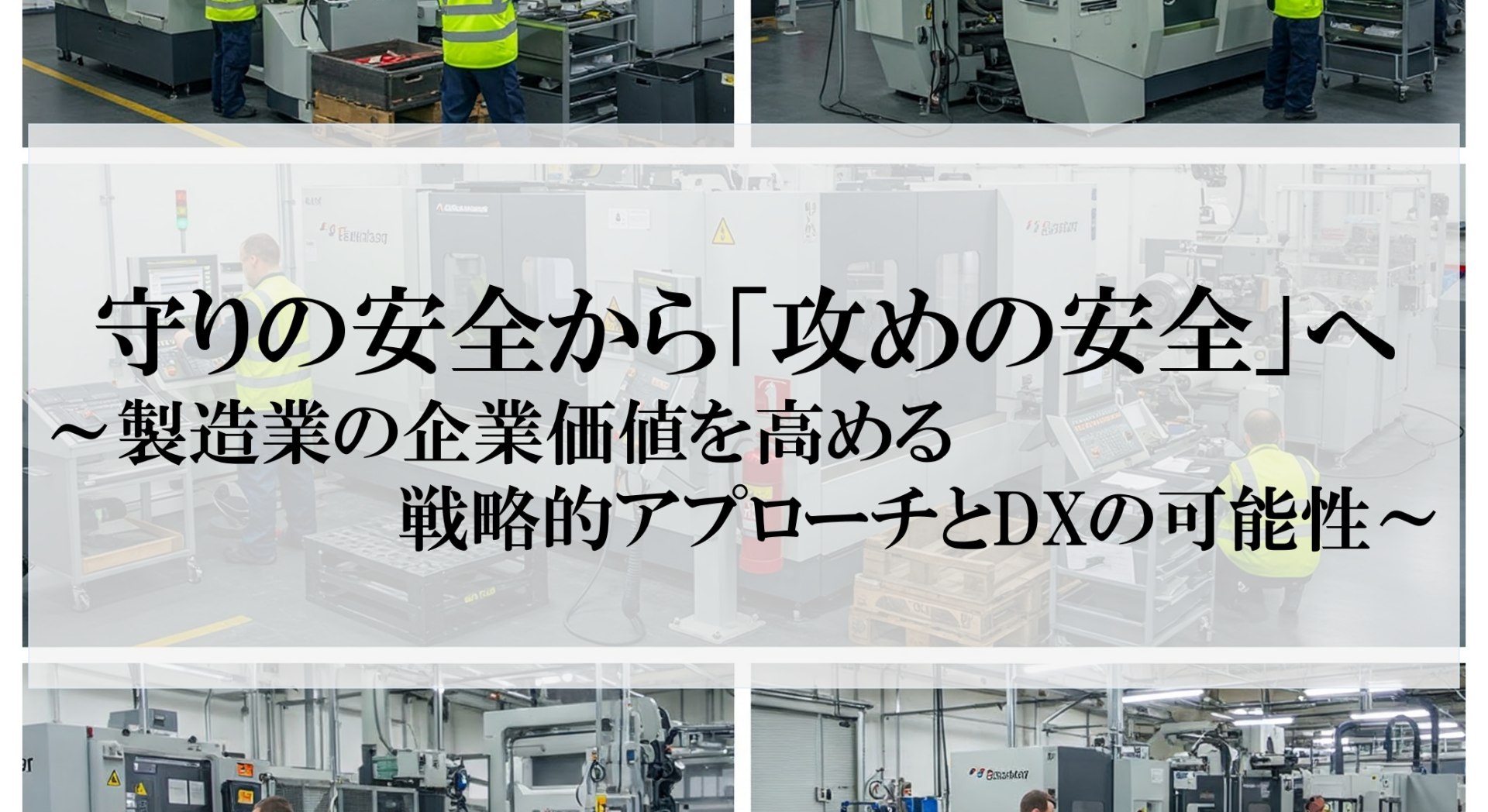
守りの安全から「攻めの安全」へ ~製造業の企業価値を高める戦略的アプローチとDXの可能性~
2025.05.27
いつもコラムをご愛読いただきありがとうございます。船井総合研究所の熊谷です。
昨今、私たち製造業を取り巻く環境は、人手不足の深刻化、原材料価格の高騰、そしてグローバル競争の激化など、かつてないほど複雑で厳しいものとなっています。このような状況下で、日々のオペレーションを維持し、さらなる成長を目指すために、経営者の皆様はコスト削減や生産性向上、新規市場開拓など、多岐にわたる課題に果敢に取り組んでいらっしゃることと存じます。
しかし、こうした経営努力の中で、ともすれば「コストセンター」として捉えられ、後回しにされがちな分野があります。それが「安全対策」です。
「安全は当たり前」「事故が起きてからでは遅い」とは誰もが理解しているものの、日々の業務に追われる中で、その戦略的な重要性を見過ごしてはいないでしょうか? 実は、この「安全対策」こそが、貴社の収益性を高め、従業員のエンゲージメントを向上させ、ひいては持続的な企業成長を実現するための「隠れた鍵」であるとしたら、どう思われますか?
本日は、長年多くの製造業の経営支援に携わってきたプロの経営コンサルタントとして、なぜ今こそ「安全対策」に真剣に向き合うべきなのか、そしてそれが具体的にどのような経営効果をもたらし、未来の成長に繋がるのか、その核心に迫りたいと思います。
https://www.funaisoken.co.jp/dl-contents/smart-factory_smart-factory_00000153_S045?media=smart-factory_S045
第1フェーズ: 「いつかやろう」では手遅れ? 安全対策を怠る真のコストとは
多くの経営者様が「安全対策にはコストがかかる」とお考えかもしれません。確かに、設備投資や教育訓練には初期費用が必要です。しかし、一度立ち止まって考えてみてください。もし、労働災害が発生してしまった場合、企業が負担するコストは、その初期費用を遥かに上回る可能性があるのです。
1.1. 目に見える「直接コスト」だけではない、甚大な「間接コスト」
労働災害が発生すると、治療費や休業補償といった直接的な費用が発生します。しかし、これは氷山の一角に過ぎません。本当に恐ろしいのは、その背後に隠れている「間接コスト」です。
例えば、
生産ラインの停止・遅延: 事故処理や原因究明のために生産がストップし、納期遅延や機会損失に繋がります。
設備の破損・修理コスト: 事故によって高価な機械設備が破損すれば、その修理や買い替えに多額の費用と時間がかかります。
代替要員の確保・教育コスト: 被災した従業員の代わりに新たな人員を配置したり、既存の従業員に残業を強いたりする必要が生じ、人件費の増加や業務負担の偏りを招きます。
企業イメージの失墜・社会的信用の低下: 「安全管理ができていない企業」というレッテルは、顧客離れや取引停止、採用難といった形で、長期的に経営を蝕みます。特に近年は、企業の社会的責任(CSR)やESG経営への関心が高まっており、安全衛生に対する取り組みは、投資家や地域社会からの評価にも直結します。
従業員の士気低下・離職率の増加: 職場の安全性が担保されていないと感じれば、従業員のモチベーションは著しく低下し、最悪の場合、優秀な人材の流出を招きかねません。これは、人手不足が叫ばれる現代において、計り知れない損失です。
行政処分・罰金・訴訟リスク: 労働安全衛生法違反による行政指導や罰金、さらには民事訴訟のリスクも伴います。
これらの間接コストは、直接コストの数倍から数十倍にものぼると言われています。つまり、目先の安全対策費用を惜しんだ結果、将来的にそれ以上の経済的損失を被る可能性があるのです。
1.2. 厳格化する法規制と社会の目
近年、労働安全衛生に関する法規制は年々厳格化しており、企業に求められる安全配慮義務のレベルも高まっています。ひとたび重大な事故が発生すれば、法的な責任を問われるだけでなく、メディアを通じて瞬く間に情報が拡散し、企業の存続すら危ぶまれる事態になりかねません。「知らなかった」「手が回らなかった」では済まされない時代なのです。
安全対策は、もはや「任意」の取り組みではなく、企業が事業を継続していく上での「必須要件」と言えるでしょう。
1.3. 「予防」こそ最大のコスト削減
結局のところ、事故が起きてから対応する「事後処理」には、莫大な費用と時間がかかります。一方で、事故を未然に防ぐための「予防」にかけるコストは、それに比べれば遥かに小さいものです。ある調査によれば、安全対策に1単位の費用を投じることで、2.7単位の経済効果が得られるというデータもあります。これは、安全対策が決して「コスト」ではなく、将来の損失を防ぎ、むしろ利益を生み出す「投資」であることを明確に示しています。
「まだ大丈夫だろう」「ウチは事故なんて起きない」といった楽観的な見通しは禁物です。問題が顕在化してからでは、取り返しがつかない事態を招く可能性があります。今こそ、安全対策の優先順位を上げ、真剣に取り組むべき時なのです。
第2フェーズ: 守りから攻めへ! 「安全対策」を成長戦略に転換する発想
さて、安全対策の重要性について、主にリスク管理の側面からお話ししました。しかし、私たちが提唱したいのは、さらに一歩進んだ「攻めの安全対策」です。つまり、安全対策を単なるコストや義務として捉えるのではなく、企業の競争力を高め、持続的な成長を牽引する「戦略的投資」として位置づけるという発想の転換です。
2.1. 生産性の向上と品質の安定
安全な職場環境は、従業員が安心して業務に集中できる基盤となります。危険を感じながら作業するのと、安全が確保された環境で作業するのとでは、生産性や作業品質に大きな差が出ることは明らかです。
ヒューマンエラーの削減: 不安全な状態や行動が減ることで、ミスや手戻りが減少し、生産効率が向上します。
設備稼働率の向上: 適切な保守・点検が行き届いた設備は故障しにくく、突発的なライン停止を防ぎ、計画通りの生産を可能にします。
品質の向上: 安定した作業環境と従業員の集中力向上は、製品の品質向上・均一化にも繋がり、不良品の削減や顧客満足度の向上に貢献します。
実際に、安全対策に積極的に取り組む企業では、生産性が向上し、不良率が低下したという事例は枚挙にいとまがありません。
2.2. 従業員エンゲージメントと人材獲得力の強化
「企業は人なり」とよく言われます。特に専門技術が求められる製造業において、従業員は最も重要な経営資源です。そして、その大切な従業員が心身ともに健康で、意欲的に働ける環境を提供することは、経営者の責務であり、企業の成長に不可欠です。
従業員のモチベーション向上: 会社が自分たちの安全と健康を第一に考えてくれていると感じることで、従業員の会社に対する信頼感や愛着(エンゲージメント)が高まります。
離職率の低下と定着率の向上: 安心して長く働ける職場は、経験豊富な従業員の定着を促し、採用・教育コストの削減にも繋がります。
採用競争力の強化: 「安全で働きやすい会社」という評判は、特に若い世代や優秀な人材にとって大きな魅力となります。人手不足が深刻化する中で、採用における優位性を確立できます。
安全への投資は、従業員の満足度を高め、結果として企業の「人的資本」を豊かにするのです。
2.3. 「安全文化」の醸成とイノベーションの促進
トップが安全に対する明確な方針を示し、全従業員が安全意識を共有する「安全文化」が醸成されると、組織には様々なプラスの効果が生まれます。
コミュニケーションの活性化: 危険箇所やヒヤリハット情報を積極的に報告・共有する風土は、部門間の壁を超えたコミュニケーションを促します。
問題発見・解決能力の向上: 従業員一人ひとりが主体的に職場のリスクを探し、改善提案を行うようになることで、現場起点のボトムアップ型改善が進みます。
イノベーションの土壌: 心理的安全性が確保された職場では、従業員が失敗を恐れずに新しいアイデアや挑戦をしやすくなり、イノベーションが生まれやすい環境が育まれます。
「安全」という共通の価値観を通じて組織の一体感を高め、変化に強く、自律的に成長できる企業体質を構築することができるのです。
このように、安全対策は、リスクを低減する「守り」の側面だけでなく、企業の収益性、人材力、組織力を高める「攻め」の経営戦略として、極めて重要な位置を占めるのです。
第3フェーズ: 未来を拓く「安全対策DX」 – テクノロジーが実現する次世代の安全管理
「安全対策の重要性は理解できた。しかし、具体的に何から始めれば良いのか?」「人手不足の中で、これ以上管理業務を増やせない」といったお悩みをお持ちの経営者様もいらっしゃるかもしれません。そこで注目したいのが、AIやIoTといった最新テクノロジーを活用した「安全対策DX(デジタルトランスフォーメーション)」です。
安全対策DXは、従来のマンパワーに頼った管理方法の限界を突破し、より効率的で効果的な安全管理を実現する新たな一手です。
3.1. 見えなかった危険を「見える化」するIoT・AI
作業員の安全見守り: ウェアラブルデバイスを活用し、作業員のバイタルデータ(心拍数、体温など)や位置情報をリアルタイムに把握。転倒や急病などの異常を即座に検知し、迅速な対応を可能にします。また、危険エリアへの立ち入りを警告することも可能です。
危険予知・異常検知: 工場内の設備や作業環境に設置したセンサーから収集したデータをAIが分析し、事故に繋がる可能性のあるわずかな変化や異常(設備の振動、温度変化、有害物質の濃度上昇など)を早期に検知。事故を未然に防ぐ「予知保全」の精度を高めます。
画像認識による不安全行動の検出: カメラ映像をAIが解析し、ヘルメットの未着用、安全帯の不使用、禁止エリアへの侵入といった不安全行動を自動で検出し、警告を発します。これにより、管理者の監視業務の負担を軽減しつつ、ヒューマンエラーによる事故リスクを低減します。
3.2. ベテランの技を「形式知化」し、技術伝承を促進
製造現場では、ベテラン作業員の経験や勘に頼る部分が多く、その技術やノウハウの伝承が大きな課題となっています。安全管理も例外ではありません。
スマートグラスを活用した遠隔作業支援・教育: 経験の浅い作業員がスマートグラスを装着し、熟練者からリアルタイムで指示やアドバイスを受けながら作業を行うことができます。これにより、OJTの質が向上し、安全な作業手順の早期習得を支援します。
作業手順のデジタル化と動画マニュアル: 紙ベースの作業手順書をデジタル化し、タブレット端末などで誰でも簡単に確認できるようにします。特に危険作業については、動画マニュアルを作成することで、より直感的に正しい作業方法を伝え、誤操作を防ぎます。
AIによる過去の事故事例分析と対策の最適化: 過去のヒヤリハット事例や事故事例のデータをAIが分析し、類似の状況下での最適な安全対策を提示。経験の浅い担当者でも、データに基づいた効果的な対策を立案できるようになります。
3.3. データドリブンな安全活動と継続的改善
DXの最大の強みは、あらゆる活動をデータに基づいて客観的に評価し、継続的な改善に繋げられる点です。
安全活動実績のデジタル管理・分析: 安全パトロールの結果、ヒヤリハット報告、教育訓練の実施状況などをデジタルデータとして一元管理。これらのデータを多角的に分析することで、安全活動の傾向や課題を客観的に把握し、より効果的な対策へと繋げることができます。
リスクアセスメントの効率化・高度化: 従来、多くの工数を要していたリスクアセスメントも、AIを活用することで、潜在的な危険源の特定やリスクレベルの評価を効率的かつ高精度に行うことが可能になります。
安全文化の定量的評価: 従業員の安全意識や行動変容をアンケートやシステムログなどから定量的に把握し、安全文化醸成の進捗度を可視化。目標設定や施策の効果測定に役立てます。
安全対策DXは、単に新しい技術を導入するということではありません。テクノロジーの力を借りて、安全管理のあり方そのものを変革し、より本質的で持続可能な安全体制を構築することを目指すものです。これにより、人的リソースへの過度な依存から脱却し、より戦略的で付加価値の高い安全活動へとシフトすることが可能になります。
「DXは難しそうだ」「うちの会社にはまだ早い」と感じる経営者様もいらっしゃるかもしれませんが、スモールスタートからでも始められるDXは数多く存在します。重要なのは、まず第一歩を踏み出すことです。
第4フェーズ: 安全と成長を両立させる未来へ – まずは現状認識から
ここまで、安全対策の重要性、その経営効果、そしてDXによる進化の可能性についてお話ししてきました。安全対策は、もはやコストではなく、企業の未来を左右する「戦略的投資」であるということをご理解いただけたのではないでしょうか。
従業員が安全に、安心して働ける環境を整備することは、生産性の向上、品質の向上、従業員エンゲージメントの強化、そして企業価値の向上へと繋がります。それは、まさに経営者が目指すべき「安全と成長の両立」の姿です。
しかし、何から手をつければ良いのか、自社の現状はどうなっているのか、具体的な進め方がわからない、という方もいらっしゃるでしょう。そのような経営者の皆様のために、私たちはこの度、**「【製造業向け】安全対策の経営効果と具体的な手法」**と題した詳細レポートをご用意いたしました。
このレポートでは、
なぜ今、製造業で安全対策が最重要経営課題なのか?(労働災害の現状、法規制の動向)
安全対策がもたらす具体的な経営効果とは?(定量的な効果、定性的な効果を徹底解説)
明日から実践できる具体的な安全対策の手法とは?(組織体制構築、リスクアセスメント、教育・訓練、5S活動から人間工学の活用まで網羅)
最先端の「安全対策DX」とは何か?(AI・IoTを活用した予知保全、不良品検知、技術伝承などの最新事例を多数紹介)
安全と成長を両立し、企業価値を高めるためのステップとは?
など、製造業の経営者様が知りたい情報を、豊富なデータと具体的な事例を交えながら、分かりやすく解説しています。長年、数多くの製造業のコンサルティングを手掛けてきた船井総合研究所の知見を結集した、実践的な内容となっております。
このレポートをダウンロードすることで、貴社は以下のメリットを得ることができます。
安全対策の費用対効果を明確に理解し、社内での意識改革を推進できる。
自社の課題に合わせた具体的な安全対策のヒントを見つけ、すぐに実行に移せる。
AIやIoTといった最新技術を安全管理に導入するための具体的なイメージが湧く。
「安全」を軸とした企業文化を醸成し、従業員の満足度と生産性を同時に高める道筋が見える。
安全投資を経営戦略に組み込み、持続的な企業成長を実現するための羅針盤となる。
ご多忙な経営者の皆様にも効率的に情報収集していただけるよう、ポイントを絞って構成しております。このレポートが、貴社の安全対策を新たなステージへと引き上げ、輝かしい未来を築くための一助となれば幸いです。
▼「【製造業向け】安全対策の経営効果と具体的な手法」レポートの無料ダウンロードはこちらから
https://www.funaisoken.co.jp/dl-contents/smart-factory_smart-factory_00000153_S045?media=smart-factory_S045
終わりに: 安全が未来を創る – 成長への確かな一歩を共に
私たち経営コンサルタントは、企業の成長と発展を支援することをミッションとしています。そして、その根幹には、そこで働く「人」の安全と健康が不可欠であると確信しています。
安全対策は、一朝一夕に完成するものではありません。しかし、経営者様が強いリーダーシップを発揮し、全社一丸となって取り組むことで、必ずや大きな成果を生み出します。それは、労働災害の削減といった直接的な効果に留まらず、生産性の向上、従業員の士気高揚、そして社会からの信頼獲得といった、企業価値を高める様々な好循環を生み出すのです。
本日のコラムが、皆様にとって、安全対策の重要性を再認識し、未来への新たな一歩を踏み出すきっかけとなれば、これに勝る喜びはありません。
レポートを手に取っていただき、貴社のさらなる発展にお役立てください。私たち船井総合研究所は、安全と成長の両立を目指す製造業の皆様を、全力でサポートさせていただきます。
https://www.funaisoken.co.jp/dl-contents/smart-factory_smart-factory_00000153_S045?media=smart-factory_S045 いつもコラムをご愛読いただきありがとうございます。船井総合研究所の熊谷です。
昨今、私たち製造業を取り巻く環境は、人手不足の深刻化、原材料価格の高騰、そしてグローバル競争の激化など、かつてないほど複雑で厳しいものとなっています。このような状況下で、日々のオペレーションを維持し、さらなる成長を目指すために、経営者の皆様はコスト削減や生産性向上、新規市場開拓など、多岐にわたる課題に果敢に取り組んでいらっしゃることと存じます。
しかし、こうした経営努力の中で、ともすれば「コストセンター」として捉えられ、後回しにされがちな分野があります。それが「安全対策」です。
「安全は当たり前」「事故が起きてからでは遅い」とは誰もが理解しているものの、日々の業務に追われる中で、その戦略的な重要性を見過ごしてはいないでしょうか? 実は、この「安全対策」こそが、貴社の収益性を高め、従業員のエンゲージメントを向上させ、ひいては持続的な企業成長を実現するための「隠れた鍵」であるとしたら、どう思われますか?
本日は、長年多くの製造業の経営支援に携わってきたプロの経営コンサルタントとして、なぜ今こそ「安全対策」に真剣に向き合うべきなのか、そしてそれが具体的にどのような経営効果をもたらし、未来の成長に繋がるのか、その核心に迫りたいと思います。
https://www.funaisoken.co.jp/dl-contents/smart-factory_smart-factory_00000153_S045?media=smart-factory_S045
第1フェーズ: 「いつかやろう」では手遅れ? 安全対策を怠る真のコストとは
多くの経営者様が「安全対策にはコストがかかる」とお考えかもしれません。確かに、設備投資や教育訓練には初期費用が必要です。しかし、一度立ち止まって考えてみてください。もし、労働災害が発生してしまった場合、企業が負担するコストは、その初期費用を遥かに上回る可能性があるのです。
1.1. 目に見える「直接コスト」だけではない、甚大な「間接コスト」
労働災害が発生すると、治療費や休業補償といった直接的な費用が発生します。しかし、これは氷山の一角に過ぎません。本当に恐ろしいのは、その背後に隠れている「間接コスト」です。
例えば、
生産ラインの停止・遅延: 事故処理や原因究明のために生産がストップし、納期遅延や機会損失に繋がります。
設備の破損・修理コスト: 事故によって高価な機械設備が破損すれば、その修理や買い替えに多額の費用と時間がかかります。
代替要員の確保・教育コスト: 被災した従業員の代わりに新たな人員を配置したり、既存の従業員に残業を強いたりする必要が生じ、人件費の増加や業務負担の偏りを招きます。
企業イメージの失墜・社会的信用の低下: 「安全管理ができていない企業」というレッテルは、顧客離れや取引停止、採用難といった形で、長期的に経営を蝕みます。特に近年は、企業の社会的責任(CSR)やESG経営への関心が高まっており、安全衛生に対する取り組みは、投資家や地域社会からの評価にも直結します。
従業員の士気低下・離職率の増加: 職場の安全性が担保されていないと感じれば、従業員のモチベーションは著しく低下し、最悪の場合、優秀な人材の流出を招きかねません。これは、人手不足が叫ばれる現代において、計り知れない損失です。
行政処分・罰金・訴訟リスク: 労働安全衛生法違反による行政指導や罰金、さらには民事訴訟のリスクも伴います。
これらの間接コストは、直接コストの数倍から数十倍にものぼると言われています。つまり、目先の安全対策費用を惜しんだ結果、将来的にそれ以上の経済的損失を被る可能性があるのです。
1.2. 厳格化する法規制と社会の目
近年、労働安全衛生に関する法規制は年々厳格化しており、企業に求められる安全配慮義務のレベルも高まっています。ひとたび重大な事故が発生すれば、法的な責任を問われるだけでなく、メディアを通じて瞬く間に情報が拡散し、企業の存続すら危ぶまれる事態になりかねません。「知らなかった」「手が回らなかった」では済まされない時代なのです。
安全対策は、もはや「任意」の取り組みではなく、企業が事業を継続していく上での「必須要件」と言えるでしょう。
1.3. 「予防」こそ最大のコスト削減
結局のところ、事故が起きてから対応する「事後処理」には、莫大な費用と時間がかかります。一方で、事故を未然に防ぐための「予防」にかけるコストは、それに比べれば遥かに小さいものです。ある調査によれば、安全対策に1単位の費用を投じることで、2.7単位の経済効果が得られるというデータもあります。これは、安全対策が決して「コスト」ではなく、将来の損失を防ぎ、むしろ利益を生み出す「投資」であることを明確に示しています。
「まだ大丈夫だろう」「ウチは事故なんて起きない」といった楽観的な見通しは禁物です。問題が顕在化してからでは、取り返しがつかない事態を招く可能性があります。今こそ、安全対策の優先順位を上げ、真剣に取り組むべき時なのです。
第2フェーズ: 守りから攻めへ! 「安全対策」を成長戦略に転換する発想
さて、安全対策の重要性について、主にリスク管理の側面からお話ししました。しかし、私たちが提唱したいのは、さらに一歩進んだ「攻めの安全対策」です。つまり、安全対策を単なるコストや義務として捉えるのではなく、企業の競争力を高め、持続的な成長を牽引する「戦略的投資」として位置づけるという発想の転換です。
2.1. 生産性の向上と品質の安定
安全な職場環境は、従業員が安心して業務に集中できる基盤となります。危険を感じながら作業するのと、安全が確保された環境で作業するのとでは、生産性や作業品質に大きな差が出ることは明らかです。
ヒューマンエラーの削減: 不安全な状態や行動が減ることで、ミスや手戻りが減少し、生産効率が向上します。
設備稼働率の向上: 適切な保守・点検が行き届いた設備は故障しにくく、突発的なライン停止を防ぎ、計画通りの生産を可能にします。
品質の向上: 安定した作業環境と従業員の集中力向上は、製品の品質向上・均一化にも繋がり、不良品の削減や顧客満足度の向上に貢献します。
実際に、安全対策に積極的に取り組む企業では、生産性が向上し、不良率が低下したという事例は枚挙にいとまがありません。
2.2. 従業員エンゲージメントと人材獲得力の強化
「企業は人なり」とよく言われます。特に専門技術が求められる製造業において、従業員は最も重要な経営資源です。そして、その大切な従業員が心身ともに健康で、意欲的に働ける環境を提供することは、経営者の責務であり、企業の成長に不可欠です。
従業員のモチベーション向上: 会社が自分たちの安全と健康を第一に考えてくれていると感じることで、従業員の会社に対する信頼感や愛着(エンゲージメント)が高まります。
離職率の低下と定着率の向上: 安心して長く働ける職場は、経験豊富な従業員の定着を促し、採用・教育コストの削減にも繋がります。
採用競争力の強化: 「安全で働きやすい会社」という評判は、特に若い世代や優秀な人材にとって大きな魅力となります。人手不足が深刻化する中で、採用における優位性を確立できます。
安全への投資は、従業員の満足度を高め、結果として企業の「人的資本」を豊かにするのです。
2.3. 「安全文化」の醸成とイノベーションの促進
トップが安全に対する明確な方針を示し、全従業員が安全意識を共有する「安全文化」が醸成されると、組織には様々なプラスの効果が生まれます。
コミュニケーションの活性化: 危険箇所やヒヤリハット情報を積極的に報告・共有する風土は、部門間の壁を超えたコミュニケーションを促します。
問題発見・解決能力の向上: 従業員一人ひとりが主体的に職場のリスクを探し、改善提案を行うようになることで、現場起点のボトムアップ型改善が進みます。
イノベーションの土壌: 心理的安全性が確保された職場では、従業員が失敗を恐れずに新しいアイデアや挑戦をしやすくなり、イノベーションが生まれやすい環境が育まれます。
「安全」という共通の価値観を通じて組織の一体感を高め、変化に強く、自律的に成長できる企業体質を構築することができるのです。
このように、安全対策は、リスクを低減する「守り」の側面だけでなく、企業の収益性、人材力、組織力を高める「攻め」の経営戦略として、極めて重要な位置を占めるのです。
第3フェーズ: 未来を拓く「安全対策DX」 – テクノロジーが実現する次世代の安全管理
「安全対策の重要性は理解できた。しかし、具体的に何から始めれば良いのか?」「人手不足の中で、これ以上管理業務を増やせない」といったお悩みをお持ちの経営者様もいらっしゃるかもしれません。そこで注目したいのが、AIやIoTといった最新テクノロジーを活用した「安全対策DX(デジタルトランスフォーメーション)」です。
安全対策DXは、従来のマンパワーに頼った管理方法の限界を突破し、より効率的で効果的な安全管理を実現する新たな一手です。
3.1. 見えなかった危険を「見える化」するIoT・AI
作業員の安全見守り: ウェアラブルデバイスを活用し、作業員のバイタルデータ(心拍数、体温など)や位置情報をリアルタイムに把握。転倒や急病などの異常を即座に検知し、迅速な対応を可能にします。また、危険エリアへの立ち入りを警告することも可能です。
危険予知・異常検知: 工場内の設備や作業環境に設置したセンサーから収集したデータをAIが分析し、事故に繋がる可能性のあるわずかな変化や異常(設備の振動、温度変化、有害物質の濃度上昇など)を早期に検知。事故を未然に防ぐ「予知保全」の精度を高めます。
画像認識による不安全行動の検出: カメラ映像をAIが解析し、ヘルメットの未着用、安全帯の不使用、禁止エリアへの侵入といった不安全行動を自動で検出し、警告を発します。これにより、管理者の監視業務の負担を軽減しつつ、ヒューマンエラーによる事故リスクを低減します。
3.2. ベテランの技を「形式知化」し、技術伝承を促進
製造現場では、ベテラン作業員の経験や勘に頼る部分が多く、その技術やノウハウの伝承が大きな課題となっています。安全管理も例外ではありません。
スマートグラスを活用した遠隔作業支援・教育: 経験の浅い作業員がスマートグラスを装着し、熟練者からリアルタイムで指示やアドバイスを受けながら作業を行うことができます。これにより、OJTの質が向上し、安全な作業手順の早期習得を支援します。
作業手順のデジタル化と動画マニュアル: 紙ベースの作業手順書をデジタル化し、タブレット端末などで誰でも簡単に確認できるようにします。特に危険作業については、動画マニュアルを作成することで、より直感的に正しい作業方法を伝え、誤操作を防ぎます。
AIによる過去の事故事例分析と対策の最適化: 過去のヒヤリハット事例や事故事例のデータをAIが分析し、類似の状況下での最適な安全対策を提示。経験の浅い担当者でも、データに基づいた効果的な対策を立案できるようになります。
3.3. データドリブンな安全活動と継続的改善
DXの最大の強みは、あらゆる活動をデータに基づいて客観的に評価し、継続的な改善に繋げられる点です。
安全活動実績のデジタル管理・分析: 安全パトロールの結果、ヒヤリハット報告、教育訓練の実施状況などをデジタルデータとして一元管理。これらのデータを多角的に分析することで、安全活動の傾向や課題を客観的に把握し、より効果的な対策へと繋げることができます。
リスクアセスメントの効率化・高度化: 従来、多くの工数を要していたリスクアセスメントも、AIを活用することで、潜在的な危険源の特定やリスクレベルの評価を効率的かつ高精度に行うことが可能になります。
安全文化の定量的評価: 従業員の安全意識や行動変容をアンケートやシステムログなどから定量的に把握し、安全文化醸成の進捗度を可視化。目標設定や施策の効果測定に役立てます。
安全対策DXは、単に新しい技術を導入するということではありません。テクノロジーの力を借りて、安全管理のあり方そのものを変革し、より本質的で持続可能な安全体制を構築することを目指すものです。これにより、人的リソースへの過度な依存から脱却し、より戦略的で付加価値の高い安全活動へとシフトすることが可能になります。
「DXは難しそうだ」「うちの会社にはまだ早い」と感じる経営者様もいらっしゃるかもしれませんが、スモールスタートからでも始められるDXは数多く存在します。重要なのは、まず第一歩を踏み出すことです。
第4フェーズ: 安全と成長を両立させる未来へ – まずは現状認識から
ここまで、安全対策の重要性、その経営効果、そしてDXによる進化の可能性についてお話ししてきました。安全対策は、もはやコストではなく、企業の未来を左右する「戦略的投資」であるということをご理解いただけたのではないでしょうか。
従業員が安全に、安心して働ける環境を整備することは、生産性の向上、品質の向上、従業員エンゲージメントの強化、そして企業価値の向上へと繋がります。それは、まさに経営者が目指すべき「安全と成長の両立」の姿です。
しかし、何から手をつければ良いのか、自社の現状はどうなっているのか、具体的な進め方がわからない、という方もいらっしゃるでしょう。そのような経営者の皆様のために、私たちはこの度、**「【製造業向け】安全対策の経営効果と具体的な手法」**と題した詳細レポートをご用意いたしました。
このレポートでは、
なぜ今、製造業で安全対策が最重要経営課題なのか?(労働災害の現状、法規制の動向)
安全対策がもたらす具体的な経営効果とは?(定量的な効果、定性的な効果を徹底解説)
明日から実践できる具体的な安全対策の手法とは?(組織体制構築、リスクアセスメント、教育・訓練、5S活動から人間工学の活用まで網羅)
最先端の「安全対策DX」とは何か?(AI・IoTを活用した予知保全、不良品検知、技術伝承などの最新事例を多数紹介)
安全と成長を両立し、企業価値を高めるためのステップとは?
など、製造業の経営者様が知りたい情報を、豊富なデータと具体的な事例を交えながら、分かりやすく解説しています。長年、数多くの製造業のコンサルティングを手掛けてきた船井総合研究所の知見を結集した、実践的な内容となっております。
このレポートをダウンロードすることで、貴社は以下のメリットを得ることができます。
安全対策の費用対効果を明確に理解し、社内での意識改革を推進できる。
自社の課題に合わせた具体的な安全対策のヒントを見つけ、すぐに実行に移せる。
AIやIoTといった最新技術を安全管理に導入するための具体的なイメージが湧く。
「安全」を軸とした企業文化を醸成し、従業員の満足度と生産性を同時に高める道筋が見える。
安全投資を経営戦略に組み込み、持続的な企業成長を実現するための羅針盤となる。
ご多忙な経営者の皆様にも効率的に情報収集していただけるよう、ポイントを絞って構成しております。このレポートが、貴社の安全対策を新たなステージへと引き上げ、輝かしい未来を築くための一助となれば幸いです。
▼「【製造業向け】安全対策の経営効果と具体的な手法」レポートの無料ダウンロードはこちらから
https://www.funaisoken.co.jp/dl-contents/smart-factory_smart-factory_00000153_S045?media=smart-factory_S045
終わりに: 安全が未来を創る – 成長への確かな一歩を共に
私たち経営コンサルタントは、企業の成長と発展を支援することをミッションとしています。そして、その根幹には、そこで働く「人」の安全と健康が不可欠であると確信しています。
安全対策は、一朝一夕に完成するものではありません。しかし、経営者様が強いリーダーシップを発揮し、全社一丸となって取り組むことで、必ずや大きな成果を生み出します。それは、労働災害の削減といった直接的な効果に留まらず、生産性の向上、従業員の士気高揚、そして社会からの信頼獲得といった、企業価値を高める様々な好循環を生み出すのです。
本日のコラムが、皆様にとって、安全対策の重要性を再認識し、未来への新たな一歩を踏み出すきっかけとなれば、これに勝る喜びはありません。
レポートを手に取っていただき、貴社のさらなる発展にお役立てください。私たち船井総合研究所は、安全と成長の両立を目指す製造業の皆様を、全力でサポートさせていただきます。
https://www.funaisoken.co.jp/dl-contents/smart-factory_smart-factory_00000153_S045?media=smart-factory_S045