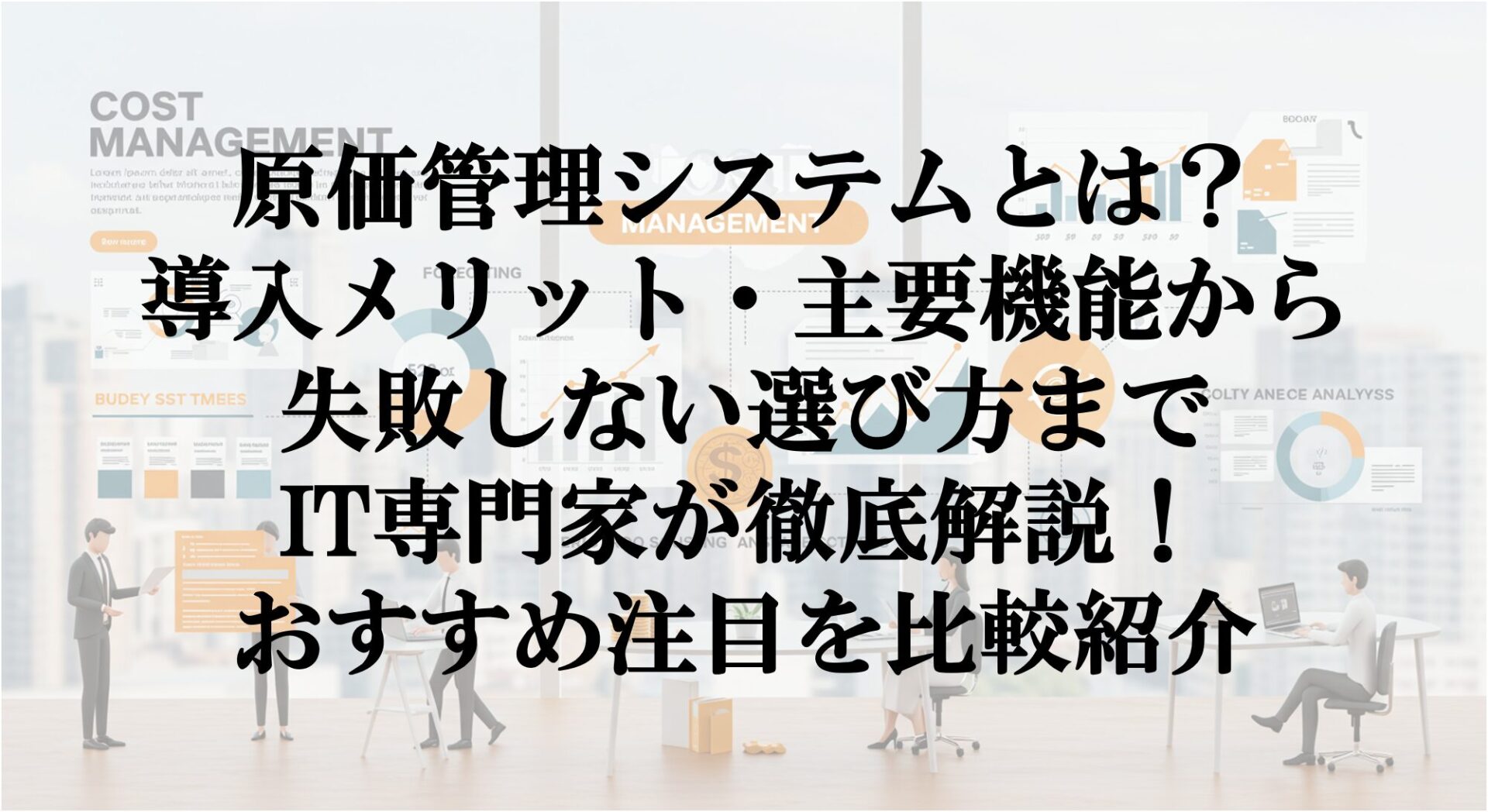
原価管理システムとは?導入メリット・主要機能から失敗しない選び方までIT専門家が徹底解説!おすすめ注目を比較紹介
2025.06.03
「製品ごとの正確なコストが分からない」
「Excelでの原価計算に限界を感じる」
「もっと戦略的な価格設定をしたい」…
多品種少量生産を行う中小製造業の皆様から、このような切実なお悩みを日々お伺いします。
原材料費の変動や競争激化が進む現代において、的確な原価管理は企業の生命線です。
しかし、従来の煩雑な手作業やExcelによる管理では、迅速かつ正確な原価把握が難しく、経営判断の遅れや利益機会の損失につながりかねません。
このような課題を解決し、競争力を高める強力なツールが「原価管理システム」です。原価管理システムの導入は、単に原価計算を効率化するだけでなく、企業の利益構造を見える化し、戦略的な経営判断を支援します。
この記事では、多品種少量生産に特化したコンサルティングで培った知見をもとに、「原価管理システム」の基礎知識から、導入のメリット・デメリット、主要機能、そして最も重要な「失敗しない選び方のポイント」まで、IT専門家の視点で徹底的に解説します。さらに、2025年現在の最新情報を踏まえ、おすすめの原価管理システムを比較紹介し、貴社に最適な一選びをサポートします。
この記事を読むことで、次のことが明確になります。
原価管理システムの基本的な仕組みと導入の必要性
Excel管理との違い、システム化による具体的なメリット
自社の課題や業種(特に製造業)に合った原価管理システムの選び方
主要な機能、タイプ別(クラウド、オンプレミス等)の特徴と比較ポイント
おすすめ原価管理システムの具体的な製品情報と導入事例
導入プロセスと成功のための注意点
原価管理に課題を感じ、業務改善や利益向上を目指すすべての中小製造業の経営者様、ご担当者様に、必ずお役立ちいただける情報をお届けします。早速、原価管理システムを詳しく見ていきましょう。
https://www.funaisoken.co.jp/dl-contents/smart-factory_smart-factory_00000153_S045?media=smart-factory_S045#_ga=2.136806070.705892685.1748526912-311123692.1748526911
1. はじめに:なぜ今、原価管理とシステム導入が重要なのか?
「この製品、本当に儲かっているのだろうか?」
「どうすればコストを抑え、もっと利益を出せるのか?」
こうした疑問は、特に私たちのお客様である多品種少量生産を営む中小製造業の経営者様にとって、常に頭を悩ませる課題ではないでしょうか。
2025年現在、原材料価格の不安定化、グローバルな競争の激化、そして深刻化する人手不足といった外部環境の変化は、企業経営における原価管理の重要性をかつてないほど高めています。
どんぶり勘定や従来のExcel頼りの管理方法では、複雑化するコスト構造を正確に把握し、迅速な経営判断を行うことがますます難しくなっています。
正確な原価情報なしには、適切な価格設定も、効果的なコスト削減策の実施も、そして持続的な利益の確保も望めません。
このような厳しい時代を勝ち抜くために、今こそ「原価管理システム」の導入が、中小製造業の皆様にとって喫緊の経営課題を解決する鍵となります。
原価管理システムは、単に原価計算を効率化するだけのツールではありません。
企業活動で発生するあらゆるコストを見える化し、分析することで、無駄の発見、業務プロセスの改善、そしてデータに基づいた戦略的な意思決定を強力に支援します。
これにより、業務効率化はもちろんのこと、製品ごとの採算性を的確に把握し、企業全体の収益力向上を実現することが可能になるのです。
いわば、原価管理システムは、デジタル変革(DX)を推進し、攻めの経営へと転じるための羅針盤と言えるでしょう。
この記事では、まさにその原価管理システムについて、基礎知識から機能、導入メリット、そして自社に最適なシステムを選ぶための具体的なポイントやおすすめ製品の比較紹介まで、あらゆる角度から徹底的に解説していきます。
この記事を読み終える頃には、なぜ今、原価管理とシステム導入がこれほどまでに重要なのか、そして貴社がどのような一歩を踏み出すべきか、その明確な答えが見つかるはずです。
原価管理の課題を解決し、企業の未来を明るく照らすシステムの世界へ一緒に進んでいきましょう。
2. 原価管理システムとは?基本を徹底解説
原価管理システムという言葉を耳にする機会が増えてきたものの、
「具体的にどのようなシステムなのか?」
「原価計算とは何が違うのか?」
といった疑問をお持ちの方も多いのではないでしょうか。
この章では、原価管理システムの最も基本的な概念、その目的、そして企業経営における重要性について、専門用語を避けながら、わかりやすく解説していきます。
原価管理システムを正しく理解することは、自社の課題解決に最適なツールを選ぶための第一歩です。
特に中小製造業の皆様にとっては、このシステムがいかにして利益創出に貢献するのか、その核心に触れる内容となります。
2.1.原価管理システムの定義と目的 - 「見える化」で経営判断を支援
原価管理システムとは、一言で表現するならば「企業が製品やサービスを提供する上で発生する様々なコスト(=原価)を、正確に収集・計算・分析し、その結果をもとにコストの最適化や利益の最大化を目指すための情報システム」のことです。
単に原価を計算するだけでなく、その原価情報を活用して経営の意思決定を支援することに主眼が置かれています。
つまり、原価管理システムは、原価の「見える化」を実現し、経営者がデータに基づいた的確な判断を行うための羅針盤のような役割を担います。
原価管理システムの主な目的は、以下の3つに集約されます。
正確な原価把握
製品ごと、プロジェクトごと、あるいは部門ごとといった様々な切り口で、実際にどれだけのコストがかかっているのかを正確に把握することが、原価管理の出発点です。
材料費、労務費、経費といった直接費はもちろんのこと、複数の製品や部門にまたがって発生する間接費を、適切な基準に基づいて配賦計算することも原価管理システムの重要な機能です。
私が以前支援したある金属加工メーカーでは、原価管理システム導入前はどんぶり勘定に近く、どの製品が本当に儲かっているのか不明瞭でした。
システム導入後、初めて製品ごとの正確な原価が明らかになり、実は主力と信じていた製品の一部が赤字であったことが判明し、大きな衝撃を受けたという経験があります。
この「正確な原価把握」こそが、全ての改善活動の基礎となります。
コストの最適化と削減
正確な原価情報が明らかになれば、次に目指すのはコストの最適化と削減です。
原価管理システムは、予算と実績の差異分析機能を備えており、どこに無駄なコストが潜んでいるのか、どの工程で効率が悪いのかを特定するのに役立ちます。
例えば、標準原価と実際原価を比較することで、材料の歩留まりが悪化している、特定の作業時間が想定以上にかかっているといった問題点を見える化できます。
これにより、具体的な改善策を立案し、実行することが可能になります。
原価管理システムは、単に問題を指摘するだけでなく、その原因究明と対策立案を支援するツールなのです。
利益最大化と経営判断の支援
最終的な目的は、企業の利益を最大化することです。
原価管理システムから得られる詳細な原価情報や採算分析の結果は、製品の価格設定、新製品開発の可否判断、不採算製品からの撤退判断、設備投資の意思決定など、企業経営における様々な重要な判断の拠り所となります。
例えば、ある製品の原価が競合他社よりも高いことが判明した場合、その原因を追求し、コスト削減努力を重ねるか、あるいは付加価値を高めて価格に転嫁するか、といった戦略的な判断が必要になります。
原価管理システムは、このような経営判断に必要な客観的なデータを提供し、経営者を力強くサポートします。
これらの目的を達成するために、原価管理システムはデータの収集から計算、分析、レポーティングまでの一連のプロセスを効率的に行う機能を備えています。特に、複雑な製品構成や製造工程を持つ多品種少量生産の製造業においては、原価管理システムなしにこれらの目的を達成することは極めて難しいと言えるでしょう。
2.2.原価管理システムの基本的な仕組みと構成要素
原価管理システムがどのようにして原価を計算し、管理しているのか、その基本的な仕組みと主要な構成要素について見ていきましょう。原価管理システムは、様々な情報源からデータを収集し、それらを基に各種計算を行い、最終的に経営判断に役立つ情報をアウトプットするという一連の流れを持っています。
この仕組みを理解することで、原価管理システムが自社のどのような業務と関連し、どのような効果をもたらすのかがより明確になります。
原価管理システムの基本的な仕組みは、大きく以下の3つのステップで構成されます。
1. データ収集・入力
原価計算に必要な元データを収集・入力する最初のステップです。このデータの精度が、最終的な原価情報の信頼性を大きく左右します。主なデータとしては、以下のようなものが挙げられます。
材料費データ
製品の製造に使用された原材料や部品の品目、数量、単価など。購買管理 システムや在庫管理 システムから連携されることが多いです。
労務費データ
製品の製造に直接関わった作業員の作業時間や賃率、あるいは間接部門の人件費など。勤怠管理 システムや人事給与システムから情報を取得します。
経費データ
外注加工費、機械の減価償却費、水道光熱費、消耗品費など、上記以外の諸経費。会計システムや経費精算システムからデータを収集します。
生産実績データ
どの製品をどれだけ生産したか、どの工程でどれだけの作業が行われたかといった実績データ。生産管理 システムやMES(製造実行システム)と連携することが一般的です。
原価管理システムの多くは、これらの関連システムとAPI連携やファイル連携を行う機能を備えており、手入力の手間を軽減し、データの正確性を向上させます。
2. 原価計算・配賦処理
収集されたデータをもとに、原価計算を実行するコアとなるステップです。
原価管理システムでは、以下のような様々な原価計算方法に対応しています。
実際原価計算
実際に発生したコストを積み上げて原価を算出する方法です。
標準原価計算
あらかじめ科学的な方法で目標となる標準原価を設定し、実際原価との差異を分析することでコスト管理を行う方法です。
直接原価計算
原価を変動費と固定費に分類し、限界利益を重視する管理会計手法です。
また、複数の製品や部門に共通して発生する間接費(工場全体の減価償却費や間接部門の人件費など)を、一定の基準(作業時間、機械稼働時間、材料使用量など)に基づいて各製品や部門に割り振る「配賦処理」もこの段階で行われます。
この配賦基準の設定が、原価の正確性に大きな影響を与えるため、原価管理システムでは柔軟な配賦基準の設定機能が重要となります。
3. 原価分析・レポーティング
計算された原価情報を分析し、経営判断に役立つレポートとして出力する最終ステップです。
原価管理システムは、以下のような多様な分析機能やレポーティング機能を提供します。
製品別原価一覧表
各製品の原価構成(材料費、労務費、経費の内訳)や利益率などを一覧で表示します。
差異分析レポート
標準原価と実際原価の差異や、予算と実績の差異を項目別に表示し、その原因究明を支援します。差異の要因を深掘りするためのドリルダウン機能を備えたシステムも多いです。
損益分岐点分析
売上高と費用の関係から、利益がゼロになる売上高(損益分岐点)を算出し、利益計画の立案に活用します。
シミュレーション機能
材料単価の変動や生産量の変更などが原価や利益にどのような影響を与えるかを事前に試算する機能です。
これらのレポートは、グラフや表を活用して視覚的にわかりやすく表示され、経営層や各部門の管理者が迅速に状況を把握し、次のアクションを検討するのに役立ちます。
これらの構成要素が有機的に連携することで、原価管理システムは複雑な原価管理業務を効率的かつ正確に遂行することを可能にしています。特に、基幹システム(ERP)の一部として原価管理機能を提供するシステムや、他のシステムとの連携を重視した製品が増えています。
2.3.原価計算との違いとは?関連性とそれぞれの役割について解説
「原価管理」と「原価計算」は、しばしば混同されたり、同じ意味で使われたりすることがありますが、厳密には異なる概念です。
この二つの違いと関連性を正しく理解することは、原価管理システムの役割をより深く把握する上で非常に重要です。
それぞれの言葉が指す意味と、企業活動における位置づけについて解説します。
まず、「原価計算」についてです。原価計算とは、「製品やサービスを生産・提供するために消費された経済価値(つまりコスト)を、一定のルールに基づいて測定し、計算する手続き」そのものを指します。具体的には、製品1単位あたりにどれだけの材料費、労務費、経費がかかったのかを算出する作業です。原価計算の主な目的は、財務諸表(特に損益計算書における売上原価や棚卸資産の評価額)を作成するために必要な原価情報を提供すること(財務会計目的)、そして製品の価格設定や予算編成の基礎資料とすること(管理会計目的)にあります。つまり、原価計算は「原価を算出する技術・プロセス」に焦点が当てられています。
一方、「原価管理」とは、その名の通り「原価を管理すること」を意味します。原価計算によって算出された原価情報を活用し、コストの標準を設定したり(標準原価設定)、実際に発生したコストがその標準から逸脱していないかを監視したり(差異分析)、逸脱があった場合にはその原因を追求し、コスト削減や業務改善のための具体的なアクションを計画・実行したりする一連の活動全体を指します。原価管理の目的は、単に原価を計算するだけにとどまらず、その情報を経営の意思決定に活かし、企業の収益性向上や競争力強化に貢献することにあります。つまり、原価管理は「原価情報を経営に活かすためのマネジメント活動」と言えます。
このように考えると、原価計算は原価管理を行うための重要なツールの一つ、あるいは原価管理という大きな枠組みの中の一部のプロセスであると位置づけることができます。正確な原価計算なくして効果的な原価管理はあり得ませんし、逆に、どれだけ正確に原価計算ができたとしても、その結果が経営改善に活かされなければ意味がありません。
原価管理システムは、この両方の側面をカバーするツールと言えます。システム内部では精緻な原価計算機能(実際原価計算、標準原価計算、配賦処理など)が実行されます。そして、その計算結果を基に、差異分析レポート、製品別損益一覧、シミュレーション機能などを提供することで、経営者が原価管理を効果的に行うことを支援します。例えば、ある部品の仕入れ単価が上昇した場合、原価計算機能がその影響を製品原価に反映し、原価管理機能(シミュレーションや分析レポート)が「どの製品の利益率がどれだけ悪化するか」「代替材料を採用した場合のコストはどうか」といった経営判断に必要な情報を提示する、といった具合です。
中小製造業においては、原価計算の手間に追われ、その先の原価管理まで手が回らないというケースが少なくありません。原価管理システムを導入することは、この原価計算の業務を大幅に効率化し、より戦略的な原価管理へとステップアップするための強力な後押しとなるのです。
2.4.Excelや手作業による原価管理の限界とシステム化のメリット
現在、多くの中小製造業において、表計算ソフトのExcelや手作業で原価管理を行っているケースが見受けられます。Excelは手軽に利用でき、柔軟性も高いため、一定規模までの企業や比較的シンプルな原価計算であれば有効なツールとなり得ます。
しかし、企業規模の拡大、取り扱い製品数の増加(多品種少量化)、製造工程の複雑化などに伴い、Excelや手作業による原価管理には様々な限界が見え始めます。ここでは、その具体的な限界点と、原価管理システムを導入してシステム化することによるメリットについて、私のコンサルティング経験を踏まえながら詳しく解説します。
まず、Excelや手作業による原価管理の主な限界点としては、以下のような点が挙げられます。
データの収集・入力に膨大な手間と時間がかかる
原価計算に必要な材料費、労務費、経費などのデータを各部門から集め、Excelのシートに手入力する作業は、非常に時間と手間がかかります。特に多品種少量生産の企業では、製品ごとに構成部品や作業工程が異なるため、入力するデータ量も膨大になりがちです。
私が担当したある食品メーカーでは、毎月、複数の担当者が数日間つきっきりで各工場からの生産実績や材料使用量の報告をExcelに転記していましたが、それでも入力ミスが後を絶たず、確認作業にさらに時間を要していました。このような状況では、担当者の負担が大きく、本来行うべき分析業務などに手が回りません。
計算ミスや人的エラーが発生しやすい
Excelの関数やマクロを駆使して複雑な原価計算ロジックを組むことは可能ですが、数式が長大になったり、複数のシート間でデータを参照したりする場合、計算ミスや参照エラーが発生するリスクが常に伴います。また、手入力による転記ミスや、担当者ごとの思い込みによる誤った処理など、人的エラーも避けられません。これらのエラーは、原価情報の精度を著しく低下させ、誤った経営判断を招く可能性があります。
ある電子部品メーカーでは、ExcelのVLOOKUP関数の範囲指定ミスにより、一部部品の単価が誤って計算され続け、長期間にわたり不採算製品に気づかなかったという苦い経験をお持ちでした。
リアルタイムな情報把握が難しい
Excelによる原価計算は、月次や都度バッチ的に行うことが一般的であり、リアルタイムに原価情報を把握することは困難です。市場環境の変化が激しい現代において、経営判断に必要な情報が1ヶ月遅れでしか出てこないのでは、迅速な意思決定は望めません。「今、この製品は儲かっているのか?」という問いに即座に答えられないことは、大きな機会損失につながります。
データの属人化と共有の難しさ
複雑なExcelファイルやマクロは、作成した担当者以外には理解が難しく、メンテナンスも困難になりがちです(いわゆる「Excel職人」問題)。その担当者が異動や退職した場合、原価計算業務が滞ってしまうリスクがあります。また、Excelファイルは個人PCや共有フォルダで管理されることが多く、最新版のファイルがどれか分からなくなったり、複数担当者による同時編集が難しかったりするなど、情報共有やバージョン管理の面でも課題があります。
高度な分析やシミュレーションへの対応が困難
製品別の詳細な損益分析、原価変動要因の深掘り、将来の原価シミュレーションといった高度な分析をExcelで行うには、専門的な知識と高度なスキルが要求され、限界があります。経営戦略に直結するような情報をタイムリーに引き出すことが難しいのです。
これらの限界点を克服し、より高度な原価管理を実現するために、原価管理システムの導入が有効となります。システム化による主なメリットは以下の通りです。
業務効率の大幅な向上(自動化)
原価管理システムは、販売管理 システム、生産管理
システム、会計システムなど、他の基幹システムとデータ連携することで、データ収集・入力の多くを自動化します。これにより、手作業による手間や時間が大幅に削減され、担当者はより付加価値の高い分析業務や改善活動に注力できます。
原価計算の精度向上と標準化
あらかじめ定義された計算ロジックと統一されたマスターデータに基づいてシステムが自動的に原価計算を行うため、人的エラーが介在する余地が大幅に減り、原価情報の精度と信頼性が格段に向上します。また、原価計算プロセスが標準化されるため、担当者によるバラつきもなくなります。
リアルタイムな原価把握と迅速な意思決定の実現
システム上でデータが一元管理され、必要な時に最新の原価情報を即座に参照できるようになります。これにより、経営層はタイムリーな情報に基づいた迅速な意思決定が可能となり、市場の変化にも柔軟に対応できるようになります。
データの属人化防止と情報共有の円滑化
原価管理システムでは、原価計算のロジックやデータがシステム内で一元的に管理されるため、特定の担当者に依存することなく、誰でも(権限に応じて)必要な情報にアクセスし、活用することが可能になります。情報の透明性が高まり、部門間の連携もスムーズになります。
高度な分析機能と経営判断の質の向上
原価管理システムは、製品別・顧客別・部門別など多角的な分析機能や、差異分析、損益分岐点分析、原価シミュレーションといった高度な機能を標準で備えているものが多く、経営戦略の立案や的確な意思決定を強力に支援します。これにより、データに基づいた科学的な経営が実現できます。
私がコンサルティングで原価管理を支援した多くの中小製造業では、Excel管理からの脱却により、これらのメリットを享受し、原価管理のレベルを飛躍的に向上させています。
例えば、ある機械部品メーカーでは、原価管理システム導入後、月次の原価確定までの期間が従来の約半分に短縮され、かつ、製品ごとの詳細な収益性が見える化されたことで、不採算製品の絞り込みと対策が迅速に打てるようになり、半年で全体の利益率が改善したという実績があります。
もちろん、原価管理システムの導入には初期費用や運用コスト、導入時の手間もかかりますが、長期的な視点で見れば、これらのメリットは企業の競争力強化と持続的成長に大きく貢献すると言えるでしょう。
3. 原価管理システム導入のメリット・デメリット
原価管理システムの導入は、多くの企業、特に私たちのお客様である中小製造業の皆様にとって、経営体質を強化し、競争優位性を確立するための重要な一手となり得ます。しかし、新しいシステムを導入する際には、その輝かしいメリットだけでなく、潜在的なデメリットや注意すべきポイントも十分に理解しておく必要があります。「こんなはずではなかった…」という事態を避けるためにも、ここでは原価管理システム導入によってもたらされる具体的な効果と、事前に把握しておくべき課題について、コンサルタントとしての経験を踏まえながら、詳しく解説していきます。
3.1.導入で得られる効果とは?企業にもたらす主なメリット一覧
原価管理システムを導入し、適切に活用することで、企業は多岐にわたるメリットを享受することが可能です。これらのメリットは、単に業務の効率化に留まらず、企業の収益構造の改善や意思決定の質の向上、ひいては企業文化の変革にまでつながる可能性があります。ここでは、特に重要と考えられる主なメリットを3つのポイントに絞って、具体的に見ていきましょう。
3.1.1.正確な原価把握と迅速な経営判断の実現
原価管理システム導入における最大のメリットの一つは、何と言っても「製品ごと、あるいはプロジェクトごとの正確な原価を、タイムリーに把握できるようになる」ことです。これは、特に多品種少量生産を特徴とする中小製造業にとっては、経営の根幹に関わる極めて重要な効果と言えるでしょう。
結論として、原価管理システムは、従来ブラックボックス化しがちだったコストの内訳を詳細に「見える化」し、データに基づいた迅速かつ的確な経営判断を可能にします。
例えば、私が以前コンサルティングで支援させていただいたある金属部品メーカーA社様は、長年Excelを駆使して熟練の担当者が原価計算を行っていました。しかし、取り扱い部品が数千点に及び、製造工程も複雑だったため、月次の原価が確定するまでに翌月の中旬を過ぎるのが常でした。そのため、ある製品が赤字になっていると判明しても、既に対策が後手に回り、損失が拡大してしまうケースが散見されたのです。さらに、Excelでは間接費の配賦基準が曖昧で、本当にその製品の原価が正確なのか、社内でも疑問の声が上がっていました。
そこでA社様は、思い切って原価管理システムの導入に踏み切りました。システム導入後は、生産管理 システムや購買管理
システムとデータが自動連携され、日々の生産実績や材料使用量などがリアルタイムに近い形で原価計算に反映されるようになりました。その結果、従来1ヶ月半かかっていた製品別原価の確定が、わずか数日で完了するようになり、経営陣はほぼリアルタイムで各製品の採算状況を把握できるようになったのです。正確な原価が明らかになったことで、A社様は驚くべき事実に直面しました。これまで主力と信じていた製品群の一部が、実は慢性的な赤字状態だったのです。この事実にいち早く気づけたことで、A社様は問題製品の価格改定交渉や製造プロセスの徹底的な見直しに迅速に着手し、半年後にはその赤字製品群を黒字転換させることに成功しました。これは、原価管理システムがもたらす「正確な原価把握」と「迅速な経営判断」の効果を如実に示す事例です。
原価管理システムは、材料費、労務費、経費といった直接費はもちろん、配賦が難しい間接費についても、事前に設定した合理的な基準に基づいて自動計算を行うため、原価計算の精度が飛躍的に向上します。これにより、「どの製品がいくら儲かっているのか(あるいは損しているのか)」、「コストが想定以上にかかっている工程はどこか」といった情報が明確になり、経営者は自信を持って価格戦略、製品ポートフォリオ戦略、コスト削減戦略などを立案・実行できるようになるのです。原価管理システムは、まさに勘や経験に頼った経営から、データドリブンな経営へと移行するための強力な推進力となります。
3.1.2.業務効率化とコスト削減への貢献(プロセス改善)
次に挙げる大きなメリットは、「原価管理に関わる一連の業務の大幅な効率化と、それに伴う間接的なコスト削減への貢献」です。日々のデータ入力や集計、レポート作成といった作業に多くの時間と手間を費やしている企業にとって、原価管理システムの導入は、まさに福音となる可能性があります。
結論として、原価管理システムは、手作業が多く非効率だった原価管理業務を自動化・標準化することで、担当者の作業負荷を大幅に軽減し、人件費を含む間接コストの削減、さらには業務プロセス全体の改善へとつなげます。
私がコンサルティングで関わった多くの中小製造業の現場では、原価計算の時期になると経理部門や生産管理部門の担当者が残業続きになる、という光景が珍しくありませんでした。各部門から集めた紙の伝票やExcelファイルを元に、膨大なデータを転記し、検算し、集計するという作業は、精神的にも肉体的にも大きな負担となります。ある食品加工会社B社様もその一社で、月次の原価計算には3名の担当者がほぼ1週間つきっきりで対応していましたが、それでも入力ミスや集計ミスが頻発し、その修正作業にさらに時間を奪われるという悪循環に陥っていました。
B社様が原価管理システムを導入した結果、その業務風景は一変しました。販売管理 システムから受注情報や売上情報を、生産管理 システムから生産実績や材料消費情報を、勤怠管理
システムから作業時間情報を、それぞれ原価管理システムが自動で取り込めるように連携させたのです。これにより、従来手作業で行っていたデータ収集・入力作業の約8割が自動化されました。担当者は、システムが算出した原価データの確認と分析、そして差異が生じた場合の深掘りといった、より付加価値の高い業務に集中できるようになりました。結果として、月次の原価計算に要する時間は従来の3分の1以下に短縮され、残業時間も大幅に削減。担当者のモチベーション向上にもつながったのです。これは、原価管理システムが直接的な業務効率化を達成した分かりやすい事例です。
さらに、業務効率化は間接的なコスト削減にも波及します。まず、単純作業の時間が減ることで、その分の人件費が実質的に削減されます。また、入力ミスや計算ミスが減ることで、手戻りや修正作業に伴う無駄なコストも発生しにくくなります。原価管理システムによって業務プロセスが標準化されることは、特定の担当者にしかできないといった「属人化」のリスクを低減し、担当者の急な欠勤や退職時にも業務が滞りなく継続できる体制づくりにも貢献します。これは、BCP(事業継続計画)の観点からも非常に重要なポイントです。
このように、原価管理システムは、日々の煩雑な原価管理業務から担当者を解放し、企業全体の生産性向上とコスト構造の改善に大きく寄与するのです。
3.1.3.詳細なデータ分析による採算管理の高度化
三つ目の大きなメリットとして、「原価管理システムが提供する豊富なデータと分析機能を活用することで、企業の採算管理をより高度なレベルへ引き上げることができる」点が挙げられます。単に原価を計算して終わりではなく、その情報を多角的に分析し、利益を生み出すための具体的なアクションに繋げることが、原価管理の本来の目的です。
結論として、原価管理システムは、製品別・顧客別・部門別といった様々な切り口での詳細な損益分析や、原価シミュレーションを可能にし、データに基づいた的確な採算改善策の立案と実行を支援します。
以前、私が支援したあるカスタム機械メーカーC社様は、個別の受注案件ごとに設計・製造を行うビジネスモデルのため、案件ごとの正確な採算把握が経営上の最重要課題でした。しかし、従来のExcelベースの管理では、各案件に間接費をどのように配賦するかが曖昧で、見積段階での原価予測の精度も低く、気づけば赤字案件を抱えていることもしばしばありました。特に、技術的に難易度の高い案件や短納期案件では、想定外の工数が発生しやすく、採算が悪化する傾向にありました。
C社様は、原価管理システムの中でも特にプロジェクト型の原価管理に強い製品を選定し、導入しました。新しいシステムでは、各案件に紐づく直接材料費、直接労務費(作業員がどの案件にどれだけ時間を投入したかを正確に記録)、外注費などがリアルタイムに集計されるようになりました。また、間接費についても、部門ごとの活動基準(例えば設計部門なら設計工数、製造部門なら機械稼働時間など)に基づいた多段階配賦を設定することで、より実態に近い形で各案件にコストが割り振られるようになりました。
その結果、C社様は、個々の案件の詳細な原価構成と利益率を、進行中であってもほぼリアルタイムで把握できるようになったのです。システムが提供する分析レポートを活用することで、
「どのタイプの案件が儲かりやすいのか」
「どの顧客との取引が最も収益性が高いのか」
「原価が予算を超過しやすいのはどのようなケースか」
といったことが、具体的なデータとして見える化されました。
これにより、C社様は赤字になりやすい案件の傾向を掴み、見積時の原価予測精度を大幅に向上させることができました。また、不採算案件については、その原因を深掘りし、設計変更によるコストダウンや顧客との価格交渉を有利に進めるための客観的な資料として原価データを活用できるようになりました。さらに、原価シミュレーション機能を使い、受注前の段階で、異なる材料を採用した場合や工程を一部外注した場合の原価変動を予測し、最も利益の出る方法を選択するといった、より戦略的なアプローチも可能になったのです。
このように、原価管理システムは、過去の実績データを分析するだけでなく、将来の収益性を予測し、改善するための洞察を提供します。これにより、企業は場当たり的な対応ではなく、データに裏打ちされた科学的なアプローチで採算管理を高度化し、持続的な利益成長を実現することができるのです。
3.2.導入前に知っておくべきデメリットや注意点
これまで原価管理システム導入の素晴らしいメリットについて述べてきましたが、一方で、導入を成功させるためには、事前に理解し、対策を講じておくべきデメリットや注意点も存在します。これらを軽視すると、期待した効果が得られないばかりか、導入プロジェクト自体が頓挫してしまう可能性すらあります。ここでは、原価管理システム導入に際して、特に中小製造業の皆様が直面しやすい一般的なデメリットと注意点を具体的に解説します。
結論として、原価管理システムの導入には、初期費用や運用コスト、導入にかかる時間と労力、既存業務フローの変更への対応、そしてシステム定着化への努力が必要であり、これらを事前に十分に検討し、計画的に進めることが成功の鍵となります。
導入コスト(初期費用・ランニングコスト)の発生
原価管理システムを導入するには、当然ながら費用がかかります。システムの購入費用(パッケージ型の場合)や開発費用(カスタマイズやスクラッチ開発の場合)、あるいはクラウド型システムの初期設定費用や月額(または年額)利用料が発生します。
これに加えて、導入支援コンサルティング費用、サーバーやネットワークなどのインフラ整備費用(オンプレミス型の場合)、社員向けの教育研修費用なども考慮する必要があります。
特に中小企業にとっては、これらのコストは決して小さくない投資となります。
注意点として、単に価格の安さだけでシステムを選ぶのではなく、自社の課題解決に本当に必要な機能を備えているか、将来的な拡張性はあるか、費用対効果(ROI)を長期的な視点で慎重に検討することが重要です。複数のベンダーから見積もりを取り、機能と価格のバランスを比較しましょう。
また、クラウド型システムは初期費用を抑えられる傾向にありますが、月額費用が継続的に発生するため、長期的な総コストも試算しておく必要があります。
導入にかかる時間と労力(手間)
原価管理システムの導入は、スイッチを押せばすぐに使えるというものではありません。自社の業務プロセスの分析、システム要件定義、システムの設定やカスタマイズ、データ移行、社員教育、テスト運用など、本稼働に至るまでには相応の時間と労力が必要です。
特に、既存の基幹システム(販売管理、生産管理、会計など)との連携が必要な場合は、その調整に時間を要することがあります。
注意点として、無理のない導入スケジュールを策定し、社内に専門のプロジェクトチームを組成するか、主要な担当者を明確に割り当てることが不可欠です。また、システムベンダーや導入支援コンサルタントのサポート体制も重要なポイントです。導入プロセスで発生しうる課題や遅延リスクを事前に洗い出し、対策を準備しておくことも求められます。ある企業では、現場の意見を十分に聞かずにシステム選定を進めた結果、導入段階で仕様変更が多発し、スケジュールが大幅に遅延した事例がありました。
既存業務フローの変更と社員の適応
新しい原価管理システムを導入するということは、多くの場合、従来の業務のやり方を変えることを意味します。例えば、データの入力方法やタイミング、レポートの形式、承認プロセスなどが変更される可能性があります。こうした変化に対して、社員が抵抗を感じたり、新しいシステムの操作に戸惑ったりすることは十分に考えられます。特に長年慣れ親しんだ方法を変えることへの心理的なハードルは意外と高いものです。
注意点として、なぜシステムを導入するのか、それによってどのようなメリットがあるのかを社員に丁寧に説明し、理解と協力を得ることが不可欠です。また、十分な教育研修の機会を設け、操作マニュアルを整備し、導入後も継続的なサポート体制を整えることが重要です。新しいシステムが定着するまでにはある程度の時間がかかることを覚悟し、辛抱強く取り組む姿勢が求められます。トップダウンでの強いリーダーシップと、現場の声を吸い上げるボトムアップの活動の両輪が効果的です。
システムの定着化と継続的な運用負荷
原価管理システムは、導入して終わりではありません。システムを有効に活用し続けるためには、データの鮮度と精度を維持するための継続的な運用努力が必要です。マスターデータ(品目マスター、構成表マスター、工程マスターなど)の定期的なメンテナンス、システムのバージョンアップへの対応、社員の異動や退職に伴う再教育なども考慮しなければなりません。これらを怠ると、せっかく導入したシステムが形骸化し、「使われないシステム」になってしまう恐れがあります。
注意点として、システム運用担当者を明確にし、その役割と責任を定義することが重要です。また、システムベンダーからの保守サポートの内容(問い合わせ対応、障害対応、バージョンアップ情報の提供など)を事前にしっかり確認しておきましょう。運用ルールを策定し、定期的にシステムの利用状況や効果をレビューし、改善を重ねていくプロセスを組み込むことも、システムを長く有効に使い続けるためには不可欠です。
これらのデメリットや注意点を事前にしっかりと認識し、対策を講じた上で原価管理システムの導入プロジェクトを進めることが、成功への確実な道筋となります。決して楽な道のりではありませんが、その先には企業の大きな成長が待っていると信じて、計画的に取り組むことが肝要です。
4. 原価管理システムの主要機能とは?自社に必要な機能を見極める
原価管理システムと一口に言っても、その機能は多岐にわたります。基本的な原価計算機能から、高度な分析機能、さらには他のシステムとの連携機能まで、実にさまざまです。自社の課題解決や目的達成に本当に必要な機能を見極めることは、最適な原価管理システムを選ぶ上で非常に重要なポイントとなります。「多機能であればあるほど良い」というわけではなく、自社の業務や規模、業種特性にマッチした機能を過不足なく備えているかどうかが肝心です。この章では、原価管理システムが持つ代表的な主要機能について、それぞれがどのような役割を果たし、どのような企業にとって特に有効なのかを、具体例を交えながら解説していきます。これらの情報を参考に、ぜひ貴社にとって「使える」機能は何かを検討してみてください。
4.1.標準機能一覧:実行予算、原価計算(標準・実際)、配賦処理など
まず、多くの原価管理システムに標準的に搭載されている基本的な機能群について見ていきましょう。これらの機能は、原価管理を行う上での土台となるものであり、企業の規模や業種を問わず、正確な原価把握と基本的なコスト管理を実現するために不可欠なものです。これらの標準機能をしっかりと理解し、自社の業務と照らし合わせることが、システム選定の第一歩となります。
結論として、原価管理システムの標準機能は、日々のコストデータを収集・計算し、計画との比較を通じて管理の基礎を築くための必須ツール群です。
主な標準機能としては、以下のものが挙げられます。
実行予算作成・管理機能
原価管理を効果的に行うためには、まず目標となる予算を設定することが重要です。
実行予算とは、特定のプロジェクトや製品、あるいは一定期間の活動に対して、事前に材料費、労務費、経費などのコストを見積もり、計画値として具体的に設定するものです。原価管理システムの実行予算機能は、過去の実績データやマスター情報を参考にしながら、効率的に実行予算を作成することを支援します。また、承認ワークフロー機能を備えたシステムであれば、予算作成から承認までのプロセスをシステム上で一元管理することも可能です。
例えば、ある建設業のお客様D社様は、従来Excelで各工事の実行予算を作成していましたが、過去の類似工事のデータを探し出すのに手間がかかり、見積もりの精度にもバラつきがありました。原価管理システム導入後は、過去の工事実績がシステムに蓄積され、類似案件の予算を簡単に参照・コピーして新しい実行予算を組めるようになり、予算作成時間が大幅に短縮され、精度も向上しました。
原価計算機能(実際原価計算・標準原価計算など)
これは原価管理システムの中核となる機能です。実際に発生したコストを集計して製品やプロジェクトの原価を算出する「実際原価計算」はもちろんのこと、多くのシステムでは、あらかじめ目標となる原価を設定しておく「標準原価計算」にも対応しています。標準原価計算を行うことで、実際にかかった原価との差異を分析し、コスト管理の指標とすることができます。また、製品の種類や企業の管理方針に応じて、ロット別原価計算、工程別原価計算、ジョブ別原価計算など、さまざまな計算方法をサポートしているシステムも多いです。
多品種少量生産の製造業では、製品ごとに原価を正確に捉えることが特に重要となるため、自社の生産形態に合った原価計算方法をサポートしているかどうかが選定のポイントとなります。
配賦処理機能
複数の製品や部門に共通して発生する間接費(例えば、工場全体の減価償却費、水道光熱費、間接部門の人件費など)を、一定の基準に基づいて各原価集計単位(製品、部門、プロジェクトなど)に割り振る処理を「配賦」と呼びます。この配賦基準の設定方法が、原価の正確性に大きな影響を与えます。原価管理システムでは、作業時間、機械稼働時間、材料費比率、生産数量など、さまざまな配賦基準を柔軟に設定できる機能が備わっています。また、複数の基準を組み合わせた多段階配賦や、活動基準原価計算(ABC:Activity
Based Costing)の考え方を取り入れた配賦が可能なシステムもあります。
私が支援したある家具メーカーE社様では、従来、間接費を単純に売上高比率で配賦していましたが、原価管理システム導入を機に、各製品の製造に実際にかかっている手間(作業時間や機械占有時間)を基準とした配賦に見直しました。その結果、これまで利益が出ていると思っていた手間のかかる特注品が、実は赤字に近いことが判明し、価格設定や製品戦略の見直しに繋がりました。適切な配賦処理機能は、より正確な原価把握に不可欠です。
マスタ管理機能
原価計算の精度と効率を維持するためには、品目マスター(原材料、部品、製品)、部品表(BOM:Bill Of
Materials)マスター、工程マスター、作業単価マスター、配賦基準マスターなど、さまざまなマスターデータを正確に管理する必要があります。原価管理システムは、これらのマスターデータを一元的に登録・更新・管理する機能を提供します。マスターデータが整備されていることで、データ入力の手間が省け、計算の標準化が図れます。
特に部品表(BOM)は製造業の原価計算の骨格となるため、原価管理システムがBOMの変更履歴管理や版管理に対応しているか、また、設計変更がスムーズに原価計算に反映される仕組みになっているかは重要なチェックポイントです。
これらの標準機能は、原価管理の基盤を構築する上で欠かせないものです。自社の業務フローや管理レベルを考慮し、これらの機能が過不足なく提供されているか、また、操作性や設定の柔軟性などをしっかりと確認することが、システム選定の第一歩となります。
4.2.プロジェクト別・部門別・製品別原価管理機能
多くの原価管理システムでは、基本的な原価計算機能に加えて、より詳細な管理単位で原価を把握し、分析するための機能が充実しています。特に、「プロジェクト別」「部門別」「製品別」といった切り口での原価管理機能は、企業が自社の収益構造を深く理解し、的確な経営判断を行う上で非常に有効です。これらの機能を活用することで、どこでコストが発生し、どこで利益が生まれているのかを、より具体的に「見える化」することが可能になります。
結論として、プロジェクト別・部門別・製品別原価管理機能は、企業活動の様々な側面からコストと収益性を掘り下げて分析し、より精密な経営管理を実現するための強力な武器となります。
プロジェクト別原価管理機能
建設業、ITシステム開発業、コンサルティング業、個別受注生産の製造業など、プロジェクト単位で業務が進行する業種においては、プロジェクトごとの原価と採算を正確に把握することが経営の生命線です。プロジェクト別原価管理機能は、各プロジェクトに紐づく材料費、労務費(誰がどのプロジェクトにどれだけの工数を投入したか)、外注費、その他経費などを個別に見積もり、実績を収集・集計し、予算と実績の差異をリアルタイムに管理することを可能にします。
例えば、あるソフトウェア開発会社F社様は、各開発プロジェクトの進捗や採算状況が不明瞭で、気づいた時には予算オーバーや納期遅延が発生していることが課題でした。プロジェクト原価管理機能を備えた原価管理システムを導入したことで、各プロジェクトの工数実績や外注費の発生状況が日々更新され、プロジェクトマネージャーはいつでも最新の採算状況を確認できるようになりました。これにより、予算超過の兆候を早期に察知し、対策を講じることが可能となり、プロジェクトの利益率改善に大きく貢献しました。また、完了したプロジェクトの実績データは、次の類似プロジェクトの見積もり精度向上にも役立っています。
部門別原価管理機能
企業内の各部門(製造部門、営業部門、開発部門、管理部門など)が、それぞれどれだけのコストを消費し、どれだけの貢献(利益や付加価値)を生み出しているのかを把握することは、部門ごとの業績評価やリソースの最適配分に不可欠です。部門別原価管理機能は、各部門で発生した直接費や、本社共通費などの間接費を適切な基準で各部門に配賦し、部門ごとの損益を明らかにします。
これにより、各部門長は自部門のコスト意識を高め、無駄の削減や効率化への取り組みを促進することができます。また、経営層は、どの部門が収益に貢献し、どの部門に課題があるのかを客観的なデータで評価し、経営資源の重点配分や組織再編などの意思決定に活用できます。
製品別原価管理機能
これは特に製造業にとって最も基本的な管理単位と言えるでしょう。どの製品がどれだけの原価で製造され、どれだけの利益を生んでいるのかを正確に把握することは、価格設定、製品ポートフォリオの最適化(不採算製品の見直しや新製品開発)、コスト削減努力の方向付けなど、あらゆる経営戦略の基礎となります。製品別原価管理機能は、各製品の材料費、労務費、製造経費を精緻に計算し、製品ごとの詳細な原価構成や利益率を明らかにします。
多品種少量生産の企業では、アイテム数が膨大になるため、手作業やExcelでの製品別原価管理は非常に困難ですが、原価管理システムを活用することで、この業務を大幅に効率化し、精度を向上させることが可能です。
あるアパレルメーカーG社様は、原価管理システムで製品別の正確な原価と販売実績を紐付けて分析した結果、売上は大きいものの利益率が極端に低い製品や、逆に売上は小さいものの非常に利益率の高いニッチな製品を発見できました。この分析結果をもとに、製品ラインナップの見直しや販売戦略の変更を行い、全体の収益性改善に成功しました。
これらの「○○別」原価管理機能は、企業が自社の事業活動をより解像度高く理解するための虫眼鏡のようなものです。どの切り口での管理が自社にとって最も重要かを見極め、それらの機能が充実している原価管理システムを選ぶことが、経営の「見える化」を加速させる鍵となります。
4.3.予算実績管理・差異分析機能とレポート出力
原価管理システムの価値は、単に原価を計算するだけに留まりません。計画(予算)と実績を比較し、その間に生じた「差異」を分析することで、問題点の早期発見や業務改善につなげることができてこそ、真の原価管理と言えます。そのために不可欠なのが、「予算実績管理機能」と「差異分析機能」、そしてそれらの結果を分かりやすく表示する「レポート出力機能」です。これらの機能は、PDCAサイクル(Plan-Do-Check-Action)を回し、継続的なコスト削減と収益性向上を実現するためのエンジンとなります。
結論として、予算実績管理・差異分析機能とレポート出力機能は、計画と結果のギャップを明らかにし、その原因を深掘りすることで、具体的な改善アクションを導き出し、経営管理レベルを向上させるための必須機能です。
予算実績管理機能
この機能は、事前に設定した実行予算や標準原価と、実際に発生した原価(実績原価)を同一画面上やレポート上で対比して表示するものです。プロジェクトの進捗状況や製品の生産状況に応じて、予算消化率や達成度などをリアルタイムに近い形で確認することができます。これにより、予算オーバーの兆候や計画からの乖離を早期に検知し、迅速な対応を促します。
例えば、ある建設現場では、原価管理システムの予算実績管理画面を毎日確認することで、特定の資材費が予算を上回りそうになっていることにいち早く気づき、代替資材の検討や発注先との交渉を行うことで、最終的な予算超過を最小限に抑えることができました。このようなタイムリーな管理は、Excelベースではなかなか難しいものです。
差異分析機能
単に予算と実績の差額を示すだけでなく、なぜその差異が発生したのか、その要因を掘り下げて分析する機能が「差異分析機能」です。例えば、標準原価計算を採用している企業であれば、実際原価との間に生じた価格差異(材料の購入価格が標準と異なった、など)や数量差異(材料の使用量が標準と異なった、作業時間が標準と異なった、など)を自動的に計算し、その内訳を表示します。
私が支援したある機械部品メーカーH社様では、原価管理システムの差異分析機能を活用し、ある製品の労務費が常に標準よりも高いことに気づきました。詳しく調べてみると、特定の工程で熟練作業者の不足から新人作業者が多く割り当てられており、作業効率が想定よりも低いことが判明しました。この分析結果をもとに、H社様は新人向けの集中的な研修プログラムを実施し、併せて作業手順書の見直しを行うことで、数ヶ月後にはその工程の労務費差異を大幅に縮小することに成功しました。このように、差異分析機能は、問題点の根本原因を特定し、具体的な改善策を導き出すための強力なツールとなります。
レポート出力機能
予算実績対比表、差異分析報告書、製品別損益一覧表、部門別原価報告書、プロジェクト別採算表など、原価管理に必要な各種帳票やレポートを、定型的なフォーマットで、あるいはユーザーがカスタマイズした形式で出力する機能です。多くの原価管理システムでは、これらのレポートをExcel形式やPDF形式で出力したり、BIツールと連携してより高度なグラフやダッシュボードとして可視化したりすることが可能です。
これにより、経営層は企業全体の収益状況やコスト構造を迅速に把握し、的確な意思決定を行うことができます。また、各部門の管理者は、自部門の業績や課題を具体的なデータで確認し、担当者レベルでは、日々の業務改善に役立つ情報を得ることができます。レポートの種類やカスタマイズの柔軟性、そして見やすさや分かりやすさが、原価管理システム選定の際のポイントの一つとなります。
これらの機能を効果的に活用することで、企業は「計画を立て(予算設定)、実行し(実績把握)、結果を検証し(差異分析)、改善する(アクション)」という原価管理のPDCAサイクルをスムーズに回せるようになります。これにより、継続的な業務改善と収益性の向上が期待できるのです。
4.4. 販売管理・生産管理・会計システム等との連携機能
原価管理システムは、それ単独で全てのデータを抱え込み、独立して機能するわけではありません。むしろ、企業内で既に稼働している他の業務システム(販売管理 システム、生産管理 システム、購買管理 システム、勤怠管理
システム、会計システムなど)と密接に連携することで、その真価を最大限に発揮します。これらの基幹システムとのスムーズなデータ連携機能は、原価管理業務の効率化と精度向上に不可欠であり、システム選定における極めて重要なポイントとなります。
結論として、他の業務システムとの連携機能は、データ入力の二度手間を排除し、リアルタイムな情報共有を促進し、企業全体の情報システムの一貫性と効率性を高めるために不可欠です。
なぜシステム連携がそれほど重要なのでしょうか。その主な理由と具体的な連携イメージは以下の通りです。
データ入力作業の自動化と効率化
原価計算に必要なデータの多くは、既に他の業務システムに存在しています。例えば、製品の受注数量や売上金額は販売管理システムに、材料の仕入れ単価や在庫数量は購買管理システムや在庫管理システムに、従業員の作業時間は勤怠管理システムや生産管理システム(製造実行システム:MES)に、実際に支払われた経費の情報は会計システムに記録されています。これらのデータを原価管理システムに再度手入力するのは、膨大な手間と時間がかかるだけでなく、入力ミスを誘発する原因にもなります。
システム連携機能があれば、これらのデータを自動的に、あるいは簡単な操作で原価管理システムに取り込むことが可能になります。これにより、データ入力の負担が劇的に軽減され、担当者はより付加価値の高い分析業務に集中できるようになります。
私が支援したある自動車部品メーカーI社様では、原価管理システム導入前は、各システムから出力したExcelファイルを担当者が手作業で集計し、原価計算用のExcelシートに転記するという煩雑な作業を毎月行っていました。システム導入と同時に主要な基幹システムとのAPI連携を構築した結果、このデータ収集・転記作業がほぼゼロになり、月次決算の早期化にも大きく貢献しました。
データのリアルタイム性と一貫性の確保
システム連携により、各業務システムで発生した情報が、タイムラグなく原価管理システムに反映されるようになります(あるいは定期的なバッチ処理で同期されます)。これにより、常に最新の情報に基づいた原価計算や分析が可能となり、経営判断の迅速化に繋がります。また、複数のシステム間でデータが二重、三重に存在することによる不整合や矛盾を防ぎ、企業全体としてのデータの一貫性と信頼性を高めることができます。
例えば、販売管理 システムで受注情報が更新されれば、それが速やかに原価管理システムの生産計画や原価予測に反映される、といった具合です。
マスタデータの一元管理
品目マスター、顧客マスター、仕入先マスター、部門マスターなど、多くの業務システムで共通して利用されるマスターデータは、一元的に管理されることが理想です。原価管理システムが他のシステムとマスターデータを共有・同期する機能を備えていれば、マスターメンテナンスの手間が軽減されるだけでなく、データの不整合を防ぐことができます。例えば、会計システムの勘定科目マスターや部門マスターを原価管理システムと同期できれば、経費データの取り込みや部門別原価計算がスムーズに行えます。
原価管理システムを選定する際には、自社で既に利用している基幹システムとの連携実績が豊富か、標準的なAPI(Application Programming Interface)が用意されているか、あるいはCSVファイルなど汎用的な形式でのデータ連携が容易に行えるか、といった点を十分に確認することが重要です。特に、企業の基幹となるERP(Enterprise Resource Planning:統合基幹業務システム)の一部として原価管理機能が提供されている場合は、会計、販売、生産などのモジュールと最初から緊密に連携しているため、データ連携の課題は発生しにくいというメリットがあります。一方で、独立した専門特化型の原価管理システムを導入する場合は、既存システムとの連携の可否やその方法、コストなどを慎重に検討する必要があります。スムーズなシステム連携は、原価管理システム導入の成功を左右する大きなポイントの一つです。
4.5.【業種別】特に注目したい機能(製造業、建設業など)
これまで述べてきた主要機能は、多くの業種で共通して重要となるものですが、業種特有の業務プロセスや管理ポイントに対応するために、特定の業種向けに強化された機能や、特に注目すべき機能が存在します。ここでは、私たちのお客様の多くを占める「製造業」と、プロジェクト単位での原価管理が不可欠な「建設業」を例に挙げ、それぞれの業種で原価管理システムを選ぶ際に特に注目したい機能について解説します。
結論として、自社の業種特性を深く理解し、それに特化した機能や柔軟な設定が可能な原価管理システムを選ぶことが、導入効果を最大化する上で不可欠です。
1. 製造業向けに特に注目したい機能
製造業、特に多品種少量生産を営む中小製造業では、製品ごとの正確な原価把握と、生産プロセス全体の効率化が課題となります。そのため、以下のような機能が重要になります。
詳細な部品表(BOM)管理機能と連携
製品の設計図とも言える部品表(BOM)は、材料費計算の基礎となります。原価管理システムが、複数階層のBOMや設計変更に柔軟に対応できるか、また、BOMの変更が即座に標準原価や実際原価計算に反映されるかは非常に重要です。PDM(製品データ管理)システムやCADシステムとBOM情報を連携できる製品もあります。
工程別原価計算機能
製造プロセスを複数の工程に分け、各工程で発生する加工費や労務費を把握・集計する機能です。これにより、どの工程にコストが集中しているのか、どの工程にボトルネックがあるのかを特定し、生産性向上やコスト削減のポイントを明確にすることができます。仕掛品評価にも役立ちます。
ロット別原価管理機能
同じ製品であっても、生産ロットによって材料の仕入れ単価や作業条件が異なる場合があります。ロットごとに原価を追跡・管理することで、より正確な原価把握とトレーサビリティの確保に繋がります。特に食品業界や医薬品業界など、品質管理やロット追跡が重要な業種で有効です。
実際原価と標準原価の精緻な差異分析機能
製造業では、標準原価を設定し、実際原価との差異を分析することでコスト管理を行うことが一般的です。材料価格差異、材料数量差異、作業時間差異、賃率差異など、差異の要因を詳細に分析できる機能が求められます。
生産管理システ、MESとの連携
生産計画、製造実績(良品数、不良品数、作業時間など)、機械の稼働状況といった生産現場のリアルタイムな情報を原価管理システムにスムーズに取り込むための連携機能は、実際原価の精度向上と効率化に不可欠です。
ある電子機器メーカーJ社様は、多品種少量生産で製品のライフサイクルも短いため、頻繁な設計変更と部品変更に原価計算が追いつかないという課題を抱えていました。詳細なBOM管理機能とPDMシステム連携機能を備えた原価管理システムを導入したことで、設計変更情報が即座に原価に反映され、常に最新の原価に基づいた見積もりや採算判断が可能となり、新製品の市場投入スピード向上にも貢献しました。
2. 建設業向けに特に注目したい機能
建設業では、個別の工事プロジェクト単位での原価管理が基本となり、実行予算の精度と進捗に合わせたタイムリーな原価把握が極めて重要です。
工事台帳管理機能(工事原価管理)
工事ごとに、材料費、労務費、外注費、経費などの原価要素を詳細に集計・管理する機能です。実行予算と実績を対比し、工事の進捗度に応じた原価発生状況や利益状況をリアルタイムに把握することが求められます。
実行予算管理機能の充実
詳細な費目ごとに実行予算を編成し、承認ワークフローを経て管理する機能。過去の類似工事の予算を流用したり、Excelで作成した予算データをインポートしたりできる柔軟性も重要です。予算変更の履歴管理機能も不可欠です。
発注・支払管理との連携
実際に業者に発注した金額や支払った金額を、工事原価として正確に紐付けて計上するための機能。購買システムや会計システムとの連携が重要になります。
工事進捗度管理機能
工事の進捗度合いに応じて、出来高や原価を評価し、予定通りに進んでいるか、コストが予算内に収まっているかを管理する機能。これにより、早期に問題を発見し、対策を講じることができます。
労務費管理の精度
建設現場では、自社社員だけでなく、協力会社の作業員も多く関わります。誰がどの工事にどれだけ従事したかを正確に把握し、労務費を適切に按分・集計する機能が求められます。出面管理システムとの連携も有効です。
豊富な帳票出力
工事原価報告書、実行予算実績対比表、工事未成工事支出金一覧など、建設業特有の管理帳票を標準で出力できるか、あるいはカスタマイズして作成できるかがポイントです。「どっと原価シリーズ」のような建設業特化型の原価管理システムは、これらの機能が充実している傾向にあります。
これらの業種特化機能は、その業界の商習慣や法制度、特有の管理ポイントに深く根ざしているため、原価管理システムを選定する際には、自社の業種に強みを持つベンダーや製品を検討することが、導入後のミスマッチを防ぎ、効果を最大限に引き出すための近道となります。自社の業務を詳細に分析し、本当に必要な機能は何かを慎重に見極めることが何よりも大切です。
5. 原価管理システムのタイプ別特徴と比較:自社に合う型は?
原価管理システムの導入を検討する際、その機能だけでなく、「どのような提供形態のシステムを選ぶか」という点も非常に重要な選択肢となります。原価管理システムには、大きく分けてクラウド型(SaaS)、オンプレミス型といった提供環境の違いや、ERP一体型、専用特化型といったシステム構成の違い、さらにはパッケージ型、スクラッチ開発といった開発方法の違いなど、いくつかのタイプが存在します。それぞれのタイプには独自の特徴があり、メリット・デメリットも異なります。自社の規模、予算、IT環境、セキュリティポリシー、そして将来の事業展開などを総合的に考慮し、最適なタイプを選ぶことが、原価管理システム導入を成功に導くための鍵となります。この章では、主要な原価管理システムのタイプ別の特徴を比較しながら、中小製造業の皆様が自社に最適な「型」を見つけるためのポイントを解説します。
5.1.クラウド型(SaaS)システムの特徴・メリット・デメリット
近年、多くの業務システムで主流となりつつあるのが「クラウド型(SaaS:Software as a
Service)」の原価管理システムです。これは、システムベンダーがインターネット経由で原価管理機能をサービスとして提供する形態で、ユーザーは自社でサーバーなどのITインフラを構築・運用する必要がありません。ブラウザとインターネット接続環境があれば、場所やデバイスを問わずにシステムを利用できる手軽さが大きな特徴です。
結論として、クラウド型原価管理システムは、初期費用を抑えて迅速に導入でき、運用負荷も軽減できるため、特にIT専門の担当者が少ない中小企業や、柔軟な働き方に対応したい企業にとって魅力的な選択肢です。
クラウド型原価管理システムの主なメリット:
初期費用の抑制と迅速な導入が可能
自社でサーバーを購入したり、ソフトウェアをインストールしたりする必要がないため、オンプレミス型に比べて導入にかかる初期費用を大幅に抑えることができます。多くの場合、アカウントを契約し、基本的な設定を済ませればすぐに利用を開始できるため、導入期間も短縮できます。
ある製造業K社様は、資金調達後すぐにでも原価管理を始めたかったため、初期コストが低く、数週間で稼働開始できたクラウド型原価管理システムを採用し、迅速な事業立ち上げに成功しました。このスピード感はクラウド型ならではのメリットと言えるでしょう。
運用・保守の負荷軽減
詳細な費目ごとに実行予算を編成し、承認ワークフローを経て管理する機能。過去の類似工事の予算を流用したり、Excelで作成した予算データをインポートしたりできる柔軟性も重要です。予算変更の履歴管理機能も不可欠です。
場所やデバイスを選ばない柔軟なアクセス
インターネット接続環境さえあれば、オフィスだけでなく、自宅や出張先など、どこからでもシステムにアクセスできます。また、パソコンだけでなく、タブレットやスマートフォンからの利用に対応しているサービスも増えています。これにより、経営者が外出先で最新の原価情報を確認したり、工場長が現場でタブレットを使いながら実績入力をしたりといった、より柔軟で効率的な働き方が実現できます。
常に最新機能を利用可能・拡張性が高い
クラウド型システムは、ベンダーによって定期的に機能改善やセキュリティ強化のためのアップデートが自動的に行われるため、ユーザーは常に最新バージョンのシステムを利用できます。また、ユーザー数や利用する機能の増減、ストレージ容量の追加など、企業の成長や事業変化に合わせて柔軟にサービス内容をスケールアップ/ダウンしやすい点もメリットです。
災害時の事業継続性(BCP)向上
データはベンダーが管理する堅牢なデータセンターに保管されるため、自社でサーバーを運用する場合に比べて、地震や火災といった災害時におけるデータ消失のリスクを低減できます。これにより、事業継続計画(BCP)の観点からも安心感が増します。
クラウド型原価管理システムの主なデメリット・注意点:
カスタマイズの制約
クラウド型システムは、多くの企業が共通で利用することを前提としているため、オンプレミス型に比べて、自社の特殊な業務フローに合わせた大幅なカスタマイズや独自機能の追加が難しい場合があります。設定範囲内での調整は可能ですが、それ以上の個別対応は限定的となることが多いです。そのため、システムに自社の業務を合わせる、という発想の転換が求められることもあります。
インターネット接続が必須
システムの利用には安定したインターネット接続環境が不可欠です。オフライン環境では基本的に利用できません。また、通信速度が遅い環境では、システムのレスポンスが悪影響を受ける可能性もあります。
セキュリティへの懸念(データ管理)
企業の重要な原価データを外部のサーバーに預けることになるため、セキュリティに対する懸念を持つ企業も少なくありません。サービス選定時には、ベンダーがどのようなセキュリティ対策(データ暗号化、アクセス制御、不正侵入防止など)を講じているか、データセンターの信頼性はどうか、国際的なセキュリティ認証を取得しているかなどを十分に確認する必要があります。
月額(年額)費用の継続発生
初期費用は抑えられますが、利用している限り月額または年額のサービス利用料が継続的に発生します。長期間利用する場合、オンプレミス型よりも総コストが高くなる可能性も考慮に入れる必要があります。ユーザー数やデータ量に応じて費用が変動する料金体系の場合は、将来的なコスト増も見込んでおく必要があります。
サービス終了のリスク
万が一、ベンダーがサービス提供を終了してしまった場合、システムが利用できなくなるリスクがゼロではありません。ベンダーの経営安定性や事業継続性、サービス移行に関するポリシーなども、選定時のポイントとして考慮しておくとよいでしょう。
クラウド型は、特にIT投資を抑えたい、専門のIT担当者が不足している、短期間でシステムを稼働させたい、テレワークなど柔軟な働き方を推進したい、といったニーズを持つ中小製造業にとって、有力な選択肢の一つです。自社の業務プロセスが標準的なものであれば、大きなメリットを享受できるでしょう。
5.2.オンプレミス型システムの特徴・メリット・デメリット
「オンプレミス型」の原価管理システムは、自社のサーバーやコンピューターにソフトウェアをインストールし、自社内でシステムを構築・運用する従来ながらの提供形態です。クラウド型の普及が進む中でも、セキュリティポリシーや既存システムとの連携、大幅なカスタマイズの必要性などから、依然としてオンプレミス型を選択する企業も少なくありません。
結論として、オンプレミス型原価管理システムは、初期投資と運用負荷は高めですが、自社の要件に合わせた高度なカスタマイズが可能で、セキュリティを自社管理下に置けるため、独自の業務プロセスを持つ企業や、機密性の高い情報を扱う企業に適しています。
オンプレミス型原価管理システムの主なメリット:
高度なカスタマイズ性と柔軟性
自社内にシステムを構築するため、自社の特有な業務フローや管理項目に合わせて、システムを大幅にカスタマイズしたり、独自の機能を追加したりすることが比較的容易です。クラウド型では対応が難しい複雑な要件にも柔軟に対応できる点が最大のメリットと言えるでしょう。
ある特殊機械メーカーL社様は、非常に複雑な原価計算ロジックと、独自の帳票フォーマットが多数存在したため、オンプレミス型を選択し、徹底的なカスタマイズを行うことで、現場の要求をほぼ完全に満たす原価管理システムを構築しました。
セキュリティの自社管理
システムやデータを全て自社の管理下に置くため、外部のネットワークから隔離したクローズドな環境で運用するなど、自社のセキュリティポリシーに合わせた厳格なセキュリティ対策を講じることが可能です。特に機密性の高い原価情報や顧客情報を扱う企業にとっては、この点は大きな安心材料となります。
既存システムとの連携のしやすさ(場合による)
自社内に他のオンプレミス型の基幹システム(ERP、生産管理、会計など)が既に稼働している場合、同じネットワーク環境内で直接的なデータ連携を構築しやすく、より密接でリアルタイムな連携が実現できることがあります。ただし、連携先のシステムや原価管理システムの仕様に大きく左右されるため、一概には言えません。
ランニングコストの変動が少ない(買い切り型の場合)
ソフトウェアライセンスを買い取る形式の場合、初期費用は高額になりますが、月々の利用料は発生しないか、あるいは保守費用のみとなるため、長期的に見るとランニングコストを抑えられる可能性があります。(ただし、サーバー維持費や専任のIT担当者の人件費は別途考慮する必要があります。)
オフライン環境でも利用可能
インターネット接続に依存しないため、万が一インターネット回線に障害が発生しても、社内ネットワークが正常であればシステムを継続して利用できます。
オンプレミス型原価管理システムの主なデメリット・注意点:
高額な初期費用と長期の導入期間
サーバーやネットワーク機器の購入・構築費用、ソフトウェアライセンス費用、カスタマイズ費用など、導入には多額の初期投資が必要となります。また、システム構築やカスタマイズ、テストなどに時間がかかるため、導入期間もクラウド型に比べて長期化する傾向があります。
運用・保守の負荷と専門知識の必要性
サーバーの管理、ソフトウェアのアップデート、セキュリティ対策、障害対応、バックアップ作業など、システムの運用・保守は全て自社で行う必要があります。これには専門的な知識を持つIT担当者が不可欠であり、その人件費も考慮しなければなりません。これらの運用負荷は中小企業にとっては大きな負担となり得ます。
災害時のリスクとBCP対策の必要性
自社内にサーバーを設置する場合、地震や火災、水害などの災害によってシステムが物理的に損傷したり、データが消失したりするリスクがあります。そのため、遠隔地へのバックアップや冗長構成の構築など、自社でBCP対策を講じる必要があります。
機能追加やバージョンアップのコストと手間
新しい機能を追加したり、システムをバージョンアップしたりする際には、追加の費用や作業が発生することが一般的です。クラウド型のように自動的に最新機能が提供されるわけではありません。
場所やデバイスの制約
基本的には社内ネットワークからのアクセスが前提となるため、外出先や自宅からシステムを利用するには、VPN接続などの別途の仕組みが必要となり、クラウド型ほどの柔軟性はありません。
オンプレミス型は、予算やITリソースに比較的余裕があり、自社独自の業務プロセスへの適合性や、高度なセキュリティ要件を重視する中小製造業にとって検討の価値があります。特に、既存の基幹システムとの密な連携や、法規制などでデータの外部保管が難しい場合などに選択されることがあります。
5.3.ERP一体型と専用特化型システムの違いと選び方
原価管理システムを選ぶ際、そのシステムが企業の他の業務システムとどのような関係性を持つか、という観点も非常に重要です。この観点からは、大きく「ERP(Enterprise Resource Planning:統合基幹業務システム)一体型」と「専用特化型」の二つのタイプに分類できます。それぞれのタイプが持つ特徴を理解し、自社の情報システム全体の構想や原価管理に求める専門性の度合いなどを考慮して選択することが求められます。
結論として、ERP一体型はデータ連携の容易さと全社的な情報統合に強みがあり、専用特化型は原価管理機能の専門性と深掘りに強みがあります。どちらを選ぶかは、企業のIT戦略や業務特性によって異なります。
ERP一体型原価管理システムの特徴:
ERPとは、会計、販売、購買、在庫、生産、人事など、企業の主要な基幹業務を統合的に管理するシステムのことです。ERP一体型の原価管理システムは、このERPパッケージの一つのモジュール(機能部品)として原価管理機能が提供されているものです。
•メリット:
データ連携の優位性
会計、販売、生産などの他モジュールと最初から密接にデータ連携がなされているため、原価計算に必要な情報(売上実績、生産実績、材料消費実績、経費情報など)をスムーズかつリアルタイムに収集・活用できます。データの二重入力や不整合が起こりにくく、業務効率化とデータ精度向上に大きく貢献します。
全社的な情報の一元管理
原価情報だけでなく、企業活動全体の情報が単一のシステム上で一元管理されるため、経営状況の全体像を把握しやすくなります。原価と他の経営指標との関連分析なども容易に行えます。
運用・保守の効率化(場合による)
複数の個別システムをバラバラに運用するよりも、ERPとして一つのシステム基盤上で運用することで、IT管理の負荷が軽減される可能性があります。
例えば、ある中堅製造業M社様は、以前は販売、生産、会計、原価管理がそれぞれ独立したシステムで稼働しており、データ連携に多くの手間と時間を費やしていました。ERP一体型の原価管理システムを導入したことで、これらのデータがシームレスに繋がり、月次決算が大幅に早期化されるとともに、原価情報に基づいた生産計画の最適化も実現できました。
•デメリット・注意点:
導入コストと期間
一般的にERPの導入は大規模なプロジェクトとなるため、初期費用が高額になり、導入期間も長期化する傾向があります。
機能の網羅性と専門性のバランス
ERPは幅広い業務をカバーするため、原価管理機能については、専用特化型システムに比べて機能の深さや細やかさ、特定の業種への対応度合いが劣る場合があります。自社が求める原価管理のレベルとERPの機能がマッチするかを慎重に見極める必要があります。
システム全体への影響
原価管理モジュールだけでなく、ERPシステム全体の仕様や操作性に習熟する必要があり、社員教育にも時間がかかります。また、一部のモジュールを変更することがシステム全体に影響を及ぼす可能性も考慮しなければなりません。
専用特化型原価管理システムの特徴:
専用特化型の原価管理システムは、その名の通り、原価管理機能に特化して開発されたシステムです。原価計算や分析機能が非常に充実しており、特定の業種や生産形態に強みを持つ製品も多く存在します。
•メリット:
高度で専門的な機能
原価管理に特化しているため、複雑な配賦ロジック、詳細な差異分析、高度な原価シミュレーションなど、専門性の高い機能が豊富に搭載されていることが多いです。特定の業種(例えば、建設業向けの「どっと原価シリーズ」や、多品種少量生産の製造業向けの特定のシステムなど)のニーズにきめ細かく対応した製品もあります。
比較的柔軟な導入とカスタマイズ
ERP全体を導入するのに比べて、導入範囲が限定されるため、比較的短期間かつ低コストで導入できる場合があります。また、特定の機能に絞ってカスタマイズを行いやすいこともあります。
既存システムとの連携でベストオブブリードを実現可能
会計システムはA社、販売管理システムはB社、そして原価管理システムはC社の専用特化型、といったように、各業務領域で最適なシステムを選択し、それらをAPIなどで連携させる「ベストオブブリード」という考え方にも適しています。
以前、私が相談を受けたあるニッチな市場で高いシェアを持つ部品メーカーN社様は、非常にユニークな製造プロセスと原価計算方法を採っていました。汎用的なERPでは対応が難しかったため、自社の特殊な要件にきめ細かく対応できる専用特化型の原価管理システムを選定し、一部カスタマイズを加えることで、理想的な原価管理を実現しました。
•デメリット・注意点:
他システムとの連携が必須
専用特化型であるため、原価計算に必要なデータを他の基幹システム(販売、生産、会計など)から取得するための連携が不可欠です。この連携の設計や構築に手間やコストがかかる場合があり、連携がスムーズに行えないとシステムの効果が半減してしまいます。
情報が分散する可能性
企業全体の情報が複数のシステムに分散するため、データの一元管理や横断的な分析がERP一体型に比べて難しくなる可能性があります。
複数のベンダーとのやり取り
各システムのベンダーが異なる場合、システム間のトラブル発生時の原因究明や責任の所在が曖昧になるリスクや、運用保守の窓口が複数になる煩雑さがあります。
【選び方のポイント】
ERP一体型が適しているのは、これから基幹システム全体を刷新したい、あるいは既に同ベンダーのERPを一部利用しており、全社的な情報統合と業務効率化を最優先で目指す企業です。一方、専用特化型は、既存の基幹システムはそのまま活かしつつ、原価管理機能だけを高度化したい、あるいは特定の業種や業務に特有の複雑な原価管理要件がある企業に適しています。自社のIT戦略、予算、求める機能の専門性、既存システムとの親和性などを総合的に比較検討し、最適なタイプを選択しましょう。
5.4.パッケージ型とスクラッチ開発の比較ポイント
原価管理システムを導入する際の開発方法という観点からは、「パッケージ型」と「スクラッチ開発」という二つのアプローチが考えられます。パッケージ型は、既製品のソフトウェアを導入する方法であり、スクラッチ開発は、自社の要件に合わせてオーダーメイドでシステムをゼロから開発する方法です。どちらの方法にも一長一短があり、自社の状況に合わせて慎重に選択する必要があります。
結論として、パッケージ型はコストと導入期間を抑えたい場合に、スクラッチ開発は独自の複雑な要件や他社との差別化をシステムで実現したい場合に適した選択肢ですが、多くの中小企業にとってはパッケージ型のカスタマイズが現実的な落としどころとなることが多いです。
パッケージ型原価管理システムの特徴:
パッケージ型システムは、多くの企業で共通して必要とされる標準的な原価管理機能をあらかじめ搭載した既製のソフトウェア製品です。ベンダーが開発・販売しており、ユーザーはライセンスを購入またはクラウドサービスとして契約して利用します。
•メリット:
導入コストと期間の抑制
既に完成されたシステムであるため、ゼロから開発するスクラッチ開発に比べて、一般的に導入コストを大幅に抑えることができ、導入期間も短縮できます。
機能の網羅性と安定性
多くの企業での利用実績があるため、機能がある程度網羅されており、バグなども比較的少なく、システムの品質や安定性が期待できます。業界標準のベストプラクティスが取り入れられていることもあります。
豊富な導入事例とノウハウ
多くの導入事例があるため、自社と似たような企業での活用方法や導入時の注意点などを参考にすることができます。ベンダーやコンサルタントも導入ノウハウを蓄積しています。
バージョンアップによる機能向上
ベンダーによる定期的なバージョンアップによって、新しい機能が追加されたり、既存機能が改善されたりするメリットがあります。
•デメリット・注意点:
カスタマイズの限界
自社の独自の業務フローや特殊な要件に完全に合致しない場合があります。ある程度の設定変更やアドオン開発(追加機能の開発)が可能なパッケージもありますが、スクラッチ開発ほどの柔軟性はありません。システムに業務を合わせる必要が生じることもあります。
不要な機能の存在
自社にとっては使わない機能が多く搭載されている場合があり、それが操作性を複雑にしたり、システムを重くしたりする可能性があります。
ベンダーへの依存
システムの将来性やサポートは、提供元であるベンダーの方針に大きく左右されます。
スクラッチ開発(オーダーメイド開発)の特徴:
スクラッチ開発は、自社の特定の要件や業務プロセスに合わせて、原価管理システムを完全にオーダーメイドでゼロから設計・開発する方法です。
•メリット:
完全な要件合致と高い柔軟性
自社の独自の業務フロー、管理項目、帳票フォーマット、原価計算ロジックなどを100%反映した、まさに自社専用のシステムを構築できます。他社にはない競争優位性をシステムで実現したい場合に有効です。
必要な機能のみを実装
自社にとって本当に必要な機能だけを厳選して実装するため、無駄がなく、操作性もシンプルにできる可能性があります。
既存システムとの最適化された連携
既存の他の社内システムとの連携も、自社の環境に合わせて最適な形で設計・構築できます。
•デメリット・注意点:
非常に高額な開発費用
オーダーメイドであるため、パッケージ型に比べて開発費用が格段に高額になります。要件定義から設計、開発、テストまで、多くの工数と専門技術が必要です。
長期の開発期間
ゼロから作り上げるため、システムが完成し、稼働するまでに長い期間(数ヶ月~数年単位)を要します。市場の変化に迅速に対応したい場合には不向きです。
開発プロジェクトの失敗リスク
要件定義が曖昧だったり、開発会社の技術力が不足していたりすると、プロジェクトが頓挫したり、期待した品質のシステムが完成しなかったりするリスクがあります。企業側にシステム開発に関する深い知識やプロジェクト管理能力が求められます。
運用・保守体制の確立が必須
完成したシステムの運用・保守は全て自社で行うか、開発会社と別途保守契約を結ぶ必要があります。システムの仕様を熟知した担当者が社内にいないと、障害発生時や仕様変更時に困る可能性があります。
【選び方のポイント】
多くの中小製造業にとっては、ゼロからのスクラッチ開発はコストやリスクの観点からハードルが高いのが実情です。まずは、自社の業種や規模、主要な業務要件に適合するパッケージ型原価管理システムをいくつかピックアップし、デモンストレーションを受けたり、トライアルを試したりしながら、機能の適合度やカスタマイズの柔軟性を比較検討するのが現実的なアプローチです。その上で、どうしてもパッケージでは対応できない重要な要件がある場合に限り、その部分的なアドオン開発や、限定的な範囲でのスクラッチ開発を検討するというのが賢明な選択と言えるでしょう。
私がよくアドバイスするのは、「システムに100%合わせる必要もなければ、100%自社に合わせようと固執する必要もない」ということです。パッケージ型の標準機能を最大限に活かしつつ、本当に譲れないポイントだけをカスタマイズで対応する、あるいは、システム導入を機に非効率な業務プロセス自体を見直す、といったバランス感覚が重要です。
6.【2025年最新版】失敗しない原価管理システムの選び方:7つの重要ポイント
原価管理システムの導入は、企業の経営体質を強化し、利益構造を改善するための重要な投資です。しかし、市場には多種多様な原価管理システムが存在し、「どの製品を選ぶべきか」「自社に本当に合ったシステムは何か」と頭を悩ませている経営者様やご担当者様も少なくないでしょう。システム選定の失敗は、期待した効果が得られないばかりか、無駄なコストと時間を費やし、現場の混乱を招くことにもなりかねません。そこでこの章では、私たちコンサルティング会社が数多くの中小製造業のシステム導入を支援してきた経験と、2025年現在の最新の市場動向を踏まえ、「失敗しない原価管理システムの選び方」として、特に重要となる7つのポイントを徹底的に解説していきます。これらのポイントを押さえることで、貴社にとって最適な一選びが可能になるはずです。
6.1. ポイント1:自社の課題と導入目的を明確化する(現状分析)
原価管理システム選定における最も重要な最初のステップは、「なぜ原価管理システムを導入するのか?」という根本的な問いに明確な答えを出すことです。つまり、自社が現在抱えている原価管理上の具体的な課題を洗い出し、システム導入によって何を達成したいのか、その「導入目的」を明確に定義することが不可欠です。これが曖昧なままシステム選定を進めてしまうと、多機能で高価なシステムを導入したものの、結局使わない機能ばかりだったり、本当に解決したかった課題が置き去りにされたりする結果を招きかねません。
結論として、原価管理システム導入の成功は、導入前に自社の現状課題を徹底的に分析し、システムによって達成したい具体的な目的・目標を社内で共有・合意形成することから始まります。
まず、現状分析として、以下のような点を具体的に洗い出してみましょう。
現在の原価計算・管理方法
Excelで管理しているのか、手作業が中心なのか、あるいは旧式のオフコンシステムを利用しているのか。
抱えている問題点
o 原価計算に時間がかかりすぎている(月次決算の遅れなど)。
o 製品ごとの正確な原価が把握できていない(どんぶり勘定になっている)。
o データ入力の手間が大きい、ミスが多い。
o リアルタイムな原価情報が取得できず、経営判断が遅れる。
o 間接費の配賦基準が曖昧で、原価の信頼性に欠ける。
o 予算と実績の差異分析が十分にできていない。
o 採算の悪い製品やプロジェクトが見過ごされている。
o 原価情報が経営戦略に活かされていない。
o 属人化しており、担当者がいないと業務が滞る。
課題の優先順位
上記のような課題の中から、特に緊急度や重要度の高いものは何か、優先順位をつけます。
次に、これらの課題を踏まえ、原価管理システム導入によって達成したい「導入目的」を具体的に設定します。目的は、定性的なものだけでなく、可能な限り定量的な目標(KPI:重要業績評価指標)を伴うことが望ましいです。
例1:原価計算業務の効率化
o 定性目的:データ入力や集計作業の手間を削減し、担当者の負担を軽減する。
o 定量目標:月次の原価計算にかかる時間を現状の〇〇時間から〇〇時間へ短縮する(例:50%削減)。データ入力ミスを〇%削減する。
例2:正確な製品別原価の把握
o 定性目的:全ての製品について、信頼性の高い原価情報をタイムリーに把握する。
o 定量目標:製品別損益を週次で把握できるようにする。原価差異を±〇%以内に抑える。
例3:経営判断の迅速化・高度化
o 定性目的:原価情報を活用し、データに基づいた迅速な経営判断を行う。
o 定量目標:不採算製品の特定と対策実行までの期間を〇ヶ月短縮する。新製品の価格設定における原価ベースのシミュレーションを必ず実施する。
私が以前コンサルティングで関わったある電子部品メーカーP社様は、「とにかく新しいシステムが欲しい」という漠然とした要望でシステム選定を開始しようとしていました。しかし、私たちが現状の業務ヒアリングと課題の掘り下げを徹底的に行った結果、「多品種少量生産における個々の製品の正確な原価が全く見えておらず、赤字受注を繰り返している可能性が高い」という深刻な課題が浮き彫りになりました。そこで、導入目的を「製品別実際原価の精度向上と、週次での損益把握体制の確立」と明確に定めました。この明確な目的があったからこそ、P社様は数ある原価管理システムの中から、自社の生産形態に最適な実際原価計算機能とリアルタイム分析機能に優れた製品を選択でき、導入後には期待通りの効果を上げることができました。
導入目的が明確になれば、おのずとシステムに求めるべき機能の優先順位も見えてきます。この最初のポイントを疎かにせず、時間をかけてでも社内で十分に議論し、合意形成を行うことが、失敗しない原価管理システム選びの最も重要な土台となるのです。2025年現在、DX推進が叫ばれる中で、システム導入そのものが目的化しないよう、常に「何のために導入するのか」を問い続ける姿勢が求められます。
6.2.ポイント2:企業規模や業種(製造業・建設業など)への適合性を見極める
自社の課題と導入目的が明確になったら、次に検討すべきポイントは、「システムが自社の企業規模や業種特性に適合しているか」という点です。大企業向けの高機能で複雑な原価管理システムが、必ずしも中小企業にとって最適とは限りません。また、業種によって原価管理のポイントや求められる機能も大きく異なります。特に、私たちのお客様である多品種少量生産の製造業や、プロジェクト単位での管理が不可欠な建設業などでは、その業種特有のニーズにきめ細かく対応できるシステムを選ぶことが成功の鍵となります。
結論として、企業の成長ステージやリソース、そして業種特有の商習慣や管理手法にマッチした原価管理システムを選ぶことが、導入後のスムーズな運用と効果の最大化につながります。
まず、企業規模への適合性についてです。
中小企業の場合
o コストパフォーマンス
予算が限られていることが多いため、初期費用やランニングコストを抑えられるクラウド型(SaaS)の原価管理システムが有力な選択肢となります。
o 操作の容易さと導入のしやすさ
専門のIT担当者が少ないケースが多いため、直感的に操作でき、導入や設定が比較的簡単なシステムが望ましいです。手厚い導入サポートや分かりやすいマニュアルが提供されているかも確認ポイントです。
o 必要十分な機能
大企業向けのような過剰な機能は不要な場合が多く、自社の業務に本当に必要な機能を過不足なく備えているかを見極めることが重要です。
中堅・大企業の場合
o 拡張性と柔軟性
将来的な事業拡大や組織変更にも対応できる拡張性や、複雑な業務プロセスに合わせたカスタマイズの柔軟性が求められます。
o 内部統制への対応
監査対応やセキュリティ要件など、内部統制を支える機能(ログ管理、権限設定など)が充実しているかも重要なポイントです。
o 多言語・多通貨対応(グローバル企業の場合)
海外拠点を持つ企業の場合は、多言語・多通貨に対応している原価管理システムが必要になります。
次に、業種への適合性です。ここでは特に製造業と建設業に焦点を当てますが、他の業種でも同様に、自社の業種特性を考慮することが重要です。
6.2.1.製造業向けシステムの選び方のポイントと機能要件
製造業、特に多品種少量生産や個別受注生産を特徴とする中小製造業においては、製品ごとの正確な原価把握と、生産プロセスの効率化が原価管理の核心となります。2025年現在、サプライチェーンの不安定化や顧客ニーズの多様化は、この課題をより一層複雑にしています。したがって、原価管理システム選定時には、以下のような製造業特有のポイントと機能要件を慎重に確認する必要があります。
精緻な部品表(BOM)管理機能と設計変更への対応
製造業の原価計算の基礎となるのは、製品を構成する部品や原材料の一覧である部品表(BOM)です。原価管理システムが、複数階層のBOM(組立品がさらに複数の部品で構成されるなど)を正確に扱えるか、設計変更や仕様変更があった場合に、その変更がスムーズかつ迅速にBOMに反映され、標準原価や実際原価の再計算が行えるかは極めて重要です。変更履歴の管理機能や版管理機能の有無も確認しましょう。PDM(製品データ管理)システムやCADシステムとBOM情報を連携できる製品であれば、設計から原価への一気通貫した情報管理が実現できます。
詳細な工程別原価計算とリアルタイムな作業時間収集の仕組み
製品が完成するまでには、切断、加工、組立、検査など複数の製造工程を経ることが一般的です。各工程でどれだけの材料費、労務費、経費が発生したかを把握する「工程別原価計算」は、製造プロセスのボトルネック発見や効率改善に不可欠です。特に労務費に関しては、作業者がどの製品のどの工程にどれだけの時間を費やしたかを正確に収集する仕組み(例えば、RFIDやバーコードリーダー、タブレット端末を活用した実績入力システムとの連携など)が重要となります。これにより、工程ごとの実際の作業時間に基づいた、より精度の高い労務費計算が可能になります。
多様な生産形態への対応(ロット生産、個別受注生産など)
製造業と一口に言っても、見込み生産、ロット生産、個別受注生産など、その生産形態はさまざまです。原価管理システムが、自社の主要な生産形態に合った原価計算方法(例えば、ロット別原価計算、ジョブオーダー別原価計算など)をサポートしているかを必ず確認しましょう。多品種少量生産の企業では、個々の製品や受注オーダ単位での原価管理が特に重要になります。
仕掛品評価の精度とリアルタイム性
月末や期末に、まだ完成していない製品(仕掛品)がどれだけあるか、そしてその仕掛品にどれだけの原価が投入されているかを正確に評価することは、正しい期間損益を把握する上で不可欠です。原価管理システムが、工程の進捗度合いに応じて仕掛品原価を自動計算し、リアルタイムに近い形で把握できる機能を備えているかを確認しましょう。
実際原価と標準原価の詳細な差異分析機能
多くの製造業では、目標となる標準原価をあらかじめ設定し、実際にかかった実際原価との差異を分析することで、コスト管理を行います。原価管理システムが、材料価格差異、材料歩留差異(数量差異)、作業時間差異、賃率差異、予算差異、能率差異など、差異の要因を詳細に分解して分析できる機能を備えていることが望ましいです。これにより、コストが計画から外れた根本原因を特定し、具体的な改善策を講じることが可能になります。
私が支援したある精密部品メーカーQ社様は、多品種少量でかつ試作品製造も多いという特徴があり、従来のExcelベースの原価計算では、試作段階でのコストが全く把握できていませんでした。製造業向けの機能が充実し、特に工程別の作業時間実績をリアルタイムに細かく収集できる原価管理システムを導入したことで、試作品ごとの実際原価を正確に把握できるようになり、量産移行時の価格設定や採算予測の精度が飛躍的に向上しました。これは、製造業特有のニーズに合ったシステム選定の成功例と言えるでしょう。
6.2.2.建設業向けシステムの選び方のポイントと機能要件(どっと原価シリーズ等)
建設業においては、個別の「工事プロジェクト」単位での原価管理が基本となり、その特徴は製造業とは大きく異なります。工事期間が長期にわたること、実行予算の精度が利益を左右すること、外注費の割合が高いこと、工事の進捗に合わせた原価把握が重要であることなどが挙げられます。2025年現在、資材価格の高騰や人手不足は建設業にとっても深刻な課題であり、より厳密な原価管理が求められています。建設業向けの原価管理システム(例えば、「どっと原価シリーズ」に代表されるような専門システム)を選定する際には、以下のポイントと機能要件に注目する必要があります。
詳細な実行予算管理機能
建設業では、工事を受注する前に、詳細な積算に基づいて実行予算を編成します。この実行予算が工事の採算目標となるため、原価管理システムが、費目(材料費、労務費、外注費、機械経費、共通仮設費、現場経費など)ごとに細かく実行予算を設定・管理できる機能を備えているかが重要です。過去の類似工事の予算を流用したり、Excelで作成した予算データをインポートしたりできる柔軟性や、予算変更の履歴を確実に管理できる機能も不可欠です。
工事台帳(工事原価台帳)の自動作成とリアルタイム更新
工事ごとに、実際に発生した原価(仕入、外注への支払、社員の労務費など)を費目別に集計し、実行予算と対比して表示する「工事台帳」は、建設業の原価管理の基本帳票です。原価管理システムが、日々の取引データからこの工事台帳を自動作成し、リアルタイムに近い形で更新できる機能を備えていれば、工事の採算状況を常に最新の状態で把握できます。
発注・支払管理機能との連携
建設工事では、資材の仕入れや専門工事業者への外注が多数発生します。これらの発注情報や支払情報を、正確に各工事の原価として紐付けて計上するための機能が重要です。購買管理システムや会計システムとスムーズに連携し、二重入力を防ぎ、支払漏れや過払いを防止する仕組みが求められます。
工事進捗度(出来高)管理機能
長期にわたる工事では、工事の進捗度合いに応じて、どれだけの原価が発生し、どれだけの売上(出来高)が計上されるべきかを評価することが重要です。原価管理システムが、工事の進捗度を登録・管理し、それに基づいて予定原価や完成工事原価をシミュレーションしたり、未成工事支出金を正確に把握したりする機能を備えているかを確認しましょう。
労務費・社員別原価の把握
どの社員がどの工事にどれだけの時間(工数)を費やしたかを正確に把握し、それを労務費として各工事に適切に配賦する機能は、特に自社で多くの職人を抱える建設会社にとって重要です。勤怠管理システムや日報システムと連携し、社員ごとの作業実績を効率的に収集できるかがポイントです。
建設業特有の帳票出力
工事一覧表、工事原価報告書、実行予算実績対比表、支払明細書、未成工事支出金明細表など、建設業の業務や会計処理に特有の帳票類を標準で出力できるか、あるいはカスタマイズして容易に作成できるかは、日々の業務効率に大きく影響します。建設業に特化したパッケージシステムは、これらの帳票機能が充実している傾向にあります。
ある工務店R社様は、複数の小規模工事を同時に多数抱えており、各工事の実行予算の精度と、リアルタイムな原価進捗の把握が最大の課題でした。建設業特化型のクラウド原価管理システムを導入し、特に実行予算のテンプレート機能と、スマートフォンから現場の経費を簡単に登録できる機能を活用したことで、予算作成の効率と精度が大幅に向上し、赤字工事の発生を未然に防ぐことができるようになりました。
このように、自社の業種特性を深く理解し、それに合致した機能を備えた原価管理システムを選ぶことが、導入効果を最大限に引き出すための近道となります。
6.3.ポイント3:必要な機能の過不足を見極める(機能比較のコツ)
原価管理システムには実に多様な機能が搭載されていますが、自社にとって本当に必要な機能は何かを冷静に見極めることが、システム選定における失敗を避けるための重要なポイントです。多機能であればあるほど良いというわけではなく、むしろ使わない機能が多すぎると、操作が複雑になったり、システムが重くなったり、余計なコストがかかったりする可能性があります。一方で、必要な機能が不足していれば、導入目的を達成することができません。
結論として、自社の導入目的と業務要件に基づいて「必須機能(Must)」「あったら良い機能(Want)」「不要な機能(Nice to have but not necessary)」を明確に仕分けし、過不足のない機能構成のシステムを選ぶことが、費用対効果の高いシステム導入につながります。
必要な機能を見極めるための具体的なステップと、機能比較のコツは以下の通りです。
RFP(提案依頼書)の作成と機能要件の明確化
ポイント1で明確にした「自社の課題と導入目的」をもとに、原価管理システムに求める具体的な機能要件をリストアップします。この際、各機能について、「なぜその機能が必要なのか」「その機能を使ってどのような業務をどのように改善したいのか」を具体的に記述することが重要です。これらの機能要件をまとめたRFP(提案依頼書)を作成し、複数のシステムベンダーに提示することで、各社からの提案を同じ土俵で比較検討することが可能になります。2025年現在では、RFPにセキュリティ要件やデータ連携要件を詳細に記述することも一般的です。
機能の優先順位付け(Must/Want/Nice to have)
リストアップした機能要件に対して、優先順位を付けます。
o 必須機能(Must): この機能がなければ導入目的を達成できない、絶対に外せない機能。
o あったら良い機能(Want): 必須ではないが、あればより業務効率化や管理レベルの向上が期待できる機能。
o 不要な機能(Nice to have but not necessary): あってもなくても、当面の業務や導入目的の達成には直接影響しない機能。
この仕分け作業を社内の関係者(経営層、経理部門、製造部門、情報システム部門など)で議論し、合意形成を行うことが大切です。
複数システムの機能比較表の作成
検討対象となる複数の原価管理システムについて、RFPで提示した機能要件をどの程度満たしているかを一覧表形式で比較します。各機能について、「〇:標準機能で対応」「△:カスタマイズやオプションで対応可」「×:対応不可」といった形で評価を記入していくと分かりやすいでしょう。この際、単に機能の有無だけでなく、その機能の使い勝手や設定の柔軟性なども、可能な範囲で確認できるとより良い比較ができます。
「ちょうど良い」機能レベルの追求
特に中小製造業の場合、大企業向けの高機能・高性能な原価管理システムは、オーバースペックとなりがちです。操作が複雑で現場が使いこなせない、導入や運用のコストがかかりすぎるといった問題が生じる可能性があります。一方で、あまりに簡易的なシステムでは、将来的な事業拡大や管理レベルの高度化に対応できないかもしれません。自社の現在の業務レベルと、数年先の将来像を見据えて、「ちょうど良い」機能レベルのシステムを選ぶバランス感覚が重要です。
デモンストレーションやトライアルでの確認
機能一覧表だけでは分からない、実際の操作感や機能の細かな仕様については、システムベンダーによるデモンストレーションを依頼したり、可能であれば無料トライアルや体験版を試したりして、実際に触れてみることが極めて重要です。特に、自社の業務シナリオに沿ったデータを使ってデモをしてもらうと、機能の適合度をより具体的に評価できます。
ある食品メーカーS社様は、当初、非常に多機能で高価なERP一体型の原価管理システムを検討していましたが、私たちが機能要件の洗い出しと優先順位付けをサポートした結果、S社様にとって本当に必要なのは、「正確なレシピベースの材料費計算」と「ロット別トレーサビリティ」であり、それ以外の多くの機能は当面不要であることが明確になりました。結果として、S社様はこれらの必須機能に特化した、よりシンプルでコストパフォーマンスの高い中堅企業向け原価管理システムを選択し、スムーズな導入と現場への定着に成功しました。
機能の比較検討は骨の折れる作業ですが、ここを丁寧に行うことが、費用対効果の高い原価管理システム導入に繋がるのです。
6.4.ポイント4:操作性(UI/UX)・画面サンプル・デモの確認
どれほど高機能で素晴らしい原価管理システムであっても、実際にシステムを操作する現場の担当者にとって「使いにくい」「分かりにくい」ものであれば、その効果は半減してしまいます。最悪の場合、せっかく導入したシステムがほとんど使われず、宝の持ち腐れになってしまう可能性すらあります。したがって、システム選定においては、機能面だけでなく、日々の業務でストレスなく使える「操作性(UI:ユーザーインターフェース/UX:ユーザーエクスペリエンス)」を十分に確認することが極めて重要なポイントとなります。
結論として、実際にシステムを利用するユーザー部門の担当者が、直感的で分かりやすく、効率的に作業できる操作性を備えているかを、画面サンプルやデモンストレーション、トライアルを通じて徹底的に確認することが、システム導入後の定着と活用促進に不可欠です。
操作性を確認する際の具体的なポイントは以下の通りです。
直感的で分かりやすい画面デザイン(UI)
メニュー構成が論理的で分かりやすいか、アイコンやボタンの意味が直感的に理解できるか、情報の配置が整理されていて見やすいか、といった画面デザインの基本が重要です。毎日使うシステムだからこそ、見た目の分かりやすさや、操作していて心地よいデザインであることは、利用者のモチベーションにも影響します。2025年現在では、モバイルフレンドリーなデザインや、カスタマイズ可能なダッシュボードを備えた原価管理システムも増えています。
効率的な操作フロー(UX)
日常的に行うデータ入力や検索、レポート出力といった一連の操作が、少ないステップでスムーズに行えるか、画面遷移が分かりやすく、迷うことなく目的の機能にたどり着けるか、といった操作フローの効率性を確認します。例えば、よく使う機能へのショートカットがあるか、キーボード操作だけでも基本的な入力が完結できるか、といった点もチェックポイントです。
入力支援機能の充実度
データ入力時のミスを減らし、効率を上げるための入力支援機能(例えば、ドロップダウンリストからの選択、コード入力による自動表示、過去の入力履歴の参照、入力エラー時の分かりやすいメッセージ表示など)が充実しているかを確認します。これらの細かな機能が、日々の作業負担の軽減に大きく貢献します。
レスポンス速度
画面の切り替えやデータの処理に時間がかかりすぎると、利用者は大きなストレスを感じ、作業効率も低下します。特にクラウド型の原価管理システムを検討する場合は、自社のインターネット環境でデモンストレーションを受け、実際のレスポンス速度を体感することが重要です。
マニュアルやヘルプ機能の分かりやすさ
操作に迷った際や、新しい機能を使う際に参照するマニュアルやオンラインヘルプが、分かりやすく整備されているかも重要なポイントです。検索機能が充実しているか、図や動画を活用した説明があるかなども確認しましょう。
実際に操作する担当者の意見を重視
システム選定の際には、経営層や情報システム部門だけでなく、実際に日々その原価管理システムを操作することになる経理部門や製造現場の担当者の意見を必ず聞くようにしましょう。彼らが「これなら使えそうだ」「分かりやすい」と感じるかどうかが、システム定着の鍵を握ります。可能であれば、選定プロセスに現場担当者にも参加してもらい、一緒にデモンストレーションを受けたり、トライアルを試したりすることが理想的です。
私が以前、ある中小製造業T社様のシステム選定に関わった際、経営陣は多機能で先進的なAシステムに魅力を感じていました。しかし、現場の経理担当者数名にAシステムのデモを見てもらったところ、「画面の文字が小さくて見づらい」「操作が複雑で覚えるのが大変そうだ」という意見が多数出ました。一方で、機能はAシステムほど多くはないものの、画面がシンプルで操作が直感的なBシステムについては、現場担当者から「これならすぐに使えそう」と好意的な反応が得られました。最終的にT社様はBシステムを採用し、現場へのスムーズな導入と定着に成功しました。この事例は、操作性の確認と現場の意見聴取の重要性を物語っています。
画面サンプルやカタログだけでは分からない操作性は、ベンダーに依頼して実際のシステムを操作させてもらう「ハンズオンデモ」や、一定期間無料で試用できる「トライアルアカウント」などを積極的に活用して、徹底的に確認するようにしましょう。
6.5.ポイント5:提供メーカー・ベンダーのサポート体制と実績
原価管理システムは、導入して終わりではなく、その後長期間にわたって安定的に活用していくものです。そのため、システムを提供するメーカーや販売ベンダーのサポート体制が充実しているか、そしてその企業が原価管理システム分野において十分な実績と信頼性を持っているかは、システム選定における非常に重要なポイントとなります。特に、専門のIT担当者が少ない中小企業にとっては、いざという時に頼れるベンダーの存在は心強い味方となるでしょう。
結論として、システム導入後の問い合わせ対応、トラブルシューティング、法改正やOSアップデートへの対応、そして継続的な情報提供など、ベンダーのサポート体制の質と、業界における導入実績や専門知識の豊富さが、長期的なシステム活用の安心感と効果の持続性を左右します。
サポート体制を確認する際の主なポイントは以下の通りです。
問い合わせ窓口と対応時間・方法
システム操作に関する疑問点や、万が一トラブルが発生した場合の問い合わせ窓口(電話、メール、専用ウェブサイトなど)が明確か、対応時間は自社の業務時間と合っているか、問い合わせに対する回答の迅速さや的確さはどうか、といった点を確認します。2025年現在では、チャットボットによる24時間対応や、FAQサイトの充実度もポイントになります。
サポートの範囲と内容
基本的な操作方法の案内だけでなく、システムの設定変更に関するアドバイス、データ移行の支援、トラブル発生時の原因調査と復旧支援、法改正(例えば消費税率の変更など)に伴うシステム改修への対応など、どの範囲までサポートが提供されるのかを具体的に確認しましょう。保守契約の内容もしっかりと目を通す必要があります。
導入支援と教育プログラムの充実度
システムの導入フェーズにおけるベンダーの支援体制(専任の導入コンサルタントの有無、導入スケジュールの策定支援、データ移行サポートなど)が手厚いか、また、システムをスムーズに使いこなせるようになるためのユーザー向け教育プログラム(集合研修、オンライン研修、eラーニングなど)が用意されているかも重要です。
バージョンアップと情報提供
システムの機能改善やセキュリティ強化のためのバージョンアップが定期的に提供されるか、その内容や適用方法に関する情報が適切に提供されるかを確認します。また、原価管理に関する最新のトレンドや法改正情報、他社の活用事例などをセミナーやニュースレターといった形で積極的に提供してくれるベンダーであれば、より心強いでしょう。
次に、ベンダーの実績と信頼性を確認するポイントです。
原価管理システム分野での導入実績
検討している原価管理システムが、自社と同業種・同規模の企業にどれだけ導入されているか、具体的な導入事例(お客様の声やケーススタディ)が公開されているかを確認します。多くの導入実績があるということは、それだけ多くの企業のニーズに応えてきた証であり、システムの信頼性やベンダーのノウハウの蓄積が期待できます。
業種特化の専門知識
特に製造業や建設業など、業種特有の原価管理ニーズがある場合は、その業種に対する深い理解と専門知識、そして豊富な導入経験を持つベンダーを選ぶことが望ましいです。業種特有の課題解決に強みを持つベンダーであれば、より的確なアドバイスやサポートが期待できます。
企業の経営安定性と将来性
原価管理システムは長期的に利用するものであるため、提供ベンダーの経営が安定しており、将来にわたって継続的に事業を続けていけるかどうかも間接的なポイントとなります。上場企業であるか、長年の実績があるか、業界での評判はどうか、といった点も参考にするとよいでしょう。
私が以前、ある機械メーカーU社様のシステム選定をお手伝いした際、機能的にはほぼ同等で価格も近い二つの原価管理システムで悩んでいました。最終的な決め手となったのは、片方のベンダーがU社様と同業種の導入事例を多数持ち、導入後のユーザーコミュニティも活発で、定期的な勉強会や情報交換の場を提供していた点でした。U社様は、「システムを導入するだけでなく、その後の活用まで含めて長期的に付き合えるベンダーだ」と判断し、そのシステムを採用。結果として、導入後も手厚いサポートと有益な情報提供を受けながら、原価管理レベルを継続的に向上させています。
ベンダーのサポート体制や実績は、システムのカタログだけでは分からない部分も多いため、既存ユーザーの評判を調べたり、ベンダーの担当者と直接面談してじっくりと話を聞いたりすることが重要です。
6.6.ポイント6:費用対効果と価格相場(初期費用・月額料金)の比較検討
原価管理システムの導入は、企業にとって少なからぬ投資となります。したがって、その投資に見合うだけの効果(費用対効果、ROI:Return on Investment)が得られるかどうかを慎重に検討することが不可欠です。また、システムの価格は、提供形態(クラウド/オンプレミス)、機能、ユーザー数、カスタマイズの有無などによって大きく変動するため、複数のシステムを比較し、おおよその価格相場を把握した上で、自社の予算内で最適な選択をすることが重要なポイントとなります。
結論として、導入によって得られる業務効率化、コスト削減、利益向上などの具体的な効果を金額換算で見積もり、それとシステム導入・運用にかかる総コストを比較して、投資回収期間や収益性を評価することが、賢明なシステム選定の基本です。
費用対効果を検討する際のステップは以下の通りです。
導入効果の具体的な見積もり
ポイント1で明確にした「導入目的」と、ポイント3で見極めた「必要な機能」をもとに、原価管理システム導入によって期待できる具体的な効果を、可能な範囲で金額換算してみます。
o 業務効率化による人件費削減効果
・ 例:原価計算業務時間が月間100時間から40時間に短縮(削減60時間)。担当者の平均時給が3,000円の場合、月間18万円、年間216万円のコスト削減。
o データ入力ミス削減による手戻りコスト削減効果
・ 例:従来、入力ミスによる修正作業に月間10時間かかっていたものがほぼゼロに。月間3万円、年間36万円のコスト削減。
o 正確な原価把握による不採算製品の改善・撤退効果
・ 例:赤字と判明した製品Aの年間損失額が500万円。対策により損失が200万円に圧縮できた場合、年間300万円の利益改善。
o 適正な価格設定による利益率向上効果
・ 例:原価情報に基づいた適切な価格設定により、全体の利益率が0.5%向上。年間売上が5億円の場合、年間250万円の利益増。 これらの効果を積み上げて、年間の総メリット額を算出します。
システム導入・運用にかかる総コストの把握: 原価管理システムの導入には、初期費用とランニングコストの双方が発生します。
o 初期費用
・ ソフトウェアライセンス料(オンプレミス型パッケージの場合)
・ サーバー・ネットワーク機器購入費(オンプレミス型の場合)
・ システム構築・設定費用、カスタマイズ費用
・ データ移行費用
・ 導入支援コンサルティング費用
・ 社員教育研修費用
o ランニングコスト(年間)
・ クラウドサービス利用料(月額または年額)
・ 保守サポート費用(オンプレミス型の場合)
・ サーバー維持費、電気代(オンプレミス型の場合)
・ 追加のカスタマイズや機能拡張費用(発生時)
・ IT担当者の人件費(一部) これらのコストを合計し、例えば5年間の総コスト(TCO:Total Cost of Ownership)を算出します。
費用対効果(ROI)の評価
算出した「年間の総メリット額」と「5年間の総コスト」を比較し、投資がどの程度の期間で回収できるか(投資回収期間)、そして投資に対してどれだけの利益が見込めるか(ROI)を評価します。
ROIは「(累計利益額 - 投資額)÷ 投資額 × 100 (%)」で計算できます。
この評価はあくまで試算であり、全ての効果を正確に金額換算することは難しいですが、客観的な判断材料として非常に有効です。
次に、価格相場の比較検討についてです。
複数のベンダーから見積もりを取得
必ず2~3社以上のベンダーから、自社の要件に基づいた正式な見積もりを取得しましょう。これにより、おおよその価格相場を把握できます。
見積もり内容の詳細な確認
提示された見積もりに、何が含まれていて何が含まれていないのか(例えば、保守内容、バージョンアップ費用、サポート範囲など)を詳細に確認します。単純な総額だけでなく、内訳を比較することが重要です。
クラウド型とオンプレミス型のコスト構造の違いを理解
クラウド型は初期費用が安いが月額費用が継続する、オンプレミス型は初期費用が高いが月額費用は抑えられる(ただしサーバー維持費などは別途)、といったコスト構造の違いを理解し、長期的な視点で総コストを比較します。
価格交渉の可能性
提示された見積もりに対して、機能の絞り込みや契約期間の調整などにより、ある程度の価格交渉が可能な場合もあります。ただし、過度な値引き要求は、その後のサポート品質の低下などに繋がる可能性もあるため注意が必要です。
私が以前、ある中小製造業V社様の原価管理システム選定をご支援した際、V社様は当初、機能の豊富さから高価格帯のAシステムに惹かれていました。しかし、詳細な費用対効果分析を行ったところ、V社様の規模や業務内容では、Aシステムの多くの機能が過剰であり、投資回収に10年以上かかる試算となりました。そこで、必要な機能を絞り込み、中価格帯で実績のあるBシステムと、低価格帯のクラウド型Cシステムを改めて比較検討。最終的に、Cシステムでも主要な導入目的は達成可能で、かつ3年程度で投資回収できる見込みが立ったため、Cシステムを採用し、結果として身の丈に合ったシステム導入で着実な効果を上げています。
費用対効果の検討と価格相場の比較は、経営資源が限られる中小企業にとっては特に重要なプロセスです。目先の価格だけでなく、長期的な視点と客観的なデータに基づいて、賢明な投資判断を行うようにしましょう。
6.7.ポイント7:将来的な拡張性・柔軟性(システム連携、機能追加)
原価管理システムを導入する際には、現在のニーズを満たすことだけでなく、将来的な企業の成長や事業環境の変化にも柔軟に対応できるか、という「拡張性」と「柔軟性」の視点も忘れてはなりません。企業は生き物であり、数年後には事業規模が拡大したり、新しい製品ラインナップが増えたり、組織体制が変更されたり、あるいは他の新しいITシステムを導入したりする可能性は十分にあります。2025年現在、市場の変化はますます速くなっており、この将来対応力はシステム選定において非常に重要なポイントとなります。
結論として、現在の要件だけでなく、数年先の事業展開や業務変化を見据え、ユーザー数やデータ量の増加、機能追加、他システムとの連携拡張などに柔軟に対応できる拡張性と柔軟性を備えた原価管理システムを選ぶことが、長期的な投資価値を最大化します。
将来的な拡張性と柔軟性を確認する際の主なポイントは以下の通りです。
ユーザー数・データ量の増加への対応
企業の成長に伴い、原価管理システムを利用するユーザー数が増加したり、取り扱うデータ量(製品マスター数、トランザクションデータなど)が増大したりすることが予想されます。システムが、これらの増加に対してスムーズにスケールアップできるか(特にクラウド型の場合はプラン変更の容易さ、オンプレミス型の場合はサーバー増強のしやすさなど)を確認しておきましょう。パフォーマンスの低下を招かないかどうかも重要です。
機能追加・カスタマイズの可能性
現在は必要なくても、将来的に新しい原価計算方法を採用したり、より高度な分析機能が欲しくなったり、特定の帳票を追加したくなったりするかもしれません。システムが、後からオプション機能を追加できるか、あるいはある程度のカスタマイズが可能な設計になっているか(例えば、ユーザー定義項目の追加、レポートレイアウトの変更など)を確認しておくと、将来のニーズ変化にも柔軟に対応できます。
他システムとの連携拡張性
現在連携を予定しているシステムだけでなく、将来的に導入する可能性のある他の業務システム(例えば、BIツール、SFA/CRM、SCMシステムなど)ともスムーズに連携できるか、標準的なAPI(Application
Programming Interface)が提供されているか、あるいはデータエクスポート/インポート機能が充実しているかなどを確認します。システム間のデータ連携は、企業全体の業務効率化と情報活用の鍵となります。
業種・業態の変化への対応力
M&A(合併・買収)や新規事業への進出などにより、企業の業種や業態が変化する可能性も考慮に入れる必要があります。原価管理システムが、異なる業種の原価計算ロジックにもある程度対応できる柔軟性を持っているか、あるいは複数会社対応機能などを備えていると、そのような変化にも対応しやすくなります。
技術的な陳腐化リスクの低減
IT技術の進歩は非常に速いため、導入したシステムが数年で技術的に陳腐化してしまうリスクも考慮しなければなりません。ベンダーが、システムの基盤技術(OS、データベースなど)のアップデートに継続的に対応しているか、新しい技術トレンド(AI、IoTなど)を将来的に取り込む計画があるかなども、長期的な視点では重要なポイントです。特にクラウド型システムは、ベンダー側でこのような技術追従が期待できるというメリットがあります。
ある成長著しい中小製造業W社様は、5年前に導入した原価管理システムが、現在の事業規模や取り扱い製品数の増加に追いつけなくなり、処理速度の低下や機能不足が深刻な問題となっていました。システム導入時には、そこまでの急成長を予測していなかったため、拡張性の低いシステムを選んでしまったことが原因でした。結局、W社様は多大なコストと時間をかけてシステムの再構築を余儀なくされました。この事例は、将来的な拡張性を軽視したシステム選定のリスクを如実に示しています。
もちろん、将来の全てを正確に予測することは不可能ですが、「現状維持」を前提とするのではなく、ある程度の事業成長や変化を織り込んでシステムの拡張性・柔軟性を評価することが、長期にわたって「使える」原価管理システムを選ぶための賢明なアプローチと言えるでしょう。ベンダーに対して、将来的なロードマップや技術戦略について質問してみるのも有効な手段です。
7.【タイプ・業種別】注目すべき原価管理システム -比較表紹介
これまでの章で、原価管理システムの基本的な知識、導入メリット・デメリット、主要機能、そして失敗しない選び方のポイントについて詳しく解説してきました。この章では、いよいよ具体的にどのような原価管理システムが市場に存在するのか、そのタイプ別・業種別の代表的な特徴や傾向、そしてどのような企業にどのようなシステムが適しているのかを、2025年現在の情報をもとに比較のポイントを紹介していきます。ここで紹介するのはあくまで一部の例や傾向であり、全ての項目を網羅するものではありませんが、皆様が自社に最適な原価管理システムを探す上での重要な羅針盤となるはずです。特定の製品を推奨するものではなく、あくまで中立的な立場から、それぞれのシステムが持つ一般的な強みや機能、そして比較検討する際の視点を提供することを目的とします。
7.1.おすすめシステムの比較表(タイプ、対象業種、主要機能、価格帯の目安)
原価管理システムを比較検討する際には、いくつかの重要な観点から各製品を整理し、自社のニーズと照らし合わせることが効果的です。具体的な製品名を挙げて詳細な比較表をここで提示することは、市場の変化の速さや個々の製品のアップデート頻度を考えると現実的ではありません。しかし、皆様がご自身で情報を収集し、比較検討を行う際に役立つ「比較のフレームワーク(観点)」をここで提示します。このフレームワークを参考に、検討候補となるシステムの情報を整理してみてください。
結論として、原価管理システムを比較する際は、提供タイプ、得意とする業種、主要機能の充足度、価格帯、そしてサポート体制といった複数の軸で情報を整理し、自社の優先順位と照らし合わせながら総合的に評価することが重要です。
原価管理システム比較検討時の主要な観点(フレームワーク例):
提供タイプ:
o クラウド型(SaaS)
初期費用、運用負荷、導入スピード、場所を選ばないアクセス性などを重視する場合。
o オンプレミス型
カスタマイズの柔軟性、セキュリティの自社管理、既存オンプレミスシステムとの親和性などを重視する場合。
o ERP一体型
全社的な情報統合、会計・販売・生産などの基幹業務とのシームレスな連携を最優先する場合。
o 専用特化型
原価管理機能の専門性、特定の業種や業務への深い適合性を求める場合。
得意とする対象業種:
o 製造業全般
部品表(BOM)管理、工程別原価計算、標準原価計算と差異分析などの機能が充実しているか。
o 組立製造業
複雑なBOMや設計変更への対応力、ロット別管理など。
o プロセス製造業(装置産業)
連産品・副産物の原価計算、バッチ管理、材料配合管理など。
o 建設業
工事原価管理(実行予算、工事台帳)、進捗度管理、外注管理などの機能が充実しているか。
o IT・ソフトウェア開発業(プロジェクト型ビジネス)
プロジェクト別原価計算、工数管理、要員別単価設定、採算分析など。
o その他サービス業
案件別原価計算、サービスごとの収益性分析など。
主要機能の充足度:
o 原価計算方法
実際原価、標準原価、直接原価など、自社が採用したい計算方法に対応しているか。
o 配賦機能
間接費の配賦基準を柔軟に設定できるか。多段階配賦やABC(活動基準原価計算)への対応はどうか。
o 分析・レポート機能
製品別損益分析、差異分析、シミュレーション機能などが充実しているか。レポートのカスタマイズ性はどうか。
o 他システム連携
既存の会計、販売、生産管理システムなどとスムーズに連携できるか。API連携やCSV連携の方法。
o マスタ管理
品目マスター、BOM、工程マスターなどの管理機能の使いやすさ。
o 予算管理
実行予算の作成、予実管理、差異分析のしやすさ。
価格帯の目安:
o 初期費用
ライセンス料、構築費用、カスタマイズ費用、導入支援費用など。
o 月額(年額)料金
クラウドサービス利用料、保守サポート費用など。
o ユーザー数に応じた価格体系
利用ユーザー数が増えた場合の費用変動。
o オプション機能の価格
追加機能を導入する場合の費用。 (具体的な価格はベンダーへの問い合わせが必須ですが、おおよそのターゲット価格帯を把握しておくことは重要です。)
導入実績とサポート体制:
o 同業種・同規模企業への導入実績は豊富か。事例を確認できるか。
o 導入支援の内容と手厚さ。
o 問い合わせ窓口、対応時間、保守内容などのサポート体制。
o ベンダーの専門知識や信頼性。
これらの観点を表形式にまとめ、検討候補の原価管理システムを横並びで比較することで、それぞれのシステムの強み・弱みが明確になり、自社の優先順位に照らし合わせて客観的な評価がしやすくなります。2025年現在では、多くのベンダーがウェブサイト上で製品情報を公開しており、資料ダウンロードやオンラインデモの申し込みも容易に行えるため、積極的に情報収集を行いましょう。
8. 原価管理システム導入のプロセスと成功のポイント
原価管理システムの選定が完了し、いよいよ導入フェーズへと進む際、多くの方が「何から手をつければ良いのか」「スムーズに導入を進めるためにはどうすれば良いのか」といった不安を抱かれることでしょう。原価管理システムの導入は、単に新しいソフトウェアをインストールするだけの作業ではありません。現状の業務プロセスの見直し、関係各部署との連携、社員への教育、そして新しいシステムを組織に定着させるための地道な努力が伴う、一大プロジェクトです。この章では、原価管理システムを導入決定してから実際に本稼働させ、その効果を最大限に引き出すための一般的な実施プロセスとスケジュール感、そしてプロジェクトを成功に導くための重要なポイントや注意点について、私たちコンサルタントの経験を交えながら具体的に解説していきます。
8.1.導入決定から本稼働までの一般的な実施プロセスとスケジュール
原価管理システムの導入プロジェクトは、一般的にいくつかのフェーズに分けて進められます。各フェーズの目的と主な作業内容を理解し、計画的に取り組むことが、スムーズな導入と期待される効果の実現に不可欠です。以下に、導入決定から本稼働までの一般的な実施プロセスと、それぞれの期間の目安(中小企業がパッケージ型やクラウド型の原価管理システムを導入する場合を想定)を示します。ただし、これはあくまで一例であり、企業規模や選択するシステムの種類、カスタマイズの度合いなどによって、実際のプロセスやスケジュールは大きく変動することをご理解ください。
結論として、原価管理システムの導入プロセスは、周到な計画と準備から始まり、要件定義、設計、開発・設定、テスト、データ移行、教育・研修を経て本稼働に至る一連のステップであり、各フェーズでの目標達成と関係者の協力が成功の鍵となります。
一般的な導入プロセスと期間の目安:
計画・準備フェーズ(約1~2ヶ月):
o 目的: システム導入プロジェクトの全体像を明確にし、推進体制を構築する。
o 主な作業内容:
・ プロジェクトチームの発足(経営層、情報システム部門、経理部門、製造部門などからメンバーを選出)。プロジェクトマネージャーの任命。
・ 導入目的の再確認と共有、具体的な目標値(KPI)の設定。
・ システムベンダーとの契約締結、役割分担の明確化。
・ 詳細な導入スケジュールの策定と、各フェーズの成果物の定義。
・ リスクの洗い出しと対応策の検討。
・ 社内へのプロジェクト開始の告知と協力体制の依頼。
o 成果物:
プロジェクト計画書、推進体制図、詳細スケジュール、RFP(提案依頼書)とベンダー選定結果(選定フェーズがここに含まれる場合もある)など。
このフェーズでのしっかりとした計画と準備が、プロジェクト全体の成否を左右すると言っても過言ではありません。
要件定義フェーズ(約1~3ヶ月):
o 目的: 新しい原価管理システムで実現したい業務要件や機能要件を具体的に定義し、システムの仕様を明確にする。
o 主な作業内容:
・ 現状の業務プロセスの詳細な分析(As-Isモデルの作成)。
・ 新しい原価管理システムを導入した後の理想的な業務プロセス(To-Beモデル)の設計。
・ システムに求める機能要件(原価計算方法、配賦ロジック、必要な帳票、他システムとの連携要件など)の洗い出しと具体化。
・ 非機能要件(セキュリティ、パフォーマンス、操作性など)の定義。
o 成果物:
要件定義書、業務フロー図(As-Is, To-Be)、機能一覧、データ移行計画など。
このフェーズでは、システムベンダーやコンサルタントと密にコミュニケーションを取りながら、自社の要求を正確に伝えることが重要です。曖昧な要件定義は、後の設計・開発フェーズでの認識のズレや手戻りの原因となります。
設計フェーズ(約1~2ヶ月):
o 目的: 要件定義書に基づいて、原価管理システムの具体的な設計を行う。
o 主な作業内容:
・ システムの基本設計(システム構成、画面設計、帳票設計、データベース設計、連携インターフェース設計など)。
・ システムの詳細設計(プログラムロジック、データ項目定義など)。
・ カスタマイズやアドオン開発が必要な場合は、その仕様設計。
o 成果物:
基本設計書、詳細設計書、カスタマイズ仕様書など。
設計書は、開発・設定作業の基盤となるため、内容に漏れや誤りがないか、関係者間で十分にレビューを行う必要があります。
開発・設定フェーズ(約1~4ヶ月、カスタマイズ規模による):
o 目的: 設計書に基づいて、原価管理システムの構築、プログラミング、設定作業を行う。
o 主な作業内容:
・ クラウド型システムの場合は、ベンダーによる環境準備とパラメータ設定。
・ オンプレミス型システムの場合は、サーバー構築、ソフトウェアインストール、パラメータ設定。
・ カスタマイズやアドオン開発が必要な場合は、プログラミングと単体テスト。
・ 他システムとの連携機能の開発・設定。
o 成果物:
構築されたシステム環境、開発されたプログラム、設定パラメータ一覧など。
このフェーズでは、ベンダーとの進捗確認や課題共有を定期的に行うことが重要です。
テストフェーズ(約1~2ヶ月):
o 目的: 開発・設定された原価管理システムが、要件定義通りに正しく動作するかを検証する。
o 主な作業内容:
・ 単体テスト(個々の機能が正しく動作するか)。
・ 結合テスト(複数の機能や他システムとの連携が正しく動作するか)。
・ 総合テスト(実際の業務シナリオに沿って、システム全体が問題なく動作するか)。
・ 受け入れテスト(ユーザー部門の担当者が実際に操作し、要件を満たしているか最終確認)。
・ テストで発見された不具合の修正と再テスト。
o 成果物:
テスト計画書、テスト仕様書、テスト結果報告書、不具合管理表など。
テストフェーズは、システムの品質を確保する上で非常に重要です。特にユーザー部門を巻き込んだ受け入れテストは、本稼働後の手戻りを防ぐために不可欠です。
データ移行フェーズ(テストフェーズと並行または直前):
o 目的: 既存のシステムやExcelファイルなどから、新しい原価管理システムへ必要なデータ(品目マスター、BOM、仕入先マスター、期首残高など)を移行する。
o 主な作業内容:
・ 移行対象データの特定と抽出。
・ データクレンジング(誤りや重複の修正)。
・ 移行プログラムの開発または手作業によるデータ入力。
・ 移行データの正当性検証。
o 成果物:
データ移行計画書、移行データ、検証結果報告書など。
データ移行は、地味ながらもシステムの精度を左右する重要な作業です。移行対象データの量や品質によっては、多大な時間と労力を要することもあります。
教育・研修フェーズ(テストフェーズと並行または直前):
o 目的:原価管理システムを利用する社員が、スムーズに操作できるようになるための教育・研修を実施する。
o 主な作業内容:
・ 研修対象者(エンドユーザー、管理者など)の特定。
・ 研修テキストやマニュアルの作成。
・ 集合研修、OJT(On-the-Job Training)、eラーニングなどの実施。
・ 理解度テストや質疑応答。
o 成果物:
研修資料、マニュアル、研修実施報告書など。
十分な教育・研修は、システムの早期定着と活用促進に不可欠です。
本稼働・運用開始フェーズ:
o 目的:全ての準備を終え、新しい原価管理システムを実際の業務で利用開始する。
o 主な作業内容:
・ 本稼働日時の決定と関係者への周知。
・ 本稼働直後のサポート体制の確立(ベンダー待機、社内ヘルプデスクなど)。
・ 旧システムからの切り替え作業(必要な場合)。
・ 本稼働後の運用ルールの徹底。
o 成果物:
本稼働宣言、運用マニュアル(改訂版)など。
本稼働直後は、予期せぬトラブルや問い合わせが集中することもあるため、迅速に対応できる体制を整えておくことが重要です。
運用・保守・評価フェーズ(本稼働後継続):
o 目的:システムの安定稼働を維持し、導入効果を評価・測定し、継続的な改善を行う。
o 主な作業内容:
・ 定期的なシステムメンテナンス、バックアップ。
・ 問い合わせ対応、トラブルシューティング。
・ データの整合性チェック。
・ システムの利用状況のモニタリング。
・ 導入効果(KPIの達成度など)の測定と評価。
・ 業務改善提案、システム改修の検討(必要な場合)。
o 成果物:
運用報告書、効果測定レポート、改善提案書など。
原価管理システムは導入して終わりではありません。継続的に活用し、効果を最大化するための取り組みが求められます。
8.2.プロジェクト体制の構築と社内準備(データ整理、業務フロー見直し)
原価管理システムの導入プロジェクトを成功させるためには、技術的な側面だけでなく、組織的な準備、特に「しっかりとしたプロジェクト体制の構築」と「事前の社内準備」が極めて重要です。これらが不十分だと、プロジェクトが迷走したり、現場の協力が得られなかったり、導入後のシステムが定着しなかったりするリスクが高まります。
結論として、経営層の強力なリーダーシップのもと、各関連部門の代表者を含む実効性の高いプロジェクトチームを組成し、導入前に既存データの整理や業務フローの見直しといった社内準備を徹底することが、スムーズなシステム導入と効果の最大化に不可欠です。
プロジェクト体制の構築におけるポイント:
経営層のコミットメントとプロジェクトオーナーの明確化
原価管理システムの導入は、単なる一部門の業務改善ではなく、全社的な経営課題に直結する取り組みです。そのため、経営トップがこのプロジェクトの重要性を強く認識し、積極的に関与・支援する姿勢(トップコミットメント)を示すことが不可欠です。また、プロジェクト全体の最終責任者である「プロジェクトオーナー」を経営層から任命し、強力なリーダーシップを発揮してもらうことが重要です。
部門横断的なプロジェクトチームの編成
原価管理は、経理部門だけでなく、製造部門、販売部門、購買部門、情報システム部門など、多くの部門が関わります。各部門から、業務に精通し、リーダーシップを発揮できるキーパーソンをプロジェクトメンバーとして選出し、部門横断的なチームを編成することが重要です。これにより、各部門のニーズや意見を的確に吸い上げ、全社的な視点での意思決定が可能になります。ある中小企業では、プロジェクトチームを経理部門のメンバーだけで構成したため、製造現場の特殊な業務フローが十分に考慮されず、導入後に現場から「使いにくい」という不満が噴出したことがあります。
プロジェクトマネージャーの任命と役割明確化
プロジェクト全体の進捗管理、課題管理、関係者間の調整、ベンダーとのコミュニケーションなどを担う「プロジェクトマネージャー」を任命し、その役割と責任を明確にします。プロジェクトマネージャーには、システムの知識だけでなく、コミュニケーション能力や問題解決能力、リーダーシップが求められます。社内に適任者がいない場合は、外部のコンサルタントに支援を依頼することも検討しましょう。
定期的な会議体と報告体制の確立
プロジェクトチームの定例会議、経営層への進捗報告会など、定期的な会議体を設け、情報共有と意思決定をスムーズに行う体制を整えます。議事録をきちんと作成し、決定事項や課題を明確にすることも重要です。
事前の社内準備におけるポイント:
既存データの整理・クレンジング
新しい原価管理システムに移行する既存のマスターデータ(品目マスター、部品表、顧客マスター、仕入先マスターなど)や取引データに、誤りや重複、欠損などがないか事前に徹底的にチェックし、整理・清掃(クレンジング)しておく必要があります。不正確なデータをそのまま新しいシステムに移行してしまうと、システムの信頼性が損なわれ、期待した効果が得られません。「ゴミを入れればゴミしか出てこない(Garbage
In, Garbage Out)」という言葉を肝に銘じましょう。
現行業務フローの見える化と課題の洗い出し
現在の原価管理に関わる業務フローを詳細に「見える化」し、どこに無駄や非効率、問題点があるのかを具体的に洗い出します。これは、新しいシステムに求める要件を明確にする上で非常に重要な作業です。
新しい業務フロー(To-Beモデル)の検討
原価管理システム導入を単なる現状業務のシステム化に終わらせるのではなく、これを機に、より効率的で付加価値の高い業務フローへと改善できないかを検討します(BPR:Business Process
Re-engineering)。システムの機能を最大限に活かせる業務フローを設計することが理想です。ただし、現場の現実とかけ離れた理想論にならないよう注意も必要です。
社内への周知と意識改革
なぜ原価管理システムを導入するのか、それによって社員や会社にどのようなメリットがあるのか、導入によって何が変わるのか、といったことを、経営トップから社員一人ひとりに対して丁寧に説明し、理解と協力を求めることが不可欠です。「やらされ感」ではなく、主体的にプロジェクトに関わってもらうための意識改革を促します。
これらの体制構築と社内準備をしっかりと行うことが、原価管理システム導入という航海を成功に導くための羅針盤と頑丈な船体を用意することに他なりません。
8.3.システム導入を成功に導くための注意点と手法
原価管理システムの導入プロジェクトは、企業にとって大きな投資であり、その成否は将来の経営に大きな影響を与えます。技術的な側面だけでなく、組織的・人的な側面も含めた多角的な視点から、プロジェクトを成功に導くための注意点と有効な手法を理解し、実践することが求められます。ここでは、私たちコンサルタントが多くの導入事例を通じて得た教訓をもとに、特に重要と考えられるいくつかのポイントを解説します。
結論として、原価管理システム導入の成功は、経営層の強いリーダーシップ、現場ユーザーの積極的な参画、明確な目標設定と共有、段階的な導入アプローチ、そしてシステムベンダーとの良好なパートナーシップ構築にかかっています。
経営トップの強力なリーダーシップと継続的なコミットメント
前述のプロジェクト体制構築でも触れましたが、原価管理システムの導入は全社的な取り組みであるため、経営トップが「このプロジェクトを必ず成功させる」という強い意志を持ち、リーダーシップを発揮し続けることが最も重要です。プロジェクトの節目節目で進捗を確認し、課題があれば迅速に意思決定を行う、予算やリソースの確保に責任を持つ、社内へのメッセージ発信を積極的に行うなど、経営トップの継続的な関与がプロジェクトの推進力となります。
現場ユーザーの早期からの巻き込みと参画意識の醸成
実際にシステムを使うのは現場のユーザーです。彼らの意見やニーズを無視してシステム導入を進めても、結局は使われない「お飾りのシステム」になってしまいます。要件定義の初期段階から現場のキーパーソンをプロジェクトチームに加え、彼らの業務知識や課題意識をシステム設計に反映させることが不可欠です。また、デモンストレーションやテストにも積極的に参加してもらい、「自分たちが使うシステムを自分たちで良くしていく」という当事者意識(オーナーシップ)を醸成することが、導入後のスムーズな定着に繋がります。
明確で共有された導入目的とゴール設定
「なぜこのシステムを導入するのか」「導入後にどのような状態を目指すのか」という目的とゴールが、経営層から現場の担当者まで、プロジェクトに関わる全てのメンバー間で明確に共有されていることが重要です。目的が曖昧だったり、人によって解釈が異なったりすると、プロジェクトの方向性がぶれ、意思決定も遅れます。設定した目的やゴールは、プロジェクトの各フェーズで常に立ち返り、当初の目論見から外れていないかを確認するべきです。
スモールスタートと段階的な導入アプローチの検討
特に初めて本格的な原価管理システムを導入する中小企業や、業務範囲が広い企業の場合、最初から全ての機能を一度に稼働させようとすると、現場の混乱が大きくなったり、プロジェクトが複雑化しすぎてコントロールが難しくなったりするリスクがあります。そのような場合は、まず特定の部門や製品群、あるいは基本的な機能に絞ってシステムを導入し(スモールスタート)、その効果を検証しながら段階的に対象範囲や機能を拡張していくアプローチが有効です。これにより、リスクを低減し、成功体験を積み重ねながら着実にシステムを定着させることができます。
業務改革(BPR)を意識したシステム導入
原価管理システムの導入を、単に現在の業務をそのままシステムに置き換えるだけの「システム化」と捉えるのではなく、これを機に非効率な業務プロセスそのものを見直し、改善する「業務改革(BPR:Business Process Re-engineering)」の絶好の機会と捉えるべきです。システムの標準機能を最大限に活かせるように業務フローを再設計することで、システム導入の効果を飛躍的に高めることが可能になります。ただし、過度な業務変更は現場の抵抗を生む可能性もあるため、バランスが重要です。
システムベンダーとの良好なパートナーシップ構築
原価管理システムの導入は、システムベンダーや導入支援コンサルタントとの共同作業です。彼らを単なる「業者」として扱うのではなく、プロジェクト成功のための「パートナー」として捉え、オープンで建設的なコミュニケーションを心がけることが重要です。自社の課題や要望を正確に伝え、彼らの専門知識や経験を最大限に引き出し、協力して問題解決にあたる姿勢が求められます。契約内容や役割分担を明確にすることも、良好な関係を築く上で不可欠です。
導入後の効果測定と継続的な改善サイクルの確立
原価管理システムは導入して終わりではありません。本稼働後、定期的に導入前に設定したKPI(重要業績評価指標)の達成度を測定・評価し、期待した効果が出ているかを確認する必要があります。思うような効果が出ていない場合は、その原因を分析し、運用方法の改善や追加の教育、あるいはシステム設定の見直しなどを検討します。このようなPDCAサイクルを回し続けることで、システムの価値を継続的に高めていくことができます。
これらのポイントは、どれも当たり前のことのように聞こえるかもしれませんが、実際のプロジェクトでは疎かになりがちな点でもあります。私が過去に見てきたシステム導入の失敗事例の多くは、技術的な問題よりも、これらの組織的・人的な要因に起因するものでした。これらの注意点を常に念頭に置き、一つ一つ丁寧に取り組むことが、原価管理システム導入を成功に導く確実な道と言えるでしょう。
8.4.導入事例紹介:成功事例と失敗から学ぶポイント
これまでに原価管理システム導入のプロセスや成功のポイントを解説してきましたが、ここではより具体的に、実際の導入事例を通じて、どのような取り組みが成功に繋がり、どのような点が失敗の原因となり得るのかを見ていきましょう。架空の企業を想定したケーススタディ形式で、製造業と建設業それぞれの事例を紹介し、そこから得られる教訓を明らかにします。
8.4.1.製造業における導入事例(ケーススタディ)
【成功事例:株式会社A製作所(中小部品メーカー)】
導入前の課題
株式会社A製作所は、多品種少量生産の精密部品メーカーです。Excelによる原価計算を行っていましたが、製品ごとの正確な原価把握が難しく、特に新規受注品の見積もり精度が低いことが課題でした。また、月次の原価確定に時間がかかり、経営判断に必要な情報がタイムリーに得られない状況でした。材料費の変動も激しく、採算管理が後手に回りがちでした。
導入したシステムと選定理由
A製作所は、製造業向けの機能が充実し、特に部品表(BOM)管理と工程別原価計算に強みを持つクラウド型原価管理システムBを選定しました。
選定の決め手は、
①自社の複雑なBOM構造に柔軟に対応できること
②生産管理システム(既存)とのデータ連携が比較的容易であること
③クラウド型で初期費用を抑えられ、IT担当者が少ない同社でも運用しやすいこと
④ベンダーの製造業における導入実績が豊富で、サポート体制も手厚いこと
でした。
導入プロセスと工夫した点
社長自らがプロジェクトオーナーとなり、製造部長、経理課長、若手エース社員からなるプロジェクトチームを結成。導入目的を「正確な製品別実際原価のリアルタイム把握と、見積もり精度向上による利益率改善」と明確に設定し、全社員に共有しました。要件定義では、ベンダーと協力し、主要な製品群について詳細なBOMと工程フローを徹底的に洗い出し、システムへの設定に落とし込みました。データ移行では、既存のExcelデータのクレンジングに時間をかけ、精度を重視しました。本稼働前に、主要なユーザー部門で十分なテストと研修を実施し、操作への習熟度を高めました。
導入後の効果
システム導入後、A製作所では以下のような顕著な効果が現れました。
1. 製品別実際原価が、ほぼリアルタイムで正確に把握できるようになり、赤字受注が大幅に減少。
2. 見積もり作成時に、過去の類似製品の実際原価データを参考にすることで、見積もり精度が飛躍的に向上し、適正な利益を確保できるように。
3. 月次の原価確定作業が従来の約3分の1の時間で完了。経理担当者は分析業務により多くの時間を割けるように。
4. 材料費の変動が原価に与える影響をシミュレーション機能で事前に予測し、迅速な価格改定や代替材料の検討が可能に。
社長は「原価管理システムは、まさに当社の経営の羅針盤となった。データに基づいて自信を持って意思決定できるようになったことが最大の成果だ」と語っています。
成功のポイント(分析)
A製作所の成功要因は、
①経営トップの強いリーダーシップと明確な導入目的の共有
②自社の課題と業種特性に合ったシステム選定
③現場を巻き込んだ丁寧な要件定義と準備
④信頼できるベンダーとの良好なパートナーシップ構築
⑤導入後の継続的なデータ活用と改善意識
にあったと考えられます。
8.4.2.建設業における導入事例(ケーススタディ)
【失敗事例から学ぶ:株式会社X建設(地方中堅ゼネコン)】
導入前の課題
株式会社X建設は、公共工事と民間工事を半々で手がける地方の中堅ゼネコンです。工事ごとの実行予算と実績の管理がExcelベースであり、複数の担当者がそれぞれ異なるフォーマットで情報を管理していたため、全社的な工事損益の把握が遅れがちでした。特に、工事の進捗と原価発生のズレが問題で、気づいた時には大幅な予算超過となっている工事が散見されました。
導入したシステムと当時の状況
X建設は、数年前に当時最新とされた多機能なオンプレミス型の建設業向け原価管理システムYを、他社の成功事例に惹かれてやや拙速に導入を決定しました。経営陣は「システムを入れれば全て解決する」という期待感が先行していました。
導入プロセスと問題点
プロジェクトチームは経理部門中心で、現場監督の意見を十分に吸い上げる機会が少ないまま要件定義が進められました。システムベンダーからは「標準機能でほとんどの業務はカバーできる」との説明があり、自社の特殊な業務フローへの適合性検証が不十分なまま、カスタマイズを最小限に抑える方針となりました。データ移行では、各担当者が個別に管理していたExcelデータの品質にばらつきがあり、移行作業が難航。現場監督向けの研修も十分な時間が確保されず、システムの操作方法が浸透しませんでした。
導入後の状況と失敗要因
システム導入後、現場監督からは「操作が複雑で使いにくい」「日々の入力作業が逆に増えた」「Excelの方が早くて楽だった」といった不満が続出。入力されるデータの精度も低く、システムから出力されるレポートの信頼性が揺らぎました。結果として、多くの現場でシステムが十分に活用されず、依然としてExcelでの二重管理が続く状況に陥ってしまいました。期待したリアルタイムな原価把握や業務効率化は達成できず、高価な投資は塩漬けに近い状態となりました。
失敗から学ぶポイント(分析)
X建設の事例から学べる教訓は数多くあります。
1. 導入目的の曖昧さと過度な期待
「システムを入れれば何とかなる」という安易な考えではなく、具体的な課題解決目標を明確にすべきでした。
2. 現場ユーザーの軽視
システムを実際に使う現場の意見を十分に聞かず、トップダウンで導入を進めたことが最大の失敗要因の一つです。
3. 業務プロセスとシステムのミスマッチ
自社の業務フローとシステムの適合性検証が不十分で、システムに業務を合わせる努力も、システムを業務に合わせるカスタマイズも中途半端でした。
4. 不十分な教育・サポート体制
現場が新しいシステムを使いこなせるようになるまでの教育・研修、そして導入後の継続的なサポートが不足していました。
5. データ品質への意識の低さ
移行するデータの重要性と、その品質担保のための事前準備を軽視していました。
このX建設の事例は、原価管理システム導入が技術的な問題だけでなく、組織的・人的な要因によっても失敗し得ることを示しています。これらの成功事例と失敗事例から学び、自社の導入プロジェクトに活かしていくことが、失敗のリスクを最小限に抑え、効果を最大限に引き出すための賢明なアプローチと言えるでしょう。
9. まとめ:最適な原価管理システムを選び、企業の競争力を強化する
ここまで、原価管理システムの基本的な知識から、導入メリット・デメリット、主要機能、タイプ別の比較、失敗しない選び方のポイント、導入プロセスに至るまで、多岐にわたる情報を解説してまいりました。この記事を通じて、原価管理システムが、いかにして中小製造業の皆様の経営課題解決と競争力強化に貢献できるか、その可能性を感じていただけたのであれば幸いです。
厳しい経済環境が続き、市場の変化も激しい現代において、どんぶり勘定や旧態依然とした管理方法では、企業の持続的な成長は望めません。「正確な原価をタイムリーに把握し、それを経営に活かす」という原価管理の基本に立ち返り、それを強力に支援する原価管理システムの導入は、もはや一部の大企業だけのものではなく、成長を目指すすべての企業にとって重要な経営戦略の一つと言えるでしょう。
この最後の章では、原価管理システム導入を成功させ、その効果を最大限に引き出すための鍵となるポイントを改めて整理し、2025年以降の展望、そして皆様が次にとるべきアクションについてお伝えします。
9.1.原価管理システム導入成功の鍵と今後の展望(2025年以降)
原価管理システムの導入プロジェクトを成功に導き、その効果を継続的に享受するためには、いくつかの重要な「鍵」が存在します。これまでの章でも触れてきましたが、改めてここで集約して強調したいと思います。
原価管理システム導入成功の5つの鍵:
明確な目的意識と経営層の強力なリーダーシップ
「なぜ原価管理システムを導入するのか」「導入して何を達成したいのか」という目的を、経営層から現場の隅々まで明確に共有することが全ての出発点です。そして、経営トップがこの変革を力強く牽引し、必要なリソースを投入し、プロジェクトを全面的に支援する姿勢が不可欠です。
現場ユーザー主体のプロジェクト推進
実際にシステムを日々利用するのは現場の社員です。彼らの業務知識や課題意識をシステム選定や要件定義に積極的に反映させ、彼らが「自分たちのためのシステムだ」と主体的に関われるような体制を築くことが、導入後のスムーズな定着と活用に繋がります。
自社に最適なシステム選定と段階的な導入
「高機能=良いシステム」とは限りません。自社の規模、業種特性、業務内容、予算、そして将来の拡張性などを総合的に考慮し、過不足のない「ちょうど良い」原価管理システムを選ぶことが肝心です。また、いきなり大規模なシステムを全社展開するのではなく、スモールスタートで効果を検証しながら段階的に進めるアプローチも有効です。
業務プロセスの見直し(BPR)への意識
原価管理システム導入を、単に既存の業務をシステムに置き換えるだけでなく、非効率な業務プロセスそのものを見直し、改善する絶好の機会と捉えましょう。システムの標準機能を最大限に活かせるように業務を再構築することで、導入効果は飛躍的に高まります。
信頼できるベンダーとの良好なパートナーシップ
システムベンダーや導入支援コンサルタントは、プロジェクト成功のための重要なパートナーです。彼らの専門知識や経験を最大限に引き出し、密なコミュニケーションを取りながら、二人三脚でプロジェクトを進めていく姿勢が求められます。
これらの「鍵」を意識して取り組むことで、原価管理システム導入の成功確率は格段に高まるでしょう。
今後の展望(2025年以降):
2025年以降の原価管理は、さらに進化していくことが予想されます。
AI(人工知能)や機械学習の活用
原価予測の精度向上、異常値の自動検知、コスト削減機会の提案など、AI技術が原価管理の高度化に貢献する場面が増えてくるでしょう。
リアルタイム性の追求
IoTデバイスからのデータ収集や、クラウドベースのシステム連携により、よりリアルタイムに近い原価把握と迅速な意思決定が一般化していくと考えられます。
DX(デジタル・トランスフォーメーション)との連携深化
原価管理システムは、企業全体のDX推進における重要な構成要素として、販売、生産、購買、会計といった他の基幹システムやBIツールとよりシームレスに連携し、経営情報のハブとしての役割を強めていくでしょう。
サステナビリティ(持続可能性)への対応
環境負荷コスト(CO2排出量など)の見える化や、サプライチェーン全体での社会的責任に関わるコストの把握など、サステナビリティの観点を取り入れた原価管理のニーズも高まる可能性があります。
私たちコンサルタントとしても、こうした新しい技術動向や社会的な要請を常に注視し、お客様である中小製造業の皆様が時代の変化に的確に対応できるよう、最新の情報と最適なソリューションを提供し続けていく所存です。
9.2.自社にマッチするシステム選定のための最終チェックポイント
原価管理システムの選定は、多くの情報を収集し、比較検討を重ねる、骨の折れる作業です。最終的な意思決定を下す前に、もう一度立ち止まって、以下のチェックポイントを確認してみましょう。これらの問いに自信を持って「Yes」と答えられるかどうかが、自社に真にマッチした原価管理システムを選ぶための最終関門となります。
【システム選定・最終チェックポイント】
目的適合性チェック:
□ 導入目的は明確であり、その目的を達成するために、この原価管理システムの機能は十分かつ適切か?
□ システム導入によって、現状の最も大きな課題(例えば、原価計算の手間、精度の問題、情報のタイムリーさなど)は具体的にどのように解決される見込みがあるか?
機能適合性チェック:
□ 自社の業種(製造業、建設業など)や生産形態(多品種少量、個別受注など)特有の原価計算や管理要件に、このシステムは十分対応できているか?
□ 部品表(BOM)管理、工程別原価計算、間接費の配賦ロジックなど、自社の原価計算のポイントとなる機能は満足できるレベルか?
□ 将来的な機能拡張やカスタマイズの柔軟性は確保されているか?
操作性・運用性チェック:
□ 実際にシステムを操作する現場の担当者が、直感的で分かりやすく、使いやすいと感じているか?(デモやトライアルでの評価)
□ 導入後の運用・保守体制(社内担当者、ベンダーサポート)は現実的に維持可能か?
□ マスターデータのメンテナンスや、日常のデータ入力作業は効率的に行えそうか?
連携性チェック:
□ 既存の会計システム、販売管理 システム、生産管理 システムなどとのデータ連携はスムーズに実現できそうか?そのための方法やコストは明確か?
費用対効果チェック:
□ 初期費用およびランニングコスト(月額費用、保守費用など)は、自社の予算規模に見合っているか?
□ 導入によって期待される効果(業務効率化、コスト削減、利益向上など)と投資コストを比較し、費用対効果は十分に期待できるか?投資回収期間の目安は?
ベンダー信頼性チェック:
□ システム提供ベンダーは、原価管理システム分野や自社業種において十分な導入実績と専門知識を持っているか?
□ 導入支援や導入後のサポート体制(問い合わせ対応、トラブル対応、バージョンアップなど)は信頼できる内容か?
□ ベンダーとのコミュニケーションは良好で、長期的なパートナーとして信頼できるか?
社内合意形成チェック:
□ 経営層から現場担当者まで、この原価管理システムを導入すること、そしてその目的や期待される効果について、社内での十分な理解と合意が得られているか?
□ システム導入に対する現場の協力体制は整っているか?
これらのチェックポイントを一つ一つ丁寧に確認し、全ての項目で納得のいく答えが得られれば、その原価管理システムは貴社にとって最適なパートナーとなる可能性が非常に高いと言えるでしょう。もし、いずれかの項目で不安が残るようであれば、再度情報収集やベンダーへの問い合わせ、社内での議論を重ねることをお勧めします。焦らず、慎重に、しかし着実に選定を進めてください。
9.3.関連サービス・ソリューションの紹介
原価管理システムは、それ単体でも大きな効果を発揮しますが、他の関連サービスやソリューションと組み合わせることで、その価値をさらに高めることが可能です。原価管理の高度化や、企業全体の業務効率化、DX推進を目指す上で、以下のような関連サービスの活用も視野に入れておくとよいでしょう。
BI(ビジネスインテリジェンス)ツール
原価管理システムに蓄積された膨大な原価データや実績データを、より視覚的に分かりやすく、多角的に分析するためのツールです。ダッシュボード機能やドリルダウン機能などを活用し、経営者や管理者が直感的に経営状況を把握し、迅速な意思決定を行うことを支援します。多くの原価管理システムが、主要なBIツールとの連携機能を備えています。
RPA(ロボティック・プロセス・オートメーション)
原価管理業務の中で、定型的で繰り返し発生するデータ入力や転記作業、レポート作成といった業務を、ソフトウェアロボットに代行させる技術です。原価管理システムへのデータ入力や、システムからのデータ抽出・加工といった作業をRPAで自動化することで、さらなる業務効率化と人的ミスの削減が期待できます。
生産スケジューラ・MES(製造実行システム)
特に製造業においては、生産計画の最適化を支援する生産スケジューラや、製造現場の進捗管理、実績収集をリアルタイムで行うMESとの連携が、より正確でタイムリーな実際原価の把握に不可欠です。これらのシステムからの情報が原価管理システムにスムーズに連携することで、原価管理の精度とスピードが向上します。
SFA(営業支援システム)/CRM(顧客関係管理システム)
顧客ごとの取引履歴や収益性を分析する上で、SFA/CRMに蓄積された営業活動情報や顧客情報と、原価管理システムの原価・利益情報を連携させることが有効です。どの顧客が最も利益に貢献しているのか、といった視点での分析が可能になります。
コンサルティングサービス
原価管理システムの導入は、単なるITツールの置き換えではなく、業務改革を伴うプロジェクトです。原価計算制度の設計、業務プロセスの見直し、導入目的の明確化、ベンダー選定支援、プロジェクト管理、導入後の定着化支援など、専門的な知識と経験を持つコンサルタントの支援を活用することで、プロジェクトの成功確率を高め、導入効果を最大化することができます。私たちのような中小製造業に特化したコンサルティング会社も、皆様の課題解決をお手伝いできます。
これらの関連サービスやソリューションは、必ずしも全ての企業に同時に必要なわけではありません。自社の課題や目指す姿に応じて、原価管理システムとの相乗効果が期待できるものを段階的に検討していくとよいでしょう。
「どの原価管理システムを選べば良いか分からない」「自社の課題に最適な解決策を見つけたい」といった場合には、私たちのような原価管理やシステム導入に詳しい専門コンサルタントにご相談いただくのも有効な手段です。客観的な立場から、貴社の状況に合わせた最適なアドバイスを提供できます。
原価管理システムの導入は、企業の未来を左右する重要な意思決定です。どうか、この記事で得た知識を活用し、積極的に情報収集を行い、比較検討を重ねて、貴社にとって真に最適な原価管理システムを見つけ出してください。そして、そのシステムを最大限に活用することで、原価管理レベルを飛躍的に向上させ、厳しい競争を勝ち抜くための強固な経営基盤を構築されることを心より願っております。
私たちも、多品種少量生産を行う中小製造業の皆様の力強いパートナーとして、これからも有益な情報発信と、きめ細やかなコンサルティングサービスを提供し続けてまいります。ご不明な点やご相談事項がございましたら、いつでもお気軽に船井総合研究所までお問い合わせください。
最後までお読みいただき、誠にありがとうございました。この記事が、貴社の原価管理の課題解決と、さらなる発展の一助となれば幸いです。 「製品ごとの正確なコストが分からない」
「Excelでの原価計算に限界を感じる」
「もっと戦略的な価格設定をしたい」…
多品種少量生産を行う中小製造業の皆様から、このような切実なお悩みを日々お伺いします。
原材料費の変動や競争激化が進む現代において、的確な原価管理は企業の生命線です。
しかし、従来の煩雑な手作業やExcelによる管理では、迅速かつ正確な原価把握が難しく、経営判断の遅れや利益機会の損失につながりかねません。
このような課題を解決し、競争力を高める強力なツールが「原価管理システム」です。原価管理システムの導入は、単に原価計算を効率化するだけでなく、企業の利益構造を見える化し、戦略的な経営判断を支援します。
この記事では、多品種少量生産に特化したコンサルティングで培った知見をもとに、「原価管理システム」の基礎知識から、導入のメリット・デメリット、主要機能、そして最も重要な「失敗しない選び方のポイント」まで、IT専門家の視点で徹底的に解説します。さらに、2025年現在の最新情報を踏まえ、おすすめの原価管理システムを比較紹介し、貴社に最適な一選びをサポートします。
この記事を読むことで、次のことが明確になります。
原価管理システムの基本的な仕組みと導入の必要性
Excel管理との違い、システム化による具体的なメリット
自社の課題や業種(特に製造業)に合った原価管理システムの選び方
主要な機能、タイプ別(クラウド、オンプレミス等)の特徴と比較ポイント
おすすめ原価管理システムの具体的な製品情報と導入事例
導入プロセスと成功のための注意点
原価管理に課題を感じ、業務改善や利益向上を目指すすべての中小製造業の経営者様、ご担当者様に、必ずお役立ちいただける情報をお届けします。早速、原価管理システムを詳しく見ていきましょう。
https://www.funaisoken.co.jp/dl-contents/smart-factory_smart-factory_00000153_S045?media=smart-factory_S045#_ga=2.136806070.705892685.1748526912-311123692.1748526911
1. はじめに:なぜ今、原価管理とシステム導入が重要なのか?
「この製品、本当に儲かっているのだろうか?」
「どうすればコストを抑え、もっと利益を出せるのか?」
こうした疑問は、特に私たちのお客様である多品種少量生産を営む中小製造業の経営者様にとって、常に頭を悩ませる課題ではないでしょうか。
2025年現在、原材料価格の不安定化、グローバルな競争の激化、そして深刻化する人手不足といった外部環境の変化は、企業経営における原価管理の重要性をかつてないほど高めています。
どんぶり勘定や従来のExcel頼りの管理方法では、複雑化するコスト構造を正確に把握し、迅速な経営判断を行うことがますます難しくなっています。
正確な原価情報なしには、適切な価格設定も、効果的なコスト削減策の実施も、そして持続的な利益の確保も望めません。
このような厳しい時代を勝ち抜くために、今こそ「原価管理システム」の導入が、中小製造業の皆様にとって喫緊の経営課題を解決する鍵となります。
原価管理システムは、単に原価計算を効率化するだけのツールではありません。
企業活動で発生するあらゆるコストを見える化し、分析することで、無駄の発見、業務プロセスの改善、そしてデータに基づいた戦略的な意思決定を強力に支援します。
これにより、業務効率化はもちろんのこと、製品ごとの採算性を的確に把握し、企業全体の収益力向上を実現することが可能になるのです。
いわば、原価管理システムは、デジタル変革(DX)を推進し、攻めの経営へと転じるための羅針盤と言えるでしょう。
この記事では、まさにその原価管理システムについて、基礎知識から機能、導入メリット、そして自社に最適なシステムを選ぶための具体的なポイントやおすすめ製品の比較紹介まで、あらゆる角度から徹底的に解説していきます。
この記事を読み終える頃には、なぜ今、原価管理とシステム導入がこれほどまでに重要なのか、そして貴社がどのような一歩を踏み出すべきか、その明確な答えが見つかるはずです。
原価管理の課題を解決し、企業の未来を明るく照らすシステムの世界へ一緒に進んでいきましょう。
2. 原価管理システムとは?基本を徹底解説
原価管理システムという言葉を耳にする機会が増えてきたものの、
「具体的にどのようなシステムなのか?」
「原価計算とは何が違うのか?」
といった疑問をお持ちの方も多いのではないでしょうか。
この章では、原価管理システムの最も基本的な概念、その目的、そして企業経営における重要性について、専門用語を避けながら、わかりやすく解説していきます。
原価管理システムを正しく理解することは、自社の課題解決に最適なツールを選ぶための第一歩です。
特に中小製造業の皆様にとっては、このシステムがいかにして利益創出に貢献するのか、その核心に触れる内容となります。
2.1.原価管理システムの定義と目的 - 「見える化」で経営判断を支援
原価管理システムとは、一言で表現するならば「企業が製品やサービスを提供する上で発生する様々なコスト(=原価)を、正確に収集・計算・分析し、その結果をもとにコストの最適化や利益の最大化を目指すための情報システム」のことです。
単に原価を計算するだけでなく、その原価情報を活用して経営の意思決定を支援することに主眼が置かれています。
つまり、原価管理システムは、原価の「見える化」を実現し、経営者がデータに基づいた的確な判断を行うための羅針盤のような役割を担います。
原価管理システムの主な目的は、以下の3つに集約されます。
正確な原価把握
製品ごと、プロジェクトごと、あるいは部門ごとといった様々な切り口で、実際にどれだけのコストがかかっているのかを正確に把握することが、原価管理の出発点です。
材料費、労務費、経費といった直接費はもちろんのこと、複数の製品や部門にまたがって発生する間接費を、適切な基準に基づいて配賦計算することも原価管理システムの重要な機能です。
私が以前支援したある金属加工メーカーでは、原価管理システム導入前はどんぶり勘定に近く、どの製品が本当に儲かっているのか不明瞭でした。
システム導入後、初めて製品ごとの正確な原価が明らかになり、実は主力と信じていた製品の一部が赤字であったことが判明し、大きな衝撃を受けたという経験があります。
この「正確な原価把握」こそが、全ての改善活動の基礎となります。
コストの最適化と削減
正確な原価情報が明らかになれば、次に目指すのはコストの最適化と削減です。
原価管理システムは、予算と実績の差異分析機能を備えており、どこに無駄なコストが潜んでいるのか、どの工程で効率が悪いのかを特定するのに役立ちます。
例えば、標準原価と実際原価を比較することで、材料の歩留まりが悪化している、特定の作業時間が想定以上にかかっているといった問題点を見える化できます。
これにより、具体的な改善策を立案し、実行することが可能になります。
原価管理システムは、単に問題を指摘するだけでなく、その原因究明と対策立案を支援するツールなのです。
利益最大化と経営判断の支援
最終的な目的は、企業の利益を最大化することです。
原価管理システムから得られる詳細な原価情報や採算分析の結果は、製品の価格設定、新製品開発の可否判断、不採算製品からの撤退判断、設備投資の意思決定など、企業経営における様々な重要な判断の拠り所となります。
例えば、ある製品の原価が競合他社よりも高いことが判明した場合、その原因を追求し、コスト削減努力を重ねるか、あるいは付加価値を高めて価格に転嫁するか、といった戦略的な判断が必要になります。
原価管理システムは、このような経営判断に必要な客観的なデータを提供し、経営者を力強くサポートします。
これらの目的を達成するために、原価管理システムはデータの収集から計算、分析、レポーティングまでの一連のプロセスを効率的に行う機能を備えています。特に、複雑な製品構成や製造工程を持つ多品種少量生産の製造業においては、原価管理システムなしにこれらの目的を達成することは極めて難しいと言えるでしょう。
2.2.原価管理システムの基本的な仕組みと構成要素
原価管理システムがどのようにして原価を計算し、管理しているのか、その基本的な仕組みと主要な構成要素について見ていきましょう。原価管理システムは、様々な情報源からデータを収集し、それらを基に各種計算を行い、最終的に経営判断に役立つ情報をアウトプットするという一連の流れを持っています。
この仕組みを理解することで、原価管理システムが自社のどのような業務と関連し、どのような効果をもたらすのかがより明確になります。
原価管理システムの基本的な仕組みは、大きく以下の3つのステップで構成されます。
1. データ収集・入力
原価計算に必要な元データを収集・入力する最初のステップです。このデータの精度が、最終的な原価情報の信頼性を大きく左右します。主なデータとしては、以下のようなものが挙げられます。
材料費データ
製品の製造に使用された原材料や部品の品目、数量、単価など。購買管理 システムや在庫管理 システムから連携されることが多いです。
労務費データ
製品の製造に直接関わった作業員の作業時間や賃率、あるいは間接部門の人件費など。勤怠管理 システムや人事給与システムから情報を取得します。
経費データ
外注加工費、機械の減価償却費、水道光熱費、消耗品費など、上記以外の諸経費。会計システムや経費精算システムからデータを収集します。
生産実績データ
どの製品をどれだけ生産したか、どの工程でどれだけの作業が行われたかといった実績データ。生産管理 システムやMES(製造実行システム)と連携することが一般的です。
原価管理システムの多くは、これらの関連システムとAPI連携やファイル連携を行う機能を備えており、手入力の手間を軽減し、データの正確性を向上させます。
2. 原価計算・配賦処理
収集されたデータをもとに、原価計算を実行するコアとなるステップです。
原価管理システムでは、以下のような様々な原価計算方法に対応しています。
実際原価計算
実際に発生したコストを積み上げて原価を算出する方法です。
標準原価計算
あらかじめ科学的な方法で目標となる標準原価を設定し、実際原価との差異を分析することでコスト管理を行う方法です。
直接原価計算
原価を変動費と固定費に分類し、限界利益を重視する管理会計手法です。
また、複数の製品や部門に共通して発生する間接費(工場全体の減価償却費や間接部門の人件費など)を、一定の基準(作業時間、機械稼働時間、材料使用量など)に基づいて各製品や部門に割り振る「配賦処理」もこの段階で行われます。
この配賦基準の設定が、原価の正確性に大きな影響を与えるため、原価管理システムでは柔軟な配賦基準の設定機能が重要となります。
3. 原価分析・レポーティング
計算された原価情報を分析し、経営判断に役立つレポートとして出力する最終ステップです。
原価管理システムは、以下のような多様な分析機能やレポーティング機能を提供します。
製品別原価一覧表
各製品の原価構成(材料費、労務費、経費の内訳)や利益率などを一覧で表示します。
差異分析レポート
標準原価と実際原価の差異や、予算と実績の差異を項目別に表示し、その原因究明を支援します。差異の要因を深掘りするためのドリルダウン機能を備えたシステムも多いです。
損益分岐点分析
売上高と費用の関係から、利益がゼロになる売上高(損益分岐点)を算出し、利益計画の立案に活用します。
シミュレーション機能
材料単価の変動や生産量の変更などが原価や利益にどのような影響を与えるかを事前に試算する機能です。
これらのレポートは、グラフや表を活用して視覚的にわかりやすく表示され、経営層や各部門の管理者が迅速に状況を把握し、次のアクションを検討するのに役立ちます。
これらの構成要素が有機的に連携することで、原価管理システムは複雑な原価管理業務を効率的かつ正確に遂行することを可能にしています。特に、基幹システム(ERP)の一部として原価管理機能を提供するシステムや、他のシステムとの連携を重視した製品が増えています。
2.3.原価計算との違いとは?関連性とそれぞれの役割について解説
「原価管理」と「原価計算」は、しばしば混同されたり、同じ意味で使われたりすることがありますが、厳密には異なる概念です。
この二つの違いと関連性を正しく理解することは、原価管理システムの役割をより深く把握する上で非常に重要です。
それぞれの言葉が指す意味と、企業活動における位置づけについて解説します。
まず、「原価計算」についてです。原価計算とは、「製品やサービスを生産・提供するために消費された経済価値(つまりコスト)を、一定のルールに基づいて測定し、計算する手続き」そのものを指します。具体的には、製品1単位あたりにどれだけの材料費、労務費、経費がかかったのかを算出する作業です。原価計算の主な目的は、財務諸表(特に損益計算書における売上原価や棚卸資産の評価額)を作成するために必要な原価情報を提供すること(財務会計目的)、そして製品の価格設定や予算編成の基礎資料とすること(管理会計目的)にあります。つまり、原価計算は「原価を算出する技術・プロセス」に焦点が当てられています。
一方、「原価管理」とは、その名の通り「原価を管理すること」を意味します。原価計算によって算出された原価情報を活用し、コストの標準を設定したり(標準原価設定)、実際に発生したコストがその標準から逸脱していないかを監視したり(差異分析)、逸脱があった場合にはその原因を追求し、コスト削減や業務改善のための具体的なアクションを計画・実行したりする一連の活動全体を指します。原価管理の目的は、単に原価を計算するだけにとどまらず、その情報を経営の意思決定に活かし、企業の収益性向上や競争力強化に貢献することにあります。つまり、原価管理は「原価情報を経営に活かすためのマネジメント活動」と言えます。
このように考えると、原価計算は原価管理を行うための重要なツールの一つ、あるいは原価管理という大きな枠組みの中の一部のプロセスであると位置づけることができます。正確な原価計算なくして効果的な原価管理はあり得ませんし、逆に、どれだけ正確に原価計算ができたとしても、その結果が経営改善に活かされなければ意味がありません。
原価管理システムは、この両方の側面をカバーするツールと言えます。システム内部では精緻な原価計算機能(実際原価計算、標準原価計算、配賦処理など)が実行されます。そして、その計算結果を基に、差異分析レポート、製品別損益一覧、シミュレーション機能などを提供することで、経営者が原価管理を効果的に行うことを支援します。例えば、ある部品の仕入れ単価が上昇した場合、原価計算機能がその影響を製品原価に反映し、原価管理機能(シミュレーションや分析レポート)が「どの製品の利益率がどれだけ悪化するか」「代替材料を採用した場合のコストはどうか」といった経営判断に必要な情報を提示する、といった具合です。
中小製造業においては、原価計算の手間に追われ、その先の原価管理まで手が回らないというケースが少なくありません。原価管理システムを導入することは、この原価計算の業務を大幅に効率化し、より戦略的な原価管理へとステップアップするための強力な後押しとなるのです。
2.4.Excelや手作業による原価管理の限界とシステム化のメリット
現在、多くの中小製造業において、表計算ソフトのExcelや手作業で原価管理を行っているケースが見受けられます。Excelは手軽に利用でき、柔軟性も高いため、一定規模までの企業や比較的シンプルな原価計算であれば有効なツールとなり得ます。
しかし、企業規模の拡大、取り扱い製品数の増加(多品種少量化)、製造工程の複雑化などに伴い、Excelや手作業による原価管理には様々な限界が見え始めます。ここでは、その具体的な限界点と、原価管理システムを導入してシステム化することによるメリットについて、私のコンサルティング経験を踏まえながら詳しく解説します。
まず、Excelや手作業による原価管理の主な限界点としては、以下のような点が挙げられます。
データの収集・入力に膨大な手間と時間がかかる
原価計算に必要な材料費、労務費、経費などのデータを各部門から集め、Excelのシートに手入力する作業は、非常に時間と手間がかかります。特に多品種少量生産の企業では、製品ごとに構成部品や作業工程が異なるため、入力するデータ量も膨大になりがちです。
私が担当したある食品メーカーでは、毎月、複数の担当者が数日間つきっきりで各工場からの生産実績や材料使用量の報告をExcelに転記していましたが、それでも入力ミスが後を絶たず、確認作業にさらに時間を要していました。このような状況では、担当者の負担が大きく、本来行うべき分析業務などに手が回りません。
計算ミスや人的エラーが発生しやすい
Excelの関数やマクロを駆使して複雑な原価計算ロジックを組むことは可能ですが、数式が長大になったり、複数のシート間でデータを参照したりする場合、計算ミスや参照エラーが発生するリスクが常に伴います。また、手入力による転記ミスや、担当者ごとの思い込みによる誤った処理など、人的エラーも避けられません。これらのエラーは、原価情報の精度を著しく低下させ、誤った経営判断を招く可能性があります。
ある電子部品メーカーでは、ExcelのVLOOKUP関数の範囲指定ミスにより、一部部品の単価が誤って計算され続け、長期間にわたり不採算製品に気づかなかったという苦い経験をお持ちでした。
リアルタイムな情報把握が難しい
Excelによる原価計算は、月次や都度バッチ的に行うことが一般的であり、リアルタイムに原価情報を把握することは困難です。市場環境の変化が激しい現代において、経営判断に必要な情報が1ヶ月遅れでしか出てこないのでは、迅速な意思決定は望めません。「今、この製品は儲かっているのか?」という問いに即座に答えられないことは、大きな機会損失につながります。
データの属人化と共有の難しさ
複雑なExcelファイルやマクロは、作成した担当者以外には理解が難しく、メンテナンスも困難になりがちです(いわゆる「Excel職人」問題)。その担当者が異動や退職した場合、原価計算業務が滞ってしまうリスクがあります。また、Excelファイルは個人PCや共有フォルダで管理されることが多く、最新版のファイルがどれか分からなくなったり、複数担当者による同時編集が難しかったりするなど、情報共有やバージョン管理の面でも課題があります。
高度な分析やシミュレーションへの対応が困難
製品別の詳細な損益分析、原価変動要因の深掘り、将来の原価シミュレーションといった高度な分析をExcelで行うには、専門的な知識と高度なスキルが要求され、限界があります。経営戦略に直結するような情報をタイムリーに引き出すことが難しいのです。
これらの限界点を克服し、より高度な原価管理を実現するために、原価管理システムの導入が有効となります。システム化による主なメリットは以下の通りです。
業務効率の大幅な向上(自動化)
原価管理システムは、販売管理 システム、生産管理
システム、会計システムなど、他の基幹システムとデータ連携することで、データ収集・入力の多くを自動化します。これにより、手作業による手間や時間が大幅に削減され、担当者はより付加価値の高い分析業務や改善活動に注力できます。
原価計算の精度向上と標準化
あらかじめ定義された計算ロジックと統一されたマスターデータに基づいてシステムが自動的に原価計算を行うため、人的エラーが介在する余地が大幅に減り、原価情報の精度と信頼性が格段に向上します。また、原価計算プロセスが標準化されるため、担当者によるバラつきもなくなります。
リアルタイムな原価把握と迅速な意思決定の実現
システム上でデータが一元管理され、必要な時に最新の原価情報を即座に参照できるようになります。これにより、経営層はタイムリーな情報に基づいた迅速な意思決定が可能となり、市場の変化にも柔軟に対応できるようになります。
データの属人化防止と情報共有の円滑化
原価管理システムでは、原価計算のロジックやデータがシステム内で一元的に管理されるため、特定の担当者に依存することなく、誰でも(権限に応じて)必要な情報にアクセスし、活用することが可能になります。情報の透明性が高まり、部門間の連携もスムーズになります。
高度な分析機能と経営判断の質の向上
原価管理システムは、製品別・顧客別・部門別など多角的な分析機能や、差異分析、損益分岐点分析、原価シミュレーションといった高度な機能を標準で備えているものが多く、経営戦略の立案や的確な意思決定を強力に支援します。これにより、データに基づいた科学的な経営が実現できます。
私がコンサルティングで原価管理を支援した多くの中小製造業では、Excel管理からの脱却により、これらのメリットを享受し、原価管理のレベルを飛躍的に向上させています。
例えば、ある機械部品メーカーでは、原価管理システム導入後、月次の原価確定までの期間が従来の約半分に短縮され、かつ、製品ごとの詳細な収益性が見える化されたことで、不採算製品の絞り込みと対策が迅速に打てるようになり、半年で全体の利益率が改善したという実績があります。
もちろん、原価管理システムの導入には初期費用や運用コスト、導入時の手間もかかりますが、長期的な視点で見れば、これらのメリットは企業の競争力強化と持続的成長に大きく貢献すると言えるでしょう。
3. 原価管理システム導入のメリット・デメリット
原価管理システムの導入は、多くの企業、特に私たちのお客様である中小製造業の皆様にとって、経営体質を強化し、競争優位性を確立するための重要な一手となり得ます。しかし、新しいシステムを導入する際には、その輝かしいメリットだけでなく、潜在的なデメリットや注意すべきポイントも十分に理解しておく必要があります。「こんなはずではなかった…」という事態を避けるためにも、ここでは原価管理システム導入によってもたらされる具体的な効果と、事前に把握しておくべき課題について、コンサルタントとしての経験を踏まえながら、詳しく解説していきます。
3.1.導入で得られる効果とは?企業にもたらす主なメリット一覧
原価管理システムを導入し、適切に活用することで、企業は多岐にわたるメリットを享受することが可能です。これらのメリットは、単に業務の効率化に留まらず、企業の収益構造の改善や意思決定の質の向上、ひいては企業文化の変革にまでつながる可能性があります。ここでは、特に重要と考えられる主なメリットを3つのポイントに絞って、具体的に見ていきましょう。
3.1.1.正確な原価把握と迅速な経営判断の実現
原価管理システム導入における最大のメリットの一つは、何と言っても「製品ごと、あるいはプロジェクトごとの正確な原価を、タイムリーに把握できるようになる」ことです。これは、特に多品種少量生産を特徴とする中小製造業にとっては、経営の根幹に関わる極めて重要な効果と言えるでしょう。
結論として、原価管理システムは、従来ブラックボックス化しがちだったコストの内訳を詳細に「見える化」し、データに基づいた迅速かつ的確な経営判断を可能にします。
例えば、私が以前コンサルティングで支援させていただいたある金属部品メーカーA社様は、長年Excelを駆使して熟練の担当者が原価計算を行っていました。しかし、取り扱い部品が数千点に及び、製造工程も複雑だったため、月次の原価が確定するまでに翌月の中旬を過ぎるのが常でした。そのため、ある製品が赤字になっていると判明しても、既に対策が後手に回り、損失が拡大してしまうケースが散見されたのです。さらに、Excelでは間接費の配賦基準が曖昧で、本当にその製品の原価が正確なのか、社内でも疑問の声が上がっていました。
そこでA社様は、思い切って原価管理システムの導入に踏み切りました。システム導入後は、生産管理 システムや購買管理
システムとデータが自動連携され、日々の生産実績や材料使用量などがリアルタイムに近い形で原価計算に反映されるようになりました。その結果、従来1ヶ月半かかっていた製品別原価の確定が、わずか数日で完了するようになり、経営陣はほぼリアルタイムで各製品の採算状況を把握できるようになったのです。正確な原価が明らかになったことで、A社様は驚くべき事実に直面しました。これまで主力と信じていた製品群の一部が、実は慢性的な赤字状態だったのです。この事実にいち早く気づけたことで、A社様は問題製品の価格改定交渉や製造プロセスの徹底的な見直しに迅速に着手し、半年後にはその赤字製品群を黒字転換させることに成功しました。これは、原価管理システムがもたらす「正確な原価把握」と「迅速な経営判断」の効果を如実に示す事例です。
原価管理システムは、材料費、労務費、経費といった直接費はもちろん、配賦が難しい間接費についても、事前に設定した合理的な基準に基づいて自動計算を行うため、原価計算の精度が飛躍的に向上します。これにより、「どの製品がいくら儲かっているのか(あるいは損しているのか)」、「コストが想定以上にかかっている工程はどこか」といった情報が明確になり、経営者は自信を持って価格戦略、製品ポートフォリオ戦略、コスト削減戦略などを立案・実行できるようになるのです。原価管理システムは、まさに勘や経験に頼った経営から、データドリブンな経営へと移行するための強力な推進力となります。
3.1.2.業務効率化とコスト削減への貢献(プロセス改善)
次に挙げる大きなメリットは、「原価管理に関わる一連の業務の大幅な効率化と、それに伴う間接的なコスト削減への貢献」です。日々のデータ入力や集計、レポート作成といった作業に多くの時間と手間を費やしている企業にとって、原価管理システムの導入は、まさに福音となる可能性があります。
結論として、原価管理システムは、手作業が多く非効率だった原価管理業務を自動化・標準化することで、担当者の作業負荷を大幅に軽減し、人件費を含む間接コストの削減、さらには業務プロセス全体の改善へとつなげます。
私がコンサルティングで関わった多くの中小製造業の現場では、原価計算の時期になると経理部門や生産管理部門の担当者が残業続きになる、という光景が珍しくありませんでした。各部門から集めた紙の伝票やExcelファイルを元に、膨大なデータを転記し、検算し、集計するという作業は、精神的にも肉体的にも大きな負担となります。ある食品加工会社B社様もその一社で、月次の原価計算には3名の担当者がほぼ1週間つきっきりで対応していましたが、それでも入力ミスや集計ミスが頻発し、その修正作業にさらに時間を奪われるという悪循環に陥っていました。
B社様が原価管理システムを導入した結果、その業務風景は一変しました。販売管理 システムから受注情報や売上情報を、生産管理 システムから生産実績や材料消費情報を、勤怠管理
システムから作業時間情報を、それぞれ原価管理システムが自動で取り込めるように連携させたのです。これにより、従来手作業で行っていたデータ収集・入力作業の約8割が自動化されました。担当者は、システムが算出した原価データの確認と分析、そして差異が生じた場合の深掘りといった、より付加価値の高い業務に集中できるようになりました。結果として、月次の原価計算に要する時間は従来の3分の1以下に短縮され、残業時間も大幅に削減。担当者のモチベーション向上にもつながったのです。これは、原価管理システムが直接的な業務効率化を達成した分かりやすい事例です。
さらに、業務効率化は間接的なコスト削減にも波及します。まず、単純作業の時間が減ることで、その分の人件費が実質的に削減されます。また、入力ミスや計算ミスが減ることで、手戻りや修正作業に伴う無駄なコストも発生しにくくなります。原価管理システムによって業務プロセスが標準化されることは、特定の担当者にしかできないといった「属人化」のリスクを低減し、担当者の急な欠勤や退職時にも業務が滞りなく継続できる体制づくりにも貢献します。これは、BCP(事業継続計画)の観点からも非常に重要なポイントです。
このように、原価管理システムは、日々の煩雑な原価管理業務から担当者を解放し、企業全体の生産性向上とコスト構造の改善に大きく寄与するのです。
3.1.3.詳細なデータ分析による採算管理の高度化
三つ目の大きなメリットとして、「原価管理システムが提供する豊富なデータと分析機能を活用することで、企業の採算管理をより高度なレベルへ引き上げることができる」点が挙げられます。単に原価を計算して終わりではなく、その情報を多角的に分析し、利益を生み出すための具体的なアクションに繋げることが、原価管理の本来の目的です。
結論として、原価管理システムは、製品別・顧客別・部門別といった様々な切り口での詳細な損益分析や、原価シミュレーションを可能にし、データに基づいた的確な採算改善策の立案と実行を支援します。
以前、私が支援したあるカスタム機械メーカーC社様は、個別の受注案件ごとに設計・製造を行うビジネスモデルのため、案件ごとの正確な採算把握が経営上の最重要課題でした。しかし、従来のExcelベースの管理では、各案件に間接費をどのように配賦するかが曖昧で、見積段階での原価予測の精度も低く、気づけば赤字案件を抱えていることもしばしばありました。特に、技術的に難易度の高い案件や短納期案件では、想定外の工数が発生しやすく、採算が悪化する傾向にありました。
C社様は、原価管理システムの中でも特にプロジェクト型の原価管理に強い製品を選定し、導入しました。新しいシステムでは、各案件に紐づく直接材料費、直接労務費(作業員がどの案件にどれだけ時間を投入したかを正確に記録)、外注費などがリアルタイムに集計されるようになりました。また、間接費についても、部門ごとの活動基準(例えば設計部門なら設計工数、製造部門なら機械稼働時間など)に基づいた多段階配賦を設定することで、より実態に近い形で各案件にコストが割り振られるようになりました。
その結果、C社様は、個々の案件の詳細な原価構成と利益率を、進行中であってもほぼリアルタイムで把握できるようになったのです。システムが提供する分析レポートを活用することで、
「どのタイプの案件が儲かりやすいのか」
「どの顧客との取引が最も収益性が高いのか」
「原価が予算を超過しやすいのはどのようなケースか」
といったことが、具体的なデータとして見える化されました。
これにより、C社様は赤字になりやすい案件の傾向を掴み、見積時の原価予測精度を大幅に向上させることができました。また、不採算案件については、その原因を深掘りし、設計変更によるコストダウンや顧客との価格交渉を有利に進めるための客観的な資料として原価データを活用できるようになりました。さらに、原価シミュレーション機能を使い、受注前の段階で、異なる材料を採用した場合や工程を一部外注した場合の原価変動を予測し、最も利益の出る方法を選択するといった、より戦略的なアプローチも可能になったのです。
このように、原価管理システムは、過去の実績データを分析するだけでなく、将来の収益性を予測し、改善するための洞察を提供します。これにより、企業は場当たり的な対応ではなく、データに裏打ちされた科学的なアプローチで採算管理を高度化し、持続的な利益成長を実現することができるのです。
3.2.導入前に知っておくべきデメリットや注意点
これまで原価管理システム導入の素晴らしいメリットについて述べてきましたが、一方で、導入を成功させるためには、事前に理解し、対策を講じておくべきデメリットや注意点も存在します。これらを軽視すると、期待した効果が得られないばかりか、導入プロジェクト自体が頓挫してしまう可能性すらあります。ここでは、原価管理システム導入に際して、特に中小製造業の皆様が直面しやすい一般的なデメリットと注意点を具体的に解説します。
結論として、原価管理システムの導入には、初期費用や運用コスト、導入にかかる時間と労力、既存業務フローの変更への対応、そしてシステム定着化への努力が必要であり、これらを事前に十分に検討し、計画的に進めることが成功の鍵となります。
導入コスト(初期費用・ランニングコスト)の発生
原価管理システムを導入するには、当然ながら費用がかかります。システムの購入費用(パッケージ型の場合)や開発費用(カスタマイズやスクラッチ開発の場合)、あるいはクラウド型システムの初期設定費用や月額(または年額)利用料が発生します。
これに加えて、導入支援コンサルティング費用、サーバーやネットワークなどのインフラ整備費用(オンプレミス型の場合)、社員向けの教育研修費用なども考慮する必要があります。
特に中小企業にとっては、これらのコストは決して小さくない投資となります。
注意点として、単に価格の安さだけでシステムを選ぶのではなく、自社の課題解決に本当に必要な機能を備えているか、将来的な拡張性はあるか、費用対効果(ROI)を長期的な視点で慎重に検討することが重要です。複数のベンダーから見積もりを取り、機能と価格のバランスを比較しましょう。
また、クラウド型システムは初期費用を抑えられる傾向にありますが、月額費用が継続的に発生するため、長期的な総コストも試算しておく必要があります。
導入にかかる時間と労力(手間)
原価管理システムの導入は、スイッチを押せばすぐに使えるというものではありません。自社の業務プロセスの分析、システム要件定義、システムの設定やカスタマイズ、データ移行、社員教育、テスト運用など、本稼働に至るまでには相応の時間と労力が必要です。
特に、既存の基幹システム(販売管理、生産管理、会計など)との連携が必要な場合は、その調整に時間を要することがあります。
注意点として、無理のない導入スケジュールを策定し、社内に専門のプロジェクトチームを組成するか、主要な担当者を明確に割り当てることが不可欠です。また、システムベンダーや導入支援コンサルタントのサポート体制も重要なポイントです。導入プロセスで発生しうる課題や遅延リスクを事前に洗い出し、対策を準備しておくことも求められます。ある企業では、現場の意見を十分に聞かずにシステム選定を進めた結果、導入段階で仕様変更が多発し、スケジュールが大幅に遅延した事例がありました。
既存業務フローの変更と社員の適応
新しい原価管理システムを導入するということは、多くの場合、従来の業務のやり方を変えることを意味します。例えば、データの入力方法やタイミング、レポートの形式、承認プロセスなどが変更される可能性があります。こうした変化に対して、社員が抵抗を感じたり、新しいシステムの操作に戸惑ったりすることは十分に考えられます。特に長年慣れ親しんだ方法を変えることへの心理的なハードルは意外と高いものです。
注意点として、なぜシステムを導入するのか、それによってどのようなメリットがあるのかを社員に丁寧に説明し、理解と協力を得ることが不可欠です。また、十分な教育研修の機会を設け、操作マニュアルを整備し、導入後も継続的なサポート体制を整えることが重要です。新しいシステムが定着するまでにはある程度の時間がかかることを覚悟し、辛抱強く取り組む姿勢が求められます。トップダウンでの強いリーダーシップと、現場の声を吸い上げるボトムアップの活動の両輪が効果的です。
システムの定着化と継続的な運用負荷
原価管理システムは、導入して終わりではありません。システムを有効に活用し続けるためには、データの鮮度と精度を維持するための継続的な運用努力が必要です。マスターデータ(品目マスター、構成表マスター、工程マスターなど)の定期的なメンテナンス、システムのバージョンアップへの対応、社員の異動や退職に伴う再教育なども考慮しなければなりません。これらを怠ると、せっかく導入したシステムが形骸化し、「使われないシステム」になってしまう恐れがあります。
注意点として、システム運用担当者を明確にし、その役割と責任を定義することが重要です。また、システムベンダーからの保守サポートの内容(問い合わせ対応、障害対応、バージョンアップ情報の提供など)を事前にしっかり確認しておきましょう。運用ルールを策定し、定期的にシステムの利用状況や効果をレビューし、改善を重ねていくプロセスを組み込むことも、システムを長く有効に使い続けるためには不可欠です。
これらのデメリットや注意点を事前にしっかりと認識し、対策を講じた上で原価管理システムの導入プロジェクトを進めることが、成功への確実な道筋となります。決して楽な道のりではありませんが、その先には企業の大きな成長が待っていると信じて、計画的に取り組むことが肝要です。
4. 原価管理システムの主要機能とは?自社に必要な機能を見極める
原価管理システムと一口に言っても、その機能は多岐にわたります。基本的な原価計算機能から、高度な分析機能、さらには他のシステムとの連携機能まで、実にさまざまです。自社の課題解決や目的達成に本当に必要な機能を見極めることは、最適な原価管理システムを選ぶ上で非常に重要なポイントとなります。「多機能であればあるほど良い」というわけではなく、自社の業務や規模、業種特性にマッチした機能を過不足なく備えているかどうかが肝心です。この章では、原価管理システムが持つ代表的な主要機能について、それぞれがどのような役割を果たし、どのような企業にとって特に有効なのかを、具体例を交えながら解説していきます。これらの情報を参考に、ぜひ貴社にとって「使える」機能は何かを検討してみてください。
4.1.標準機能一覧:実行予算、原価計算(標準・実際)、配賦処理など
まず、多くの原価管理システムに標準的に搭載されている基本的な機能群について見ていきましょう。これらの機能は、原価管理を行う上での土台となるものであり、企業の規模や業種を問わず、正確な原価把握と基本的なコスト管理を実現するために不可欠なものです。これらの標準機能をしっかりと理解し、自社の業務と照らし合わせることが、システム選定の第一歩となります。
結論として、原価管理システムの標準機能は、日々のコストデータを収集・計算し、計画との比較を通じて管理の基礎を築くための必須ツール群です。
主な標準機能としては、以下のものが挙げられます。
実行予算作成・管理機能
原価管理を効果的に行うためには、まず目標となる予算を設定することが重要です。
実行予算とは、特定のプロジェクトや製品、あるいは一定期間の活動に対して、事前に材料費、労務費、経費などのコストを見積もり、計画値として具体的に設定するものです。原価管理システムの実行予算機能は、過去の実績データやマスター情報を参考にしながら、効率的に実行予算を作成することを支援します。また、承認ワークフロー機能を備えたシステムであれば、予算作成から承認までのプロセスをシステム上で一元管理することも可能です。
例えば、ある建設業のお客様D社様は、従来Excelで各工事の実行予算を作成していましたが、過去の類似工事のデータを探し出すのに手間がかかり、見積もりの精度にもバラつきがありました。原価管理システム導入後は、過去の工事実績がシステムに蓄積され、類似案件の予算を簡単に参照・コピーして新しい実行予算を組めるようになり、予算作成時間が大幅に短縮され、精度も向上しました。
原価計算機能(実際原価計算・標準原価計算など)
これは原価管理システムの中核となる機能です。実際に発生したコストを集計して製品やプロジェクトの原価を算出する「実際原価計算」はもちろんのこと、多くのシステムでは、あらかじめ目標となる原価を設定しておく「標準原価計算」にも対応しています。標準原価計算を行うことで、実際にかかった原価との差異を分析し、コスト管理の指標とすることができます。また、製品の種類や企業の管理方針に応じて、ロット別原価計算、工程別原価計算、ジョブ別原価計算など、さまざまな計算方法をサポートしているシステムも多いです。
多品種少量生産の製造業では、製品ごとに原価を正確に捉えることが特に重要となるため、自社の生産形態に合った原価計算方法をサポートしているかどうかが選定のポイントとなります。
配賦処理機能
複数の製品や部門に共通して発生する間接費(例えば、工場全体の減価償却費、水道光熱費、間接部門の人件費など)を、一定の基準に基づいて各原価集計単位(製品、部門、プロジェクトなど)に割り振る処理を「配賦」と呼びます。この配賦基準の設定方法が、原価の正確性に大きな影響を与えます。原価管理システムでは、作業時間、機械稼働時間、材料費比率、生産数量など、さまざまな配賦基準を柔軟に設定できる機能が備わっています。また、複数の基準を組み合わせた多段階配賦や、活動基準原価計算(ABC:Activity
Based Costing)の考え方を取り入れた配賦が可能なシステムもあります。
私が支援したある家具メーカーE社様では、従来、間接費を単純に売上高比率で配賦していましたが、原価管理システム導入を機に、各製品の製造に実際にかかっている手間(作業時間や機械占有時間)を基準とした配賦に見直しました。その結果、これまで利益が出ていると思っていた手間のかかる特注品が、実は赤字に近いことが判明し、価格設定や製品戦略の見直しに繋がりました。適切な配賦処理機能は、より正確な原価把握に不可欠です。
マスタ管理機能
原価計算の精度と効率を維持するためには、品目マスター(原材料、部品、製品)、部品表(BOM:Bill Of
Materials)マスター、工程マスター、作業単価マスター、配賦基準マスターなど、さまざまなマスターデータを正確に管理する必要があります。原価管理システムは、これらのマスターデータを一元的に登録・更新・管理する機能を提供します。マスターデータが整備されていることで、データ入力の手間が省け、計算の標準化が図れます。
特に部品表(BOM)は製造業の原価計算の骨格となるため、原価管理システムがBOMの変更履歴管理や版管理に対応しているか、また、設計変更がスムーズに原価計算に反映される仕組みになっているかは重要なチェックポイントです。
これらの標準機能は、原価管理の基盤を構築する上で欠かせないものです。自社の業務フローや管理レベルを考慮し、これらの機能が過不足なく提供されているか、また、操作性や設定の柔軟性などをしっかりと確認することが、システム選定の第一歩となります。
4.2.プロジェクト別・部門別・製品別原価管理機能
多くの原価管理システムでは、基本的な原価計算機能に加えて、より詳細な管理単位で原価を把握し、分析するための機能が充実しています。特に、「プロジェクト別」「部門別」「製品別」といった切り口での原価管理機能は、企業が自社の収益構造を深く理解し、的確な経営判断を行う上で非常に有効です。これらの機能を活用することで、どこでコストが発生し、どこで利益が生まれているのかを、より具体的に「見える化」することが可能になります。
結論として、プロジェクト別・部門別・製品別原価管理機能は、企業活動の様々な側面からコストと収益性を掘り下げて分析し、より精密な経営管理を実現するための強力な武器となります。
プロジェクト別原価管理機能
建設業、ITシステム開発業、コンサルティング業、個別受注生産の製造業など、プロジェクト単位で業務が進行する業種においては、プロジェクトごとの原価と採算を正確に把握することが経営の生命線です。プロジェクト別原価管理機能は、各プロジェクトに紐づく材料費、労務費(誰がどのプロジェクトにどれだけの工数を投入したか)、外注費、その他経費などを個別に見積もり、実績を収集・集計し、予算と実績の差異をリアルタイムに管理することを可能にします。
例えば、あるソフトウェア開発会社F社様は、各開発プロジェクトの進捗や採算状況が不明瞭で、気づいた時には予算オーバーや納期遅延が発生していることが課題でした。プロジェクト原価管理機能を備えた原価管理システムを導入したことで、各プロジェクトの工数実績や外注費の発生状況が日々更新され、プロジェクトマネージャーはいつでも最新の採算状況を確認できるようになりました。これにより、予算超過の兆候を早期に察知し、対策を講じることが可能となり、プロジェクトの利益率改善に大きく貢献しました。また、完了したプロジェクトの実績データは、次の類似プロジェクトの見積もり精度向上にも役立っています。
部門別原価管理機能
企業内の各部門(製造部門、営業部門、開発部門、管理部門など)が、それぞれどれだけのコストを消費し、どれだけの貢献(利益や付加価値)を生み出しているのかを把握することは、部門ごとの業績評価やリソースの最適配分に不可欠です。部門別原価管理機能は、各部門で発生した直接費や、本社共通費などの間接費を適切な基準で各部門に配賦し、部門ごとの損益を明らかにします。
これにより、各部門長は自部門のコスト意識を高め、無駄の削減や効率化への取り組みを促進することができます。また、経営層は、どの部門が収益に貢献し、どの部門に課題があるのかを客観的なデータで評価し、経営資源の重点配分や組織再編などの意思決定に活用できます。
製品別原価管理機能
これは特に製造業にとって最も基本的な管理単位と言えるでしょう。どの製品がどれだけの原価で製造され、どれだけの利益を生んでいるのかを正確に把握することは、価格設定、製品ポートフォリオの最適化(不採算製品の見直しや新製品開発)、コスト削減努力の方向付けなど、あらゆる経営戦略の基礎となります。製品別原価管理機能は、各製品の材料費、労務費、製造経費を精緻に計算し、製品ごとの詳細な原価構成や利益率を明らかにします。
多品種少量生産の企業では、アイテム数が膨大になるため、手作業やExcelでの製品別原価管理は非常に困難ですが、原価管理システムを活用することで、この業務を大幅に効率化し、精度を向上させることが可能です。
あるアパレルメーカーG社様は、原価管理システムで製品別の正確な原価と販売実績を紐付けて分析した結果、売上は大きいものの利益率が極端に低い製品や、逆に売上は小さいものの非常に利益率の高いニッチな製品を発見できました。この分析結果をもとに、製品ラインナップの見直しや販売戦略の変更を行い、全体の収益性改善に成功しました。
これらの「○○別」原価管理機能は、企業が自社の事業活動をより解像度高く理解するための虫眼鏡のようなものです。どの切り口での管理が自社にとって最も重要かを見極め、それらの機能が充実している原価管理システムを選ぶことが、経営の「見える化」を加速させる鍵となります。
4.3.予算実績管理・差異分析機能とレポート出力
原価管理システムの価値は、単に原価を計算するだけに留まりません。計画(予算)と実績を比較し、その間に生じた「差異」を分析することで、問題点の早期発見や業務改善につなげることができてこそ、真の原価管理と言えます。そのために不可欠なのが、「予算実績管理機能」と「差異分析機能」、そしてそれらの結果を分かりやすく表示する「レポート出力機能」です。これらの機能は、PDCAサイクル(Plan-Do-Check-Action)を回し、継続的なコスト削減と収益性向上を実現するためのエンジンとなります。
結論として、予算実績管理・差異分析機能とレポート出力機能は、計画と結果のギャップを明らかにし、その原因を深掘りすることで、具体的な改善アクションを導き出し、経営管理レベルを向上させるための必須機能です。
予算実績管理機能
この機能は、事前に設定した実行予算や標準原価と、実際に発生した原価(実績原価)を同一画面上やレポート上で対比して表示するものです。プロジェクトの進捗状況や製品の生産状況に応じて、予算消化率や達成度などをリアルタイムに近い形で確認することができます。これにより、予算オーバーの兆候や計画からの乖離を早期に検知し、迅速な対応を促します。
例えば、ある建設現場では、原価管理システムの予算実績管理画面を毎日確認することで、特定の資材費が予算を上回りそうになっていることにいち早く気づき、代替資材の検討や発注先との交渉を行うことで、最終的な予算超過を最小限に抑えることができました。このようなタイムリーな管理は、Excelベースではなかなか難しいものです。
差異分析機能
単に予算と実績の差額を示すだけでなく、なぜその差異が発生したのか、その要因を掘り下げて分析する機能が「差異分析機能」です。例えば、標準原価計算を採用している企業であれば、実際原価との間に生じた価格差異(材料の購入価格が標準と異なった、など)や数量差異(材料の使用量が標準と異なった、作業時間が標準と異なった、など)を自動的に計算し、その内訳を表示します。
私が支援したある機械部品メーカーH社様では、原価管理システムの差異分析機能を活用し、ある製品の労務費が常に標準よりも高いことに気づきました。詳しく調べてみると、特定の工程で熟練作業者の不足から新人作業者が多く割り当てられており、作業効率が想定よりも低いことが判明しました。この分析結果をもとに、H社様は新人向けの集中的な研修プログラムを実施し、併せて作業手順書の見直しを行うことで、数ヶ月後にはその工程の労務費差異を大幅に縮小することに成功しました。このように、差異分析機能は、問題点の根本原因を特定し、具体的な改善策を導き出すための強力なツールとなります。
レポート出力機能
予算実績対比表、差異分析報告書、製品別損益一覧表、部門別原価報告書、プロジェクト別採算表など、原価管理に必要な各種帳票やレポートを、定型的なフォーマットで、あるいはユーザーがカスタマイズした形式で出力する機能です。多くの原価管理システムでは、これらのレポートをExcel形式やPDF形式で出力したり、BIツールと連携してより高度なグラフやダッシュボードとして可視化したりすることが可能です。
これにより、経営層は企業全体の収益状況やコスト構造を迅速に把握し、的確な意思決定を行うことができます。また、各部門の管理者は、自部門の業績や課題を具体的なデータで確認し、担当者レベルでは、日々の業務改善に役立つ情報を得ることができます。レポートの種類やカスタマイズの柔軟性、そして見やすさや分かりやすさが、原価管理システム選定の際のポイントの一つとなります。
これらの機能を効果的に活用することで、企業は「計画を立て(予算設定)、実行し(実績把握)、結果を検証し(差異分析)、改善する(アクション)」という原価管理のPDCAサイクルをスムーズに回せるようになります。これにより、継続的な業務改善と収益性の向上が期待できるのです。
4.4. 販売管理・生産管理・会計システム等との連携機能
原価管理システムは、それ単独で全てのデータを抱え込み、独立して機能するわけではありません。むしろ、企業内で既に稼働している他の業務システム(販売管理 システム、生産管理 システム、購買管理 システム、勤怠管理
システム、会計システムなど)と密接に連携することで、その真価を最大限に発揮します。これらの基幹システムとのスムーズなデータ連携機能は、原価管理業務の効率化と精度向上に不可欠であり、システム選定における極めて重要なポイントとなります。
結論として、他の業務システムとの連携機能は、データ入力の二度手間を排除し、リアルタイムな情報共有を促進し、企業全体の情報システムの一貫性と効率性を高めるために不可欠です。
なぜシステム連携がそれほど重要なのでしょうか。その主な理由と具体的な連携イメージは以下の通りです。
データ入力作業の自動化と効率化
原価計算に必要なデータの多くは、既に他の業務システムに存在しています。例えば、製品の受注数量や売上金額は販売管理システムに、材料の仕入れ単価や在庫数量は購買管理システムや在庫管理システムに、従業員の作業時間は勤怠管理システムや生産管理システム(製造実行システム:MES)に、実際に支払われた経費の情報は会計システムに記録されています。これらのデータを原価管理システムに再度手入力するのは、膨大な手間と時間がかかるだけでなく、入力ミスを誘発する原因にもなります。
システム連携機能があれば、これらのデータを自動的に、あるいは簡単な操作で原価管理システムに取り込むことが可能になります。これにより、データ入力の負担が劇的に軽減され、担当者はより付加価値の高い分析業務に集中できるようになります。
私が支援したある自動車部品メーカーI社様では、原価管理システム導入前は、各システムから出力したExcelファイルを担当者が手作業で集計し、原価計算用のExcelシートに転記するという煩雑な作業を毎月行っていました。システム導入と同時に主要な基幹システムとのAPI連携を構築した結果、このデータ収集・転記作業がほぼゼロになり、月次決算の早期化にも大きく貢献しました。
データのリアルタイム性と一貫性の確保
システム連携により、各業務システムで発生した情報が、タイムラグなく原価管理システムに反映されるようになります(あるいは定期的なバッチ処理で同期されます)。これにより、常に最新の情報に基づいた原価計算や分析が可能となり、経営判断の迅速化に繋がります。また、複数のシステム間でデータが二重、三重に存在することによる不整合や矛盾を防ぎ、企業全体としてのデータの一貫性と信頼性を高めることができます。
例えば、販売管理 システムで受注情報が更新されれば、それが速やかに原価管理システムの生産計画や原価予測に反映される、といった具合です。
マスタデータの一元管理
品目マスター、顧客マスター、仕入先マスター、部門マスターなど、多くの業務システムで共通して利用されるマスターデータは、一元的に管理されることが理想です。原価管理システムが他のシステムとマスターデータを共有・同期する機能を備えていれば、マスターメンテナンスの手間が軽減されるだけでなく、データの不整合を防ぐことができます。例えば、会計システムの勘定科目マスターや部門マスターを原価管理システムと同期できれば、経費データの取り込みや部門別原価計算がスムーズに行えます。
原価管理システムを選定する際には、自社で既に利用している基幹システムとの連携実績が豊富か、標準的なAPI(Application Programming Interface)が用意されているか、あるいはCSVファイルなど汎用的な形式でのデータ連携が容易に行えるか、といった点を十分に確認することが重要です。特に、企業の基幹となるERP(Enterprise Resource Planning:統合基幹業務システム)の一部として原価管理機能が提供されている場合は、会計、販売、生産などのモジュールと最初から緊密に連携しているため、データ連携の課題は発生しにくいというメリットがあります。一方で、独立した専門特化型の原価管理システムを導入する場合は、既存システムとの連携の可否やその方法、コストなどを慎重に検討する必要があります。スムーズなシステム連携は、原価管理システム導入の成功を左右する大きなポイントの一つです。
4.5.【業種別】特に注目したい機能(製造業、建設業など)
これまで述べてきた主要機能は、多くの業種で共通して重要となるものですが、業種特有の業務プロセスや管理ポイントに対応するために、特定の業種向けに強化された機能や、特に注目すべき機能が存在します。ここでは、私たちのお客様の多くを占める「製造業」と、プロジェクト単位での原価管理が不可欠な「建設業」を例に挙げ、それぞれの業種で原価管理システムを選ぶ際に特に注目したい機能について解説します。
結論として、自社の業種特性を深く理解し、それに特化した機能や柔軟な設定が可能な原価管理システムを選ぶことが、導入効果を最大化する上で不可欠です。
1. 製造業向けに特に注目したい機能
製造業、特に多品種少量生産を営む中小製造業では、製品ごとの正確な原価把握と、生産プロセス全体の効率化が課題となります。そのため、以下のような機能が重要になります。
詳細な部品表(BOM)管理機能と連携
製品の設計図とも言える部品表(BOM)は、材料費計算の基礎となります。原価管理システムが、複数階層のBOMや設計変更に柔軟に対応できるか、また、BOMの変更が即座に標準原価や実際原価計算に反映されるかは非常に重要です。PDM(製品データ管理)システムやCADシステムとBOM情報を連携できる製品もあります。
工程別原価計算機能
製造プロセスを複数の工程に分け、各工程で発生する加工費や労務費を把握・集計する機能です。これにより、どの工程にコストが集中しているのか、どの工程にボトルネックがあるのかを特定し、生産性向上やコスト削減のポイントを明確にすることができます。仕掛品評価にも役立ちます。
ロット別原価管理機能
同じ製品であっても、生産ロットによって材料の仕入れ単価や作業条件が異なる場合があります。ロットごとに原価を追跡・管理することで、より正確な原価把握とトレーサビリティの確保に繋がります。特に食品業界や医薬品業界など、品質管理やロット追跡が重要な業種で有効です。
実際原価と標準原価の精緻な差異分析機能
製造業では、標準原価を設定し、実際原価との差異を分析することでコスト管理を行うことが一般的です。材料価格差異、材料数量差異、作業時間差異、賃率差異など、差異の要因を詳細に分析できる機能が求められます。
生産管理システ、MESとの連携
生産計画、製造実績(良品数、不良品数、作業時間など)、機械の稼働状況といった生産現場のリアルタイムな情報を原価管理システムにスムーズに取り込むための連携機能は、実際原価の精度向上と効率化に不可欠です。
ある電子機器メーカーJ社様は、多品種少量生産で製品のライフサイクルも短いため、頻繁な設計変更と部品変更に原価計算が追いつかないという課題を抱えていました。詳細なBOM管理機能とPDMシステム連携機能を備えた原価管理システムを導入したことで、設計変更情報が即座に原価に反映され、常に最新の原価に基づいた見積もりや採算判断が可能となり、新製品の市場投入スピード向上にも貢献しました。
2. 建設業向けに特に注目したい機能
建設業では、個別の工事プロジェクト単位での原価管理が基本となり、実行予算の精度と進捗に合わせたタイムリーな原価把握が極めて重要です。
工事台帳管理機能(工事原価管理)
工事ごとに、材料費、労務費、外注費、経費などの原価要素を詳細に集計・管理する機能です。実行予算と実績を対比し、工事の進捗度に応じた原価発生状況や利益状況をリアルタイムに把握することが求められます。
実行予算管理機能の充実
詳細な費目ごとに実行予算を編成し、承認ワークフローを経て管理する機能。過去の類似工事の予算を流用したり、Excelで作成した予算データをインポートしたりできる柔軟性も重要です。予算変更の履歴管理機能も不可欠です。
発注・支払管理との連携
実際に業者に発注した金額や支払った金額を、工事原価として正確に紐付けて計上するための機能。購買システムや会計システムとの連携が重要になります。
工事進捗度管理機能
工事の進捗度合いに応じて、出来高や原価を評価し、予定通りに進んでいるか、コストが予算内に収まっているかを管理する機能。これにより、早期に問題を発見し、対策を講じることができます。
労務費管理の精度
建設現場では、自社社員だけでなく、協力会社の作業員も多く関わります。誰がどの工事にどれだけ従事したかを正確に把握し、労務費を適切に按分・集計する機能が求められます。出面管理システムとの連携も有効です。
豊富な帳票出力
工事原価報告書、実行予算実績対比表、工事未成工事支出金一覧など、建設業特有の管理帳票を標準で出力できるか、あるいはカスタマイズして作成できるかがポイントです。「どっと原価シリーズ」のような建設業特化型の原価管理システムは、これらの機能が充実している傾向にあります。
これらの業種特化機能は、その業界の商習慣や法制度、特有の管理ポイントに深く根ざしているため、原価管理システムを選定する際には、自社の業種に強みを持つベンダーや製品を検討することが、導入後のミスマッチを防ぎ、効果を最大限に引き出すための近道となります。自社の業務を詳細に分析し、本当に必要な機能は何かを慎重に見極めることが何よりも大切です。
5. 原価管理システムのタイプ別特徴と比較:自社に合う型は?
原価管理システムの導入を検討する際、その機能だけでなく、「どのような提供形態のシステムを選ぶか」という点も非常に重要な選択肢となります。原価管理システムには、大きく分けてクラウド型(SaaS)、オンプレミス型といった提供環境の違いや、ERP一体型、専用特化型といったシステム構成の違い、さらにはパッケージ型、スクラッチ開発といった開発方法の違いなど、いくつかのタイプが存在します。それぞれのタイプには独自の特徴があり、メリット・デメリットも異なります。自社の規模、予算、IT環境、セキュリティポリシー、そして将来の事業展開などを総合的に考慮し、最適なタイプを選ぶことが、原価管理システム導入を成功に導くための鍵となります。この章では、主要な原価管理システムのタイプ別の特徴を比較しながら、中小製造業の皆様が自社に最適な「型」を見つけるためのポイントを解説します。
5.1.クラウド型(SaaS)システムの特徴・メリット・デメリット
近年、多くの業務システムで主流となりつつあるのが「クラウド型(SaaS:Software as a
Service)」の原価管理システムです。これは、システムベンダーがインターネット経由で原価管理機能をサービスとして提供する形態で、ユーザーは自社でサーバーなどのITインフラを構築・運用する必要がありません。ブラウザとインターネット接続環境があれば、場所やデバイスを問わずにシステムを利用できる手軽さが大きな特徴です。
結論として、クラウド型原価管理システムは、初期費用を抑えて迅速に導入でき、運用負荷も軽減できるため、特にIT専門の担当者が少ない中小企業や、柔軟な働き方に対応したい企業にとって魅力的な選択肢です。
クラウド型原価管理システムの主なメリット:
初期費用の抑制と迅速な導入が可能
自社でサーバーを購入したり、ソフトウェアをインストールしたりする必要がないため、オンプレミス型に比べて導入にかかる初期費用を大幅に抑えることができます。多くの場合、アカウントを契約し、基本的な設定を済ませればすぐに利用を開始できるため、導入期間も短縮できます。
ある製造業K社様は、資金調達後すぐにでも原価管理を始めたかったため、初期コストが低く、数週間で稼働開始できたクラウド型原価管理システムを採用し、迅速な事業立ち上げに成功しました。このスピード感はクラウド型ならではのメリットと言えるでしょう。
運用・保守の負荷軽減
詳細な費目ごとに実行予算を編成し、承認ワークフローを経て管理する機能。過去の類似工事の予算を流用したり、Excelで作成した予算データをインポートしたりできる柔軟性も重要です。予算変更の履歴管理機能も不可欠です。
場所やデバイスを選ばない柔軟なアクセス
インターネット接続環境さえあれば、オフィスだけでなく、自宅や出張先など、どこからでもシステムにアクセスできます。また、パソコンだけでなく、タブレットやスマートフォンからの利用に対応しているサービスも増えています。これにより、経営者が外出先で最新の原価情報を確認したり、工場長が現場でタブレットを使いながら実績入力をしたりといった、より柔軟で効率的な働き方が実現できます。
常に最新機能を利用可能・拡張性が高い
クラウド型システムは、ベンダーによって定期的に機能改善やセキュリティ強化のためのアップデートが自動的に行われるため、ユーザーは常に最新バージョンのシステムを利用できます。また、ユーザー数や利用する機能の増減、ストレージ容量の追加など、企業の成長や事業変化に合わせて柔軟にサービス内容をスケールアップ/ダウンしやすい点もメリットです。
災害時の事業継続性(BCP)向上
データはベンダーが管理する堅牢なデータセンターに保管されるため、自社でサーバーを運用する場合に比べて、地震や火災といった災害時におけるデータ消失のリスクを低減できます。これにより、事業継続計画(BCP)の観点からも安心感が増します。
クラウド型原価管理システムの主なデメリット・注意点:
カスタマイズの制約
クラウド型システムは、多くの企業が共通で利用することを前提としているため、オンプレミス型に比べて、自社の特殊な業務フローに合わせた大幅なカスタマイズや独自機能の追加が難しい場合があります。設定範囲内での調整は可能ですが、それ以上の個別対応は限定的となることが多いです。そのため、システムに自社の業務を合わせる、という発想の転換が求められることもあります。
インターネット接続が必須
システムの利用には安定したインターネット接続環境が不可欠です。オフライン環境では基本的に利用できません。また、通信速度が遅い環境では、システムのレスポンスが悪影響を受ける可能性もあります。
セキュリティへの懸念(データ管理)
企業の重要な原価データを外部のサーバーに預けることになるため、セキュリティに対する懸念を持つ企業も少なくありません。サービス選定時には、ベンダーがどのようなセキュリティ対策(データ暗号化、アクセス制御、不正侵入防止など)を講じているか、データセンターの信頼性はどうか、国際的なセキュリティ認証を取得しているかなどを十分に確認する必要があります。
月額(年額)費用の継続発生
初期費用は抑えられますが、利用している限り月額または年額のサービス利用料が継続的に発生します。長期間利用する場合、オンプレミス型よりも総コストが高くなる可能性も考慮に入れる必要があります。ユーザー数やデータ量に応じて費用が変動する料金体系の場合は、将来的なコスト増も見込んでおく必要があります。
サービス終了のリスク
万が一、ベンダーがサービス提供を終了してしまった場合、システムが利用できなくなるリスクがゼロではありません。ベンダーの経営安定性や事業継続性、サービス移行に関するポリシーなども、選定時のポイントとして考慮しておくとよいでしょう。
クラウド型は、特にIT投資を抑えたい、専門のIT担当者が不足している、短期間でシステムを稼働させたい、テレワークなど柔軟な働き方を推進したい、といったニーズを持つ中小製造業にとって、有力な選択肢の一つです。自社の業務プロセスが標準的なものであれば、大きなメリットを享受できるでしょう。
5.2.オンプレミス型システムの特徴・メリット・デメリット
「オンプレミス型」の原価管理システムは、自社のサーバーやコンピューターにソフトウェアをインストールし、自社内でシステムを構築・運用する従来ながらの提供形態です。クラウド型の普及が進む中でも、セキュリティポリシーや既存システムとの連携、大幅なカスタマイズの必要性などから、依然としてオンプレミス型を選択する企業も少なくありません。
結論として、オンプレミス型原価管理システムは、初期投資と運用負荷は高めですが、自社の要件に合わせた高度なカスタマイズが可能で、セキュリティを自社管理下に置けるため、独自の業務プロセスを持つ企業や、機密性の高い情報を扱う企業に適しています。
オンプレミス型原価管理システムの主なメリット:
高度なカスタマイズ性と柔軟性
自社内にシステムを構築するため、自社の特有な業務フローや管理項目に合わせて、システムを大幅にカスタマイズしたり、独自の機能を追加したりすることが比較的容易です。クラウド型では対応が難しい複雑な要件にも柔軟に対応できる点が最大のメリットと言えるでしょう。
ある特殊機械メーカーL社様は、非常に複雑な原価計算ロジックと、独自の帳票フォーマットが多数存在したため、オンプレミス型を選択し、徹底的なカスタマイズを行うことで、現場の要求をほぼ完全に満たす原価管理システムを構築しました。
セキュリティの自社管理
システムやデータを全て自社の管理下に置くため、外部のネットワークから隔離したクローズドな環境で運用するなど、自社のセキュリティポリシーに合わせた厳格なセキュリティ対策を講じることが可能です。特に機密性の高い原価情報や顧客情報を扱う企業にとっては、この点は大きな安心材料となります。
既存システムとの連携のしやすさ(場合による)
自社内に他のオンプレミス型の基幹システム(ERP、生産管理、会計など)が既に稼働している場合、同じネットワーク環境内で直接的なデータ連携を構築しやすく、より密接でリアルタイムな連携が実現できることがあります。ただし、連携先のシステムや原価管理システムの仕様に大きく左右されるため、一概には言えません。
ランニングコストの変動が少ない(買い切り型の場合)
ソフトウェアライセンスを買い取る形式の場合、初期費用は高額になりますが、月々の利用料は発生しないか、あるいは保守費用のみとなるため、長期的に見るとランニングコストを抑えられる可能性があります。(ただし、サーバー維持費や専任のIT担当者の人件費は別途考慮する必要があります。)
オフライン環境でも利用可能
インターネット接続に依存しないため、万が一インターネット回線に障害が発生しても、社内ネットワークが正常であればシステムを継続して利用できます。
オンプレミス型原価管理システムの主なデメリット・注意点:
高額な初期費用と長期の導入期間
サーバーやネットワーク機器の購入・構築費用、ソフトウェアライセンス費用、カスタマイズ費用など、導入には多額の初期投資が必要となります。また、システム構築やカスタマイズ、テストなどに時間がかかるため、導入期間もクラウド型に比べて長期化する傾向があります。
運用・保守の負荷と専門知識の必要性
サーバーの管理、ソフトウェアのアップデート、セキュリティ対策、障害対応、バックアップ作業など、システムの運用・保守は全て自社で行う必要があります。これには専門的な知識を持つIT担当者が不可欠であり、その人件費も考慮しなければなりません。これらの運用負荷は中小企業にとっては大きな負担となり得ます。
災害時のリスクとBCP対策の必要性
自社内にサーバーを設置する場合、地震や火災、水害などの災害によってシステムが物理的に損傷したり、データが消失したりするリスクがあります。そのため、遠隔地へのバックアップや冗長構成の構築など、自社でBCP対策を講じる必要があります。
機能追加やバージョンアップのコストと手間
新しい機能を追加したり、システムをバージョンアップしたりする際には、追加の費用や作業が発生することが一般的です。クラウド型のように自動的に最新機能が提供されるわけではありません。
場所やデバイスの制約
基本的には社内ネットワークからのアクセスが前提となるため、外出先や自宅からシステムを利用するには、VPN接続などの別途の仕組みが必要となり、クラウド型ほどの柔軟性はありません。
オンプレミス型は、予算やITリソースに比較的余裕があり、自社独自の業務プロセスへの適合性や、高度なセキュリティ要件を重視する中小製造業にとって検討の価値があります。特に、既存の基幹システムとの密な連携や、法規制などでデータの外部保管が難しい場合などに選択されることがあります。
5.3.ERP一体型と専用特化型システムの違いと選び方
原価管理システムを選ぶ際、そのシステムが企業の他の業務システムとどのような関係性を持つか、という観点も非常に重要です。この観点からは、大きく「ERP(Enterprise Resource Planning:統合基幹業務システム)一体型」と「専用特化型」の二つのタイプに分類できます。それぞれのタイプが持つ特徴を理解し、自社の情報システム全体の構想や原価管理に求める専門性の度合いなどを考慮して選択することが求められます。
結論として、ERP一体型はデータ連携の容易さと全社的な情報統合に強みがあり、専用特化型は原価管理機能の専門性と深掘りに強みがあります。どちらを選ぶかは、企業のIT戦略や業務特性によって異なります。
ERP一体型原価管理システムの特徴:
ERPとは、会計、販売、購買、在庫、生産、人事など、企業の主要な基幹業務を統合的に管理するシステムのことです。ERP一体型の原価管理システムは、このERPパッケージの一つのモジュール(機能部品)として原価管理機能が提供されているものです。
•メリット:
データ連携の優位性
会計、販売、生産などの他モジュールと最初から密接にデータ連携がなされているため、原価計算に必要な情報(売上実績、生産実績、材料消費実績、経費情報など)をスムーズかつリアルタイムに収集・活用できます。データの二重入力や不整合が起こりにくく、業務効率化とデータ精度向上に大きく貢献します。
全社的な情報の一元管理
原価情報だけでなく、企業活動全体の情報が単一のシステム上で一元管理されるため、経営状況の全体像を把握しやすくなります。原価と他の経営指標との関連分析なども容易に行えます。
運用・保守の効率化(場合による)
複数の個別システムをバラバラに運用するよりも、ERPとして一つのシステム基盤上で運用することで、IT管理の負荷が軽減される可能性があります。
例えば、ある中堅製造業M社様は、以前は販売、生産、会計、原価管理がそれぞれ独立したシステムで稼働しており、データ連携に多くの手間と時間を費やしていました。ERP一体型の原価管理システムを導入したことで、これらのデータがシームレスに繋がり、月次決算が大幅に早期化されるとともに、原価情報に基づいた生産計画の最適化も実現できました。
•デメリット・注意点:
導入コストと期間
一般的にERPの導入は大規模なプロジェクトとなるため、初期費用が高額になり、導入期間も長期化する傾向があります。
機能の網羅性と専門性のバランス
ERPは幅広い業務をカバーするため、原価管理機能については、専用特化型システムに比べて機能の深さや細やかさ、特定の業種への対応度合いが劣る場合があります。自社が求める原価管理のレベルとERPの機能がマッチするかを慎重に見極める必要があります。
システム全体への影響
原価管理モジュールだけでなく、ERPシステム全体の仕様や操作性に習熟する必要があり、社員教育にも時間がかかります。また、一部のモジュールを変更することがシステム全体に影響を及ぼす可能性も考慮しなければなりません。
専用特化型原価管理システムの特徴:
専用特化型の原価管理システムは、その名の通り、原価管理機能に特化して開発されたシステムです。原価計算や分析機能が非常に充実しており、特定の業種や生産形態に強みを持つ製品も多く存在します。
•メリット:
高度で専門的な機能
原価管理に特化しているため、複雑な配賦ロジック、詳細な差異分析、高度な原価シミュレーションなど、専門性の高い機能が豊富に搭載されていることが多いです。特定の業種(例えば、建設業向けの「どっと原価シリーズ」や、多品種少量生産の製造業向けの特定のシステムなど)のニーズにきめ細かく対応した製品もあります。
比較的柔軟な導入とカスタマイズ
ERP全体を導入するのに比べて、導入範囲が限定されるため、比較的短期間かつ低コストで導入できる場合があります。また、特定の機能に絞ってカスタマイズを行いやすいこともあります。
既存システムとの連携でベストオブブリードを実現可能
会計システムはA社、販売管理システムはB社、そして原価管理システムはC社の専用特化型、といったように、各業務領域で最適なシステムを選択し、それらをAPIなどで連携させる「ベストオブブリード」という考え方にも適しています。
以前、私が相談を受けたあるニッチな市場で高いシェアを持つ部品メーカーN社様は、非常にユニークな製造プロセスと原価計算方法を採っていました。汎用的なERPでは対応が難しかったため、自社の特殊な要件にきめ細かく対応できる専用特化型の原価管理システムを選定し、一部カスタマイズを加えることで、理想的な原価管理を実現しました。
•デメリット・注意点:
他システムとの連携が必須
専用特化型であるため、原価計算に必要なデータを他の基幹システム(販売、生産、会計など)から取得するための連携が不可欠です。この連携の設計や構築に手間やコストがかかる場合があり、連携がスムーズに行えないとシステムの効果が半減してしまいます。
情報が分散する可能性
企業全体の情報が複数のシステムに分散するため、データの一元管理や横断的な分析がERP一体型に比べて難しくなる可能性があります。
複数のベンダーとのやり取り
各システムのベンダーが異なる場合、システム間のトラブル発生時の原因究明や責任の所在が曖昧になるリスクや、運用保守の窓口が複数になる煩雑さがあります。
【選び方のポイント】
ERP一体型が適しているのは、これから基幹システム全体を刷新したい、あるいは既に同ベンダーのERPを一部利用しており、全社的な情報統合と業務効率化を最優先で目指す企業です。一方、専用特化型は、既存の基幹システムはそのまま活かしつつ、原価管理機能だけを高度化したい、あるいは特定の業種や業務に特有の複雑な原価管理要件がある企業に適しています。自社のIT戦略、予算、求める機能の専門性、既存システムとの親和性などを総合的に比較検討し、最適なタイプを選択しましょう。
5.4.パッケージ型とスクラッチ開発の比較ポイント
原価管理システムを導入する際の開発方法という観点からは、「パッケージ型」と「スクラッチ開発」という二つのアプローチが考えられます。パッケージ型は、既製品のソフトウェアを導入する方法であり、スクラッチ開発は、自社の要件に合わせてオーダーメイドでシステムをゼロから開発する方法です。どちらの方法にも一長一短があり、自社の状況に合わせて慎重に選択する必要があります。
結論として、パッケージ型はコストと導入期間を抑えたい場合に、スクラッチ開発は独自の複雑な要件や他社との差別化をシステムで実現したい場合に適した選択肢ですが、多くの中小企業にとってはパッケージ型のカスタマイズが現実的な落としどころとなることが多いです。
パッケージ型原価管理システムの特徴:
パッケージ型システムは、多くの企業で共通して必要とされる標準的な原価管理機能をあらかじめ搭載した既製のソフトウェア製品です。ベンダーが開発・販売しており、ユーザーはライセンスを購入またはクラウドサービスとして契約して利用します。
•メリット:
導入コストと期間の抑制
既に完成されたシステムであるため、ゼロから開発するスクラッチ開発に比べて、一般的に導入コストを大幅に抑えることができ、導入期間も短縮できます。
機能の網羅性と安定性
多くの企業での利用実績があるため、機能がある程度網羅されており、バグなども比較的少なく、システムの品質や安定性が期待できます。業界標準のベストプラクティスが取り入れられていることもあります。
豊富な導入事例とノウハウ
多くの導入事例があるため、自社と似たような企業での活用方法や導入時の注意点などを参考にすることができます。ベンダーやコンサルタントも導入ノウハウを蓄積しています。
バージョンアップによる機能向上
ベンダーによる定期的なバージョンアップによって、新しい機能が追加されたり、既存機能が改善されたりするメリットがあります。
•デメリット・注意点:
カスタマイズの限界
自社の独自の業務フローや特殊な要件に完全に合致しない場合があります。ある程度の設定変更やアドオン開発(追加機能の開発)が可能なパッケージもありますが、スクラッチ開発ほどの柔軟性はありません。システムに業務を合わせる必要が生じることもあります。
不要な機能の存在
自社にとっては使わない機能が多く搭載されている場合があり、それが操作性を複雑にしたり、システムを重くしたりする可能性があります。
ベンダーへの依存
システムの将来性やサポートは、提供元であるベンダーの方針に大きく左右されます。
スクラッチ開発(オーダーメイド開発)の特徴:
スクラッチ開発は、自社の特定の要件や業務プロセスに合わせて、原価管理システムを完全にオーダーメイドでゼロから設計・開発する方法です。
•メリット:
完全な要件合致と高い柔軟性
自社の独自の業務フロー、管理項目、帳票フォーマット、原価計算ロジックなどを100%反映した、まさに自社専用のシステムを構築できます。他社にはない競争優位性をシステムで実現したい場合に有効です。
必要な機能のみを実装
自社にとって本当に必要な機能だけを厳選して実装するため、無駄がなく、操作性もシンプルにできる可能性があります。
既存システムとの最適化された連携
既存の他の社内システムとの連携も、自社の環境に合わせて最適な形で設計・構築できます。
•デメリット・注意点:
非常に高額な開発費用
オーダーメイドであるため、パッケージ型に比べて開発費用が格段に高額になります。要件定義から設計、開発、テストまで、多くの工数と専門技術が必要です。
長期の開発期間
ゼロから作り上げるため、システムが完成し、稼働するまでに長い期間(数ヶ月~数年単位)を要します。市場の変化に迅速に対応したい場合には不向きです。
開発プロジェクトの失敗リスク
要件定義が曖昧だったり、開発会社の技術力が不足していたりすると、プロジェクトが頓挫したり、期待した品質のシステムが完成しなかったりするリスクがあります。企業側にシステム開発に関する深い知識やプロジェクト管理能力が求められます。
運用・保守体制の確立が必須
完成したシステムの運用・保守は全て自社で行うか、開発会社と別途保守契約を結ぶ必要があります。システムの仕様を熟知した担当者が社内にいないと、障害発生時や仕様変更時に困る可能性があります。
【選び方のポイント】
多くの中小製造業にとっては、ゼロからのスクラッチ開発はコストやリスクの観点からハードルが高いのが実情です。まずは、自社の業種や規模、主要な業務要件に適合するパッケージ型原価管理システムをいくつかピックアップし、デモンストレーションを受けたり、トライアルを試したりしながら、機能の適合度やカスタマイズの柔軟性を比較検討するのが現実的なアプローチです。その上で、どうしてもパッケージでは対応できない重要な要件がある場合に限り、その部分的なアドオン開発や、限定的な範囲でのスクラッチ開発を検討するというのが賢明な選択と言えるでしょう。
私がよくアドバイスするのは、「システムに100%合わせる必要もなければ、100%自社に合わせようと固執する必要もない」ということです。パッケージ型の標準機能を最大限に活かしつつ、本当に譲れないポイントだけをカスタマイズで対応する、あるいは、システム導入を機に非効率な業務プロセス自体を見直す、といったバランス感覚が重要です。
6.【2025年最新版】失敗しない原価管理システムの選び方:7つの重要ポイント
原価管理システムの導入は、企業の経営体質を強化し、利益構造を改善するための重要な投資です。しかし、市場には多種多様な原価管理システムが存在し、「どの製品を選ぶべきか」「自社に本当に合ったシステムは何か」と頭を悩ませている経営者様やご担当者様も少なくないでしょう。システム選定の失敗は、期待した効果が得られないばかりか、無駄なコストと時間を費やし、現場の混乱を招くことにもなりかねません。そこでこの章では、私たちコンサルティング会社が数多くの中小製造業のシステム導入を支援してきた経験と、2025年現在の最新の市場動向を踏まえ、「失敗しない原価管理システムの選び方」として、特に重要となる7つのポイントを徹底的に解説していきます。これらのポイントを押さえることで、貴社にとって最適な一選びが可能になるはずです。
6.1. ポイント1:自社の課題と導入目的を明確化する(現状分析)
原価管理システム選定における最も重要な最初のステップは、「なぜ原価管理システムを導入するのか?」という根本的な問いに明確な答えを出すことです。つまり、自社が現在抱えている原価管理上の具体的な課題を洗い出し、システム導入によって何を達成したいのか、その「導入目的」を明確に定義することが不可欠です。これが曖昧なままシステム選定を進めてしまうと、多機能で高価なシステムを導入したものの、結局使わない機能ばかりだったり、本当に解決したかった課題が置き去りにされたりする結果を招きかねません。
結論として、原価管理システム導入の成功は、導入前に自社の現状課題を徹底的に分析し、システムによって達成したい具体的な目的・目標を社内で共有・合意形成することから始まります。
まず、現状分析として、以下のような点を具体的に洗い出してみましょう。
現在の原価計算・管理方法
Excelで管理しているのか、手作業が中心なのか、あるいは旧式のオフコンシステムを利用しているのか。
抱えている問題点
o 原価計算に時間がかかりすぎている(月次決算の遅れなど)。
o 製品ごとの正確な原価が把握できていない(どんぶり勘定になっている)。
o データ入力の手間が大きい、ミスが多い。
o リアルタイムな原価情報が取得できず、経営判断が遅れる。
o 間接費の配賦基準が曖昧で、原価の信頼性に欠ける。
o 予算と実績の差異分析が十分にできていない。
o 採算の悪い製品やプロジェクトが見過ごされている。
o 原価情報が経営戦略に活かされていない。
o 属人化しており、担当者がいないと業務が滞る。
課題の優先順位
上記のような課題の中から、特に緊急度や重要度の高いものは何か、優先順位をつけます。
次に、これらの課題を踏まえ、原価管理システム導入によって達成したい「導入目的」を具体的に設定します。目的は、定性的なものだけでなく、可能な限り定量的な目標(KPI:重要業績評価指標)を伴うことが望ましいです。
例1:原価計算業務の効率化
o 定性目的:データ入力や集計作業の手間を削減し、担当者の負担を軽減する。
o 定量目標:月次の原価計算にかかる時間を現状の〇〇時間から〇〇時間へ短縮する(例:50%削減)。データ入力ミスを〇%削減する。
例2:正確な製品別原価の把握
o 定性目的:全ての製品について、信頼性の高い原価情報をタイムリーに把握する。
o 定量目標:製品別損益を週次で把握できるようにする。原価差異を±〇%以内に抑える。
例3:経営判断の迅速化・高度化
o 定性目的:原価情報を活用し、データに基づいた迅速な経営判断を行う。
o 定量目標:不採算製品の特定と対策実行までの期間を〇ヶ月短縮する。新製品の価格設定における原価ベースのシミュレーションを必ず実施する。
私が以前コンサルティングで関わったある電子部品メーカーP社様は、「とにかく新しいシステムが欲しい」という漠然とした要望でシステム選定を開始しようとしていました。しかし、私たちが現状の業務ヒアリングと課題の掘り下げを徹底的に行った結果、「多品種少量生産における個々の製品の正確な原価が全く見えておらず、赤字受注を繰り返している可能性が高い」という深刻な課題が浮き彫りになりました。そこで、導入目的を「製品別実際原価の精度向上と、週次での損益把握体制の確立」と明確に定めました。この明確な目的があったからこそ、P社様は数ある原価管理システムの中から、自社の生産形態に最適な実際原価計算機能とリアルタイム分析機能に優れた製品を選択でき、導入後には期待通りの効果を上げることができました。
導入目的が明確になれば、おのずとシステムに求めるべき機能の優先順位も見えてきます。この最初のポイントを疎かにせず、時間をかけてでも社内で十分に議論し、合意形成を行うことが、失敗しない原価管理システム選びの最も重要な土台となるのです。2025年現在、DX推進が叫ばれる中で、システム導入そのものが目的化しないよう、常に「何のために導入するのか」を問い続ける姿勢が求められます。
6.2.ポイント2:企業規模や業種(製造業・建設業など)への適合性を見極める
自社の課題と導入目的が明確になったら、次に検討すべきポイントは、「システムが自社の企業規模や業種特性に適合しているか」という点です。大企業向けの高機能で複雑な原価管理システムが、必ずしも中小企業にとって最適とは限りません。また、業種によって原価管理のポイントや求められる機能も大きく異なります。特に、私たちのお客様である多品種少量生産の製造業や、プロジェクト単位での管理が不可欠な建設業などでは、その業種特有のニーズにきめ細かく対応できるシステムを選ぶことが成功の鍵となります。
結論として、企業の成長ステージやリソース、そして業種特有の商習慣や管理手法にマッチした原価管理システムを選ぶことが、導入後のスムーズな運用と効果の最大化につながります。
まず、企業規模への適合性についてです。
中小企業の場合
o コストパフォーマンス
予算が限られていることが多いため、初期費用やランニングコストを抑えられるクラウド型(SaaS)の原価管理システムが有力な選択肢となります。
o 操作の容易さと導入のしやすさ
専門のIT担当者が少ないケースが多いため、直感的に操作でき、導入や設定が比較的簡単なシステムが望ましいです。手厚い導入サポートや分かりやすいマニュアルが提供されているかも確認ポイントです。
o 必要十分な機能
大企業向けのような過剰な機能は不要な場合が多く、自社の業務に本当に必要な機能を過不足なく備えているかを見極めることが重要です。
中堅・大企業の場合
o 拡張性と柔軟性
将来的な事業拡大や組織変更にも対応できる拡張性や、複雑な業務プロセスに合わせたカスタマイズの柔軟性が求められます。
o 内部統制への対応
監査対応やセキュリティ要件など、内部統制を支える機能(ログ管理、権限設定など)が充実しているかも重要なポイントです。
o 多言語・多通貨対応(グローバル企業の場合)
海外拠点を持つ企業の場合は、多言語・多通貨に対応している原価管理システムが必要になります。
次に、業種への適合性です。ここでは特に製造業と建設業に焦点を当てますが、他の業種でも同様に、自社の業種特性を考慮することが重要です。
6.2.1.製造業向けシステムの選び方のポイントと機能要件
製造業、特に多品種少量生産や個別受注生産を特徴とする中小製造業においては、製品ごとの正確な原価把握と、生産プロセスの効率化が原価管理の核心となります。2025年現在、サプライチェーンの不安定化や顧客ニーズの多様化は、この課題をより一層複雑にしています。したがって、原価管理システム選定時には、以下のような製造業特有のポイントと機能要件を慎重に確認する必要があります。
精緻な部品表(BOM)管理機能と設計変更への対応
製造業の原価計算の基礎となるのは、製品を構成する部品や原材料の一覧である部品表(BOM)です。原価管理システムが、複数階層のBOM(組立品がさらに複数の部品で構成されるなど)を正確に扱えるか、設計変更や仕様変更があった場合に、その変更がスムーズかつ迅速にBOMに反映され、標準原価や実際原価の再計算が行えるかは極めて重要です。変更履歴の管理機能や版管理機能の有無も確認しましょう。PDM(製品データ管理)システムやCADシステムとBOM情報を連携できる製品であれば、設計から原価への一気通貫した情報管理が実現できます。
詳細な工程別原価計算とリアルタイムな作業時間収集の仕組み
製品が完成するまでには、切断、加工、組立、検査など複数の製造工程を経ることが一般的です。各工程でどれだけの材料費、労務費、経費が発生したかを把握する「工程別原価計算」は、製造プロセスのボトルネック発見や効率改善に不可欠です。特に労務費に関しては、作業者がどの製品のどの工程にどれだけの時間を費やしたかを正確に収集する仕組み(例えば、RFIDやバーコードリーダー、タブレット端末を活用した実績入力システムとの連携など)が重要となります。これにより、工程ごとの実際の作業時間に基づいた、より精度の高い労務費計算が可能になります。
多様な生産形態への対応(ロット生産、個別受注生産など)
製造業と一口に言っても、見込み生産、ロット生産、個別受注生産など、その生産形態はさまざまです。原価管理システムが、自社の主要な生産形態に合った原価計算方法(例えば、ロット別原価計算、ジョブオーダー別原価計算など)をサポートしているかを必ず確認しましょう。多品種少量生産の企業では、個々の製品や受注オーダ単位での原価管理が特に重要になります。
仕掛品評価の精度とリアルタイム性
月末や期末に、まだ完成していない製品(仕掛品)がどれだけあるか、そしてその仕掛品にどれだけの原価が投入されているかを正確に評価することは、正しい期間損益を把握する上で不可欠です。原価管理システムが、工程の進捗度合いに応じて仕掛品原価を自動計算し、リアルタイムに近い形で把握できる機能を備えているかを確認しましょう。
実際原価と標準原価の詳細な差異分析機能
多くの製造業では、目標となる標準原価をあらかじめ設定し、実際にかかった実際原価との差異を分析することで、コスト管理を行います。原価管理システムが、材料価格差異、材料歩留差異(数量差異)、作業時間差異、賃率差異、予算差異、能率差異など、差異の要因を詳細に分解して分析できる機能を備えていることが望ましいです。これにより、コストが計画から外れた根本原因を特定し、具体的な改善策を講じることが可能になります。
私が支援したある精密部品メーカーQ社様は、多品種少量でかつ試作品製造も多いという特徴があり、従来のExcelベースの原価計算では、試作段階でのコストが全く把握できていませんでした。製造業向けの機能が充実し、特に工程別の作業時間実績をリアルタイムに細かく収集できる原価管理システムを導入したことで、試作品ごとの実際原価を正確に把握できるようになり、量産移行時の価格設定や採算予測の精度が飛躍的に向上しました。これは、製造業特有のニーズに合ったシステム選定の成功例と言えるでしょう。
6.2.2.建設業向けシステムの選び方のポイントと機能要件(どっと原価シリーズ等)
建設業においては、個別の「工事プロジェクト」単位での原価管理が基本となり、その特徴は製造業とは大きく異なります。工事期間が長期にわたること、実行予算の精度が利益を左右すること、外注費の割合が高いこと、工事の進捗に合わせた原価把握が重要であることなどが挙げられます。2025年現在、資材価格の高騰や人手不足は建設業にとっても深刻な課題であり、より厳密な原価管理が求められています。建設業向けの原価管理システム(例えば、「どっと原価シリーズ」に代表されるような専門システム)を選定する際には、以下のポイントと機能要件に注目する必要があります。
詳細な実行予算管理機能
建設業では、工事を受注する前に、詳細な積算に基づいて実行予算を編成します。この実行予算が工事の採算目標となるため、原価管理システムが、費目(材料費、労務費、外注費、機械経費、共通仮設費、現場経費など)ごとに細かく実行予算を設定・管理できる機能を備えているかが重要です。過去の類似工事の予算を流用したり、Excelで作成した予算データをインポートしたりできる柔軟性や、予算変更の履歴を確実に管理できる機能も不可欠です。
工事台帳(工事原価台帳)の自動作成とリアルタイム更新
工事ごとに、実際に発生した原価(仕入、外注への支払、社員の労務費など)を費目別に集計し、実行予算と対比して表示する「工事台帳」は、建設業の原価管理の基本帳票です。原価管理システムが、日々の取引データからこの工事台帳を自動作成し、リアルタイムに近い形で更新できる機能を備えていれば、工事の採算状況を常に最新の状態で把握できます。
発注・支払管理機能との連携
建設工事では、資材の仕入れや専門工事業者への外注が多数発生します。これらの発注情報や支払情報を、正確に各工事の原価として紐付けて計上するための機能が重要です。購買管理システムや会計システムとスムーズに連携し、二重入力を防ぎ、支払漏れや過払いを防止する仕組みが求められます。
工事進捗度(出来高)管理機能
長期にわたる工事では、工事の進捗度合いに応じて、どれだけの原価が発生し、どれだけの売上(出来高)が計上されるべきかを評価することが重要です。原価管理システムが、工事の進捗度を登録・管理し、それに基づいて予定原価や完成工事原価をシミュレーションしたり、未成工事支出金を正確に把握したりする機能を備えているかを確認しましょう。
労務費・社員別原価の把握
どの社員がどの工事にどれだけの時間(工数)を費やしたかを正確に把握し、それを労務費として各工事に適切に配賦する機能は、特に自社で多くの職人を抱える建設会社にとって重要です。勤怠管理システムや日報システムと連携し、社員ごとの作業実績を効率的に収集できるかがポイントです。
建設業特有の帳票出力
工事一覧表、工事原価報告書、実行予算実績対比表、支払明細書、未成工事支出金明細表など、建設業の業務や会計処理に特有の帳票類を標準で出力できるか、あるいはカスタマイズして容易に作成できるかは、日々の業務効率に大きく影響します。建設業に特化したパッケージシステムは、これらの帳票機能が充実している傾向にあります。
ある工務店R社様は、複数の小規模工事を同時に多数抱えており、各工事の実行予算の精度と、リアルタイムな原価進捗の把握が最大の課題でした。建設業特化型のクラウド原価管理システムを導入し、特に実行予算のテンプレート機能と、スマートフォンから現場の経費を簡単に登録できる機能を活用したことで、予算作成の効率と精度が大幅に向上し、赤字工事の発生を未然に防ぐことができるようになりました。
このように、自社の業種特性を深く理解し、それに合致した機能を備えた原価管理システムを選ぶことが、導入効果を最大限に引き出すための近道となります。
6.3.ポイント3:必要な機能の過不足を見極める(機能比較のコツ)
原価管理システムには実に多様な機能が搭載されていますが、自社にとって本当に必要な機能は何かを冷静に見極めることが、システム選定における失敗を避けるための重要なポイントです。多機能であればあるほど良いというわけではなく、むしろ使わない機能が多すぎると、操作が複雑になったり、システムが重くなったり、余計なコストがかかったりする可能性があります。一方で、必要な機能が不足していれば、導入目的を達成することができません。
結論として、自社の導入目的と業務要件に基づいて「必須機能(Must)」「あったら良い機能(Want)」「不要な機能(Nice to have but not necessary)」を明確に仕分けし、過不足のない機能構成のシステムを選ぶことが、費用対効果の高いシステム導入につながります。
必要な機能を見極めるための具体的なステップと、機能比較のコツは以下の通りです。
RFP(提案依頼書)の作成と機能要件の明確化
ポイント1で明確にした「自社の課題と導入目的」をもとに、原価管理システムに求める具体的な機能要件をリストアップします。この際、各機能について、「なぜその機能が必要なのか」「その機能を使ってどのような業務をどのように改善したいのか」を具体的に記述することが重要です。これらの機能要件をまとめたRFP(提案依頼書)を作成し、複数のシステムベンダーに提示することで、各社からの提案を同じ土俵で比較検討することが可能になります。2025年現在では、RFPにセキュリティ要件やデータ連携要件を詳細に記述することも一般的です。
機能の優先順位付け(Must/Want/Nice to have)
リストアップした機能要件に対して、優先順位を付けます。
o 必須機能(Must): この機能がなければ導入目的を達成できない、絶対に外せない機能。
o あったら良い機能(Want): 必須ではないが、あればより業務効率化や管理レベルの向上が期待できる機能。
o 不要な機能(Nice to have but not necessary): あってもなくても、当面の業務や導入目的の達成には直接影響しない機能。
この仕分け作業を社内の関係者(経営層、経理部門、製造部門、情報システム部門など)で議論し、合意形成を行うことが大切です。
複数システムの機能比較表の作成
検討対象となる複数の原価管理システムについて、RFPで提示した機能要件をどの程度満たしているかを一覧表形式で比較します。各機能について、「〇:標準機能で対応」「△:カスタマイズやオプションで対応可」「×:対応不可」といった形で評価を記入していくと分かりやすいでしょう。この際、単に機能の有無だけでなく、その機能の使い勝手や設定の柔軟性なども、可能な範囲で確認できるとより良い比較ができます。
「ちょうど良い」機能レベルの追求
特に中小製造業の場合、大企業向けの高機能・高性能な原価管理システムは、オーバースペックとなりがちです。操作が複雑で現場が使いこなせない、導入や運用のコストがかかりすぎるといった問題が生じる可能性があります。一方で、あまりに簡易的なシステムでは、将来的な事業拡大や管理レベルの高度化に対応できないかもしれません。自社の現在の業務レベルと、数年先の将来像を見据えて、「ちょうど良い」機能レベルのシステムを選ぶバランス感覚が重要です。
デモンストレーションやトライアルでの確認
機能一覧表だけでは分からない、実際の操作感や機能の細かな仕様については、システムベンダーによるデモンストレーションを依頼したり、可能であれば無料トライアルや体験版を試したりして、実際に触れてみることが極めて重要です。特に、自社の業務シナリオに沿ったデータを使ってデモをしてもらうと、機能の適合度をより具体的に評価できます。
ある食品メーカーS社様は、当初、非常に多機能で高価なERP一体型の原価管理システムを検討していましたが、私たちが機能要件の洗い出しと優先順位付けをサポートした結果、S社様にとって本当に必要なのは、「正確なレシピベースの材料費計算」と「ロット別トレーサビリティ」であり、それ以外の多くの機能は当面不要であることが明確になりました。結果として、S社様はこれらの必須機能に特化した、よりシンプルでコストパフォーマンスの高い中堅企業向け原価管理システムを選択し、スムーズな導入と現場への定着に成功しました。
機能の比較検討は骨の折れる作業ですが、ここを丁寧に行うことが、費用対効果の高い原価管理システム導入に繋がるのです。
6.4.ポイント4:操作性(UI/UX)・画面サンプル・デモの確認
どれほど高機能で素晴らしい原価管理システムであっても、実際にシステムを操作する現場の担当者にとって「使いにくい」「分かりにくい」ものであれば、その効果は半減してしまいます。最悪の場合、せっかく導入したシステムがほとんど使われず、宝の持ち腐れになってしまう可能性すらあります。したがって、システム選定においては、機能面だけでなく、日々の業務でストレスなく使える「操作性(UI:ユーザーインターフェース/UX:ユーザーエクスペリエンス)」を十分に確認することが極めて重要なポイントとなります。
結論として、実際にシステムを利用するユーザー部門の担当者が、直感的で分かりやすく、効率的に作業できる操作性を備えているかを、画面サンプルやデモンストレーション、トライアルを通じて徹底的に確認することが、システム導入後の定着と活用促進に不可欠です。
操作性を確認する際の具体的なポイントは以下の通りです。
直感的で分かりやすい画面デザイン(UI)
メニュー構成が論理的で分かりやすいか、アイコンやボタンの意味が直感的に理解できるか、情報の配置が整理されていて見やすいか、といった画面デザインの基本が重要です。毎日使うシステムだからこそ、見た目の分かりやすさや、操作していて心地よいデザインであることは、利用者のモチベーションにも影響します。2025年現在では、モバイルフレンドリーなデザインや、カスタマイズ可能なダッシュボードを備えた原価管理システムも増えています。
効率的な操作フロー(UX)
日常的に行うデータ入力や検索、レポート出力といった一連の操作が、少ないステップでスムーズに行えるか、画面遷移が分かりやすく、迷うことなく目的の機能にたどり着けるか、といった操作フローの効率性を確認します。例えば、よく使う機能へのショートカットがあるか、キーボード操作だけでも基本的な入力が完結できるか、といった点もチェックポイントです。
入力支援機能の充実度
データ入力時のミスを減らし、効率を上げるための入力支援機能(例えば、ドロップダウンリストからの選択、コード入力による自動表示、過去の入力履歴の参照、入力エラー時の分かりやすいメッセージ表示など)が充実しているかを確認します。これらの細かな機能が、日々の作業負担の軽減に大きく貢献します。
レスポンス速度
画面の切り替えやデータの処理に時間がかかりすぎると、利用者は大きなストレスを感じ、作業効率も低下します。特にクラウド型の原価管理システムを検討する場合は、自社のインターネット環境でデモンストレーションを受け、実際のレスポンス速度を体感することが重要です。
マニュアルやヘルプ機能の分かりやすさ
操作に迷った際や、新しい機能を使う際に参照するマニュアルやオンラインヘルプが、分かりやすく整備されているかも重要なポイントです。検索機能が充実しているか、図や動画を活用した説明があるかなども確認しましょう。
実際に操作する担当者の意見を重視
システム選定の際には、経営層や情報システム部門だけでなく、実際に日々その原価管理システムを操作することになる経理部門や製造現場の担当者の意見を必ず聞くようにしましょう。彼らが「これなら使えそうだ」「分かりやすい」と感じるかどうかが、システム定着の鍵を握ります。可能であれば、選定プロセスに現場担当者にも参加してもらい、一緒にデモンストレーションを受けたり、トライアルを試したりすることが理想的です。
私が以前、ある中小製造業T社様のシステム選定に関わった際、経営陣は多機能で先進的なAシステムに魅力を感じていました。しかし、現場の経理担当者数名にAシステムのデモを見てもらったところ、「画面の文字が小さくて見づらい」「操作が複雑で覚えるのが大変そうだ」という意見が多数出ました。一方で、機能はAシステムほど多くはないものの、画面がシンプルで操作が直感的なBシステムについては、現場担当者から「これならすぐに使えそう」と好意的な反応が得られました。最終的にT社様はBシステムを採用し、現場へのスムーズな導入と定着に成功しました。この事例は、操作性の確認と現場の意見聴取の重要性を物語っています。
画面サンプルやカタログだけでは分からない操作性は、ベンダーに依頼して実際のシステムを操作させてもらう「ハンズオンデモ」や、一定期間無料で試用できる「トライアルアカウント」などを積極的に活用して、徹底的に確認するようにしましょう。
6.5.ポイント5:提供メーカー・ベンダーのサポート体制と実績
原価管理システムは、導入して終わりではなく、その後長期間にわたって安定的に活用していくものです。そのため、システムを提供するメーカーや販売ベンダーのサポート体制が充実しているか、そしてその企業が原価管理システム分野において十分な実績と信頼性を持っているかは、システム選定における非常に重要なポイントとなります。特に、専門のIT担当者が少ない中小企業にとっては、いざという時に頼れるベンダーの存在は心強い味方となるでしょう。
結論として、システム導入後の問い合わせ対応、トラブルシューティング、法改正やOSアップデートへの対応、そして継続的な情報提供など、ベンダーのサポート体制の質と、業界における導入実績や専門知識の豊富さが、長期的なシステム活用の安心感と効果の持続性を左右します。
サポート体制を確認する際の主なポイントは以下の通りです。
問い合わせ窓口と対応時間・方法
システム操作に関する疑問点や、万が一トラブルが発生した場合の問い合わせ窓口(電話、メール、専用ウェブサイトなど)が明確か、対応時間は自社の業務時間と合っているか、問い合わせに対する回答の迅速さや的確さはどうか、といった点を確認します。2025年現在では、チャットボットによる24時間対応や、FAQサイトの充実度もポイントになります。
サポートの範囲と内容
基本的な操作方法の案内だけでなく、システムの設定変更に関するアドバイス、データ移行の支援、トラブル発生時の原因調査と復旧支援、法改正(例えば消費税率の変更など)に伴うシステム改修への対応など、どの範囲までサポートが提供されるのかを具体的に確認しましょう。保守契約の内容もしっかりと目を通す必要があります。
導入支援と教育プログラムの充実度
システムの導入フェーズにおけるベンダーの支援体制(専任の導入コンサルタントの有無、導入スケジュールの策定支援、データ移行サポートなど)が手厚いか、また、システムをスムーズに使いこなせるようになるためのユーザー向け教育プログラム(集合研修、オンライン研修、eラーニングなど)が用意されているかも重要です。
バージョンアップと情報提供
システムの機能改善やセキュリティ強化のためのバージョンアップが定期的に提供されるか、その内容や適用方法に関する情報が適切に提供されるかを確認します。また、原価管理に関する最新のトレンドや法改正情報、他社の活用事例などをセミナーやニュースレターといった形で積極的に提供してくれるベンダーであれば、より心強いでしょう。
次に、ベンダーの実績と信頼性を確認するポイントです。
原価管理システム分野での導入実績
検討している原価管理システムが、自社と同業種・同規模の企業にどれだけ導入されているか、具体的な導入事例(お客様の声やケーススタディ)が公開されているかを確認します。多くの導入実績があるということは、それだけ多くの企業のニーズに応えてきた証であり、システムの信頼性やベンダーのノウハウの蓄積が期待できます。
業種特化の専門知識
特に製造業や建設業など、業種特有の原価管理ニーズがある場合は、その業種に対する深い理解と専門知識、そして豊富な導入経験を持つベンダーを選ぶことが望ましいです。業種特有の課題解決に強みを持つベンダーであれば、より的確なアドバイスやサポートが期待できます。
企業の経営安定性と将来性
原価管理システムは長期的に利用するものであるため、提供ベンダーの経営が安定しており、将来にわたって継続的に事業を続けていけるかどうかも間接的なポイントとなります。上場企業であるか、長年の実績があるか、業界での評判はどうか、といった点も参考にするとよいでしょう。
私が以前、ある機械メーカーU社様のシステム選定をお手伝いした際、機能的にはほぼ同等で価格も近い二つの原価管理システムで悩んでいました。最終的な決め手となったのは、片方のベンダーがU社様と同業種の導入事例を多数持ち、導入後のユーザーコミュニティも活発で、定期的な勉強会や情報交換の場を提供していた点でした。U社様は、「システムを導入するだけでなく、その後の活用まで含めて長期的に付き合えるベンダーだ」と判断し、そのシステムを採用。結果として、導入後も手厚いサポートと有益な情報提供を受けながら、原価管理レベルを継続的に向上させています。
ベンダーのサポート体制や実績は、システムのカタログだけでは分からない部分も多いため、既存ユーザーの評判を調べたり、ベンダーの担当者と直接面談してじっくりと話を聞いたりすることが重要です。
6.6.ポイント6:費用対効果と価格相場(初期費用・月額料金)の比較検討
原価管理システムの導入は、企業にとって少なからぬ投資となります。したがって、その投資に見合うだけの効果(費用対効果、ROI:Return on Investment)が得られるかどうかを慎重に検討することが不可欠です。また、システムの価格は、提供形態(クラウド/オンプレミス)、機能、ユーザー数、カスタマイズの有無などによって大きく変動するため、複数のシステムを比較し、おおよその価格相場を把握した上で、自社の予算内で最適な選択をすることが重要なポイントとなります。
結論として、導入によって得られる業務効率化、コスト削減、利益向上などの具体的な効果を金額換算で見積もり、それとシステム導入・運用にかかる総コストを比較して、投資回収期間や収益性を評価することが、賢明なシステム選定の基本です。
費用対効果を検討する際のステップは以下の通りです。
導入効果の具体的な見積もり
ポイント1で明確にした「導入目的」と、ポイント3で見極めた「必要な機能」をもとに、原価管理システム導入によって期待できる具体的な効果を、可能な範囲で金額換算してみます。
o 業務効率化による人件費削減効果
・ 例:原価計算業務時間が月間100時間から40時間に短縮(削減60時間)。担当者の平均時給が3,000円の場合、月間18万円、年間216万円のコスト削減。
o データ入力ミス削減による手戻りコスト削減効果
・ 例:従来、入力ミスによる修正作業に月間10時間かかっていたものがほぼゼロに。月間3万円、年間36万円のコスト削減。
o 正確な原価把握による不採算製品の改善・撤退効果
・ 例:赤字と判明した製品Aの年間損失額が500万円。対策により損失が200万円に圧縮できた場合、年間300万円の利益改善。
o 適正な価格設定による利益率向上効果
・ 例:原価情報に基づいた適切な価格設定により、全体の利益率が0.5%向上。年間売上が5億円の場合、年間250万円の利益増。 これらの効果を積み上げて、年間の総メリット額を算出します。
システム導入・運用にかかる総コストの把握: 原価管理システムの導入には、初期費用とランニングコストの双方が発生します。
o 初期費用
・ ソフトウェアライセンス料(オンプレミス型パッケージの場合)
・ サーバー・ネットワーク機器購入費(オンプレミス型の場合)
・ システム構築・設定費用、カスタマイズ費用
・ データ移行費用
・ 導入支援コンサルティング費用
・ 社員教育研修費用
o ランニングコスト(年間)
・ クラウドサービス利用料(月額または年額)
・ 保守サポート費用(オンプレミス型の場合)
・ サーバー維持費、電気代(オンプレミス型の場合)
・ 追加のカスタマイズや機能拡張費用(発生時)
・ IT担当者の人件費(一部) これらのコストを合計し、例えば5年間の総コスト(TCO:Total Cost of Ownership)を算出します。
費用対効果(ROI)の評価
算出した「年間の総メリット額」と「5年間の総コスト」を比較し、投資がどの程度の期間で回収できるか(投資回収期間)、そして投資に対してどれだけの利益が見込めるか(ROI)を評価します。
ROIは「(累計利益額 - 投資額)÷ 投資額 × 100 (%)」で計算できます。
この評価はあくまで試算であり、全ての効果を正確に金額換算することは難しいですが、客観的な判断材料として非常に有効です。
次に、価格相場の比較検討についてです。
複数のベンダーから見積もりを取得
必ず2~3社以上のベンダーから、自社の要件に基づいた正式な見積もりを取得しましょう。これにより、おおよその価格相場を把握できます。
見積もり内容の詳細な確認
提示された見積もりに、何が含まれていて何が含まれていないのか(例えば、保守内容、バージョンアップ費用、サポート範囲など)を詳細に確認します。単純な総額だけでなく、内訳を比較することが重要です。
クラウド型とオンプレミス型のコスト構造の違いを理解
クラウド型は初期費用が安いが月額費用が継続する、オンプレミス型は初期費用が高いが月額費用は抑えられる(ただしサーバー維持費などは別途)、といったコスト構造の違いを理解し、長期的な視点で総コストを比較します。
価格交渉の可能性
提示された見積もりに対して、機能の絞り込みや契約期間の調整などにより、ある程度の価格交渉が可能な場合もあります。ただし、過度な値引き要求は、その後のサポート品質の低下などに繋がる可能性もあるため注意が必要です。
私が以前、ある中小製造業V社様の原価管理システム選定をご支援した際、V社様は当初、機能の豊富さから高価格帯のAシステムに惹かれていました。しかし、詳細な費用対効果分析を行ったところ、V社様の規模や業務内容では、Aシステムの多くの機能が過剰であり、投資回収に10年以上かかる試算となりました。そこで、必要な機能を絞り込み、中価格帯で実績のあるBシステムと、低価格帯のクラウド型Cシステムを改めて比較検討。最終的に、Cシステムでも主要な導入目的は達成可能で、かつ3年程度で投資回収できる見込みが立ったため、Cシステムを採用し、結果として身の丈に合ったシステム導入で着実な効果を上げています。
費用対効果の検討と価格相場の比較は、経営資源が限られる中小企業にとっては特に重要なプロセスです。目先の価格だけでなく、長期的な視点と客観的なデータに基づいて、賢明な投資判断を行うようにしましょう。
6.7.ポイント7:将来的な拡張性・柔軟性(システム連携、機能追加)
原価管理システムを導入する際には、現在のニーズを満たすことだけでなく、将来的な企業の成長や事業環境の変化にも柔軟に対応できるか、という「拡張性」と「柔軟性」の視点も忘れてはなりません。企業は生き物であり、数年後には事業規模が拡大したり、新しい製品ラインナップが増えたり、組織体制が変更されたり、あるいは他の新しいITシステムを導入したりする可能性は十分にあります。2025年現在、市場の変化はますます速くなっており、この将来対応力はシステム選定において非常に重要なポイントとなります。
結論として、現在の要件だけでなく、数年先の事業展開や業務変化を見据え、ユーザー数やデータ量の増加、機能追加、他システムとの連携拡張などに柔軟に対応できる拡張性と柔軟性を備えた原価管理システムを選ぶことが、長期的な投資価値を最大化します。
将来的な拡張性と柔軟性を確認する際の主なポイントは以下の通りです。
ユーザー数・データ量の増加への対応
企業の成長に伴い、原価管理システムを利用するユーザー数が増加したり、取り扱うデータ量(製品マスター数、トランザクションデータなど)が増大したりすることが予想されます。システムが、これらの増加に対してスムーズにスケールアップできるか(特にクラウド型の場合はプラン変更の容易さ、オンプレミス型の場合はサーバー増強のしやすさなど)を確認しておきましょう。パフォーマンスの低下を招かないかどうかも重要です。
機能追加・カスタマイズの可能性
現在は必要なくても、将来的に新しい原価計算方法を採用したり、より高度な分析機能が欲しくなったり、特定の帳票を追加したくなったりするかもしれません。システムが、後からオプション機能を追加できるか、あるいはある程度のカスタマイズが可能な設計になっているか(例えば、ユーザー定義項目の追加、レポートレイアウトの変更など)を確認しておくと、将来のニーズ変化にも柔軟に対応できます。
他システムとの連携拡張性
現在連携を予定しているシステムだけでなく、将来的に導入する可能性のある他の業務システム(例えば、BIツール、SFA/CRM、SCMシステムなど)ともスムーズに連携できるか、標準的なAPI(Application
Programming Interface)が提供されているか、あるいはデータエクスポート/インポート機能が充実しているかなどを確認します。システム間のデータ連携は、企業全体の業務効率化と情報活用の鍵となります。
業種・業態の変化への対応力
M&A(合併・買収)や新規事業への進出などにより、企業の業種や業態が変化する可能性も考慮に入れる必要があります。原価管理システムが、異なる業種の原価計算ロジックにもある程度対応できる柔軟性を持っているか、あるいは複数会社対応機能などを備えていると、そのような変化にも対応しやすくなります。
技術的な陳腐化リスクの低減
IT技術の進歩は非常に速いため、導入したシステムが数年で技術的に陳腐化してしまうリスクも考慮しなければなりません。ベンダーが、システムの基盤技術(OS、データベースなど)のアップデートに継続的に対応しているか、新しい技術トレンド(AI、IoTなど)を将来的に取り込む計画があるかなども、長期的な視点では重要なポイントです。特にクラウド型システムは、ベンダー側でこのような技術追従が期待できるというメリットがあります。
ある成長著しい中小製造業W社様は、5年前に導入した原価管理システムが、現在の事業規模や取り扱い製品数の増加に追いつけなくなり、処理速度の低下や機能不足が深刻な問題となっていました。システム導入時には、そこまでの急成長を予測していなかったため、拡張性の低いシステムを選んでしまったことが原因でした。結局、W社様は多大なコストと時間をかけてシステムの再構築を余儀なくされました。この事例は、将来的な拡張性を軽視したシステム選定のリスクを如実に示しています。
もちろん、将来の全てを正確に予測することは不可能ですが、「現状維持」を前提とするのではなく、ある程度の事業成長や変化を織り込んでシステムの拡張性・柔軟性を評価することが、長期にわたって「使える」原価管理システムを選ぶための賢明なアプローチと言えるでしょう。ベンダーに対して、将来的なロードマップや技術戦略について質問してみるのも有効な手段です。
7.【タイプ・業種別】注目すべき原価管理システム -比較表紹介
これまでの章で、原価管理システムの基本的な知識、導入メリット・デメリット、主要機能、そして失敗しない選び方のポイントについて詳しく解説してきました。この章では、いよいよ具体的にどのような原価管理システムが市場に存在するのか、そのタイプ別・業種別の代表的な特徴や傾向、そしてどのような企業にどのようなシステムが適しているのかを、2025年現在の情報をもとに比較のポイントを紹介していきます。ここで紹介するのはあくまで一部の例や傾向であり、全ての項目を網羅するものではありませんが、皆様が自社に最適な原価管理システムを探す上での重要な羅針盤となるはずです。特定の製品を推奨するものではなく、あくまで中立的な立場から、それぞれのシステムが持つ一般的な強みや機能、そして比較検討する際の視点を提供することを目的とします。
7.1.おすすめシステムの比較表(タイプ、対象業種、主要機能、価格帯の目安)
原価管理システムを比較検討する際には、いくつかの重要な観点から各製品を整理し、自社のニーズと照らし合わせることが効果的です。具体的な製品名を挙げて詳細な比較表をここで提示することは、市場の変化の速さや個々の製品のアップデート頻度を考えると現実的ではありません。しかし、皆様がご自身で情報を収集し、比較検討を行う際に役立つ「比較のフレームワーク(観点)」をここで提示します。このフレームワークを参考に、検討候補となるシステムの情報を整理してみてください。
結論として、原価管理システムを比較する際は、提供タイプ、得意とする業種、主要機能の充足度、価格帯、そしてサポート体制といった複数の軸で情報を整理し、自社の優先順位と照らし合わせながら総合的に評価することが重要です。
原価管理システム比較検討時の主要な観点(フレームワーク例):
提供タイプ:
o クラウド型(SaaS)
初期費用、運用負荷、導入スピード、場所を選ばないアクセス性などを重視する場合。
o オンプレミス型
カスタマイズの柔軟性、セキュリティの自社管理、既存オンプレミスシステムとの親和性などを重視する場合。
o ERP一体型
全社的な情報統合、会計・販売・生産などの基幹業務とのシームレスな連携を最優先する場合。
o 専用特化型
原価管理機能の専門性、特定の業種や業務への深い適合性を求める場合。
得意とする対象業種:
o 製造業全般
部品表(BOM)管理、工程別原価計算、標準原価計算と差異分析などの機能が充実しているか。
o 組立製造業
複雑なBOMや設計変更への対応力、ロット別管理など。
o プロセス製造業(装置産業)
連産品・副産物の原価計算、バッチ管理、材料配合管理など。
o 建設業
工事原価管理(実行予算、工事台帳)、進捗度管理、外注管理などの機能が充実しているか。
o IT・ソフトウェア開発業(プロジェクト型ビジネス)
プロジェクト別原価計算、工数管理、要員別単価設定、採算分析など。
o その他サービス業
案件別原価計算、サービスごとの収益性分析など。
主要機能の充足度:
o 原価計算方法
実際原価、標準原価、直接原価など、自社が採用したい計算方法に対応しているか。
o 配賦機能
間接費の配賦基準を柔軟に設定できるか。多段階配賦やABC(活動基準原価計算)への対応はどうか。
o 分析・レポート機能
製品別損益分析、差異分析、シミュレーション機能などが充実しているか。レポートのカスタマイズ性はどうか。
o 他システム連携
既存の会計、販売、生産管理システムなどとスムーズに連携できるか。API連携やCSV連携の方法。
o マスタ管理
品目マスター、BOM、工程マスターなどの管理機能の使いやすさ。
o 予算管理
実行予算の作成、予実管理、差異分析のしやすさ。
価格帯の目安:
o 初期費用
ライセンス料、構築費用、カスタマイズ費用、導入支援費用など。
o 月額(年額)料金
クラウドサービス利用料、保守サポート費用など。
o ユーザー数に応じた価格体系
利用ユーザー数が増えた場合の費用変動。
o オプション機能の価格
追加機能を導入する場合の費用。 (具体的な価格はベンダーへの問い合わせが必須ですが、おおよそのターゲット価格帯を把握しておくことは重要です。)
導入実績とサポート体制:
o 同業種・同規模企業への導入実績は豊富か。事例を確認できるか。
o 導入支援の内容と手厚さ。
o 問い合わせ窓口、対応時間、保守内容などのサポート体制。
o ベンダーの専門知識や信頼性。
これらの観点を表形式にまとめ、検討候補の原価管理システムを横並びで比較することで、それぞれのシステムの強み・弱みが明確になり、自社の優先順位に照らし合わせて客観的な評価がしやすくなります。2025年現在では、多くのベンダーがウェブサイト上で製品情報を公開しており、資料ダウンロードやオンラインデモの申し込みも容易に行えるため、積極的に情報収集を行いましょう。
8. 原価管理システム導入のプロセスと成功のポイント
原価管理システムの選定が完了し、いよいよ導入フェーズへと進む際、多くの方が「何から手をつければ良いのか」「スムーズに導入を進めるためにはどうすれば良いのか」といった不安を抱かれることでしょう。原価管理システムの導入は、単に新しいソフトウェアをインストールするだけの作業ではありません。現状の業務プロセスの見直し、関係各部署との連携、社員への教育、そして新しいシステムを組織に定着させるための地道な努力が伴う、一大プロジェクトです。この章では、原価管理システムを導入決定してから実際に本稼働させ、その効果を最大限に引き出すための一般的な実施プロセスとスケジュール感、そしてプロジェクトを成功に導くための重要なポイントや注意点について、私たちコンサルタントの経験を交えながら具体的に解説していきます。
8.1.導入決定から本稼働までの一般的な実施プロセスとスケジュール
原価管理システムの導入プロジェクトは、一般的にいくつかのフェーズに分けて進められます。各フェーズの目的と主な作業内容を理解し、計画的に取り組むことが、スムーズな導入と期待される効果の実現に不可欠です。以下に、導入決定から本稼働までの一般的な実施プロセスと、それぞれの期間の目安(中小企業がパッケージ型やクラウド型の原価管理システムを導入する場合を想定)を示します。ただし、これはあくまで一例であり、企業規模や選択するシステムの種類、カスタマイズの度合いなどによって、実際のプロセスやスケジュールは大きく変動することをご理解ください。
結論として、原価管理システムの導入プロセスは、周到な計画と準備から始まり、要件定義、設計、開発・設定、テスト、データ移行、教育・研修を経て本稼働に至る一連のステップであり、各フェーズでの目標達成と関係者の協力が成功の鍵となります。
一般的な導入プロセスと期間の目安:
計画・準備フェーズ(約1~2ヶ月):
o 目的: システム導入プロジェクトの全体像を明確にし、推進体制を構築する。
o 主な作業内容:
・ プロジェクトチームの発足(経営層、情報システム部門、経理部門、製造部門などからメンバーを選出)。プロジェクトマネージャーの任命。
・ 導入目的の再確認と共有、具体的な目標値(KPI)の設定。
・ システムベンダーとの契約締結、役割分担の明確化。
・ 詳細な導入スケジュールの策定と、各フェーズの成果物の定義。
・ リスクの洗い出しと対応策の検討。
・ 社内へのプロジェクト開始の告知と協力体制の依頼。
o 成果物:
プロジェクト計画書、推進体制図、詳細スケジュール、RFP(提案依頼書)とベンダー選定結果(選定フェーズがここに含まれる場合もある)など。
このフェーズでのしっかりとした計画と準備が、プロジェクト全体の成否を左右すると言っても過言ではありません。
要件定義フェーズ(約1~3ヶ月):
o 目的: 新しい原価管理システムで実現したい業務要件や機能要件を具体的に定義し、システムの仕様を明確にする。
o 主な作業内容:
・ 現状の業務プロセスの詳細な分析(As-Isモデルの作成)。
・ 新しい原価管理システムを導入した後の理想的な業務プロセス(To-Beモデル)の設計。
・ システムに求める機能要件(原価計算方法、配賦ロジック、必要な帳票、他システムとの連携要件など)の洗い出しと具体化。
・ 非機能要件(セキュリティ、パフォーマンス、操作性など)の定義。
o 成果物:
要件定義書、業務フロー図(As-Is, To-Be)、機能一覧、データ移行計画など。
このフェーズでは、システムベンダーやコンサルタントと密にコミュニケーションを取りながら、自社の要求を正確に伝えることが重要です。曖昧な要件定義は、後の設計・開発フェーズでの認識のズレや手戻りの原因となります。
設計フェーズ(約1~2ヶ月):
o 目的: 要件定義書に基づいて、原価管理システムの具体的な設計を行う。
o 主な作業内容:
・ システムの基本設計(システム構成、画面設計、帳票設計、データベース設計、連携インターフェース設計など)。
・ システムの詳細設計(プログラムロジック、データ項目定義など)。
・ カスタマイズやアドオン開発が必要な場合は、その仕様設計。
o 成果物:
基本設計書、詳細設計書、カスタマイズ仕様書など。
設計書は、開発・設定作業の基盤となるため、内容に漏れや誤りがないか、関係者間で十分にレビューを行う必要があります。
開発・設定フェーズ(約1~4ヶ月、カスタマイズ規模による):
o 目的: 設計書に基づいて、原価管理システムの構築、プログラミング、設定作業を行う。
o 主な作業内容:
・ クラウド型システムの場合は、ベンダーによる環境準備とパラメータ設定。
・ オンプレミス型システムの場合は、サーバー構築、ソフトウェアインストール、パラメータ設定。
・ カスタマイズやアドオン開発が必要な場合は、プログラミングと単体テスト。
・ 他システムとの連携機能の開発・設定。
o 成果物:
構築されたシステム環境、開発されたプログラム、設定パラメータ一覧など。
このフェーズでは、ベンダーとの進捗確認や課題共有を定期的に行うことが重要です。
テストフェーズ(約1~2ヶ月):
o 目的: 開発・設定された原価管理システムが、要件定義通りに正しく動作するかを検証する。
o 主な作業内容:
・ 単体テスト(個々の機能が正しく動作するか)。
・ 結合テスト(複数の機能や他システムとの連携が正しく動作するか)。
・ 総合テスト(実際の業務シナリオに沿って、システム全体が問題なく動作するか)。
・ 受け入れテスト(ユーザー部門の担当者が実際に操作し、要件を満たしているか最終確認)。
・ テストで発見された不具合の修正と再テスト。
o 成果物:
テスト計画書、テスト仕様書、テスト結果報告書、不具合管理表など。
テストフェーズは、システムの品質を確保する上で非常に重要です。特にユーザー部門を巻き込んだ受け入れテストは、本稼働後の手戻りを防ぐために不可欠です。
データ移行フェーズ(テストフェーズと並行または直前):
o 目的: 既存のシステムやExcelファイルなどから、新しい原価管理システムへ必要なデータ(品目マスター、BOM、仕入先マスター、期首残高など)を移行する。
o 主な作業内容:
・ 移行対象データの特定と抽出。
・ データクレンジング(誤りや重複の修正)。
・ 移行プログラムの開発または手作業によるデータ入力。
・ 移行データの正当性検証。
o 成果物:
データ移行計画書、移行データ、検証結果報告書など。
データ移行は、地味ながらもシステムの精度を左右する重要な作業です。移行対象データの量や品質によっては、多大な時間と労力を要することもあります。
教育・研修フェーズ(テストフェーズと並行または直前):
o 目的:原価管理システムを利用する社員が、スムーズに操作できるようになるための教育・研修を実施する。
o 主な作業内容:
・ 研修対象者(エンドユーザー、管理者など)の特定。
・ 研修テキストやマニュアルの作成。
・ 集合研修、OJT(On-the-Job Training)、eラーニングなどの実施。
・ 理解度テストや質疑応答。
o 成果物:
研修資料、マニュアル、研修実施報告書など。
十分な教育・研修は、システムの早期定着と活用促進に不可欠です。
本稼働・運用開始フェーズ:
o 目的:全ての準備を終え、新しい原価管理システムを実際の業務で利用開始する。
o 主な作業内容:
・ 本稼働日時の決定と関係者への周知。
・ 本稼働直後のサポート体制の確立(ベンダー待機、社内ヘルプデスクなど)。
・ 旧システムからの切り替え作業(必要な場合)。
・ 本稼働後の運用ルールの徹底。
o 成果物:
本稼働宣言、運用マニュアル(改訂版)など。
本稼働直後は、予期せぬトラブルや問い合わせが集中することもあるため、迅速に対応できる体制を整えておくことが重要です。
運用・保守・評価フェーズ(本稼働後継続):
o 目的:システムの安定稼働を維持し、導入効果を評価・測定し、継続的な改善を行う。
o 主な作業内容:
・ 定期的なシステムメンテナンス、バックアップ。
・ 問い合わせ対応、トラブルシューティング。
・ データの整合性チェック。
・ システムの利用状況のモニタリング。
・ 導入効果(KPIの達成度など)の測定と評価。
・ 業務改善提案、システム改修の検討(必要な場合)。
o 成果物:
運用報告書、効果測定レポート、改善提案書など。
原価管理システムは導入して終わりではありません。継続的に活用し、効果を最大化するための取り組みが求められます。
8.2.プロジェクト体制の構築と社内準備(データ整理、業務フロー見直し)
原価管理システムの導入プロジェクトを成功させるためには、技術的な側面だけでなく、組織的な準備、特に「しっかりとしたプロジェクト体制の構築」と「事前の社内準備」が極めて重要です。これらが不十分だと、プロジェクトが迷走したり、現場の協力が得られなかったり、導入後のシステムが定着しなかったりするリスクが高まります。
結論として、経営層の強力なリーダーシップのもと、各関連部門の代表者を含む実効性の高いプロジェクトチームを組成し、導入前に既存データの整理や業務フローの見直しといった社内準備を徹底することが、スムーズなシステム導入と効果の最大化に不可欠です。
プロジェクト体制の構築におけるポイント:
経営層のコミットメントとプロジェクトオーナーの明確化
原価管理システムの導入は、単なる一部門の業務改善ではなく、全社的な経営課題に直結する取り組みです。そのため、経営トップがこのプロジェクトの重要性を強く認識し、積極的に関与・支援する姿勢(トップコミットメント)を示すことが不可欠です。また、プロジェクト全体の最終責任者である「プロジェクトオーナー」を経営層から任命し、強力なリーダーシップを発揮してもらうことが重要です。
部門横断的なプロジェクトチームの編成
原価管理は、経理部門だけでなく、製造部門、販売部門、購買部門、情報システム部門など、多くの部門が関わります。各部門から、業務に精通し、リーダーシップを発揮できるキーパーソンをプロジェクトメンバーとして選出し、部門横断的なチームを編成することが重要です。これにより、各部門のニーズや意見を的確に吸い上げ、全社的な視点での意思決定が可能になります。ある中小企業では、プロジェクトチームを経理部門のメンバーだけで構成したため、製造現場の特殊な業務フローが十分に考慮されず、導入後に現場から「使いにくい」という不満が噴出したことがあります。
プロジェクトマネージャーの任命と役割明確化
プロジェクト全体の進捗管理、課題管理、関係者間の調整、ベンダーとのコミュニケーションなどを担う「プロジェクトマネージャー」を任命し、その役割と責任を明確にします。プロジェクトマネージャーには、システムの知識だけでなく、コミュニケーション能力や問題解決能力、リーダーシップが求められます。社内に適任者がいない場合は、外部のコンサルタントに支援を依頼することも検討しましょう。
定期的な会議体と報告体制の確立
プロジェクトチームの定例会議、経営層への進捗報告会など、定期的な会議体を設け、情報共有と意思決定をスムーズに行う体制を整えます。議事録をきちんと作成し、決定事項や課題を明確にすることも重要です。
事前の社内準備におけるポイント:
既存データの整理・クレンジング
新しい原価管理システムに移行する既存のマスターデータ(品目マスター、部品表、顧客マスター、仕入先マスターなど)や取引データに、誤りや重複、欠損などがないか事前に徹底的にチェックし、整理・清掃(クレンジング)しておく必要があります。不正確なデータをそのまま新しいシステムに移行してしまうと、システムの信頼性が損なわれ、期待した効果が得られません。「ゴミを入れればゴミしか出てこない(Garbage
In, Garbage Out)」という言葉を肝に銘じましょう。
現行業務フローの見える化と課題の洗い出し
現在の原価管理に関わる業務フローを詳細に「見える化」し、どこに無駄や非効率、問題点があるのかを具体的に洗い出します。これは、新しいシステムに求める要件を明確にする上で非常に重要な作業です。
新しい業務フロー(To-Beモデル)の検討
原価管理システム導入を単なる現状業務のシステム化に終わらせるのではなく、これを機に、より効率的で付加価値の高い業務フローへと改善できないかを検討します(BPR:Business Process
Re-engineering)。システムの機能を最大限に活かせる業務フローを設計することが理想です。ただし、現場の現実とかけ離れた理想論にならないよう注意も必要です。
社内への周知と意識改革
なぜ原価管理システムを導入するのか、それによって社員や会社にどのようなメリットがあるのか、導入によって何が変わるのか、といったことを、経営トップから社員一人ひとりに対して丁寧に説明し、理解と協力を求めることが不可欠です。「やらされ感」ではなく、主体的にプロジェクトに関わってもらうための意識改革を促します。
これらの体制構築と社内準備をしっかりと行うことが、原価管理システム導入という航海を成功に導くための羅針盤と頑丈な船体を用意することに他なりません。
8.3.システム導入を成功に導くための注意点と手法
原価管理システムの導入プロジェクトは、企業にとって大きな投資であり、その成否は将来の経営に大きな影響を与えます。技術的な側面だけでなく、組織的・人的な側面も含めた多角的な視点から、プロジェクトを成功に導くための注意点と有効な手法を理解し、実践することが求められます。ここでは、私たちコンサルタントが多くの導入事例を通じて得た教訓をもとに、特に重要と考えられるいくつかのポイントを解説します。
結論として、原価管理システム導入の成功は、経営層の強いリーダーシップ、現場ユーザーの積極的な参画、明確な目標設定と共有、段階的な導入アプローチ、そしてシステムベンダーとの良好なパートナーシップ構築にかかっています。
経営トップの強力なリーダーシップと継続的なコミットメント
前述のプロジェクト体制構築でも触れましたが、原価管理システムの導入は全社的な取り組みであるため、経営トップが「このプロジェクトを必ず成功させる」という強い意志を持ち、リーダーシップを発揮し続けることが最も重要です。プロジェクトの節目節目で進捗を確認し、課題があれば迅速に意思決定を行う、予算やリソースの確保に責任を持つ、社内へのメッセージ発信を積極的に行うなど、経営トップの継続的な関与がプロジェクトの推進力となります。
現場ユーザーの早期からの巻き込みと参画意識の醸成
実際にシステムを使うのは現場のユーザーです。彼らの意見やニーズを無視してシステム導入を進めても、結局は使われない「お飾りのシステム」になってしまいます。要件定義の初期段階から現場のキーパーソンをプロジェクトチームに加え、彼らの業務知識や課題意識をシステム設計に反映させることが不可欠です。また、デモンストレーションやテストにも積極的に参加してもらい、「自分たちが使うシステムを自分たちで良くしていく」という当事者意識(オーナーシップ)を醸成することが、導入後のスムーズな定着に繋がります。
明確で共有された導入目的とゴール設定
「なぜこのシステムを導入するのか」「導入後にどのような状態を目指すのか」という目的とゴールが、経営層から現場の担当者まで、プロジェクトに関わる全てのメンバー間で明確に共有されていることが重要です。目的が曖昧だったり、人によって解釈が異なったりすると、プロジェクトの方向性がぶれ、意思決定も遅れます。設定した目的やゴールは、プロジェクトの各フェーズで常に立ち返り、当初の目論見から外れていないかを確認するべきです。
スモールスタートと段階的な導入アプローチの検討
特に初めて本格的な原価管理システムを導入する中小企業や、業務範囲が広い企業の場合、最初から全ての機能を一度に稼働させようとすると、現場の混乱が大きくなったり、プロジェクトが複雑化しすぎてコントロールが難しくなったりするリスクがあります。そのような場合は、まず特定の部門や製品群、あるいは基本的な機能に絞ってシステムを導入し(スモールスタート)、その効果を検証しながら段階的に対象範囲や機能を拡張していくアプローチが有効です。これにより、リスクを低減し、成功体験を積み重ねながら着実にシステムを定着させることができます。
業務改革(BPR)を意識したシステム導入
原価管理システムの導入を、単に現在の業務をそのままシステムに置き換えるだけの「システム化」と捉えるのではなく、これを機に非効率な業務プロセスそのものを見直し、改善する「業務改革(BPR:Business Process Re-engineering)」の絶好の機会と捉えるべきです。システムの標準機能を最大限に活かせるように業務フローを再設計することで、システム導入の効果を飛躍的に高めることが可能になります。ただし、過度な業務変更は現場の抵抗を生む可能性もあるため、バランスが重要です。
システムベンダーとの良好なパートナーシップ構築
原価管理システムの導入は、システムベンダーや導入支援コンサルタントとの共同作業です。彼らを単なる「業者」として扱うのではなく、プロジェクト成功のための「パートナー」として捉え、オープンで建設的なコミュニケーションを心がけることが重要です。自社の課題や要望を正確に伝え、彼らの専門知識や経験を最大限に引き出し、協力して問題解決にあたる姿勢が求められます。契約内容や役割分担を明確にすることも、良好な関係を築く上で不可欠です。
導入後の効果測定と継続的な改善サイクルの確立
原価管理システムは導入して終わりではありません。本稼働後、定期的に導入前に設定したKPI(重要業績評価指標)の達成度を測定・評価し、期待した効果が出ているかを確認する必要があります。思うような効果が出ていない場合は、その原因を分析し、運用方法の改善や追加の教育、あるいはシステム設定の見直しなどを検討します。このようなPDCAサイクルを回し続けることで、システムの価値を継続的に高めていくことができます。
これらのポイントは、どれも当たり前のことのように聞こえるかもしれませんが、実際のプロジェクトでは疎かになりがちな点でもあります。私が過去に見てきたシステム導入の失敗事例の多くは、技術的な問題よりも、これらの組織的・人的な要因に起因するものでした。これらの注意点を常に念頭に置き、一つ一つ丁寧に取り組むことが、原価管理システム導入を成功に導く確実な道と言えるでしょう。
8.4.導入事例紹介:成功事例と失敗から学ぶポイント
これまでに原価管理システム導入のプロセスや成功のポイントを解説してきましたが、ここではより具体的に、実際の導入事例を通じて、どのような取り組みが成功に繋がり、どのような点が失敗の原因となり得るのかを見ていきましょう。架空の企業を想定したケーススタディ形式で、製造業と建設業それぞれの事例を紹介し、そこから得られる教訓を明らかにします。
8.4.1.製造業における導入事例(ケーススタディ)
【成功事例:株式会社A製作所(中小部品メーカー)】
導入前の課題
株式会社A製作所は、多品種少量生産の精密部品メーカーです。Excelによる原価計算を行っていましたが、製品ごとの正確な原価把握が難しく、特に新規受注品の見積もり精度が低いことが課題でした。また、月次の原価確定に時間がかかり、経営判断に必要な情報がタイムリーに得られない状況でした。材料費の変動も激しく、採算管理が後手に回りがちでした。
導入したシステムと選定理由
A製作所は、製造業向けの機能が充実し、特に部品表(BOM)管理と工程別原価計算に強みを持つクラウド型原価管理システムBを選定しました。
選定の決め手は、
①自社の複雑なBOM構造に柔軟に対応できること
②生産管理システム(既存)とのデータ連携が比較的容易であること
③クラウド型で初期費用を抑えられ、IT担当者が少ない同社でも運用しやすいこと
④ベンダーの製造業における導入実績が豊富で、サポート体制も手厚いこと
でした。
導入プロセスと工夫した点
社長自らがプロジェクトオーナーとなり、製造部長、経理課長、若手エース社員からなるプロジェクトチームを結成。導入目的を「正確な製品別実際原価のリアルタイム把握と、見積もり精度向上による利益率改善」と明確に設定し、全社員に共有しました。要件定義では、ベンダーと協力し、主要な製品群について詳細なBOMと工程フローを徹底的に洗い出し、システムへの設定に落とし込みました。データ移行では、既存のExcelデータのクレンジングに時間をかけ、精度を重視しました。本稼働前に、主要なユーザー部門で十分なテストと研修を実施し、操作への習熟度を高めました。
導入後の効果
システム導入後、A製作所では以下のような顕著な効果が現れました。
1. 製品別実際原価が、ほぼリアルタイムで正確に把握できるようになり、赤字受注が大幅に減少。
2. 見積もり作成時に、過去の類似製品の実際原価データを参考にすることで、見積もり精度が飛躍的に向上し、適正な利益を確保できるように。
3. 月次の原価確定作業が従来の約3分の1の時間で完了。経理担当者は分析業務により多くの時間を割けるように。
4. 材料費の変動が原価に与える影響をシミュレーション機能で事前に予測し、迅速な価格改定や代替材料の検討が可能に。
社長は「原価管理システムは、まさに当社の経営の羅針盤となった。データに基づいて自信を持って意思決定できるようになったことが最大の成果だ」と語っています。
成功のポイント(分析)
A製作所の成功要因は、
①経営トップの強いリーダーシップと明確な導入目的の共有
②自社の課題と業種特性に合ったシステム選定
③現場を巻き込んだ丁寧な要件定義と準備
④信頼できるベンダーとの良好なパートナーシップ構築
⑤導入後の継続的なデータ活用と改善意識
にあったと考えられます。
8.4.2.建設業における導入事例(ケーススタディ)
【失敗事例から学ぶ:株式会社X建設(地方中堅ゼネコン)】
導入前の課題
株式会社X建設は、公共工事と民間工事を半々で手がける地方の中堅ゼネコンです。工事ごとの実行予算と実績の管理がExcelベースであり、複数の担当者がそれぞれ異なるフォーマットで情報を管理していたため、全社的な工事損益の把握が遅れがちでした。特に、工事の進捗と原価発生のズレが問題で、気づいた時には大幅な予算超過となっている工事が散見されました。
導入したシステムと当時の状況
X建設は、数年前に当時最新とされた多機能なオンプレミス型の建設業向け原価管理システムYを、他社の成功事例に惹かれてやや拙速に導入を決定しました。経営陣は「システムを入れれば全て解決する」という期待感が先行していました。
導入プロセスと問題点
プロジェクトチームは経理部門中心で、現場監督の意見を十分に吸い上げる機会が少ないまま要件定義が進められました。システムベンダーからは「標準機能でほとんどの業務はカバーできる」との説明があり、自社の特殊な業務フローへの適合性検証が不十分なまま、カスタマイズを最小限に抑える方針となりました。データ移行では、各担当者が個別に管理していたExcelデータの品質にばらつきがあり、移行作業が難航。現場監督向けの研修も十分な時間が確保されず、システムの操作方法が浸透しませんでした。
導入後の状況と失敗要因
システム導入後、現場監督からは「操作が複雑で使いにくい」「日々の入力作業が逆に増えた」「Excelの方が早くて楽だった」といった不満が続出。入力されるデータの精度も低く、システムから出力されるレポートの信頼性が揺らぎました。結果として、多くの現場でシステムが十分に活用されず、依然としてExcelでの二重管理が続く状況に陥ってしまいました。期待したリアルタイムな原価把握や業務効率化は達成できず、高価な投資は塩漬けに近い状態となりました。
失敗から学ぶポイント(分析)
X建設の事例から学べる教訓は数多くあります。
1. 導入目的の曖昧さと過度な期待
「システムを入れれば何とかなる」という安易な考えではなく、具体的な課題解決目標を明確にすべきでした。
2. 現場ユーザーの軽視
システムを実際に使う現場の意見を十分に聞かず、トップダウンで導入を進めたことが最大の失敗要因の一つです。
3. 業務プロセスとシステムのミスマッチ
自社の業務フローとシステムの適合性検証が不十分で、システムに業務を合わせる努力も、システムを業務に合わせるカスタマイズも中途半端でした。
4. 不十分な教育・サポート体制
現場が新しいシステムを使いこなせるようになるまでの教育・研修、そして導入後の継続的なサポートが不足していました。
5. データ品質への意識の低さ
移行するデータの重要性と、その品質担保のための事前準備を軽視していました。
このX建設の事例は、原価管理システム導入が技術的な問題だけでなく、組織的・人的な要因によっても失敗し得ることを示しています。これらの成功事例と失敗事例から学び、自社の導入プロジェクトに活かしていくことが、失敗のリスクを最小限に抑え、効果を最大限に引き出すための賢明なアプローチと言えるでしょう。
9. まとめ:最適な原価管理システムを選び、企業の競争力を強化する
ここまで、原価管理システムの基本的な知識から、導入メリット・デメリット、主要機能、タイプ別の比較、失敗しない選び方のポイント、導入プロセスに至るまで、多岐にわたる情報を解説してまいりました。この記事を通じて、原価管理システムが、いかにして中小製造業の皆様の経営課題解決と競争力強化に貢献できるか、その可能性を感じていただけたのであれば幸いです。
厳しい経済環境が続き、市場の変化も激しい現代において、どんぶり勘定や旧態依然とした管理方法では、企業の持続的な成長は望めません。「正確な原価をタイムリーに把握し、それを経営に活かす」という原価管理の基本に立ち返り、それを強力に支援する原価管理システムの導入は、もはや一部の大企業だけのものではなく、成長を目指すすべての企業にとって重要な経営戦略の一つと言えるでしょう。
この最後の章では、原価管理システム導入を成功させ、その効果を最大限に引き出すための鍵となるポイントを改めて整理し、2025年以降の展望、そして皆様が次にとるべきアクションについてお伝えします。
9.1.原価管理システム導入成功の鍵と今後の展望(2025年以降)
原価管理システムの導入プロジェクトを成功に導き、その効果を継続的に享受するためには、いくつかの重要な「鍵」が存在します。これまでの章でも触れてきましたが、改めてここで集約して強調したいと思います。
原価管理システム導入成功の5つの鍵:
明確な目的意識と経営層の強力なリーダーシップ
「なぜ原価管理システムを導入するのか」「導入して何を達成したいのか」という目的を、経営層から現場の隅々まで明確に共有することが全ての出発点です。そして、経営トップがこの変革を力強く牽引し、必要なリソースを投入し、プロジェクトを全面的に支援する姿勢が不可欠です。
現場ユーザー主体のプロジェクト推進
実際にシステムを日々利用するのは現場の社員です。彼らの業務知識や課題意識をシステム選定や要件定義に積極的に反映させ、彼らが「自分たちのためのシステムだ」と主体的に関われるような体制を築くことが、導入後のスムーズな定着と活用に繋がります。
自社に最適なシステム選定と段階的な導入
「高機能=良いシステム」とは限りません。自社の規模、業種特性、業務内容、予算、そして将来の拡張性などを総合的に考慮し、過不足のない「ちょうど良い」原価管理システムを選ぶことが肝心です。また、いきなり大規模なシステムを全社展開するのではなく、スモールスタートで効果を検証しながら段階的に進めるアプローチも有効です。
業務プロセスの見直し(BPR)への意識
原価管理システム導入を、単に既存の業務をシステムに置き換えるだけでなく、非効率な業務プロセスそのものを見直し、改善する絶好の機会と捉えましょう。システムの標準機能を最大限に活かせるように業務を再構築することで、導入効果は飛躍的に高まります。
信頼できるベンダーとの良好なパートナーシップ
システムベンダーや導入支援コンサルタントは、プロジェクト成功のための重要なパートナーです。彼らの専門知識や経験を最大限に引き出し、密なコミュニケーションを取りながら、二人三脚でプロジェクトを進めていく姿勢が求められます。
これらの「鍵」を意識して取り組むことで、原価管理システム導入の成功確率は格段に高まるでしょう。
今後の展望(2025年以降):
2025年以降の原価管理は、さらに進化していくことが予想されます。
AI(人工知能)や機械学習の活用
原価予測の精度向上、異常値の自動検知、コスト削減機会の提案など、AI技術が原価管理の高度化に貢献する場面が増えてくるでしょう。
リアルタイム性の追求
IoTデバイスからのデータ収集や、クラウドベースのシステム連携により、よりリアルタイムに近い原価把握と迅速な意思決定が一般化していくと考えられます。
DX(デジタル・トランスフォーメーション)との連携深化
原価管理システムは、企業全体のDX推進における重要な構成要素として、販売、生産、購買、会計といった他の基幹システムやBIツールとよりシームレスに連携し、経営情報のハブとしての役割を強めていくでしょう。
サステナビリティ(持続可能性)への対応
環境負荷コスト(CO2排出量など)の見える化や、サプライチェーン全体での社会的責任に関わるコストの把握など、サステナビリティの観点を取り入れた原価管理のニーズも高まる可能性があります。
私たちコンサルタントとしても、こうした新しい技術動向や社会的な要請を常に注視し、お客様である中小製造業の皆様が時代の変化に的確に対応できるよう、最新の情報と最適なソリューションを提供し続けていく所存です。
9.2.自社にマッチするシステム選定のための最終チェックポイント
原価管理システムの選定は、多くの情報を収集し、比較検討を重ねる、骨の折れる作業です。最終的な意思決定を下す前に、もう一度立ち止まって、以下のチェックポイントを確認してみましょう。これらの問いに自信を持って「Yes」と答えられるかどうかが、自社に真にマッチした原価管理システムを選ぶための最終関門となります。
【システム選定・最終チェックポイント】
目的適合性チェック:
□ 導入目的は明確であり、その目的を達成するために、この原価管理システムの機能は十分かつ適切か?
□ システム導入によって、現状の最も大きな課題(例えば、原価計算の手間、精度の問題、情報のタイムリーさなど)は具体的にどのように解決される見込みがあるか?
機能適合性チェック:
□ 自社の業種(製造業、建設業など)や生産形態(多品種少量、個別受注など)特有の原価計算や管理要件に、このシステムは十分対応できているか?
□ 部品表(BOM)管理、工程別原価計算、間接費の配賦ロジックなど、自社の原価計算のポイントとなる機能は満足できるレベルか?
□ 将来的な機能拡張やカスタマイズの柔軟性は確保されているか?
操作性・運用性チェック:
□ 実際にシステムを操作する現場の担当者が、直感的で分かりやすく、使いやすいと感じているか?(デモやトライアルでの評価)
□ 導入後の運用・保守体制(社内担当者、ベンダーサポート)は現実的に維持可能か?
□ マスターデータのメンテナンスや、日常のデータ入力作業は効率的に行えそうか?
連携性チェック:
□ 既存の会計システム、販売管理 システム、生産管理 システムなどとのデータ連携はスムーズに実現できそうか?そのための方法やコストは明確か?
費用対効果チェック:
□ 初期費用およびランニングコスト(月額費用、保守費用など)は、自社の予算規模に見合っているか?
□ 導入によって期待される効果(業務効率化、コスト削減、利益向上など)と投資コストを比較し、費用対効果は十分に期待できるか?投資回収期間の目安は?
ベンダー信頼性チェック:
□ システム提供ベンダーは、原価管理システム分野や自社業種において十分な導入実績と専門知識を持っているか?
□ 導入支援や導入後のサポート体制(問い合わせ対応、トラブル対応、バージョンアップなど)は信頼できる内容か?
□ ベンダーとのコミュニケーションは良好で、長期的なパートナーとして信頼できるか?
社内合意形成チェック:
□ 経営層から現場担当者まで、この原価管理システムを導入すること、そしてその目的や期待される効果について、社内での十分な理解と合意が得られているか?
□ システム導入に対する現場の協力体制は整っているか?
これらのチェックポイントを一つ一つ丁寧に確認し、全ての項目で納得のいく答えが得られれば、その原価管理システムは貴社にとって最適なパートナーとなる可能性が非常に高いと言えるでしょう。もし、いずれかの項目で不安が残るようであれば、再度情報収集やベンダーへの問い合わせ、社内での議論を重ねることをお勧めします。焦らず、慎重に、しかし着実に選定を進めてください。
9.3.関連サービス・ソリューションの紹介
原価管理システムは、それ単体でも大きな効果を発揮しますが、他の関連サービスやソリューションと組み合わせることで、その価値をさらに高めることが可能です。原価管理の高度化や、企業全体の業務効率化、DX推進を目指す上で、以下のような関連サービスの活用も視野に入れておくとよいでしょう。
BI(ビジネスインテリジェンス)ツール
原価管理システムに蓄積された膨大な原価データや実績データを、より視覚的に分かりやすく、多角的に分析するためのツールです。ダッシュボード機能やドリルダウン機能などを活用し、経営者や管理者が直感的に経営状況を把握し、迅速な意思決定を行うことを支援します。多くの原価管理システムが、主要なBIツールとの連携機能を備えています。
RPA(ロボティック・プロセス・オートメーション)
原価管理業務の中で、定型的で繰り返し発生するデータ入力や転記作業、レポート作成といった業務を、ソフトウェアロボットに代行させる技術です。原価管理システムへのデータ入力や、システムからのデータ抽出・加工といった作業をRPAで自動化することで、さらなる業務効率化と人的ミスの削減が期待できます。
生産スケジューラ・MES(製造実行システム)
特に製造業においては、生産計画の最適化を支援する生産スケジューラや、製造現場の進捗管理、実績収集をリアルタイムで行うMESとの連携が、より正確でタイムリーな実際原価の把握に不可欠です。これらのシステムからの情報が原価管理システムにスムーズに連携することで、原価管理の精度とスピードが向上します。
SFA(営業支援システム)/CRM(顧客関係管理システム)
顧客ごとの取引履歴や収益性を分析する上で、SFA/CRMに蓄積された営業活動情報や顧客情報と、原価管理システムの原価・利益情報を連携させることが有効です。どの顧客が最も利益に貢献しているのか、といった視点での分析が可能になります。
コンサルティングサービス
原価管理システムの導入は、単なるITツールの置き換えではなく、業務改革を伴うプロジェクトです。原価計算制度の設計、業務プロセスの見直し、導入目的の明確化、ベンダー選定支援、プロジェクト管理、導入後の定着化支援など、専門的な知識と経験を持つコンサルタントの支援を活用することで、プロジェクトの成功確率を高め、導入効果を最大化することができます。私たちのような中小製造業に特化したコンサルティング会社も、皆様の課題解決をお手伝いできます。
これらの関連サービスやソリューションは、必ずしも全ての企業に同時に必要なわけではありません。自社の課題や目指す姿に応じて、原価管理システムとの相乗効果が期待できるものを段階的に検討していくとよいでしょう。
「どの原価管理システムを選べば良いか分からない」「自社の課題に最適な解決策を見つけたい」といった場合には、私たちのような原価管理やシステム導入に詳しい専門コンサルタントにご相談いただくのも有効な手段です。客観的な立場から、貴社の状況に合わせた最適なアドバイスを提供できます。
原価管理システムの導入は、企業の未来を左右する重要な意思決定です。どうか、この記事で得た知識を活用し、積極的に情報収集を行い、比較検討を重ねて、貴社にとって真に最適な原価管理システムを見つけ出してください。そして、そのシステムを最大限に活用することで、原価管理レベルを飛躍的に向上させ、厳しい競争を勝ち抜くための強固な経営基盤を構築されることを心より願っております。
私たちも、多品種少量生産を行う中小製造業の皆様の力強いパートナーとして、これからも有益な情報発信と、きめ細やかなコンサルティングサービスを提供し続けてまいります。ご不明な点やご相談事項がございましたら、いつでもお気軽に船井総合研究所までお問い合わせください。
最後までお読みいただき、誠にありがとうございました。この記事が、貴社の原価管理の課題解決と、さらなる発展の一助となれば幸いです。