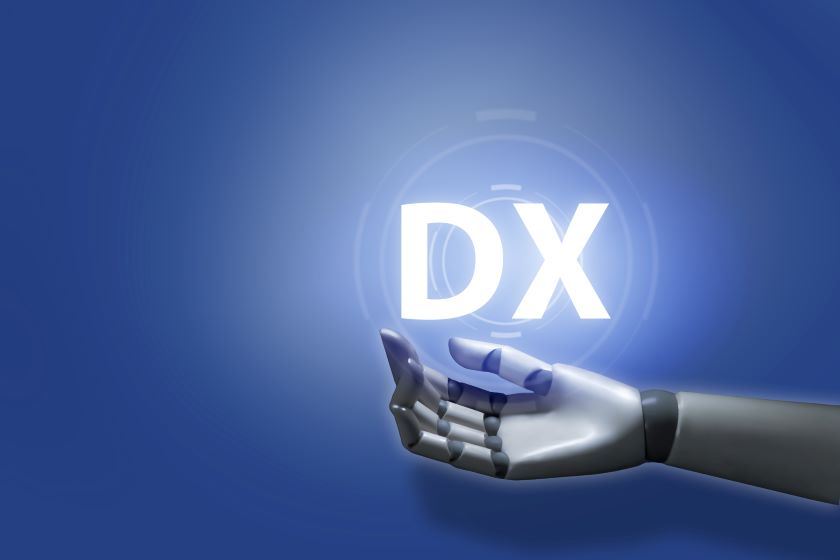
「何か良いシステムはないかな?」 と思ったときに読むコラム
2025.07.02
1.自社にとっての「良いシステム」とは何か?
「何か良いシステムはないかな?」と考えるとき、私たちは往々にして、他社の成功事例や最新のITトレンドに目を向けがちです。しかし、A社にとっての「良いシステム」が、必ずしも貴社にとっての「良いシステム」であるとは限りません。自社にとっての「良いシステム」とは、突き詰めて言えば、貴社の経営課題や業務課題を明確に解決し、具体的な目標達成に貢献するシステムです。
例えば、顧客からの問い合わせ対応に時間がかかり、顧客満足度が低下している課題がある場合、「良いシステム」とは顧客からの問い合わせを効率的に管理し、迅速な対応を可能にするCRM(顧客関係管理)システムかもしれません。あるいは、在庫管理が属人化しており、過剰在庫や欠品が頻発しているならば、正確な在庫情報をリアルタイムで把握できる生産管理システムが「良いシステム」となり得るでしょう。
重要なのは、システム導入ありきで考えるのではなく、まず貴社が抱える具体的な課題や、達成したい目標を明確にすることです。そして、その課題解決や目標達成のために、システムがどのような役割を果たすべきかを深く掘り下げて検討することが、「良いシステム」を見つけるための第一歩となります。
2.「良いシステム」の定義が曖昧なまま、システム会社へ直接問い合わせていませんか?
多くの企業が陥りやすいのが、「良いシステム」の定義が曖昧なまま、あるいは自社の課題が不明瞭なままシステム会社へ問い合わせをしてしまうことです。例えば、「最新の〇〇システムを導入したい」「他社でうまくいっている△△を導入できないか」といった漠然とした依頼では、システム会社も貴社の真のニーズを理解することが困難です。
結果として、システム会社からは一般的なパッケージ製品の紹介や、貴社の状況に合致しない提案がなされる可能性が高まります。最悪の場合、導入されたシステムが「思っていたものと違った」「結局、何の課題も解決されなかった」といった結果になりかねません。
これは、家を建てる際に「良い家を建てたい」とだけ言って工務店に丸投げするようなものです。「どんな家族構成か」「何部屋必要か」「どのような暮らしがしたいか」といった具体的な要望がなければ、住む人にとって本当に良い家は建ちません。システム導入もこれと同じで、自社の課題と目的を明確にし、システムに求める要件を具体的に整理することなくして、最適なシステムに出会うことはできないのです。
この「自社の課題と目的を明確にし、システムに求める要件を具体的に整理する」プロセスこそが、システム開発における上流工程であり、この工程を疎かにすることが、多くのシステム導入プロジェクト失敗の根本原因となっています。
3.システム導入の成功確度を高めるためのポイント
自社にとっての「良いシステム」を導入し、プロジェクトの成功確度を高めるためには、以下のポイントを強く意識する必要があります。
①現状の課題と目標を明確にする
まずは、自社の業務プロセスを徹底的に分析し、非効率な点、ボトルネックとなっている点、顧客からの不満点などを洗い出します。そして、それらの課題を解決することで、どのような状態を目指すのか、具体的な数値目標(例:〇〇の作業時間を△△%削減する、顧客満足度を〇〇%向上させるなど)を設定します。
②システムに求める要件を具体化する
課題と目標が明確になったら、それを解決するためにシステムがどのような機能を持つべきか、どのような性能が必要か、誰がどのように利用するか、といった要件を具体的に定義します。この際、現場の業務担当者の意見をしっかりとヒアリングし、現実的な要件と理想的な要件を区別し、優先順位を付けることが重要です。
③システム導入の目的を関係者間で共有する
経営層から現場の利用者まで、システム導入に関わるすべてのステークホルダーが、なぜこのシステムを導入するのか、導入によって何を達成したいのか、という目的を共有することが不可欠です。目的が共有されていれば、途中で生じるであろう様々な課題や困難に対しても、共通の認識を持って対処することができます。
④適切なパートナーを見つけるための準備をする
上記のプロセスを経て、自社の課題、目的、そしてシステムに求める具体的な要件が明確になれば、初めてシステム会社へ具体的な相談を始める準備が整ったと言えます。明確な情報を提供することで、システム会社も貴社に最適な提案をすることができ、費用対効果の高いシステム導入に繋がります。
これらのポイントは、システム開発における上流工程に相当します。この工程に十分な時間とリソースを投資し、徹底的に検討することで、貴社にとって本当に価値のある「良いシステム」に出会い、システム導入プロジェクトを成功へと導くことができるでしょう。
4.さいごに
システム導入において、ここまでに紹介した上流工程は「急がば回れ」の精神が非常に重要になります。一見すると、すぐにシステム会社に相談して見積もりを取り、開発を始めた方が早いように感じるかもしれません。しかし、課題や要件が曖昧なまま進めると、後になって大規模な手戻りが発生し、結果的に時間もコストも大幅にかかってしまうケースが少なくありません。
上流工程での綿密な準備は、まさに「遠回りに見えて、実は近道」なのです。この初期段階での丁寧な作業が、プロジェクト全体の進行をスムーズにし、最終的な成功へと最短で導く鍵となります。
貴社は、自社にとっての「良いシステム」を明確に定義できていますか?
7月28日(月)東京開催
【システム実演デモ付き】基幹システム刷新 成功事例セミナー
https://www.funaisoken.co.jp/seminar/130217 1.自社にとっての「良いシステム」とは何か?
「何か良いシステムはないかな?」と考えるとき、私たちは往々にして、他社の成功事例や最新のITトレンドに目を向けがちです。しかし、A社にとっての「良いシステム」が、必ずしも貴社にとっての「良いシステム」であるとは限りません。自社にとっての「良いシステム」とは、突き詰めて言えば、貴社の経営課題や業務課題を明確に解決し、具体的な目標達成に貢献するシステムです。
例えば、顧客からの問い合わせ対応に時間がかかり、顧客満足度が低下している課題がある場合、「良いシステム」とは顧客からの問い合わせを効率的に管理し、迅速な対応を可能にするCRM(顧客関係管理)システムかもしれません。あるいは、在庫管理が属人化しており、過剰在庫や欠品が頻発しているならば、正確な在庫情報をリアルタイムで把握できる生産管理システムが「良いシステム」となり得るでしょう。
重要なのは、システム導入ありきで考えるのではなく、まず貴社が抱える具体的な課題や、達成したい目標を明確にすることです。そして、その課題解決や目標達成のために、システムがどのような役割を果たすべきかを深く掘り下げて検討することが、「良いシステム」を見つけるための第一歩となります。
2.「良いシステム」の定義が曖昧なまま、システム会社へ直接問い合わせていませんか?
多くの企業が陥りやすいのが、「良いシステム」の定義が曖昧なまま、あるいは自社の課題が不明瞭なままシステム会社へ問い合わせをしてしまうことです。例えば、「最新の〇〇システムを導入したい」「他社でうまくいっている△△を導入できないか」といった漠然とした依頼では、システム会社も貴社の真のニーズを理解することが困難です。
結果として、システム会社からは一般的なパッケージ製品の紹介や、貴社の状況に合致しない提案がなされる可能性が高まります。最悪の場合、導入されたシステムが「思っていたものと違った」「結局、何の課題も解決されなかった」といった結果になりかねません。
これは、家を建てる際に「良い家を建てたい」とだけ言って工務店に丸投げするようなものです。「どんな家族構成か」「何部屋必要か」「どのような暮らしがしたいか」といった具体的な要望がなければ、住む人にとって本当に良い家は建ちません。システム導入もこれと同じで、自社の課題と目的を明確にし、システムに求める要件を具体的に整理することなくして、最適なシステムに出会うことはできないのです。
この「自社の課題と目的を明確にし、システムに求める要件を具体的に整理する」プロセスこそが、システム開発における上流工程であり、この工程を疎かにすることが、多くのシステム導入プロジェクト失敗の根本原因となっています。
3.システム導入の成功確度を高めるためのポイント
自社にとっての「良いシステム」を導入し、プロジェクトの成功確度を高めるためには、以下のポイントを強く意識する必要があります。
①現状の課題と目標を明確にする
まずは、自社の業務プロセスを徹底的に分析し、非効率な点、ボトルネックとなっている点、顧客からの不満点などを洗い出します。そして、それらの課題を解決することで、どのような状態を目指すのか、具体的な数値目標(例:〇〇の作業時間を△△%削減する、顧客満足度を〇〇%向上させるなど)を設定します。
②システムに求める要件を具体化する
課題と目標が明確になったら、それを解決するためにシステムがどのような機能を持つべきか、どのような性能が必要か、誰がどのように利用するか、といった要件を具体的に定義します。この際、現場の業務担当者の意見をしっかりとヒアリングし、現実的な要件と理想的な要件を区別し、優先順位を付けることが重要です。
③システム導入の目的を関係者間で共有する
経営層から現場の利用者まで、システム導入に関わるすべてのステークホルダーが、なぜこのシステムを導入するのか、導入によって何を達成したいのか、という目的を共有することが不可欠です。目的が共有されていれば、途中で生じるであろう様々な課題や困難に対しても、共通の認識を持って対処することができます。
④適切なパートナーを見つけるための準備をする
上記のプロセスを経て、自社の課題、目的、そしてシステムに求める具体的な要件が明確になれば、初めてシステム会社へ具体的な相談を始める準備が整ったと言えます。明確な情報を提供することで、システム会社も貴社に最適な提案をすることができ、費用対効果の高いシステム導入に繋がります。
これらのポイントは、システム開発における上流工程に相当します。この工程に十分な時間とリソースを投資し、徹底的に検討することで、貴社にとって本当に価値のある「良いシステム」に出会い、システム導入プロジェクトを成功へと導くことができるでしょう。
4.さいごに
システム導入において、ここまでに紹介した上流工程は「急がば回れ」の精神が非常に重要になります。一見すると、すぐにシステム会社に相談して見積もりを取り、開発を始めた方が早いように感じるかもしれません。しかし、課題や要件が曖昧なまま進めると、後になって大規模な手戻りが発生し、結果的に時間もコストも大幅にかかってしまうケースが少なくありません。
上流工程での綿密な準備は、まさに「遠回りに見えて、実は近道」なのです。この初期段階での丁寧な作業が、プロジェクト全体の進行をスムーズにし、最終的な成功へと最短で導く鍵となります。
貴社は、自社にとっての「良いシステム」を明確に定義できていますか?
7月28日(月)東京開催
【システム実演デモ付き】基幹システム刷新 成功事例セミナー
https://www.funaisoken.co.jp/seminar/130217