記事公開日:2025.07.16
最終更新日:2025.08.25
AI外観検査の導入、その投資を無駄にしないための「6つの鉄則」
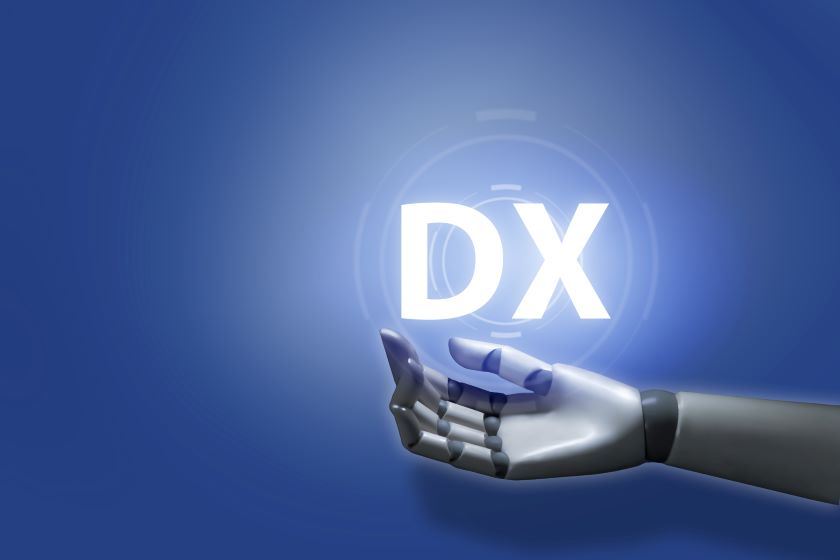
目次
1. はじめに:AI外観検査の成否を分ける「導入プロセス」の重要性
AI(人工知能)技術の発展に伴い、製造業の品質検査工程にAI外観検査を導入する動きが加速しています。人手不足の解消、検査精度の向上、コスト削減といった大きな経営効果が期待される一方で、残念ながら「期待した成果が得られなかった」「高額な投資が無駄になった」という声も少なくありません。
私どもが数多くの製造業の現場をご支援する中で明らかになったのは、成功する企業と失敗する企業の差は、AI技術そのものの優劣よりも、むしろ「導入プロセスの進め方」にあるという厳然たる事実です。
失敗する企業には、いくつかの共通した特徴が見られます。 例えば、「競合が導入したから」といった曖昧な動機でプロジェクトを開始したり 、AIをあたかも魔法の杖のように捉え、その限界を理解しないまま過度な期待を寄せたりします。 また、プロジェクトを特定の担当者に丸投げし、実際にシステムを使用する現場を巻き込まずに進めた結果、実態に合わないシステムが完成してしまうケースも後を絶ちません。 このような無計画な進め方は、多くの場合、実証実験や費用対効果の検証が不十分なまま高額な投資判断へと至り、失敗という結果を招きます。
対照的に、成功を収める企業は、導入プロセスを極めて戦略的に進めます。 まず、「なぜAIを導入するのか」という目的を明確にし、解決すべき課題と期待する効果を具体的な数値で定義します。 その上で、導入の前提となる技術的な実現可能性、特に「欠陥を安定的に撮像できるか」という光学的な検証を徹底的に行います。 さらに、プロジェクトを一部の担当者だけのものとせず、経営層から製造、品質管理といった現場の隅々まで関係者を巻き込み、全社的な協力体制を構築します。 そして、スモールスタートで効果を検証しながら、段階的かつ計画的にプロジェクトを推進し、導入後の運用体制までを確立しているのです。
本コラムでは、この成否を分ける分岐点となる、多くの企業が陥りがちな「6つの罠」と、それを乗り越えるための具体的な「回避策」について、体系的に解説していきます。 AI外観検査導入の成功確率を最大限に高めるための一助となれば幸いです
2. 失敗の罠①②:曖昧な目的と撮像の軽視が招く致命的な過ち
AI外観検査プロジェクトが失敗に至る最初の、そして最も根本的なつまずきは、プロジェクトの根幹を揺るがす「目的の曖昧化」と、技術的な前提を無視した「撮像の軽視」にあります。これら二つの罠は、後続のすべてのプロセスに悪影響を及ぼすため、特に注意が必要です。
【罠1】目的の曖昧化:「とりあえずAI」で高額投資が無駄になる罠
「とりあえずAIで自動化しよう」 「競合他社が導入したから、うちもやらなくては」 このような漠然とした動機からプロジェクトがスタートするケースは、失敗の典型例です。 「何を、どれだけ改善するためにAIを導入するのか」という最も重要な目的が明確でないため、導入するシステムの選定基準も曖昧になり、ベンダーの営業トークに流されてしまいます。 結果として、目的が不明確なままでは投資対効果(ROI)を測定することすらできず 、関係者間の協力も得られず 、最終的に「期待した効果が得られない」 「AIは使えない」といった誤った結論に至る悪循環に陥ります。
この罠を回避する唯一の方法は、「導入目的の数値定義」です。 まず、製造、品質、経営など関係部門を集めてワークショップを実施し、現状の課題を洗い出します。 そして、「品質課題(不良流出による年間損失額)」、「コスト課題(検査工程の人件費総額)」、「生産性課題(検査ボトルネックによる機会損失)」といった項目を、具体的な数値で定量化します。 例えば、「不良流出による年間500万円の損失を100万円以下に抑える」といった明確な数値目標を設定し、文書化することが成功の第一歩です。 この数値目標こそが、投資の判断基準となり、プロジェクトの羅針盤となるのです。
【罠2】撮像の軽視:「AIなら何とかしてくれる」が招くGIGOの罠
「AIは賢いから、人間の目で見てわかる欠陥なら簡単な写真でも認識してくれるだろう」 という考えは、致命的な誤解です。AI外観検査の成否は、AIアルゴリズム以前に「入力される画像の質」でその大半が決まります。これはITの世界で古くから言われる「GIGO(Garbage In, Garbage Out)」、つまり「ゴミを入れればゴミしか出てこない」という原則そのものです。 照明やカメラの性能・設定が不適切で、欠陥が明確に写っていない不鮮明な画像(Garbage In)を入力すれば、どれほど優れたAIを使っても不正確な判定(Garbage Out)しか得られません。 撮像の失敗は、後工程のAI開発や学習への投資をすべて無駄にする根本的な問題なのです。
この罠の回避策は、「徹底的な光学検証」に尽きます。 AI導入プロセスの成否は、「いかにして欠陥を安定して撮像できるか」という導入前の検証にかかっていると言っても過言ではありません。 重要なのは、
専門知識を持つエンジニアと共に、カメラ、レンズ、照明(種類、角度、色など)の無数の組み合わせを体系的にテストし、自社の検査対象物と欠陥に対して最適な「勝ちパターン」を確立することです。 例えば、一般的な正面照明では見えない傷が、照明の角度を変えるだけで劇的に浮かび上がるケースは頻繁にあります。 この「見えない欠陥を見える化する」ための地道なフィジビリティ・スタディこそが、AIの能力を最大限に引き出し、プロジェクトを成功に導く鍵なのです。
3. 失敗の罠③:自社に合わないベンダー選定がもたらす大きな損失
目的を明確化し、撮像の重要性を理解した次に待ち受ける大きな関門が「ベンダー選定」です。ここで犯す誤りは、プロジェクト全体の失敗に直結する極めてリスクの高いものです。
【罠3】ベンダー選定の誤り:「1社の話」を鵜呑みにしてしまう罠
展示会で見たデモが印象的だった、あるいは付き合いのある装置メーカーから勧められた、といった理由だけで、たった1社のベンダーの話だけを聞いて導入を決定してしまう。 これは、非常によく見られる失敗パターンです。当然ながら、そのベンダーは自社製品の長所を雄弁に語りますが、他社製品との客観的な比較情報や、自社製品にとって都合の悪い弱点については決して話しません。
なぜこれが問題なのでしょうか。AIソフトウェアの世界は複雑で、ベンダー各社ごとに提供価値が大きく異なるためです。 1社の話だけでは、これらの違いは決して見抜けません。
具体的には、以下のような違いが存在します。
技術領域の違い: AIソフトウェアのライセンス提供のみを行うベンダーもいれば、撮像システムや搬送装置を含めた検査装置全体を設計・構築できるベンダーもいます。
性能の違い: 特定の種類の欠陥検出には非常に強いが、他の欠陥には弱いなど、ソフトウェアの性能は各社各様です。
ビジネスモデルの違い: 初期費用は安価でも、高額な年間ライセンス費用が毎年発生し、長期的に見てコスト負担が増大するモデルもあれば、買い切り型のモデルもあります。
サポート体制の違い: 導入後の問い合わせや、新たな不良に対する精度改善の相談に、親身かつ迅速に対応してくれるベンダーばかりとは限りません。
これらの違いを理解せずに1社だけの情報で判断を下すことは、自社の真の要件に合わないシステムを選んでしまうリスクを著しく高めます。その結果、期待した性能が出なかったり、想定外のランニングコストに悩まされたり、あるいはトラブル発生時に適切なサポートを受けられなかったりと、プロジェクトが頓挫する原因となります。
この罠を回避するための最適なプロセスは、「多角的かつ客観的なベンダー評価」です。
まず、
評価基準を明確化します。 価格、性能、ビジネスモデル、サポート体制といった項目ごとに、自社が何を重視するのか優先順位をあらかじめ決定しておきます。
次に、複数の候補ベンダーに対し、**同一条件での性能評価(PoC:Proof of Concept / 概念実証)**を実施します。 すべてのベンダーに全く同じサンプル画像セットを提供して検証を依頼し、その結果を比較することで、各社の実力を客観的に評価できます。
さらに有効なのが、
中立的な専門家の活用です。 特定のベンダーに偏らない第三者のコンサルタントは、客観的な視点から各社の長所・短所を評価し、貴社の要件に最も合致するパートナーが誰なのかを的確にアドバイスできます。
これらのステップを経て、数値化された評価結果と専門家の意見を踏まえ、
総合的に評価し最終選定を行う。 このような手間を惜しまない姿勢こそが、自社にとって最適なベンダーを選び出し、導入成功の確率を飛躍的に高めるのです。
4. 失敗の罠④⑤:AIへの過信と関係者の不在が引き起こす現場の混乱
プロジェクトの計画が具体化していく中で、技術と組織の両面にまたがる二重のリスク、「AIへの過信」と「関係者の不在」が顕在化してきます。これらは非現実的な期待と、現場を軽視したプロジェクト推進がもたらすものであり、社内に深刻な不信感と混乱を生む原因となります。
【罠4】AIへの過信:「100%完璧」を求めて現場が混乱する罠
「AIを導入すれば不良品の流出はゼロになる」 「これで検査員は一人もいらなくなる」 といった、AIに対する非現実的な期待は、プロジェクトを頓挫させる典型的な罠です。
なぜなら、現在のAI技術は100%の精度を保証するものではないからです。 学習していない未知の不良を見逃す可能性や、正常な製品を不良と誤判定(過検出)する可能性は常に存在します。 この現実を無視して「完璧」を追求すると、現場からは「AIは使えない」という不信感が増大し、本来であれば達成可能な「検査の99%を自動化する」といった価値ある解決策すらも放棄してしまうことになりかねません。
この罠を回避するには、「現実志向」のアプローチが不可欠です。 まず、PoC(概念実証)を通じて、実データを用いた正確な検出率や誤検出率を把握し、その現実的な性能を関係者全員で共有することが重要です。 その上で、「不良流出を現状の1/10に削減する」といった達成可能な目標を設定します。 そして、AIと人間の協業体制を構築するのです。 大量の定型的な検査はAIが高速で処理し、AIが「疑わしい」と判断したものや、これまでにないパターンのものを人間が最終確認・判断するという役割分担が、最も現実的で効果的な検査体制です。
【罠5】関係者の不在:担当者任せでプロジェクトが形骸化する罠
AI導入を情報システム部門や特定の担当者だけに任せ、「IT部門案件」として他人事のように扱ってしまう。 これもまた、極めて危険な罠です。実際にシステムを使う製造現場や、検査基準を熟知する品質管理部門の意見を聞かずにプロジェクトを進めると、現場の実態に合わない「使えない」システムが完成してしまいます。 また、現場からは「自分たちの仕事が奪われる」という反発や不安を招き、協力が得られなくなることもあります。 結果として、プロジェクトは形骸化し、導入後に担当者が異動すれば誰も触れないシステムと化し、部門間の不信感だけが残ります。
AI導入は単なる「技術導入」ではなく、業務プロセスや組織のあり方を変える「変革プロジェクト」です。 したがって、回避策は「関係者全員の参画」を確保することに尽きます。 プロジェクト開始時に経営層、製造、品質管理、システム部門など、すべての関係者を集めたキックオフミーティングを開催し、目的とゴールを共有することが不可欠です。 経営層は最終判断とリソース確保に責任を持ち、各部門はそれぞれの専門的な立場から要件定義や評価に参加する、明確な推進体制を構築します。 特に、現場の声を引き出す工夫は重要です。定期的なヒアリングの実施や、実際の検査担当者に設計段階からレビューを依頼することで、当事者意識を醸成し、現場の知見を最大限に活用することができます。
5. 失敗の罠⑥と成功への道筋:持続的な成果を生むための運用計画
数々の罠を乗り越え、AI外観検査装置が無事に稼働を開始したとしても、そこで終わりではありません。最後の、そして見過ごされがちな罠が、「導入後の計画の欠如」です。これを乗り越えられて初めて、AI導入は真の成功と言えるのです。
【罠6】計画の欠如:「導入して終わり」でシステムが陳腐化する罠
無事にAI検査装置が稼働したことに満足し、「導入がゴール」となってしまうケース。 これは、導入後の運用体制や継続的な改善計画を全く立てていない場合に起こる罠です。製造現場では、製品の仕様変更や新たな種類の不良など、状況は常に変化します。これらの変化に対応してAIモデルを更新(再学習)する仕組みがなければ、AIの検出精度は時間と共に劣化し、陳腐化していきます。 高額な投資をして導入したシステムが、数年後には誰も使わない置物と化し、「やはりAIは使えなかった」という誤った教訓だけが社内に残ってしまうのです。
この深刻な事態を回避するためには、「導入前に運用・改善計画を立てる」ことが極めて重要です。 AIは導入して完成するものではなく、継続的に運用し、データを蓄積し、再学習させることで賢くなっていく「生き物」です。 この「育て続ける」ための仕組みを、導入前から計画しておく必要があります。
具体的には、以下の二つの計画を定義します。
運用体制の定義: システムを誰が日常的に監視し、AIが検出したデータの傾向を誰が分析するのか。新たな不良が見つかった際に、AIの再学習(追加学習)を実施する担当者は誰で、その際の最終的な判断は誰が下すのか。こうした具体的な役割分担を明確に定めておく必要があります。
改善サイクルの構築: 新たな不良品が見つかったり、過検出が多発したりした場合に、どのようにデータを収集し、AIに追加学習させるかという一連のプロセスをルール化します。 「運用 → データ収集 → 再学習 → 精度向上」という継続的な改善サイクルを回すことで、AIは変化に対応し、その価値を持続的に高めていくことができます。
成功への道筋:6つの罠を乗り越えるために
本コラムで解説してきた6つの罠を乗り越え、AI外観検査で真の成果を創出するためには、以下の6つの鉄則を確実に実行することが不可欠です。
目的を明確化する: 「とりあえず」ではなく、「年間〇〇万円の損失削減」など、導入目的を具体的な数値で定義します。
撮像検証を徹底する: AIの性能は画像で決まります。欠陥を確実に「見える化」する光学システムの構築に、労を惜しまないでください。
複数ベンダーを比較する: 1社の話を鵜呑みにせず、同一条件での評価と中立的な専門家の意見を活用し、最適なパートナーを選定します。
AIの限界を理解する: 「100%完璧」は求めず、現実的な目標を設定し、人間との適切な協業体制を構築します。
全関係者を巻き込む: 担当者任せにせず、初期段階から経営層、現場、管理部門すべての参画を確保します。
運用・改善計画を立てる: 導入をゴールとせず、AIを「育て続ける」ための運用体制と改善サイクルを確立します。
これらのポイントを事前に理解し、一つひとつ着実に対策すれば、AI外観検査導入の成功確率は劇的に高まることをお約束します。
このコラムを読んだ後に取るべき行動
本コラムを通じて、AI外観検査導入における課題や成功への道筋について、ご理解いただけたことと存じます。次のステップとして、貴社が抱える具体的な課題を整理し、専門家と共に解決策を検討されることをお勧めします。
株式会社船井総合研究所では、AI外観検査導入に関する貴社の具体的な課題や不安点について、専門コンサルタントが個別にアドバイスさせていただく「無料個別相談」を承っております。
「自社のこの検査工程はAI化できるのか?」
「投資対効果の具体的な試算を手伝ってほしい」
「ベンダー選定の客観的なアドバイスが欲しい」
といった、どのようなご相談でも構いません。貴社の貴重な経営資源を無駄にすることなく、品質向上やコスト削減といった成果を最短距離で実現するための一助となれれば幸いです。
https://formslp.funaisoken.co.jp/form01/lp/post/inquiry-S045.html?siteno=S045&_gl=1*a9eoti*_gcl_au*MTQxOTg2OTc5LjE3NDg0MDQ4OTA.*_ga*MTQwMzYyNzIxNC4xNzAxMTQ4MzQz*_ga_D8HCS71KCM*czE3NTI2MjU5NjgkbzQ1OCRnMSR0MTc1MjYyNzAyMCRqNjAkbDAkaDA.
【お電話でのお問い合わせ】
フリーダイヤル: 0120-958-270
受付時間:平日 9時45分~17時30分(土日祝、年末年始を除く)
【無料ダウンロード】AI外観検査導入で陥りがちな6つの罠とその回避策
https://www.funaisoken.co.jp/dl-contents/smart-factory_smart-factory_00000389_S045?media=smart-factory_S045
【レポートの内容】
多くの製造業で注目されるAI外観検査ですが、「とりあえず導入したものの、期待した効果が出ない」という声が後を絶ちません。実は、その成否を分けるのはAI技術の優劣ではなく、多くの場合「導入プロセスの進め方」にあります。
本レポートでは、私ども船井総合研究所が数多くのご支援を通じて見てきた、AI外観検査の導入プロジェクトで陥りがちな「6つの罠」を徹底的に解説します。具体的には、「目的の曖昧化」 、「撮像の軽視」 、「ベンダー選定の誤り」 、「AIへの過信」 といった、多くの企業が経験する典型的な失敗パターンを挙げ、なぜその問題が起きるのか、根本原因から明らかにします。その上で、各々の罠に対して、具体的な回避策を専門コンサルタントの視点からご提案します。AIを活用した外観検査で確実に成果を出すための、実践的なノウハウが詰まった一冊です。
【このレポートを読むメリット】
AI外観検査への投資を、””博打””ではなく””確実な一手””に変えるための具体的な知見が手に入ります。
本レポートをお読みいただくことで、まず、高額な投資が無駄になるリスクを大幅に軽減できます。AI外観検査でありがちな失敗パターンを事前に学ぶことで、「AIは使えなかった」という最悪の結末を回避し、成功への道筋を明確に描くことが可能です。
次に、「何から始め、何を、いつまでに、どう判断すべきか」という導入のロードマップが手に入ります 。これにより、担当者任せにすることなく、経営者様ご自身がプロジェクトを主導し、関係各所に対して説得力のある導入計画を策定・推進できるようになります。
さらに、導入成功の先にある「成果の最大化」まで見据えています。不良流出率の低減といった品質向上はもちろん、検査工数の削減によるコスト削減、ひいては従業員を単純作業から解放し、より付加価値の高い業務へシフトさせる、といった本質的な生産性向上を実現するためのヒントを得られます。