記事公開日:2024.11.22
最終更新日:2024.12.02
11/15に開催された市川港開発協議会の勉強会にて、飯塚と徳竹が登壇しました
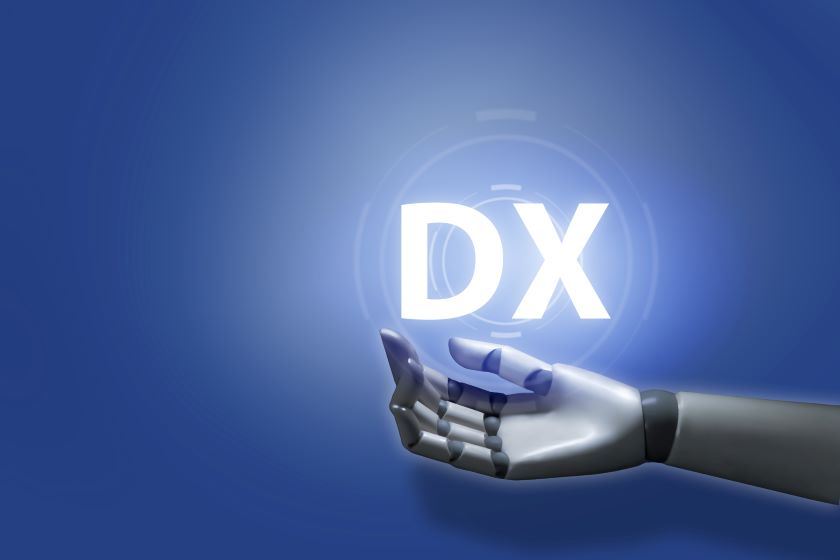
皆様、こんにちは。
株式会社船井総合研究所の塩田です。
11月15日に開催されました、市川港開発協議会の研修会にて、弊社の飯塚・徳竹が講演いたしました。
今回は、「人材不足時代を勝ち抜くDX戦略(基本編)」をテーマに、DXとは何か、またDXの進め方について講演をおこないました。
▽当日の様子
当日は、DXを成功させるための以下のポイントについてご説明させていただきました。
- 業務の見直し(標準化・一元化)
DXを成功させるためには、既存のアナログ作業をデジタル化するだけでは不十分です。まず、業務内容やフローを見直し、無駄をなくし、標準化・一元化を進めることが重要です。 - 優先順位付け
DXを進めるには、解決すべき課題は山積みです。限られた時間とリソースを有効活用するためには、課題の重要度や緊急性を評価し、優先順位をつけて取り組むことが重要です。 - 全社員への周知徹底
DXは、一部の担当者だけで進めるものではありません。全社員がDXの目的や内容を理解し、積極的に参加しなければ、真の変革は実現できません。そのため、経営者が率先してビジョンや戦略を共有し、社員の意識改革を促進する必要があります。 - スモールスタート
最初から完璧なシステムを構築しようとすると、時間やコストがかかりすぎるだけでなく、失敗のリスクも高まります。まずは、比較的小規模なプロジェクトから着手し、成功体験を積み重ねながら、段階的にDXを推進していくことが重要です。 - 目的を見失わない
DXを進める過程で、最新の技術やシステムに目を奪われ、本来の目的を見失ってしまうことがあります。DXはあくまでも手段であり、目的は企業の成長や競争力強化です。常に目的を意識し、手段が目的化しないように注意する必要があります。
船井総研では、コンサルタントの講演依頼を承っております。ご希望の際は、弊社問い合わせフォームよりご依頼をお願いいたします。
関連コラム
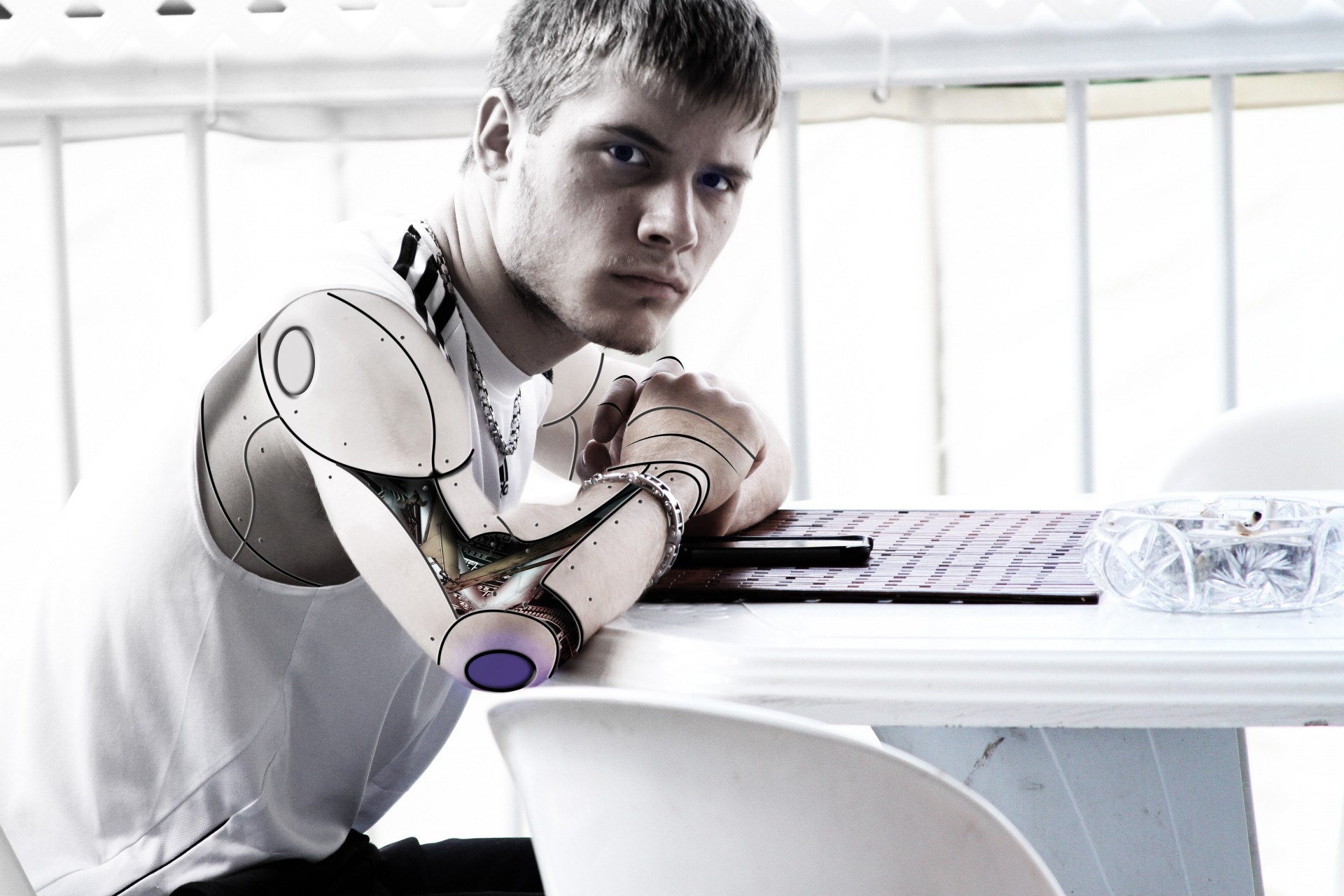
ロボットのティーチングとは?ティーチングの種類と概要を解説
2019.08.27
ティーチング作業とは?
近年、工場のロボット化は製造業種を問わず、様々な分野で進んできております。
また、大企業だけでなく中小企業においてもロボット化・自動化は進んでいます。
しかしながら、ロボットを選定し導入したらそれで自動化を実現でき、生産性を高めることができるわけではありません。
周知の事実の通り、
ロボットはプログラミングを行うことにより動作を制御しています。
そのため、中小企業の様に品種が多品種でありながら、
ロット数が少量であるということは生産工程が逐次変化するということを表しています。
このように変化が多い、中小企業に良くある状況では
ロボット化を進めるために本ページで述べていく
”ティーチング“という作業が欠かせなくなっていきます。
では、一体“ティーチング”とは何なのか?
簡単に一言で表すと、
ティーチングとは「ロボットに望む動作を教えること」です。
このように、ロボットに望む動作を教える方法には様々な種類があります。
その中には、作業工程に最適な方法があることも分かっています。
そのため、本記事をご覧になっている方は
「このティーチング手法が自社に一番適していたのか、、、!」
というような、導入後の後悔が無くなることでしょう。
それでは、まず次項では
ティーチングの種類とその概要について簡単に説明していきます。
ティーチングの種類とその概要
ロボットに直接触れることなくティーチング(間接教示)する
1.オフラインティーチング
2.オンラインティーチング(ティーチング・プレイバック)
ロボットに直接触れながらティーチング(直接教示)する
3.ダイレクトティーチング
上記のように、分類することが可能です。
AIによるティーチングレスは厳密に言うと、
ティーチング作業をAIにより行うこととなります。
本ページでは一般的な教示方法である
間接教示法と直接教示法について述べていきます。
その前にまず、
本項ではそれぞれのティーチング方法を表にまとめてみました。
それぞれのティーチング方法を体系的にまとめましたので
どのような方法が自社には適しているのかを考える参考にして頂ければと思います。
それでは、まずはティーチングの1つであるオフラインティーチングからみていきましょう。
ダイレクトティーチング教示者が直接ロボット本体を動かすことにより動きを教示する方法になります。導入が増加している協働ロボットのティーチングではこの方法が多く採用されています。教示者が可動部を動かし、動作を記録させることで、より直観的にティーチングすることを可能にします。AIによるティーチングレスティーチング作業は属人的なものでありましたが、近年AIの自己学習機能を活用したティーチングレス化が進んでいます。オフラインティーチングにて行ったプログラミング作業に加え、オンラインティーチングで修正を繰り返すことで高品質の作業をミスなく高速で行うことが可能となります。
ティーチングの種類
オフライン
ティーチング
テキスト型
ロボットの動きの元となる、プログラムをテキストエディット用のソフトウェアで直接記入します。複雑な動きのプログラムには向かないため、簡単な動きをするロボットに用いられます。
シミュレータ型
ロボット言語のアップロードや、ダウンロードなどのデータのやり取りが可能です。ロボット言語を変換することができるため、各社のロボットに対応することが可能です。
エミュレータ型
教示者にとってティーチングが容易であるため、多くの産業用ロボットに採用されています。ロボット言語を用いて動作をプログラムし、直接実行させるティーチング方法となるためプログラム精度が高いという利点があります。
自動ティーチングシステム
CADデータから加工プログラムを自動的に作成するシステムです。技術的な難易度の高さから、まだ導入例は多くないと言われています。
オンライン
ティーチング
(ティーチング・プレイバック)
ロボットの教示者がティーチングペンダント(ロボットを動かすコントローラ)を用いて動作を記録します。次に、記録したデータを再生(プレイバック)させながら、さらに動作を微調整します。
オンラインティーチングでは実機を実際に稼働させながら教示する方法であるため、生産ラインを一度止めなければならず、時間的損失が発生することがデメリットとなります。
ダイレクト
ティーチング
教示者が直接ロボット本体を動かすことにより動きを教示する方法になります。導入が増加している協働ロボットのティーチングではこの方法が多く採用されています。教示者が可動部を動かし、動作を記録させることで、より直観的にティーチングすることを可能にします。
AIによる
ティーチングレス
ティーチング作業は属人的なものでありましたが、近年AIの自己学習機能を活用したティーチングレス化が進んでいます。オフラインティーチングにて行ったプログラミング作業に加え、オンラインティーチングで修正を繰り返すことで高品質の作業をミスなく高速で行うことが可能となります。
自社にはどの教示方法が適しているのか?
ここまでご覧になって頂けた方は
間接教示法と直接教示法の違いをご理解いただけたかと思います。
では、自社がロボットを導入し、自動化を実現するためには
どのような教示法、あるいはティーチングを行えるロボットが
適しているのかということで悩まれると思います。
本項では
・間接教示法に適した作業工程
・直接教示法に適した作業工程
上記に分けて説明していきたいと思います。
これらをご理解して頂けますと、
ロボット選定の際に自社に最適なロボットを
検討し易くなることでしょう。
まず、間接教示法と直接教示法のそれぞれが許容できる
作業工程を包含関係で表してみたいと思います。
上記で表す図のように、
直接教示法にできる作業工程が限られることが分かります。
では、包含関係を示したうえで
直接教示法にはどのような作業工程が向いているのかを説明していきます。
直接教示法に適した作業工程とは?
直接教示法とは、前述したようにロボットを直接動かすことによって動作を教示する方法になります。この教示方法はロボットの動作に対して比較的精密度が求められない作業において用いることが一般的となります。
具体的には、以下のような作業工程において用いられております。
ネジ締め作業工程
組立て作業工程
部品の仕分け工程
整列工程
箱詰め工程
ピッキング工程
搬送工程
検査工程
測定工程
間接教示法に適した作業工程とは?
間接教示法は、精密度が求められる工程においても対応することが可能となります。
これは、人の手によるティーチングではなく機械を用いたプログラミングを行うことにより、精度を高めることが可能となるからです。
これらの教示方法により可能となる作業工程は
以下のような作業があります。
溶接
バリ取り
シーリング
ローラーヘム
カット
穴あけ
溶射
塗装
洗浄
搬送(軽量でないもの)
上記のような作業は勿論のこと、
前述した包含関係の図からも、この間接教示法は
直接教示法による作業もカバーすることが可能です。
まとめ
本記事では2つの教示方法と、
ティーチングの種類について説明してきました。
間接教示法は直接教示法が可能とする作業工程を包含していることから
汎用性が高い教示方法であることがわかります。
これを考えると、「間接教示法だけで良いのでは?」
と、思われるかもしれません。
しかし、直接教示法では、ティーチングペンダントを用いることなく
教示者が直接ロボットにティーイングすることが可能であるということから
間接的な教示法よりもティーチングが簡単です。
つまりはティーチングに掛かる作業時間を短縮することができるため、
生産性が高くなるというメリットも考えられます。
このように、それぞれの作業工程に
適した教示方法があることを理解すると
自社におけるロボット選定や導入した後の運用面が明らかになり、
ロボット化・自動化のイメージが着きやすくなると思います。
さらに、本サイトでは
ティーチングの種類や教示方法だけでなく、
それぞれの業種やその工程に特化したロボットについて
様々な事例をもとに解説しております。
そのため、そちらをご覧になって頂けると
より自社に適したロボットがどのようなものか
理解を深めることが出来ると思います。
是非、自社のロボットにおける導入検討のために
御一読いただければと思います。
[clink url="https://smart-factory.funaisoken.co.jp/special/quality-improvement-through-inspection-quality-challenged-by-a-company-with-50-employees/"]
[clink url="https://smart-factory.funaisoken.co.jp/special/a-town-factory-with-40-colleagues-performs-100-inspection-using-robots/"]
[clink url="https://smart-factory.funaisoken.co.jp/special/robotization-of-stud-welding-process/"]
[clink url="https://smart-factory.funaisoken.co.jp/special/robotization-of-attachment-and-detachment-work-in-multiple-processing-machines/"] ティーチング作業とは?
近年、工場のロボット化は製造業種を問わず、様々な分野で進んできております。
また、大企業だけでなく中小企業においてもロボット化・自動化は進んでいます。
しかしながら、ロボットを選定し導入したらそれで自動化を実現でき、生産性を高めることができるわけではありません。
周知の事実の通り、
ロボットはプログラミングを行うことにより動作を制御しています。
そのため、中小企業の様に品種が多品種でありながら、
ロット数が少量であるということは生産工程が逐次変化するということを表しています。
このように変化が多い、中小企業に良くある状況では
ロボット化を進めるために本ページで述べていく
”ティーチング“という作業が欠かせなくなっていきます。
では、一体“ティーチング”とは何なのか?
簡単に一言で表すと、
ティーチングとは「ロボットに望む動作を教えること」です。
このように、ロボットに望む動作を教える方法には様々な種類があります。
その中には、作業工程に最適な方法があることも分かっています。
そのため、本記事をご覧になっている方は
「このティーチング手法が自社に一番適していたのか、、、!」
というような、導入後の後悔が無くなることでしょう。
それでは、まず次項では
ティーチングの種類とその概要について簡単に説明していきます。
ティーチングの種類とその概要
ロボットに直接触れることなくティーチング(間接教示)する
1.オフラインティーチング
2.オンラインティーチング(ティーチング・プレイバック)
ロボットに直接触れながらティーチング(直接教示)する
3.ダイレクトティーチング
上記のように、分類することが可能です。
AIによるティーチングレスは厳密に言うと、
ティーチング作業をAIにより行うこととなります。
本ページでは一般的な教示方法である
間接教示法と直接教示法について述べていきます。
その前にまず、
本項ではそれぞれのティーチング方法を表にまとめてみました。
それぞれのティーチング方法を体系的にまとめましたので
どのような方法が自社には適しているのかを考える参考にして頂ければと思います。
それでは、まずはティーチングの1つであるオフラインティーチングからみていきましょう。
ダイレクトティーチング教示者が直接ロボット本体を動かすことにより動きを教示する方法になります。導入が増加している協働ロボットのティーチングではこの方法が多く採用されています。教示者が可動部を動かし、動作を記録させることで、より直観的にティーチングすることを可能にします。AIによるティーチングレスティーチング作業は属人的なものでありましたが、近年AIの自己学習機能を活用したティーチングレス化が進んでいます。オフラインティーチングにて行ったプログラミング作業に加え、オンラインティーチングで修正を繰り返すことで高品質の作業をミスなく高速で行うことが可能となります。
ティーチングの種類
オフライン
ティーチング
テキスト型
ロボットの動きの元となる、プログラムをテキストエディット用のソフトウェアで直接記入します。複雑な動きのプログラムには向かないため、簡単な動きをするロボットに用いられます。
シミュレータ型
ロボット言語のアップロードや、ダウンロードなどのデータのやり取りが可能です。ロボット言語を変換することができるため、各社のロボットに対応することが可能です。
エミュレータ型
教示者にとってティーチングが容易であるため、多くの産業用ロボットに採用されています。ロボット言語を用いて動作をプログラムし、直接実行させるティーチング方法となるためプログラム精度が高いという利点があります。
自動ティーチングシステム
CADデータから加工プログラムを自動的に作成するシステムです。技術的な難易度の高さから、まだ導入例は多くないと言われています。
オンライン
ティーチング
(ティーチング・プレイバック)
ロボットの教示者がティーチングペンダント(ロボットを動かすコントローラ)を用いて動作を記録します。次に、記録したデータを再生(プレイバック)させながら、さらに動作を微調整します。
オンラインティーチングでは実機を実際に稼働させながら教示する方法であるため、生産ラインを一度止めなければならず、時間的損失が発生することがデメリットとなります。
ダイレクト
ティーチング
教示者が直接ロボット本体を動かすことにより動きを教示する方法になります。導入が増加している協働ロボットのティーチングではこの方法が多く採用されています。教示者が可動部を動かし、動作を記録させることで、より直観的にティーチングすることを可能にします。
AIによる
ティーチングレス
ティーチング作業は属人的なものでありましたが、近年AIの自己学習機能を活用したティーチングレス化が進んでいます。オフラインティーチングにて行ったプログラミング作業に加え、オンラインティーチングで修正を繰り返すことで高品質の作業をミスなく高速で行うことが可能となります。
自社にはどの教示方法が適しているのか?
ここまでご覧になって頂けた方は
間接教示法と直接教示法の違いをご理解いただけたかと思います。
では、自社がロボットを導入し、自動化を実現するためには
どのような教示法、あるいはティーチングを行えるロボットが
適しているのかということで悩まれると思います。
本項では
・間接教示法に適した作業工程
・直接教示法に適した作業工程
上記に分けて説明していきたいと思います。
これらをご理解して頂けますと、
ロボット選定の際に自社に最適なロボットを
検討し易くなることでしょう。
まず、間接教示法と直接教示法のそれぞれが許容できる
作業工程を包含関係で表してみたいと思います。
上記で表す図のように、
直接教示法にできる作業工程が限られることが分かります。
では、包含関係を示したうえで
直接教示法にはどのような作業工程が向いているのかを説明していきます。
直接教示法に適した作業工程とは?
直接教示法とは、前述したようにロボットを直接動かすことによって動作を教示する方法になります。この教示方法はロボットの動作に対して比較的精密度が求められない作業において用いることが一般的となります。
具体的には、以下のような作業工程において用いられております。
ネジ締め作業工程
組立て作業工程
部品の仕分け工程
整列工程
箱詰め工程
ピッキング工程
搬送工程
検査工程
測定工程
間接教示法に適した作業工程とは?
間接教示法は、精密度が求められる工程においても対応することが可能となります。
これは、人の手によるティーチングではなく機械を用いたプログラミングを行うことにより、精度を高めることが可能となるからです。
これらの教示方法により可能となる作業工程は
以下のような作業があります。
溶接
バリ取り
シーリング
ローラーヘム
カット
穴あけ
溶射
塗装
洗浄
搬送(軽量でないもの)
上記のような作業は勿論のこと、
前述した包含関係の図からも、この間接教示法は
直接教示法による作業もカバーすることが可能です。
まとめ
本記事では2つの教示方法と、
ティーチングの種類について説明してきました。
間接教示法は直接教示法が可能とする作業工程を包含していることから
汎用性が高い教示方法であることがわかります。
これを考えると、「間接教示法だけで良いのでは?」
と、思われるかもしれません。
しかし、直接教示法では、ティーチングペンダントを用いることなく
教示者が直接ロボットにティーイングすることが可能であるということから
間接的な教示法よりもティーチングが簡単です。
つまりはティーチングに掛かる作業時間を短縮することができるため、
生産性が高くなるというメリットも考えられます。
このように、それぞれの作業工程に
適した教示方法があることを理解すると
自社におけるロボット選定や導入した後の運用面が明らかになり、
ロボット化・自動化のイメージが着きやすくなると思います。
さらに、本サイトでは
ティーチングの種類や教示方法だけでなく、
それぞれの業種やその工程に特化したロボットについて
様々な事例をもとに解説しております。
そのため、そちらをご覧になって頂けると
より自社に適したロボットがどのようなものか
理解を深めることが出来ると思います。
是非、自社のロボットにおける導入検討のために
御一読いただければと思います。
[clink url="https://smart-factory.funaisoken.co.jp/special/quality-improvement-through-inspection-quality-challenged-by-a-company-with-50-employees/"]
[clink url="https://smart-factory.funaisoken.co.jp/special/a-town-factory-with-40-colleagues-performs-100-inspection-using-robots/"]
[clink url="https://smart-factory.funaisoken.co.jp/special/robotization-of-stud-welding-process/"]
[clink url="https://smart-factory.funaisoken.co.jp/special/robotization-of-attachment-and-detachment-work-in-multiple-processing-machines/"]
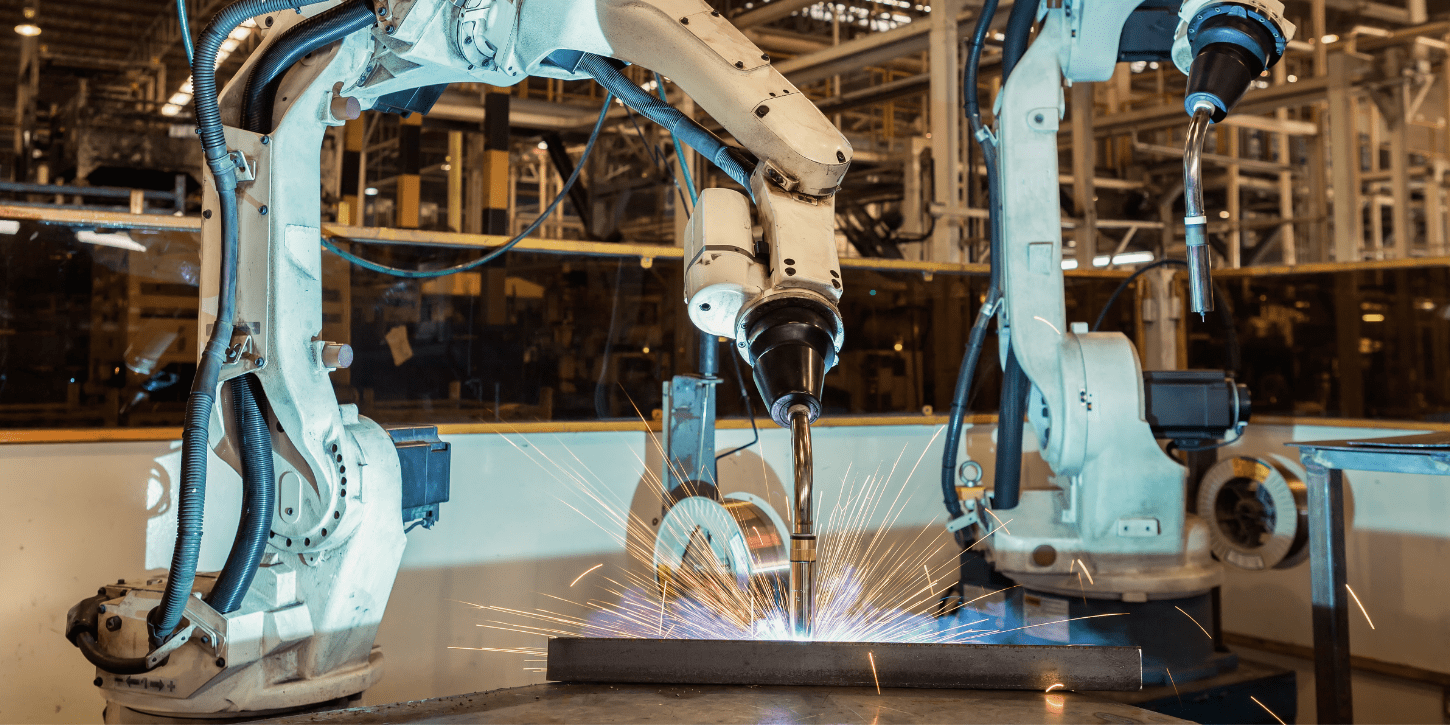
溶接ロボットで行う自動化の方法とは?
2019.08.29
▼無料ダウンロードはこちらをクリック
1 はじめに
溶接工程の自動化、工場内物流における搬送工程の自動化、加工機へのワーク投入・取り出
しの自動化…
近年の技術革新により、これらが実現可能な時代になりました。
それも、資金が潤沢にある大企業のみならず、規模がそこまで大きくない工場も当てはまります。
しかし、これまで「自動化」や用途の広い「ロボット」に触れてこなかったが故に、
「どのようにしたらいいかわからない」
「誰に相談すればいいのかわからない」
このようなお悩みを抱える方は多いのではないでしょうか。
実は、「自動化」や「溶接ロボット」の導入により、「労働者数は増加し、業績は好調になり、生産性も高くなる」という研究が発表されています。
https://gigazine.net/news/20190711-robots-and-firms/
この研究の結論として、「産業用溶接ロボットを導入した製造業をはじめとする企業はその業績が好調で労働者も増加である一方、導入していない企業はその生産高はマイナスで、ハイテク企業に太刀打ちできずに雇用状況も悪化する」とされています。
つまり、
「どのようにしたらいいかわからない」
「誰に相談すればいいのかわからない」
という状態のまま躊躇していても、事態は好転するどころか、じわじわと悪化していく一方なのです。
ではどうすればいいか。
答えは単純で、「今すぐ自動化、ロボットの導入」を検討すればいいのです。
この記事では、「中小規模の製造業が、溶接の自動化・溶接ロボット導入をするために関わる情報」を掲載していますから、「自動化、溶接ロボットの導入」を検討し始めの役に立つことでしょう。
この記事では、
・種々の溶接に最適な溶接ロボット装置の種類
・溶接の自動化、ロボット化によるメリット
を知ることができます。
これらを知ることで、
・「自分たちの工場での自動化・ロボット化はどんな感じになるのか?」
・「いざ、自動化・溶接ロボットの導入をするときに、溶接ロボットの機種があり過ぎて分からない!」
といったモヤモヤを解消し、工場経営の改善につながることでしょう。
最後の方では、様々な製品を取り扱う工場が自動化・溶接ロボットを導入することで成し遂げた成功事例について紹介しています。
ぜひ最後までお読みいただき、工場経営の改善にお役立てください。
2 溶接の自動化・ロボット化とは?
溶接作業をはじめとする製造業の多くは作業者の勘や技術に頼ることが多く、いわゆる職人的な作業となってしまうため、品質のばらつきが大きくなりがちです。また、溶接作業には強烈な紫外線やヒュームが発生するため、作業者にとって過酷な作業になります。
このように、属人的になりがちで過酷な溶接作業において、溶接ロボットを適用し自動化を図る事で、
品質を一定の基準に保つ
生産管理の効率化
人手不足の解消
作業環境の改善
などを実現することが可能です。
3 溶接によって変わる最適な溶接ロボット
溶接ロボットによる溶接の自動化は、大きく「スポット溶接」と「アーク溶接」の2つに分けられています。
スポット溶接は自動車の車体溶接などで多く使用されており、比較的大型な溶接ロボットが用いられます。
アーク溶接ロボットは鉄骨フレームをはじめ比較的細かい製品の溶接に使用されることも多く、設置される溶接ロボット機器のサイズも小型になります。
このように製造業の溶接ロボットによる自動化は溶接の方法によってどのような種類が最適であり、かつロボット自体がどれくらいの面積を占めるのかということも異なっていきます。
本項では現在ある溶接の作業において、どの溶接ロボットが適するのかという水平的な目線で、それぞれの溶接方法により溶接ロボットの大きさが異なることを解説しました。
次項では、溶接作業が自動化へと進化している背景について、それぞれのメリットとデメリットを基にして解説していきます。
4 溶接作業はどのように進化してきたのか?
近年、製造業における工場のロボット化が著しく進み、生産性が向上しています。
また、その対象は大企業だけでなく、中小企業にも拡がってきています。
溶接の方法は大きく分類すると下記のような進化を遂げてきています。
手溶接(被覆アーク溶接) → 半自動溶接(半自動アーク溶接)→ 自動溶接(ロボット溶接)
自動溶接(ロボット溶接)を理解するには、それ以前の背景を辿ることが必要不可欠です。
本項では、溶接の発展を追うごとに何故進化の必要性があるのかということを、それぞれの方法に対してメリット、デメリットを列挙しながら解説します。
そちらを見ていただくと何故溶接工程がロボット化を遂げたのかがわかるかと思います。
以下の表は、各作業方法のメリット・デメリットを簡潔にまとめたものになります。
ティーチングの種類
メリット
デメリット
手溶接
①設備や溶接棒が小型かつ安価である。
②手作業のため、素材・構造に左右されない。
③シールド効果を得ることができる。
①スラグ除去や、溶着効率が低い。
②品質にバラツキが出る。
③ヒュームが多量に発生する。
半自動溶接
①手溶接より効率が高い。
②溶接材の交換が少ない。
③溶接スピードが高い。
④溶接後のフラックスやスパッタ処理を短縮することができる。
①品質が技術者の技量に依存する。
②無風な屋内での作業が必要。
溶接ロボット
①ヒュームやスパッタ発生が少ない。
②風における影響が減少。
③品質が一定である。
④別の高付加価値業務へ熟練者を移行可能に。
①施工面の形状が限定される。
②制御・設計・管理において異なる技能が必要。
4.1 手溶接
この溶接方法は、溶接法の中で最も一般的であった方法です。
手溶接とは、被覆アーク溶接のことを一般的に指しています。
この溶接方法は手溶接棒にフラックスを塗布し、電流を流すことによりアークを発生させることにより熱を発生させる方法です。
作業者が溶接トーチを持ち、文字通り手の動作に従って溶接を行います。
この手法には下記のようなメリットとデメリットが考えられます。
メリット
① 設備や溶接棒が小型かつ安価であるため、導入が比較的しやすい。
② 手による作業のため、素材であったり、構造によることなく溶接することが可能である。
③ フラックスが溶けることによって生じるガス・スラグが母材を覆うことにより、シールド効果を得ることができる。
デメリット
① スラグの除去をしなければならないことや、溶着効率が低いなどの問題がある。
② 品質が技術者の技量によって左右される。人によって高品質となることがあれば低品質となることもある。
③ ヒュームが多量に発生することなどである。
4.2 半自動溶接
半自動アーク溶接はガスシールドアーク溶接の一種であり、この溶接手法は溶着効率の低さを解決するために生み出されました。
現在ではこの半自動アーク溶接のことを指すほど一般的な手法となりました。
手溶接のデメリットを改善した半自動溶接には、以下のようなメリットとデメリットがあります。
メリット
① 手溶接と比較した際に効率が高いこと。また、長い時間の作業が溶接材を交換することなく可能である。
② 溶接のスピードが高く、溶接をした後に生じるフラックスやスパッタの処理などを短縮することが出来る。
デメリット
① 溶接作業者の技量により品質が左右される。
② シールドガスを用いるため、基本的に風のない屋内で作業する必要がある(ノンガスワイヤーを使用する場合を除く)。
4.3 自動溶接
今までの半自動溶接では、溶接者の技術力によって生じる品質の違いは防ぐことはできませんでした。
本項の最後には、自動溶接により今までの溶接手法からどのような変化が期待できるのか解説します。
自動溶接には自動溶接機によるものと、溶接ロボットによるものの2種類があります。
本稿では、溶接ロボットによる自動溶接に焦点を当てて紹介します。
まず、自動溶接機による自動溶接は工場のラインなどで連続に行う溶接手法です。
この手法を進化させたものが、ロボット溶接となります。
これにより、自動溶接時に発生していた課題である溶接姿勢における問題を解決することができるようになりました。
ロボット溶接・自動溶接と比較した際の変化は下記になります。
メリット
① 人の安全に影響を与えるヒュームやスパッタの発生が少ない。
② 風により生じる影響が減少する。
③ 作業者によって品質が左右されない。
デメリット
① 溶接する際、施工面の形状が直線、緩やかなカーブに限られてしまう。
② シーケンスの制御や、機構の設計、安全管理の面で今までと異なる技能が必要である。
5 まとめ
近年、技術力の進歩に伴い、溶接の在り方、より大きな視点で見れば製造業の在り方自体大きく変わってきました。
今まで主流となっていた方法では、作業者の作業環境や、製品の品質にバラツキが生じるなどの様々な問題が生じておりました。
このような悩みは溶接だけでなく、加工や検査、組立など多方面からも聞こえます。
しかし、昨今の製造業分野においては、溶接工程の自動化・ロボット化が急速に進んできております。
このようなロボット化は大量生産に向いているものであると思われがちでありましたが、ティーチング作業を行うことにより、多品種少量生産である、中小企業においても工場の自動化を果たし生産性を高めることが期待できます。
これらの自動化・ロボット化を実現することは、上記のような機能的なメリットだけでなく、中小企業においては採用面などにもメリットを享受することが期待できます。
文部科学省も学校教育においてプログラミングの必修化の準備を着実に進めています。
このような流れが意味することとしては、プログラミング環境がない企業には人が集まらない、採用ができないということになりそうです。
「自社では生産面でロボットを導入しなくても問題ない。」という近視眼的な考え方では、ロボットを先に導入した中小企業と比較すると、生産面だけでなく採用面でも後塵を拝する結果となりかねません。
いつか導入しなければならないものですし、製造業においては人手不足が大きな課題となっているのが現状です。
早めに行動しなければ徐々にその差は開いていく一方のようです。
また、本稿では溶接作業の自動化・ロボット化に焦点を置いてご紹介してまいりました。
しかし、近年では、溶接工程という部分的な括りだけではなく、様々な工程においてこれらのロボット化は裾野を広げてきております。
当サイトでは溶接だけでなく加工や検査、組立の工程など、多種多様な自動化・ロボット化の事例を掲載しておりますので是非そちらもご覧くださいませ。
▼無料ダウンロードはこちらをクリック
[sc name="welding-robot"][/sc]
[sc name="robot"][/sc] ▼無料ダウンロードはこちらをクリック
1 はじめに
溶接工程の自動化、工場内物流における搬送工程の自動化、加工機へのワーク投入・取り出
しの自動化…
近年の技術革新により、これらが実現可能な時代になりました。
それも、資金が潤沢にある大企業のみならず、規模がそこまで大きくない工場も当てはまります。
しかし、これまで「自動化」や用途の広い「ロボット」に触れてこなかったが故に、
「どのようにしたらいいかわからない」
「誰に相談すればいいのかわからない」
このようなお悩みを抱える方は多いのではないでしょうか。
実は、「自動化」や「溶接ロボット」の導入により、「労働者数は増加し、業績は好調になり、生産性も高くなる」という研究が発表されています。
https://gigazine.net/news/20190711-robots-and-firms/
この研究の結論として、「産業用溶接ロボットを導入した製造業をはじめとする企業はその業績が好調で労働者も増加である一方、導入していない企業はその生産高はマイナスで、ハイテク企業に太刀打ちできずに雇用状況も悪化する」とされています。
つまり、
「どのようにしたらいいかわからない」
「誰に相談すればいいのかわからない」
という状態のまま躊躇していても、事態は好転するどころか、じわじわと悪化していく一方なのです。
ではどうすればいいか。
答えは単純で、「今すぐ自動化、ロボットの導入」を検討すればいいのです。
この記事では、「中小規模の製造業が、溶接の自動化・溶接ロボット導入をするために関わる情報」を掲載していますから、「自動化、溶接ロボットの導入」を検討し始めの役に立つことでしょう。
この記事では、
・種々の溶接に最適な溶接ロボット装置の種類
・溶接の自動化、ロボット化によるメリット
を知ることができます。
これらを知ることで、
・「自分たちの工場での自動化・ロボット化はどんな感じになるのか?」
・「いざ、自動化・溶接ロボットの導入をするときに、溶接ロボットの機種があり過ぎて分からない!」
といったモヤモヤを解消し、工場経営の改善につながることでしょう。
最後の方では、様々な製品を取り扱う工場が自動化・溶接ロボットを導入することで成し遂げた成功事例について紹介しています。
ぜひ最後までお読みいただき、工場経営の改善にお役立てください。
2 溶接の自動化・ロボット化とは?
溶接作業をはじめとする製造業の多くは作業者の勘や技術に頼ることが多く、いわゆる職人的な作業となってしまうため、品質のばらつきが大きくなりがちです。また、溶接作業には強烈な紫外線やヒュームが発生するため、作業者にとって過酷な作業になります。
このように、属人的になりがちで過酷な溶接作業において、溶接ロボットを適用し自動化を図る事で、
品質を一定の基準に保つ
生産管理の効率化
人手不足の解消
作業環境の改善
などを実現することが可能です。
3 溶接によって変わる最適な溶接ロボット
溶接ロボットによる溶接の自動化は、大きく「スポット溶接」と「アーク溶接」の2つに分けられています。
スポット溶接は自動車の車体溶接などで多く使用されており、比較的大型な溶接ロボットが用いられます。
アーク溶接ロボットは鉄骨フレームをはじめ比較的細かい製品の溶接に使用されることも多く、設置される溶接ロボット機器のサイズも小型になります。
このように製造業の溶接ロボットによる自動化は溶接の方法によってどのような種類が最適であり、かつロボット自体がどれくらいの面積を占めるのかということも異なっていきます。
本項では現在ある溶接の作業において、どの溶接ロボットが適するのかという水平的な目線で、それぞれの溶接方法により溶接ロボットの大きさが異なることを解説しました。
次項では、溶接作業が自動化へと進化している背景について、それぞれのメリットとデメリットを基にして解説していきます。
4 溶接作業はどのように進化してきたのか?
近年、製造業における工場のロボット化が著しく進み、生産性が向上しています。
また、その対象は大企業だけでなく、中小企業にも拡がってきています。
溶接の方法は大きく分類すると下記のような進化を遂げてきています。
手溶接(被覆アーク溶接) → 半自動溶接(半自動アーク溶接)→ 自動溶接(ロボット溶接)
自動溶接(ロボット溶接)を理解するには、それ以前の背景を辿ることが必要不可欠です。
本項では、溶接の発展を追うごとに何故進化の必要性があるのかということを、それぞれの方法に対してメリット、デメリットを列挙しながら解説します。
そちらを見ていただくと何故溶接工程がロボット化を遂げたのかがわかるかと思います。
以下の表は、各作業方法のメリット・デメリットを簡潔にまとめたものになります。
ティーチングの種類
メリット
デメリット
手溶接
①設備や溶接棒が小型かつ安価である。
②手作業のため、素材・構造に左右されない。
③シールド効果を得ることができる。
①スラグ除去や、溶着効率が低い。
②品質にバラツキが出る。
③ヒュームが多量に発生する。
半自動溶接
①手溶接より効率が高い。
②溶接材の交換が少ない。
③溶接スピードが高い。
④溶接後のフラックスやスパッタ処理を短縮することができる。
①品質が技術者の技量に依存する。
②無風な屋内での作業が必要。
溶接ロボット
①ヒュームやスパッタ発生が少ない。
②風における影響が減少。
③品質が一定である。
④別の高付加価値業務へ熟練者を移行可能に。
①施工面の形状が限定される。
②制御・設計・管理において異なる技能が必要。
4.1 手溶接
この溶接方法は、溶接法の中で最も一般的であった方法です。
手溶接とは、被覆アーク溶接のことを一般的に指しています。
この溶接方法は手溶接棒にフラックスを塗布し、電流を流すことによりアークを発生させることにより熱を発生させる方法です。
作業者が溶接トーチを持ち、文字通り手の動作に従って溶接を行います。
この手法には下記のようなメリットとデメリットが考えられます。
メリット
① 設備や溶接棒が小型かつ安価であるため、導入が比較的しやすい。
② 手による作業のため、素材であったり、構造によることなく溶接することが可能である。
③ フラックスが溶けることによって生じるガス・スラグが母材を覆うことにより、シールド効果を得ることができる。
デメリット
① スラグの除去をしなければならないことや、溶着効率が低いなどの問題がある。
② 品質が技術者の技量によって左右される。人によって高品質となることがあれば低品質となることもある。
③ ヒュームが多量に発生することなどである。
4.2 半自動溶接
半自動アーク溶接はガスシールドアーク溶接の一種であり、この溶接手法は溶着効率の低さを解決するために生み出されました。
現在ではこの半自動アーク溶接のことを指すほど一般的な手法となりました。
手溶接のデメリットを改善した半自動溶接には、以下のようなメリットとデメリットがあります。
メリット
① 手溶接と比較した際に効率が高いこと。また、長い時間の作業が溶接材を交換することなく可能である。
② 溶接のスピードが高く、溶接をした後に生じるフラックスやスパッタの処理などを短縮することが出来る。
デメリット
① 溶接作業者の技量により品質が左右される。
② シールドガスを用いるため、基本的に風のない屋内で作業する必要がある(ノンガスワイヤーを使用する場合を除く)。
4.3 自動溶接
今までの半自動溶接では、溶接者の技術力によって生じる品質の違いは防ぐことはできませんでした。
本項の最後には、自動溶接により今までの溶接手法からどのような変化が期待できるのか解説します。
自動溶接には自動溶接機によるものと、溶接ロボットによるものの2種類があります。
本稿では、溶接ロボットによる自動溶接に焦点を当てて紹介します。
まず、自動溶接機による自動溶接は工場のラインなどで連続に行う溶接手法です。
この手法を進化させたものが、ロボット溶接となります。
これにより、自動溶接時に発生していた課題である溶接姿勢における問題を解決することができるようになりました。
ロボット溶接・自動溶接と比較した際の変化は下記になります。
メリット
① 人の安全に影響を与えるヒュームやスパッタの発生が少ない。
② 風により生じる影響が減少する。
③ 作業者によって品質が左右されない。
デメリット
① 溶接する際、施工面の形状が直線、緩やかなカーブに限られてしまう。
② シーケンスの制御や、機構の設計、安全管理の面で今までと異なる技能が必要である。
5 まとめ
近年、技術力の進歩に伴い、溶接の在り方、より大きな視点で見れば製造業の在り方自体大きく変わってきました。
今まで主流となっていた方法では、作業者の作業環境や、製品の品質にバラツキが生じるなどの様々な問題が生じておりました。
このような悩みは溶接だけでなく、加工や検査、組立など多方面からも聞こえます。
しかし、昨今の製造業分野においては、溶接工程の自動化・ロボット化が急速に進んできております。
このようなロボット化は大量生産に向いているものであると思われがちでありましたが、ティーチング作業を行うことにより、多品種少量生産である、中小企業においても工場の自動化を果たし生産性を高めることが期待できます。
これらの自動化・ロボット化を実現することは、上記のような機能的なメリットだけでなく、中小企業においては採用面などにもメリットを享受することが期待できます。
文部科学省も学校教育においてプログラミングの必修化の準備を着実に進めています。
このような流れが意味することとしては、プログラミング環境がない企業には人が集まらない、採用ができないということになりそうです。
「自社では生産面でロボットを導入しなくても問題ない。」という近視眼的な考え方では、ロボットを先に導入した中小企業と比較すると、生産面だけでなく採用面でも後塵を拝する結果となりかねません。
いつか導入しなければならないものですし、製造業においては人手不足が大きな課題となっているのが現状です。
早めに行動しなければ徐々にその差は開いていく一方のようです。
また、本稿では溶接作業の自動化・ロボット化に焦点を置いてご紹介してまいりました。
しかし、近年では、溶接工程という部分的な括りだけではなく、様々な工程においてこれらのロボット化は裾野を広げてきております。
当サイトでは溶接だけでなく加工や検査、組立の工程など、多種多様な自動化・ロボット化の事例を掲載しておりますので是非そちらもご覧くださいませ。
▼無料ダウンロードはこちらをクリック
[sc name="welding-robot"][/sc]
[sc name="robot"][/sc]
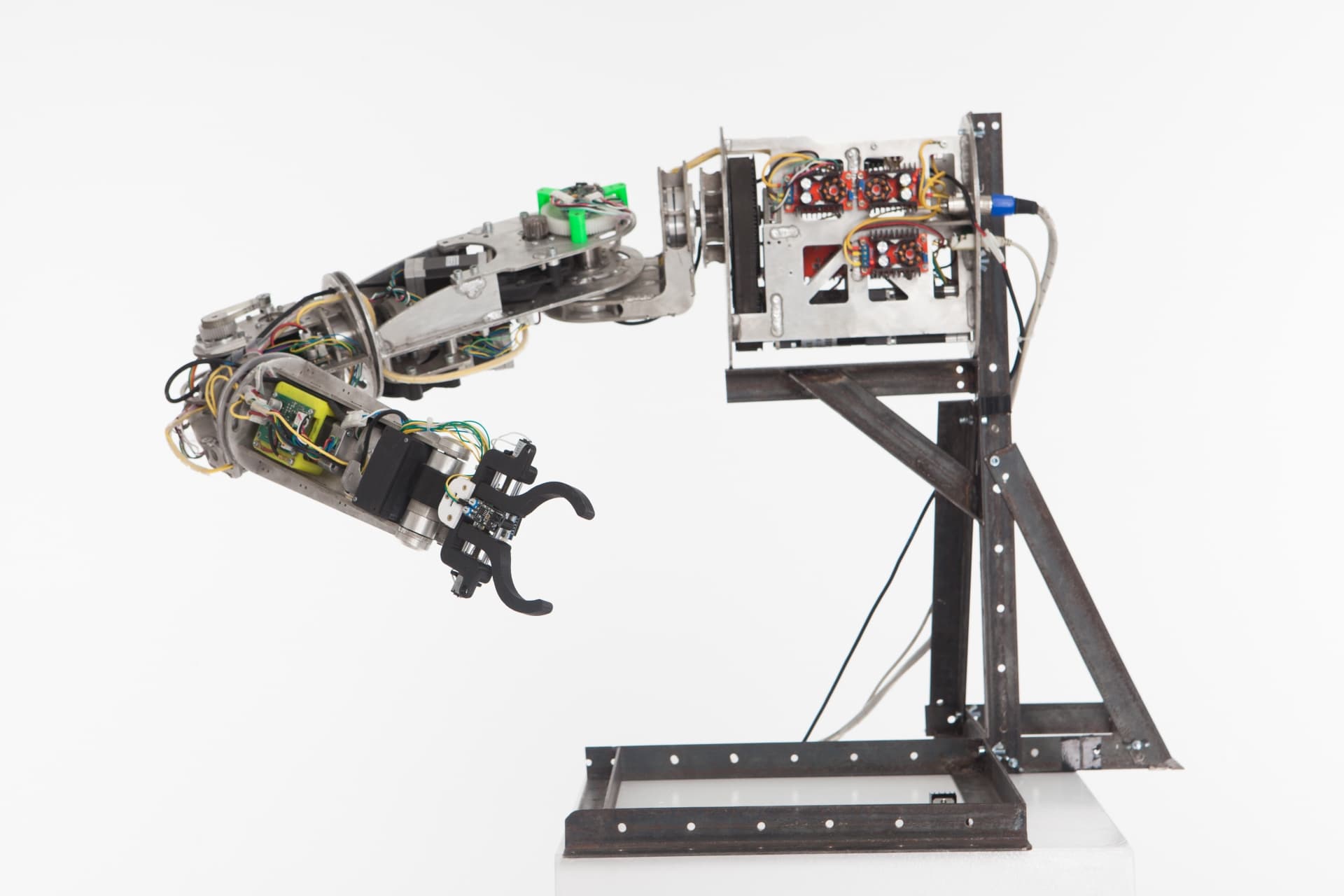
産業用ロボットとは?最新動向からロボットの違いを知る
2019.09.17
近年、「ロボット」という言葉は様々な業界において幅広く聞かれるようになってきました。
そのせいか、ロボットの定義は明確に定まっている訳ではなく所々で色々な定義がされているようです。
そんな中、この「ロボット」という言葉の一つの定義として、“人の代わりに何等かの作業を自律的に行う装置、もしくは機械のこと。”とあります。
このように、どのような用途でロボットが使用されるものかという大まかに定義づけがある他、学術的なロボットの定義の一つとしては、日本ロボット学会が編纂したロボット工学ハンドブックで紹介されているものとして、“自動性、知能性、個体性、半機械半人間性、作業性、汎用性、情報性、柔軟性、有限性、移動性を持つもの”だと言われることもあります。
我々の日常の業務は多くの産業において“人”によって行われているため、この「ロボット」はどのような産業においても遅かれ早かれ関係を持つものとなるだろうことが予想されます。
近年では、日本の人口ピラミッドの推移からも考察できるように、国内の人口は減少傾向であることは明確です。
さらにそれに加え、人口の分布としては高齢者の割合は増加傾向でありながら、若い世代の割合は減少するということが予測されております。
このことから、
国内の人口は減少傾向にあるということ
人口分布は高齢者人口が多くなっていくということ(=国内人口における生産年齢人口の割合が低下するということ)
上記のことが容易に予測できます。
もう一度、「ロボット」の定義の一つを下記に示してみます。
ロボットとは、“人の代わりに何等かの作業を自律的に行う装置、もしくは機械のこと。”
世界的な人口は増加傾向にあります。
しかしながら、一方で日本国内の人口は減少傾向にあります。
そのような環境下において我々に代わって作業を代替してくれる装置・機械である「ロボット」の需要は日に日に増していくことでしょう。
以下のレポートにおいても、中小企業の全体的な方向性としては、社内のシニア、ベテラン人材の継続確保よりも、自動機やロボットによる自動化・省人化のポイントが増加しているようです。
https://www.meti.go.jp/report/whitepaper/mono/2018/honbun_pdf/pdf/honbun01_01_02.pdf
これらのことからも、ロボットへの期待は既に高まっていることが覗えます。
では、このような「ロボット」、多くの産業から耳にするようになっておりますが、具体的にはどのような分野においてロボット化は進んでいるのでしょうか?
ロボット化が進む分野は?
産業用ロボット
BtoBにおけるロボットとしては産業用ロボットが代表的です。
この産業用ロボットという括りではざっくりとしすぎているため、以下の様に分類してみました。
農業用
農業のロボット化というと、スマート農業という言葉が最近では聞かれるようになってきています。スマート農業を牽引させている企業としては、クボタなどが代表的な企業となります。農業人口が減少している中で、クボタの開発した無人コンバインや、無人田植え機は高齢者の農業を手助けするだけでなく、生産年齢人口が減少している中で大きな貢献が期待されています。
林業用
林業用のロボットとしては、自動枝払い機や下草刈りロボットなどが挙げられます。木にロボットを装着するだけで、自動でロボットが枝を切断してくれるロボットなどが代表的な例です。高い木などの切断が困難である中で、林業者の手助けをしてくれるロボットです。草刈りロボットはルンバのような形状で、自動で草を刈り人の作業を手助けしてくれています。
工業用
産業用のロボットというと、日本の製造業から考えていくと工業のロボット化を表すことが多いかもしれません。工業用ロボットは、アームロボットであれば、溶接の工程に用いられたり、組立工程において用いられたりと使用の用途は様々です。このようなロボット化は減少している生産年齢人口に対応するだけでなく、過酷作業を低減させることや、中小企業にとっては採用面でも強化が期待できるようです。
商業用
マネキン型ロボット「Palette」は人感センサーを備え、人が近づくとさまざまなポーズを披露するマネキン型ロボットです。ファッション業界においてこれらのロボットが現在では活用されているようです。また、物流クライシスや物流事業の危機が囁かれ、更なる宅配ニーズが急激に増加するなかで、自動運搬ロボットは少子高齢化、深刻な人手不足にみまわれている状況における一つの打開策として期待が持たれています。
サービス用ロボット
サービス産業におけるロボット化としては、看護ロボットにおいてはMoxiなどの看護師を支援するロボットがあります。また、ビルや公共建物清掃などを行うロボットや福祉業界においても近年需要が高まっています。このようなことから、サービス分野においてもロボット化が急速に進むことが予測されています。
ペットロボット
また、産業用ロボットやサービス用ロボットは主に人間が行っている作業を代替するものがほとんどでありました。しかし、ペットロボットは人間にセラピー効果を与えることへ期待が持たれているものです。このようなロボットの代表としては、SONYにより開発されたAIBOや、バロなどが有名です。これらロボットの効果としては、うつ状態の効果を改善させる心理的効果、ストレス低減といった生理的効果、発話の増加による社会的効果増進などの効果に寄与するようです。
今回の記事では、上記のように分類してみましたが、人それぞれで分類の方法は異なるでしょう。
これは、ロボットという定義が場所によって人によって状況によって変わってくるものであるから避けられないことかもしれません。
産業用ロボットとは?
「ロボット」と一口に言っても様々な種類があることをご紹介してきました。
そのような中で、製造業において注目したロボット化とは、産業のロボット化にあたります。
この日本のお家芸であったロボットに世界が追い付こうと、ドイツではインダストリー4.0、アメリカではインダストリー・インターネット・コンソーシアムというように世界的にもロボット化が進んでいます。
しかし、近年では中小企業においても産業のロボット化は急速に進んできています。
このような産業のロボット化、その中でも工業のロボット化に注目が集まっている理由としては、顧客のニーズが多様化していることもありますし、それに加え、これから課題となる生産人口の減少にも対応することが可能となるからでしょう。
そもそも、この産業ロボットの定義はどのようなものなのかというと、日本工業規格(JIS)によれば、「自動制御によるマニピュレーション機能または移動機能をもち、各種の作業をプログラムによって実行できる、産業に使用される機械」と定義されています。
そして、このような産業のロボット化とは大企業が大きな投資をすることにより実現することが可能なものだと考えられておりました。
しかし、近年では資金が大企業のように潤沢ではなく、規模もそれほどではないような中小企業においてもロボット化が可能となってきております。
このように、中小企業のロボット化は大企業のそれとは異なります。
中小企業のロボット化は
ロボットによる熟練作業の代替
熟練作業員は更なる付加価値の高い業務へと移行可能に
ロボットによる3K業務の代替
ロボット導入により、若い人材を採用可能に
中小企業のロボット化は大企業のそれとは異なり、上記のようなメリットを享受することに期待がもてることになりそうです。
【産業用ロボット例】例えば垂直多関節ロボットとは?
垂直多関節ロボットについてもう少し具体的に用途や事例を紹介したいと思います。
次に垂直多関節ロボットは、「6軸ロボット」や「5軸ロボット」とも呼ばれています。複数個の間接を持つロボットという意味で多関節ロボットと呼称されています。
ロボットは軸が多いほど自由に動けます。それぞれの関節がほぼ360°の動きに対応しており、その関節の動きの組み合わせにより様々な動きを実現出来ます。
ここで言う関節にはサーボモータが組み込まれており、関節数はサーボモータの数と同じです。つまりロボットとはサーボモータの集合体なのです。
そして、このサーボモータの性能と複数のサーボモーターを同時に制御するソフトウェアの合体したものが産業用ロボットです。
さらにロボットハンドの先端に用途に合わせて様々なハンドを装着する事が出来ます。このハンドにはモノを掴んだり、加工したり、形状を測定したり、塗装したり、溶接したりと、色々な種類があり、その組み合わせと使い方は無限大の可能性を秘めてます。
その汎用性の高さ故に、様々な分野で使用されており、世界中のものづくりに変革をもたらしています。
代表的な使用方法
1、バラ積みピッキング
垂直多関節ロボットやパラレルリンクロボットにカメラを追加して、ばらばらに置かれている製品や材料の向きや角度を判別してロボットが自動でピッキング(把持する)する機構です。
機械加工をはじめ食品、倉庫等様々な分野で利用されています。
2、溶接
ロボットハンドに溶接トーチを持たせて自動で溶接を行います。
TIG,MIG,MAG,YEG様々な溶接にも対応可能です。特殊な肉盛り溶接やアルミ溶接など難易度の高い溶接にも対応しており、現在もメーカーから様々なロボット溶接用トーチが開発販売されています。
3、研磨ロボット
ハンドにて製品や材料をピッキングし、研磨機等に押し付ける事で研磨を行う工程に用いられています。
ロボットは力加減が出来ないモノなのですが、ハンドに力覚センサーを初めとするセンサーを用いる事で研磨機への押し付け強さ等もコントロールする事が出来、従来では研磨の職人さんしか出来なかった分野への利用が進んでいます。
鋳物部品のバリ取りから眼鏡レンズの研磨など粗いものから精密なものまで幅広く使用されてます。
4、塗装
塗装についても非常に自動化が進んでいる分野です。塗装も非常に高い技術が必要な加工なのですが、ロボットでの塗装も非常に広く利用されてます。
例えば自動車ですが、基本的に全てロボットで塗ってます。
携帯電話のケースやOA機器等のケース等の量産品も多くの場合ロボットで塗られています。逆に職人さんが手吹きで塗装しているモノの方が少なくなってきていると思います。
5、検査
検査といえば、検査専用用カメラですが、ここにもロボットを用いられるケースが増えてきています。
なぜなら、検査用カメラは動く事が出来ない為です。立体物の多面を検査する為には、立体物を動かす必要があるからです。従来の検査方法では、人間が製品や材料を動かして多方向からカメラで撮像、検査を行う必要がありました。検査用カメラも非常に高価なものなので、複数個のカメラを用いて多方向から同時検出する事が現実的に不可能でした。そこでロボットを活用します。
カメラは一つでロボットが検査する面をカメラにむけて撮像、検査、面を変えて検査という方法や、ロボットハンドにカメラを持たせて立体物の周囲全方向から撮像、検査を実施する場合もあります。
特に非常に大きなモノや重たいモノの検査に重宝されています。
このように様々な分野に垂直多関節ロボットは利用されています。何にでも利用出来る反面、用途や環境に合わせたカスタマイズをしっかりと行う必要があるのが垂直多関節ロボットであり、このカスタマイズを如何に現場に最適なモノにするかが導入の最も大きなポイントです。
垂直多関節ロボットの導入を検討している方は、しっかりと目的・用途・環境等を吟味した上でロボットのカスタマイズする事をおすすめします。
まとめ
このように近年では、様々な業界においてロボットが用いられるようになってきています。
背景には将来的な人口減少により生産年齢人口が減少することや、顧客のニーズを満たすようなロボットを製造することが出来るまでに技術が発展していることなどが挙げられます。
その中で産業用ロボットやサービス用ロボット、ペットロボットなど種類・業界は多岐に渡って活躍していくことでしょう。
色々な環境においてロボット化が進んでいることから、ロボットの定義は場所や人、状況によって様々なものとなっているようです。
また、「ロボット」は日本のお家芸であり常に世界の先陣を走っていました。
しかし、それに追いつこうと近頃ではインダストリー4.0やインダストリー・インターネット・コンソーシアム(IIC)など工場の自動化に注目が非常に集まってきています。
近年、中小企業でもこのような工場の自動化の事例は急速に増えてきています。
これはロボットがプログラミングによって動作を変更することができることの他、ロボットに付随するアプリケーションの発展があり、多品種少量に対応することが出来るようになった事も要因として挙げられます。
本記事ではロボットとはどのような種類があるのかを簡単にまとめてきました。
他の記事では、中小企業がロボット化を実現している事例なども紹介しておりますから、ロボット化をお考えの方のきっとお役に立つことと思います。
是非一度、ご覧になって下さい。
[clink url="https://smart-factory.funaisoken.co.jp/special/quality-improvement-through-inspection-quality-challenged-by-a-company-with-50-employees/"]
[clink url="https://smart-factory.funaisoken.co.jp/special/a-town-factory-with-40-colleagues-performs-100-inspection-using-robots/"]
[clink url="https://smart-factory.funaisoken.co.jp/special/robotization-of-stud-welding-process/"]
[clink url="https://smart-factory.funaisoken.co.jp/special/robotization-of-attachment-and-detachment-work-in-multiple-processing-machines/"]
ーーーーーーーーーーーーーーーーーーーーーーーーーーーーーーーーーー
自動化・ロボット化事例集 vol.2
本事例集は、全国の先進的な工場が取り組む「自動化・ロボット化」の事例をまとめたものとなります。
これから自動化・ロボット化に取組もうと考える皆さまに、
「工場にロボット・IoTを導入する」ための具体的なノウハウを、
事例を通して知っていただくことを目的に作成しました。
ーーーーーーーーーーーーーーーーーーーーーーーーーーーーーーーーーー
https://smart-factory.funaisoken.co.jp/download/automation-robotization-examples-02/ 近年、「ロボット」という言葉は様々な業界において幅広く聞かれるようになってきました。
そのせいか、ロボットの定義は明確に定まっている訳ではなく所々で色々な定義がされているようです。
そんな中、この「ロボット」という言葉の一つの定義として、“人の代わりに何等かの作業を自律的に行う装置、もしくは機械のこと。”とあります。
このように、どのような用途でロボットが使用されるものかという大まかに定義づけがある他、学術的なロボットの定義の一つとしては、日本ロボット学会が編纂したロボット工学ハンドブックで紹介されているものとして、“自動性、知能性、個体性、半機械半人間性、作業性、汎用性、情報性、柔軟性、有限性、移動性を持つもの”だと言われることもあります。
我々の日常の業務は多くの産業において“人”によって行われているため、この「ロボット」はどのような産業においても遅かれ早かれ関係を持つものとなるだろうことが予想されます。
近年では、日本の人口ピラミッドの推移からも考察できるように、国内の人口は減少傾向であることは明確です。
さらにそれに加え、人口の分布としては高齢者の割合は増加傾向でありながら、若い世代の割合は減少するということが予測されております。
このことから、
国内の人口は減少傾向にあるということ
人口分布は高齢者人口が多くなっていくということ(=国内人口における生産年齢人口の割合が低下するということ)
上記のことが容易に予測できます。
もう一度、「ロボット」の定義の一つを下記に示してみます。
ロボットとは、“人の代わりに何等かの作業を自律的に行う装置、もしくは機械のこと。”
世界的な人口は増加傾向にあります。
しかしながら、一方で日本国内の人口は減少傾向にあります。
そのような環境下において我々に代わって作業を代替してくれる装置・機械である「ロボット」の需要は日に日に増していくことでしょう。
以下のレポートにおいても、中小企業の全体的な方向性としては、社内のシニア、ベテラン人材の継続確保よりも、自動機やロボットによる自動化・省人化のポイントが増加しているようです。
https://www.meti.go.jp/report/whitepaper/mono/2018/honbun_pdf/pdf/honbun01_01_02.pdf
これらのことからも、ロボットへの期待は既に高まっていることが覗えます。
では、このような「ロボット」、多くの産業から耳にするようになっておりますが、具体的にはどのような分野においてロボット化は進んでいるのでしょうか?
ロボット化が進む分野は?
産業用ロボット
BtoBにおけるロボットとしては産業用ロボットが代表的です。
この産業用ロボットという括りではざっくりとしすぎているため、以下の様に分類してみました。
農業用
農業のロボット化というと、スマート農業という言葉が最近では聞かれるようになってきています。スマート農業を牽引させている企業としては、クボタなどが代表的な企業となります。農業人口が減少している中で、クボタの開発した無人コンバインや、無人田植え機は高齢者の農業を手助けするだけでなく、生産年齢人口が減少している中で大きな貢献が期待されています。
林業用
林業用のロボットとしては、自動枝払い機や下草刈りロボットなどが挙げられます。木にロボットを装着するだけで、自動でロボットが枝を切断してくれるロボットなどが代表的な例です。高い木などの切断が困難である中で、林業者の手助けをしてくれるロボットです。草刈りロボットはルンバのような形状で、自動で草を刈り人の作業を手助けしてくれています。
工業用
産業用のロボットというと、日本の製造業から考えていくと工業のロボット化を表すことが多いかもしれません。工業用ロボットは、アームロボットであれば、溶接の工程に用いられたり、組立工程において用いられたりと使用の用途は様々です。このようなロボット化は減少している生産年齢人口に対応するだけでなく、過酷作業を低減させることや、中小企業にとっては採用面でも強化が期待できるようです。
商業用
マネキン型ロボット「Palette」は人感センサーを備え、人が近づくとさまざまなポーズを披露するマネキン型ロボットです。ファッション業界においてこれらのロボットが現在では活用されているようです。また、物流クライシスや物流事業の危機が囁かれ、更なる宅配ニーズが急激に増加するなかで、自動運搬ロボットは少子高齢化、深刻な人手不足にみまわれている状況における一つの打開策として期待が持たれています。
サービス用ロボット
サービス産業におけるロボット化としては、看護ロボットにおいてはMoxiなどの看護師を支援するロボットがあります。また、ビルや公共建物清掃などを行うロボットや福祉業界においても近年需要が高まっています。このようなことから、サービス分野においてもロボット化が急速に進むことが予測されています。
ペットロボット
また、産業用ロボットやサービス用ロボットは主に人間が行っている作業を代替するものがほとんどでありました。しかし、ペットロボットは人間にセラピー効果を与えることへ期待が持たれているものです。このようなロボットの代表としては、SONYにより開発されたAIBOや、バロなどが有名です。これらロボットの効果としては、うつ状態の効果を改善させる心理的効果、ストレス低減といった生理的効果、発話の増加による社会的効果増進などの効果に寄与するようです。
今回の記事では、上記のように分類してみましたが、人それぞれで分類の方法は異なるでしょう。
これは、ロボットという定義が場所によって人によって状況によって変わってくるものであるから避けられないことかもしれません。
産業用ロボットとは?
「ロボット」と一口に言っても様々な種類があることをご紹介してきました。
そのような中で、製造業において注目したロボット化とは、産業のロボット化にあたります。
この日本のお家芸であったロボットに世界が追い付こうと、ドイツではインダストリー4.0、アメリカではインダストリー・インターネット・コンソーシアムというように世界的にもロボット化が進んでいます。
しかし、近年では中小企業においても産業のロボット化は急速に進んできています。
このような産業のロボット化、その中でも工業のロボット化に注目が集まっている理由としては、顧客のニーズが多様化していることもありますし、それに加え、これから課題となる生産人口の減少にも対応することが可能となるからでしょう。
そもそも、この産業ロボットの定義はどのようなものなのかというと、日本工業規格(JIS)によれば、「自動制御によるマニピュレーション機能または移動機能をもち、各種の作業をプログラムによって実行できる、産業に使用される機械」と定義されています。
そして、このような産業のロボット化とは大企業が大きな投資をすることにより実現することが可能なものだと考えられておりました。
しかし、近年では資金が大企業のように潤沢ではなく、規模もそれほどではないような中小企業においてもロボット化が可能となってきております。
このように、中小企業のロボット化は大企業のそれとは異なります。
中小企業のロボット化は
ロボットによる熟練作業の代替
熟練作業員は更なる付加価値の高い業務へと移行可能に
ロボットによる3K業務の代替
ロボット導入により、若い人材を採用可能に
中小企業のロボット化は大企業のそれとは異なり、上記のようなメリットを享受することに期待がもてることになりそうです。
【産業用ロボット例】例えば垂直多関節ロボットとは?
垂直多関節ロボットについてもう少し具体的に用途や事例を紹介したいと思います。
次に垂直多関節ロボットは、「6軸ロボット」や「5軸ロボット」とも呼ばれています。複数個の間接を持つロボットという意味で多関節ロボットと呼称されています。
ロボットは軸が多いほど自由に動けます。それぞれの関節がほぼ360°の動きに対応しており、その関節の動きの組み合わせにより様々な動きを実現出来ます。
ここで言う関節にはサーボモータが組み込まれており、関節数はサーボモータの数と同じです。つまりロボットとはサーボモータの集合体なのです。
そして、このサーボモータの性能と複数のサーボモーターを同時に制御するソフトウェアの合体したものが産業用ロボットです。
さらにロボットハンドの先端に用途に合わせて様々なハンドを装着する事が出来ます。このハンドにはモノを掴んだり、加工したり、形状を測定したり、塗装したり、溶接したりと、色々な種類があり、その組み合わせと使い方は無限大の可能性を秘めてます。
その汎用性の高さ故に、様々な分野で使用されており、世界中のものづくりに変革をもたらしています。
代表的な使用方法
1、バラ積みピッキング
垂直多関節ロボットやパラレルリンクロボットにカメラを追加して、ばらばらに置かれている製品や材料の向きや角度を判別してロボットが自動でピッキング(把持する)する機構です。
機械加工をはじめ食品、倉庫等様々な分野で利用されています。
2、溶接
ロボットハンドに溶接トーチを持たせて自動で溶接を行います。
TIG,MIG,MAG,YEG様々な溶接にも対応可能です。特殊な肉盛り溶接やアルミ溶接など難易度の高い溶接にも対応しており、現在もメーカーから様々なロボット溶接用トーチが開発販売されています。
3、研磨ロボット
ハンドにて製品や材料をピッキングし、研磨機等に押し付ける事で研磨を行う工程に用いられています。
ロボットは力加減が出来ないモノなのですが、ハンドに力覚センサーを初めとするセンサーを用いる事で研磨機への押し付け強さ等もコントロールする事が出来、従来では研磨の職人さんしか出来なかった分野への利用が進んでいます。
鋳物部品のバリ取りから眼鏡レンズの研磨など粗いものから精密なものまで幅広く使用されてます。
4、塗装
塗装についても非常に自動化が進んでいる分野です。塗装も非常に高い技術が必要な加工なのですが、ロボットでの塗装も非常に広く利用されてます。
例えば自動車ですが、基本的に全てロボットで塗ってます。
携帯電話のケースやOA機器等のケース等の量産品も多くの場合ロボットで塗られています。逆に職人さんが手吹きで塗装しているモノの方が少なくなってきていると思います。
5、検査
検査といえば、検査専用用カメラですが、ここにもロボットを用いられるケースが増えてきています。
なぜなら、検査用カメラは動く事が出来ない為です。立体物の多面を検査する為には、立体物を動かす必要があるからです。従来の検査方法では、人間が製品や材料を動かして多方向からカメラで撮像、検査を行う必要がありました。検査用カメラも非常に高価なものなので、複数個のカメラを用いて多方向から同時検出する事が現実的に不可能でした。そこでロボットを活用します。
カメラは一つでロボットが検査する面をカメラにむけて撮像、検査、面を変えて検査という方法や、ロボットハンドにカメラを持たせて立体物の周囲全方向から撮像、検査を実施する場合もあります。
特に非常に大きなモノや重たいモノの検査に重宝されています。
このように様々な分野に垂直多関節ロボットは利用されています。何にでも利用出来る反面、用途や環境に合わせたカスタマイズをしっかりと行う必要があるのが垂直多関節ロボットであり、このカスタマイズを如何に現場に最適なモノにするかが導入の最も大きなポイントです。
垂直多関節ロボットの導入を検討している方は、しっかりと目的・用途・環境等を吟味した上でロボットのカスタマイズする事をおすすめします。
まとめ
このように近年では、様々な業界においてロボットが用いられるようになってきています。
背景には将来的な人口減少により生産年齢人口が減少することや、顧客のニーズを満たすようなロボットを製造することが出来るまでに技術が発展していることなどが挙げられます。
その中で産業用ロボットやサービス用ロボット、ペットロボットなど種類・業界は多岐に渡って活躍していくことでしょう。
色々な環境においてロボット化が進んでいることから、ロボットの定義は場所や人、状況によって様々なものとなっているようです。
また、「ロボット」は日本のお家芸であり常に世界の先陣を走っていました。
しかし、それに追いつこうと近頃ではインダストリー4.0やインダストリー・インターネット・コンソーシアム(IIC)など工場の自動化に注目が非常に集まってきています。
近年、中小企業でもこのような工場の自動化の事例は急速に増えてきています。
これはロボットがプログラミングによって動作を変更することができることの他、ロボットに付随するアプリケーションの発展があり、多品種少量に対応することが出来るようになった事も要因として挙げられます。
本記事ではロボットとはどのような種類があるのかを簡単にまとめてきました。
他の記事では、中小企業がロボット化を実現している事例なども紹介しておりますから、ロボット化をお考えの方のきっとお役に立つことと思います。
是非一度、ご覧になって下さい。
[clink url="https://smart-factory.funaisoken.co.jp/special/quality-improvement-through-inspection-quality-challenged-by-a-company-with-50-employees/"]
[clink url="https://smart-factory.funaisoken.co.jp/special/a-town-factory-with-40-colleagues-performs-100-inspection-using-robots/"]
[clink url="https://smart-factory.funaisoken.co.jp/special/robotization-of-stud-welding-process/"]
[clink url="https://smart-factory.funaisoken.co.jp/special/robotization-of-attachment-and-detachment-work-in-multiple-processing-machines/"]
ーーーーーーーーーーーーーーーーーーーーーーーーーーーーーーーーーー
自動化・ロボット化事例集 vol.2
本事例集は、全国の先進的な工場が取り組む「自動化・ロボット化」の事例をまとめたものとなります。
これから自動化・ロボット化に取組もうと考える皆さまに、
「工場にロボット・IoTを導入する」ための具体的なノウハウを、
事例を通して知っていただくことを目的に作成しました。
ーーーーーーーーーーーーーーーーーーーーーーーーーーーーーーーーーー
https://smart-factory.funaisoken.co.jp/download/automation-robotization-examples-02/