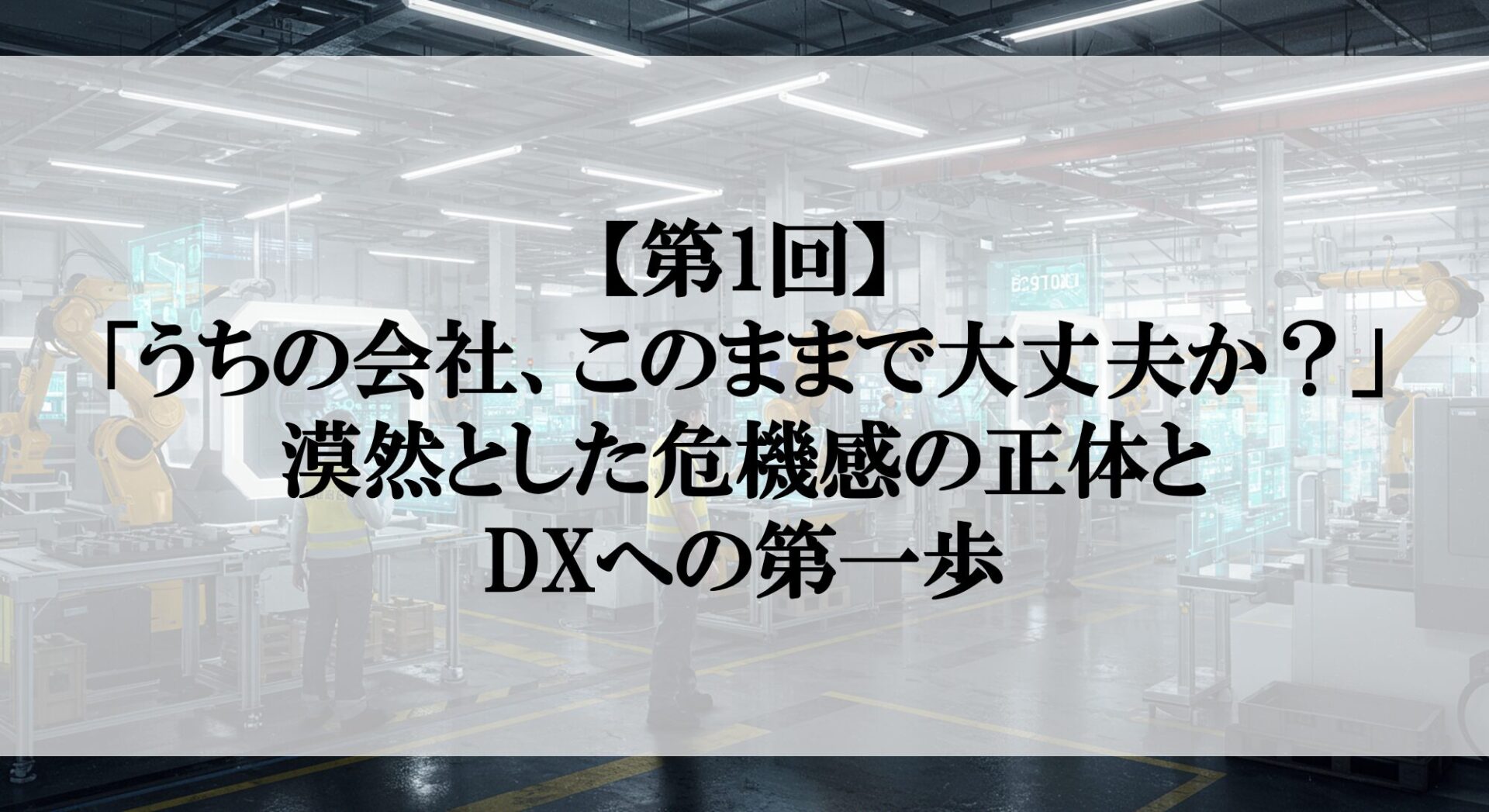
【第1回】「うちの会社、このままで大丈夫か?」漠然とした危機感の正体とDXへの第一歩
2025.06.04
―――見えない不安に揺れる、中堅製造業の今
「このままのやり方で、うちの会社は本当に大丈夫なのだろうか…」
日々、懸命に業務に取り組む中で、ふとこんな漠然とした不安が胸をよぎることはありませんか。
長年培ってきた技術力、顧客からの信頼、そして従業員の頑張り。
それらが今、盤石なものとは言い切れなくなりつつある。競合他社は新しい技術を取り入れ、業界の常識は刻々と変化し、顧客からの要求はますます高度化・多様化しています。
一方で、社内を見渡せば、熟練技術者の高齢化、若手の人材不足、なかなか上がらない生産性、そして依然として残る紙とハンコのアナログな業務…。
こうした状況に、経営者の方々はもちろん、現場のリーダーや管理職の皆様も、言葉にはしにくい危機感を抱えていらっしゃるのではないでしょうか。「何かしなければ」という焦りはありつつも、日々の業務に追われ、何から手をつければ良いのか、どこへ向かうべきなのか、具体的な一歩を踏み出せずにいる。そんな中堅製造業の皆様は、決して少なくありません。
このコラムでは、そんな皆様が抱える「漠然とした危機感」の正体を明らかにし、変化の時代を乗り越え、未来を切り拓くための「DX(デジタルトランスフォーメーション)への第一歩」をどのように踏み出せば良いのか、具体的なヒントを提示していきます。
第1章:その危機感の正体とは?~中堅製造業を取り巻く環境変化~
私たちが感じる漠然とした不安の多くは、企業を取り巻く「環境の変化」と、それに対する「自社の対応の遅れ」から生じています。特に中堅製造業は、今、かつてないほど複雑で急激な変化の波にさらされています。
グローバル競争の激化とサプライチェーンの変容かつては国内市場だけを見ていれば良かった時代もありましたが、今は海外企業との競争が当たり前です。新興国の安価な製品だけでなく、先進的な技術やビジネスモデルを持つ海外企業の日本市場参入も活発化しています。また、コロナ禍や地政学的リスクは、従来のサプライチェーンの脆弱性を露呈させ、より強靭で柔軟な供給網の再構築を迫っています。部品調達の遅延やコスト高騰は、直接的に経営を圧迫する要因となります。
顧客ニーズの多様化・高度化と「コト売り」へのシフト顧客は単に「モノ」を手に入れるだけでなく、その製品が生み出す価値や体験、すなわち「コト」を求めるようになっています。多品種少量生産への対応はもちろん、個別カスタマイズや短納期への要求もますます高まっています。これに応えるためには、企画・開発から製造、販売、アフターサービスに至るまでの全プロセスで、より高度な連携と柔軟性が不可欠です。
労働人口の減少と深刻化する人手不足少子高齢化に伴う労働人口の減少は、製造業にとって特に深刻な問題です。若年層の製造業離れも進み、技能を持った人材の採用はますます困難になっています。一方で、熟練技術者の高齢化とリタイアは、貴重な技術やノウハウの喪失リスクを高めています。「人手が足りないから」と現状維持に甘んじていては、いずれ事業の継続すら難しくなるかもしれません。
急速な技術革新とデジタル化の波IoT、AI、ロボティクス、3Dプリンティングといったデジタル技術の進化は、製造業のあり方を根本から変えようとしています。これらの技術をうまく活用すれば、生産性の飛躍的な向上、コスト削減、品質向上、そして新たなビジネスモデルの創出も可能です。しかし、この変化のスピードに乗り遅れることは、競争力の低下に直結します。
環境問題への意識の高まりとサステナビリティ経営の要請脱炭素社会への移行は、製造業にとってもはや無視できない大きな潮流です。エネルギー効率の改善、廃棄物の削減、リサイクルの推進など、環境負荷低減への取り組みは、企業の社会的責任としてだけでなく、取引条件や企業価値評価にも影響を与えるようになっています。
これらの外部環境の変化に加え、中堅製造業の多くは、以下のような内部的な課題も抱えています。
設備の老朽化と更新の遅れ長年使用してきた生産設備の老朽化が進み、故障リスクや生産効率の低下を招いているものの、設備投資の負担が大きく、更新が思うように進まない。
技術・ノウハウの属人化と伝承の困難特定の熟練技術者に業務が集中し、その人の経験や勘に頼らざるを得ない状況。マニュアル化や標準化が不十分で、若手への技術伝承が円滑に進まない。
部門間のサイロ化と連携不足設計、製造、営業といった部門間の壁が高く、情報共有や連携がスムーズに行えない。結果として、手戻りやリードタイムの長期化、顧客ニーズへの迅速な対応の遅れが生じている。
旧態依然とした業務プロセス未だに紙ベースの帳票や手作業によるデータ入力が多く、非効率な業務が改善されないまま放置されている。変化を嫌う企業風土が、新しい取り組みの導入を阻んでいる。
こうした外部環境の変化と内部の課題が複雑に絡み合い、将来への「漠然とした危機感」を生み出しているのです。そして、この危機感を放置すれば、徐々に競争力は削がれ、利益率は悪化し、優秀な人材は流出し、最悪の場合、時代の変化に対応できずに市場からの退出を余儀なくされる可能性すらあるのです。
第2章:なぜ「何から手をつければ良いか分からない」のか?~DX推進を阻む壁~
「危機感はよく分かった。でも、だからといって、具体的に何をどうすれば…」
多くの経営者や担当者が、ここで立ち往生してしまいます。その背景には、DX推進を阻むいくつかの「壁」が存在します。
「DX」という言葉の曖昧さと過度な期待DX(デジタルトランスフォーメーション)という言葉が独り歩きし、「何かすごいことをしなければならない」「AIやIoTを導入すれば全て解決する」といった誤解や過度な期待が先行しがちです。しかし、DXの本質は「デジタル技術の導入」そのものではなく、「デジタル技術を活用して、ビジネスモデルや業務プロセス、企業文化を変革し、新たな価値を創出し、競争上の優位性を確立すること」です。この本質を理解しないままでは、具体的なアクションプランを描くことはできません。
成功事例の不足と情報過多大企業の華々しいDX成功事例は見聞きするものの、自社と同じような規模や業種の中堅製造業の具体的な成功事例は、まだ少ないのが現状です。一方で、ITベンダーからは様々なソリューションが提案され、情報が溢れすぎて「どれが本当に自社に必要なのか」を見極めるのが困難になっています。
IT投資に対する過去のトラウマと費用対効果への不安DXを推進したくても、社内に適切な知識やスキルを持つ人材がいない、という悩みは深刻です。外部から専門家を採用しようにも、採用競争は激しく、中堅企業にとってはハードルが高いのが実情です。また、IT部門に任せきりにするのではなく、経営層や各業務部門が主体的に関わる必要がありますが、そのためのリテラシーやマインドセットが十分に醸成されていない場合もあります。
デジタル人材・DX推進人材の不足IoT、AI、ロボティクス、3Dプリンティングといったデジタル技術の進化は、製造業のあり方を根本から変えようとしています。これらの技術をうまく活用すれば、生産性の飛躍的な向上、コスト削減、品質向上、そして新たなビジネスモデルの創出も可能です。しかし、この変化のスピードに乗り遅れることは、競争力の低下に直結します。
日々の業務への忙殺と「変わること」への抵抗感「新しいことを始める余裕なんてない」というのが、多くの現場の本音かもしれません。目の前の業務に追われ、現状維持で手一杯。また、長年慣れ親しんだやり方を変えることへの心理的な抵抗感も根強く存在します。「今のままでも何とかなっている」「新しいことを覚えてまでやる必要性を感じない」といった声が、変革へのブレーキとなってしまうのです。
これらの「壁」が、DXへの第一歩を踏み出すことを躊躇させ、「何から手をつければ良いか分からない」という袋小路へと追い込んでいるのです。これらの『壁』を前に、自社だけで解決策を見出すのは容易ではありません。どこから情報を集め、何から始めるべきか、具体的な道筋が見えずに悩んでしまうのは当然のことです。もし、同じような課題意識を持つ他の企業がどのようにこの壁を乗り越えようとしているのか、専門家の具体的なアドバイスを聞いてみたいとお考えでしたら、私たちが開催する中堅製造業のためのMES活用&事例紹介セミナーが一つのヒントになるかもしれません。そこでは、中堅製造業の皆様に特化したDX推進の初期ステップや、陥りがちな罠を避けるための実践的なノウハウを共有しています。
▼中堅製造業のためのMES活用&事例紹介セミナー
https://www.funaisoken.co.jp/seminar/130320
第3章:DXは「魔法の杖」ではない~誤解を解き、地に足の着いた第一歩を~
では、この袋小路から抜け出し、確かな一歩を踏み出すためにはどうすれば良いのでしょうか。まず大切なのは、DXに対する誤解を解き、地に足の着いたアプローチを取ることです。DXは決して、導入すれば全ての問題が一気に解決する「魔法の杖」ではありません。
DXの目的を再確認する:「何のため」のDXか?繰り返しになりますが、DXの目的は「デジタル技術の導入」そのものではありません。自社が抱える課題を解決し、将来どのような姿になりたいのか、そのためにデジタル技術をどう活用するのか、という「目的」を明確にすることが最も重要です。例えば、「生産リードタイムを20%短縮する」「不良品率を現状の半分にする」「新しいサービスで売上10%アップを目指す」といった具体的な目標を設定することから始めましょう。
「スモールスタート」と「クイックウィン」の重要性いきなり全社規模での大規模なシステム刷新やビジネスモデル変革を目指す必要はありません。むしろ、それは失敗のリスクを高めます。まずは、特定の部門や業務プロセスに絞って、比較的小さなテーマから取り組み始める「スモールスタート」が賢明です。そして、短期間で目に見える成果(クイックウィン)を出すことを目指しましょう。小さな成功体験を積み重ねることで、社内のDXに対する理解や協力が得られやすくなり、次のステップへと繋げる推進力が生まれます。
第一歩は「現状の見える化」から何から手をつければ良いか分からないのであれば、まずは自社の現状を客観的に把握することから始めましょう。○ 業務プロセスの棚卸し各部門でどのような業務を行っているのか、どのような手順で進めているのか、紙やExcelで管理している情報はないか、などを洗い出します。○ 課題の洗い出しと優先順位付け棚卸しした業務プロセスの中で、どこに無駄があるのか、どこで時間がかかっているのか、どこでミスが発生しやすいのか、といった課題を具体的に特定します。そして、その課題の中から、解決することで効果が大きいもの、取り組みやすいものなどを考慮して優先順位をつけます。○ データの収集と分析勘や経験だけに頼るのではなく、できる限りデータを収集し、客観的な事実に基づいて現状を分析します。例えば、設備の稼働状況、不良品の発生状況、作業時間などを記録・分析することで、これまで見えていなかった問題点や改善のヒントが見つかることがあります。
部門横断的なコミュニケーションと協力体制の構築DXはIT部門だけの仕事ではありません。経営層の強いリーダーシップのもと、製造、設計、営業、品質管理、経理といったあらゆる部門が連携し、一体となって取り組む必要があります。そのためには、部門間の壁を取り払い、それぞれの立場から意見を出し合い、共通の目標に向かって協力できる体制を構築することが不可欠です。定期的な会議やワークショップの開催、情報共有ツールの活用などが有効です。
ITベンダーとの賢い付き合い方ITベンダーはDX推進の頼れるパートナーとなり得ますが、丸投げは禁物です。自社の課題や目的、DXで実現したいことを明確に伝え、ベンダーの提案を鵜呑みにするのではなく、本当に自社に合っているか、費用対効果は見合うかなどを吟味する必要があります。複数のベンダーから話を聞き、比較検討することも重要です。また、導入後のサポート体制や、自社の人材育成にも協力してくれるようなベンダーを選ぶと良いでしょう。
【事例】中堅部品メーカーA社の挑戦:紙ベースの日報電子化から始まったDX
A社は、長年、自動車メーカー向けに精密部品を供給してきた中堅企業です。
技術力には定評がありましたが、現場では紙の日報や作業指示書が飛び交い、データの集計や分析に多大な時間がかかっていました。また、熟練工の経験と勘に頼る部分が多く、若手への技術伝承も課題でした。
社長はDXの必要性を感じていましたが、何から手をつけるべきか悩んでいました。そこで、まずは最も身近な課題である「日報の電子化」からスモールスタートすることにしました。高価なシステムではなく、タブレットと比較的安価なクラウドサービスを導入し、現場の作業者が簡単に入力できるように工夫しました。
最初は戸惑いの声もありましたが、入力が楽になったこと、リアルタイムで生産状況が把握できるようになったこと、手書きによる読み間違いや集計ミスがなくなったことなど、徐々にメリットが実感されるようになりました。日報から得られるデータを分析することで、これまで気づかなかったボトルネック工程が明らかになり、改善活動にも繋がりました。
この小さな成功体験は、現場の社員の自信となり、「次はあの業務もデジタル化できないか」「もっとデータを活用して品質を改善したい」といった前向きな声が上がるようになりました。A社は現在、IoTセンサーを導入して設備の稼働状況を詳細に把握し、予兆保全に取り組む準備を進めています。日報の電子化という小さな一歩が、A社のDXを加速させる大きなきっかけとなったのです。
第4章:未来を切り拓くために~今こそ、変革への一歩を踏み出す時~
ここまで、中堅製造業が抱える危機感の正体と、DX推進を阻む壁、そしてその乗り越え方について述べてきました。漠然とした不安を抱えたまま立ち止まっていては、何も変わりません。大切なのは、その危機感を「変革へのエネルギー」に変え、具体的な行動を起こすことです。
DXは、決して楽な道のりではありません。試行錯誤も必要ですし、時には失敗もあるかもしれません。しかし、その一つひとつの経験が、自社にとっての貴重な学びとなり、次へと繋がる力になります。
重要なのは、以下の3つの心構えです。
経営者の強いコミットメントDXはトップダウンで進めるべき改革です。経営者がDXの重要性を深く理解し、明確なビジョンを示し、変革を牽引していくという強い意志を示すことが不可欠です。リソースの配分、権限委譲、そして失敗を許容する文化の醸成も経営者の重要な役割です。
全社的な意識改革と学習する組織づくりDXは一部の担当者だけが進めるものではなく、全従業員が当事者意識を持って取り組むべきものです。そのためには、DXの目的やメリットを丁寧に説明し、新しい技術や考え方を学ぶ機会を提供し、変化を前向きに捉える企業文化を育むことが重要です。
小さく始めて、継続的に改善する一度に全てを変えようとするのではなく、スモールスタートで成功体験を積み重ね、そこから得られた学びを活かして次のステップに進む。このアジャイルなアプローチが、中堅製造業のDXを成功に導く鍵となります。
今、あなたの会社が抱えている「このままで大丈夫か?」という危機感は、決してネガティブなものではありません。それは、変化の必要性に気づき、未来をより良くするための「出発点」に立っている証なのです。
もし、このコラムをお読みいただき、『まさに自社の課題だ』『DXへの具体的な一歩をどう踏み出せば良いのか、もっと詳しく知りたい』『他の企業の事例を参考にしたい』と強く感じられたなら、ぜひ私たちが開催するセミナーへのご参加をご検討ください。
本コラムでお伝えした内容をさらに深掘りし、皆様が抱える疑問や不安を解消し、具体的な行動計画を立てるためのお手伝いをいたします。同じ志を持つ仲間との出会いも、きっと新たな気づきや勇気を与えてくれるはずです。
▼中堅製造業のためのMES活用&事例紹介セミナー
https://www.funaisoken.co.jp/seminar/130320
おわりに:未来は、今日の小さな一歩から
今回のコラムでは、中堅製造業の皆様が抱える漠然とした危機感の背景と、DXへの第一歩を踏み出すための基本的な考え方についてお伝えしました。変化の激しい時代において、現状維持は緩やかな後退を意味します。しかし、悲観的になる必要はありません。自社の強みを再認識し、デジタル技術を賢く活用することで、新たな成長の道筋を描くことは十分に可能です。
本コラムが、皆様にとって、自社の未来を真剣に考え、変革への勇気ある一歩を踏み出すきっかけとなれば、これほど嬉しいことはありません。
次回は、DX推進において多くの企業が直面する具体的な課題の一つである「『また新しいシステムか…』現場の嘆きを共感に変える、IT導入成功の秘訣」というテーマで、現場の抵抗を乗り越え、全社一丸となってDXを推進していくためのコミュニケーションや巻き込み方について、より深く掘り下げていきます。ご期待ください。
https://www.funaisoken.co.jp/seminar/130320
■成功事例
【1】<愛知県>多品種少量生産の企業がIoT活用を実施し、データ分析による現場改善を実践した事例!
【2】<岐阜県>MES活用により、人+機械の生産進捗をデータ化!工場内全体進捗管理を実践した事例!
【3】<大阪府>複数拠点の工場をIoTを活用することによって本社で統括管理できるようになった事例!
【4】<大阪府>MES活用により、生産計画~製造指示~実績取得をすべてペーパレス化した事例!
【5】<愛知県>工場現場のペーパレス化を実現!月2,240時間の削減に成功した事例!
【本セミナーで学べるポイント】
従業員200~2000名の製造業におけるMES活用の重要性が学べる!
~市場動向を踏まえ、なぜ今中堅製造業がMESに取り組むべきなのか、具体的なメリットや実現できる姿を理解できます。~
IoT連携による製造現場の革新事例が学べる!
~デンソーウェーブ様にご登壇いただき、IoTをどのように生産性向上や現場の可視化を実現できるのか、具体的な事例を通して学ぶことができます。~
人手不足・コスト増の課題解決のヒントが学べる!
~MESやIoTの導入によって、どのように省人化を進め、コストを削減できるのか、具体的な取り組みや効果について理解を深めることができます。~
自社に適したMES導入への第一歩が学べる!
~中堅製造業がMES導入を検討する上で重要なポイントや、成功のためのステップ、注意点などを把握することができます。~ ―――見えない不安に揺れる、中堅製造業の今
「このままのやり方で、うちの会社は本当に大丈夫なのだろうか…」
日々、懸命に業務に取り組む中で、ふとこんな漠然とした不安が胸をよぎることはありませんか。
長年培ってきた技術力、顧客からの信頼、そして従業員の頑張り。
それらが今、盤石なものとは言い切れなくなりつつある。競合他社は新しい技術を取り入れ、業界の常識は刻々と変化し、顧客からの要求はますます高度化・多様化しています。
一方で、社内を見渡せば、熟練技術者の高齢化、若手の人材不足、なかなか上がらない生産性、そして依然として残る紙とハンコのアナログな業務…。
こうした状況に、経営者の方々はもちろん、現場のリーダーや管理職の皆様も、言葉にはしにくい危機感を抱えていらっしゃるのではないでしょうか。「何かしなければ」という焦りはありつつも、日々の業務に追われ、何から手をつければ良いのか、どこへ向かうべきなのか、具体的な一歩を踏み出せずにいる。そんな中堅製造業の皆様は、決して少なくありません。
このコラムでは、そんな皆様が抱える「漠然とした危機感」の正体を明らかにし、変化の時代を乗り越え、未来を切り拓くための「DX(デジタルトランスフォーメーション)への第一歩」をどのように踏み出せば良いのか、具体的なヒントを提示していきます。
第1章:その危機感の正体とは?~中堅製造業を取り巻く環境変化~
私たちが感じる漠然とした不安の多くは、企業を取り巻く「環境の変化」と、それに対する「自社の対応の遅れ」から生じています。特に中堅製造業は、今、かつてないほど複雑で急激な変化の波にさらされています。
グローバル競争の激化とサプライチェーンの変容かつては国内市場だけを見ていれば良かった時代もありましたが、今は海外企業との競争が当たり前です。新興国の安価な製品だけでなく、先進的な技術やビジネスモデルを持つ海外企業の日本市場参入も活発化しています。また、コロナ禍や地政学的リスクは、従来のサプライチェーンの脆弱性を露呈させ、より強靭で柔軟な供給網の再構築を迫っています。部品調達の遅延やコスト高騰は、直接的に経営を圧迫する要因となります。
顧客ニーズの多様化・高度化と「コト売り」へのシフト顧客は単に「モノ」を手に入れるだけでなく、その製品が生み出す価値や体験、すなわち「コト」を求めるようになっています。多品種少量生産への対応はもちろん、個別カスタマイズや短納期への要求もますます高まっています。これに応えるためには、企画・開発から製造、販売、アフターサービスに至るまでの全プロセスで、より高度な連携と柔軟性が不可欠です。
労働人口の減少と深刻化する人手不足少子高齢化に伴う労働人口の減少は、製造業にとって特に深刻な問題です。若年層の製造業離れも進み、技能を持った人材の採用はますます困難になっています。一方で、熟練技術者の高齢化とリタイアは、貴重な技術やノウハウの喪失リスクを高めています。「人手が足りないから」と現状維持に甘んじていては、いずれ事業の継続すら難しくなるかもしれません。
急速な技術革新とデジタル化の波IoT、AI、ロボティクス、3Dプリンティングといったデジタル技術の進化は、製造業のあり方を根本から変えようとしています。これらの技術をうまく活用すれば、生産性の飛躍的な向上、コスト削減、品質向上、そして新たなビジネスモデルの創出も可能です。しかし、この変化のスピードに乗り遅れることは、競争力の低下に直結します。
環境問題への意識の高まりとサステナビリティ経営の要請脱炭素社会への移行は、製造業にとってもはや無視できない大きな潮流です。エネルギー効率の改善、廃棄物の削減、リサイクルの推進など、環境負荷低減への取り組みは、企業の社会的責任としてだけでなく、取引条件や企業価値評価にも影響を与えるようになっています。
これらの外部環境の変化に加え、中堅製造業の多くは、以下のような内部的な課題も抱えています。
設備の老朽化と更新の遅れ長年使用してきた生産設備の老朽化が進み、故障リスクや生産効率の低下を招いているものの、設備投資の負担が大きく、更新が思うように進まない。
技術・ノウハウの属人化と伝承の困難特定の熟練技術者に業務が集中し、その人の経験や勘に頼らざるを得ない状況。マニュアル化や標準化が不十分で、若手への技術伝承が円滑に進まない。
部門間のサイロ化と連携不足設計、製造、営業といった部門間の壁が高く、情報共有や連携がスムーズに行えない。結果として、手戻りやリードタイムの長期化、顧客ニーズへの迅速な対応の遅れが生じている。
旧態依然とした業務プロセス未だに紙ベースの帳票や手作業によるデータ入力が多く、非効率な業務が改善されないまま放置されている。変化を嫌う企業風土が、新しい取り組みの導入を阻んでいる。
こうした外部環境の変化と内部の課題が複雑に絡み合い、将来への「漠然とした危機感」を生み出しているのです。そして、この危機感を放置すれば、徐々に競争力は削がれ、利益率は悪化し、優秀な人材は流出し、最悪の場合、時代の変化に対応できずに市場からの退出を余儀なくされる可能性すらあるのです。
第2章:なぜ「何から手をつければ良いか分からない」のか?~DX推進を阻む壁~
「危機感はよく分かった。でも、だからといって、具体的に何をどうすれば…」
多くの経営者や担当者が、ここで立ち往生してしまいます。その背景には、DX推進を阻むいくつかの「壁」が存在します。
「DX」という言葉の曖昧さと過度な期待DX(デジタルトランスフォーメーション)という言葉が独り歩きし、「何かすごいことをしなければならない」「AIやIoTを導入すれば全て解決する」といった誤解や過度な期待が先行しがちです。しかし、DXの本質は「デジタル技術の導入」そのものではなく、「デジタル技術を活用して、ビジネスモデルや業務プロセス、企業文化を変革し、新たな価値を創出し、競争上の優位性を確立すること」です。この本質を理解しないままでは、具体的なアクションプランを描くことはできません。
成功事例の不足と情報過多大企業の華々しいDX成功事例は見聞きするものの、自社と同じような規模や業種の中堅製造業の具体的な成功事例は、まだ少ないのが現状です。一方で、ITベンダーからは様々なソリューションが提案され、情報が溢れすぎて「どれが本当に自社に必要なのか」を見極めるのが困難になっています。
IT投資に対する過去のトラウマと費用対効果への不安DXを推進したくても、社内に適切な知識やスキルを持つ人材がいない、という悩みは深刻です。外部から専門家を採用しようにも、採用競争は激しく、中堅企業にとってはハードルが高いのが実情です。また、IT部門に任せきりにするのではなく、経営層や各業務部門が主体的に関わる必要がありますが、そのためのリテラシーやマインドセットが十分に醸成されていない場合もあります。
デジタル人材・DX推進人材の不足IoT、AI、ロボティクス、3Dプリンティングといったデジタル技術の進化は、製造業のあり方を根本から変えようとしています。これらの技術をうまく活用すれば、生産性の飛躍的な向上、コスト削減、品質向上、そして新たなビジネスモデルの創出も可能です。しかし、この変化のスピードに乗り遅れることは、競争力の低下に直結します。
日々の業務への忙殺と「変わること」への抵抗感「新しいことを始める余裕なんてない」というのが、多くの現場の本音かもしれません。目の前の業務に追われ、現状維持で手一杯。また、長年慣れ親しんだやり方を変えることへの心理的な抵抗感も根強く存在します。「今のままでも何とかなっている」「新しいことを覚えてまでやる必要性を感じない」といった声が、変革へのブレーキとなってしまうのです。
これらの「壁」が、DXへの第一歩を踏み出すことを躊躇させ、「何から手をつければ良いか分からない」という袋小路へと追い込んでいるのです。これらの『壁』を前に、自社だけで解決策を見出すのは容易ではありません。どこから情報を集め、何から始めるべきか、具体的な道筋が見えずに悩んでしまうのは当然のことです。もし、同じような課題意識を持つ他の企業がどのようにこの壁を乗り越えようとしているのか、専門家の具体的なアドバイスを聞いてみたいとお考えでしたら、私たちが開催する中堅製造業のためのMES活用&事例紹介セミナーが一つのヒントになるかもしれません。そこでは、中堅製造業の皆様に特化したDX推進の初期ステップや、陥りがちな罠を避けるための実践的なノウハウを共有しています。
▼中堅製造業のためのMES活用&事例紹介セミナー
https://www.funaisoken.co.jp/seminar/130320
第3章:DXは「魔法の杖」ではない~誤解を解き、地に足の着いた第一歩を~
では、この袋小路から抜け出し、確かな一歩を踏み出すためにはどうすれば良いのでしょうか。まず大切なのは、DXに対する誤解を解き、地に足の着いたアプローチを取ることです。DXは決して、導入すれば全ての問題が一気に解決する「魔法の杖」ではありません。
DXの目的を再確認する:「何のため」のDXか?繰り返しになりますが、DXの目的は「デジタル技術の導入」そのものではありません。自社が抱える課題を解決し、将来どのような姿になりたいのか、そのためにデジタル技術をどう活用するのか、という「目的」を明確にすることが最も重要です。例えば、「生産リードタイムを20%短縮する」「不良品率を現状の半分にする」「新しいサービスで売上10%アップを目指す」といった具体的な目標を設定することから始めましょう。
「スモールスタート」と「クイックウィン」の重要性いきなり全社規模での大規模なシステム刷新やビジネスモデル変革を目指す必要はありません。むしろ、それは失敗のリスクを高めます。まずは、特定の部門や業務プロセスに絞って、比較的小さなテーマから取り組み始める「スモールスタート」が賢明です。そして、短期間で目に見える成果(クイックウィン)を出すことを目指しましょう。小さな成功体験を積み重ねることで、社内のDXに対する理解や協力が得られやすくなり、次のステップへと繋げる推進力が生まれます。
第一歩は「現状の見える化」から何から手をつければ良いか分からないのであれば、まずは自社の現状を客観的に把握することから始めましょう。○ 業務プロセスの棚卸し各部門でどのような業務を行っているのか、どのような手順で進めているのか、紙やExcelで管理している情報はないか、などを洗い出します。○ 課題の洗い出しと優先順位付け棚卸しした業務プロセスの中で、どこに無駄があるのか、どこで時間がかかっているのか、どこでミスが発生しやすいのか、といった課題を具体的に特定します。そして、その課題の中から、解決することで効果が大きいもの、取り組みやすいものなどを考慮して優先順位をつけます。○ データの収集と分析勘や経験だけに頼るのではなく、できる限りデータを収集し、客観的な事実に基づいて現状を分析します。例えば、設備の稼働状況、不良品の発生状況、作業時間などを記録・分析することで、これまで見えていなかった問題点や改善のヒントが見つかることがあります。
部門横断的なコミュニケーションと協力体制の構築DXはIT部門だけの仕事ではありません。経営層の強いリーダーシップのもと、製造、設計、営業、品質管理、経理といったあらゆる部門が連携し、一体となって取り組む必要があります。そのためには、部門間の壁を取り払い、それぞれの立場から意見を出し合い、共通の目標に向かって協力できる体制を構築することが不可欠です。定期的な会議やワークショップの開催、情報共有ツールの活用などが有効です。
ITベンダーとの賢い付き合い方ITベンダーはDX推進の頼れるパートナーとなり得ますが、丸投げは禁物です。自社の課題や目的、DXで実現したいことを明確に伝え、ベンダーの提案を鵜呑みにするのではなく、本当に自社に合っているか、費用対効果は見合うかなどを吟味する必要があります。複数のベンダーから話を聞き、比較検討することも重要です。また、導入後のサポート体制や、自社の人材育成にも協力してくれるようなベンダーを選ぶと良いでしょう。
【事例】中堅部品メーカーA社の挑戦:紙ベースの日報電子化から始まったDX
A社は、長年、自動車メーカー向けに精密部品を供給してきた中堅企業です。
技術力には定評がありましたが、現場では紙の日報や作業指示書が飛び交い、データの集計や分析に多大な時間がかかっていました。また、熟練工の経験と勘に頼る部分が多く、若手への技術伝承も課題でした。
社長はDXの必要性を感じていましたが、何から手をつけるべきか悩んでいました。そこで、まずは最も身近な課題である「日報の電子化」からスモールスタートすることにしました。高価なシステムではなく、タブレットと比較的安価なクラウドサービスを導入し、現場の作業者が簡単に入力できるように工夫しました。
最初は戸惑いの声もありましたが、入力が楽になったこと、リアルタイムで生産状況が把握できるようになったこと、手書きによる読み間違いや集計ミスがなくなったことなど、徐々にメリットが実感されるようになりました。日報から得られるデータを分析することで、これまで気づかなかったボトルネック工程が明らかになり、改善活動にも繋がりました。
この小さな成功体験は、現場の社員の自信となり、「次はあの業務もデジタル化できないか」「もっとデータを活用して品質を改善したい」といった前向きな声が上がるようになりました。A社は現在、IoTセンサーを導入して設備の稼働状況を詳細に把握し、予兆保全に取り組む準備を進めています。日報の電子化という小さな一歩が、A社のDXを加速させる大きなきっかけとなったのです。
第4章:未来を切り拓くために~今こそ、変革への一歩を踏み出す時~
ここまで、中堅製造業が抱える危機感の正体と、DX推進を阻む壁、そしてその乗り越え方について述べてきました。漠然とした不安を抱えたまま立ち止まっていては、何も変わりません。大切なのは、その危機感を「変革へのエネルギー」に変え、具体的な行動を起こすことです。
DXは、決して楽な道のりではありません。試行錯誤も必要ですし、時には失敗もあるかもしれません。しかし、その一つひとつの経験が、自社にとっての貴重な学びとなり、次へと繋がる力になります。
重要なのは、以下の3つの心構えです。
経営者の強いコミットメントDXはトップダウンで進めるべき改革です。経営者がDXの重要性を深く理解し、明確なビジョンを示し、変革を牽引していくという強い意志を示すことが不可欠です。リソースの配分、権限委譲、そして失敗を許容する文化の醸成も経営者の重要な役割です。
全社的な意識改革と学習する組織づくりDXは一部の担当者だけが進めるものではなく、全従業員が当事者意識を持って取り組むべきものです。そのためには、DXの目的やメリットを丁寧に説明し、新しい技術や考え方を学ぶ機会を提供し、変化を前向きに捉える企業文化を育むことが重要です。
小さく始めて、継続的に改善する一度に全てを変えようとするのではなく、スモールスタートで成功体験を積み重ね、そこから得られた学びを活かして次のステップに進む。このアジャイルなアプローチが、中堅製造業のDXを成功に導く鍵となります。
今、あなたの会社が抱えている「このままで大丈夫か?」という危機感は、決してネガティブなものではありません。それは、変化の必要性に気づき、未来をより良くするための「出発点」に立っている証なのです。
もし、このコラムをお読みいただき、『まさに自社の課題だ』『DXへの具体的な一歩をどう踏み出せば良いのか、もっと詳しく知りたい』『他の企業の事例を参考にしたい』と強く感じられたなら、ぜひ私たちが開催するセミナーへのご参加をご検討ください。
本コラムでお伝えした内容をさらに深掘りし、皆様が抱える疑問や不安を解消し、具体的な行動計画を立てるためのお手伝いをいたします。同じ志を持つ仲間との出会いも、きっと新たな気づきや勇気を与えてくれるはずです。
▼中堅製造業のためのMES活用&事例紹介セミナー
https://www.funaisoken.co.jp/seminar/130320
おわりに:未来は、今日の小さな一歩から
今回のコラムでは、中堅製造業の皆様が抱える漠然とした危機感の背景と、DXへの第一歩を踏み出すための基本的な考え方についてお伝えしました。変化の激しい時代において、現状維持は緩やかな後退を意味します。しかし、悲観的になる必要はありません。自社の強みを再認識し、デジタル技術を賢く活用することで、新たな成長の道筋を描くことは十分に可能です。
本コラムが、皆様にとって、自社の未来を真剣に考え、変革への勇気ある一歩を踏み出すきっかけとなれば、これほど嬉しいことはありません。
次回は、DX推進において多くの企業が直面する具体的な課題の一つである「『また新しいシステムか…』現場の嘆きを共感に変える、IT導入成功の秘訣」というテーマで、現場の抵抗を乗り越え、全社一丸となってDXを推進していくためのコミュニケーションや巻き込み方について、より深く掘り下げていきます。ご期待ください。
https://www.funaisoken.co.jp/seminar/130320
■成功事例
【1】<愛知県>多品種少量生産の企業がIoT活用を実施し、データ分析による現場改善を実践した事例!
【2】<岐阜県>MES活用により、人+機械の生産進捗をデータ化!工場内全体進捗管理を実践した事例!
【3】<大阪府>複数拠点の工場をIoTを活用することによって本社で統括管理できるようになった事例!
【4】<大阪府>MES活用により、生産計画~製造指示~実績取得をすべてペーパレス化した事例!
【5】<愛知県>工場現場のペーパレス化を実現!月2,240時間の削減に成功した事例!
【本セミナーで学べるポイント】
従業員200~2000名の製造業におけるMES活用の重要性が学べる!
~市場動向を踏まえ、なぜ今中堅製造業がMESに取り組むべきなのか、具体的なメリットや実現できる姿を理解できます。~
IoT連携による製造現場の革新事例が学べる!
~デンソーウェーブ様にご登壇いただき、IoTをどのように生産性向上や現場の可視化を実現できるのか、具体的な事例を通して学ぶことができます。~
人手不足・コスト増の課題解決のヒントが学べる!
~MESやIoTの導入によって、どのように省人化を進め、コストを削減できるのか、具体的な取り組みや効果について理解を深めることができます。~
自社に適したMES導入への第一歩が学べる!
~中堅製造業がMES導入を検討する上で重要なポイントや、成功のためのステップ、注意点などを把握することができます。~