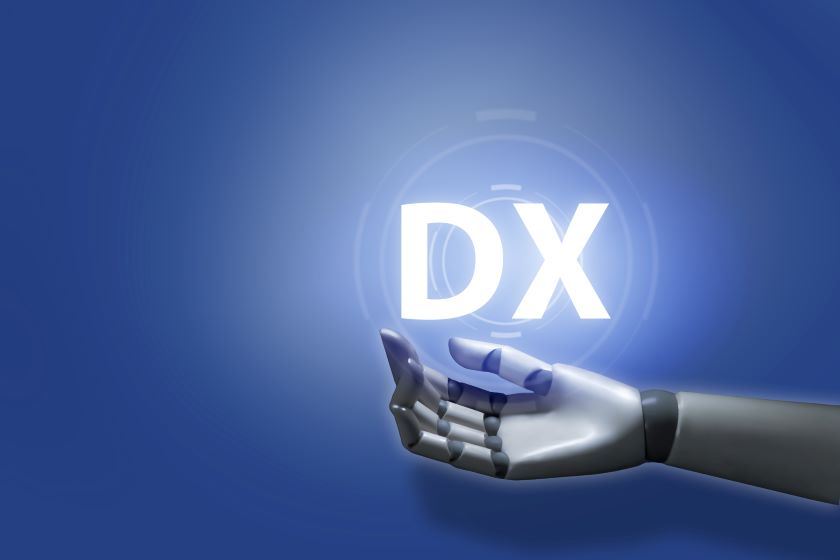
スマートファクトリー(SmartFactory)完全ガイド:基礎知識から導入メリット、最新技術、成功の秘訣まで徹底解説
2025.04.11
製造業の未来を拓くスマートファクトリー(SmartFactory)とは?
現代の製造業は、グローバルな競争激化、少子高齢化による労働力不足、顧客ニーズの多様化・高度化、そして急速なデジタル技術の進展という、かつてない変化の波に直面しています。このような時代において、競争優位性を確立し、持続的な成長を遂げるための鍵として注目されているのが「スマートファクトリー(SmartFactory)」です。
しかし、「スマートファクトリー」という言葉は広く知られるようになった一方で、「具体的に何を指すのか?」「自社にどのようなメリットがあるのか?」「どうすれば実現できるのか?」といった疑問を持つ方も少なくないでしょう。
本稿では、「スマートファクトリー(SmartFactory)」に関する基礎知識から、導入によって得られる具体的なメリット、実現に不可欠な技術要素、導入プロセス、成功のためのポイント、そして未来の展望に至るまで、包括的かつ詳細に解説します。この記事を通じて、**スマートファクトリー(SmartFactory)**への理解を深め、自社の製造現場変革への第一歩を踏み出すための一助となれば幸いです。
1. スマートファクトリー(SmartFactory)の基礎知識:定義、必要性、目指す姿
まず、**スマートファクトリー(SmartFactory)**の基本的な概念を理解することから始めましょう。
1.1. スマートファクトリー(SmartFactory)の定義と仕組み
**スマートファクトリー(SmartFactory)**とは、工場内の設備、機器、作業者、生産プロセスなどがネットワーク(主にIoT技術)で接続され、そこから収集される膨大なデータをリアルタイムで分析・活用することで、生産活動全体の最適化、自律化を目指す新しい工場のあり方です。
従来の工場が各工程の部分最適化に留まっていたのに対し、**スマートファクトリー(SmartFactory)**では、設計から製造、検査、出荷、さらには保守・保全に至るまで、バリューチェーン全体をデジタルデータで繋ぎ、全体最適を図ります。これにより、状況に応じた柔軟な生産調整や、予知保全によるダウンタイムの削減、リソースの最適配分などが可能になります。
1.2. なぜ今スマートファクトリー(SmartFactory)が求められるのか?
**スマートファクトリー(SmartFactory)**の必要性が高まっている背景には、以下のような複合的な要因があります。
労働力不足の深刻化: 製造現場における人手不足は、特に日本では喫緊の課題です。自動化・省人化を進める**スマートファクトリー(SmartFactory)**は、この課題への直接的な解決策となります。
グローバル競争の激化: 低コスト生産や高い品質要求に応えるため、生産効率の抜本的な向上が不可欠です。データに基づいた改善は、競争力を維持・強化する上で欠かせません。
顧客ニーズの多様化と高度化: 多品種少量生産やマスカスタマイゼーションへの対応が求められています。**スマートファクトリー(SmartFactory)**は、生産ラインの柔軟性を高め、変化する市場要求に迅速に対応する能力を提供します。
技術の進化と普及: IoTセンサー、AI、ロボット、クラウドコンピューティングなどの技術が進化し、導入コストも下がってきたことで、**スマートファクトリー(SmartFactory)**の実現がより現実的なものとなっています。
サステナビリティへの要求: 省エネルギー化や廃棄物削減など、環境負荷低減への取り組みも重要性を増しています。データ活用によるエネルギー効率の最適化なども**スマートファクトリー(SmartFactory)**の重要な側面です。
1.3. スマートファクトリー(SmartFactory)で目指す姿
**スマートファクトリー(SmartFactory)**が目指すのは、単なる自動化や効率化だけではありません。以下のような、より高度でインテリジェントな工場の実現を目指します。
自律的な生産: 状況変化をリアルタイムで検知し、AIなどが最適な判断を下し、生産計画や設備稼働を自律的に調整します。
予知保全の実現: 設備の状態を常時監視し、故障の兆候を事前に検知してメンテナンスを行うことで、突発的な停止を防ぎ、稼働率を最大化します。
柔軟な生産体制: 市場の需要変動や仕様変更に対し、生産ラインを迅速かつ柔軟に組み替えて対応します。
データドリブンな意思決定: 経験や勘だけに頼るのではなく、収集・分析された客観的なデータに基づいて、経営判断や現場改善を行います。
人と機械の協調: 人はより付加価値の高い作業(改善、分析、判断など)に集中し、単純作業や危険作業はロボットなどが担う、安全で効率的な作業環境を実現します。
2. スマートファクトリー(SmartFactory)実現の3つの鍵率
**スマートファクトリー(SmartFactory)**を実現するためには、大きく分けて以下の3つの要素が相互に連携することが不可欠です。
2.1. データ:あらゆる情報を繋ぐ神経網
**スマートファクトリー(SmartFactory)**の根幹をなすのが「データ」です。IoTセンサーなどを活用し、生産設備(稼働状況、温度、振動等)、製品(品質データ、位置情報等)、作業者(作業時間、動線等)、環境(温度、湿度等)など、工場内のあらゆる情報をリアルタイムで収集・蓄積します。このデータが、現状把握、分析、予測、そして最適化の基盤となります。
2.2. ロボット・自動化機器:フィジカルな実行部隊
収集・分析されたデータに基づく指示を実行するのが、ロボットや自動搬送車(AGV/AMR)、自動倉庫などの自動化機器です。これらは、組み立て、搬送、検査といった物理的な作業を正確かつ効率的に行い、省人化や生産スピード向上に貢献します。近年では、人と隣り合って安全に作業できる協働ロボットの導入も進んでいます。
2.3. システム:データ活用と制御の中枢
収集したデータを蓄積・分析し、ロボットや設備への指示を行うのが各種「システム」です。MES(製造実行システム)、ERP(統合基幹業務システム)、PLM(製品ライフサイクル管理)、SCM(サプライチェーン管理)などの既存システムに加え、IoTプラットフォームやAI分析ツールなどが連携し、**スマートファクトリー(SmartFactory)**全体の頭脳として機能します。クラウドやエッジコンピューティングの活用も進んでいます。
これら3つの要素(データ、ロボット・自動化機器、システム)が、IoT、AI、5Gなどの通信技術によって有機的に結びつくことで、**スマートファクトリー(SmartFactory)**は成り立っています。これは、企業全体のデジタルトランスフォーメーション(DX)の一環としても捉えられます。
3. スマートファクトリー(SmartFactory)導入によるメリット
**スマートファクトリー(SmartFactory)**を導入することで、企業は多岐にわたるメリットを享受できます。
3.1. 生産性の飛躍的向上
自動化・省人化: ロボット等による自動化で、作業時間を短縮し、人手不足を解消。人はより高度な業務へシフト。
稼働率の最大化: 予知保全による設備ダウンタイムの削減、データに基づく最適な人員・設備配置。
ボトルネックの解消: データ分析により生産プロセス全体のボトルネックを特定し、集中的に改善。
3.2. 品質向上と安定化
リアルタイム品質監視: センサー等で製造中の製品品質を常時監視し、異常を早期に検知・対応。
不良原因の特定: 蓄積された品質データと製造条件データをAIなどで分析し、不良発生の根本原因を特定・排除。
作業の標準化: デジタルマニュアルやロボットによる作業で、人的ミスやスキル差による品質ばらつきを抑制。
3.3. コスト削減
労務費の削減: 自動化・省人化による人件費の抑制。
不良コストの削減: 不良品発生率の低減による材料費、手直し工数の削減。
エネルギーコストの削減: 設備稼働の最適化やエネルギー使用量の見える化による無駄の排除。
在庫コストの削減: 需要予測精度向上や生産計画最適化による適正在庫の維持。
3.4. リードタイム短縮と市場変化への対応力強化
生産計画の最適化: リアルタイムな情報に基づき、最適な生産順序や段取り替えを計画・実行。
サプライチェーン連携: 受注から設計、調達、生産、出荷までの情報を連携し、プロセス全体を高速化。
柔軟な生産ライン: 多品種少量生産や仕様変更に迅速に対応できるライン構成。
3.5. その他のメリット
トレーサビリティ向上: 製品個体ごとに、いつ、どこで、誰が、どのように製造したかの履歴を追跡可能にし、品質保証体制を強化。
技術・技能伝承の促進: 熟練者の動きや判断をデータ化・マニュアル化し、若手への教育や技術継承を効率化(属人化の解消)。
安全な労働環境の実現: 危険作業や過酷な作業をロボットに代替させ、労働災害リスクを低減。
従業員のモチベーション向上: 単純作業から解放され、より創造的・分析的な業務に従事することによる働きがいの向上。
企業価値・ブランドイメージ向上: 先進的な取り組みによる対外的なアピール力強化(例:アスザック株式会社様の事例)。
4. スマートファクトリー(SmartFactory)を支える主要技術
**スマートファクトリー(SmartFactory)**の実現は、様々なデジタル技術の組み合わせによって支えられています。
IoT (Internet of Things): 工場内のあらゆるモノ(設備、製品、治具、人など)にセンサーを取り付け、インターネットに接続してデータを収集・交換する基盤技術。**スマートファクトリー(SmartFactory)**の神経網と言えます。
AI (人工知能): 収集された膨大なデータを分析し、パターン認識、異常検知、需要予測、最適化提案などを行う頭脳。機械学習やディープラーニングが活用されます。
ロボット: 産業用ロボット、協働ロボットなどが、組み立て、溶接、塗装、搬送、検査などの作業を自動化します。
5G/ローカル5G: 高速・大容量・低遅延・多接続という特徴を持つ次世代通信規格。多数のセンサーやロボットをリアルタイムに接続・制御するために重要です。
クラウド/エッジコンピューティング: 大容量データの蓄積・分析基盤となるクラウドと、現場に近い場所でリアルタイムなデータ処理を行うエッジコンピューティングを適材適所で活用します。
サイバーセキュリティ: 工場ネットワークが外部と接続されるため、不正アクセスや情報漏洩を防ぐための堅牢なセキュリティ対策が不可欠です。
デジタルツイン: 現実の工場や生産ラインをデジタルの仮想空間に再現する技術。シミュレーションによる事前検証や、リアルタイムな遠隔監視・操作を可能にします。
各種システム連携: MES(製造実行システム)、ERP(統合基幹業務システム)、PLM(製品ライフサイクル管理)、SCM(サプライチェーン管理)などを連携させ、データの一元管理と活用を促進します。
これらの技術を、自社の目的や課題に合わせて適切に選択し、組み合わせていくことが**スマートファクトリー(SmartFactory)**構築の鍵となります。
5. スマートファクトリー(SmartFactory)導入のステップと成功のポイント
**スマートファクトリー(SmartFactory)**の導入は、やみくもに進めても成功しません。段階的かつ計画的なアプローチが重要です。
5.1. 導入ステップ
目的・目標設定: 「何のためにスマートファクトリー化するのか」「具体的な数値目標は何か」を明確にします(例:生産性15%向上、不良率0.5%削減)。経営層のコミットメントが不可欠です。
現状分析・課題特定: 自社の生産現場の現状を把握し、データに基づいてボトルネックとなっている課題を特定します(見える化)。
導入計画策定: 目標達成のために、どの技術を、どの範囲に、どの順序で導入するか、具体的なロードマップと投資計画を作成します。費用対効果の試算も重要です。
技術選定・パートナー選定: 計画に基づき、最適な技術、ソリューション、そして導入を支援してくれる信頼できるベンダーやコンサルティングパートナーを選定します。
PoC (Proof of Concept) / スモールスタート: まずは限定的な範囲(特定のラインや工程)で試験的に導入し、効果を検証します(小さく始めて大きく育てる)。
本格導入・横展開: PoCで効果が確認できたら、対象範囲を広げて本格導入を進めます。
運用・継続的改善: 導入後もデータを活用し、効果測定と改善活動を継続的に行い、**スマートファクトリー(SmartFactory)**を深化させていきます。
5.2. 成功のポイント
経営層の強いリーダーシップ: トップが**スマートファクトリー(SmartFactory)**化の重要性を理解し、全社的な取り組みとして強力に推進することが最も重要です。
明確なビジョンと目標共有: 全従業員が目指す姿と目標を共有し、一体感を持って取り組むことが大切です。
「見える化」からのスタート: まずは現状をデータで正確に把握することから始め、課題を明確にすることが着実な第一歩です。
スモールスタートと段階的導入: 最初から完璧を目指さず、小さく始めて効果を検証しながら、リスクを抑えて進めます。
データ活用文化の醸成: 収集したデータを意思決定や改善活動に活かす文化を組織全体で育てることが重要です。人材育成も並行して行います。
現場との連携: 実際にシステムや設備を使う現場の意見を取り入れ、使いやすく効果的な**スマートファクトリー(SmartFactory)**を目指します。
適切なパートナーとの連携: 自社だけでは知見やリソースが不足する場合、経験豊富な外部パートナー(コンサルタント、ベンダー等)と協力することが成功の鍵となります。特に、アスザック株式会社様の事例のように、プロジェクト推進力や客観的な効果判断を提供できるパートナーは有効です。
セキュリティ対策の徹底: 導入計画の初期段階からセキュリティリスクを考慮し、対策を講じます。
6. スマートファクトリー(SmartFactory)導入における課題と対策
**スマートファクトリー(SmartFactory)**導入には多くのメリットがありますが、一方で乗り越えるべき課題も存在します。
課題1:導入・運用コスト:
対策: スモールスタートや段階的導入で初期投資を抑制。リースや補助金の活用。費用対効果(ROI)を事前にしっかり試算・評価。
課題2:IT・デジタル人材の不足:
対策: 社内人材の育成(研修、OJT)。外部専門家(コンサルタント、ベンダー)の活用。使いやすいツールの選定。
課題3:セキュリティリスク:
対策: 最新のセキュリティ対策(ファイアウォール、侵入検知システム等)の導入。従業員へのセキュリティ教育。専門家による診断。
課題4:既存システム・設備との連携:
対策: 連携可能なインターフェースを持つシステムの選定。段階的な設備更新計画。レガシーシステムに対応できるパートナーの選定。
課題5:組織文化・抵抗:
対策: 経営層からの明確なメッセージ発信。導入メリットの丁寧な説明と従業員の巻き込み。成功体験の共有。
これらの課題を事前に認識し、対策を計画に盛り込むことが、**スマートファクトリー(SmartFactory)**導入プロジェクトを円滑に進める上で重要です。
7. スマートファクトリー(SmartFactory)の未来と最新トレンド
**スマートファクトリー(SmartFactory)**は、今後も技術の進化とともに更なる発展が期待されています。
AIの更なる高度化: より自律的な判断・制御、複雑な要因分析、高度な需要予測などが可能に。
サステナビリティとの融合: 省エネ、資源効率の最大化、廃棄物削減など、環境負荷低減(グリーンファクトリー)への貢献がより重視されます。
マスカスタマイゼーションの進展: 個別最適化された製品を効率的に生産する体制が進化します。
人間中心のスマートファクトリー: 人とロボットがより高度に協調し、人は創造性や判断力が求められる業務に集中する、働きがいのある工場へ。
サプライチェーン全体への展開: 工場内だけでなく、サプライヤーから顧客まで、バリューチェーン全体がデジタルで繋がり、より高度な連携が実現します。
**スマートファクトリー(SmartFactory)**は、単なる生産現場の効率化ツールではなく、企業の競争力そのものを左右する経営戦略となっています。
まとめ:未来への投資としてのスマートファクトリー(SmartFactory)
本稿では、**スマートファクトリー(SmartFactory)**の基礎知識からメリット、技術、導入ステップ、課題、そして未来像までを包括的に解説しました。
**スマートファクトリー(SmartFactory)**は、製造業が抱える多くの課題を解決し、生産性、品質、コスト競争力、そして市場への対応力を飛躍的に向上させる可能性を秘めています。導入には課題も伴いますが、明確なビジョンと計画、そして段階的なアプローチ、さらには適切なパートナーとの連携によって、着実に実現していくことが可能です。
変化の激しい時代を勝ち抜くために、**スマートファクトリー(SmartFactory)への取り組みは、もはや避けては通れない道と言えるでしょう。この記事が、貴社のスマートファクトリー(SmartFactory)**化検討の一助となり、輝かしい未来を築くための一歩となることを願っています。
スマートファクトリー導入に関するお問い合わせ
https://www.funaisoken.co.jp/solution/maker_smartfactory_703_S045
「スマートファクトリー」の導入について、自社の状況に合わせた具体的なご相談や、記事の内容に関するご不明な点などがございましたら、お気軽にお問い合わせください。経験豊富な専門のコンサルタントが、お客様の状況を丁寧にヒアリングさせていただき、最適なソリューションをご提案させていただきます。
【船井総合研究所】のスマートファクトリーソリューションについて
私たち船井総合研究所は、長年にわたり製造業の皆様の経営課題解決を支援してまいりました。その豊富な経験と確かな実績に基づき、お客様の生産性向上・自動化を強力に支援し、「スマートファクトリー化」を実現するための総合支援サービス「FunaisokenSmartFactoryConnection」を提供しています。
■ビジネス概要:
現代の製造業を取り巻く環境は、人手不足の深刻化、原材料価格の高騰、顧客からのより高度な品質要求など、常に変化しており、その厳しさを増しています。このような状況下において、製造業が持続的に成長していくためには、「スマートファクトリー化」はもはや避けて通れない喫緊の課題となっています。IoT、AI、ロボット技術などの飛躍的な進化により、工場全体のデータを高度に連携・活用し、生産性向上、品質管理の高度化、大幅な省人化、サプライチェーン全体の最適化などを実現する動きが世界中で加速しています。
「スマートファクトリー化」への戦略的な投資は、「①自動化・省人化設備(高性能ロボット、AGVなどの無人搬送車) ②デジタル化基盤(IoTプラットフォーム、高度な生産管理システムなど) ③データ分析・活用(最先端のAI、BIツールなど) ④堅牢なセキュリティ対策」といった主要な領域が特に重要となります。お客様の現状の課題や将来の明確な目標に合わせて、これらの要素に戦略的に投資していくことが、「スマートファクトリー化」を真に成功させるための重要な鍵となります。
■【Funai-soken Smart Factory Connection】の強み・選ぶべき理由
総合的なコンサルティング力: 船井総研は、幅広いコンサルティング領域で長年にわたり培ってきた豊富な知識と確かな経験を活かし、お客様の「スマートファクトリー化」を部分的な効率化ではなく、工場全体の最適化を見据えた、真に総合的な視点から強力に支援します。
豊富なネットワーク: 長年のコンサルティング活動を通じて、様々な分野のSIer(システムインテグレーター)や、最先端の技術を持つ各種ソリューションベンダーとの強固なネットワークを構築しています。お客様の抱える具体的な課題や潜在的なニーズに合わせて、最適なパートナーを選定し、質の高いソリューションを提供することが可能です。
高いプロジェクト推進力: 計画策定という上流工程から、実際のシステムの導入・実行、そして導入後の効果測定まで、「スマートファクトリー化」プロジェクトの全フェーズにおいて、お客様を強力に推進します。お客様は安心してプロジェクトを進めることができます。
徹底した顧客視点: 特定の企業や製品に偏ることなく、常にお客様の利益を最優先に考えたサービスを提供します。現状分析から始まり、真の課題の特定、そしてお客様の個別のニーズに合わせた最適なソリューション提案に至るまで、お客様に寄り添ったきめ細やかなサポートを行います。
■【Funai-soken Smart Factory Connection】による具体的なサービスの流れ
【Funai-soken Smart Factory Connection】では、お客様の「スマートファクトリー化」を以下の段階的な流れで強力に支援します。
① 現状分析・課題特定フェーズ
まず、お客様の工場を詳細に調査し、現在の生産工程、使用されている設備、日々の運用状況などを徹底的に分析します。製品分析や作業分析を通じて、自動化・ロボット化、デジタル化などを優先的に検討すべき工程を明確にします。潜在的な課題や改善の機会を特定し、お客様の個別のニーズに合わせた最適なソリューション提案のための詳細な基礎データを収集します。
② ソリューション提案フェーズ
現状分析の結果に基づき、自動化・ロボット化、デジタル化、高度な生産管理システム導入など、お客様にとって最適なソリューションを組み合わせた具体的なご提案を行います。単なる部分的な効率化ではなく、工場全体の最適化を見据えた提案を行うとともに、船井総研が長年にわたり培ってきたSIerや各種ソリューションベンダーとの強力なネットワークを活用し、お客様のニーズに最適なパートナーを選定します。
③ 導入計画策定・プロジェクト推進フェーズ
選定された信頼できるSIerやベンダーとともに、具体的な導入計画を策定します。導入スケジュール、必要な費用、各関係者の役割分担、そして期待される効果などを明確にし、プロジェクト全体の像を可視化します。船井総研の経験豊富なコンサルタントが、プロジェクトの進捗管理、関係者間の調整、そして発生する様々な課題解決などを強力に支援し、計画の着実な実行を推進します。
④ 導入後の効果測定・継続的改善フェーズ
ソリューション導入後の効果を、生産性、製品の品質、コスト削減額など、事前に設定した様々な指標を用いて厳密に測定し、当初の目標が達成されているかを客観的に評価します。その結果に基づき、継続的な改善活動を強力に支援し、「スマートファクトリー化」の更なる深化をサポートします。
■成功事例
アスザック株式会社様は、2010年代後半から自社で自動化を推進していましたが、専門知識の不足やプロジェクトを力強く推進できるリーダーシップを発揮できる人材がいないため、取り組みに限界を感じていました。また、プロジェクトを進める中で、予期せぬ仕様変更や追加要求が頻繁に発生し、コストが当初の計画よりも大幅に増加してしまうという課題も抱えていました。
そこで、船井総研の「Smart Factory Connection」をご導入いただいた結果、以下の目覚ましい効果が得られました。
計画的な自動化推進: 船井総研がプロジェクト全体の強力なリーダーシップを発揮し、アスザック株式会社様の各メンバーと緊密に連携してプロジェクトを推進したことで、ほぼ当初の計画通りに自動化を進めることができました。
対外的なアピール力向上: 自動化を積極的に進めていることが、顧客からの信頼に繋がり、結果として新たな案件の獲得にも大きく貢献しました。
自社の自動化戦略精度向上: 実施したい自動化施策に対して、船井総研の経験豊富なコンサルタントが客観的な視点からその効果の有無を判断してくれるため、自社の自動化戦略策定に非常に役立ちました。
「FunaisokenSmartFactoryConnection」導入から4年が経過した2024年には、アスザック株式会社様は前年比10%増という驚異的な売上向上を達成されました。少ない人員で生産性を大幅に向上させるという当初の目標を見事に実現されています。アスザック株式会社様は、自社だけで進めることの難しさを痛感していた自動化を、船井総合研究所のプロフェッショナルな支援によって着実に実現できたことを高く評価してくださっています。 製造業の未来を拓くスマートファクトリー(SmartFactory)とは?
現代の製造業は、グローバルな競争激化、少子高齢化による労働力不足、顧客ニーズの多様化・高度化、そして急速なデジタル技術の進展という、かつてない変化の波に直面しています。このような時代において、競争優位性を確立し、持続的な成長を遂げるための鍵として注目されているのが「スマートファクトリー(SmartFactory)」です。
しかし、「スマートファクトリー」という言葉は広く知られるようになった一方で、「具体的に何を指すのか?」「自社にどのようなメリットがあるのか?」「どうすれば実現できるのか?」といった疑問を持つ方も少なくないでしょう。
本稿では、「スマートファクトリー(SmartFactory)」に関する基礎知識から、導入によって得られる具体的なメリット、実現に不可欠な技術要素、導入プロセス、成功のためのポイント、そして未来の展望に至るまで、包括的かつ詳細に解説します。この記事を通じて、**スマートファクトリー(SmartFactory)**への理解を深め、自社の製造現場変革への第一歩を踏み出すための一助となれば幸いです。
1. スマートファクトリー(SmartFactory)の基礎知識:定義、必要性、目指す姿
まず、**スマートファクトリー(SmartFactory)**の基本的な概念を理解することから始めましょう。
1.1. スマートファクトリー(SmartFactory)の定義と仕組み
**スマートファクトリー(SmartFactory)**とは、工場内の設備、機器、作業者、生産プロセスなどがネットワーク(主にIoT技術)で接続され、そこから収集される膨大なデータをリアルタイムで分析・活用することで、生産活動全体の最適化、自律化を目指す新しい工場のあり方です。
従来の工場が各工程の部分最適化に留まっていたのに対し、**スマートファクトリー(SmartFactory)**では、設計から製造、検査、出荷、さらには保守・保全に至るまで、バリューチェーン全体をデジタルデータで繋ぎ、全体最適を図ります。これにより、状況に応じた柔軟な生産調整や、予知保全によるダウンタイムの削減、リソースの最適配分などが可能になります。
1.2. なぜ今スマートファクトリー(SmartFactory)が求められるのか?
**スマートファクトリー(SmartFactory)**の必要性が高まっている背景には、以下のような複合的な要因があります。
労働力不足の深刻化: 製造現場における人手不足は、特に日本では喫緊の課題です。自動化・省人化を進める**スマートファクトリー(SmartFactory)**は、この課題への直接的な解決策となります。
グローバル競争の激化: 低コスト生産や高い品質要求に応えるため、生産効率の抜本的な向上が不可欠です。データに基づいた改善は、競争力を維持・強化する上で欠かせません。
顧客ニーズの多様化と高度化: 多品種少量生産やマスカスタマイゼーションへの対応が求められています。**スマートファクトリー(SmartFactory)**は、生産ラインの柔軟性を高め、変化する市場要求に迅速に対応する能力を提供します。
技術の進化と普及: IoTセンサー、AI、ロボット、クラウドコンピューティングなどの技術が進化し、導入コストも下がってきたことで、**スマートファクトリー(SmartFactory)**の実現がより現実的なものとなっています。
サステナビリティへの要求: 省エネルギー化や廃棄物削減など、環境負荷低減への取り組みも重要性を増しています。データ活用によるエネルギー効率の最適化なども**スマートファクトリー(SmartFactory)**の重要な側面です。
1.3. スマートファクトリー(SmartFactory)で目指す姿
**スマートファクトリー(SmartFactory)**が目指すのは、単なる自動化や効率化だけではありません。以下のような、より高度でインテリジェントな工場の実現を目指します。
自律的な生産: 状況変化をリアルタイムで検知し、AIなどが最適な判断を下し、生産計画や設備稼働を自律的に調整します。
予知保全の実現: 設備の状態を常時監視し、故障の兆候を事前に検知してメンテナンスを行うことで、突発的な停止を防ぎ、稼働率を最大化します。
柔軟な生産体制: 市場の需要変動や仕様変更に対し、生産ラインを迅速かつ柔軟に組み替えて対応します。
データドリブンな意思決定: 経験や勘だけに頼るのではなく、収集・分析された客観的なデータに基づいて、経営判断や現場改善を行います。
人と機械の協調: 人はより付加価値の高い作業(改善、分析、判断など)に集中し、単純作業や危険作業はロボットなどが担う、安全で効率的な作業環境を実現します。
2. スマートファクトリー(SmartFactory)実現の3つの鍵率
**スマートファクトリー(SmartFactory)**を実現するためには、大きく分けて以下の3つの要素が相互に連携することが不可欠です。
2.1. データ:あらゆる情報を繋ぐ神経網
**スマートファクトリー(SmartFactory)**の根幹をなすのが「データ」です。IoTセンサーなどを活用し、生産設備(稼働状況、温度、振動等)、製品(品質データ、位置情報等)、作業者(作業時間、動線等)、環境(温度、湿度等)など、工場内のあらゆる情報をリアルタイムで収集・蓄積します。このデータが、現状把握、分析、予測、そして最適化の基盤となります。
2.2. ロボット・自動化機器:フィジカルな実行部隊
収集・分析されたデータに基づく指示を実行するのが、ロボットや自動搬送車(AGV/AMR)、自動倉庫などの自動化機器です。これらは、組み立て、搬送、検査といった物理的な作業を正確かつ効率的に行い、省人化や生産スピード向上に貢献します。近年では、人と隣り合って安全に作業できる協働ロボットの導入も進んでいます。
2.3. システム:データ活用と制御の中枢
収集したデータを蓄積・分析し、ロボットや設備への指示を行うのが各種「システム」です。MES(製造実行システム)、ERP(統合基幹業務システム)、PLM(製品ライフサイクル管理)、SCM(サプライチェーン管理)などの既存システムに加え、IoTプラットフォームやAI分析ツールなどが連携し、**スマートファクトリー(SmartFactory)**全体の頭脳として機能します。クラウドやエッジコンピューティングの活用も進んでいます。
これら3つの要素(データ、ロボット・自動化機器、システム)が、IoT、AI、5Gなどの通信技術によって有機的に結びつくことで、**スマートファクトリー(SmartFactory)**は成り立っています。これは、企業全体のデジタルトランスフォーメーション(DX)の一環としても捉えられます。
3. スマートファクトリー(SmartFactory)導入によるメリット
**スマートファクトリー(SmartFactory)**を導入することで、企業は多岐にわたるメリットを享受できます。
3.1. 生産性の飛躍的向上
自動化・省人化: ロボット等による自動化で、作業時間を短縮し、人手不足を解消。人はより高度な業務へシフト。
稼働率の最大化: 予知保全による設備ダウンタイムの削減、データに基づく最適な人員・設備配置。
ボトルネックの解消: データ分析により生産プロセス全体のボトルネックを特定し、集中的に改善。
3.2. 品質向上と安定化
リアルタイム品質監視: センサー等で製造中の製品品質を常時監視し、異常を早期に検知・対応。
不良原因の特定: 蓄積された品質データと製造条件データをAIなどで分析し、不良発生の根本原因を特定・排除。
作業の標準化: デジタルマニュアルやロボットによる作業で、人的ミスやスキル差による品質ばらつきを抑制。
3.3. コスト削減
労務費の削減: 自動化・省人化による人件費の抑制。
不良コストの削減: 不良品発生率の低減による材料費、手直し工数の削減。
エネルギーコストの削減: 設備稼働の最適化やエネルギー使用量の見える化による無駄の排除。
在庫コストの削減: 需要予測精度向上や生産計画最適化による適正在庫の維持。
3.4. リードタイム短縮と市場変化への対応力強化
生産計画の最適化: リアルタイムな情報に基づき、最適な生産順序や段取り替えを計画・実行。
サプライチェーン連携: 受注から設計、調達、生産、出荷までの情報を連携し、プロセス全体を高速化。
柔軟な生産ライン: 多品種少量生産や仕様変更に迅速に対応できるライン構成。
3.5. その他のメリット
トレーサビリティ向上: 製品個体ごとに、いつ、どこで、誰が、どのように製造したかの履歴を追跡可能にし、品質保証体制を強化。
技術・技能伝承の促進: 熟練者の動きや判断をデータ化・マニュアル化し、若手への教育や技術継承を効率化(属人化の解消)。
安全な労働環境の実現: 危険作業や過酷な作業をロボットに代替させ、労働災害リスクを低減。
従業員のモチベーション向上: 単純作業から解放され、より創造的・分析的な業務に従事することによる働きがいの向上。
企業価値・ブランドイメージ向上: 先進的な取り組みによる対外的なアピール力強化(例:アスザック株式会社様の事例)。
4. スマートファクトリー(SmartFactory)を支える主要技術
**スマートファクトリー(SmartFactory)**の実現は、様々なデジタル技術の組み合わせによって支えられています。
IoT (Internet of Things): 工場内のあらゆるモノ(設備、製品、治具、人など)にセンサーを取り付け、インターネットに接続してデータを収集・交換する基盤技術。**スマートファクトリー(SmartFactory)**の神経網と言えます。
AI (人工知能): 収集された膨大なデータを分析し、パターン認識、異常検知、需要予測、最適化提案などを行う頭脳。機械学習やディープラーニングが活用されます。
ロボット: 産業用ロボット、協働ロボットなどが、組み立て、溶接、塗装、搬送、検査などの作業を自動化します。
5G/ローカル5G: 高速・大容量・低遅延・多接続という特徴を持つ次世代通信規格。多数のセンサーやロボットをリアルタイムに接続・制御するために重要です。
クラウド/エッジコンピューティング: 大容量データの蓄積・分析基盤となるクラウドと、現場に近い場所でリアルタイムなデータ処理を行うエッジコンピューティングを適材適所で活用します。
サイバーセキュリティ: 工場ネットワークが外部と接続されるため、不正アクセスや情報漏洩を防ぐための堅牢なセキュリティ対策が不可欠です。
デジタルツイン: 現実の工場や生産ラインをデジタルの仮想空間に再現する技術。シミュレーションによる事前検証や、リアルタイムな遠隔監視・操作を可能にします。
各種システム連携: MES(製造実行システム)、ERP(統合基幹業務システム)、PLM(製品ライフサイクル管理)、SCM(サプライチェーン管理)などを連携させ、データの一元管理と活用を促進します。
これらの技術を、自社の目的や課題に合わせて適切に選択し、組み合わせていくことが**スマートファクトリー(SmartFactory)**構築の鍵となります。
5. スマートファクトリー(SmartFactory)導入のステップと成功のポイント
**スマートファクトリー(SmartFactory)**の導入は、やみくもに進めても成功しません。段階的かつ計画的なアプローチが重要です。
5.1. 導入ステップ
目的・目標設定: 「何のためにスマートファクトリー化するのか」「具体的な数値目標は何か」を明確にします(例:生産性15%向上、不良率0.5%削減)。経営層のコミットメントが不可欠です。
現状分析・課題特定: 自社の生産現場の現状を把握し、データに基づいてボトルネックとなっている課題を特定します(見える化)。
導入計画策定: 目標達成のために、どの技術を、どの範囲に、どの順序で導入するか、具体的なロードマップと投資計画を作成します。費用対効果の試算も重要です。
技術選定・パートナー選定: 計画に基づき、最適な技術、ソリューション、そして導入を支援してくれる信頼できるベンダーやコンサルティングパートナーを選定します。
PoC (Proof of Concept) / スモールスタート: まずは限定的な範囲(特定のラインや工程)で試験的に導入し、効果を検証します(小さく始めて大きく育てる)。
本格導入・横展開: PoCで効果が確認できたら、対象範囲を広げて本格導入を進めます。
運用・継続的改善: 導入後もデータを活用し、効果測定と改善活動を継続的に行い、**スマートファクトリー(SmartFactory)**を深化させていきます。
5.2. 成功のポイント
経営層の強いリーダーシップ: トップが**スマートファクトリー(SmartFactory)**化の重要性を理解し、全社的な取り組みとして強力に推進することが最も重要です。
明確なビジョンと目標共有: 全従業員が目指す姿と目標を共有し、一体感を持って取り組むことが大切です。
「見える化」からのスタート: まずは現状をデータで正確に把握することから始め、課題を明確にすることが着実な第一歩です。
スモールスタートと段階的導入: 最初から完璧を目指さず、小さく始めて効果を検証しながら、リスクを抑えて進めます。
データ活用文化の醸成: 収集したデータを意思決定や改善活動に活かす文化を組織全体で育てることが重要です。人材育成も並行して行います。
現場との連携: 実際にシステムや設備を使う現場の意見を取り入れ、使いやすく効果的な**スマートファクトリー(SmartFactory)**を目指します。
適切なパートナーとの連携: 自社だけでは知見やリソースが不足する場合、経験豊富な外部パートナー(コンサルタント、ベンダー等)と協力することが成功の鍵となります。特に、アスザック株式会社様の事例のように、プロジェクト推進力や客観的な効果判断を提供できるパートナーは有効です。
セキュリティ対策の徹底: 導入計画の初期段階からセキュリティリスクを考慮し、対策を講じます。
6. スマートファクトリー(SmartFactory)導入における課題と対策
**スマートファクトリー(SmartFactory)**導入には多くのメリットがありますが、一方で乗り越えるべき課題も存在します。
課題1:導入・運用コスト:
対策: スモールスタートや段階的導入で初期投資を抑制。リースや補助金の活用。費用対効果(ROI)を事前にしっかり試算・評価。
課題2:IT・デジタル人材の不足:
対策: 社内人材の育成(研修、OJT)。外部専門家(コンサルタント、ベンダー)の活用。使いやすいツールの選定。
課題3:セキュリティリスク:
対策: 最新のセキュリティ対策(ファイアウォール、侵入検知システム等)の導入。従業員へのセキュリティ教育。専門家による診断。
課題4:既存システム・設備との連携:
対策: 連携可能なインターフェースを持つシステムの選定。段階的な設備更新計画。レガシーシステムに対応できるパートナーの選定。
課題5:組織文化・抵抗:
対策: 経営層からの明確なメッセージ発信。導入メリットの丁寧な説明と従業員の巻き込み。成功体験の共有。
これらの課題を事前に認識し、対策を計画に盛り込むことが、**スマートファクトリー(SmartFactory)**導入プロジェクトを円滑に進める上で重要です。
7. スマートファクトリー(SmartFactory)の未来と最新トレンド
**スマートファクトリー(SmartFactory)**は、今後も技術の進化とともに更なる発展が期待されています。
AIの更なる高度化: より自律的な判断・制御、複雑な要因分析、高度な需要予測などが可能に。
サステナビリティとの融合: 省エネ、資源効率の最大化、廃棄物削減など、環境負荷低減(グリーンファクトリー)への貢献がより重視されます。
マスカスタマイゼーションの進展: 個別最適化された製品を効率的に生産する体制が進化します。
人間中心のスマートファクトリー: 人とロボットがより高度に協調し、人は創造性や判断力が求められる業務に集中する、働きがいのある工場へ。
サプライチェーン全体への展開: 工場内だけでなく、サプライヤーから顧客まで、バリューチェーン全体がデジタルで繋がり、より高度な連携が実現します。
**スマートファクトリー(SmartFactory)**は、単なる生産現場の効率化ツールではなく、企業の競争力そのものを左右する経営戦略となっています。
まとめ:未来への投資としてのスマートファクトリー(SmartFactory)
本稿では、**スマートファクトリー(SmartFactory)**の基礎知識からメリット、技術、導入ステップ、課題、そして未来像までを包括的に解説しました。
**スマートファクトリー(SmartFactory)**は、製造業が抱える多くの課題を解決し、生産性、品質、コスト競争力、そして市場への対応力を飛躍的に向上させる可能性を秘めています。導入には課題も伴いますが、明確なビジョンと計画、そして段階的なアプローチ、さらには適切なパートナーとの連携によって、着実に実現していくことが可能です。
変化の激しい時代を勝ち抜くために、**スマートファクトリー(SmartFactory)への取り組みは、もはや避けては通れない道と言えるでしょう。この記事が、貴社のスマートファクトリー(SmartFactory)**化検討の一助となり、輝かしい未来を築くための一歩となることを願っています。
スマートファクトリー導入に関するお問い合わせ
https://www.funaisoken.co.jp/solution/maker_smartfactory_703_S045
「スマートファクトリー」の導入について、自社の状況に合わせた具体的なご相談や、記事の内容に関するご不明な点などがございましたら、お気軽にお問い合わせください。経験豊富な専門のコンサルタントが、お客様の状況を丁寧にヒアリングさせていただき、最適なソリューションをご提案させていただきます。
【船井総合研究所】のスマートファクトリーソリューションについて
私たち船井総合研究所は、長年にわたり製造業の皆様の経営課題解決を支援してまいりました。その豊富な経験と確かな実績に基づき、お客様の生産性向上・自動化を強力に支援し、「スマートファクトリー化」を実現するための総合支援サービス「FunaisokenSmartFactoryConnection」を提供しています。
■ビジネス概要:
現代の製造業を取り巻く環境は、人手不足の深刻化、原材料価格の高騰、顧客からのより高度な品質要求など、常に変化しており、その厳しさを増しています。このような状況下において、製造業が持続的に成長していくためには、「スマートファクトリー化」はもはや避けて通れない喫緊の課題となっています。IoT、AI、ロボット技術などの飛躍的な進化により、工場全体のデータを高度に連携・活用し、生産性向上、品質管理の高度化、大幅な省人化、サプライチェーン全体の最適化などを実現する動きが世界中で加速しています。
「スマートファクトリー化」への戦略的な投資は、「①自動化・省人化設備(高性能ロボット、AGVなどの無人搬送車) ②デジタル化基盤(IoTプラットフォーム、高度な生産管理システムなど) ③データ分析・活用(最先端のAI、BIツールなど) ④堅牢なセキュリティ対策」といった主要な領域が特に重要となります。お客様の現状の課題や将来の明確な目標に合わせて、これらの要素に戦略的に投資していくことが、「スマートファクトリー化」を真に成功させるための重要な鍵となります。
■【Funai-soken Smart Factory Connection】の強み・選ぶべき理由
総合的なコンサルティング力: 船井総研は、幅広いコンサルティング領域で長年にわたり培ってきた豊富な知識と確かな経験を活かし、お客様の「スマートファクトリー化」を部分的な効率化ではなく、工場全体の最適化を見据えた、真に総合的な視点から強力に支援します。
豊富なネットワーク: 長年のコンサルティング活動を通じて、様々な分野のSIer(システムインテグレーター)や、最先端の技術を持つ各種ソリューションベンダーとの強固なネットワークを構築しています。お客様の抱える具体的な課題や潜在的なニーズに合わせて、最適なパートナーを選定し、質の高いソリューションを提供することが可能です。
高いプロジェクト推進力: 計画策定という上流工程から、実際のシステムの導入・実行、そして導入後の効果測定まで、「スマートファクトリー化」プロジェクトの全フェーズにおいて、お客様を強力に推進します。お客様は安心してプロジェクトを進めることができます。
徹底した顧客視点: 特定の企業や製品に偏ることなく、常にお客様の利益を最優先に考えたサービスを提供します。現状分析から始まり、真の課題の特定、そしてお客様の個別のニーズに合わせた最適なソリューション提案に至るまで、お客様に寄り添ったきめ細やかなサポートを行います。
■【Funai-soken Smart Factory Connection】による具体的なサービスの流れ
【Funai-soken Smart Factory Connection】では、お客様の「スマートファクトリー化」を以下の段階的な流れで強力に支援します。
① 現状分析・課題特定フェーズ
まず、お客様の工場を詳細に調査し、現在の生産工程、使用されている設備、日々の運用状況などを徹底的に分析します。製品分析や作業分析を通じて、自動化・ロボット化、デジタル化などを優先的に検討すべき工程を明確にします。潜在的な課題や改善の機会を特定し、お客様の個別のニーズに合わせた最適なソリューション提案のための詳細な基礎データを収集します。
② ソリューション提案フェーズ
現状分析の結果に基づき、自動化・ロボット化、デジタル化、高度な生産管理システム導入など、お客様にとって最適なソリューションを組み合わせた具体的なご提案を行います。単なる部分的な効率化ではなく、工場全体の最適化を見据えた提案を行うとともに、船井総研が長年にわたり培ってきたSIerや各種ソリューションベンダーとの強力なネットワークを活用し、お客様のニーズに最適なパートナーを選定します。
③ 導入計画策定・プロジェクト推進フェーズ
選定された信頼できるSIerやベンダーとともに、具体的な導入計画を策定します。導入スケジュール、必要な費用、各関係者の役割分担、そして期待される効果などを明確にし、プロジェクト全体の像を可視化します。船井総研の経験豊富なコンサルタントが、プロジェクトの進捗管理、関係者間の調整、そして発生する様々な課題解決などを強力に支援し、計画の着実な実行を推進します。
④ 導入後の効果測定・継続的改善フェーズ
ソリューション導入後の効果を、生産性、製品の品質、コスト削減額など、事前に設定した様々な指標を用いて厳密に測定し、当初の目標が達成されているかを客観的に評価します。その結果に基づき、継続的な改善活動を強力に支援し、「スマートファクトリー化」の更なる深化をサポートします。
■成功事例
アスザック株式会社様は、2010年代後半から自社で自動化を推進していましたが、専門知識の不足やプロジェクトを力強く推進できるリーダーシップを発揮できる人材がいないため、取り組みに限界を感じていました。また、プロジェクトを進める中で、予期せぬ仕様変更や追加要求が頻繁に発生し、コストが当初の計画よりも大幅に増加してしまうという課題も抱えていました。
そこで、船井総研の「Smart Factory Connection」をご導入いただいた結果、以下の目覚ましい効果が得られました。
計画的な自動化推進: 船井総研がプロジェクト全体の強力なリーダーシップを発揮し、アスザック株式会社様の各メンバーと緊密に連携してプロジェクトを推進したことで、ほぼ当初の計画通りに自動化を進めることができました。
対外的なアピール力向上: 自動化を積極的に進めていることが、顧客からの信頼に繋がり、結果として新たな案件の獲得にも大きく貢献しました。
自社の自動化戦略精度向上: 実施したい自動化施策に対して、船井総研の経験豊富なコンサルタントが客観的な視点からその効果の有無を判断してくれるため、自社の自動化戦略策定に非常に役立ちました。
「FunaisokenSmartFactoryConnection」導入から4年が経過した2024年には、アスザック株式会社様は前年比10%増という驚異的な売上向上を達成されました。少ない人員で生産性を大幅に向上させるという当初の目標を見事に実現されています。アスザック株式会社様は、自社だけで進めることの難しさを痛感していた自動化を、船井総合研究所のプロフェッショナルな支援によって着実に実現できたことを高く評価してくださっています。