記事公開日:2025.05.26
最終更新日:2025.05.26
AI外観検査導入を成功に導く!基礎から学ぶ実践ポイントと最新事例
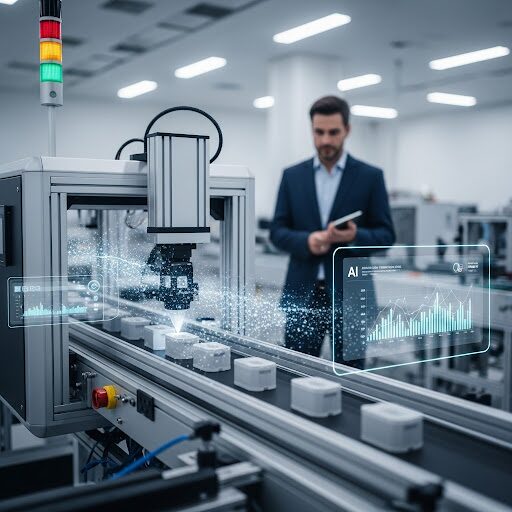
製造業の未来を拓く一手!AI外観検査で品質向上と省人化を実現。専門コンサルタントが導入成功の秘訣を徹底解説します。
このコラムをお勧めしたい方のイメージ
- AI技術を活用して製造プロセスの革新を目指している
- 検査工程の自動化による品質向上とコスト削減に関心がある
- 人手不足や検査員の負担軽減といった課題解決を模索している
- AI外観検査の導入事例や具体的な進め方について情報収集をしたい
- 投資対効果の高いDX戦略を検討している
このコラムの内容
本コラムでは、AI(人工知能)技術、特にディープラーニングを活用した外観検査の導入を検討されている製造業の経営者様やご担当者様に向けて、その基礎知識から具体的な導入フロー、成功事例までを網羅的に解説します。AI外観検査とは何か、従来の画像検査との違い、導入に必要な学習データ作成のポイント、そして実際の導入プロセスにおける要件定義、画像評価、PoC(概念実証)、機器構成、Sler選定といった各ステップで押さえるべき重要な点について、株式会社船井総合研究所のコンサルタントが専門的な知見を基に分かりやすく説明します。さらに、透明樹脂成型品、金属加工品、コネクタ、ワッシャ、冷却ジェルシートといった多様な製品におけるAI外観検査の導入事例を紹介し、具体的な費用対効果や投資回収期間についても触れることで、読者の皆様が自社への導入イメージを具体的に描けるよう支援します。
このコラムを読むメリット
このコラムをお読みいただくことで、AI外観検査導入に関する漠然とした不安や疑問を解消し、具体的な導入計画を立てる上での実践的な知識を得ることができます。AI外観検査の基本的な仕組みから、導入を成功させるためのステップごとの詳細なポイント、さらには実際の企業がどのようにAIを活用して課題を解決し、省人化や品質向上といった成果を上げているのかを多数の事例を通じて学ぶことができます。特に、学習データの準備方法や、AI画像処理ソフトの選定基準、そして最も重要な投資対効果の試算に至るまで、専門コンサルタントの視点から具体的なノウハウを提供します。これにより、自社におけるAI外観検査導入の可能性、期待される効果、そして導入までの道筋を明確に理解し、DX推進に向けた次の一歩を踏み出すための確かな指針を得ることが可能となります。
目次
1. AI外観検査とは?~基礎知識と従来技術との違い~
AI外観検査の定義と進化
AI外観検査とは、AI(人工知能)技術、特にディープラーニング(深層学習)を活用して、画像データから製品の欠陥、異物、寸法の異常などを自動で検出・判定する技術のことです。 近年、製造業における品質管理の高度化や人手不足といった課題を背景に、その重要性が急速に高まっています。
従来のルールベースの画像検査では、あらかじめ設定された明確な基準(例:傷の長さ、色の閾値など)に基づいて良否判定を行っていましたが、曖昧な欠陥や複雑なパターンの認識、あるいは個体差の大きい製品の検査には限界がありました。これに対し、AI外観検査は、大量の画像データ(学習データ)をAIに学習させることで、人間が経験や勘で行っていたような高度な判断を自動化できる可能性があります。特にディープラーニングの登場は、AI自身が画像の中から特徴量を自動的に抽出し、学習することを可能にしたため、これまで自動化が困難とされてきた複雑な外観検査への応用が飛躍的に進みました。
AI技術は、機械学習の中にニューラルネットワークがあり、その一部としてディープラーニングが存在します。 2006年頃にはニューラルネットワークによる数字認識といった技術も研究されており、これが現在のAI画像検査技術の萌芽と言えるでしょう。
AI画像検査装置の構成要素
一般的なAI画像検査装置は、検査対象物を撮影するための「FAカメラ&レンズ」 、対象物を適切に照らし出す「LED照明」 、撮影タイミングを指示する「トリガセンサー」 、撮影された画像を処理しAIが良否判定を行う「AI画像処理用PC」 または画像処理コントローラ、そして検査対象物を搬送し、時には不良品を排出する「搬送装置」 などから構成されます。これらの機器が連携し、検査対象物の搬送、トリガセンサーによる検知、撮影、AIによる画像処理と良否判定、そして判定結果に基づく良品と不良品の仕分けといった一連のフローを自動的に実行します。 このように、AI画像検査装置は単にAIソフトウェアだけでなく、撮像系、搬送系を含むシステム全体として捉えることが重要です。
AIの進化は目覚ましく、より少ないデータで高精度な学習が可能になる技術や、未知の不良品を検知する技術なども開発が進んでいます。これにより、導入のハードルが下がり、より多くの製造現場でAI外観検査の恩恵を受けられる時代が到来しつつあります。株式会社船井総合研究所では、最新のAI技術動向を踏まえ、お客様に最適なAI外観検査ソリューションの導入をご支援いたします。
2. AI外観検査導入の鍵を握る「学習データ」とは?
学習データの重要性
AI外観検査の性能を左右する最も重要な要素の一つが「学習データ」です。 AIモデル、特にディープラーニングを用いたモデルは、この学習データを通じて何を「正常」とし、何を「異常」や「特定の対象」として認識すべきかを学びます。 「Garbage in, garbage out(ゴミを入れればゴミしか出てこない)」という言葉があるように、学習データの質と量がAIの認識精度や信頼性に直接影響するため、不適切なデータで学習させると、AIは期待通りに機能しません。
学習データの内容
具体的に学習データには以下のようなものが含まれます。
- 画像そのもの:
○ 良品(正常)画像: 欠陥や異常がない状態の製品や部品の画像。AIはこれらの画像から「正常なパターン」を学習します。
○ 不良品(異常)画像: 検出したい欠陥(傷、汚れ、異物混入、欠け、変形など)や異常箇所を含む画像。AIはこれらの画像から「異常なパターン」を学習します。
○ 分類対象の画像: 特定の種類やカテゴリに分類したい場合(例:製品A、製品Bなど)は、それぞれのカテゴリに対応する画像。 - 教師ラベル(アノテーション): 各画像に対して付与される「正解」情報です。 これがなければ、AIは何を学習すれば良いかわかりません。このような学習方法を「教師あり学習」と呼びます。 具体的なアノテーション作業としては、以下のようなタスクがあります。
○ 分類タスク: 画像全体に対して「良品」「不良品(傷)」「不良品(汚れ)」といったラベルを付けます。
○ 物体検出タスク: 画像内の欠陥箇所や特定の対象物を四角い枠(バウンディングボックス)で囲み、その枠に「傷」「異物」などのラベルを付けます。
○ セグメンテーションタスク: 画像内の欠陥領域や対象物の輪郭をピクセル単位で正確に塗りつぶし(マスク作成)、「傷領域」「部品領域」といったラベルを付けます。
学習データ作成のポイント
AI外観検査の導入を成功させるためには、質の高い学習データを効率的に準備することが不可欠です。学習データ作成用の良品画像、不良品画像を集め、それらに適切なアノテーションを施す必要があります。 また、AIが様々な状況に対応できるよう、想定される照明の変化、製品の個体差、欠陥の種類の多様性などをカバーする多様な学習データを用意することが、実際の現場で安定した性能を発揮させるために重要となります。 特にディープラーニングを用いる場合、AIが複雑な特徴を捉えるためには、一般的に大量の学習データが必要となります。
学習データの準備は、時間とコストがかかる作業ですが、ここでの努力が後の検査精度に大きく影響します。株式会社船井総合研究所では、効率的な学習データ収集・作成方法から、アノテーション作業の代行、さらには学習済みモデルの提供まで、お客様の状況に合わせたサポートを提供しています。
3. 失敗しないためのAI外観検査導入フロー徹底解説
AI外観検査の導入は、単にAIソフトウェアを導入すれば完了というものではなく、計画的なステップを踏むことが成功の鍵となります。 株式会社船井総合研究所では、お客様の状況に合わせたきめ細やかな導入支援を行っており、一般的に以下のようなフローで進めていきます。
Step1:調査分析からSier選定まで
- 調査分析・要件定義: まず、お客様の現状の検査方法、課題、そしてAI外観検査導入によって達成したい目標(省人化、品質向上など)を詳細にヒアリングします。検査対象製品の種類、検査項目、検査基準、処理能力(タクトタイム)、予算などを明確にし、具体的な要件を定義します。例えば、ある金属加工品の事例では、検査要員8名を派遣技術者4~5名に省人化し、年間1200万円の費用対効果を目指すという具体的な目標を設定しました。 この段階で、実際に現場を訪問し、調査分析を行うことも重要です。
- 画像評価: 次に、実際の検査対象物を用いて撮像テストを行い、最適なカメラ、レンズ、照明の選定や、それらの配置(カメラレイアウト)を検討します。 異なる照明条件や角度で撮影し、欠陥が最も鮮明に撮像できる条件を見つけ出すことが重要です。例えば、ある事例では、2種類の撮影方法を用いることで、全ての欠陥検出が可能であることを確認しました。 この段階で、多品種に対応する必要がある場合は、品種ごとに専用の撮像治具が必要になるかなども検討します。
- PoC(Proof of Concept:概念実証): 画像評価で得られた良好な画像を基に、複数のAI画像処理ソフトウェアを選定し、実際に学習と推論を行い、検出精度や処理速度を比較検証します。 様々なメーカーのAIソフトウェアがあり、価格体系(買い切り型、サブスクリプション型、ライセンス料、保守契約料など)や実績も異なります。 例えば、ある事例では12社のAI画像処理ソフトメーカーから3社に絞り込み、最終的に価格、運用コスト、検査検出精度、使い勝手、過去の導入実績などを総合的に評価して1社を決定しました。 このPoCを通じて、導入の実現可能性と期待効果を具体的に検証します。
- 機器構成・Sier(システムインテグレータ)選定: PoCの結果を踏まえ、AIソフトウェアだけでなく、カメラ、レンズ、照明、PC、搬送装置など、システム全体に必要な機器構成を決定します。 そして、これらの機器を組み合わせて自動検査装置を構築・導入できるSierを選定します。Sierの技術力や実績、サポート体制などを考慮し、最適なパートナーを選ぶことが重要です。
Step2:発注から納品まで
- 発注・開発: 選定したSierに自動検査装置の開発を発注します。この段階で、装置の仕様や納期、費用などを最終確認します。開発期間中は、定期的な進捗確認や仕様のすり合わせを行います。
- 検収・納品: 完成した装置が、事前に取り決めた仕様や性能を満たしているかを確認する検収作業を行います。問題がなければ装置が納品され、設置作業が行われます。
Step3:運用と保守
- 仮運用・本運用: 納品された装置を実際の生産ラインに組み込み、まずは仮運用を開始します。この期間に、実際の運用状況下での課題や改善点を見つけ出し、調整を行います。問題が解消されれば、本格的な運用へと移行します。
- 保守サポート: 導入後も、安定した稼働を維持するためには定期的なメンテナンスや、万が一のトラブル発生時の迅速な対応が不可欠です。SierやAIソフトウェアメーカーとの保守契約を結び、継続的なサポート体制を確保することが重要です。
株式会社船井総合研究所は、これら全てのステップにおいて、お客様の立場に立ち、専門的な知見と豊富な経験に基づいたコンサルティングを提供し、AI外観検査導入の成功を力強くサポートいたします。
4. 【導入事例集】AI外観検査はここまでできる!5つの成功例
AI外観検査は、様々な業種や製品で導入が進み、省人化、品質向上、コスト削減といった具体的な成果を生み出しています。ここでは、株式会社船井総合研究所が支援した事例を含め、多様なケーススタディをご紹介します。
1.事例①:透明・乳白色の樹脂成型品の外観検査
- 導入前: 成型機から搬出された製品を目視検査員が検査し、その後梱包作業を行っていました。
- 課題: 目視検査員の確保と負担、検査精度のばらつき。
- 導入後: AI画像検査システムを導入し、自動検査と自動梱包を実現しました。
- 効果: 検査員2名(交代制)の省人化に成功。年間約1,400万円の費用対効果を見込み、投資回収期間は約1.7年と試算されました。
2.事例②:既存画像検査機との連携による高精度良否判定
- 導入前: 既存のK社製画像検査機でNGと判定された製品の中に、実際にはOK品が含まれており、これを目視で再検査していました。
- 課題: 既存検査機の過検出による再検査の手間とコスト。
- 導入後: K社画像検査機でNGと判定された画像に対し、AIで再検査を行うシステムを構築。
- 効果: 目視再検査員3名(交代制)の省人化を実現。年間約624万円の費用対効果、投資回収期間約1.6年を見込んでいます。
3.事例③:多品種・多項目検査が求められるコネクタの外観検査
- 導入前: 寸法計測6ヶ所、表裏左右前後からの傷・打痕・汚れ、印字検査など、多岐にわたる項目を目視検査員3名で行っていました。
- 課題: 検査項目が多く自動化が困難、局面部分の欠陥検出の難しさ、不良品流出のリスク。
- 導入後: ロボットアーム、複数のカメラ&照明、AI画像処理PC、タッチパネルなどを組み合わせたAI外観検査システムを構築。 ワークの吸着・搬送・反転も自動化し、約7~8秒/個のタクトタイムを実現。
- 効果: 検査員2名の省人化に成功。年間約416万円の費用対効果。装置費用は約4,000万円で、補助金を活用し、投資回収は約4.8年を計画。
4.事例④:検査数量が多く、基準も曖昧だったワッシャの外観検査
- 導入前: 大量のワッシャを目視検査員2名で検査。検査員ごとの判定基準のばらつきや、検査員確保の難しさ、不良品流出が課題でした。
- 課題: 膨大な検査数量、全数検査の困難さ、判定基準の曖昧さ、検査員の定着率の低さ。
- 導入後: パーツフィーダー、振動フィーダーで製品を供給し、表面・裏面をそれぞれカメラで撮影、AIで傷・打痕・汚れを検査し、ルールベースで寸法計測も行うシステムを導入。品種ごとに照明条件も自動変更します。 タクトタイムは約3秒/個。
- 効果: 検査員2名の省人化に成功し、他の加工作業へ配置転換。年間約416万円の費用対効果。装置費用約2,500万円で、補助金を活用し、投資回収約3.6年を目指します。
5.事例⑤:高速ラインで流れる冷却ジェルシートの検査
- 導入前: 高速でベルトコンベアを流れる製品(表面にフィルム、不織布に柄あり)の異物、気泡、髪の毛、冷却材範囲などを目視検査員3名で検査。
- 課題: 高速移動する製品の目視検査の困難さ、フィルムや柄による検査の難しさ、検査員ごとの判定基準のばらつき、不良品流出。
- 導入後: 画像検査装置を導入し、自動検査、自動梱包、自動箱詰めまでを実現。
- 効果: 検査員4名の省人化に成功し、他の加工作業へ配置転換。年間約1,200万円の費用対効果。装置費用約4,000万円で、投資回収約3.3年を計画。
これらの事例は、AI外観検査が多様な課題解決に貢献できることを示しています。貴社の課題解決にも、AI外観検査が有効な手段となるかもしれません。
5. まとめ:AI外観検査導入成功へのネクストステップ
本コラムでは、AI外観検査の基礎知識から、導入の鍵となる学習データの重要性、具体的な導入フロー、そして多様な成功事例に至るまで、網羅的に解説してまいりました。
AI外観検査は、AI技術、特にディープラーニングを活用し、画像データから製品の欠陥や異常を自動で検出・判定する技術です。 その導入には、カメラ、照明、AIソフトウェア、PC、搬送装置などを含むシステム全体の検討が必要です。 AIの性能を最大限に引き出すためには、質の高い「学習データ」(良品画像、不良品画像、そしてそれらに対する教師ラベル)の準備が不可欠であり、これがAIの認識精度を大きく左右します。
AI外観検査の導入フローは、一般的に「調査分析・要件定義、画像評価、PoC、機器構成・Sier選定」といった準備段階(Step1)、その後の「発注、開発、検収、納品」(Step2)、そして「仮運用、本運用、保守サポート」(Step3)というステップで進められます。 各ステップで適切な判断と対応を行うことが、導入成功の鍵となります。
ご紹介した導入事例からも明らかなように、AI外観検査は既に多くの製造現場で活用され、省人化、品質向上、コスト削減といった具体的な成果を上げています。 透明樹脂製品から金属加工品、電子部品、日用品に至るまで、その適用範囲は広く、貴社の抱える課題解決にも貢献できる可能性を秘めています。
このコラムを読んだ後に取るべき行動
AI外観検査の導入は、製造業におけるDX推進の重要な一手となり得ます。本コラムを通じて、AI外観検査の可能性を感じていただけたのであれば、次の一歩として、まずは専門家にご相談いただくことをお勧めいたします。
株式会社船井総合研究所では、AI外観検査導入に関する豊富な知見と実績を持つコンサルタントが、お客様の状況を丁寧にヒアリングし、最適な導入プランをご提案させていただきます。
- 自社のどの工程にAI外観検査を適用できるか知りたい
- 具体的な費用対効果や投資回収期間について試算してほしい
- 学習データの準備やAIモデルの選定についてアドバイスがほしい
- PoC(概念実証)を実施してみたい
このようなご要望がございましたら、ぜひお気軽にお問い合わせください。貴社の製造現場における課題解決と競争力強化に向けて、全力でサポートさせていただきます。
お問い合わせはこちら
https://www.funaisoken.co.jp/solution/maker_smartfactory_703_S045