:C 社溶接ロボット・研磨ロボット
C社では、高い品質が求められる製品において、溶接工程と研磨工程の自動化に成功しました。
業種 | 鈑金溶接品製造 |
---|---|
自動化効果 | 溶接・研磨の熟練技術の継承に成功 |
投資金額 | 7700 万円 (うち 4000 万円は補助金) |
C社の成功事例の特徴は、非常に難易度の高い薄板ステンレスの TIG 溶接と鏡面研磨を最新技術を活用して自動化した点です。さらに投資金額 7700 万円のうち 4000 万円は事業再構築補助金を活用することにより投資コストを抑えています。
薄板の TIG 溶接は非常に熟練度が要求される作業であり、早い人でも製品として出荷できるレベルに達するまでには 5 年はかかる職人技術と言われています。また、C社の製品における研磨工程は鏡面仕上げとなっており相当の工数がかかっている状態でした。
これら難易度の高い職人技術を 6 軸力覚、加速度、位置センサー、アクティブ・コンプライアンス制御技術を用いて自動化に成功しました。
2-6.DX成功事例⑥:A社 協働ロボット
A社では、100 台の協働ロボットを導入し、ワーク投入やエアブロー、検査などの自動化に成功しました。
業種 | 金属部品加工 |
---|---|
自動化効果 | 人員 60名削減・2.5億/年のコスト削減 |
投資金額 | 協働ロボット 100台分 |
A社の成功事例の特徴は、S社と同様SIerレスで自動化に成功した点です。PLCが扱える人材を採用し、徹底してロボット活用の社内教育を行うことで、コストを抑えた圧倒的な自動化を実現しました。
総額では大きい投資となっていますが、それに見合うだけの費用対効果を実現しています。
さらに事例の詳細について気になる方は、1時間程度の無料相談会を活用ください。
HP 上には記載しきれていない、実際にロボットが稼働している様子や、自動化に関する情報を余すことなくご提供させていただきます。
3.DXの3つのメリット
製造業における、DXのメリットは以下の3点です。
3-1.DXのメリット①:生産性の向上
DXにより、工場の自動化や無人化が進むことで、生産性が大幅に向上します。IoTセンサーによるデータ収集や、AIを活用した最適化により、ムダな動作を排除し、無駄なく効率的に製造できるようになります。また、ロボットやコンベアなどの自動化設備の導入により、人的ミスを最小限に抑えることができます。
3-2.DXのメリット②:品質の安定化
DXを推進することで、製品の品質を安定的に保つことができます。例えば、ロボットによる自動組立てなどにより、人的なばらつきを排除でき、均一な製品を作り出せます。また、センサーでデータを常時監視することで、不良品の発生を未然に防ぐことも可能です。このように、DXは製品の品質保証に大きく貢献します。
3-3.DXのメリット③:顧客視点での製品開発
DXを進めることで、顧客の声をリアルタイムで製品開発に反映しやすくなります。例えば、IoTデバイスから集まる顧客の使用実態データや、SNSでの声などを分析することで、顧客のニーズをリアルタイムで製品にフィードバックすることができます。その上で、サンプル製品のシミュレーションや試作を効率的におこなえば、顧客目線での開発が可能となります。
4.製造業におけるDXの5つの課題
製造業における、DXの課題は以下の5点に集約されます。自社でもココが課題になっている、と感じるところはあるのではないでしょうか。一つずつ見ていきましょう。
4-1.製造業におけるDXの課題①:技術者の不足と社内教育への投資不足
DXにおいては、専門的な技術者やデジタルスキルに精通した人材が不足していることが課題の一つに挙げられます。広範囲にわたる技術的知識がなければ、DXの構想を考えることは難しいでしょう。更に、社内に技術者がいたとしても、他の従業員が最新のテクノロジーやデジタルツールについて一定程度理解していないと、宝の持ち腐れになってしまいます。デジタル技術を活用するための、社内教育への投資をおこなうことも重要です。
4-2.製造業におけるDXの課題②:旧来システムとの統合
製造業は歴史が古く、既存のシステムが複雑に絡み合っている企業が多いのが実情です。そのため、最新のデジタル技術を導入する際に、旧来のシステムとの親和性が課題となります。直近でいえば、2025年の崖問題が目前に迫っています。社内の状況によっては、一気にシステム刷新をする必要もあるかもしれません。
⇒関連記事:2025年の崖を対策をしなかった場合の5つのリスク
4-3.製造業におけるDXの課題③:データの統合や分析プロセスの確立の難しさ
製造業では、工数データ、生産実績データなどの膨大な量のデータが生まれますが、それらのデータを統合し、分析する手法の確立は非常に困難です。管理する項目(生産管理、原価管理など)ごとにシステムを導入しており、スムーズなデータ統合ができないケースも多く存在します。また、データの品質や信頼性も重要な課題となっています。例えば工数データをRFIDで取得したとしても、データ利活用に必要十分な工数実績が正しく取得できているとは限りません。
4-4.製造業におけるDXの課題④:かさむ投資コスト
DX化の必要性は理解しているが、コストがかかりすぎてしまい、投資に踏み切れない、という工場も多いでしょう。例えば、社内システム/ネットワークを統合しようとすれば、多方面に開発費用がかかってしまい、その分コストは上がります。自社の状況に合わせ、何から手をつけていけば最適なのか?をよく検討する必要があります。
しかし、近年は補助金制度が充実しています。諸条件はありますが、補助金を活用することで、通常よりも少ない投資金額で設備を導入することができるでしょう。
⇒関連記事:ものづくり補助金最新動向
4-5.製造業におけるDXの課題⑤:従来の組織文化やプロセスの変革への抵抗
DXは、業務プロセスを抜本的に改革していく取り組みです。そのため、従業員の協力が得られない限りは効果的に推進することはできません。DXを推進していくためには、それぞれの部署に対して趣旨の共有をおこない、コミュニケーションをとり、合意形成を取っていく必要があります。人間の感情や、部署間の関係性がおおいに関わってくる領域になるため、最も大きな課題の一つということができます。立場が異なるメンバー・グループ同士が同じゴールを目指していけるよう、統括していく必要があります。
いかがでしたでしょうか。上記の課題が自社にあてはまっている…と感じる方は、船井総研の無料経営相談サービスを活用ください。専門のコンサルタントが対応し、豊富な他社事例やDXの方法などを情報共有いたします。
⇒船井総研の無料経営相談フォームはこちら
5.DXを進めるためのプロセス
製造業がDXを推進する際のプロセスは、おおよそ以下のようになります。
ステップ1: 経営ビジョンの明確化と戦略の策定
ステップ2: 全体構想と意識改革
ステップ3: 本格推進
(参考:経済産業省 デジタルガバナンスコード実践の手引き)
それぞれのステップについて解説していきます。
5-1.ステップ1: 経営ビジョンの明確化と戦略の策定
会社が目指すべき方向性を明確化します。
経営層の観点から、なぜ改革をおこなっていくのか、また目指すべき目標がなにかを議論していきます。生産性の向上、コスト削減、新しいビジネスモデルの構築などが目標として設定されます。
ビジョン・戦略策定の時点で目的や目標があいまいになってしまうと、全社的な合意形成を取ることが難しくなるため、注意が必要です。
5-2.ステップ2: 全体構想と意識改革
ビジョン達成のためのDXの構想を設計し、また社内の意識改革を促します。
一口にDXといっても、会社の業種や状況によってさまざまな解があります。目指すビジョンと現状の差を把握しながら、全体設計をおこなうことが非常に重要です。また、経営者が自らDX推進の必要性を理解し、従業員に共有することで、社内に変革を受け入れる空気感を醸成します。“経営者が自ら”旗振り役として推進していくことで、プロジェクトを進めやすくなります。
このタイミングでDXを推進するメンバーを選定し、プロジェクトを立ち上げますが、エンジニアやシステム導入の知見があるメンバーがいない場合は、外部から人材を採用したり、コンサルタント・SIer活用の検討もおこなう必要があります。
⇒関連記事:DXロードマップのポイントと戦略的手法を解説!製造業のDX化を成功に導く方法とは?
5-3.ステップ3:本格推進
プロジェクトメンバー主導で、業務プロセスの現状把握・見直しとシステム構築をおこなっていきます。
既存の業務プロセス、インフラ、データ管理の状態を評価し、目標と現実とのギャップを正確に把握します。現状、現場で起きている不都合は何か?目的達成のために、今足りない部分はどこなのか?細かく精査をしていく必要があります。現状評価が不十分だと、適切なプロジェクト策定は行えません。
現状の業務プロセスが把握できたら、データの収集、管理、分析、活用のための戦略を立て、実行にうつります。多くの施策に同時並行で着手すると、プロジェクトメンバーや従業員への負荷が大きく、スムーズに進めることが難しくなってしまいます。はじめはスモールステップ的に実行していくことが重要です。
DXの成果は定期的に評価し、フィードバックを基に持続的な改善を実施する。生産性やコスト削減のKPIを設定し、定量的な評価を行います。成果の評価が適切でないと、改善の余地が見落とされるため、客観的で透明性のある評価プロセスを確立することが重要です。
6.製造業でDXを実現させるための3つのポイント
6-1.工場の自動化を実現する際のポイント①:経営者が旗振り役となること
まず第一に、「経営者が旗振り役となって、DXを進めていくこと」が極めて重要です。経営者自身がDXの重要性を深く理解し、自らが先頭に立って取り組む姿勢を示すことで、組織全体が一丸となって改革に取り組む風土が生まれます。反対に、会社をどうしていきたいのか?理想に近づくためにデジタル技術をどのように活用していくのか?などのコアな部分を従業員やコンサル会社任せにしてしまうと、どこかに齟齬が生まれてしまい、理想的な成果を上げることは難しいでしょう。経営者が率先してビジョンや目標を社員と共有し、具体的なアクションプランを策定することができれば、DXの推進力を格段に上げることができます。
6-2.工場の自動化を実現する際のポイント②:中長期的な取り組みをスモールステップで推進
次に重要なのは、「中長期的な取り組みをスモールステップで推進すること」です。DXは時間も、お金も、労力もかかる取り組みであり、1、2年という短期間で本当の効果が出るものではありません。急激に進めようとすれば、従業員への負荷が高まり、かえって生産性が低下するリスクがあります。
そのため、まずはスモールステップで着実に進めることが重要ですが、小さなステップだけを繰り返していては、最終的なゴールにはたどり着くことができません。したがって、「5年や10年先を見据えた中長期的なビジョンを持ちつつ、現在できることに集中して取り組む」というような中長期的なゴールと短期的なゴールの両方を見据えながら取り組みを進めることが重要です。具体的には、まず既存の生産プロセスの一部をデジタル化し、小さな成功体験を積み重ねると共に、従業員の慣れやスキルを向上させます。これによって、次第により複雑で広範囲なDXの取り組みに挑戦することが可能となります。
6-3.工場の自動化を実現する際のポイント③:人材育成と外部リソースの活用
最後に重要な点は、「人材育成と外部リソースの活用」です。DX推進にはデジタル技術に精通した人材が不可欠であり、これを内部で育てるための育成プログラムの整備が求められます。作業者が導入したツールや技術を構想通りに活用できる様、サポートしていくことが重要です。
さらに、デジタル技術の専門知識やスキルが不足している場合には、外部の専門家やコンサルタントの力を借りることが効果的です。コンサルタントや専門企業の知見を活用することで、効率的かつ迅速にDXを進めることができます。社内人材のみでDXを推進する場合は、既存の業務と平行して進める必要があるため、プロジェクトに十分な時間を割くことができない、というジレンマがあります。プロジェクトを迅速に進めたい方は、外部リソースの活用を強く推奨します。
最後までお読みいただきありがとうございました。
製造業におけるDX推進の成功に向けた具体的なステップと重要なポイントがご理解いただけたでしょうか?自社のDX実現においてお困りの際は、船井総研の無料経営相談をご活用ください。特に、以下のようなお悩みをお持ちの際は、是非弊社の無料経営相談をご活用ください。
⇒ 株式会社船井総合研究所の無料経営相談はこちらから!
自社でDXを推進しようと、すでにシステムを導入したが、なかなかうまくいかない…
現場の反発が大きく思うようにプロジェクトが進まない…
DXを進めていきたいが、何から手を付けたらよいかわからない…アイデアが欲しい…
専門のコンサルタントが豊富な他社事例を共有しながら、貴社に最適なご提案をさせていただきます。