記事公開日:2025.07.17
最終更新日:2025.07.17
金属加工業の生産性革命! マシニングセンター・旋盤への協働ロボット導入事例
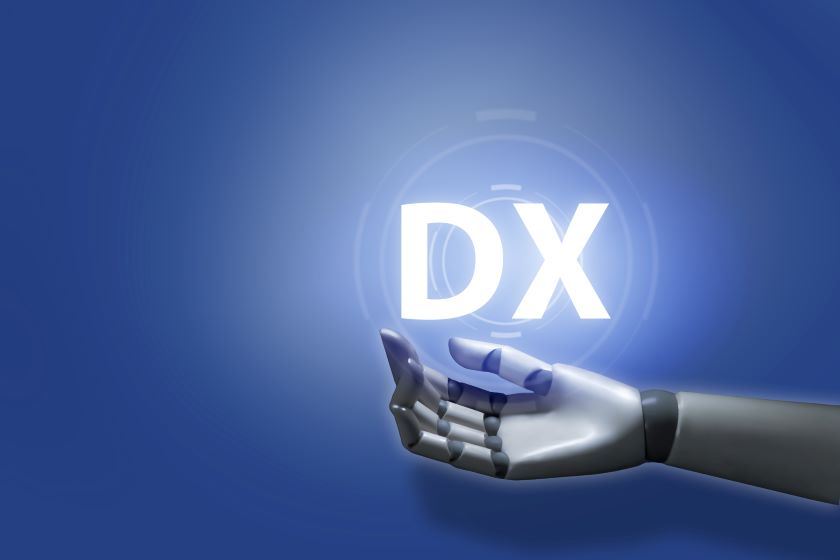
目次
はじめに:なぜ今、金属加工業に協働ロボットが求められるのか
日本の製造業、特に金属加工分野は、長年培ってきた高い技術力で世界をリードしてきました。しかし、近年はグローバルな競争激化、多品種少量生産への移行、そして何よりも深刻な人手不足という三重苦に直面しています。熟練技能者の高齢化と若年層の入職者減少は、多くの現場で技術継承や生産能力の維持を困難にしています。
このような状況において、高価なマシニングセンターや旋盤といった加工機が持つ本来の性能を最大限に引き出せていないという課題が浮き彫りになっています。ワークの投入・取出し作業が人手に頼っているため、機械が停止し稼働率が低下、24時間稼働が難しい、残業時間が増えるなど上げれば切りがありません。
この課題を解決し、金属加工業の未来を拓く鍵として注目されているのが「協働ロボット」です。協働ロボットは、人と共に働くことを前提に開発されており、従来の産業用ロボットのような大掛かりな安全柵が不要な場合が多く、既存の設備にも比較的容易に導入できるのが特長です。
本コラムでは、金属加工業のワーク投入・取出し工程における協働ロボットの具体的な活用事例を、船井総研のコンサルタントの視点から詳しく解説します。導入によるメリット、成功のポイント、そして今後の展望について触れ、貴社の生産性向上、品質安定化、そして働き方改革の一助となれば幸いです。
ワーク投入・取出し工程が抱える課題と協働ロボット導入の必然性
マシニングセンターや旋盤におけるワークの投入・取出し作業は、一見単純な作業に見えますが、実は多くの課題を抱えています。
金属加工現場の主な課題
- 非効率な作業と生産性の限界:
- ワークの投入・取出し作業は、作業者が機械のそばに張り付く必要があり、他の付加価値の高い業務(プログラミング、段取り替え、品質検査など)に時間を割くことができません。
- 作業者の休憩や交代により、機械が停止する時間が生まれ、設備の稼働率が低下します。
- 人手による身体的負担と安全リスク:
- ワークは重いものも多く、繰り返し持ち運ぶことで作業者の腰や腕に大きな負担がかかります。
- 重いワークの落下や、稼働中の機械との接触など、潜在的な安全リスクが常に存在します。
- 品質のバラつきと不良発生リスク:
- ワークのセッティングが人手で行われるため、わずかな位置ずれや締め付けのバラつきが発生する可能性があります。
- ワークの取り扱いにばらつきが出ると、製品に傷がついたり、品質が安定しなかったりする原因となります。
- 人手不足と技術継承の難しさ:
- 単純反復作業でありながら、身体的な負担が大きいワーク投入・取出し作業は、若年層が敬遠しがちです。
- 熟練オペレーターは、貴重なノウハウを伝承する時間がないまま、定年を迎えるケースが増えています。
これらの課題は、中小の金属加工業者にとって、生産性向上と競争力強化を阻む大きな壁となっています。ここで協働ロボットを導入することは、単なる自動化に留まらず、これらの課題を根本的に解決し、製造現場に変革をもたらす「必然性」があると言えるでしょう。
協働ロボット導入がもたらす革新
協働ロボットは、その特性からワーク投入・取出し工程に以下のような革新をもたらします。
- 稼働率の飛躍的向上:
- ロボットは休憩や残業なく24時間稼働できるため、加工機のアイドルタイムを削減し、稼働率を最大化します。
- これにより、生産量を大幅に増加させることが可能になります。
- 品質の安定化:
- プログラムされた通りにワークを正確に把持・セットするため、位置ずれや締め付けのバラつきがなくなり、品質が均一化します。
- ワークへの傷や汚れのリスクも軽減されます。
- 作業環境の改善と安全性向上:
- ロボットが重いワークの搬送や危険な作業を代替することで、作業者の身体的負担を大幅に軽減し、労働災害のリスクを低減します。
- 作業者はロボットの隣で、プログラミングや品質検査といったより付加価値の高い業務に集中できるようになります。
- 生産体制の柔軟化:
- 多品種少量生産においても、協働ロボットはティーチングが容易なため、段取り替え時間を短縮できます。
- 熟練オペレーターは、ロボットの運用管理や、ロボットでは難しい微細加工、複雑な加工プログラムの作成など、より専門的な業務に専念できます。
ワーク投入・取出しにおける協働ロボット活用事例:具体的なシナリオ
それでは、実際に協働ロボットがどのようにワーク投入・取出し工程で活用されているのか、具体的な事例をいくつかご紹介します。
事例1:多品種少量生産に対応するマシニングセンターへの導入
多品種少量生産を行っているA社では、製品が変わるたびにワークの投入・取出し作業を人が行う必要があり、頻繁な段取り替えが生産性向上の妨げとなっていました。
【課題】
- 製品ごとに異なるワークの投入・取出しに時間がかかる
- 手作業によるワークのセッティング位置のばらつきが発生
- 作業者の負担が大きく、生産効率が上がらない
【協働ロボット導入による解決策】 協働ロボットに、複数のワークに対応できる汎用性の高いグリッパーや、必要に応じて工具を交換するツールチェンジャーを装着しました。ワークは治具に固定せず、ロボットがビジョンシステムで認識し、位置を自動補正しながら把持。マシニングセンターの扉を自動で開閉し、ワークを正確にチャックにセットします。加工完了後も、ロボットが自動でワークを取り出し、次のワークをセットします。作業者は、事前にワークが並べられたトレイを交換するだけで済みます。
【導入効果】
- 段取り替え時間が大幅に短縮され、多品種少量生産への対応力が向上。
- ロボットによるワークの正確なセッティングで、不良率が低減し、品質が安定。
- 作業者は単純作業から解放され、マシニングセンターを複数台管理したり、プログラミングを行ったりできるようになりました。
事例2:旋盤加工における24時間無人稼働の実現
自動車部品のシャフトなど、円筒形のワークを旋盤で大量生産しているB社では、ワークの投入・取出し作業が生産のボトルネックとなっていました。特に夜間や休日も機械を稼働させたいというニーズが高まっていました。
【課題】
- ワーク投入・取出しの反復作業が重労働
- 夜間や休日の無人稼働ができない
- 生産量の増加要求に応えきれない
【協働ロボット導入による解決策】 旋盤の隣に協働ロボットを設置し、専用のワーク供給システムと連携させました。ロボットは、供給システムから生材(加工前のワーク)を一つずつ取り出し、旋盤のチャックに正確にセットします。加工が完了すると、ロボットがチャックから製品を取り出し、完成品を排出します。協働ロボットは旋盤の制御盤と通信し、加工機の稼働状況に合わせて安全に動作します。
【導入効果】
- 24時間体制での無人稼働が実現し、設備の稼働率が劇的に向上。
- 生産量が2倍に増加し、短納期化やコスト削減に貢献。
- 作業者は夜勤から解放され、働き方改革が進みました。
事例3:ワークの搬送と同時に品質検査も行う多機能化
加工後のワークに傷がないか、寸法が規定内かといった簡易的な品質検査も、オペレーターの重要な業務です。しかし、この検査に多くの時間を要し、作業の効率を下げていました。
【課題】
- ワークの投入・取出しに加えて品質検査も手作業で行う必要がある
- 検査の精度が作業者の経験や疲労に左右される
- 単純な検査作業でオペレーターの時間が奪われている
【協働ロボット導入による解決策】 協働ロボットに、ワークの投入・取出し用グリッパーに加え、ビジョンセンサーや簡単な検査ツール(エアーマイクロメーターなど)を搭載しました。ロボットは加工後のワークを取り出すと、事前に設定された位置でビジョンセンサーによる外観検査や、検査ツールによる寸法チェックを自動で行います。検査結果に応じて、ワークを「良品トレイ」または「不良品トレイ」に仕分けします。
【導入効果】
- ワークの投入・取出しと品質検査を同時に自動化でき、大幅な時間短縮を実現。
- 検査精度が均一化され、ヒューマンエラーによる不良品の見逃しが減少。
- オペレーターは、より複雑な検査や不良原因の究明といった、専門性の高い業務に集中できるようになりました。
事例4:複数の機械を1台の協働ロボットで管理
工場レイアウトの制約上、複数の異なる加工機が近接して配置されており、それぞれの機械にオペレーターを配置する必要がありました。この非効率な人員配置がコスト増の要因となっていました。
【課題】
- 複数の加工機にオペレーターが分散し、人員配置が非効率
- 工場の限られたスペースを有効活用したい
- 少人数で複数台の機械を管理したい
【協働ロボット導入による解決策】 可搬重量とリーチ(稼働範囲)の大きい協働ロボットを1台導入し、複数のマシニングセンターや旋盤の間に配置しました。ロボットはツールチェンジャーで異なる種類のグリッパーを使い分け、複数の機械のワーク投入・取出しを順次行います。作業者は、ロボットの監視と、各機械の段取り替えを順次行うだけで済み、1人で複数の機械を管理できる体制を構築しました。
【導入効果】
- 1人のオペレーターが複数の機械を管理できる「ワンオペレーション」が実現し、生産コストを削減。
- 工場スペースが有効活用され、生産効率が向上。
- 生産計画の変更にも柔軟に対応できる体制が構築できました。
協働ロボット導入を成功させるためのポイント
協働ロボットの導入は、単に機械を導入すれば成功するものではありません。特に中小の金属加工業の皆様がその効果を最大限に引き出すためには、いくつかの重要なポイントを押さえる必要があります。
1. 目的の明確化とスモールスタート
まず、なぜ協働ロボットを導入するのか、その目的を明確にすることが極めて重要です。「人手不足の解消」「品質向上」「稼働率向上」など、具体的な目標を設定します。そして、いきなり全てを自動化しようとせず、最も負担が大きい、あるいは効果が見えやすい一つの作業(例:単純なワークの投入・取出し)から自動化を試みるスモールスタートをお勧めします。
2. 適切な協働ロボットと周辺設備の選定
市場には様々なメーカーから多種多様な協働ロボットが提供されています。自社のワークや加工機に合った協働ロボットと周辺設備を選定することが成功の鍵です。
- 可搬重量: ワークやグリッパーの重量を考慮し、十分な可搬重量を持つロボットを選びます。
- リーチ: ワークの大きさや、機械の配置を考慮し、適切なリーチ(稼働範囲)を持つロボットを選びます。
- ティーチングの容易さ: 直感的な操作でティーチングができるユーザーフレンドリーなインターフェースを持つロボットは、導入後の運用負荷を軽減します。手で直接ロボットを動かしてティーチングできる機能があると非常に便利です。
- 周辺機器との連携: 加工機、治具、ワーク供給システムなど、既存の設備やこれから導入する周辺機器との連携がスムーズに行えるかを確認します。システム全体として最適な構成を検討しましょう。
3. 熟練工の「役割転換」を促す社内体制の構築
協働ロボットの導入は、単なる設備の入れ替えではなく、生産体制そのものに変革をもたらします。そのため、社内体制の構築と人材育成が不可欠です。
- 熟練技能者の役割転換: 熟練オペレーターには、ロボットでは難しい多面加工や、品質管理、ロボットのプログラム修正、後進の指導など、より付加価値の高い業務へのシフトを促します。彼らの経験と知見が、ロボットシステムの最適化に不可欠です。
- 安全教育の徹底: 協働ロボットであっても、人と機械が共存する環境では安全に関する知識と意識の共有は必須です。関係者全員への安全教育を徹底し、リスクアセスメントを定期的に実施しましょう。
4. 導入後の継続的な改善と補助金の活用
協働ロボットの導入はゴールではありません。導入後も継続的に運用状況をモニタリングし、改善を重ねていくことが重要です。また、初期投資の負担を軽減するため、国や地方自治体が提供する補助金・助成金制度を積極的に活用しましょう。
まとめ:金属加工業の持続的成長のために
本コラムでは、金属加工業のワーク投入・取出し工程における協働ロボットの活用事例とその導入メリット、成功のポイント、そして今後の展望について解説しました。
深刻化する人手不足、高まる品質要求、そして多様化する生産形態に対応するためには、従来のやり方だけでは限界があります。協働ロボットは、これらの課題を解決し、貴社の競争力を強化し、持続的な成長を可能にするための強力なツールとなりえます。
協働ロボットの導入は、短期的な視点で見れば投資費用がかかるかもしれません。しかし、長期的な視点で見れば、生産性向上、品質安定化、コスト削減、そして従業員の労働環境改善といった多岐にわたるメリットを享受することができます。特に、従業員が単純作業から解放され、より付加価値の高い業務に集中できることは、企業の組織力強化にも繋がります。
貴社にとって最適な協働ロボットの活用方法を見つけ出し、未来の製造現場を創造していくための一歩を踏み出してみませんか。船井総研は、貴社の状況に応じた最適なロボット導入計画の立案から、実行、導入後のフォローアップまで、トータルでサポートさせていただきます。
ご興味をお持ちいただけましたら、ぜひ一度お問い合わせください。貴社の課題解決、そして企業価値向上に貢献できることを楽しみにしております。