記事公開日:2025.04.11
最終更新日:2025.04.14
基幹システム導入が実現する工程分析:多品種少量生産の課題解決と生産性向上のための新たな道筋
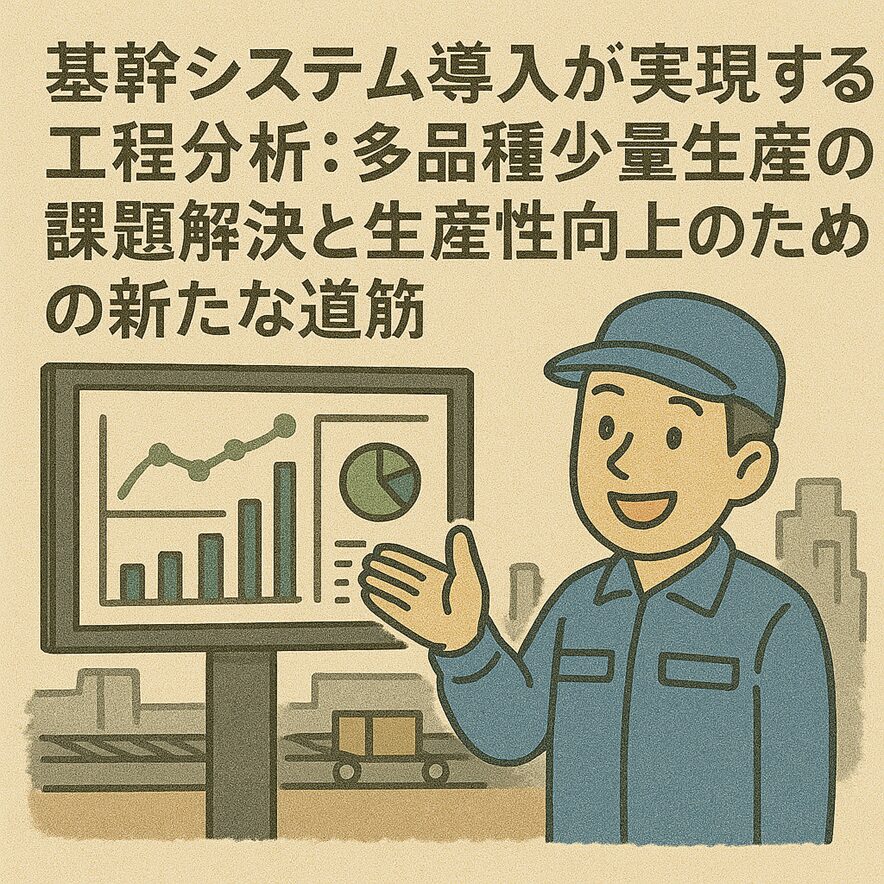
「多品種少量生産で、どこにムダがあるのか、どう改善すればいいか、経験と勘だけでは限界を感じている…」
もしあなたが、このような悩みを抱える多品種少量生産の中小製造業の経営者、または現場管理者なら、この記事はまさに、暗闇に差し込む一筋の光となるでしょう。
この記事では、基幹システム導入が、これまで困難だった多品種少量生産における詳細な工程分析をいかに可能にするのか、そしてその分析結果をどのように課題解決と生産性向上に繋げていくのかを、具体的な事例を交えながら徹底的に解説します。
- なぜ多品種少量生産で工程分析が重要でありながら難しかったのか?
- 基幹システムが工程分析を容易にする具体的な機能とは?
- 基幹システムを活用した工程分析による、驚くべき生産性向上とコスト削減の事例
- 基幹システム導入における注意点と、分析を最大限に活かすためのステップ
この記事を読むことで、あなたは基幹システムが単なる業務効率化ツールではなく、自社の生産工程を深く理解し、改善するための強力な武器となることを確信できるでしょう。
多品種少量生産の複雑な工程に潜むムダや課題は、従来の管理方法ではなかなか可視化できませんでした。しかし、基幹システムを導入することで、客観的なデータに基づいた精密な工程分析が可能になり、これまで見えなかった改善の糸口を掴むことができるのです。
さあ、基幹システムが拓く、新たな生産性向上の道筋を一緒に見ていきましょう。
目次
多品種少量生産における工程分析の壁:なぜ今まで困難だったのか?
多品種少量生産の現場では、製品の多様性、生産量の変動性、頻繁な段取り替えなどが複雑に絡み合い、工程内の様々な情報を正確に把握し、分析することが非常に困難でした。
従来の管理方法における限界
1. 手作業によるデータ収集の限界
- 紙の帳票やExcelなどを用いた手作業でのデータ収集では、時間と手間がかかり、リアルタイムな情報の把握が困難でした。また、入力ミスや集計ミスも発生しやすく、データの信頼性に課題がありました。
- 例えば、作業時間の記録を手書きで行っていた場合、作業者は本来の作業に集中できず、正確な時間を記録することも難しいでしょう。また、集計作業にも膨大な時間がかかり、タイムリーな分析には繋がりませんでした。
2. 情報のサイロ化と連携の悪さ
- 生産部門、営業部門、購買部門など、各部門が個別のシステムや方法で情報を管理している場合、部門間の情報連携がスムーズに行かず、全体的な視点での工程分析が困難でした。
- 例えば、生産部門は生産実績データを持っていても、営業部門の販売予測データと連携していなければ、需要に基づいた最適な生産計画を立てることができません。
3. リアルタイムな進捗状況の把握の困難さ
- 複数の製品が同時並行で生産される多品種少量生産では、各製品の現在の進捗状況をリアルタイムに把握することが難しく、ボトルネックとなっている工程の特定や、納期遅延のリスク管理が困難でした。
- ホワイトボードや日報などを用いた管理では、情報の更新に時間がかかり、常に最新の状況を把握することは不可能に近かったと言えます。
4. 客観的なデータに基づいた分析の欠如
- 経験や勘に頼った管理では、具体的なデータに基づいた問題点の特定や改善策の立案が難しく、効果的な対策を講じることができませんでした。
- 例えば、「なんとなくこの工程が遅れている気がする」といった主観的な判断だけで対策を講じても、根本的な解決には繋がらない可能性がありました。
5. 多岐にわたる要因の複雑な絡み合い
- 多品種少量生産の工程には、多くの要因が複雑に絡み合っており、手作業での分析では、どの要因が生産性に最も影響を与えているのかを特定することが困難でした。
基幹システムが工程分析を可能にする革新的な機能
基幹システムは、これらの従来の管理方法の限界を克服し、多品種少量生産における精密かつ効率的な工程分析を実現するための強力な機能を提供します。
データの一元管理とリアルタイムな可視化
・基幹システムの機能:
- 生産実績、在庫情報、購買情報、販売情報など、企業のあらゆる基幹業務に関するデータを一元的に管理します。
- 各工程の進捗状況、作業時間、不良発生状況などをリアルタイムにデータとして収集し、ダッシュボードなどで可視化します。
・工程分析への貢献:
- これまで手作業では困難だったリアルタイムなデータ収集と可視化により、ボトルネックとなっている工程や、遅延が発生している箇所を瞬時に特定することができます。
- 各部門のデータが統合されることで、全体最適の視点から工程を分析することが可能になります。
詳細な作業実績の記録と分析
・基幹システムの機能:
- 作業者、設備、製品ごとに、作業時間、作業内容、不良原因などの詳細な実績データを記録します。
- 記録されたデータを集計・分析し、標準作業時間との比較、不良発生傾向の分析、作業者別の生産性分析などを行うことができます。
・工程分析への貢献:
- 客観的なデータに基づいて、ムダな作業時間の特定、不良の発生しやすい作業の特定、熟練者と非熟練者の作業時間の差異の分析などが可能になり、効率的な改善策の立案に繋がります。
生産計画と実績の比較分析
・基幹システムの機能:
- 事前に立てられた生産計画と、実際の実績データを比較分析することができます。
- 計画に対する遅延状況の把握、計画達成率の算出、計画変更の影響分析などを行うことができます。
・工程分析への貢献:
- 生産計画の妥当性を検証し、計画の精度向上に役立ちます。また、計画からの乖離要因を分析することで、計画の実行を妨げる工程の問題点を特定することができます。
部品・在庫のトレーサビリティと連携分析
・基幹システムの機能:
- 部品の入荷から製品の出荷までのトレーサビリティ情報を管理します。
- 在庫情報と生産情報を連携させることで、在庫状況が生産計画に与える影響、欠品による生産遅延のリスクなどを分析することができます。
・工程分析への貢献:
- 不良が発生した場合に、どのロットの部品に問題があったのかを迅速に追跡することができ、原因究明と対策を効率的に行うことができます。また、適切な在庫水準の設定にも役立ちます。
レポート・分析機能の充実
・基幹システムの機能:
- 収集・蓄積されたデータに基づいて、様々な切り口でレポートを作成したり、多角的な分析を行ったりすることができます。
- KPI(重要業績評価指標)のモニタリング、異常値の検出、将来予測などに活用できます。
・工程分析への貢献:
- 定期的なレポートを通じて、工程の現状を客観的に把握し、問題点や改善の兆しを早期に発見することができます。また、高度な分析機能を用いることで、複雑な要因が絡み合う問題の原因を特定することも可能になります。
基幹システムを活用した工程分析による生産性向上とコスト削減の事例
基幹システムを導入し、その分析機能を活用することで、多品種少量生産の現場で実際に生産性向上とコスト削減を実現した事例をご紹介します。
事例1:機械部品製造業D社
D社は、多品種少量生産で精密機械部品を製造しており、熟練作業者の退職による技能伝承の遅れと、それに伴う品質のばらつきが課題でした。
- 基幹システムの活用: 作業時間管理機能、作業手順書管理機能を持つ基幹システムを導入。各作業の標準時間と実績時間を比較分析し、熟練者の作業ノウハウを基に標準作業手順書を動画付きで作成・共有しました。
- 工程分析による効果: 作業時間のばらつきが大幅に減少し、不良率が30%低減しました。また、新人教育の時間が短縮され、早期の戦力化に成功しました。
事例2:プラスチック加工業E社
E社は、顧客の細かなニーズに対応したオーダーメイドのプラスチック製品を多品種少量生産しており、頻繁な設計変更による手戻りや、材料のロスが課題でした。
- 基幹システムの活用: 生産管理機能、在庫管理機能、設計情報連携機能を持つ基幹システムを導入。設計変更情報をリアルタイムに製造現場に連携し、過去の設計データと材料使用実績を分析することで、類似製品の設計を流用し、材料ロスを削減しました。
- 工程分析による効果: 設計変更に伴う手戻り工数を20%削減し、材料ロスを15%削減しました。また、類似製品の設計流用により、開発期間も短縮されました。
事例3:食品製造業F社
F社は、季節や顧客の要望に応じて多種多様な食品を少量生産しており、原材料の在庫管理の複雑さと、トレーサビリティの確保が課題でした。
- 基幹システムの活用: 在庫管理機能、トレーサビリティ管理機能を持つ基幹システムを導入。原材料の入庫から製品の出荷までの情報をロット単位で管理し、過去の販売実績と在庫状況を分析することで、最適な発注量を算出し、廃棄ロスを削減しました。
- 工程分析による効果: 原材料の廃棄ロスを10%削減し、賞味期限切れによる損失を大幅に低減しました。また、トレーサビリティ機能の強化により、万が一の食品事故発生時にも迅速な対応が可能になり、顧客からの信頼性も向上しました。
基幹システム導入と工程分析を成功させるためのステップ
基幹システムの導入は、工程分析を始めるための重要な第一歩です。導入を成功させ、その分析機能を最大限に活用するためには、以下のステップを踏むことが重要です。
ステップ1:導入目的の明確化と現状分析
- なぜ基幹システムを導入し、工程分析を行いたいのか、具体的な目的(例:リードタイムの短縮、不良率の低減、コスト削減など)を明確にします。
- 現在の生産工程の課題や問題点を洗い出し、どの情報を基幹システムで管理・分析したいかを具体的に定義します。
ステップ2:適切な基幹システムの選定
- 自社の業種、業務規模、生産形態(多品種少量生産の特徴を考慮)、予算に合った基幹システムを選定します。
- デモンストレーションなどを通じて、工程分析に必要な機能(リアルタイムなデータ収集・可視化、作業実績管理、生産計画との比較、在庫連携、レポート・分析機能など)が十分に備わっているかを確認します。
- ベンダーの導入実績やサポート体制も重要な選定ポイントです。
ステップ3:導入計画の策定とデータ移行
- 導入スケジュール、担当者、必要なリソースなどを明確にした導入計画を策定します。
- 既存のシステムや手作業で管理しているデータを、新しい基幹システムに正確かつ効率的に移行するための計画を立てます。
ステップ4:システムの設定とカスタマイズ
- 導入した基幹システムを、自社の業務プロセスに合わせて設定・カスタマイズします。
- 工程分析に必要なデータ項目やレポートのテンプレートなどを事前に準備します。
ステップ5:従業員への教育と運用開始
- システムの操作方法や、データ入力のルールなどを従業員に丁寧に教育します。
- 導入初期は、ベンダーのサポートを受けながら、システムを安定的に運用するための体制を構築します。
ステップ6:データの蓄積と工程分析の実施
- 基幹システムの運用が安定したら、蓄積されたデータを活用して本格的な工程分析を開始します。
- リアルタイムダッシュボードの監視、作業実績データの分析、生産計画との差異分析、ボトルネック工程の特定などを行います。
ステップ7:分析結果に基づいた改善策の実施と効果測定
- 工程分析によって明らかになった問題点に対して、具体的な改善策を立案・実行します。
- 改善策の実施後には、基幹システムで再度データを分析し、その効果を客観的に測定します。
ステップ8:継続的な改善サイクルの確立
- 一度改善したら終わりではなく、定期的に工程分析を実施し、継続的に改善活動を行うための仕組みを構築します。
- 基幹システムを常に最新の状態に保ち、変化する状況に合わせて活用方法を見直します。
まとめ
多品種少量生産における工程分析は、従来の管理方法では多くの困難を伴いましたが、基幹システム導入によって、その状況は劇的に変化します。基幹システムが提供するリアルタイムなデータ収集・可視化、詳細な作業実績の管理、生産計画との比較分析などの機能は、これまで見えなかった工程のムダや課題を明確にし、データに基づいた客観的な改善策の立案を可能にします。
本記事で紹介した成功事例からもわかるように、基幹システムを活用した工程分析は、生産性の向上、コスト削減、品質の安定化といった具体的な効果をもたらし、多品種少量生産を行う中小製造業の競争力強化に大きく貢献します。
もしあなたが、経験と勘に頼る管理から脱却し、データに基づいた科学的なアプローチで生産性向上を目指したいと考えているなら、基幹システムの導入と、それを活用した工程分析こそが、その第一歩となるでしょう。今こそ、基幹システムという新たな武器を手に入れ、あなたの会社の未来を切り拓いてください。