記事公開日:2024.05.22
最終更新日:2024.05.22
理想的な新工場のビジョンと実現方法:持続的生産技術を導入するためのガイド
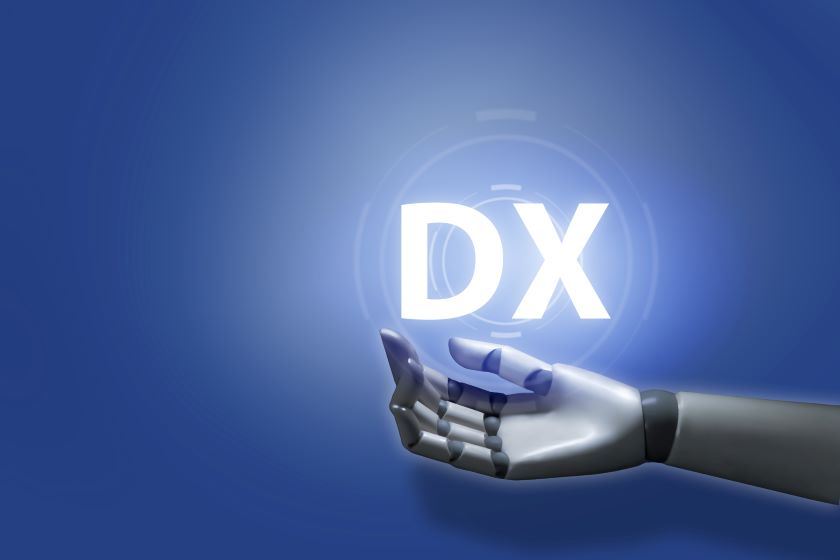
新工場を設立する際、私たちが抱くビジョンはただの夢物語ではありません
新しい工場を設立することは、多くの製造業の経営者にとって大きな挑戦であり、同時に絶好の機会でもあります
新工場の成功は、将来を見据えた持続的生産技術を導入し、効率と生産性を最大限に引き出すことにあります
この記事では、新工場のビジョンの立て方から具体的な課題の整理方法、工程設計のポイント、そしてデジタルトランスフォーメーション(DX)技術の活用法まで詳しく解説します
これを読むことで、製造業の経営者やその関係者が新工場設立のプロセスを理解し、成功への道筋を描けるようになるでしょう
1.新工場のビジョンの立て方のポイント
新工場のビジョンを立てる際には、目的と目標の明確化、市場動向と技術トレンドの分析、そしてステークホルダーの意見収集を行い、関係者全員でビジョンを共有し作り上げていくことが重要です
以下にポイントを整理します
1)目的と目標の明確化
新工場の設立にあたって、具体的な目標を設定することが重要です
例えば、生産性の向上、コスト削減、品質の向上など、どのような成果を達成したいのかを明確にします
目標はより具体的に、出来る限り定量的に評価できるもの(数値目標など)を設定します
これにより、工場の設計や導入技術の選定の基準が明確になり、一貫性のある計画が立てられます
2)市場動向と技術トレンドの分析
業界の最新トレンドや技術革新を把握し、競争力を持つために必要な技術を特定します
例えば、自動化技術やIoT、AIの導入など、いわゆるDX化が急速に進んでいる現在、これらの技術をどのように活用するかが、工場の競争力を左右します
3)ステークホルダーの意見収集
工場の設立に関わるすべてのステークホルダー、すなわち従業員、取引先、顧客などから意見を収集し、それをビジョンに反映させます
これにより、関係者全員が納得し、協力して新工場立上プロジェクトを進められるようになります
2.現状分析と課題整理・分析方法
新工場の設立に際して、現状把握と課題を整理・分析することはプロジェクトの成功に欠かせません。
現状を論理的に分析し、客観的に評価した上で新工場のビジョンを達成するためのロードマップを作成します。
分析や課題整理には様々な手法が存在し、状況に応じて使い分けし総合的に判断しますが、ここでは比較的良く使われる手法を幾つかご紹介します。
1)SWOT分析
SWOT分析は、強み(Strengths)、弱み(Weaknesses)、機会(Opportunities)、脅威(Threats)を洗い出す手法です。
新工場設立において、例えば以下のような内容で分析します。
- 強み(Strengths)
-
新工場が持つ強みを特定します。
例えば、新しい自動化設備の導入により生産効率が向上することや、最新の環境基準を満たすことでエコフレンドリーな工場となる点が挙げられます。
- 弱み(Weaknesses)
-
新工場における課題や弱点を洗い出します。
例えば、新技術の導入に対する従業員のスキル不足や、高額な初期投資が必要である点が考えられます。
- 機会(Opportunities)
-
新工場がもたらす機会を見つけます。
例えば、市場での需要増加に迅速に対応できることや、最新技術を活用して新製品開発が可能となる点が含まれます。
- 脅威(Threats)
-
新工場設立におけるリスクを評価します。
例えば、競合他社の動向や市場の不確実性、規制の変化などが挙げられます。
SWOT分析により、新工場の内外環境を総合的に評価し、戦略的な意思決定をサポートします。
2)5F分析(ファイブフォース分析)
マイケル・ポーターが提唱したファイブフォース分析(5F分析)は、競争環境を評価するためのフレームワークで、5つの力(フォース)を考慮します。
新工場設立において、以下のように適用します。
- 競争企業の脅威
-
同じ市場内の既存企業との競争状況を評価します。
例えば、同業他社がどのような技術を導入しているか、価格競争力がどの程度あるかを分析します。
- 新規参入の脅威
-
新規参入者が市場に参入する可能性とその影響を評価します。
例えば、参入障壁が低い市場では、新たな競合が容易に現れる可能性があります。
- 代替品の脅威
-
他の製品やサービスが代替として選ばれる可能性を評価します。
例えば、製品の代替品が市場に存在する場合、それらが新工場の売上に与える影響を考慮します。
- 買い手の交渉力
-
顧客が価格や品質に対してどれだけの交渉力を持っているかを評価します。
例えば、大口顧客が多い場合、価格交渉力が高くなる可能性があります。
- 供給者の交渉力
-
原材料や部品の供給者が価格や供給条件に対してどれだけの交渉力を持っているかを評価します。
例えば、特定の部品の供給者が限られている場合、供給者の交渉力が強くなる可能性があります。
これらの5つの力を総合的に評価することで、新工場が直面する競争環境を明確にし、適切な戦略を策定することができます。
3)DCF法(Discounted Cash Flow)
新工場設立には多額の投資が必要です。
投資判断を行うための有効な手法として、DCF法(割引キャッシュフロー法)を紹介します。
これは未来のキャッシュフローを現在価値に割り引いて評価する方法です。
新工場設立の投資判断では以下のステップで分析します。
- キャッシュフローの予測
-
新工場から得られる予想キャッシュフローを年間ごとに見積もります。
例えば、年間売上高、運転費用、減価償却費、税引き後の純利益などを計算します。
- 割引率の設定
-
キャッシュフローを現在価値に割り引くための割引率を設定します。
これは、企業の資本コスト(WACC)を基に決定します。
- 現在価値の計算
- 各年のキャッシュフローを割引率で割り引いて現在価値を計算し、全ての現在価値を合計します。
- 投資の評価
- 現在価値の合計が初期投資額を上回る場合、投資は経済的に妥当と判断されます。
例えば、新工場が5年間で総額10億円のキャッシュフローを生むと予測し、割引率を5%と設定した場合、5年間のキャッシュフロー(毎年2億円、5年総額で10億円と仮定)の現在価値の合計を計算すると約8.6627億円となります。
つまり初期投資額がこの価格を下回れば、投資は経済的に成功すると判断できます。
4)Eisenhowerマトリックス(優先順位付け手法)
プロジェクト中に発生する様々な課題を解決しなければなりませんが、課題の重要度と緊急度を評価し、優先順位をつけることで効率的に対応するために優先順位をつける必要があります。
ここでは、Eisenhowerマトリックスを用いた優先順位付けの手法を紹介します。
Eisenhowerマトリックスは、課題を重要性と緊急性の2つの軸で分類し、効果的に優先順位を付ける手法です。
各課題に対して重要度と緊急性にスコア付け(5段階評価など)を行い2次元プロットを行います。
これにより、各課題がプロットされたエリア(第1~第4象限)によって各々取るべきアクションが分類できます。
- 「第1象限」重要かつ緊急(Do First)
-
すぐに対応が必要な課題です。
例えば、工期に直接影響を与える資材の供給遅れなど。
- 「第2象限」重要だが緊急でない(Schedule)
-
計画的に取り組むべき課題です。
例えば、新技術の習得や設備のメンテナンススケジュールなど。
- 「第3象限」緊急だが重要でない(Delegate)
-
他の人に任せられる課題です。
例えば、日常的な書類作業や簡単な報告業務など。
- 「第4象限」重要でも緊急でもない(Eliminate)
-
後回しにできる課題です。
例えば、工場の美化活動など。
プロット図を作成することで課題とその重要性が可視化できるため効率的に課題解決を行うことが出来ます。
3.工場全体の能力を考慮した工程設計方法
効率的な工場レイアウトと物流動線の設計は、各プロセスの処理能力、生産方式、トラブル時の対応を考慮して行う必要があります。
つまり、処理能力のバランス調整を行い、ボトルネックが生じないように工程を設計し、レイアウトと物流動線に落とし込みます。
この設計に活用できる手法の一つがVSM(Value Stream Mapping)です。
VSMは、工場における生産の全プロセス、つまり工場に材料が到着して、保管、加工、検査、梱包、在庫、出荷及び各工程間の運搬までの全体を視覚的に示した図です。
これを用いることで、各工程の処理能力のバランス、工程間の搬送能力、仕掛及び製品の在庫管理などの計画と検証を効率的に行うことができます。
また、工程トラブルなどでボトルネックが生じた場合に影響を受けるプロセスも容易に把握でき、工場の運用が開始された後も適切にアップデートを行うことで常に活用できる手法です。
4.検討すべきDX技術と期待される効果
新工場に導入するDX技術は、自動化、人工知能(AI)、IoT、システム化など様々です。
どんな技術を、どこにどう組み合わせて導入するのかは最初に決めたプロジェクトのビジョンに照らして戦略を立てる必要があります。
ここでは、それぞれの技術の具体例と期待される効果を纏めます。
自動化
生産ラインの自動化により、効率を向上させ、人件費を削減します。
例えば、最新の自動搬送装置(AGV)は、原材料や部品を必要な場所に正確に運びます。
これにより、作業員が材料の運搬に費やす時間(無付加価値作業)を削減し、より付加価値の高い業務に集中できます。
また、ロボットの導入により、精密な組み立て作業が可能となり、不良品の発生を抑えることができます。
特に、精密機器の製造においては、人間の手では難しい微細な作業を高精度に行えるため、品質の向上と生産効率の改善が期待できます。
人工知能(AI)
AIを活用したデータ分析や予測モデルにより、品質管理や需要予測を行います。
例えば、AIを用いた画像認識システムは、従来の画像処理では困難だった検査も実用レベルになって来ており、検査基準の数値化、検査ばらつきの低減、目視検査員の削減などに貢献します。
また、AIによる需要予測モデルを導入し過去の販売データや市場のトレンドを解析することで、製品の需要変動を予測し、在庫と生産計画の最適化が可能となります。
これは、過剰在庫のリスクを減らし、キャッシュフローの改善に寄与します。
IoT(Internet of Things)
IoT技術を活用し、工場内の機器やセンサーをネットワークでつなぎ、リアルタイムでデータを収集・分析します。
例えば、設備の稼働状況や温度、湿度などの環境データをリアルタイムで監視し、異常が検知された場合には即座にアラートを発するシステムを構築します。
またIoTの導入により設備の予防保全が可能となり、突発的な故障を未然に防ぎます。
また、エネルギー消費データのモニタリングにより、省エネルギー対策を強化し、運営コストの削減を図ります。
システム化
生産実行システム(MES)や統合基幹業務システム(ERP)を導入し、情報の一元管理を実現します。
例えば、生産実行システム(MES)を導入することで、製造プロセスの全体をリアルタイムで把握し、生産計画の最適化を図ります。
これにより、生産リードタイムの短縮や、顧客の急な注文変更にも柔軟に対応可能となります。
また、ERPシステムとの連携により、財務、在庫、購買などの情報を統合管理し、業務の効率化と透明性の向上を実現します。
これにより、全社的な情報共有が促進され、迅速な意思決定が可能となります。
5.まとめ
新工場の設立は大きな挑戦ですが、適切なビジョンと計画を持ち、最新のDX技術を活用することで、理想的な工場を実現することができます。
様々な手法を用いて課題を整理・評価し、優先順位をつけて対応することで効率的かつ効果的なプロジェクトマネジメントが可能です。
新工場の成功は、技術と人間の知恵の結晶です。
挑戦を恐れず、一歩一歩着実に前進していきましょう。
製造業の皆様がこのコラムを通じて新たな気づきを得て、理想的な工場設立の一助となることを願っています。
■関連するセミナーのご案内
補助金活用して自動化・省人化・DX化工場の新設・増設セミナー
セミナー詳細・申込はこちらから
https://www.funaisoken.co.jp/seminar/115304
このような方にオススメ
- 最大50億円の補助金を活用して工場新設・増設・移転を行いたい製造業様
- 工場新設・増設・移転を計画しておりDX・自動化・省人化・システム化・IoT化を推進したい製造業様
- 工場新設・増設・移転における事業計画・建築計画・設備計画を成功させたい製造業様
- DX・自動化・省人化・システム化・IoT化された最新のスマートファクトリーを知りたい製造業様
- はじめての工場新設・増設・移転で何から始めたら良いかわからない製造業様
お申し込みはこちらから⇒
https://www.funaisoken.co.jp/seminar/115304
製造業のための 海外工場「再構築DX戦略」 解説レポート
グローバル市場において、日本メーカーが生産する「日本企業製の製品」の評価は非常に高いことはご存じのとおりです。
業務用、民生品といった最終製品のみならず、部品や生産設備でも非常に高い評価を得ており、大きな存在感を維持しています。
つまりキラーコンテンツ=“強い製品”は持っているのです。
そこでDX推進が課題解決の大きな選択肢になります。
単なる省人化・省力化に留まらず、AIなど新たな価値を創出する可能性がある技術もあります。
DX推進によって製造の課題を克服し、今ある基盤を活用して強い製品を効率的に生産し、大きな市場で勝ち抜く。
このDXロードマップを構築することが必要で、最も重要な経営戦略となります。
https://www.funaisoken.co.jp/dl-contents/smart-factory__02738_S045