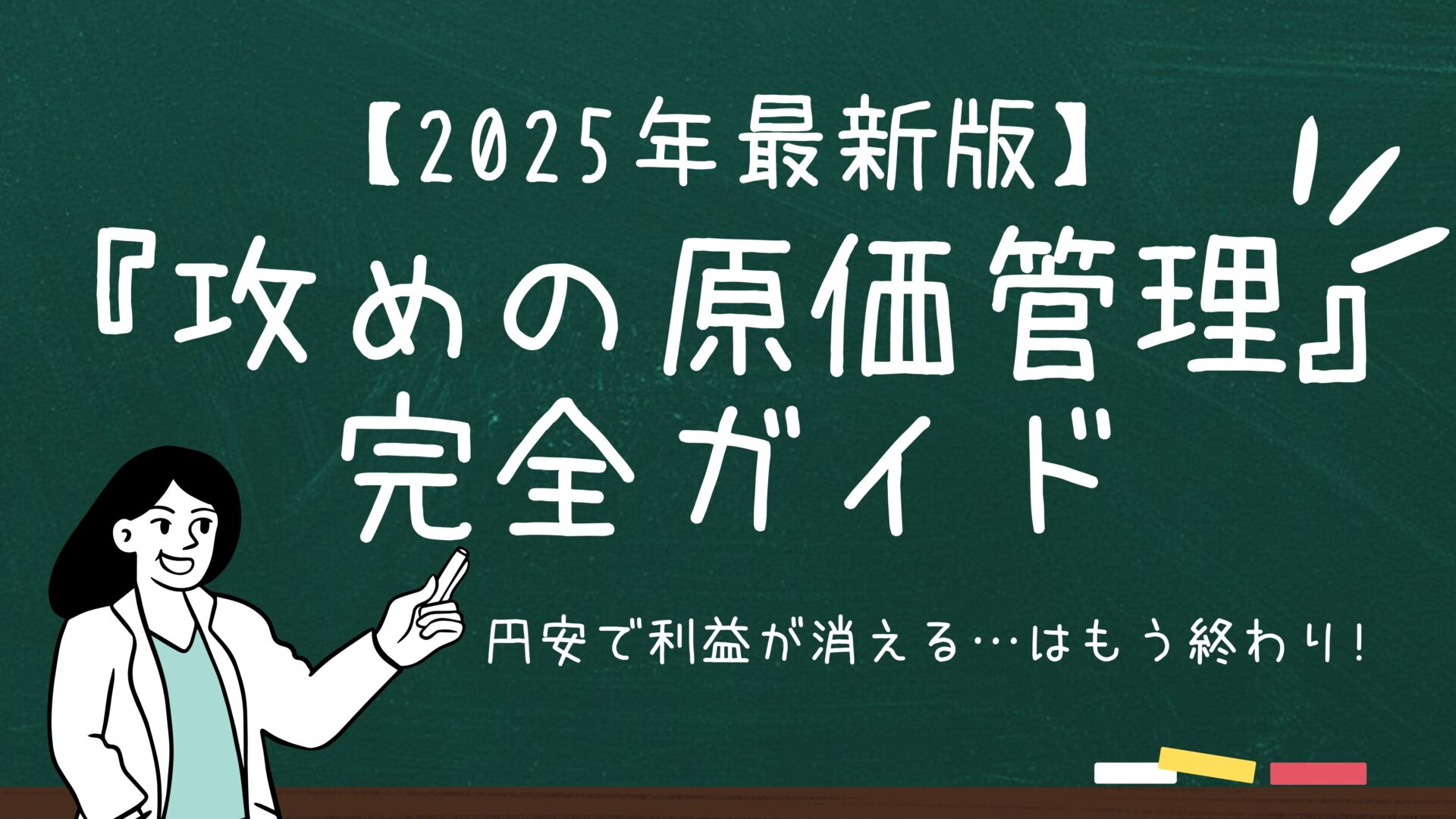
【2025年最新版】円安で利益が消える…はもう終わり。専門家が教える、価格転嫁を成功させる『攻めの原価管理』完全ガイド
2025.06.16
「また原材料が値上げか…」「電気代も高すぎる…」「コスト削減も、もう限界だ…」
2025年現在、記録的な円安と物価高騰の波に、多くの中小製造業の経営者様が悲鳴を上げています。必死にコストを切り詰めても、利益はあっという間に吹き飛んでしまう。そんな状況に、打つ手なしと感じてはいませんか?
しかし、諦めるのはまだ早いです。 従来の「守り」のコスト削減ではなく、自社の価値を正確にデータで示し、自信を持って価格転嫁を要求する『攻めの原価管理』こそが、今の時代を生き抜く唯一の道です。
本記事では、中堅・中小製造業専門のコンサルタントである筆者が、価格転嫁を成功に導くための具体的なステップを、体系的に解説します。
第1章:『どんぶり勘定』からの脱却。製造原価の正しい構造
すべての基本は「自社を正しく知る」ことから始まります。あなたの会社の一番の課題は、製品を作るのに「本当はいくらかかっているか」を、経営者自身が把握できていないことです。
製造原価は、大きく分けて「材料費」「労務費」「経費」の3つで構成されます。
材料費: 製品を作るための主原料や部品代。
労務費: 製造ラインで働く従業員の賃金。
経費: 工場の電気代、機械の減価償却費、消耗品費など。
これらを、「直接費(特定の製品に直接紐づく費用)」と「間接費(複数の製品にまたがる費用)」に分類することが、正確な原価計算の第一歩です。特に見落としがちなのが、事務所の家賃や管理部門の人件費といった「間接費」の配賦です。ここが曖昧だと、原価は全く不正確なものになります。
第2章:赤字製品を見抜け!製品別『活動基準原価計算(ABC)』超入門
「うちはA製品が儲かっているはずだ」…その常識、間違っているかもしれません。 間接費を売上高などで安易に配賦すると、手間のかかる少量生産品が不当に安く計算され、実は赤字なのに気づかない、という事態が起こります。
そこでおすすめしたいのが、簡易版の『活動基準原価計算(Activity-Based Costing)』です。
難しく考える必要はありません。「間接費が発生する原因(=コストドライバー)」を見つけ、その活動量に応じて費用を配賦する方法です。
簡単なステップ:
間接費を活動ごとに分類する(例:段取り、品質検査、運搬など)
活動の回数や時間などを製品ごとにカウントする
その回数に応じて、間接費を各製品に割り振る
これにより、「儲かっていると思っていた製品が実は赤字だった」「意外な製品が利益の柱だった」という衝撃の事実が明らかになります。
第3章:価格交渉で「ノー」と言わせない!データに基づく価格転嫁の技術
正確な原価が算出できれば、それは価格交渉における最強の「武器」になります。 「お願い」や「泣き落とし」では、相手もプロです、決して首を縦に振りません。必要なのは、客観的でロジカルなデータです。
交渉時に提示する資料のポイント:
原価構成の変化を示す: 「1年前と比較して、材料費が〇%、エネルギー費が△%上昇しました」と具体的な数字で示す。
貴社製品の原価計算書を提示: 「これらのコスト上昇により、貴社向けの製品XXXの原価は〇円から△円になっています」と明示する。
自助努力をアピール: 「弊社でもこれだけのコスト削減努力を行いましたが、吸収しきれない状況です」と伝える。
感情論を排し、事実とデータで交渉することで、相手は「仕方ない」と納得せざるを得なくなります。
IoTで実現する「リアルタイム原価管理」の世界
月締めでExcelに手入力…そんな原価管理はもう過去のものです。今は、安価なIoTセンサーを機械に取り付けるだけで、電力使用量や稼働時間をリアルタイムで収集できます。これにより、「昨日作った製品の、今日の時点での正確な原価」を把握することさえ可能になります。日々の改善活動が、即座に原価データに反映される。これは経営の意思決定を劇的に高速化させます。
▼関連記事「IoT導入による工場の見える化とは?成功事例と現場改革におけるメリット・注意点を紹介」
https://smart-factory.funaisoken.co.jp/250108-2/
まとめ:守りのコスト削減から、攻めの原価管理へ
厳しい時代だからこそ、経営者は自社の足元を深く見つめ直す必要があります。『攻めの原価管理』は、単なるコスト計算ではありません。自社の価値を再発見し、自信を取り戻し、未来を切り拓くための経営戦略そのものです。
▼関連記事「製造業必見! 6つのステップで解説!原価管理の取り組み方とは?」
https://smart-factory.funaisoken.co.jp/220714/
▼関連記事「原価管理システムとは?導入メリット・主要機能から失敗しない選び方までIT専門家が徹底解説!おすすめ注目を比較紹介」
https://smart-factory.funaisoken.co.jp/250603-2/
【ある企業では、たった6ヶ月で工場の生産数が1.2倍に!】
「なぜ、あの工程はいつも時間がかかるのだろう?」
「どうすれば、工場の生産能力を最大化できるのか?」
多くの場合、答えは現場に眠っているデータの中にあります。ある企業では、私たちのプログラムを通じてプレス工程がボトルネックであることをデータから発見。生産計画の見直しや人材の多能工化といった改善策を実行した結果、プレス工程の稼働率は20%向上し、工場全体の生産数が1.2倍に増加しました。
これは特別な事例ではありません。貴社の現場にも、まだ気づいていない大きな改善の可能性が眠っているはずです。船井総研の「6ヶ月集中・変革プログラム」で、貴社のポテンシャルを最大限に引き出します。
▼次はあなたの番です!お問い合わせはこちら。
https://formslp.funaisoken.co.jp/form01/lp/post/inquiry-S045.html?siteno=S045 「また原材料が値上げか…」「電気代も高すぎる…」「コスト削減も、もう限界だ…」
2025年現在、記録的な円安と物価高騰の波に、多くの中小製造業の経営者様が悲鳴を上げています。必死にコストを切り詰めても、利益はあっという間に吹き飛んでしまう。そんな状況に、打つ手なしと感じてはいませんか?
しかし、諦めるのはまだ早いです。 従来の「守り」のコスト削減ではなく、自社の価値を正確にデータで示し、自信を持って価格転嫁を要求する『攻めの原価管理』こそが、今の時代を生き抜く唯一の道です。
本記事では、中堅・中小製造業専門のコンサルタントである筆者が、価格転嫁を成功に導くための具体的なステップを、体系的に解説します。
第1章:『どんぶり勘定』からの脱却。製造原価の正しい構造
すべての基本は「自社を正しく知る」ことから始まります。あなたの会社の一番の課題は、製品を作るのに「本当はいくらかかっているか」を、経営者自身が把握できていないことです。
製造原価は、大きく分けて「材料費」「労務費」「経費」の3つで構成されます。
材料費: 製品を作るための主原料や部品代。
労務費: 製造ラインで働く従業員の賃金。
経費: 工場の電気代、機械の減価償却費、消耗品費など。
これらを、「直接費(特定の製品に直接紐づく費用)」と「間接費(複数の製品にまたがる費用)」に分類することが、正確な原価計算の第一歩です。特に見落としがちなのが、事務所の家賃や管理部門の人件費といった「間接費」の配賦です。ここが曖昧だと、原価は全く不正確なものになります。
第2章:赤字製品を見抜け!製品別『活動基準原価計算(ABC)』超入門
「うちはA製品が儲かっているはずだ」…その常識、間違っているかもしれません。 間接費を売上高などで安易に配賦すると、手間のかかる少量生産品が不当に安く計算され、実は赤字なのに気づかない、という事態が起こります。
そこでおすすめしたいのが、簡易版の『活動基準原価計算(Activity-Based Costing)』です。
難しく考える必要はありません。「間接費が発生する原因(=コストドライバー)」を見つけ、その活動量に応じて費用を配賦する方法です。
簡単なステップ:
間接費を活動ごとに分類する(例:段取り、品質検査、運搬など)
活動の回数や時間などを製品ごとにカウントする
その回数に応じて、間接費を各製品に割り振る
これにより、「儲かっていると思っていた製品が実は赤字だった」「意外な製品が利益の柱だった」という衝撃の事実が明らかになります。
第3章:価格交渉で「ノー」と言わせない!データに基づく価格転嫁の技術
正確な原価が算出できれば、それは価格交渉における最強の「武器」になります。 「お願い」や「泣き落とし」では、相手もプロです、決して首を縦に振りません。必要なのは、客観的でロジカルなデータです。
交渉時に提示する資料のポイント:
原価構成の変化を示す: 「1年前と比較して、材料費が〇%、エネルギー費が△%上昇しました」と具体的な数字で示す。
貴社製品の原価計算書を提示: 「これらのコスト上昇により、貴社向けの製品XXXの原価は〇円から△円になっています」と明示する。
自助努力をアピール: 「弊社でもこれだけのコスト削減努力を行いましたが、吸収しきれない状況です」と伝える。
感情論を排し、事実とデータで交渉することで、相手は「仕方ない」と納得せざるを得なくなります。
IoTで実現する「リアルタイム原価管理」の世界
月締めでExcelに手入力…そんな原価管理はもう過去のものです。今は、安価なIoTセンサーを機械に取り付けるだけで、電力使用量や稼働時間をリアルタイムで収集できます。これにより、「昨日作った製品の、今日の時点での正確な原価」を把握することさえ可能になります。日々の改善活動が、即座に原価データに反映される。これは経営の意思決定を劇的に高速化させます。
▼関連記事「IoT導入による工場の見える化とは?成功事例と現場改革におけるメリット・注意点を紹介」
https://smart-factory.funaisoken.co.jp/250108-2/
まとめ:守りのコスト削減から、攻めの原価管理へ
厳しい時代だからこそ、経営者は自社の足元を深く見つめ直す必要があります。『攻めの原価管理』は、単なるコスト計算ではありません。自社の価値を再発見し、自信を取り戻し、未来を切り拓くための経営戦略そのものです。
▼関連記事「製造業必見! 6つのステップで解説!原価管理の取り組み方とは?」
https://smart-factory.funaisoken.co.jp/220714/
▼関連記事「原価管理システムとは?導入メリット・主要機能から失敗しない選び方までIT専門家が徹底解説!おすすめ注目を比較紹介」
https://smart-factory.funaisoken.co.jp/250603-2/
【ある企業では、たった6ヶ月で工場の生産数が1.2倍に!】
「なぜ、あの工程はいつも時間がかかるのだろう?」
「どうすれば、工場の生産能力を最大化できるのか?」
多くの場合、答えは現場に眠っているデータの中にあります。ある企業では、私たちのプログラムを通じてプレス工程がボトルネックであることをデータから発見。生産計画の見直しや人材の多能工化といった改善策を実行した結果、プレス工程の稼働率は20%向上し、工場全体の生産数が1.2倍に増加しました。
これは特別な事例ではありません。貴社の現場にも、まだ気づいていない大きな改善の可能性が眠っているはずです。船井総研の「6ヶ月集中・変革プログラム」で、貴社のポテンシャルを最大限に引き出します。
▼次はあなたの番です!お問い合わせはこちら。
https://formslp.funaisoken.co.jp/form01/lp/post/inquiry-S045.html?siteno=S045