記事公開日:2025.02.05
最終更新日:2025.04.02
IoTで工場はどう変わる?事例から学ぶ導入メリット・課題・手順を解説
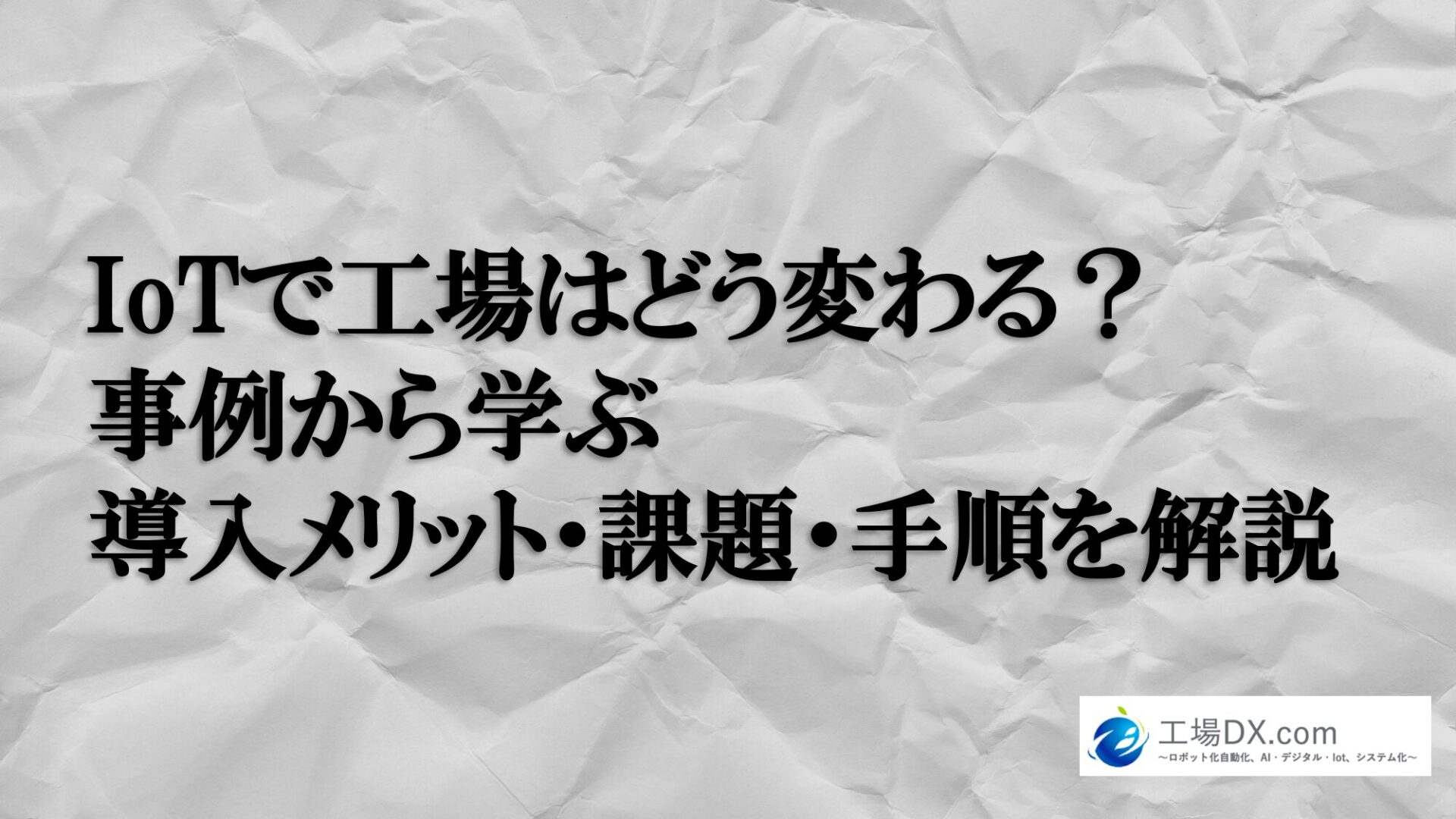
IoT化で工場はどう変わる?本記事では、IoT導入による工場のメリットを、事例を交えて解説します。
生産性向上、コスト削減など、IoTで何を実現できるのか?導入手順や課題もわかりやすく解説。IoT化を検討中の工場担当者必見の記事です。
目次
1. 工場におけるIoT化とは?わかりやすく解説
近年の製造業において、IoT(Internet of Things)の導入が急速に進んでいます。IoTとは、従来インターネットに接続されていなかった様々なモノ(機械、設備、製品など)をインターネットに接続し、データの収集・分析・活用を行うことで、業務効率化や新たな価値創出を実現する技術です。
本記事では、工場におけるIoT化について、基礎知識から導入メリット、課題、事例、そして成功させるためのポイントまで、わかりやすく解説していきます。IoT化を検討中の工場担当者の方々にとって、有益な情報となるよう、具体的な事例やデータも交えながら詳しく解説してまいりますので、ぜひ最後までお読みください。
1.1. IoTとは?
IoTとは、「Internet of Things」の略で、日本語では「モノのインターネット」と訳されます。センサーや通信機能を内蔵した様々な機器をインターネットに接続することで、機器同士がデータを送受信し、相互に連携する仕組みです。
例えば、工場の生産ラインでは、各工程の機械にセンサーを取り付け、稼働状況や生産量などのデータをリアルタイムに収集することができます。これらのデータは、クラウド上のプラットフォームに集約され、分析・活用することで、生産効率の向上や品質改善などに役立ちます。
IoTは、私たちの身の回りにある様々なモノに組み込まれ、生活を便利にするだけでなく、産業分野においても大きな変革をもたらしています。工場におけるIoT化は、その最たる例と言えるでしょう。
1.2. スマートファクトリーとは?
スマートファクトリーとは、IoT、AI(人工知能)、ビッグデータなどの先進技術を活用し、工場のあらゆる活動を自動化・効率化・最適化した工場のことです。
従来の工場では、人間の経験や勘に頼った作業が多く、非効率な部分や属人的な部分がありました。しかし、スマートファクトリーでは、データに基づいた科学的な意思決定が可能となり、人為的なミスや無駄を削減することができます。
スマートファクトリーは、単なる自動化された工場ではなく、データに基づいて自律的に改善を続ける工場と言えます。これにより、変化の激しい市場環境にも柔軟に対応できる、持続可能な工場を実現することができます。
1.3. 製造業におけるIoT化の必要性
製造業において、IoT化が求められる背景には、以下のような要因があります。
- グローバル競争の激化
世界的な競争が激化する中、コスト削減や品質向上、リードタイム短縮など、競争力を強化するための取り組みが求められています。 - 人材不足
少子高齢化による労働人口の減少に伴い、製造現場では深刻な人材不足が課題となっています。 - 顧客ニーズの多様化
顧客のニーズが多様化・変化する中で、多品種少量生産やマスカスタマイゼーションなど、柔軟な生産体制の構築が求められています。 - 技術革新の加速
AIやロボットなど、新しい技術が次々と登場しており、これらの技術を活用した新たな生産方法やビジネスモデルが生まれています。
IoTを活用することで、これらの課題を解決し、企業の競争力を強化することが可能となります。
1.4. DX(デジタルトランスフォーメーション)との関係
DX(デジタルトランスフォーメーション)とは、データとデジタル技術を活用して、企業のビジネスモデルや業務プロセス、組織文化などを変革し、競争上の優位性を確立することです。
IoTは、DXを推進するための重要な要素技術の一つであり、工場におけるデータ収集・活用を促進することで、DXの実現に貢献します。
IoTによって収集されたデータは、企業の様々な部門で共有され、分析・活用されることで、部門間の連携強化や意思決定の迅速化にもつながります。
2. 工場にIoTを導入するメリット
工場にIoTを導入することで、様々なメリットを得ることができます。ここでは、代表的なメリットを6つご紹介します。
2.1. 生産性向上
IoTを導入することで、工場の生産性を向上させることができます。
例えば、生産ラインの各工程にセンサーを取り付け、稼働状況をリアルタイムに監視することで、ボトルネックとなっている工程を特定し、改善することができます。また、設備の稼働データを分析することで、故障の予兆を検知し、計画的なメンテナンスを行うことで、設備のダウンタイムを削減することができます。
ある工場では、IoTを導入することで、生産ラインの停止時間を20%削減し、生産量を10%増加させたという事例があります。
2.2. コスト削減
IoTを導入することで、工場のコストを削減することができます。
例えば、エネルギー使用量をリアルタイムに監視し、無駄な電力消費を削減することができます。また、在庫管理システムを導入することで、適切な在庫量を維持し、在庫保管コストや欠品による損失を削減することができます。
ある企業では、IoTを活用したエネルギー管理システムを導入することで、エネルギーコストを15%削減したという事例があります。
2.3. 品質向上
IoTを導入することで、製品の品質を向上させることができます。
例えば、製造工程のデータを収集・分析することで、不良品の発生原因を特定し、品質改善につなげることができます。また、製品にセンサーを取り付け、使用状況や環境データを収集することで、製品の改良や新製品開発に役立てることができます。
ある工場では、IoTを活用した品質管理システムを導入することで、不良品発生率を50%削減したという事例があります。
2.4. 人材不足解消
IoTを導入することで、人材不足の解消に貢献することができます。
例えば、自動搬送ロボットや無人搬送車(AGV)を導入することで、搬送作業を自動化し、人手に頼っていた作業を削減することができます。また、遠隔監視システムを導入することで、熟練作業員のノウハウを共有し、人材育成を効率化することができます。
ある企業では、IoTを活用した搬送システムを導入することで、搬送作業に必要な人員を30%削減したという事例があります。
2.5. サステナビリティへの貢献
IoTを導入することで、環境負荷の低減など、サステナビリティに貢献することができます。
例えば、エネルギー消費量を最適化することで、CO2排出量を削減することができます。また、資源の有効活用や廃棄物削減などにも貢献することができます。
ある工場では、IoTを活用したエネルギー管理システムを導入することで、CO2排出量を20%削減したという事例があります。
2.6. データ活用による新たな価値創出
IoTを導入することで、収集したデータを活用し、新たな価値を創出することができます。
例えば、顧客の製品使用状況データを分析することで、顧客のニーズに合わせた製品開発やサービス提供を行うことができます。また、収集したデータを外部に販売することで、新たな収益源を獲得することもできます。
ある企業では、IoTを活用したデータ分析サービスを提供することで、年間1億円の新たな収益を上げたという事例があります。
3. IoT導入の課題と解決策
IoT導入には、様々な課題が伴います。ここでは、代表的な課題と解決策について解説します。
3.1. セキュリティ対策
IoTデバイスは、インターネットに接続されているため、サイバー攻撃のリスクがあります。そのため、適切なセキュリティ対策を講じる必要があります。
具体的には、ファイアウォールやウイルス対策ソフトの導入、アクセス権限の設定、セキュリティ教育の実施などが挙げられます。
また、IoTデバイスの脆弱性を定期的にチェックし、最新のセキュリティパッチを適用することも重要です。
3.2. 人材育成
IoTシステムを運用・管理するためには、専門的な知識やスキルを持った人材が必要です。そのため、人材育成が重要な課題となります。
社内研修や外部研修、資格取得支援など、人材育成のための取り組みを行う必要があります。
また、IoTに関する最新情報を常に収集し、社員のスキルアップを図ることも重要です。
3.3. コスト
IoTシステムの導入には、初期費用や運用費用など、多額のコストがかかります。そのため、導入前に費用対効果を十分に検討する必要があります。
補助金制度の活用やクラウドサービスの利用など、コスト削減のための工夫も必要です。
また、段階的に導入を進めることで、初期投資を抑えることも可能です。
3.4. 既存システムとの連携
IoTシステムを導入する際には、既存のシステムとの連携が必要となる場合があります。そのため、システム間の互換性やデータ形式などを考慮する必要があります。
API(Application Programming Interface)を活用することで、異なるシステム間でのデータ連携をスムーズに行うことができます。
また、システム連携に関する専門家やベンダーに相談することも有効です。
3.5. 失敗事例から学ぶ注意点
IoT導入を成功させるためには、過去の失敗事例から学ぶことも重要です。
よくある失敗例としては、目的が明確でないまま導入を進めてしまう、PoC(Proof of Concept)を実施せずに本格導入してしまう、セキュリティ対策が不十分である、などが挙げられます。
導入前に目的や目標を明確化し、PoCを実施して検証を行い、セキュリティ対策を徹底することが重要です。
また、専門家やコンサルタントに相談することで、失敗のリスクを減らすことができます。
4. 工場におけるIoT導入事例
ここでは、工場におけるIoT導入事例を5つご紹介します。
【事例1:製造業における生産ラインの効率化(富士電機)】
富士電機は、自社の工場にIoTを導入し、生産ラインの効率化を実現しました。具体的には、生産設備にセンサーを取り付け、稼働状況や生産量などのデータを収集・分析することで、ボトルネックとなっている工程を特定し、改善しました。また、設備の故障予知を行うことで、ダウンタイムを削減しました。
富士電機の事例では、IoT導入によって生産性が20%向上し、リードタイムが15%短縮されたという効果が出ています。
【事例2:中小企業におけるIoT活用事例】
中小企業でも、IoTを導入することで、様々な効果を得ることができます。例えば、ある中小企業では、IoTを活用した温度管理システムを導入することで、製品の品質向上と省エネルギー化を実現しました。また、別の企業では、IoTを活用した在庫管理システムを導入することで、在庫管理業務の効率化とコスト削減を実現しました。
ある中小企業では、IoT導入によって品質不良率を30%削減し、在庫管理コストを10%削減したという事例があります。
【事例3:スマートマニファクチャリングソリューションの導入事例(日立ソリューションズ)】
日立ソリューションズは、スマートマニファクチャリングソリューションを提供しており、多くの企業のIoT導入を支援しています。ある企業では、日立ソリューションズのソリューションを導入することで、生産計画の精度向上、在庫管理の効率化、品質管理の強化などを実現しました。
日立ソリューションズの事例では、IoT導入によって生産計画精度が15%向上し、在庫管理コストが20%削減されたという効果が出ています。
【事例4:Predictive Maintenance(予知保全)の導入事例】
Predictive Maintenance(予知保全)とは、設備の故障を事前に予測し、計画的なメンテナンスを行うことで、設備のダウンタイムを削減する手法です。ある工場では、IoTを活用した予知保全システムを導入することで、設備の故障による突発的な生産停止を防止し、安定稼働を実現しました。
ある工場では、予知保全システム導入によって設備のダウンタイムを50%削減し、メンテナンスコストを20%削減したという事例があります。
【事例5:在庫管理の効率化事例】
IoTを活用することで、在庫管理を効率化することができます。例えば、倉庫内の製品にRFIDタグを取り付け、在庫状況をリアルタイムに把握することで、発注業務の効率化や在庫切れの防止などが可能となります。
ある企業では、IoTを活用した在庫管理システムを導入することで、在庫管理コストを15%削減し、欠品率を5%削減したという事例があります。
5. IoT導入の手順をステップごとに解説
IoT導入を成功させるためには、適切な手順で進めることが重要です。ここでは、IoT導入の手順を5つのステップに分けて解説します。
5.1. ステップ1:現状分析と課題の明確化
まず、現状を分析し、IoT導入によって解決すべき課題を明確化します。具体的には、以下の項目について分析します。
- 生産性
- 品質
- コスト
- 納期
- 人材
- 環境
これらの項目について、現状における課題や問題点を洗い出します。
5.2. ステップ2:目的の設定とKPIの設定
次に、IoT導入の目的を明確化し、達成すべき目標値(KPI)を設定します。目的としては、例えば、以下のようなものが考えられます。
- 生産性の向上
- 品質の向上
- コストの削減
- 納期の短縮
- 人材不足の解消
- 環境負荷の低減
KPIは、目的を達成するための具体的な指標であり、数値で測定可能なものを設定します。
関連記事:製造業の生産現場で活用するKPI設定:成功事例と必要なデータ活用法を解説
https://smart-factory.funaisoken.co.jp/241226-2/
5.3. ステップ3:適切なIoTデバイス・システムの選定
目的やKPIを達成するために、適切なIoTデバイスやシステムを選定します。IoTデバイスとしては、センサー、カメラ、通信モジュールなど、様々な種類があります。システムとしては、データ収集・分析プラットフォーム、生産管理システム、在庫管理システムなどがあります。
選定の際には、自社のニーズや課題、予算などを考慮する必要があります。
5.4. ステップ4:導入計画の策定と実行
IoTデバイスやシステムを選定したら、導入計画を策定し、実行します。導入計画には、以下の項目を盛り込みます。
- 導入スケジュール
- 担当者
- 予算
- リスク対策
計画に基づき、IoTデバイスの設置、システムの構築、データ収集・分析環境の整備などを行います。
5.5. ステップ5:データ分析と改善
IoTシステムを稼働させたら、収集したデータを分析し、改善活動を行います。データ分析によって、課題や問題点の発見、改善策の検討、効果測定などを行うことができます。
分析結果に基づき、システムの調整や運用方法の見直しなどを行い、継続的な改善を図ります。
6. IoT導入を成功させるためのポイント
IoT導入を成功させるためには、以下のポイントを押さえることが重要です。
6.1. 経営層の理解とコミットメント
IoT導入は、全社的な取り組みとなるため、経営層の理解とコミットメントが不可欠です。経営層がIoT導入の意義を理解し、積極的に推進することで、プロジェクトをスムーズに進めることができます。
6.2. 部門間連携
IoT導入は、製造部門だけでなく、営業部門、企画部門、情報システム部門など、様々な部門が関わるプロジェクトです。そのため、部門間で連携し、情報共有や協力体制を構築することが重要です。
6.3. プロジェクト体制の構築
IoT導入を推進するためには、専任のプロジェクトチームを立ち上げることが有効です。プロジェクトチームは、リーダー、メンバー、推進担当者などで構成し、役割分担を明確にします。
6.4. 効果測定と改善
IoT導入の効果を測定し、継続的な改善活動を行うことが重要です。KPIを設定し、定期的に効果測定を行うことで、改善点を特定し、より効果的なIoT活用につなげることができます。
6.5. 最新技術の活用(AI、クラウドなど)
IoTとAI、クラウドなどの最新技術を組み合わせることで、より高度なデータ分析や活用が可能となります。最新技術の動向を常に把握し、積極的に活用していくことが重要です。
7. 今後の工場におけるIoT活用と展望
IoTは、今後も工場の進化を加速させる重要な技術として、ますます発展していくと考えられます。ここでは、今後の工場におけるIoT活用と展望について解説します。
7.1. スマートファクトリー化の進展
IoT、AI、ロボットなどの技術革新により、スマートファクトリー化がさらに進展していくと考えられます。工場の自動化・自律化が加速し、人手に頼らない効率的な生産体制が構築されることで、生産性向上、コスト削減、品質向上などが実現すると期待されます。
7.2. データ活用による新たなビジネスモデル創出
IoTで収集したデータを活用することで、新たなビジネスモデルを創出する動きが加速すると考えられます。例えば、製品の稼働状況データを分析し、故障予知やメンテナンスサービスを提供する、顧客のニーズに合わせた製品のカスタマイズサービスを提供する、などが考えられます。
7.3. サステナビリティへの貢献
環境問題への関心の高まりから、工場におけるサステナビリティへの取り組みがますます重要になっています。IoTを活用することで、エネルギー消費量の削減、CO2排出量の削減、資源の有効活用など、環境負荷を低減することができます。
7.4. データ蓄積とAI活用によるさらなる進化
IoTの導入によって、工場では膨大なデータが収集されます。これらのデータを単なる記録として扱うのではなく、貴重な資産として蓄積し、社内のノウハウとして活用していくことが重要です。
例えば、ベテラン作業員が持つ経験や勘といった暗黙知を、センサーデータや作業記録などと組み合わせることで形式知化し、AIに学習させることで、誰でもベテラン作業員と同等の判断ができるようなシステムを構築することができます。
AIを活用することで、過去の類似データを参照し、状況に応じた最適な判断を導き出すことが可能になります。これにより、業務効率化や意思決定の迅速化、人材不足の解消などが期待できます。
さらに、蓄積したデータを分析することで、新たな課題や改善点の発見にもつながります。例えば、これまで見過ごされていた小さな異常や非効率な作業工程などをAIが検知することで、これまで以上に精度の高い改善活動が可能になります。
IoTとAIの連携は、工場のさらなる進化を加速させる鍵となるでしょう。
8. IoT導入に役立つ補助金制度
IoT導入を検討している企業にとって、補助金制度の活用は有効な手段となります。経済産業省では、中小企業のIoT導入を支援するための補助金制度を提供しています。
補助金制度を利用することで、IoT導入にかかる費用の一部のみの負担で有効活用することができます。補助金制度の活用を検討する際は、最新の情報を経済産業省のウェブサイトなどで確認するようにしましょう。
9. ユースケース紹介
IoTは、様々な分野で活用されています。ここでは、工場におけるIoTのユースケースをいくつかご紹介します。
- 生産管理
- 品質管理
- 設備管理
- エネルギー管理
- 安全管理
- 環境管理
10. よくある質問集
Q1. IoT導入にはどれくらいの費用がかかりますか?
A1. 導入するシステムの規模や機能、導入するデバイスの数などによって費用は大きく異なります。小規模なシステムであれば数百万円から、大規模なシステムであれば数億円かかる場合もあります。小規模なシステムであれば数十万円から、大規模なシステムであれば数億円かかる場合もあります。
Q2. IoT導入に必要な期間はどれくらいですか?
A2. 導入するシステムの規模や複雑さ、企業の規模や体制などによって期間は異なります。一般的には、数ヶ月から数年かかる場合が多いです。
Q3. IoT導入で失敗しないためにはどうすればよいですか?
A3. 導入前に目的や目標を明確化し、PoCを実施して検証を行い、セキュリティ対策を徹底することが重要です。
11. 関連サービス・ソリューション
当社では、工場のIoT化を支援する様々なサービス・ソリューションを提供しています。詳しくは、当社のウェブサイトをご覧ください。
IoT導入に関するご相談は、お気軽にお問い合わせください。
12. まとめ
この記事では、工場におけるIoT化について、基礎知識から導入メリット、課題、事例、そして成功させるためのポイントまで解説しました。
IoTを導入することで、工場の生産性向上、コスト削減、品質向上、人材不足解消、サステナビリティへの貢献など、様々なメリットを得ることができます。
IoT導入を検討する際は、本記事で紹介した内容を参考に、自社の課題やニーズに合わせて適切なシステムを構築していくことが重要です。
当社では、工場のIoT化を支援する様々なサービス・ソリューションを提供しています。IoT導入に関するご相談は、お気軽にお問い合わせください。
※注釈
本記事の内容は、2024年5月15日現在の情報です。
本記事に記載されている会社名、製品名、サービス名等は、それぞれ各社の商標または登録商標です。
本記事の内容は、予告なく変更される場合があります。
13. 参考文献
経済産業省ウェブサイト:https://www.meti.go.jp/english/press/2024/0315_001.html
富士電機ウェブサイト:https://www.fujielectric.co.jp/
日立ソリューションズウェブサイト:https://www.hitachi-solutions.com/about_us/
今回では、工場のIoT活用事例をもとに、DXとの関連性について説明をしてまいりました。
弊社が主催している下記セミナーでは、自社の生き残りをかけたDXの取組を、実際の事例をもとにお話ししています。
改めて、下記のような課題を抱えられている方はぜひご参加ください。
- 多品種少量生産の紡績・繊維業の社長
- 昨今の紡績業界の市場動向を鑑みて、自社はどのように生き残る戦略を立てるべきかを知りたい社長
- 紙日報による手書き運用が続いており、その後のデータ活用ができていない。
- 標準原価で収益管理しているが、材料費高騰・賃上げに対応できていない。
- Excel運用が多く、社内での情報共有がリアルタイムにできない。
- 原価管理をどのように利益UPに結びつけるか具体的な方法を知りたい。
- 経営指標はもちろんだが、現場指標を設けて従業員に経営意識を持たせたい。
https://www.funaisoken.co.jp/seminar/123657
https://www.funaisoken.co.jp/dl-contents/smart-factory_smart-factory_03729_S045