記事公開日:2025.02.14
最終更新日:2025.08.26
工場における安全対策とは? 事例から学ぶ対策のポイントと製造業のリスク管理を紹介!
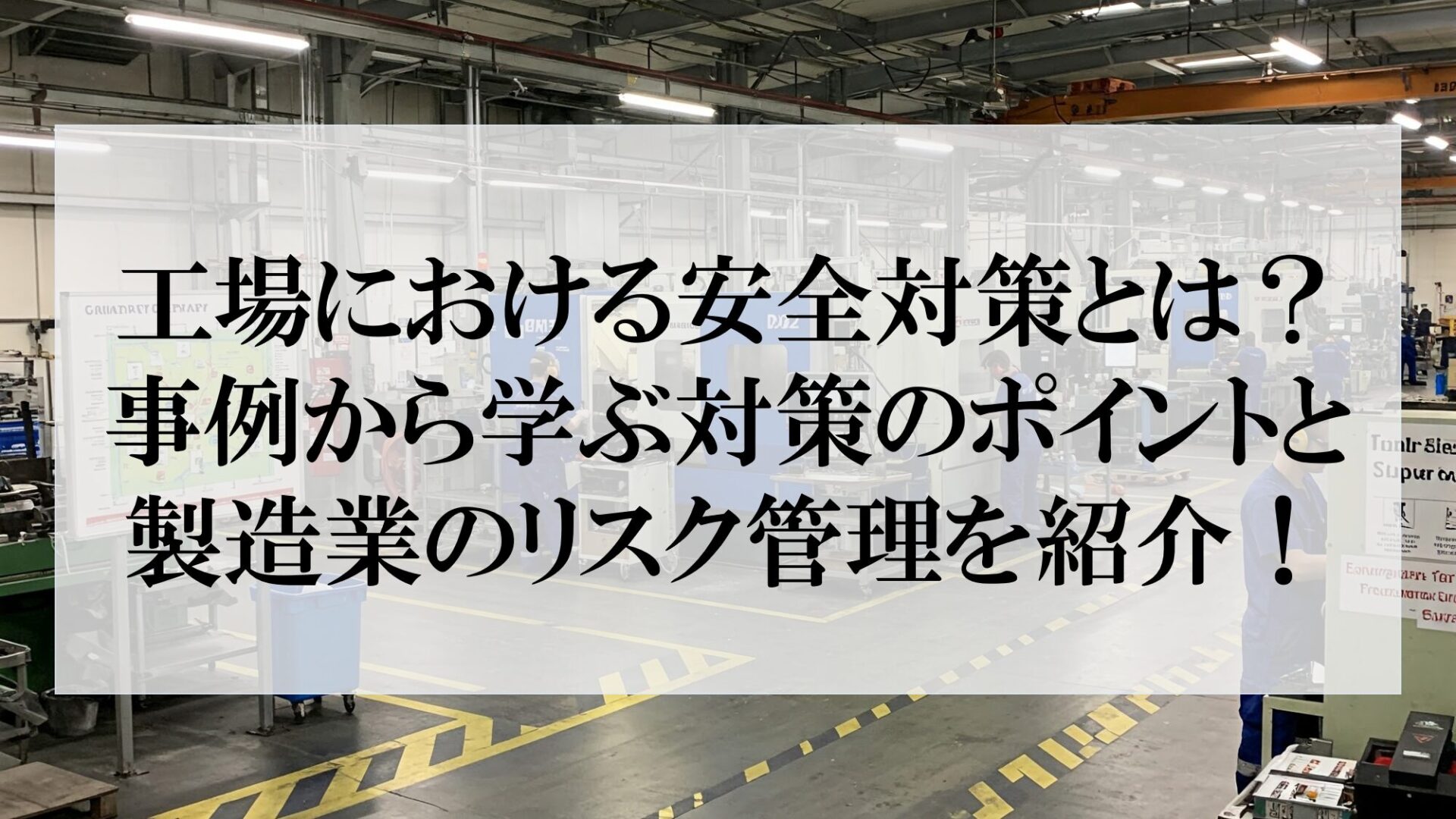
工場における安全対策は、作業者の安全確保と事故発生のリスク低減に必要不可欠です。
本記事では、工場で発生するさまざまな事故のリスクと、安全対策のポイントを事例を交えながら解説します。
機械の安全管理から現場作業におけるリスク管理まで、製造業に携わる全ての方に役立つ情報をご紹介します。
目次
1.はじめに:なぜ工場における安全対策が重要視されるのか?
日本の製造業は、世界的に見ても高い技術力と品質を誇り、経済成長を支える重要な役割を担っています。しかし、その一方で、工場における労働災害は依然として発生しており、尊い命が失われたり、大きな怪我を負ってしまう事故も後を絶ちません。工場における安全対策は、労働者・作業員の安全と健康を守るだけでなく、企業の生産活動を維持し、社会的な信頼を得る上でも非常に重要な取り組みです。
1.1.労働災害の現状と課題
厚生労働省の調査によると、令和4年の労働災害による死傷者数は8万件を超え、そのうち製造業における割合が最も高くなっています。特に、中小規模の工場では、安全対策が十分に行われていないケースも多く、労働災害発生のリスクが高い状況です。労働災害は、個人の不幸だけでなく、企業の生産性低下やイメージダウンにもつながるため、早急な対策が必要です。
1.2.工場における安全対策の必要性
工場では、機械設備や化学物質の取り扱い、高所作業など、さまざまな危険が潜んでいます。これらの危険源を特定し、適切な安全対策を講じることで、労働災害の発生を未然に防ぐことが可能です。また、安全対策は、労働者のモチベーション向上や生産性向上にもつながり、企業全体の発展に貢献します。安全な職場環境は、従業員・作業員の定着率向上にもつながり、人材不足の解消にも役立ちます。
1.3.本記事で得られること
本記事では、工場で起こりうる事故の種類や原因、安全対策の基礎知識、具体的な対策事例、安全対策の進め方など、工場における安全対策に関するあらゆる情報を網羅的に解説します。この記事を読むことで、工場における安全対策の重要性を再認識し、自社の安全対策をより強化するためのヒントを得ることができます。安全対策に関する知識を深めることで、より安全な職場環境を構築し、労働災害ゼロを目指しましょう。
2.工場で起こる事故の種類と原因
工場では、さまざまな種類の事故が発生する可能性があります。ここでは、代表的な事故の種類と原因について解説します。
2.1. 転倒・転落事故
転倒・転落事故は、工場で最も多く発生する事故の一つです。床面の段差や滑りやすい場所での作業、通路の障害物などが原因で発生します。特に、雨の日や清掃直後など、床が濡れている状況では、転倒のリスクが高まります。また、作業者の不注意や、急いで移動する際にも転倒事故が起こりやすいです。
2.2. 挟まれ・巻き込まれ事故
挟まれ・巻き込まれ事故は、機械設備の不適切な操作やメンテナンス不足、安全装置の未設置などが原因で発生します。重大な怪我につながるケースが多く、特に注意が必要です。機械の点検・整備時には、必ず電源を切り、安全ロックをかけるなど、安全対策を徹底する必要があります。また、作業者は、機械の操作手順を十分に理解し、安全装置の正しい使い方を習得する必要があります。
2.3. 衝突事故
衝突事故は、フォークリフトなどの運搬車両の操作ミスや、作業者の不注意などが原因で発生します。作業スペースの確保や安全通路の確保が重要です。特に、狭い場所や見通しの悪い場所での作業は、衝突のリスクが高まります。フォークリフトの運転者は、運転資格を取得し、安全運転を心がける必要があります。また、作業者は、運搬車両の通行ルートを把握し、注意しながら作業する必要があります。
2.4. 火災・爆発事故
火災・爆発事故は、可燃性物質の取り扱いミスや、電気系統の不具合などが原因で発生します。初期消火の徹底や、火災発生時の避難経路の確保が重要です。工場では、可燃性物質の保管場所や取り扱い方法を明確にし、火災発生時の対応マニュアルを作成しておく必要があります。また、定期的な消防訓練を実施し、従業員が適切な消火活動や避難行動をとれるようにする必要があります。
2.5. 感電事故
感電事故は、電気設備の絶縁不良や、作業者の不注意などが原因で発生します。電気設備の定期的な点検や、作業者の安全教育が重要です。電気設備は、定期的に点検し、絶縁不良箇所を修理する必要があります。また、電気作業を行う際は、資格のある作業者が行い、安全対策を徹底する必要があります。作業者は、電気に関する知識を習得し、感電の危険性を理解する必要があります。
2.6. 化学物質による事故
化学物質による事故は、化学物質の漏洩や誤使用などが原因で発生します。MSDS(安全データシート)の活用や、適切な保護具の着用が重要です。化学物質を使用する際は、MSDSをよく読み、安全な取り扱い方法を確認する必要があります。また、化学物質の保管場所や使用量を適切に管理し、漏洩時の対応マニュアルを作成しておく必要があります。作業者は、化学物質の危険性を理解し、適切な保護具を着用する必要があります。
2.7. その他(熱中症、有害物質など)
その他にも、熱中症や有害物質による事故が発生する可能性があります。作業環境の改善や、作業者の健康管理が重要です。特に、夏場の高温多湿な環境下では、熱中症のリスクが高まります。作業場所の換気を良くしたり、休憩時間を確保するなど、熱中症対策を講じる必要があります。また、有害物質を取り扱う際は、適切な保護具を着用し、作業環境を管理する必要があります。
2.8. 事故原因の分析と対策
事故が発生した際は、原因を徹底的に分析し、再発防止対策を講じることが重要です。事故調査委員会を設置し、事故状況、原因、対策などを記録することで、今後の安全対策に役立てることができます。事故原因の分析には、5W1H(いつ、どこで、誰が、何を、なぜ、どのように)などの手法を活用し、多角的な視点から原因を究明することが重要です。
3.工場における安全対策の基礎知識
工場における安全対策は、労働者の安全を確保し、事故を未然に防ぐために不可欠な取り組みです。ここでは、安全対策の基礎知識について解説します。
3.1. 安全とは?
安全とは、危険な状態がなく、安心して作業できる環境のことです。工場における安全は、労働者の身体的な安全だけでなく、精神的な安定も含まれます。安全な職場環境は、労働者のモチベーション向上や生産性向上にもつながります。また、安全な職場環境は、企業のイメージアップにもつながり、優秀な人材の確保にも役立ちます。
3.2. 安全対策の基本原則
安全対策の基本原則は、危険源を特定し、リスクを評価し、適切な対策を講じることです。具体的には、以下の3つの原則が重要です。
- 危険源の除去:危険な設備や作業をできる限り排除する
- 安全対策の実施:危険源を除去できない場合は、安全装置を設置したり、作業方法を改善したりする
- 保護具の着用:安全対策だけでは防ぎきれないリスクに対して、保護具を着用する
これらの原則を基に、具体的な安全対策を講じることで、労働災害の発生を未然に防ぐことができます。
3.3. リスクアセスメントとは?
リスクアセスメントとは、作業における危険源を特定し、リスクを評価し、適切な対策を講じるための手法です。リスクアセスメントは、労働災害を未然に防ぐために重要な取り組みです。リスクアセスメントを実施することで、潜在的な危険源を洗い出し、適切な対策を講じることができます。また、リスクアセスメントの結果は、安全教育や訓練の教材としても活用できます。
3.4. 危険源の特定とリスクの評価
危険源の特定は、作業現場を隈なく調査し、潜在的な危険源を洗い出すことから始めます。リスクの評価は、危険源が現実化した場合に、どの程度の被害が発生するかを評価します。危険源を特定する際は、作業者の意見を聞き取り、現場の状況を把握することが重要です。また、過去の事故事例やヒヤリハット事例を参考にすることも有効です。
3.5. 対策の優先順位付け
リスクアセスメントの結果に基づいて、対策の優先順位を決定します。最もリスクの高いものから優先的に対策を講じることが重要です。対策の優先順位を決定する際は、リスクの大きさだけでなく、対策の費用や効果なども考慮する必要があります。また、緊急性の高いものや、多数の作業者に影響を与えるものから優先的に対策を講じる必要があります。
4.労働安全衛生法とは?
労働安全衛生法は、労働者の安全と健康を確保するために制定された法律です。工場における安全対策は、労働安全衛生法に基づいて行われます。
4.1. 労働安全衛生法の概要
労働安全衛生法は、事業者の義務と責任、安全衛生管理体制、安全衛生教育制度、作業環境管理、健康管理などについて定めています。労働安全衛生法は、事業者が労働者の安全と健康を確保するための最低限の基準を定めたものであり、事業者は、労働安全衛生法を遵守し、労働者の安全と健康を確保する必要があります。
4.2. 事業者の義務と責任
事業者は、労働者の安全と健康を確保するために、必要な措置を講じる義務があります。具体的には、安全衛生管理体制の構築、安全衛生教育の実施、作業環境の改善、健康管理の実施などが挙げられます。事業者は、労働安全衛生法に基づき、安全衛生管理計画を作成し、計画的に安全対策を実施する必要があります。また、労働者からの意見や要望を尊重し、安全対策に反映させることも重要です。
4.3. 安全衛生管理体制
事業者は、労働者の安全と健康を管理するために、安全衛生管理体制を構築する必要があります。具体的には、安全管理者、衛生管理者、産業医などの選任が必要です。安全管理者は、工場全体の安全管理を担当し、安全衛生教育の実施や、安全対策の推進を行います。衛生管理者は、労働者の健康管理を担当し、健康診断の実施や、健康相談に応じます。産業医は、労働者の健康状態を把握し、健康上の問題があれば適切なアドバイスを行います。
4.4. 罰則規定
労働安全衛生法に違反した場合、罰則が科せられることがあります。事業者は、労働安全衛生法を遵守し、労働者の安全と健康を確保する必要があります。罰則の内容は、違反の程度によって異なり、懲役や罰金などが科せられます。また、重大な労働災害が発生した場合は、事業者の責任が問われることもあります。
5.工場における具体的な安全対策
工場における安全対策は、機械設備の安全対策、作業環境の安全対策、作業者の安全対策、化学物質の安全対策、火災・爆発対策など、多岐にわたります。ここでは、具体的な安全対策について解説します。
5.1. 機械設備の安全対策
機械設備の安全対策は、挟まれ・巻き込まれ事故を防止するために重要です。具体的には、安全装置の設置、定期的な点検・メンテナンス、作業手順書の作成などが挙げられます。機械設備は、定期的に点検し、不具合があれば直ちに修理する必要があります。また、機械の操作手順やメンテナンス手順を明確に記載した作業手順書を作成し、作業者が遵守する必要があります。
5.2. 安全装置の設置と点検
機械設備には、安全装置が設置されている必要があります。安全装置が正常に作動するか定期的に点検し、不具合があれば直ちに修理する必要があります。安全装置には、非常停止ボタン、安全カバー、インターロック装置などがあります。これらの装置が正常に作動することで、事故を未然に防ぐことができます。
5.3. 作業手順書の作成と遵守
機械設備の操作手順やメンテナンス手順を明確に記載した作業手順書を作成し、作業者が遵守する必要があります。作業手順書は、作業者が安全に作業を行うための指針となります。作業手順書を作成する際は、作業者の意見を聞き取り、現場の状況を把握することが重要です。
5.4. 異常時の対応マニュアル
機械設備に異常が発生した場合の対応マニュアルを作成し、作業者が適切に対応できるようにする必要があります。異常発生時の対応マニュアルには、連絡先、避難経路、応急処置などが記載されています。
5.5. 作業環境の安全対策
作業環境の安全対策は、転倒・転落事故や衝突事故を防止するために重要です。具体的には、整理整頓(5S)の徹底、照明、換気、温度管理、通路の確保と表示などが挙げられます。
5.6. 整理整頓(5S)の徹底
整理整頓(5S)とは、整理、整頓、清掃、清潔、しつけの頭文字をとったもので、作業環境を改善するための活動です。5Sを徹底することで、転倒・転落事故や衝突事故を防止することができます。整理とは、不要なものを処分し、必要なものだけを置くことです。整頓とは、必要なものを使いやすい場所に置き、表示を明確にすることです。清掃とは、作業場所を清潔に保ち、不具合箇所を早期に発見することです。清潔とは、整理、整頓、清掃の状態を維持することです。しつけとは、決められたことを守り、習慣化することです。
5.7. 照明、換気、温度管理
適切な照明、換気、温度管理は、作業者の疲労を軽減し、集中力を高めるために重要です。照明が不足していると、作業者の視力が低下し、事故につながる可能性があります。また、換気が不十分だと、作業環境が汚染され、健康被害を引き起こす可能性があります。適切な温度管理は、作業者の体調を維持し、熱中症などを予防するために重要です。
5.8. 通路の確保と表示
通路を確保し、表示を明確にすることで、作業者の移動を安全にすることができます。通路が狭かったり、障害物が多いと、作業者がつまずいたり、衝突したりする可能性があります。通路には、通行方向や制限速度などを表示し、作業者が安全に通行できるようにする必要があります。
5.9. 作業者の安全対策
作業者の安全対策は、保護具の着用、安全教育と訓練、健康管理などが挙げられます。
5.10. 保護具の着用
作業者は、作業内容に応じて適切な保護具(ヘルメット、安全靴、保護メガネなど)を着用する必要があります。保護具は、作業者の身体を危険から守るために重要なものです。作業者は、保護具の正しい着用方法を理解し、作業中は必ず着用する必要があります。
5.11. 安全教育と訓練
作業者は、安全に関する知識や技能を習得するために、安全教育と訓練を受ける必要があります。安全教育は、新入社員教育や定期的な安全衛生教育などがあります。安全訓練は、消火訓練や避難訓練などがあります。安全教育や訓練を通じて、作業者は、危険に対する意識を高め、適切な対応をとれるようにする必要があります。
5.12. 健康管理
事業者は、作業者の健康管理を行い、健康診断の実施や、健康相談の窓口を設ける必要があります。健康管理は、作業者の健康状態を把握し、健康上の問題があれば早期に対応するために重要です。事業者は、定期的に健康診断を実施し、作業者の健康状態を把握する必要があります。また、健康相談窓口を設け、作業者が健康上の悩みを相談できる環境を整える必要があります。
5.13. 化学物質の安全対策
化学物質の安全対策は、化学物質による事故を防止するために重要です。具体的には、MSDS(安全データシート)の活用、保管と取り扱い、漏洩時の対応などが挙げられます。
5.14. MSDS(安全データシート)の活用
MSDS(安全データシート)とは、化学物質の危険性や取り扱い方法に関する情報が記載された書類です。化学物質を使用する際は、MSDSをよく読み、安全な取り扱い方法を確認する必要があります。MSDSには、化学物質の名称、成分、危険性、取り扱い方法、緊急時の対応などが記載されています。
5.15. 保管と取り扱い
化学物質は、種類に応じて適切な場所で保管し、取り扱い方法を遵守する必要があります。化学物質は、保管場所や取り扱い方法を誤ると、火災や爆発、中毒などを引き起こす可能性があります。化学物質の保管場所は、通気性の良い場所や、直射日光の当たらない場所を選ぶ必要があります。また、化学物質の種類に応じて、保管容器や保管方法を適切に選ぶ必要があります。
5.16. 漏洩時の対応
化学物質が漏洩した場合の対応マニュアルを作成し、作業者が適切に対応できるようにする必要があります。化学物質が漏洩した場合、適切な保護具を着用し、二次災害を防止することが重要です。漏洩した化学物質の種類や量に応じて、適切な処理方法を選択する必要があります。処理方法が不明な場合は、専門業者に依頼することを検討しましょう。
5.17. 火災・爆発対策
火災・爆発対策は、可燃性物質の取り扱い、消火設備の設置、緊急時の避難経路の確保などが挙げられます。
5.18. 消火設備の設置と点検
工場には、適切な消火設備(消火器、スプリンクラーなど)を設置し、定期的に点検する必要があります。消火設備は、火災発生時に初期消火を行うために重要なものです。消火設備の設置場所や種類は、工場の規模や業種、取り扱う物質によって異なります。
5.19. 可燃物の管理
可燃物は、適切に管理し、火災の原因となる可能性を低減する必要があります。可燃物は、指定された場所に保管し、火気厳禁の場所では使用しないようにしましょう。また、可燃物の保管量や保管方法についても、法令で定められた基準を遵守する必要があります。
5.20. 緊急時の避難経路確保
火災発生時などに、作業者が安全に避難できる経路を確保しておく必要があります。避難経路は、複数確保しておくと、万が一の場合にも対応できます。また、避難経路には、誘導灯や避難標識を設置し、作業者が迷わずに避難できるようにする必要があります。
6.製造業における安全対策のポイント
製造業における安全対策は、製造工程におけるリスク、工程別安全対策事例、設備のレイアウトと配置、作業動線の改善、安全意識の向上などが挙げられます。
6.1. 製造工程におけるリスク
製造工程では、さまざまな危険が潜んでいます。これらの危険を特定し、適切な安全対策を講じる必要があります。製造工程における危険には、機械設備の不具合、作業者の不注意、環境要因などがあります。これらの危険を特定し、それぞれの原因に応じた対策を講じる必要があります。
6.2. 工程別安全対策事例
製造工程における安全対策は、工程ごとに異なります。各工程におけるリスクを分析し、適切な対策を講じる必要があります。例えば、組み立て工程では、部品の落下や工具の誤使用による事故が起こりやすいです。これらの事故を防ぐために、部品の固定や工具の点検、作業者の安全教育などが重要になります。
6.3. 設備のレイアウトと配置
設備のレイアウトと配置は、作業者の安全に大きな影響を与えます。作業動線を考慮し、安全なレイアウトと配置にする必要があります。設備の配置が悪いと、作業者が移動する際に障害物にぶつかったり、機械に巻き込まれたりする危険があります。設備のレイアウトを検討する際は、作業動線を分析し、無駄な移動や危険な場所がないように配慮する必要があります。
6.4. 作業動線の改善
作業動線を改善することで、作業者の移動距離を減らし、衝突事故などのリスクを低減することができます。作業動線を改善するには、設備の配置を見直したり、作業方法を変更したりする必要があります。作業動線を改善することで、作業効率も向上する可能性があります。
6.5. 安全意識の向上
安全対策は、作業者の安全意識の向上によって、より効果を発揮します。安全教育やKYT(危険予知訓練)などを通じて、作業者の安全意識を高める必要があります。安全意識が高い作業者は、危険な状況に気づきやすく、事故を未然に防ぐことができます。また、安全意識が高い作業者は、安全対策を遵守し、安全な作業を心がけます。
6.6. 危険予知活動(KYT)
KYTとは、作業前に危険を予知し、対策を講じる活動です。KYTを実践することで、事故を未然に防ぐことができます。KYTは、グループで行うことが多く、作業者同士で意見交換をすることで、危険に対する認識を高めることができます。
6.7. ヒヤリハット事例の活用
ヒヤリハットとは、事故には至らなかったものの、ヒヤリとしたり、ハッとしたりする事例のことです。ヒヤリハット事例を分析し、共有することで、事故の未然防止に役立てることができます。ヒヤリハット事例は、小さなミスや不注意が大きな事故につながる可能性を示唆しています。ヒヤリハット事例を収集し、分析することで、潜在的な危険源を把握し、対策を講じることができます。
・関連記事
【工場のヒヤリハット事例を解説】原因と対策方法を紹介! 報告を活かして事故防止
https://smart-factory.funaisoken.co.jp/250204-3/
7.安全対策の進め方
安全対策は、段階的な導入、PDCAサイクル、計画(Plan)、実行(Do)、評価(Check)、改善(Action)などの手順で進めることが重要です。
7.1. 段階的な導入
安全対策は、一度にすべてを実施するのではなく、段階的に導入していくことが効果的です。段階的に導入することで、費用や手間を分散させることができます。また、従業員の理解と協力を得ながら、徐々に安全対策を定着させることができます。
7.2. PDCAサイクル
PDCAサイクルとは、計画(Plan)、実行(Do)、評価(Check)、改善(Action)の頭文字をとったもので、業務改善の手法の一つです。PDCAサイクルを回すことで、安全対策を継続的に改善することができます。計画段階では、安全対策の目標や計画を立てます。実行段階では、計画に基づいて安全対策を実施します。評価段階では、安全対策の効果を評価します。改善段階では、評価結果に基づいて、安全対策を改善します。
計画(Plan)
安全対策の計画を立てます。具体的には、リスクアセスメントの実施、対策の選定、目標設定などを行います。リスクアセスメントでは、工場内の危険源を特定し、それぞれのリスクを評価します。対策の選定では、リスクを低減するための具体的な対策を検討します。目標設定では、安全対策の達成目標を設定します。
実行(Do)
計画に基づいて、安全対策を実行します。具体的には、設備の設置、作業手順書の作成、安全教育の実施などを行います。設備の設置では、安全装置や保護具などを設置します。作業手順書の作成では、安全な作業方法を定めます。安全教育の実施では、従業員に安全に関する知識や技能を教えます。
評価(Check)
安全対策の効果を評価します。具体的には、事故発生状況の分析、作業者のアンケート調査などを行います。事故発生状況の分析では、事故の発生件数や原因などを調べます。作業者のアンケート調査では、安全対策に対する満足度や意見などを聞きます。
改善(Action)
評価結果に基づいて、安全対策を改善します。具体的には、設備の改善、作業手順書の修正、安全教育の見直しなどを行います。設備の改善では、安全装置の改良や保護具の改善などを行います。作業手順書の修正では、より安全な作業方法を検討します。安全教育の見直しでは、教育内容や教育方法を見直します。
8.安全対策に役立つツールとサービス
安全対策には、安全管理システム、リスクアセスメントツール、安全教育コンテンツ、専門家によるコンサルティングなど、さまざまなツールとサービスが役立ちます。
8.1. 安全管理システム
安全管理システムとは、安全管理に関する情報を一元管理するシステムです。安全管理システムを活用することで、安全管理業務の効率化や、リスク管理の強化を図ることができます。安全管理システムには、事故情報管理機能、教育管理機能、点検管理機能などがあります。これらの機能を活用することで、安全管理業務を効率的に行うことができます。
8.2. リスクアセスメントツール
リスクアセスメントツールとは、リスクアセスメントを効率的に行うためのツールです。リスクアセスメントツールを活用することで、リスクの特定や評価を容易に行うことができます。リスクアセスメントツールには、チェックリスト形式のものや、ソフトウェア形式のものなどがあります。
8.3. 安全教育コンテンツ
安全教育コンテンツとは、安全教育に必要な教材です。安全教育コンテンツを活用することで、効果的な安全教育を実施することができます。安全教育コンテンツには、動画形式のものや、テキスト形式のものなどがあります。
8.4. 専門家によるコンサルティング
専門家によるコンサルティングを受けることで、自社の安全対策の課題や改善点などを把握することができます。専門家は、豊富な知識や経験に基づいて、適切なアドバイスや指導を行います。
9.事例から学ぶ安全対策
過去の事故事例や安全対策の成功事例、失敗事例などを分析し、教訓や学びを得ることは、安全対策を推進する上で非常に重要です。
9.1. 実際の事故例とその原因
過去に発生した事故例とその原因を分析することで、同様の事故を未然に防ぐことができます。事故例を分析する際は、5W1Hなどの手法を活用し、多角的な視点から原因を究明することが重要です。
9.2. 対策事例
事故例を踏まえて、どのような対策が有効かを検討します。具体的な対策事例を参考に、自社に合った対策を検討することが重要です。対策事例を検討する際は、費用対効果や実現可能性なども考慮する必要があります。
9.3. 成功事例
安全対策に成功した事例を参考に、自社の安全対策を推進することができます。成功事例から、どのような取り組みが効果的なのかを学ぶことができます。成功事例を参考にする際は、自社の状況と照らし合わせ、適切な方法を取り入れることが重要です。
9.4. 失敗事例
安全対策に失敗した事例を参考に、同様の失敗を繰り返さないようにする必要があります。失敗事例から、どのような点に注意すべきかを学ぶことができます。失敗事例を参考にする際は、原因を深く分析し、二度と繰り返さないように対策を講じることが重要です。
9.5. 教訓と学び
各組織図の業務所掌を明確にし、それぞれの役割を明確化することにより、「誰がどの責任のもと業務を進める」ということが分かるようになり、会社として業務を進めやすくなります。責任体制が明確になることで、業務の進捗管理や問題発生時の対応が迅速かつ適切に行われるようになります。
9.6. 部署横断的な改善活動の推進
事故事例や対策事例から得られた教訓や学びは、今後の安全対策に活かす必要があります。教訓や学びを共有し、組織全体の安全意識を高めることが重要です。教訓や学びを共有するには、社内報や安全会議などを活用することが有効です。また、過去の事故やヒヤリハット事例をデータベース化し、従業員がいつでも閲覧できるようにすることも効果的です。
10. 安全対策に関するQ&A
工場における安全対策に関するよくある質問とその回答をまとめました。
Q:安全対策は、どのくらいの頻度で実施する必要がありますか?
A:安全対策は、定期的に見直し、必要に応じて改善する必要があります。また、法令で定められた点検や教育などは、定期的に実施する必要があります。安全対策の実施頻度は、工場の規模や業種、取り扱う物質によって異なります。定期的にリスクアセスメントを実施し、必要に応じて安全対策を見直すことが重要です。
Q:安全対策には、どのくらいの費用がかかりますか?
A:安全対策にかかる費用は、工場の規模や業種、対策の内容によって異なります。しかし、安全対策は、労働災害による損失を未然に防ぐための投資と考えることができます。安全対策を適切に行うことで、長期的に見るとコスト削減につながる可能性があります。
Q:安全対策に関する情報は、どこで入手できますか?
A:労働安全衛生総合研究所のウェブサイトや、厚生労働省のウェブサイトなどで、安全対策に関する情報を入手することができます。これらのウェブサイトでは、労働安全衛生法に関する情報や、安全対策に関する事例、ツールなどが紹介されています。また、専門家によるコンサルティングを受けることも可能です。
11. まとめ:工場における安全対策の重要性と継続的な取り組み
工場における安全対策は、労働者の安全と健康を守るだけでなく、企業の生産活動を維持し、社会的な信頼を得る上でも非常に重要です。労働災害を未然に防ぐためには、危険源を特定し、リスクを評価し、適切な対策を講じる必要があります。また、安全対策は、一度実施したら終わりではなく、継続的に改善していくことが重要です。安全対策は、企業の経営戦略の一環として捉え、長期的な視点で取り組む必要があります。
本記事で紹介した情報は、一般的な安全対策に関するものであり、すべての工場に当てはまるわけではありません。各工場の状況に合わせて、適切な安全対策を講じる必要があります。
今回の内容に限らず、下記のようなことを感じられた場合はお気軽にお問い合わせください。
- 自社ではこういう課題があるんだけど・・・
- こういった場合はどのような取り組みが出来るのか?
- この部分について興味がある。
12. 関連情報
- 工場の組織について相談してみる(無料相談も可能)
https://formslp.funaisoken.co.jp/form01/lp/post/inquiry-S045.html?siteno=S045 - 【工場の改善事例100選】小さなアイデア&ネタで収益UP! 製造業の改善提案例を紹介
https://smart-factory.funaisoken.co.jp/250123-2/ - 【製造業向け】現場を巻き込んだ業務改善で外せない重要なポイントとは
https://www.funaisoken.co.jp/dl-contents/smart-factory_smart-factory_03657_S045 - 【社長特別インタビュー】IoT×AIで製造業革命!従業員14名で売上1.75倍を達成した会社とは?
https://www.funaisoken.co.jp/dl-contents/smart-factory_smart-factory_03729_S045 - IoT導入による工場の見える化とは?成功事例と現場改革におけるメリット・注意点を紹介
https://smart-factory.funaisoken.co.jp/250108-2/
今回では、工場の安全対策について事例をもとに説明をしてまいりました。
弊社が主催している下記セミナーでは、自社の生き残りをかけたDXの取組を、実際の事例をもとにお話ししています。
改めて、下記のような課題を抱えられている方はぜひご参加ください。