記事公開日:2024.12.06
最終更新日:2024.12.06
製造現場のデータ可視化:利益向上を実現する最新事例と未来展望

本コラムをお読みいただきありがとうございます。船井総合研究所の熊谷俊作です。
データ可視化は、製造現場の様々な課題解決に役立ちます。例えば、製品ごとの原価を可視化することで収益性の高い製品を把握し、生産計画に反映できます。本記事では、製造現場におけるデータ可視化の具体的な実際の事例と、その効果について解説します。
目次
1.はじめに
製造業を取り巻く環境は、グローバル競争の激化、顧客ニーズの多様化、人手不足など、かつてないほど厳しさを増しています。こうした状況を打破し、持続的な成長を実現するためには、従来の経験や勘に基づいた経営から脱却し、データに基づいた論理的な意思決定を行うことが不可欠です。
特に、製造現場におけるデータ活用は、生産性向上、コスト削減、品質向上といったあらゆる経営課題の解決に直結する、極めて重要なテーマと言えます。
2.データ可視化がもたらす、製造現場の革新
製造現場におけるデータ活用において、近年特に注目されているのが「データ可視化」です。これは、センサーやIoTデバイスなどから収集した膨大なデータを、グラフや図表などを用いて視覚的に分かりやすく表現する手法です。
DXが叫ばれてしばらく時期が経ちましたが、多くの製造業ではまだまだこのデータの可視化が進んでいない企業が多くあります。データ可視化によって、これまで見えにくかった現場の状況が明確化され、以下のような効果が期待できます。
- リアルタイムな状況把握: 生産状況、設備稼働状況、品質データなどをリアルタイムに可視化することで、問題発生時の迅速な対応が可能となります。
- ボトルネックの発見と解消: 工程ごとの進捗状況や作業時間、設備の稼働率などを可視化することで、生産のボトルネックを容易に特定し、改善に繋げることができます。
- 潜在的な問題の予防: 過去のデータ分析や傾向把握を通じて、潜在的な問題を事前に予測し、未然に防ぐことが可能になります。
- 従業員の意識改革: データに基づいた目標設定や進捗共有を行うことで、従業員のモチベーション向上、主体的な改善活動促進に繋がります。
3.現場データ可視化:成功事例に学ぶ
では、具体的にどのようなデータが、どのように可視化され、現場改善に活用されているのでしょうか?今回、船井総研が発行したレポート「リアルタイム現場データ可視化事例20選」では、業種、規模、課題別に、様々な企業における具体的な可視化事例を実際の可視化レポートを用いてご紹介しています。
3-1.利益管理:収益向上に直結するデータ可視化
a.製品個別原価算出
従来、製造原価は、製品群全体でまとめて計算されることが多く、また製品ごとの標準原価計算が行われているものの実際原価との差が生まれてしまい、実態と異なる原価計算をされてしまう等、製品ごとの収益性を正確に把握することは困難でした。しかし、センサーやIoT技術を活用することで、材料費、加工費、人件費など、製品一つひとつにかかった原価をリアルタイムに把握することが可能になりました。
レポートでは、この製品個別原価をグラフや表で可視化し、利益率の高い製品、低い製品を明確に示す事例を紹介しています。
この情報に基づき、高収益製品の生産比率増加、低収益製品の製造工程見直し、販売価格調整など、戦略的な意思決定を行うことができます。
b.製品別原価一覧
製品の種類が多い企業では、製品ごとの原価を一覧で比較できるように可視化することで、より効率的な原価管理が可能になります。レポートでは、製品名、原価、販売価格、利益率などを一覧表示し、一目で各製品の収益性を把握できる事例を紹介しています。
これにより、全社的な収益目標達成に向けた、製品ポートフォリオの最適化や、製造原価低減活動の重点化などを推進することができます。
c.客先別売上総額と粗利率
顧客別、あるいは取引先別の売上総額と粗利率を可視化することで、収益性の高い顧客、低い顧客を把握することができます。レポートでは、顧客名、売上高、原価、粗利率などをランキング形式で表示する事例を紹介しています。 この情報に基づき、優良顧客への営業強化、低収益顧客への価格交渉、新規顧客開拓など、営業戦略の最適化を図ることができます。
3-2.稼働監視:ムダをなくし、効率性を最大化する
a.設備別稼働監視
設備の稼働状況をリアルタイムに可視化することで、設備の稼働率向上、ダウンタイムの削減に繋げることができます。レポートでは、設備ごとに稼働時間、停止時間、稼働率をグラフで表示し、設備の稼働状況を「見える化」する事例を紹介しています。 これにより、設備の故障予兆検知、予防保全の実施、稼働率の低い設備の活用方法検討など、設備の効率的な運用が可能になります。
b.工場内稼働監視
工場全体の設備稼働状況を俯瞰的に可視化することで、工場全体の生産効率を把握することができます。レポートでは、工場内の各設備の稼働状況を色分けして表示し、稼働状況が一目でわかるようにした事例を紹介しています。 これにより、工場全体の稼働率向上に向けた、設備レイアウトの見直し、工程の標準化、人員配置の最適化などを検討することができます。
c.ライン別稼働監視
生産ラインごとの稼働状況を可視化することで、ライン間の能力差やボトルネックを把握することができます。レポートでは、各ラインの生産量、稼働率、停止時間などをグラフで比較表示し、ライン間の能力差を明確に示す事例を紹介しています。 これにより、能力の低いラインへの重点的な改善活動、ライン間の作業分担調整、生産計画の精緻化などを実施することができます。
3-3.不良管理:品質向上とコスト削減を両立
a.工場別不良管理
工場ごとの不良発生状況を可視化することで、工場間の品質管理レベルの差を把握することができます。レポートでは、各工場の不良率、不良発生件数、不良原因などをグラフで比較表示し、不良対策の重点工場を明確にする事例を紹介しています。 これにより、不良対策のノウハウ共有、品質管理体制の見直し、従業員教育の強化など、工場全体の品質レベル向上を図ることができます。
b.検査記録集計表
製品別、工程別、検査項目別の不良発生状況を可視化することで、不良発生の傾向を分析することができます。レポートでは、検査記録を集計し、不良発生率の高い製品、工程、検査項目を特定する事例を紹介しています。 これにより、不良発生原因の特定、再発防止策の実施、検査工程の見直しなど、効果的な品質改善活動が可能になります。
4.未来展望:進化し続けるデータ可視化
今後、AIや機械学習などの技術革新により、データ可視化はさらに進化していくと予想されます。
例えば、AIによるデータ分析の自動化が進み、人間では気づかなかったような潜在的な問題点や改善ポイントを、AIが発見してくれるようになるでしょう。
AIを活用するには、データが必要です。最近では生成AIの登場などによって、よりAI活用が注目されていますが、一番重要なのはどのAIを使うかではなく、どれだけ正確なデータを蓄積することができるかなのです。
正確なデータを蓄積させることができるようになれば、自社データを学習させたAI活用を実施することが可能となります。これにより、自社の過去データ(=ノウハウ)をいつでもだれでも参照することができるようになり、属人化解消・業務効率化が実現できるようになるのです。
5.最後に
データ可視化は、製造現場のあらゆる課題解決に貢献する強力なツールです。ぜひ、本コラムやレポート「リアルタイム現場データ可視化事例20選」を参考に、自社のデータ活用戦略に役立てていただければ幸いです。
そして、船井総研では、製造業の皆様のデータ活用を支援するためのセミナーやコンサルティングサービスも提供しております。データ活用でお困りのことがございましたら、お気軽にご相談ください。
セミナーページ:https://smart-factory.funaisoken.co.jp/event/
■【製造業向け】リアルタイム現場データ可視化事例20選
https://www.funaisoken.co.jp/dl-contents/smart-factory_smart-factory_03546_S045
関連コラム
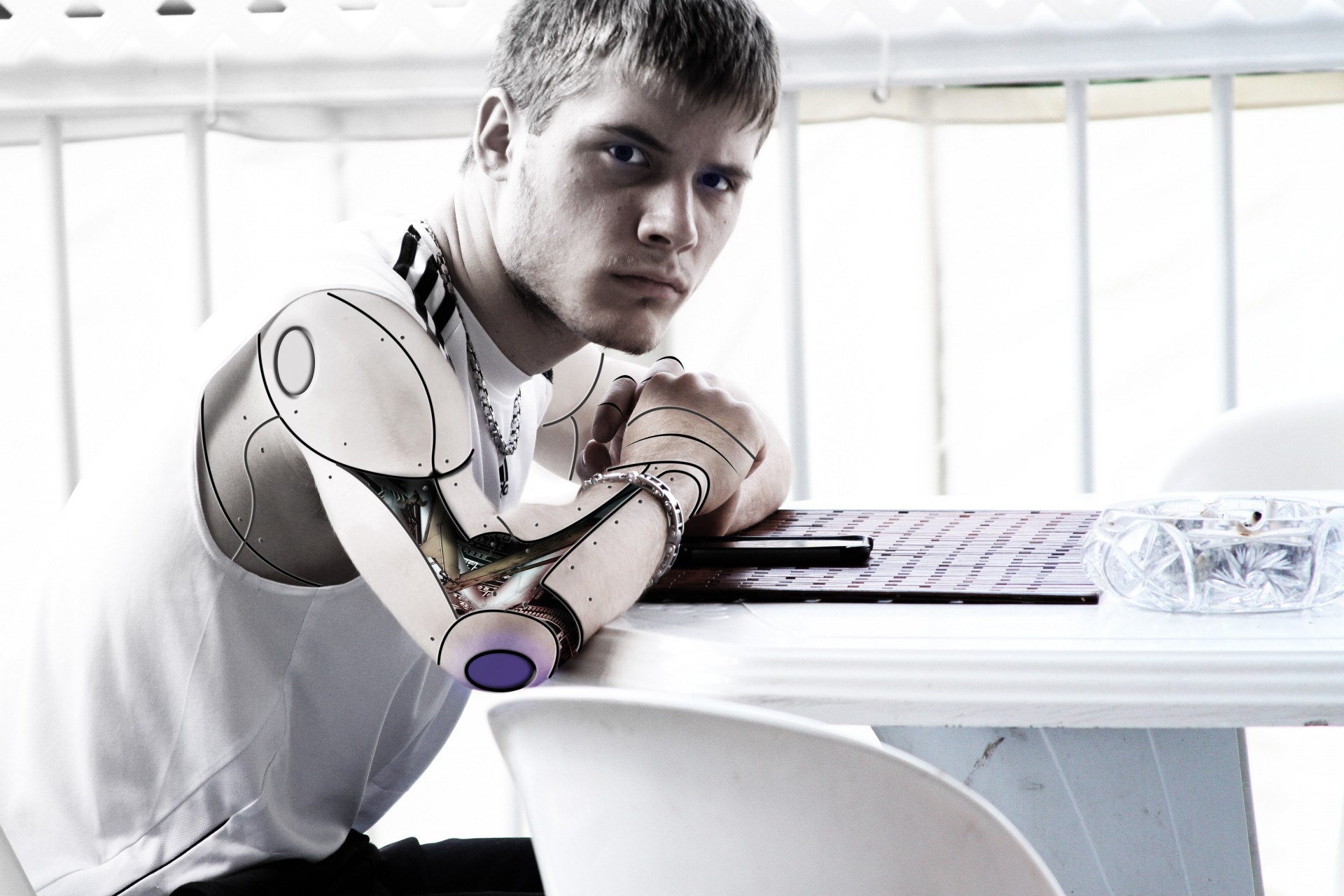
ロボットのティーチングとは?ティーチングの種類と概要を解説
2019.08.27
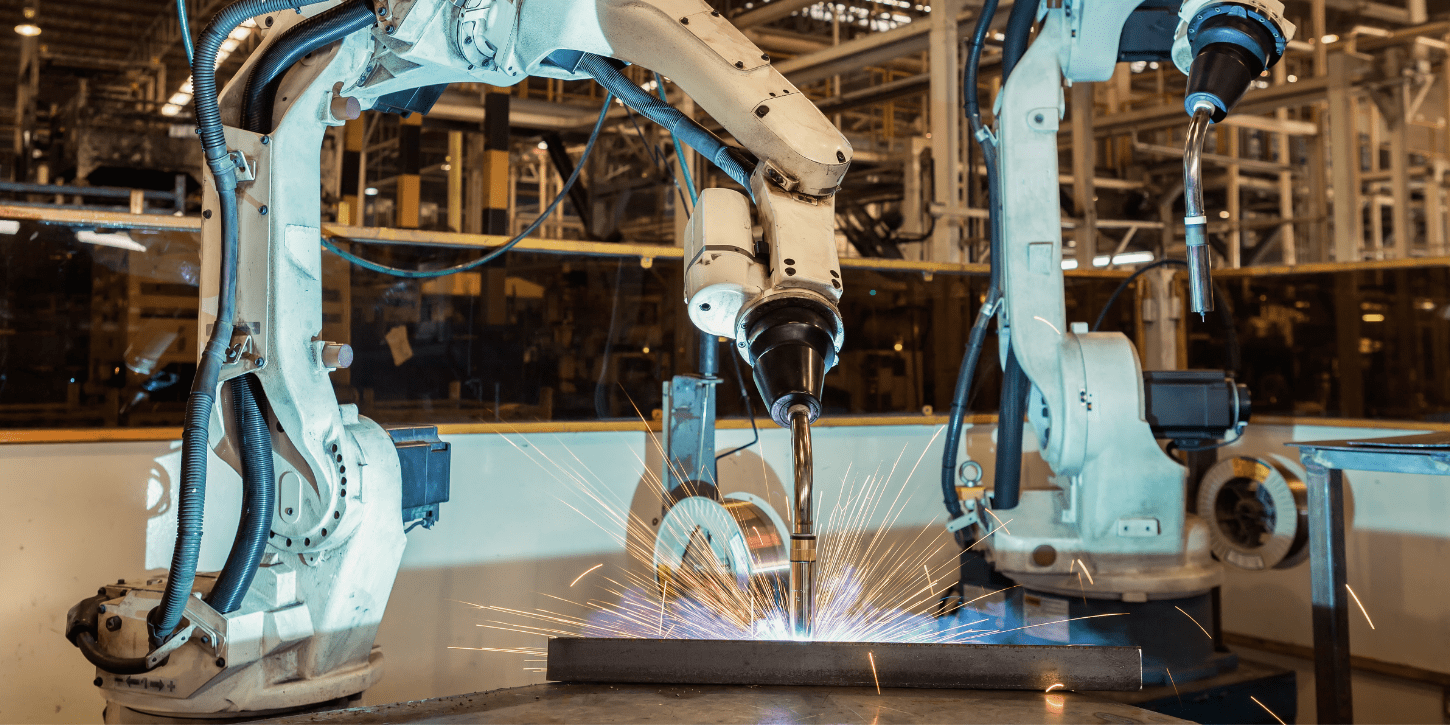
溶接ロボットで行う自動化の方法とは?
2019.08.29
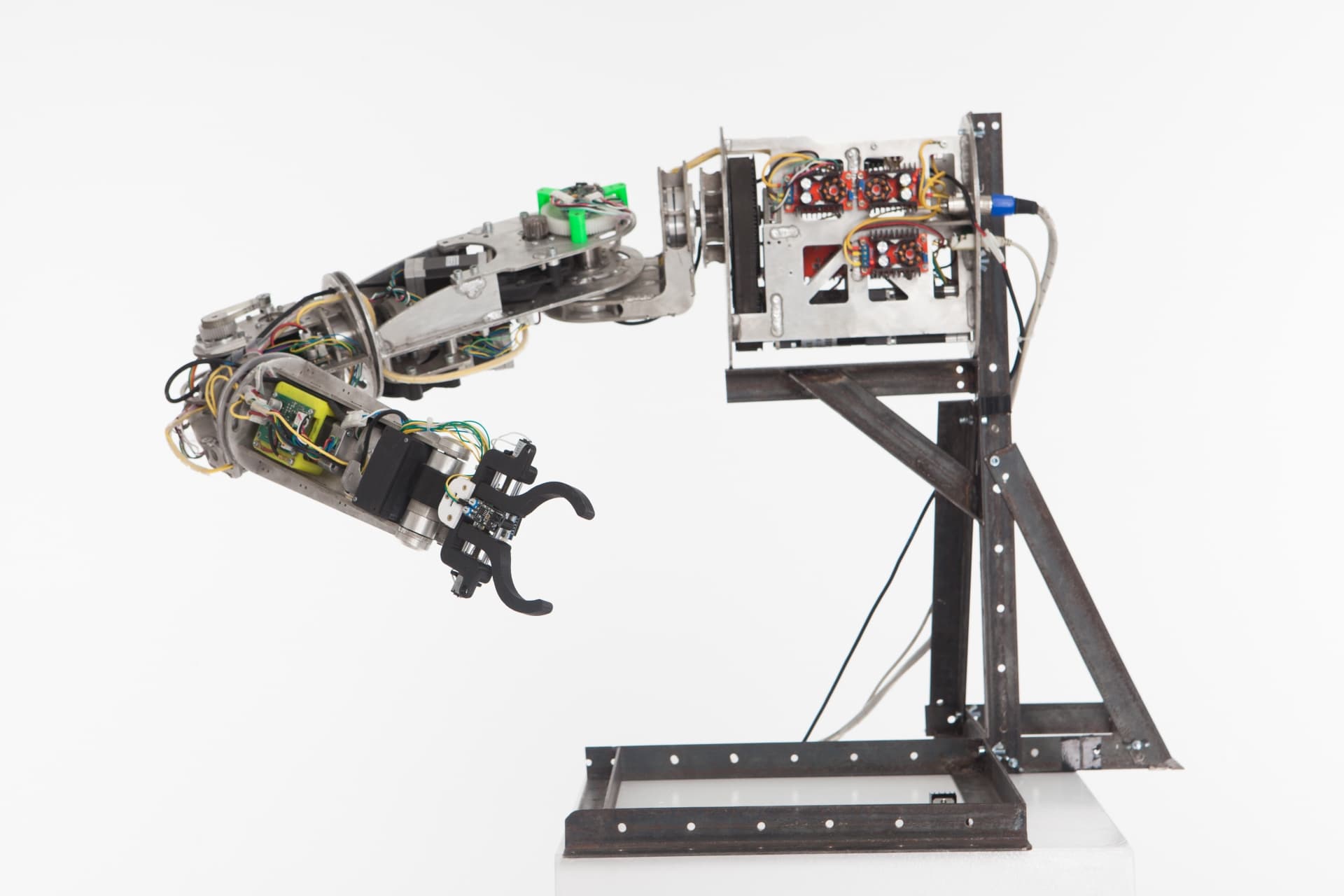
産業用ロボットとは?最新動向からロボットの違いを知る
2019.09.17