記事公開日:2025.04.14
最終更新日:2025.04.14
『もうダメか…』からのV字回復! ある町工場のAI外観検査導入物語
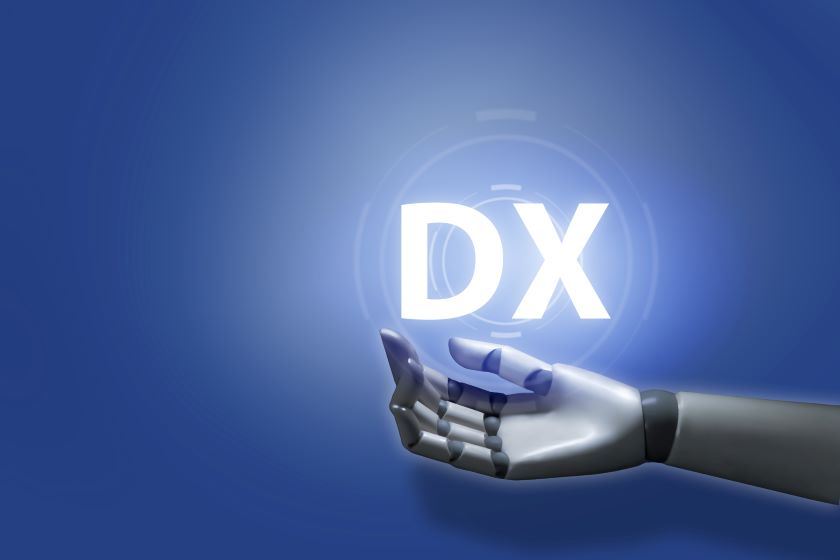
日本のものづくりを支える製造業。しかし今、多くの中小製造業が、深刻な課題に直面しています。熟練技術者の高齢化と後継者不足、若手人材の採用難、そして激化する価格競争と高度化する品質要求…。中でも、「外観検査」の工程は、多くの企業にとって頭の痛い問題ではないでしょうか。
「人手が足りず、検査が追いつかない」
「検査員の経験や勘に頼るしかなく、品質が安定しない」
「不良品の見逃しで、顧客からのクレームが発生してしまった」
「自動化したいが、過去に画像検査で失敗した経験がある」
「AIが良いと聞くけれど、ウチみたいな会社には無理だろう…」
もし、このような悩みを抱え、日々の業務に追われながらも、心のどこかで「このままではいけない」「何かを変えなければ」と感じているなら、ぜひこのコラムを読み進めてください。
これは、まさに同じような苦境に立たされながらも、AI外観検査という新しい技術への挑戦を決意し、数々の試練を乗り越え、奇跡的な再生を遂げた、ある町工場「田中精密工業(仮名)」の物語です。彼らの軌跡は、きっと、あなたの会社の未来を切り拓くための、勇気とヒントを与えてくれるはずです。
目次
第一章:迫りくる危機と経営者の苦悩
田中精密工業は、創業から30年、自動車産業向けの中小精密部品を手掛ける、地域では名の知れた企業でした。かつては右肩上がりの成長を続けていましたが、ここ数年は売上が横ばい、いや、微減傾向にありました。新興国メーカーの台頭、EV化の流れによる部品需要の変化、そして原材料費や人件費の高騰が、経営をじわじわと圧迫していたのです。
田中社長の最大の悩みは、工場の片隅にある「検査室」に象徴されていました。十数名のパート従業員が、小さな部品の傷やバリを目で見てチェックする、昔ながらの目視検査。勤続20年のベテラン鈴木さんの「神の目」が品質を支えていましたが、彼女も高齢化し、後継者は育っていません。そもそも人手不足で、検査員の確保自体が困難になっていました。
人間である以上、見逃し(ヒューマンエラー)のリスクは常に付きまといます。数ヶ月に一度発生する顧客からのクレームは、会社の信用を揺るがし、対応コストも甚大でした。年間数千万円に上る検査員の人件費も、利益を圧迫する大きな要因です。
「この検査工程を自動化できれば…」
田中社長はそう考え、数年前に一度、画像検査装置の導入を検討しました。しかし、複雑な形状の部品や、光沢のある金属部品の検査では、期待した精度が出ず、導入を断念。その時の苦い経験は、「検査の自動化は難しい」という固定観念を、田中社長の中に深く植え付けていました。
そんな中、追い打ちをかけるように、競合の山田製作所がAI検査システムを導入したという噂が耳に入ります。時代の変化に取り残されていく焦燥感。何かを変えなければならない。しかし、何をどうすれば良いのか分からない…。田中社長は、繰り返される日常の中で、深い閉塞感と孤独感に苛まれていたのです。
田中社長が抱えていた悩みは、決して彼だけの特殊なものではありません。多くの中小製造業が、同様の構造的な問題を抱えています。
属人化のリスク: 熟練者の経験と勘に依存した工程は、その人がいなくなれば維持できません。技術承継は、多くの企業にとって喫緊の課題です。
品質の不安定さ: 人間の集中力や体調は一定ではありません。見逃しや判定基準のばらつきは、不良流出や歩留まり悪化に直結します。
コスト増加: 人件費の高騰に加え、採用・教育コスト、不良対応コストなど、目視検査には多くのコストが付随します。
人手不足: そもそも、検査工程のような根気のいる仕事の担い手を確保すること自体が、年々難しくなっています。
自動化の壁: 従来の画像検査技術では、複雑な形状、多様な材質、微妙な欠陥などに対応しきれず、自動化を断念したケースも少なくありません。
これらの問題は、放置すれば企業の競争力を確実に蝕んでいきます。では、どうすればこの状況を打破できるのか?近年、その解決策として急速に注目を集めているのが「AI(人工知能)」、特に「ディープラーニング(深層学習)」を活用した外観検査なのです。
AI外観検査は、大量の画像データを学習することで、人間が言葉で定義できないような複雑な特徴やパターンを自ら認識し、高精度な判定を可能にします。熟練者の「目」を再現するだけでなく、客観的で安定した検査を24時間365日行うことができるのです。
しかし、「AI」と聞くと、「難しそう」「高そう」「ウチには関係ない」と感じてしまう経営者も多いのではないでしょうか?田中社長も、当初はそうでした。しかし、ある出会いが、彼の考えを大きく変えることになります。
第二章:一通のDMと、セミナーでの出会い
それは、絶望的な状況の中で、田中社長が偶然手に取った一通のダイレクトメールでした。「AI外観検査自動化セミナー」の案内状。そこには、田中社長の悩みに真正面から応えるような言葉が並んでいました。
「実際に不良が検出できるのか不安がある製造業向け」
「目視検査から脱却したい製造業向け」
「過去に自動化に失敗した経験がある製造業向け」
そして、何よりも田中社長の心を捉えたのは、**「貴社のサンプルワークの持ち込み検査(会場にて開催)」**という一文でした。自社の「問題児」である部品を、その場でAIが検査してくれる?半信半疑ながらも、藁にもすがる思いで、田中社長はセミナーへの参加を決意します。
セミナー当日、会場には同じような課題を抱える多くの製造業関係者が集まっていました。そして、登壇した講師の話に、田中社長は引き込まれていきます。
講師は、AI外観検査の最新技術動向だけでなく、
熟練者のレベルをAIで再現するための具体的なポイント
AIを有効活用するための教師データの重要性や運用体制
中小企業でも導入可能なコストを抑える手法(スモールスタート、補助金活用など)
そして、実際にAI導入に成功した企業のリアルな事例(苦労と成果)
などを、分かりやすく、かつ具体的に解説しました。
「AIは魔法の杖ではない。しかし、正しく使えば強力な武器になる」
「AI導入の成否は、技術だけでなく、導入プロセスと運用にかかっている」
「過去の失敗は、未来の成功のための貴重な学びになる」
講師の言葉は、田中社長が抱いていたAIへの漠然とした不安や不信感を、具体的な知識と理解へと変えていきました。そして、セミナーのハイライトである「持ち込みサンプル検査」。田中社長が持参した、これまで検出が困難だった樹脂部品の黒点や、金属部品の微細クラックを、AI検査機が一瞬で、かつ正確に検出してみせたのです。
「信じられない…でも、これは現実だ!」
田中社長は、AIの持つ可能性を目の当たりにし、興奮を隠せませんでした。セミナー後の個別相談では、講師から自社の状況に合わせた具体的な導入ステップや、FS(実現可能性調査)の提案を受けます。
「もう迷っている時間はない。やるしかない!」
セミナーでの「賢者」との出会いは、田中社長に、AI導入への確信と、困難に立ち向かう勇気を与えました。彼は、停滞した日常から抜け出し、未知なる「冒険」への入口に立ったのです。
セミナーで得た確信と勇気を胸に、田中社長は会社に戻り、AI導入に向けた具体的な行動を開始しました。しかし、それは決して平坦な道のりではありませんでした。むしろ、ここからが本当の「試練」の始まりだったのです・・・
第三章:立ちはだかる試練と、仲間の結束
田中社長がまず着手したのは、AI導入の第一歩となるFS(実現可能性調査)プロジェクトの立ち上げでした。しかし、その決断に対して、社内からは様々な反応が返ってきます。
品質管理部長(伊藤課長): 「AI導入には莫大なコストと時間が…。現実的でしょうか?」(慎重論)
製造現場リーダー(斎藤班長): 「AIなんて信用できん!現場の勘が一番だ!」(経験からの抵抗)
経理部長(山田部長): 「会社の金がない時に、効果不明な投資はできない!」(財務的な懸念)
さらに、FSプロジェクトを進める中で、次々と技術的な壁が立ちはだかります。AIの学習に必要な「教師データ」の不足、AIモデルの精度がなかなか上がらない、実際の生産ラインでの運用への不安…。
追い打ちをかけるように、外部からの圧力も強まります。主要取引先のA社、B製作所から、相次いで、極めて厳しい品質要求(全数検査、内部欠陥保証など)と、それができなければ取引停止も辞さないという最後通牒が突きつけられたのです。
そして、最大の危機が訪れます。FSプロジェクトのリーダーとして奮闘していた伊藤課長が、「このプロジェクトは成功しないかもしれない…」と、突然の退職意向を示したのです。
内部崩壊の危機と、外部からの致命的な圧力。まさに八方塞がり。田中社長は、経営者人生で最大の窮地に立たされ、深い絶望感に襲われます。「もうダメかもしれない…」
しかし、彼は諦めなかった。
「この会社を、従業員を守る!」
その強い覚悟を、残った主要メンバー(斎藤班長、山田部長、若手の高橋君など)に伝え、協力を訴えます。
社長の本気度に触れ、当初は懐疑的だった仲間たちの心にも火が灯りました。
「社長がそこまで言うなら、ワシも腹を括る!」(斎藤班長)
「最後まで付き合います!資金面で最大限バックアップします!」(山田部長)
「僕も諦めません!この会社で挑戦したいです!」(高橋君)
絶望的な状況の中で、彼らは再び結束し、「最大の試練」に立ち向かうことを決意したのです。
「変化を恐れるな、変化できないことを恐れよ」
あのセミナーで聞いた言葉が、彼らの合言葉となりました。
彼らは、限られた時間とリソースの中で、知恵と力を結集させました。
第四章:最大の試練を乗り越えて
B製作所が要求する内部欠陥保証。これは最大の難関でした。チームは、AIとX線などのセンサー技術を組み合わせる、前例のない挑戦に挑みます。コンサルタントや外部専門家の知恵も借り、斎藤班長の現場知識、高橋君の情報収集力も活かし、昼夜を問わず試行錯誤を繰り返しました。そして、ついに、これまで不可能だった微細な内部欠陥を、AIが高精度で検出する技術的ブレイクスルーを達成したのです!
同時に、A社への回答期限も迫る中、FSプロジェクトの最終報告書作成も急ピッチで進められました。リーダー不在の穴を全員でカバーし、徹夜作業の末、AI導入の有効性を具体的なデータで示す報告書を完成させました。
不良検出率99.8%以上達成!
検査工程の人員60%削減可能!
年間数千万円の人件費削減効果!
投資回収期間は3年以内!
これらの成果を携え、田中社長は顧客との最終交渉に臨みます。単に要求に応えるだけでなく、AIを活用した独自の品質保証体制という「付加価値」を提案。その本気度と具体的な計画が評価され、A社、B製作所共に、取引継続、関係改善へと繋がったのです!
会社に戻り、交渉成功を報告すると、従業員たちから歓声と拍手が沸き起こりました。倒産の危機を回避し、未来への道を切り拓いた瞬間。苦労を共にした仲間たちと、涙ながらに喜びを分かち合いました。
これは、単なる問題解決ではありませんでした。絶望的な状況から這い上がり、未来を自らの手で掴み取った「勝利」だったのです。
「どんな困難な状況でも、諦めなければ道は開ける」
彼らは、この最大の試練を乗り越えた経験を通じて、何物にも代えがたい自信と、強い絆を手に入れました。
この勝利は、田中精密工業に、想像以上の「報酬」と「副産物」をもたらしました。
第五章:成功がもたらした「報酬」と「副産物」
AI外観検査システムの本格導入は、田中精密工業を劇的に変えました。
<具体的な成果(報酬)>
品質の飛躍的向上: クレームゼロを達成。顧客からの信頼が回復・向上し、業界内での評価も高まりました(品質改善大賞受賞など)。
圧倒的なコスト削減: 年間数千万円の人件費削減に加え、不良削減によるコスト減で、利益率が大幅に改善しました。
生産性の向上: リードタイム短縮、納期遵守率100%を実現しました。
売上の回復と成長: 既存顧客との取引拡大、新規顧客(医療機器分野など)の獲得に成功し、成長軌道に復帰しました。
しかし、手に入れた「報酬」は、目に見える業績だけではありませんでした。当初は予期していなかった、数多くのポジティブな「副産物」が、会社をさらに豊かにしていったのです。
<予期せぬ「副産物」>
従業員の成長と働きがい: 単調作業から解放され、AIオペレーションやデータ分析など、新たなスキルを習得。多能工化が進み、組織全体の柔軟性が向上しました。何より、会社の変化と自身の成長を実感し、仕事への意欲が高まりました。
組織文化の変革: 部署間の壁がなくなり、全体最適で考える文化、失敗を恐れず挑戦する文化、データに基づいて改善を進める文化が根付きました。従業員からの改善提案も活発になりました。
人材の好循環: 会社の評判向上により、優秀な若手人材(Uターン・Iターン含む)の採用が容易になり、離職率も大幅に低下(10%超→3%以下)。従業員が定着し、成長できる環境が生まれました。
地域との良好な関係: 地域での評価が高まり、自治体や他企業との連携も生まれました。地域貢献活動を通じて、従業員の誇りも高まりました。
経営者自身の成長: 田中社長も、この経験を通じて、自信を取り戻し、従業員の声に耳を傾ける柔軟なリーダーへと成長しました。
苦労した経験そのものが、組織を、そして人を強く、豊かにする。田中精密工業は、AI導入という挑戦を通じて、単に危機を乗り越えただけでなく、持続的な成長を可能にする、強固な基盤を手に入れたのです。
第六章:終わりなき挑戦へ
AI導入の成功に、田中精密工業は安住しませんでした。田中社長は、この成功を冷静に分析し、次なる課題を発見し、新たな挑戦を開始しています。
AI技術の他工程への応用、スマートファクトリー化、医療・航空宇宙といった新市場への本格参入、そして、自社のノウハウを活かした他社支援事業…。さらに、従業員一人ひとりが輝き、挑戦し続けられる組織作り、地域社会への貢献…。
田中社長は、経営とは、一つの山を越えても、また次の山を目指し続ける「終わりなき旅」であると悟りました。しかし、その表情に悲壮感はありません。むしろ、未来への希望と、挑戦への意欲に満ち溢れています。なぜなら、彼には、苦難を乗り越えた自信と、共に歩む信頼できる仲間がいるからです。
この田中精密工業の物語は、私たちに多くのことを教えてくれます。
どんな困難な状況でも、諦めなければ道は開けること。
変化を恐れず、一歩を踏み出す勇気が未来を変えること。
正しい知識と、信頼できる仲間(パートナー)の存在が不可欠であること。
AIは、正しく使えば、中小企業にとっても強力な武器となり得ること。
今、外観検査の課題に悩み、会社の未来に不安を感じているあなたへ。
田中精密工業の物語は、決して他人事ではありません。あなたの会社にも、必ず変われる可能性があります。
まずは、情報収集から始めてみませんか?
現状を変えるための「最初の一歩」を踏み出してみませんか?
私たちが開催する**【AI外観検査自動化セミナー】**は、まさにそのための最適な機会です。
最新の技術動向、成功と失敗の実例、そして何より、貴社のサンプルをその場でAIが評価するという、他にはない体験をご提供します。
あなたの会社の「冒険」を、ここから始めてみませんか?
▼セミナー詳細・お申し込みはこちら
<開催概要>
日時:
東京会場:2025年 5月15日(木) 10:00~12:30
大阪会場:2025年 5月27日(火) 10:00~12:30
会場:
東京会場:船井総研グループ 東京本社
大阪会場:株式会社船井総合研究所 大阪本社
受講料: 11,000円(税込)/ 一名様 ※会員価格あり
※お席には限りがございます。ご興味のある方はお早めにお申し込みください。
※持ち込みサンプル検査をご希望の場合は、事前にお問い合わせください。
会場でお会いできることを楽しみにしています。
※田中精密工業(仮名)のストーリーはフィクションです
※文中の削減効果などはイメージです
© 株式会社船井総合研究所 All rights reserved.
その場で判明!サンプル持ち込みでわかる外観検査体験!
https://www.funaisoken.co.jp/seminar/12711P5