記事公開日:2019.06.19
最終更新日:2022.12.14
地場産業の素材加工工程にロボット導入
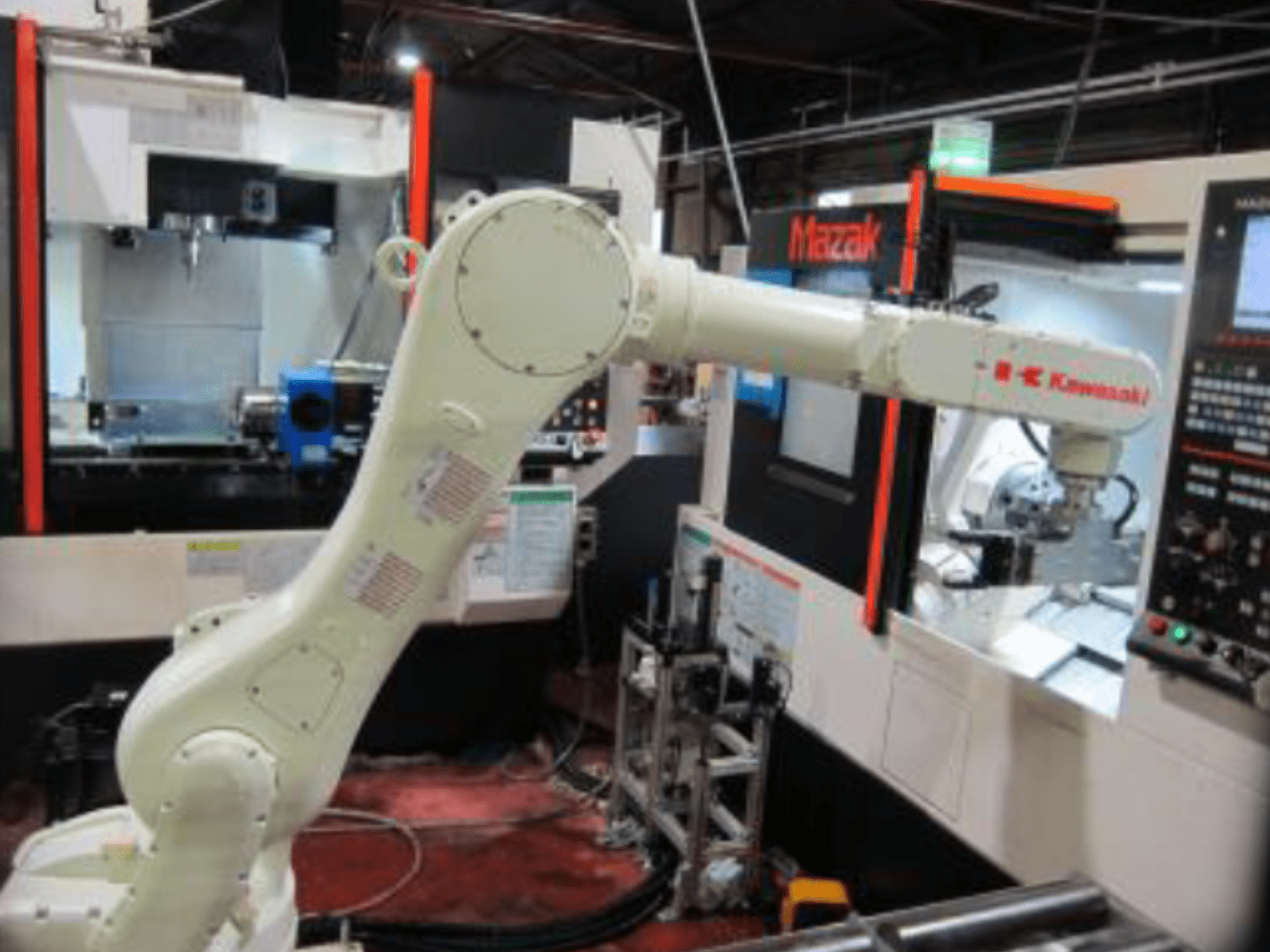
この事例におけるロボット化によるメリット
□ ロボット導入による省人化・省力化
□ ロボット導入での生産性向上
□ 職人不足の中の労働力補填
当社の課題
地元の地場産業業界では職人の高齢化や少子化により、生産人材不足が慢性化しており、自社の生産稼動も非常に不安定な状態でした。
こうした時代の変化に対応する必要性の高まりから、地場産業を維持・発展させていく取組みとして、ロボット導入を行いました。
ロボットを導入した工程
ワークの複数台の加工機への投入と工程間の搬送
ポイント
導入前の対象生産ラインは各加工工程が離れており、ワークの搬送を手作業によって行っていました。
ロボット導入を実施するに際し、従来の加工工程を見直し、ロボットがあるからこそ可能な工程内容・レイアウトに更新し、ワークの搬送をロボットで行うことで、設備の無人稼動化に取り組みました。
ロボット導入により、人員の削減、生産性の向上、専有スペースの削減を実現できました。
ただ、完全無人稼動のためには計測システムの計測方法や切粉処理について改善する必要があります。
ーーーーーーーーーーーーーーーーーーーーーーーーーーーーーーーーーー
NC旋盤・切削加工業様向け NC旋盤スマートロボットシステム導入解説レポート
この一冊でNC旋盤スマートロボットシステムの導入フローがわかる!
①NC旋盤スマートロボットシステム初めてのロボット導入の進め方
②スマートロボットシステム6つの強み
③補助金を活用した機械加工設備向けロボット導入成功事例
ーーーーーーーーーーーーーーーーーーーーーーーーーーーーーーーーーー
関連コラム
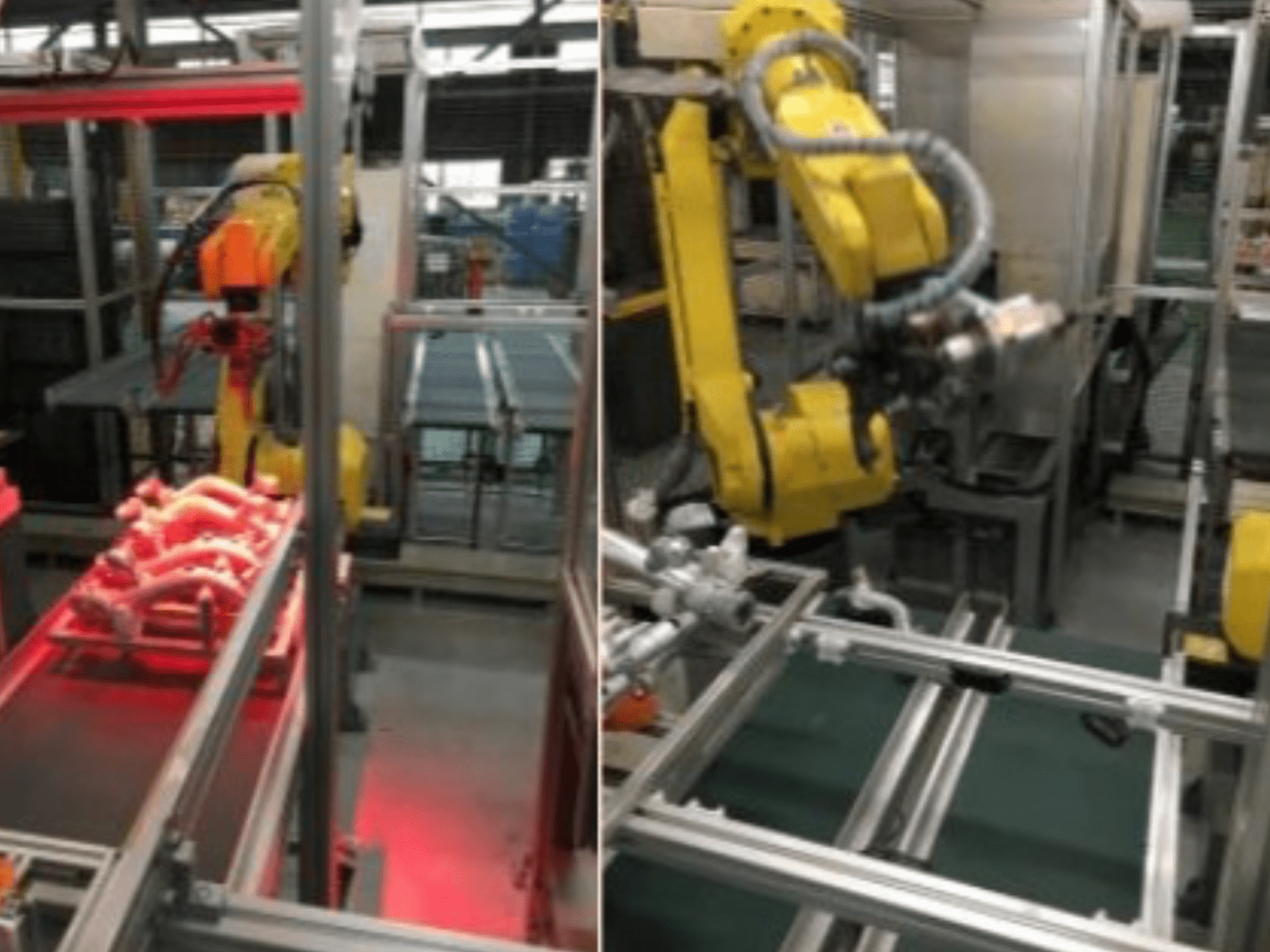
アルミ鋳造ラインの仕上げ作業にロボットを導入
2019.06.25
企業情報
業種:非鉄金属鋳物製造業
従業員数:31人
エリア:群馬県
この事例におけるロボット化によるメリット
□ ロボット導入による省人化・省力化
□ ロボット導入での生産性向上
□ ロボットによる危険作業の代替
当社の課題
アルミ製品の鋳バリは、金型の老朽化等で多く発生します。付加価値を産み出さない工程ながら、手作業で実施する必要があったため、粉塵など従業員への安全面での懸念も多く、自動化が求められる環境でした。
ロボットを導入した工程
押し湯と呼ばれる不要部品や、主に外周部に発生する鋳バリを除去する工程
ポイント
自動化の内容は下記のようになります。
①ベルトコンベアでランダムに流れてくる製品をビジョンカメラで撮影
②ビジョンに基づき、製品の種類や向きなどを自動判定し、作業開始する
③ロボットにより押し湯の切断、外周部のバリ取りを実施
④製品コンベアへ排出する
設置後のトライアルの結果、仕上げ作業で3名の人員が閣下っていましたが、2名分をロボットで自動化することができました。
ビジョンカメラを使用した製品・向きの判定を積極的に採用した事で、少量多品種型の生産体系であっても、ロボットシステムが人手での作業に劣る事の無い結果を出す事に成功しました。
※一般社団法人 日本ロボット工業会(JARA)「ロボット導入実証事業:事例紹介ハンドブック2016 」より
概要
本事例集は、全国の先進的な工場が取り組む「自動化・ロボット化」の事例をまとめたものとなります。
これから自動化・ロボット化に取組もうと考える皆さまに、
「町工場にロボット・IoTを導入する」ための具体的なノウハウを、
事例を通して知っていただくことを目的に作成しました。
以下のフォームボタンより、必要事項を入力し送信ください。
2〜3営業日以内に担当者より事例集を送付いたします。
事例集を申し込む
【ご確認ください】
こちらの事例集は、導入を検討している工場の担当者様限定となっております。
同業他社、メーカーや商社、SI事業者の方にはご送付をお断りする場合がございます。 企業情報
業種:非鉄金属鋳物製造業
従業員数:31人
エリア:群馬県
この事例におけるロボット化によるメリット
□ ロボット導入による省人化・省力化
□ ロボット導入での生産性向上
□ ロボットによる危険作業の代替
当社の課題
アルミ製品の鋳バリは、金型の老朽化等で多く発生します。付加価値を産み出さない工程ながら、手作業で実施する必要があったため、粉塵など従業員への安全面での懸念も多く、自動化が求められる環境でした。
ロボットを導入した工程
押し湯と呼ばれる不要部品や、主に外周部に発生する鋳バリを除去する工程
ポイント
自動化の内容は下記のようになります。
①ベルトコンベアでランダムに流れてくる製品をビジョンカメラで撮影
②ビジョンに基づき、製品の種類や向きなどを自動判定し、作業開始する
③ロボットにより押し湯の切断、外周部のバリ取りを実施
④製品コンベアへ排出する
設置後のトライアルの結果、仕上げ作業で3名の人員が閣下っていましたが、2名分をロボットで自動化することができました。
ビジョンカメラを使用した製品・向きの判定を積極的に採用した事で、少量多品種型の生産体系であっても、ロボットシステムが人手での作業に劣る事の無い結果を出す事に成功しました。
※一般社団法人 日本ロボット工業会(JARA)「ロボット導入実証事業:事例紹介ハンドブック2016 」より
概要
本事例集は、全国の先進的な工場が取り組む「自動化・ロボット化」の事例をまとめたものとなります。
これから自動化・ロボット化に取組もうと考える皆さまに、
「町工場にロボット・IoTを導入する」ための具体的なノウハウを、
事例を通して知っていただくことを目的に作成しました。
以下のフォームボタンより、必要事項を入力し送信ください。
2〜3営業日以内に担当者より事例集を送付いたします。
事例集を申し込む
【ご確認ください】
こちらの事例集は、導入を検討している工場の担当者様限定となっております。
同業他社、メーカーや商社、SI事業者の方にはご送付をお断りする場合がございます。
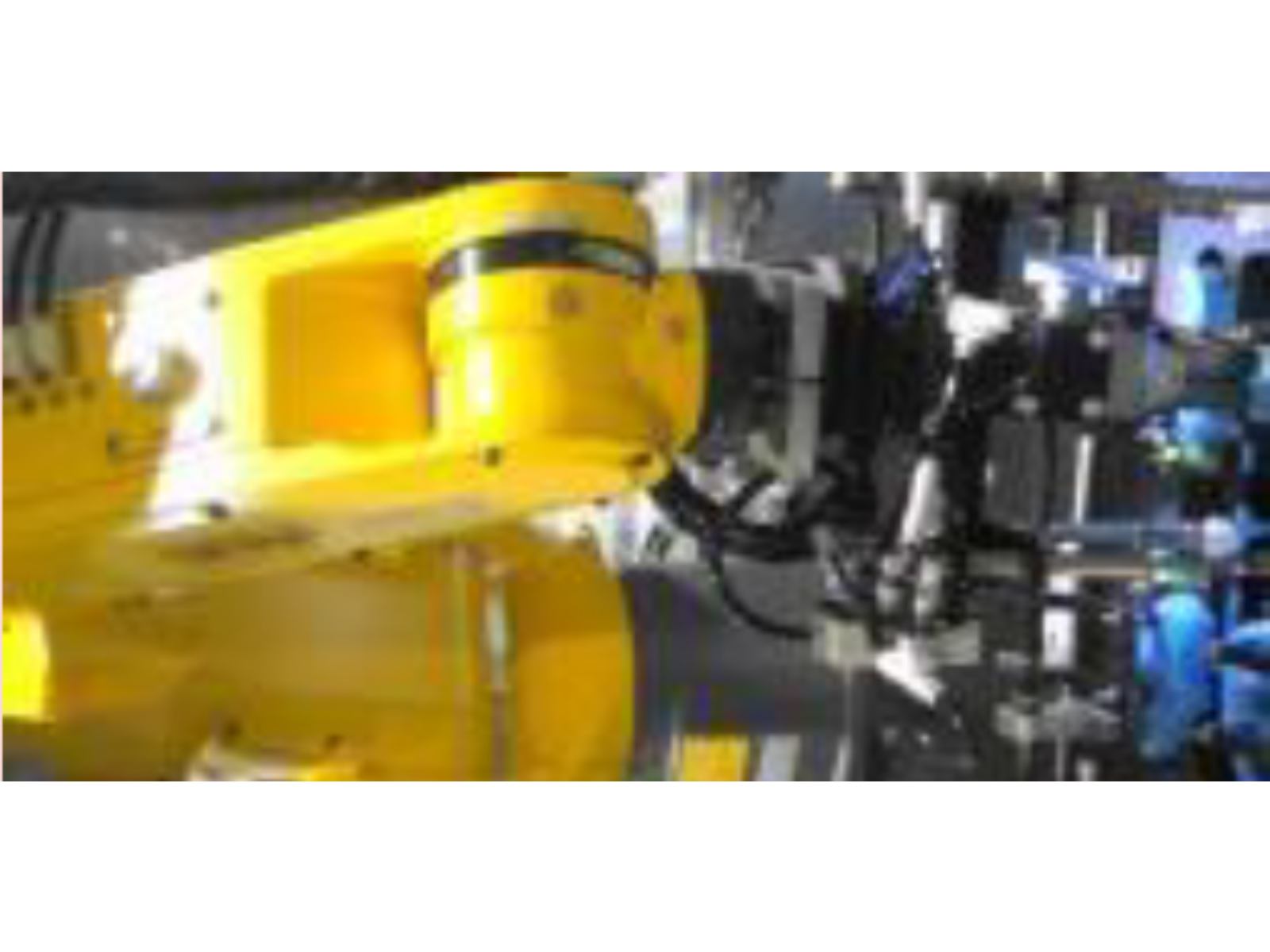
夜間操業の人手不足対策 ロボットを導入して24時間連続稼働を実現した事例!
2019.07.02
企業情報
業種:プラスチック異形押出製品製造業
従業員数:33人
エリア:滋賀県
この事例におけるロボット化によるメリット
□ ロボット導入による生産性の向上
□ ロボットによる夜間作業の代替
当社の課題
当社工場では24時間操業を行っているのですが、夜間操業においては人材の確保が難しく、一部の製造機械では操業時間の短縮を余儀なくされている状況でした。
そこで多関節ロボットを導入する事を考え、ゲートカット工程を全自動化し労働生産性や設備稼働率を高めようと考えました。
ロボットを導入した工程
プラスティック製品のゲートカット工程
ポイント
自動化の内容は下記のようになります。
①プラスチック成形機に設置してある専用の取り出し機からの排出
②成形品をロボットが受け取る
③成形品の輪郭をビジョンセンサで検出する
④カット位置を検知し、ロボットでゲートカットを行う。
⑤ロボットに取り付けた吸着ハンドで保持し、ストッカーへ搬送する
2名の人員がかかる工程を、 1名に削減することに成功しました。
成功ポイントとしては、当社は初めてのロボット導入を検討しましたが、難しい作業ではなくシンプルな作業を選定した点が良かったと思います。
ただ、設置後に判明したことですが、設置場所の確保が不十分だったため、後行程の作業に課題が発生しました。
今後はこの点を解決し、当初目標とした16時間稼動を実現したいと思います。
※一般社団法人 日本ロボット工業会(JARA)「ロボット導入実証事業:事例紹介ハンドブック2016 」より
コンサルタントの視点
所謂3K(「きつい」「きたない」「きけん」)といわれる過酷作業に、ロボットを導入する事は非常に多いですが、
簡単な作業でも、夜間となると非常に過酷な作業となります。
寝ぼけ眼の中、小さなバリを見つけカットする作業を延々と続けることは、体力的にも精神的にも厳しいものです。
この事例では、作業選定をシンプルな箇所に設定したとありますが、
人の作業としてはシンプルでも、ロボットに目の機能を持たせるために「ビジョンセンサ」が必要となってくるとなると、少々ハードルが上がり、導入費用も少々高くなります。
コストメリットをより大きく得るために、夜間作業をターゲットにし、ビジョンセンサ導入費用への抵抗感も小さくできています。
ターゲットとする工程の選定はロボット導入の最初の壁です。
多品種対応、人手不足等、考えなければいけないことは山ほどあります。
ロボットでできる作業の幅は広がっています。
それはビジョンセンサを含むロボット周辺アプリケーションの拡充と、色々な企業の参入があるからこそです。
ただ、情報も多く企業選定も難しくなってきているのも事実。
“ゲートカット ロボット”と検索すればたくさんヒットします。
中小規模の工場経営者様ほど、日々、会社の色々なことを見なければならず、情報収集に時間を割けないことも多々あると思いますが、
こういった事例を参考に皆様の企業運営の一助となれば幸いです。
概要
本事例集は、全国の先進的な工場が取り組む「自動化・ロボット化」の事例をまとめたものとなります。
これから自動化・ロボット化に取組もうと考える皆さまに、
「町工場にロボット・IoTを導入する」ための具体的なノウハウを、
事例を通して知っていただくことを目的に作成しました。
以下のフォームボタンより、必要事項を入力し送信ください。
2〜3営業日以内に担当者より事例集を送付いたします。
事例集を申し込む
【ご確認ください】
こちらの事例集は、導入を検討している工場の担当者様限定となっております。
同業他社、メーカーや商社、SI事業者の方にはご送付をお断りする場合がございます。 企業情報
業種:プラスチック異形押出製品製造業
従業員数:33人
エリア:滋賀県
この事例におけるロボット化によるメリット
□ ロボット導入による生産性の向上
□ ロボットによる夜間作業の代替
当社の課題
当社工場では24時間操業を行っているのですが、夜間操業においては人材の確保が難しく、一部の製造機械では操業時間の短縮を余儀なくされている状況でした。
そこで多関節ロボットを導入する事を考え、ゲートカット工程を全自動化し労働生産性や設備稼働率を高めようと考えました。
ロボットを導入した工程
プラスティック製品のゲートカット工程
ポイント
自動化の内容は下記のようになります。
①プラスチック成形機に設置してある専用の取り出し機からの排出
②成形品をロボットが受け取る
③成形品の輪郭をビジョンセンサで検出する
④カット位置を検知し、ロボットでゲートカットを行う。
⑤ロボットに取り付けた吸着ハンドで保持し、ストッカーへ搬送する
2名の人員がかかる工程を、 1名に削減することに成功しました。
成功ポイントとしては、当社は初めてのロボット導入を検討しましたが、難しい作業ではなくシンプルな作業を選定した点が良かったと思います。
ただ、設置後に判明したことですが、設置場所の確保が不十分だったため、後行程の作業に課題が発生しました。
今後はこの点を解決し、当初目標とした16時間稼動を実現したいと思います。
※一般社団法人 日本ロボット工業会(JARA)「ロボット導入実証事業:事例紹介ハンドブック2016 」より
コンサルタントの視点
所謂3K(「きつい」「きたない」「きけん」)といわれる過酷作業に、ロボットを導入する事は非常に多いですが、
簡単な作業でも、夜間となると非常に過酷な作業となります。
寝ぼけ眼の中、小さなバリを見つけカットする作業を延々と続けることは、体力的にも精神的にも厳しいものです。
この事例では、作業選定をシンプルな箇所に設定したとありますが、
人の作業としてはシンプルでも、ロボットに目の機能を持たせるために「ビジョンセンサ」が必要となってくるとなると、少々ハードルが上がり、導入費用も少々高くなります。
コストメリットをより大きく得るために、夜間作業をターゲットにし、ビジョンセンサ導入費用への抵抗感も小さくできています。
ターゲットとする工程の選定はロボット導入の最初の壁です。
多品種対応、人手不足等、考えなければいけないことは山ほどあります。
ロボットでできる作業の幅は広がっています。
それはビジョンセンサを含むロボット周辺アプリケーションの拡充と、色々な企業の参入があるからこそです。
ただ、情報も多く企業選定も難しくなってきているのも事実。
“ゲートカット ロボット”と検索すればたくさんヒットします。
中小規模の工場経営者様ほど、日々、会社の色々なことを見なければならず、情報収集に時間を割けないことも多々あると思いますが、
こういった事例を参考に皆様の企業運営の一助となれば幸いです。
概要
本事例集は、全国の先進的な工場が取り組む「自動化・ロボット化」の事例をまとめたものとなります。
これから自動化・ロボット化に取組もうと考える皆さまに、
「町工場にロボット・IoTを導入する」ための具体的なノウハウを、
事例を通して知っていただくことを目的に作成しました。
以下のフォームボタンより、必要事項を入力し送信ください。
2〜3営業日以内に担当者より事例集を送付いたします。
事例集を申し込む
【ご確認ください】
こちらの事例集は、導入を検討している工場の担当者様限定となっております。
同業他社、メーカーや商社、SI事業者の方にはご送付をお断りする場合がございます。
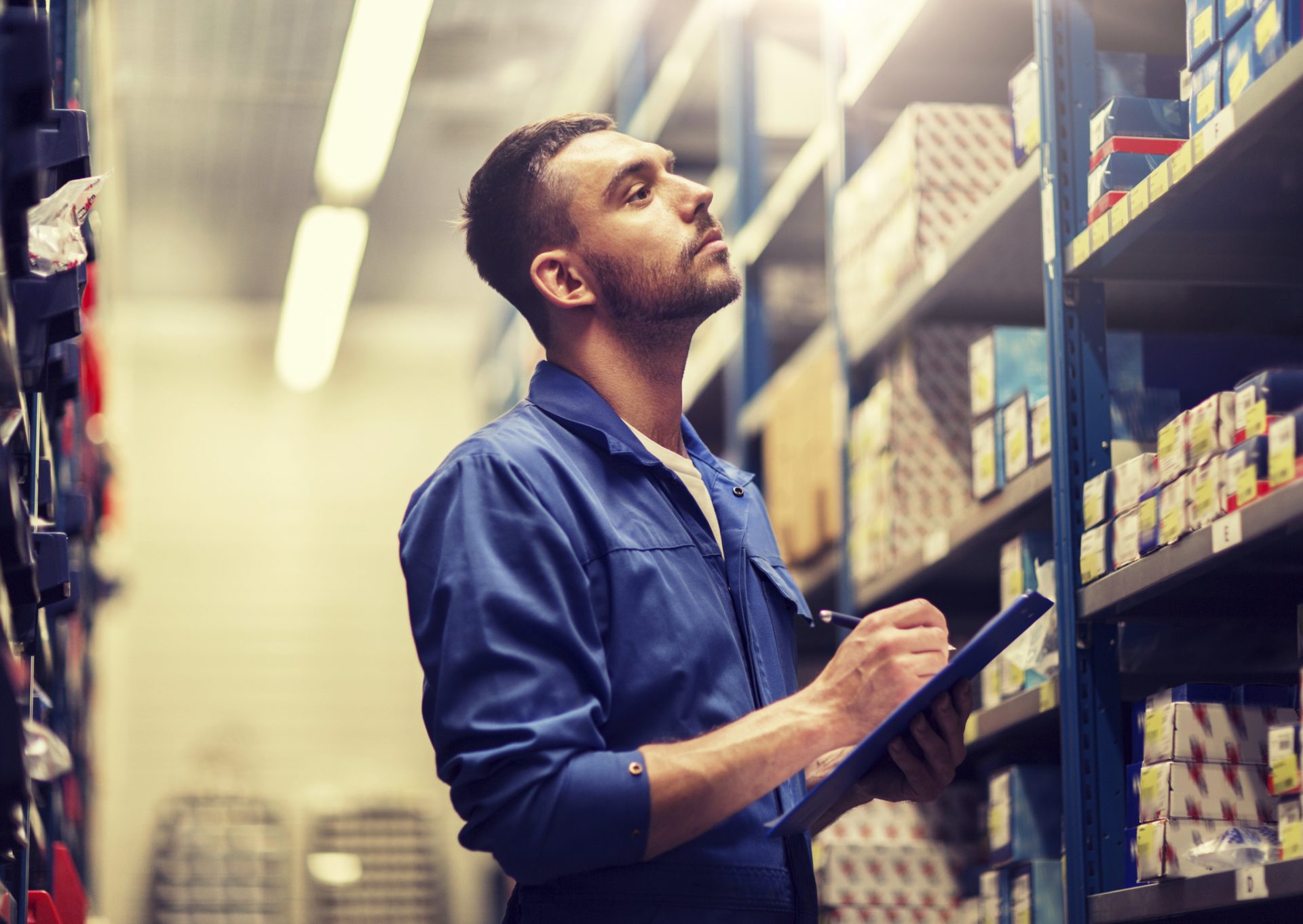
【成功事例に学ぶ】産業用ロボット活用による小物部品出庫(ピッキング)の自動化
2020.05.22
※以下導入事例は一般社団法人 日本ロボット工業会(JARA)「ロボット導入実証事業:事例紹介ハンドブック2017 」より抜粋
企業情報
業種:金属部品製造業
従業員規模:500名
エリア:関西
投資金額 66,000千円
直接効果・・省人効果4名省人(労働生産性3倍)
間接効果・・ミスピッキングの抑制、労働環境改善
この事例におけるロボット化によるメリット
□ 人手に頼っていた部品の入出庫作業(使用先別の仕分け)のロボット化を実現。
□ 入庫時の衝撃や部品の接触による傷、破損を防止するハンドリング。
□ 4名分の工数を省人化
課題
こちらの企業様では、毎日の生産に合わせて自動機を製作する為に必要な部品をピッキングする作業を6名で実施されていました。ピッキング作業は従来の部品棚に並んでいるコンテナから一つ一つリストと照合しながら歩いて部品を探す為に部品間違いやピッキングの時間に多くの工数を費やしていました。歩行量が多く時間もかかる作業である点とピッキングが完了しないと生産が開始できないという点、6名もの作業者が必要という点、一人当たりの労働生産性を向上させる為に自動化を取り組む必要がありました。
ロボットを導入した工程
大小様々な形状で3000品目ある自動機組立用部品のピッキング作業
ポイント
貨幣処理機、自動サービス機器の組立用に納品された部品を、各組立ラインの工程別に用意された部品箱に入庫(振り分け)する。部品は、材質、大きさ、重量、形状がそれぞれ異なり、1日に3,000品目が入荷している。
この作業を、可動式の垂直多関節ロボット2台を使用し自動化を実施した。作業者が伝票のバーコードを読み取り、部品をコンベア上のトレーに入れると、バーコードの情報をもとに専用アプリケーションが必要な情報をICタグに書き込み、これを利用してロボットが行き先別の部品箱に部品を投入するシステムである。
ハンドリング方法の検討により、重量2,000gまでの部品の傷つかない形での投入を実現した。作業者に占める高齢者や女性の比率が高いため、これらの自動化をはかることで、作業者を身体および神経疲労から開放するとともに、4名分の工数が削減できた。
コンサルタントの視点
今回の事例の様に、製造業のうち特に組立を行う業態では、部品のピッキングが必要不可欠です。ピッキングを自動化する為には色々な方法がありますがこちらの企業様の様に汎用の多関節ロボットを用いて投資額を抑制しつつ自社で使いやすい様にカスタマイズする方法もあります。
産業用ロボットとQRコードなどによるデジタル機器との併用による部品管理は直近では多くのメーカーが開発設計を行っており、部品の入出庫を全自動で行う自動倉庫がコンパクトサイズで販売されるようになりました。ロボットとQR、ICタグ等のデジタル機器を用いた自動化システムの開発は今後更に加速していく事でしょう。
またアプリケーションについても改良が加えられロボットに対して知見が無い人でも操作できる様に更に使いやすくなっていく事でしょう。このような自動ピッキングシステムは大規模の倉庫だけではなく、小規模で多品種少量生産方式の採用している企業に導入してこそ真価を発揮すると考えています。
日本の働き手の減少の問題は深刻であり、すでにこのような倉庫でのピッキングシステムを導入し自動化されている企業様も多いです。まだ自動化に取り組まれていない企業様は要チェックですね。
ーーーーーーーーーーーーーーーーーーーーーーーーーーーーーーーーーー
自動化・ロボット化事例集 vol.2
本事例集は、全国の先進的な工場が取り組む「自動化・ロボット化」の事例をまとめたものとなります。
これから自動化・ロボット化に取組もうと考える皆さまに、
「工場にロボット・IoTを導入する」ための具体的なノウハウを、
事例を通して知っていただくことを目的に作成しました。
※こちらの事例集は、導入を検討している工場の担当者様限定となっております。
同業他社、メーカーや商社、SI事業者の方にはご送付をお断わりさせていただいております。
ーーーーーーーーーーーーーーーーーーーーーーーーーーーーーーーーーー
https://smart-factory.funaisoken.co.jp/download/automation-robotization-examples-02/ ※以下導入事例は一般社団法人 日本ロボット工業会(JARA)「ロボット導入実証事業:事例紹介ハンドブック2017 」より抜粋
企業情報
業種:金属部品製造業
従業員規模:500名
エリア:関西
投資金額 66,000千円
直接効果・・省人効果4名省人(労働生産性3倍)
間接効果・・ミスピッキングの抑制、労働環境改善
この事例におけるロボット化によるメリット
□ 人手に頼っていた部品の入出庫作業(使用先別の仕分け)のロボット化を実現。
□ 入庫時の衝撃や部品の接触による傷、破損を防止するハンドリング。
□ 4名分の工数を省人化
課題
こちらの企業様では、毎日の生産に合わせて自動機を製作する為に必要な部品をピッキングする作業を6名で実施されていました。ピッキング作業は従来の部品棚に並んでいるコンテナから一つ一つリストと照合しながら歩いて部品を探す為に部品間違いやピッキングの時間に多くの工数を費やしていました。歩行量が多く時間もかかる作業である点とピッキングが完了しないと生産が開始できないという点、6名もの作業者が必要という点、一人当たりの労働生産性を向上させる為に自動化を取り組む必要がありました。
ロボットを導入した工程
大小様々な形状で3000品目ある自動機組立用部品のピッキング作業
ポイント
貨幣処理機、自動サービス機器の組立用に納品された部品を、各組立ラインの工程別に用意された部品箱に入庫(振り分け)する。部品は、材質、大きさ、重量、形状がそれぞれ異なり、1日に3,000品目が入荷している。
この作業を、可動式の垂直多関節ロボット2台を使用し自動化を実施した。作業者が伝票のバーコードを読み取り、部品をコンベア上のトレーに入れると、バーコードの情報をもとに専用アプリケーションが必要な情報をICタグに書き込み、これを利用してロボットが行き先別の部品箱に部品を投入するシステムである。
ハンドリング方法の検討により、重量2,000gまでの部品の傷つかない形での投入を実現した。作業者に占める高齢者や女性の比率が高いため、これらの自動化をはかることで、作業者を身体および神経疲労から開放するとともに、4名分の工数が削減できた。
コンサルタントの視点
今回の事例の様に、製造業のうち特に組立を行う業態では、部品のピッキングが必要不可欠です。ピッキングを自動化する為には色々な方法がありますがこちらの企業様の様に汎用の多関節ロボットを用いて投資額を抑制しつつ自社で使いやすい様にカスタマイズする方法もあります。
産業用ロボットとQRコードなどによるデジタル機器との併用による部品管理は直近では多くのメーカーが開発設計を行っており、部品の入出庫を全自動で行う自動倉庫がコンパクトサイズで販売されるようになりました。ロボットとQR、ICタグ等のデジタル機器を用いた自動化システムの開発は今後更に加速していく事でしょう。
またアプリケーションについても改良が加えられロボットに対して知見が無い人でも操作できる様に更に使いやすくなっていく事でしょう。このような自動ピッキングシステムは大規模の倉庫だけではなく、小規模で多品種少量生産方式の採用している企業に導入してこそ真価を発揮すると考えています。
日本の働き手の減少の問題は深刻であり、すでにこのような倉庫でのピッキングシステムを導入し自動化されている企業様も多いです。まだ自動化に取り組まれていない企業様は要チェックですね。
ーーーーーーーーーーーーーーーーーーーーーーーーーーーーーーーーーー
自動化・ロボット化事例集 vol.2
本事例集は、全国の先進的な工場が取り組む「自動化・ロボット化」の事例をまとめたものとなります。
これから自動化・ロボット化に取組もうと考える皆さまに、
「工場にロボット・IoTを導入する」ための具体的なノウハウを、
事例を通して知っていただくことを目的に作成しました。
※こちらの事例集は、導入を検討している工場の担当者様限定となっております。
同業他社、メーカーや商社、SI事業者の方にはご送付をお断わりさせていただいております。
ーーーーーーーーーーーーーーーーーーーーーーーーーーーーーーーーーー
https://smart-factory.funaisoken.co.jp/download/automation-robotization-examples-02/