記事公開日:2025.05.28
最終更新日:2025.05.28
AIで実現!納期短縮と高品質、製造業の競争力強化
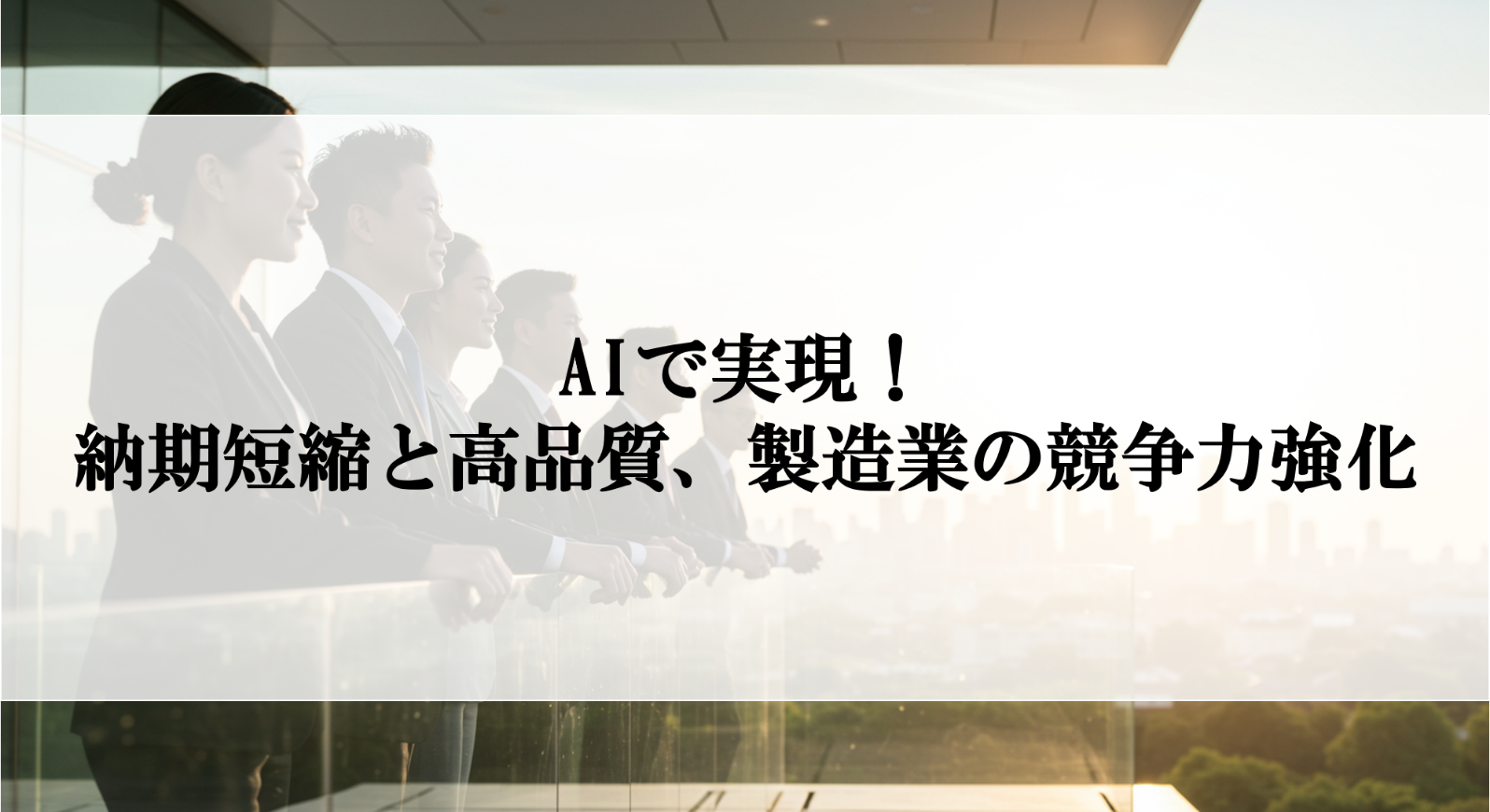
目次
1.「納期短縮」と「高品質」は両立できる!熟練技術への依存から脱却し、競争力を強化する次の一手
1.1.「また納期変更か…」「この精度、ウチのベテランにしか出せないんだよな…」
金型製造の現場では、顧客からの厳しい納期要求と、ますます高度化する品質要求に日々応え続けていらっしゃることと存じます。特に、経験豊富な熟練技術者のノウハウに頼らざるを得ない状況は、技術伝承の難しさや、属人化による生産計画の不安定さを招きかねません。
1.2.その課題、放置していませんか?
- 短納期対応の限界: 熟練技術者の経験と勘に頼った工程では、急な仕様変更やトラブル発生時の対応に遅れが生じ、納期遅延のリスクが高まります。
- 品質のばらつき: 作業者による微妙な感覚の違いが、金型の品質にばらつきを生じさせ、不良率の増加や手戻り作業の発生につながることがあります。
- 技術伝承の断絶: 若手技術者への効果的な技術伝承が進まなければ、将来的に深刻な人材不足に陥り、企業の競争力低下は避けられません。
- コスト競争力の低下: 試作や修正に時間がかかり、歩留まりが上がらなければ、コストは膨らむ一方です。海外企業との価格競争はますます厳しくなっています。
1.3.変化への対応こそ、成長の鍵
「長年培ってきた技術があるから大丈夫」という時代は、終わりを告げようとしています。今こそ、従来のやり方を見直し、新たな技術や考え方を取り入れる勇気が必要です。
例えば、
- 設計プロセスのデジタル化: 3D CAD/CAMの高度活用はもちろん、設計初期段階でのシミュレーション導入により、試作回数の大幅削減と手戻り防止が期待できます。
- 製造工程の見える化と標準化: IoT技術などを活用して加工状況をリアルタイムに把握し、データを分析することで、最適な加工条件の割り出しや、技術の標準化を推進できます。
- 若手でも扱えるツールの導入: AIを活用した設計支援ツールや、自動化された加工機などを導入することで、熟練技術者の負担を軽減しつつ、若手技術者の早期戦力化を図ることが可能です。
これらの取り組みは、単に目の前の課題を解決するだけでなく、貴社の「働き方改革」や「生産性向上」、そして「企業価値向上」へと繋がります。
2.「またこの不良か…」はもう終わりにしたい!樹脂成形不良の根本原因を見抜き、”儲かる工場”へ転換する方法
2.1.「歩留まりがなかなか改善しない…」「不良の原因が特定できず、対策が後手に回っている…」
樹脂加工の現場において、「不良ゼロ」は永遠のテーマかもしれません。しかし、日々の生産に追われる中で、発生した不良への対処療法に終始し、根本的な原因解決に至らないケースは少なくないのではないでしょうか。
2.2.その「小さなロス」が、経営を圧迫していませんか?
- 材料費の無駄: 不良品の発生は、貴重な樹脂材料のロスに直結します。原材料価格が高止まりする中で、この無駄は見過ごせません。
- 生産性の低下: 不良品の選別や手直し作業は、本来の生産時間を奪い、生産効率を著しく低下させます。
- 納期遅延のリスク: 不良の多発は、計画通りの生産を妨げ、最悪の場合、顧客への納期遅延を引き起こし、信頼を損なう可能性があります。
- 品質への不信感: 安定した品質の製品を供給できなければ、顧客からのクレーム増加や取引停止のリスクも高まります。
2.3.「なぜ?」を繰り返す先に、答えがある
不良が発生した際、「成形条件を変えてみよう」「金型を修正してみよう」といった対症療法も重要ですが、それだけでは根本的な解決には至りません。
- 真の原因究明: 「なぜその不良が発生したのか?」を、材料、金型、成形機、作業方法など、多角的な視点から徹底的に掘り下げる必要があります。
- データの活用: 成形条件や品質検査のデータを蓄積・分析し、不良発生の傾向や相関関係を明らかにすることで、科学的根拠に基づいた対策が可能になります。
- 未然防止の仕組みづくり: 不良が発生する前にその兆候を捉え、事前に対策を講じる「予知保全」や「予防保全」の考え方を導入することが理想です。
- 標準化と教育: 最適な成形条件や作業手順を標準化し、作業者全員がそれを遵守できるよう、継続的な教育と訓練を行うことが不可欠です。
3. 多品種少量生産は”脅威”ではない!変化を力に変え、利益を生み出す生産体制構築の秘訣
3.1.「小ロットの注文ばかりで、段取り替えに追われて儲からない…」「顧客の要求が多様化しすぎて、生産計画が立てづらい…」
市場の成熟化や顧客ニーズの多様化により、製造業の現場では「多品種少量生産」への対応が不可避となっています。しかし、この変化を脅威と捉えるか、チャンスと捉えるかで、企業の未来は大きく左右されます。
3.2.従来のやり方では、もう限界かもしれません
- 頻繁な段取り替えによる生産効率の低下: 多品種少量生産では、生産品目を切り替える際の段取り作業が頻繁に発生し、設備の稼働率低下や作業者の負担増を招きます。
- 在庫管理の複雑化とコスト増: 多様な部品や製品の在庫を抱えることは、管理コストの増加やデッドストックのリスクを高めます。
- 熟練技術への依存と対応力の限界: 特定の製品や工程に精通した技術者に頼った生産体制では、急な需要変動や多様な要求への柔軟な対応が難しくなります。
- 情報共有の遅れによる手戻りやミス: 設計変更や仕様変更の情報が製造現場へ迅速かつ正確に伝わらないと、手戻りや不良発生の原因となります。
3.3.変化に強い企業だけが、未来を掴む
多品種少量生産を「儲かる仕組み」に変えるためには、生産体制全体の変革が必要です。
- 生産プロセスの徹底的な「見える化」: 各工程の進捗状況、設備の稼働状況、仕掛品の状況などをリアルタイムに把握することで、ボトルネックの特定や迅速な意思決定が可能になります。
- デジタル技術を活用した「段取り改善」: シミュレーション技術による最適な段取り計画の立案や、段取り作業の標準化・自動化を進めることで、切り替え時間を大幅に短縮できます。
- 柔軟な「生産スケジューリング」: AIなどを活用し、受注状況や納期、設備の空き状況などを考慮した最適な生産計画を自動で立案することで、生産効率と納期遵守率を両立させます。
- 部門間連携を強化する「情報共有基盤」: 設計、製造、検査、購買といった各部門が、リアルタイムに情報を共有し連携できる仕組みを構築することで、リードタイムの短縮と品質向上を実現します。
次回のセミナーでは、多品種少量生産時代を勝ち抜くための具体的な戦略、生産管理システムの最新動向、そして実際に成果を上げている企業の事例などを詳しくご紹介いたします。
貴社の生産現場が抱える課題を解決し、競争優位性を確立するためのヒントをご提供できるものと確信しております。
【このような方にオススメ】
- 多品種少量生産の金型製造、樹脂加工製造業の方
- 次世代若手育成、ノウハウ蓄積に向けて、AIを活用したいと考えている方
- 長年の職人技術に依存した生産体制が続いている方
- 自社のデータを、どのようにAIへ活かせるのかを知りたい方
- 生成AIを知らない・知っているが、製造業ではどのように活用できるのかが分からない方
【本セミナーで学べるポイント】
- 「経営者目線」で知っておくべき製造業で実践できる具体的なAI取組事例が実際の画面をもとに学べる!
AIに関心はあるが、具体的な行動が取れない方のためのセミナーです - 生産技術・生産計画・生産管理にAIを活用して熟練者だけに依存しない取組事例が学べる!
生産技術・生産計画・生産管理部門でどのようにAIが活用できるのかが明確になるセミナーです - AIを活用するためには、具体的に何をすれば良いのかが分かる!
AIには〇〇が必要!そのためには自社で何をすべきなのかが分かります - 多品種少量”だからこそ”今すぐ実践できるAI活用が分かる!
自社にはまだ早い・・・そんな方のためのセミナーです
【第1講座 AI活用基礎:製造業がAI活用できる業務とは?】
- 市場におけるAIの役割・AI動向
- 中小企業だからこそ取り組むべきAI活用戦略
- AIを活用するためには、具体的に何をすれば良いのか?
- 多品種少量生産製造業が実践すべきAI活用他社事例
- AI活用と原価管理の深い関係性
株式会社船井総合研究所 DXコンサルティング部 熊谷俊作
【第2講座 カワイ精工様登壇!従業員26名の社内DX・生成AI活用で年間1,100時間削減】
- DX取り組み前の当時のリアルな課題
- DX取り組み時の苦悩・乗り越え
- 金型カルテ(実績のデジタル化)により、300時間/年削減
- IoT活用!在庫管理自動化により管理工数削減!在庫最適化を実現!
- その他IoT活用による業務改善事例
- RPA活用!部品発注作業を自動化!800時間/年削減
- 製造業における生成AI活用事例
●生成AIシステム実演!
株式会社カワイ精工 専務取締役 川合忠実氏
【第3講座 多品種少量生産製造業が知っておくべきAI・IoT活用戦略】
- 自社データを基盤としたAI活用~”失敗しない”ためのDX経営~
- 多品種少量生産の製造業が取り組むべきAI活用戦略
株式会社船井総合研究所 AI推進室 リーダー 飯塚佳史
関連コラム
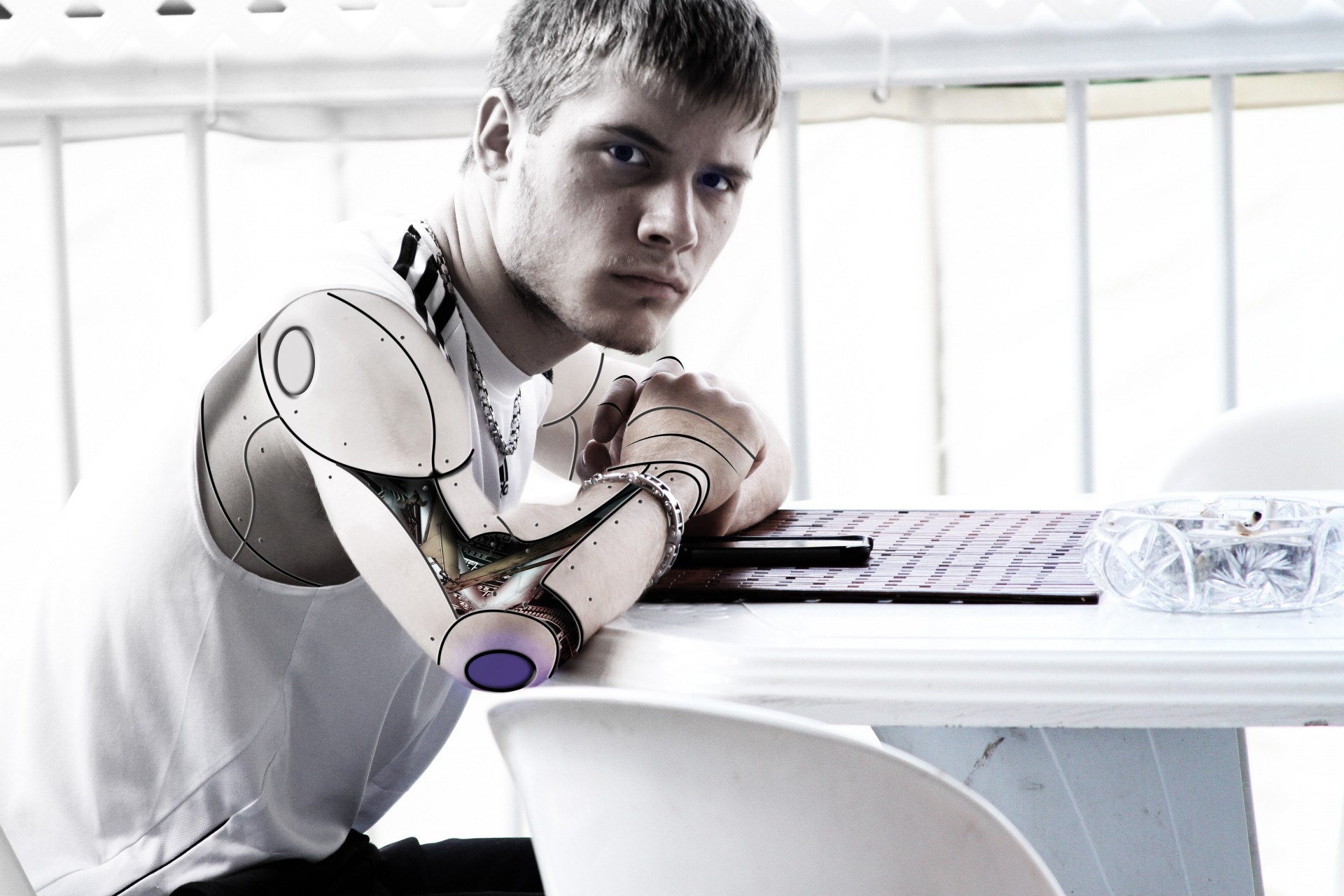
ロボットのティーチングとは?ティーチングの種類と概要を解説
2019.08.27
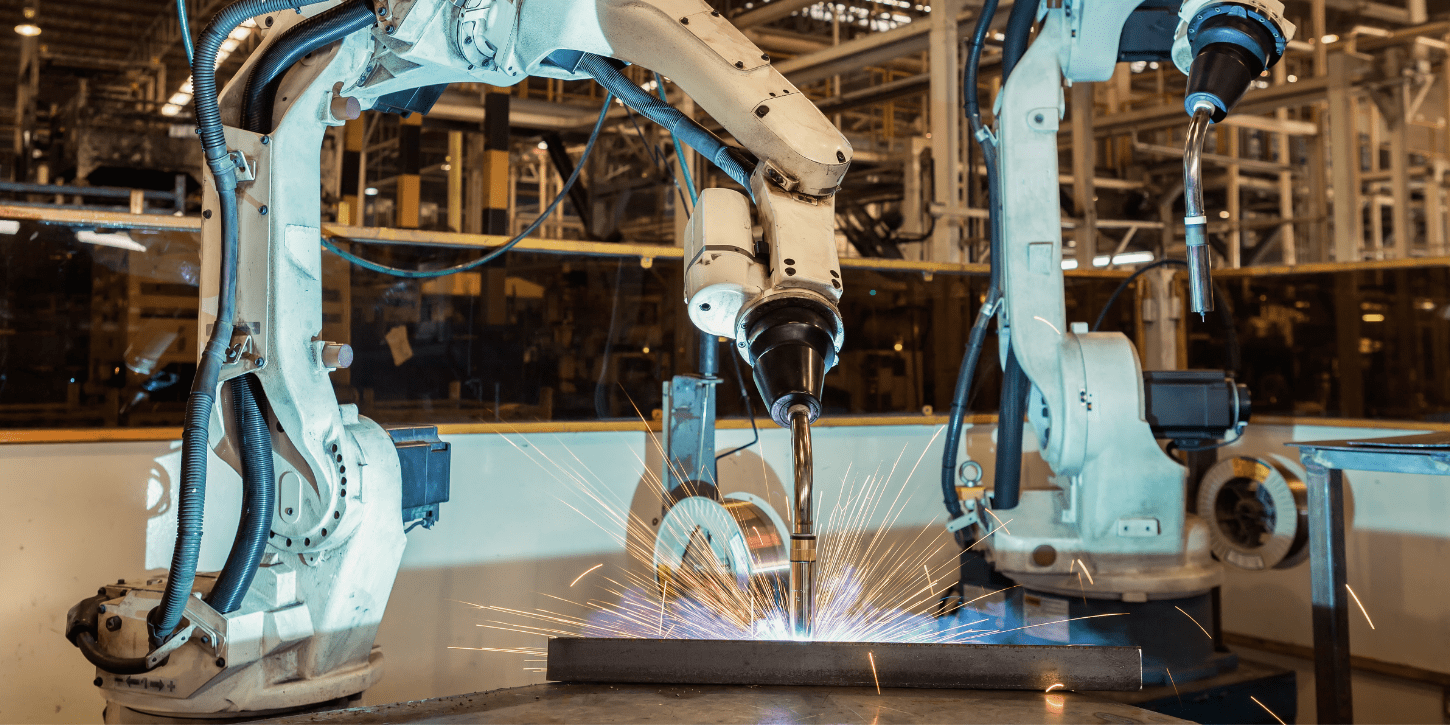
溶接ロボットで行う自動化の方法とは?
2019.08.29
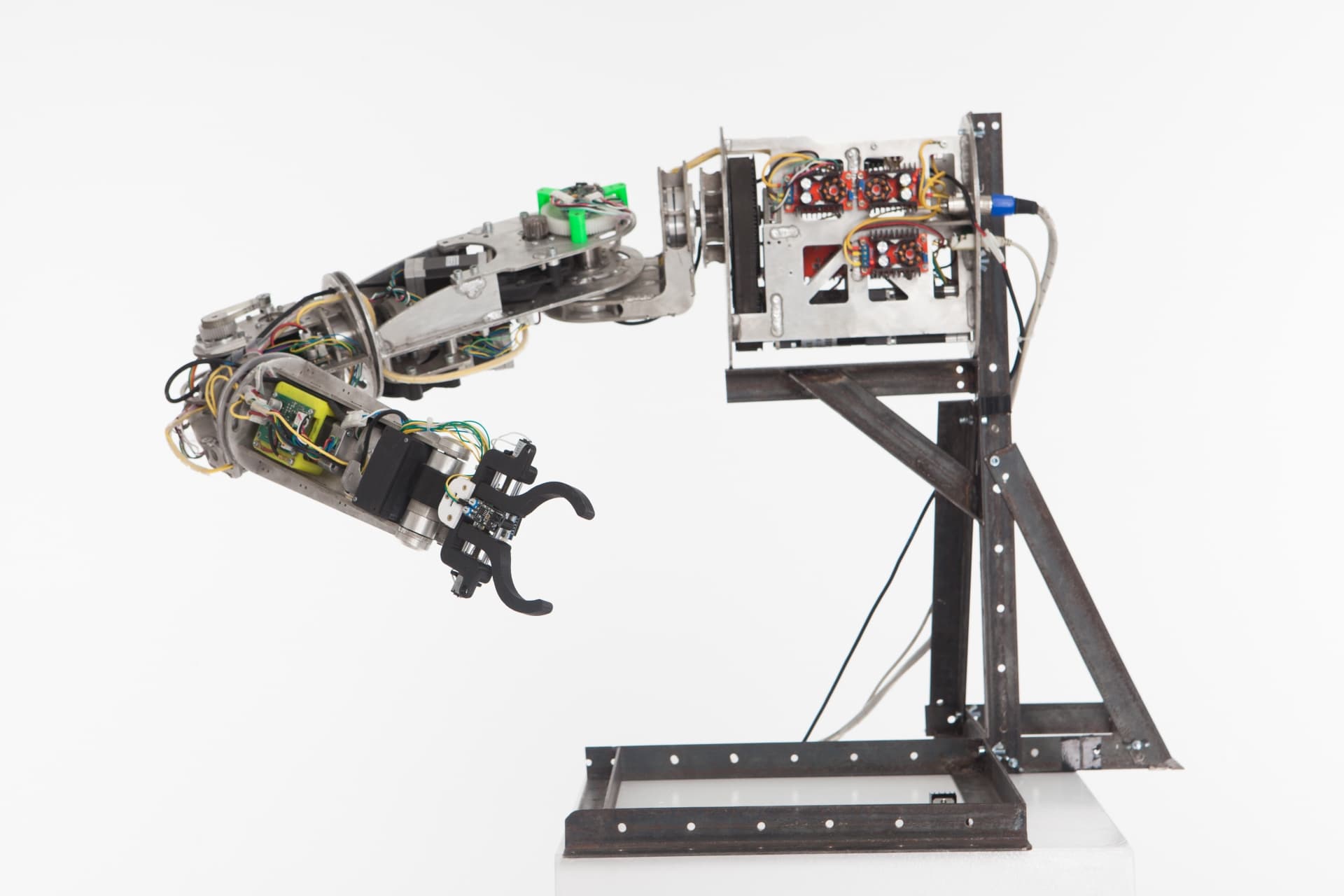
産業用ロボットとは?最新動向からロボットの違いを知る
2019.09.17