記事公開日:2025.01.20
最終更新日:2025.04.02
業務改革への道! システム導入時の生産管理・原価管理のポイントを徹底解説
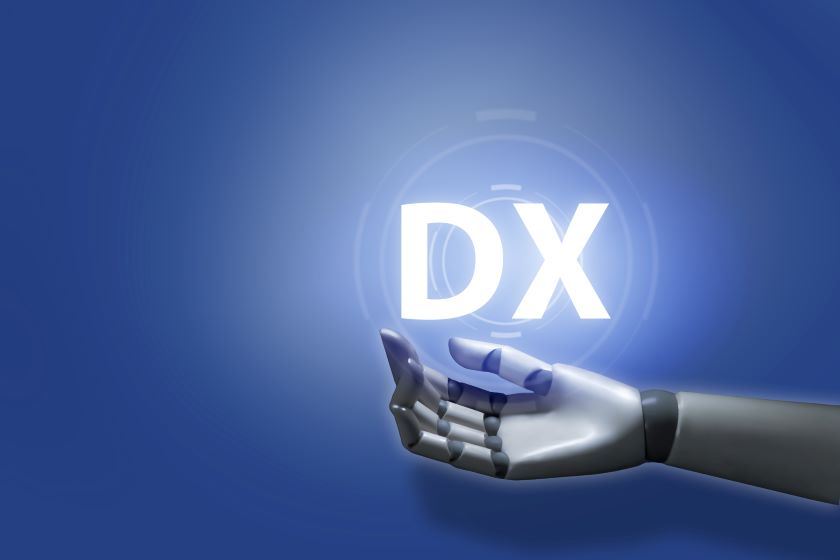
いつも当コラムをお読み頂きありがとうございます。
システム導入の目的として、生産管理、原価管理を実現したいというご要望をよく伺います。
しかし当然システムを導入するだけではこれらの目的に繋がらないと言えます。また導入プロセスにおいて誤った方向へ進んでしまうと、属人化や非効率化を改善できずに実現したい生産管理・原価管理のシステム化とならないケースがございます。そこで今回はシステム導入における課題と成功のポイントを幾つかお伝えいたします。
1.よくある生産管理・原価管理の課題とは?
【生産管理業務上の課題】
- 短納期や急な変更の仕事が入ると、計画の組み直しが現状の仕組みではできない。結局時間を掛けてExcelで実施している。
- 生産計画及び実作業のノウハウがベテラン担当者(職人)の頭の中にだけある(属人化)
- 生産計画の平準化、効率化が出来ない。
- 機械毎(工程毎)の稼働状況が把握されていない
- 受注処理に追われてばかりで現場の負担は増える一方
【原価業務運用上の課題】
- 製品別採算(収支)が把握できていない
- 歩留り確認を1年に1回しか実施できていない(Excel、手作業)(ベテラン担当者は何となくはわかっているが・・・)
- 現場は原価低減をしていると言うが、検証ができない(ロスの実態が分からない・・)
- 原価差異がどんぶり勘定になっているので、各部門や工程毎の評価ができない
2.「システム導入の進め方」の成功例・失敗例
【利用者(発注側企業)】
- 前のシステムより使いにくい、面倒で仕事が増えて不満…
- 新しいシステムを入れたのに、結局手作業で加工して上司に提出している…
- 操作説明を受けたが、昔行っていた業務がなく前のシステムを使わざるを得ない…
- 過去データが移行してなかったため大変なことになっている…
- 今まであったシステムと連携していないため手作業が増えた…
- 判断に必要な情報がすぐに出てくる予定が3日くらいかかる…
【システム会社(請負側企業)】
- システム開発の業務委託契約であり、業務改善までは請け負っていない。
- お客さんの協力や情報提供が弱く、スケジュールが延び赤字になってしまっている。
- 操作教育は当然している、新旧業務の準備や説明は我々の範囲ではない。
- データ移行作業は請けたが、チェック確認はお客さんの責任である事は言っていた。
- お客さん側がプロジェクト慣れしていなく、現場や経営を巻き込めていない。
- お客さんができていないところは、なんとかしてあげたいが稼働(工数)に限度がある。
3.システム関連における運用上の課題
- 過去にシステム化のチャレンジをしたが頓挫してしまった
(品目マスター、部品構成マスターが作り切れなかった) - 過去のシステム導入で効果がイマイチ感じられない
- 情報システムに関するコストまたは要員コストが掛かっている
- ITやパソコンに詳しいメンバーに導入を任せたら上手く進まなかった
- 経営判断に必要な製品別や工程別データが出せない、もしくは時間がかかる
続いて生産・原価管理システム導入を成功させるポイントをお伝えします!
4.生産・原価管理システム導入を成功させるポイント
- 経営者がDX化を理解し、変革の意識を持つ
- DX化のキーマンを選出する (標準化推進)
- 全体を俯瞰し、自社にフィットする計画をつくる
- パイロット運用ですぐに新業務のイメージを浸透させる
- 新しい仕組みに合ったルールを明確にし、これを遵守する
- 統合型クラウドのDXツールを短期・安価で導入
- システムベンダーを頼らずに極力自社で運用できる仕組みを構築する
- 段階的なKPI/KGI設定と生産性向上の目的をもつ
5.まとめ
生産・原価を見える化し改善する為のDX化の認識と取り組みとして、経営者がDXを理解し、変革の意思を持って臨むこと、全体を俯瞰できるキーマンを立てることが何より重要です。
その為の計画をたてて目的目標を持って実行すること。またシステムで見える化(データ化)を実現(業務標準化・適正化・属人化排除)し、導入後は業務データと経営判断に必要なデータをシステム化+業務改善(DX化)で見える化をする。
最終的には実際の戦略アクションに繋げるところまでを通していくことが成功への道となると考えます。
▼「食品加工業の為の原価改善!」 社長セミナー
生産管理&原価管理を徹底的に見直す為のシステム利用方法が分かる!
本セミナーで学べるポイント
従業員数10名以上の食品加工業の社長が知っておくべき原価管理システムが分かる!
-
~社長の為の生産管理・原価管理システムで「見える化」する具体的な方法が分かります~
職人・属人化している生産管理・個別原価管理業務を改善する為のシステムを導入する方法が分かる! -
~一部の熟練者・職人に依存している業務にシステムを導入・活用する方法が分かります~
基礎知識や導入経験がない社長でも個別原価をデータ化してデータ経営する方法が分かります。 -
~生産・購買・在庫・原価をシステムで統合的する方法が良く分からない…そんな社長の為のセミナーです~
個別原価を可視化する事で何が儲かっているのか?儲かっていないのか?が明確になりその具体的な対策が分かる! -
~理論・理屈ではなく、自社の現場で実践できるやり方が分かります~
システムにおける食品の構成部品設定方法が分かる! - ~食品特性に対応したシステムにおける構成部品設定方法が分かります~
https://www.funaisoken.co.jp/seminar/123081
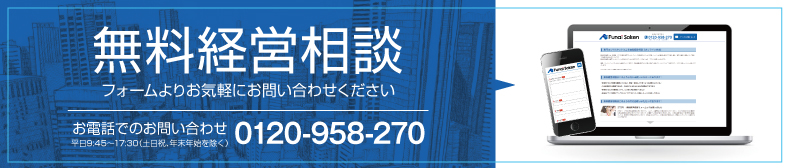
◾️この記事を書いたコンサルタント

株式会社船井総合研究所
DXコンサルティング部 リーダー
岩松 将史
全国各地の中堅・中小製造業における業務改革ならびに生産性向上支援に従事し、その実績は計30件以上。
支援先企業のDX実行計画の策定に加えて、生産工程やバックオフィス業務の調査&分析、生産性向上に向けたビジネスプロセスの抜本的な見直しを手掛ける。
また、AIやERP等のシステムベンダー選定やシステム導入に関するプロジェクトマネジメントも主導。
これまでに計20件以上のDX関連セミナー登壇実績あり。「製造業のDX」に特化した会員数50社以上の事例勉強会「船井総研 スマートファクトリー経営部会」の主宰でもある。
関連コラム
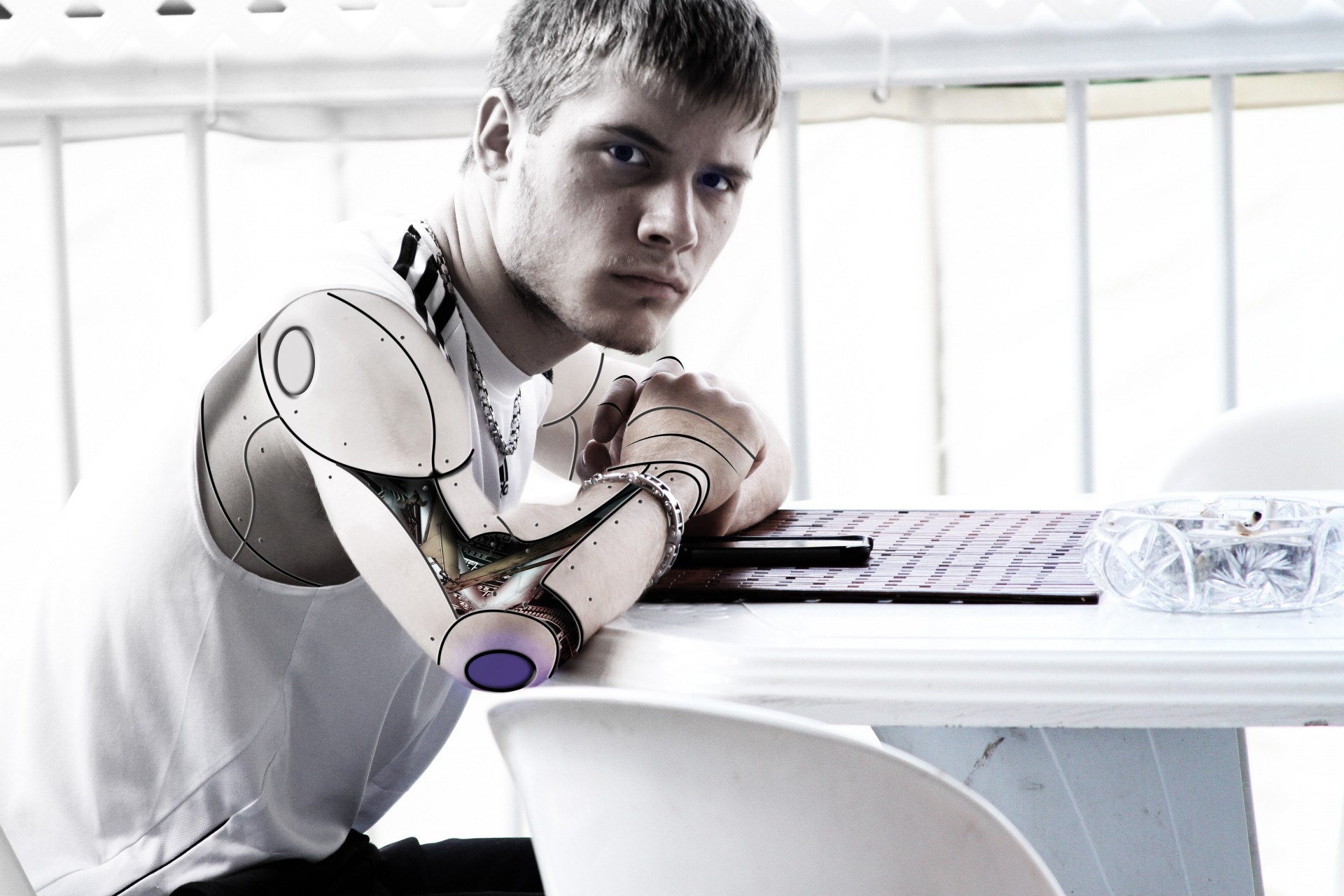
ロボットのティーチングとは?ティーチングの種類と概要を解説
2019.08.27
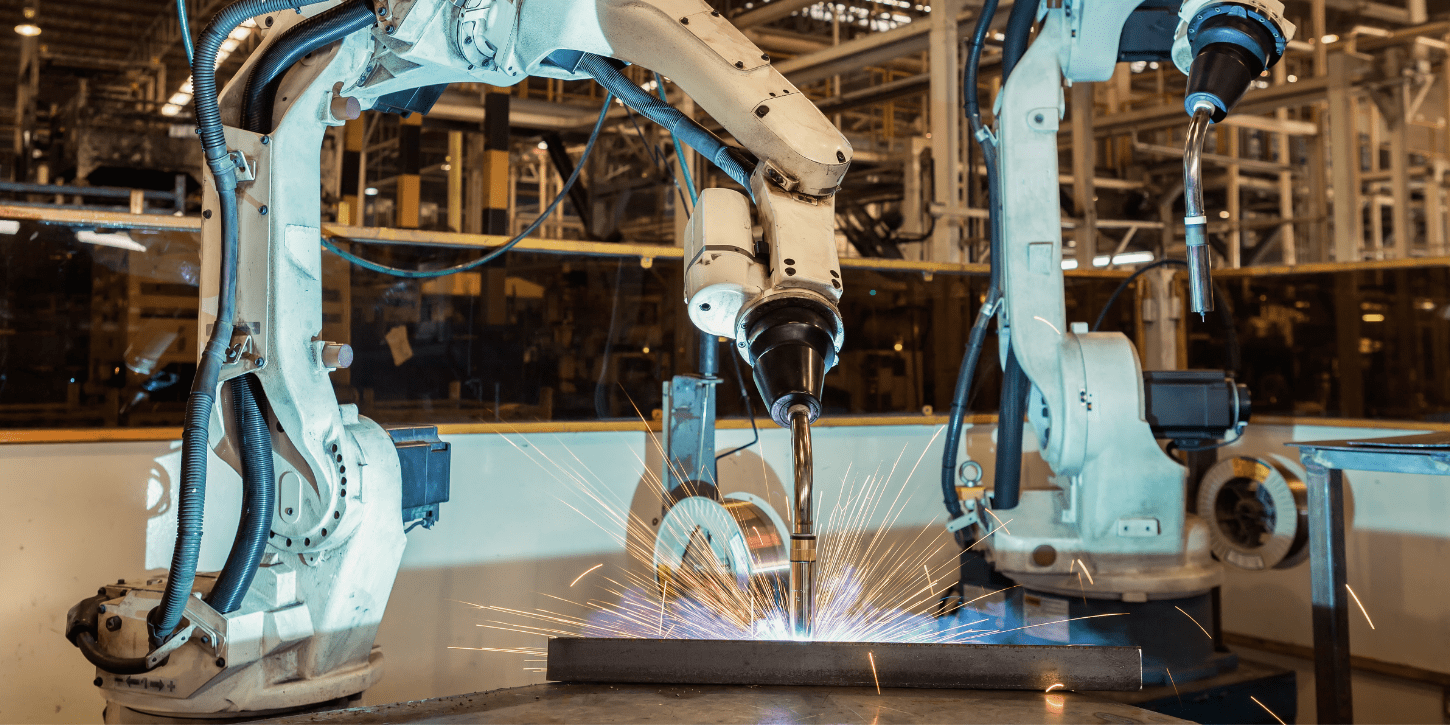
溶接ロボットで行う自動化の方法とは?
2019.08.29
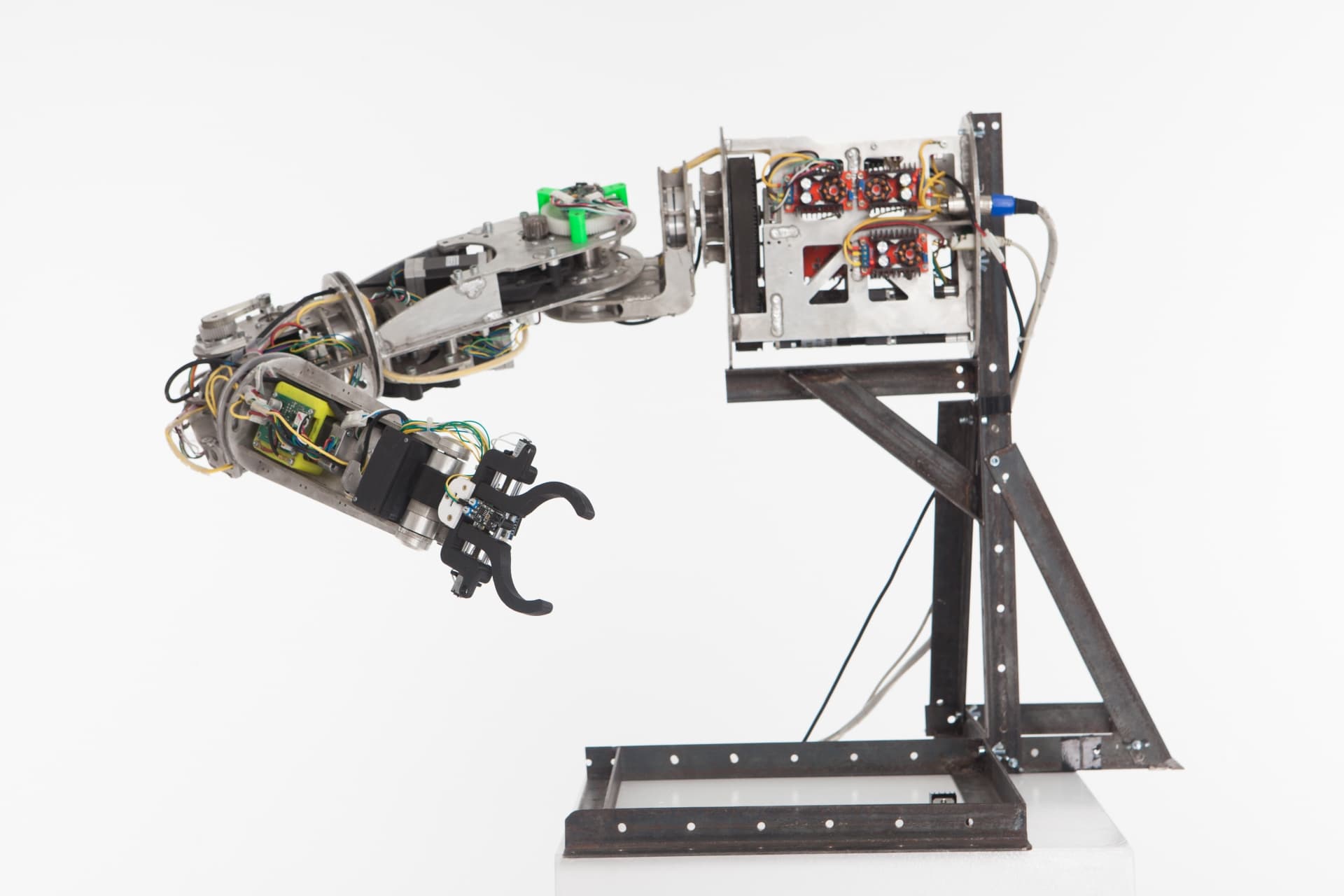
産業用ロボットとは?最新動向からロボットの違いを知る
2019.09.17