記事公開日:2025.01.17
最終更新日:2025.06.23
品質向上!生産性向上!を実現する現場改善の手法と事例
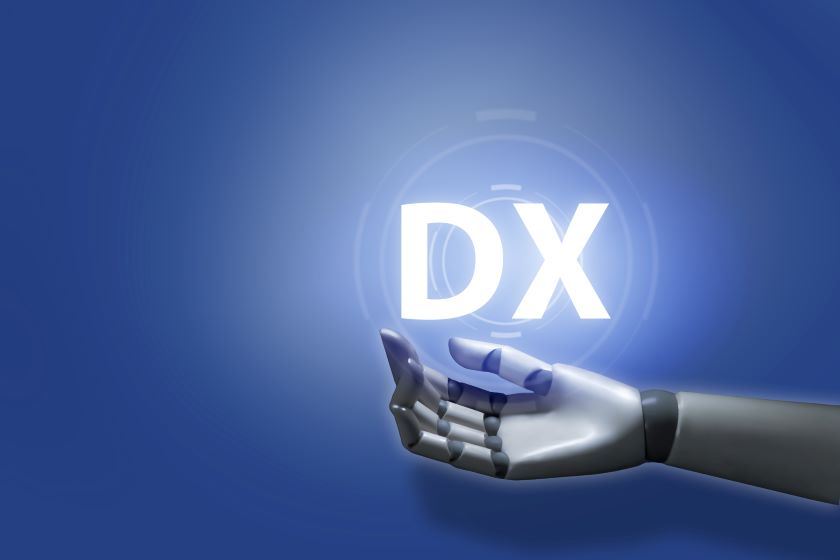
1.なぜ現場改善が必要なのか?
グローバル化の進展に伴い、製造業における競争は激化の一途を辿っています。顧客ニーズは
かつてないほど多様化し、製品ライフサイクルは短縮化しています。このような状況下では、
高品質な製品を効率的に生産し、市場の変化に迅速に対応できる企業だけが生き残ることがで
きます。
しかし、多くの企業では、以下のような問題を抱えています。
- 品質問題の発生: 人為的なミスや設備の不具合などにより、不良品が発生し、顧客からの信頼を失墜させてしまう。
- 生産性の低下: 非効率な作業やムダな工程により、生産性が低下し、コスト増加や納期遅延に繋がってしまう。
- 従業員のモチベーション低下: 単調な作業や過酷な労働環境により、従業員のモチベーションが低下し、離職率増加や人材不足に陥ってしまう。
これらの問題を解決し、企業の競争力を強化するためには、現場改善が不可欠です。現場改善
とは、現場の従業員が中心となり、日々の業務プロセスを見直し、改善していく活動です。
現場改善によって、以下のような効果が期待できます。
- 品質の向上: 不良品の発生原因を突き止め、再発防止策を講じることで、品質を向上させることができます。
- 生産性の向上: ムダな作業や工程を排除し、作業効率を改善することで、生産性を向上させることができます。
- コストの削減: 生産性向上や品質向上により、コストを削減することができます。
- 納期の短縮: 生産リードタイムを短縮することで、納期を短縮することができます。
- 従業員満足度の向上: 働きがいのある職場環境を作ることで、従業員のモチベーションを高め、定着率を向上させることができます。
- 顧客満足度の向上: 高品質な製品をタイムリーに提供することで、顧客満足度を向上させることができます。
現場改善は、単なるコスト削減のための活動ではありません。企業の競争力を強化し、持続的な成長を遂げるための重要な戦略なのです。
2.現場改善の基本的な考え方
現場改善を効果的に進めるには、いくつかの基本的な考え方を理解しておく必要があります。
① ムダの排除(トヨタ生産方式の考え方)
トヨタ生産方式では、あらゆるムダを徹底的に排除することが、品質向上と生産性向上に不可欠であると考えられています。
主なムダには、以下のようなものが挙げられます。
- 動作のムダ: 無駄な動きや移動
- 手待ちのムダ: 作業の待ち時間
- 不良品のムダ: 不良品の発生による手直しや廃棄
- 在庫のムダ: 過剰な在庫の保管
- 過剰品質のムダ: 必要以上の品質を求めること
- 運搬のムダ: 物品の移動
- 加工そのもののムダ: 工程や作業の順番、方法
これらのムダを徹底的に排除することで、資源の効率的な活用とコスト削減を実現し、競争力を強化することができます。
② 3S(整理・整頓・清掃)の徹底
3Sとは、「整理」「整頓」「清掃」の頭文字をとったもので、職場環境を改善するための基本的な活動です。
- 整理: 不要なものを捨てる
- 整頓: 必要なものを決められた場所に置く
- 清掃: 職場をきれいにする
3Sを徹底することで、作業効率が向上し、ミスや事故を防止することができます。また、清潔な職場は従業員のモチベーション向上にも繋がります。
③ 標準化と可視化
標準化とは、作業の手順や方法を統一することで、品質の安定化と作業効率の向上を図ることを指します。可視化とは、情報を分かりやすく表示することで、問題点を発見しやすくし、改善活動を促進することを指します。
標準化と可視化を推進することで、誰でも同じように作業ができ、問題点もすぐに把握できるため、効率的な改善活動が可能になります。
④従業員参加型改善 (カイゼン)
現場改善を成功させるためには、現場の従業員一人ひとりが積極的に改善活動に参加することが重要です。従業員一人ひとりが問題意識を持ち、改善提案を行うことで、より効果的な改善活動を進めることができます。
従業員参加型の改善活動は、従業員のモチベーション向上や人材育成にも繋がり、企業全体の活性化に貢献します。
これらの基本的な考え方を踏まえ、具体的な改善手法を導入することで、より効果的に現場改善を進めることができます。
3. 具体的な現場改善手法
現場改善には、様々な手法がありますが、ここでは代表的なものを紹介します。
① 5S活動 (整理・整頓・清掃・清潔・躾)
5Sは、職場環境を改善するための基礎的な活動です。3Sに「清潔」と「躾」を加えたもので、以下の5つの要素からなります。
- 整理: 不要なものを捨てる
- 整頓: 必要なものを決められた場所に置く
- 清掃: 職場をきれいにする
- 清潔: 整理・整頓・清掃を維持する
- 躾: 決められたルールを守る
5Sを徹底することで、作業効率が向上し、ミスや事故を防止することができます。また、清潔で整理整頓された職場は、従業員のモチベーション向上や企業イメージの向上にも繋がります。
②TPM (Total Productive Maintenance:全員参加の生産保全)
TPMは、設備の効率的な運用と保全を目的とした活動です。設備の故障を未然に防ぎ、設備の寿命を延ばすことで、生産性の向上とコスト削減を図ります。TPMでは、オペレーターを含む全ての従業員が設備保全に参加し、自主的な改善活動を行います。
③IE (Industrial Engineering:作業の効率化)
IEは、作業の効率化を図るための手法です。作業の動作分析や時間分析などを行い、ムダな動作や工程を排除することで、作業効率を向上させます。IEは、製造業だけでなく、サービス業や事務部門など、様々な分野で活用されています。
④QCサークル活動 (Quality Control Circle:小集団改善活動)
QCサークル活動は、従業員が小集団で自主的に行う改善活動です。現場の課題や問題点を共有し、解決策を検討することで、品質向上や生産性向上を図ります。QCサークル活動は、従業員のモチベーション向上やチームワーク強化にも効果があります。
⑤見える化 (カンバン方式、Andonなど)
見える化とは、情報を分かりやすく表示することで、問題点を発見しやすくし、改善活動を促進することを指します。カンバン方式は、生産現場における情報共有を目的とした手法で、Andonは、異常発生を知らせるためのシステムです。
⑥ポカヨケ (ヒューマンエラー防止)
ポカヨケとは、ヒューマンエラーを防止するための工夫です。作業ミスが起こらないように、作業手順や設備を改善することで、品質向上と安全性の向上を図ります。
⑦レイアウト改善 (作業動線の効率化)
レイアウト改善は、作業動線を改善することで、移動距離や作業時間を削減し、作業効率を向上させることを目的とした活動です。
これらの手法を組み合わせることで、より効果的に現場改善を進めることができます。
4. 現場改善の事例
現場改善がもたらす効果を、具体的な事例を通してご紹介します。
① 組立メーカーにおける意識改革とボトムアップ型改善
従業員30名規模の組立メーカー様では、長年、属人的な作業方法や整理整頓の不徹底、標準化の欠如といった課題を抱えていました。
当初、経営層は改善に消極的でしたが、従業員一人ひとりの意識を丁寧にヒアリングし、匿名アンケートを実施することで、現状への課題意識と改善への潜在的な意欲を可視化しました。
その結果を経営層にフィードバックすることで、意識改革を促し、ボトムアップ型の改善プロジェクトへと発展させることができました。
ポイント: 従業員の意見を丁寧に汲み上げ、可視化することで、経営層の意識改革を促し、ボトムアップ型の改善を促進することが可能です。
② レイアウト変更による物流倉庫の効率化
ある資材管理倉庫では、管理する資材に変更があったにも関わらず、長年レイアウトが固定化され、非効率な状態が続いていました。
現場リーダーは、現状における入出庫の遅延が生産性に悪影響を及ぼしていることを認識し、レイアウト変更と棚の入れ替え、収納ルールの変更を提案しました。
この提案は、入出庫にかかる時間を1/2に短縮できる可能性があり、人件費と設備コストの費用対効果を明確に示すことができました。
その結果、経営層の同意を得て、リーダー主導で改善プロジェクトを推進。導入後は、現場の意見が反映されたという実感から、従業員のモチベーション向上と更なる改善への意欲向上に繋がりました。
ポイント: 問題点を明確化し、具体的な改善策と費用対効果を示すことで、経営層の理解と協力を得やすくなります。
③ IEによるピッキング作業の効率化
多品種少量生産を行う製造現場では、ピッキング作業の非効率性が課題となっていました。
製造指示が前日夕方にならないと確定せず、各製造部署からバラバラに指示が出されるため、同じ資材を何度もピッキングする必要があり、ピッキング担当者は常に残業状態でした。
そこで、13時までに翌日製造予定を確定させ、製造指示書を一括管理するルールを導入。さらに、製造指示書のデータをシステム化し、品目と数量を正確に計算することで、ピッキング担当者は必要な情報を事前に把握できるようになりました。
その結果、ピッキング工数を2/3に短縮、残業時間を1/3に削減することに成功しました。
ポイント: 情報共有とシステム化による作業の標準化は、大幅な効率化に繋がります。
④ ポカヨケによる誤操作防止
複数のボタン操作を伴う製造現場では、誤操作による損失や災害発生のリスクが課題となっていました。
そこで、ポカヨケの考え方を導入し、以下の対策を実施しました。
- ボタンの形状や色分けによる識別性の向上
- 操作手順の明確化と表示
- 安全装置の設置
- ダブルチェック体制の導入
これらの対策により、誤操作を大幅に削減し、安全性を向上させることができました。
ポイント: ヒューマンエラーを防止するための工夫は、作業の安全性と品質向上に大きく貢献します。
5. 現場改善を成功させるためのポイント
現場改善を成功させるためには、以下のポイントを押さえることが重要です。
①経営層のコミットメントとリーダーシップ
現場改善は、全社的な取り組みとして推進することが重要です。そのためには、経営層が現場改善の重要性を理解し、積極的にコミットメントすることが必要です。また、経営層がリーダーシップを発揮し、現場を支援することで、改善活動をスムーズに進めることができます。
②現場の意見を尊重するボトムアップ型アプローチ
現場改善は、現場の従業員が中心となって進めることが重要です。そのため、現場の意見を尊重し、ボトムアップ型のアプローチを採用することが重要です。現場の従業員が積極的に改善活動に参加できるような環境を作ることで、より効果的な改善活動を進めることができます。
③PDCAサイクルによる継続的な改善
現場改善は、一度実施すれば終わりではありません。PDCAサイクル(Plan-Do-Check-Action)を回し、継続的に改善活動を行うことが重要です。改善活動の効果を測定し、問題点があれば改善策を検討することで、より効果的な改善活動を進めることができます。
④ 目標設定と効果測定
現場改善を行う際には、具体的な目標を設定することが重要です。目標を設定することで、改善活動の進捗状況を把握することができます。また、改善活動の効果を測定することで、改善活動の成果を可視化することができます。
⑤ ITツール活用による効率化
近年では、現場改善を支援するためのITツールが数多く開発されています。これらのITツールを活用することで、データ分析や情報共有を効率化し、より効果的な改善活動を進めることができます。
これらのポイントを踏まえ、計画的に現場改善を進めることで、企業の競争力を強化し、持続的な成長を遂げることができるでしょう。
6. 現場診断で現場改善のポイントを掴む
現場改善を成功させるためには、まず現状を正確に把握することが重要です。しかし、多くの企業では、自社の課題や問題点を客観的に把握することができていないのが現状です。
そこで、外部の専門家による現場診断が有効な手段となります。
船井総合研究所の製造業専門コンサルタントが現場改善のポイントを診断
船井総合研究所では、長年培ってきたコンサルティングノウハウを活かし、製造業の現場改善を支援しています。経験豊富なコンサルタントが、貴社の製造現場を訪問し、現状を詳細に分析いたします。
具体的には、以下の項目について診断を行います。
- 生産性: サイクルタイム、稼働率、不良率などを分析し、生産性の現状を把握します。
- 品質: 品質管理体制、検査体制などを分析し、品質管理の現状を把握します。
- コスト: 材料費、人件費、設備費などを分析し、コスト構造の現状を把握します。
- 納期: 納期遵守率、リードタイムなどを分析し、納期管理の現状を把握します。
- 安全: 安全管理体制、作業環境などを分析し、安全管理の現状を把握します。
- 従業員満足度: 従業員のモチベーション、働きがいなどを分析し、従業員満足度の現状を把握します。
3か月間の現場診断を通して製造現場の課題と解決策を提案
3か月間の現場診断を通して、貴社の製造現場における課題を明確化し、具体的な解決策を提案いたします。
例えば、以下のような課題に対して、具体的な解決策を提案いたします。
- 生産性が低い
- ボトルネック工程の特定と改善
- レイアウト改善による作業動線の効率化
- 設備の自動化による省人化
- 品質不良が多い
- 品質管理体制の強化
- 検査工程の標準化
- ポカヨケの導入
- コストが高い
- 材料費の削減
- 人件費の削減
- エネルギーコストの削減
- 納期が守れない
- 生産計画の見直し
- 在庫管理の改善
- 外注の活用
- 従業員のモチベーションが低い
- コミュニケーションの活性化
- 人材育成の強化
- 評価制度の見直し
現場診断を通して、貴社の製造現場の課題を明確化し、最適な解決策を提案することで、品質向上、生産性向上、コスト削減、納期短縮、従業員満足度向上など、様々な効果が期待できます。
■無料ダウンロードレポート
【このような方におすすめ】
- 他社と比べて、自社の製造現場における課題がわからない方
- 人口減少による製造現場の人材不足に悩んでいる方
- 製造現場の生産性向上を目指したい方
- 製造現場のDX推進の方法がわからない方
- 製造現場のコスト削減を実現したい方
ダウンロードはこちら
https://www.funaisoken.co.jp/dl-contents/smart-factory__03690_S045