記事公開日:2025.07.04
最終更新日:2025.07.07
板金業界の溶接工程を変革する! 協働ロボット活用最前線
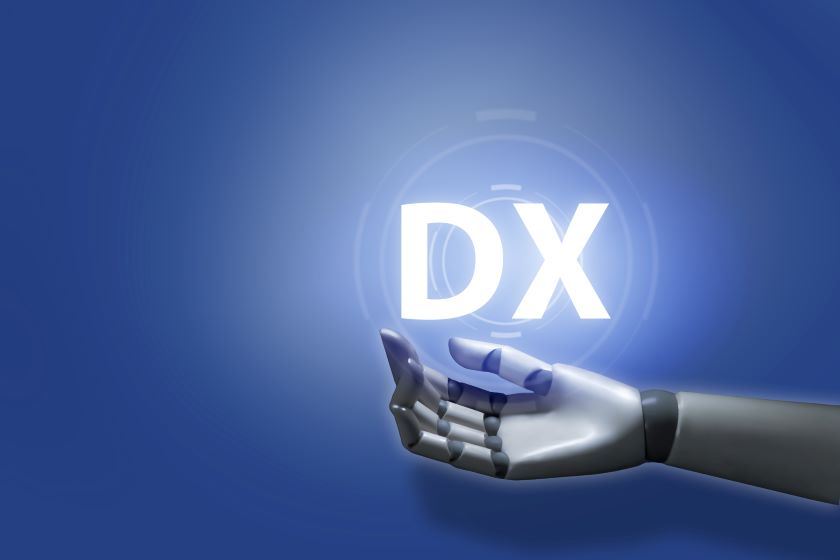
目次
はじめに:人手不足と品質向上の両立を叶える協働ロボット
近年、製造業全体で人手不足が深刻化する中、板金業界も例外ではありません。特に溶接工程においては、熟練技能者の高齢化と若年層の入職者減少により、技術伝承や生産能力の維持が喫緊の課題となっています。一方で、多品種少量生産の増加や短納期化の要求は高まる一方であり、いかにして生産性を向上させつつ、高品質な製品を提供し続けるかが問われています。
このような状況において、注目を集めているのが「協働ロボット」の活用です。協働ロボットは、その名の通り、人と協調して作業を行うことを前提に設計されたロボットであり、従来の産業用ロボットとは一線を画します。安全柵なしで人と同じ空間で作業できるため、限られたスペースでの導入が容易であり、多品種少量生産における段取り替えの頻繁な発生にも柔軟に対応できます。
本コラムでは、板金業界の溶接工程における協働ロボットの具体的な活用事例に焦点を当て、その導入によるメリット、成功のポイント、そして今後の展望について詳しく解説していきます。人手不足の解消、品質の安定化、生産性の向上といった課題を抱える板金加工企業の皆様にとって、本コラムが協働ロボット導入を検討する上での一助となれば幸いです。
溶接工程における協働ロボット導入がもたらす革新
板金加工における溶接工程は、製品の品質を左右する重要な工程でありながら、多くの課題を抱えています。熟練技能者への依存、作業環境の過酷さ、品質のバラつきなどが挙げられますが、協働ロボットの導入はこれらの課題を根本的に解決する可能性を秘めています。
1. 人手不足の解消と生産性の向上
最も顕著なメリットは、人手不足の解消と生産性の向上です。協働ロボットが単純な繰り返し作業や危険を伴う作業を代替することで、熟練技能者はより付加価値の高い作業や、ロボットでは難しい微調整、品質チェックなどに専念できるようになります。
例えば、
- アーク溶接、スポット溶接の自動化: 定型的な溶接作業を協働ロボットが担当することで、24時間稼働も可能となり、生産量を飛躍的に高めることができます。
- 多品種少量生産への対応: 協働ロボットはティーチングが容易であり、段取り替えの時間を短縮できます。これにより、多品種少量生産の現場でも効率的な生産体制を構築できます。
- 残業時間の削減: ロボットが一定の作業量をこなすことで、従業員の残業時間を削減し、労働環境の改善にも寄与します。
2. 品質安定化と不良率の低減
溶接品質は、熟練技能者の腕に左右される部分が大きく、作業者によるバラつきが生じやすいという課題がありました。協働ロボットは、常に一定の品質で溶接作業を行うことが可能です。
- 溶接条件の均一化: ロボットはプログラムされた溶接条件(電流、電圧、速度など)を忠実に再現するため、溶接ビードの形状、深さ、強度が安定します。
- ヒューマンエラーの排除: 人間が行う作業で発生しがちな溶接忘れ、溶接位置のズレ、品質チェックの見落としといったヒューマンエラーを排除できます。
- トレーサビリティの確保: ロボットによる作業データはデジタルで記録されるため、万が一不良が発生した場合でも、原因究明や対策が容易になります。
3. 労働環境の改善と安全性の向上
溶接作業は危険要因が多く、作業者にとって過酷な環境です。協働ロボットは、これらの危険な作業から作業者を解放し、労働環境を劇的に改善します。
- 危険作業の代替: 協働ロボットが危険を伴う溶接作業を行うことで、火傷や感電などのリスクを低減できます。
- 健康被害の軽減: ヒュームや粉じんの発生源に近い作業をロボットが担当することで、作業者の呼吸器系への影響を軽減できます。
- 身体的負担の軽減: 重いワークの持ち運びや、無理な体勢での溶接作業など、身体的負担の大きい作業をロボットが代替することで、作業者の疲労を軽減し、腰痛などの職業病のリスクを低減します。
- 安全柵不要による作業スペースの有効活用: 協働ロボットの安全機能により、従来の産業用ロボットで必要だった大規模な安全柵が不要となる場合が多く、限られた工場スペースを有効活用できます。
溶接工程における協働ロボット活用事例:
それでは、実際に板金業界の溶接工程で協働ロボットがどのように活用されているのでしょうか。
事例1:狭小スペースでの多工程連携溶接
自動車部品の製造工場では、限られたスペース内で複数の加工工程が密接しており、従来の大型ロボットの導入が困難でした。特に、溶接工程ではワークの搬送と溶接作業を連続して行う必要がありました。
【課題】
- 狭い作業スペースでのロボット導入の制約
- ワークの搬送から溶接までの一連の作業を自動化したい
- 人とロボットが安全に共存できる環境の構築
【協働ロボット導入による解決策】
小型の協働ロボットを導入し、既存のラインに組み込みました。ロボットはまず、隣接するプレス機から排出されたワークを把持し、溶接治具にセット。その後、溶接トーチに切り替えて指定された箇所を溶接します。協働ロボットの安全機能により、作業者がロボットの動作範囲内にいても安全に作業ができ、ワークの供給や治具の交換などもスムーズに行われました。
【導入効果】
- 狭小スペースでもロボット自動化を実現し、生産ライン全体の効率が向上。
- ワークの搬送と溶接を連続して行うことで、工程間の滞留時間を削減。
- 作業者は危険なワークの取り扱いから解放され、安全性が向上しました。
事例2:季節変動の大きい製品における手溶接工数の削減
暖房機器メーカーでは、冬場に向けて生産量が急増する製品群があり、その際の溶接工程がボトルネックとなっていました。特に、多くの種類の手溶接作業があり、熟練工への負担が集中していました。
【課題】
- 季節変動による生産量の急増への対応
- 手溶接作業の熟練工への依存と負担集中
- 溶接品質の均一化の難しさ
【協働ロボット導入による解決策】
生産量の変動が大きい主要な溶接箇所に協働ロボットを導入しました。ロボットには、アーク溶接トーチと、ワークの位置ずれを補正するビジョンセンサーを搭載。これにより、簡単なティーチングで多種類の製品の溶接に対応できるようになりました。閑散期には他の作業に協働ロボットを転用することも可能です。
【導入効果】
- 繁忙期の溶接工数を大幅に削減し、生産能力が向上。
- ロボットによる溶接品質の安定化により、不良率が低減。
- 熟練工の負担が軽減され、より高度な溶接や製品開発に時間を割けるようになりました。
事例3:溶接準備・段取り作業の自動化支援
板金加工現場では、溶接作業そのものだけでなく、ワークのセット、治具の準備、溶接ワイヤーの交換など、溶接前後の段取り作業に多くの時間を要していました。これらの作業も人手不足の影響を受けていました。
【課題】
- 溶接前後の段取り作業に時間がかかり、生産効率を低下させている
- 多種多様な治具の交換作業の負担
- 作業者の肉体的負担
【協働ロボット導入による解決策】
協働ロボットにグリッパーと簡単なツールチェンジャー機能を搭載し、治具の自動交換や、ワークの供給・セット作業を支援するシステムを構築しました。作業者はロボットに指示を出すだけで、ロボットが指定された治具を自動でロードし、ワークを所定の位置に正確にセットします。これにより、作業者は本溶接に集中できる環境が整いました。
【導入効果】
- 段取り時間が平均で20%短縮され、実質的な溶接稼働率が向上。
- 作業者の肉体的負担が軽減され、疲労によるミスが減少。
- 生産計画の変更にも柔軟に対応できる体制が構築できました。
協働ロボット導入を成功させるためのポイント
協働ロボットの導入は、単に機械を導入すれば成功するものではありません。いくつかの重要なポイントを押さえることで、その効果を最大限に引き出すことができます。
1. 目的の明確化と現状分析
まず、なぜ協働ロボットを導入するのか、その目的を明確にすることが重要です。「人手不足の解消」「品質向上」「生産性向上」など、具体的な目標を設定します。次に、現状の溶接工程における課題を詳細に分析し、どの工程に協働ロボットを導入することで、最も大きな効果が得られるのかを見極めます。ボトルネックとなっている工程や、安全性に課題のある作業などを特定することが第一歩です。
2. 適切な協働ロボットと周辺設備の選定
市場には様々なメーカーから多種多様な協働ロボットが提供されています。自社の溶接工程の特性に合った協働ロボットを選定することが極めて重要です。
- 可搬重量: 溶接トーチやワイヤー送給装置、場合によってはワーク自体の重量を考慮し、十分な可搬重量を持つロボットを選びます。
- リーチ: 溶接するワークの大きさや、作業スペースを考慮し、適切なリーチ(稼働範囲)を持つロボットを選びます。
- 安全性: 人と協働することを前提としているため、ISO 10218-1やISO/TS 15066などの安全規格に準拠しているか確認が必要です。衝突検知機能や速度制限機能など、安全機能が充実しているかを確認します。
- ティーチングの容易さ: 直感的な操作でティーチングができるユーザーフレンドリーなインターフェースを持つロボットは、導入後の運用負荷を軽減します。
- 周辺機器との連携: 溶接機、治具、センサーなど、既存の設備やこれから導入する周辺機器との連携がスムーズに行えるかを確認します。
また、ロボット本体だけでなく、溶接電源、トーチ、治具、安全センサー、ヒュームコレクター、オフラインティーチングソフトなどの周辺設備の選定も重要です。システム全体として最適な構成を検討しましょう。
3. スモールスタートと段階的導入
いきなり大規模な自動化を目指すのではなく、まずは小規模な範囲で協働ロボットを導入し、効果を検証する「スモールスタート」をお勧めします。
- 簡単な作業から始める: 単純な繰り返し作業や、リスクの低い工程から協働ロボットを導入し、運用ノウハウを蓄積します。
- パイロットラインの設置: 特定の製品やラインで先行導入を行い、そこで得られた知見や課題を、本格導入の際に活かします。
- 段階的な拡張: スモールスタートで成功体験を積んだ後、徐々に適用範囲を広げたり、ロボット台数を増やしたりすることで、リスクを抑えながら導入を進めることができます。
4. 社内体制の構築と人材育成
協働ロボットの導入は、単なる設備の入れ替えではなく、生産体制そのものに変革をもたらします。そのため、社内体制の構築と人材育成が不可欠です。
- 専門チームの編成: ロボット導入の企画から運用、保守までを一貫して担当する専門チームを編成します。
- オペレーターの育成: ロボットの操作、ティーチング、簡単なメンテナンスができるオペレーターを育成します。メーカーや代理店が提供する研修プログラムを活用しましょう。
- 熟練技能者の役割転換: 熟練技能者には、ロボットでは難しい高度な溶接や、品質管理、ロボットのプログラム修正、後進の指導など、より付加価値の高い業務へのシフトを促します。
- 安全教育の徹底: 協働ロボットであっても、安全に関する知識と意識の共有は必須です。関係者全員への安全教育を徹底します。
5. 導入後の継続的な改善
協働ロボットの導入はゴールではありません。導入後も継続的に運用状況をモニタリングし、改善を重ねていくことが重要です。
- 効果測定: 定期的に生産性、品質、コスト、作業者の負担などを測定し、導入効果を数値で把握します。
- データ活用: ロボットの稼働データ、溶接データ、不良データなどを収集・分析し、更なる改善点を発見します。
- フィードバックと改善: 現場からのフィードバックを積極的に取り入れ、ティーチングの改善、治具の改良、周辺設備の最適化などを行います。
- メンテナンス計画: ロボットの定期的なメンテナンス計画を立て、ダウンタイムを最小限に抑えます。
協働ロボット導入の障壁と乗り越え方
協働ロボットの導入には多くのメリットがある一方で、いくつかの障壁も存在します。これらの障壁を理解し、適切に対処することで、導入成功への道を切り開くことができます。
1. 初期投資費用
協働ロボット本体に加え、溶接機、治具、センサー、ソフトウェアなど、初期投資費用は決して小さくありません。特に中小企業にとっては大きな負担となる可能性があります。
【乗り越え方】
- 補助金・助成金の活用: 国や地方自治体、業界団体などが提供する補助金や助成金制度を積極的に活用しましょう。ロボット導入を支援する制度は多数存在します。
- 投資対効果(ROI)の明確化: 協働ロボット導入によって得られる生産性向上、品質改善、コスト削減などの効果を具体的に算出し、投資対効果を経営層に明確に提示することが重要です。
2. 技術的な知識・ノウハウの不足
協働ロボットの操作やプログラミング、システム構築に関する技術的な知識・ノウハウが社内に不足している場合があります。
【乗り越え方】
- メーカー・SIerとの連携: ロボットメーカーやシステムインテグレーター(SIer)は、導入支援から運用、メンテナンスまで一貫したサポートを提供しています。専門家の知見を積極的に活用しましょう。
- 社内研修・教育: 前述の人材育成の項目でも触れましたが、社内での研修プログラムを充実させ、従業員のスキルアップを図ることが重要です。
- 情報収集: 展示会やセミナーへの参加、業界誌、Webサイトなどから最新の技術情報や導入事例を積極的に収集し、自社の参考にします。
3. 従業員の抵抗感
新しい技術の導入は、従業員に「自分の仕事が奪われるのではないか」「操作が難しいのではないか」といった不安や抵抗感を与えることがあります。
【乗り越え方】
- 丁寧な説明と情報共有: 導入の目的やメリット、従業員の役割の変化について、早期から丁寧に説明し、透明性のある情報共有を心がけます。
- 不安の払拭: ロボットはあくまで作業を「代替」するものではなく、「支援」するものであることを強調し、より付加価値の高い仕事へのシフトを促します。
- 参加意識の醸成: 導入プロジェクトに現場の従業員を巻き込み、意見やアイデアを積極的に取り入れることで、当事者意識を高め、抵抗感を軽減できます。
- 成功事例の共有: 導入によって得られた具体的な成果や、従業員の負担が軽減された事例などを共有し、ポジティブなイメージを醸成します。
4. 溶接品質への懸念
特に熟練技能者からは、「人がやった方が早い」「ロボットでは人間の感覚的な調整ができない」「品質が落ちるのではないか」といった懸念の声が上がることがあります。
【乗り越え方】
- スモールスタート:早い段階でロボット導入の効果を体感してもらい、抵抗感を減らしていきます。
- 徹底した事前テストと検証: 導入前に、実際のワークを用いて徹底的な溶接テストを行い、品質を確認します。必要に応じて、溶接条件の最適化や治具の改善を行います。
- 熟練技能者の関与: 熟練技能者の知識や経験をロボットのティーチングやプログラミングに反映させることで、品質に対する懸念を払拭します。ロボットと熟練技能者の「共創」を目指します。
- センサー技術の活用: ビード高さや幅、入熱量などをリアルタイムで監視・制御するセンサー技術を組み合わせることで、溶接品質の安定性をさらに高めることができます。
まとめ:未来の板金溶接現場を創造する協働ロボット
本コラムでは、板金業界の溶接工程における協働ロボットの活用事例とその導入メリット、成功のポイント、そして今後の展望について解説しました。
深刻化する人手不足、高まる品質要求、そして多様化する生産形態に対応するためには、従来のやり方だけでは限界があります。協働ロボットは、熟練技能者の持つ匠の技と、ロボットの持つ高精度・高再現性を融合させることで、これらの課題を解決し、板金業界の溶接工程に新たな価値と競争力をもたらす可能性を秘めています。
協働ロボットの導入は、短期的な視点で見れば投資費用がかかるかもしれません。しかし、長期的な視点で見れば、生産性向上、品質安定化、コスト削減、そして従業員の労働環境改善といった多岐にわたるメリットを享受することができます。
貴社にとって最適な協働ロボットの活用方法を見つけ出し、未来の板金溶接現場を創造していくための一歩を踏み出してみませんか。船井総研は、貴社の状況に応じた最適なロボット導入計画の立案から、実行、導入後のフォローアップまで、トータルでサポートさせていただきます。
ご興味をお持ちいただけましたら、ぜひ一度お問い合わせください。