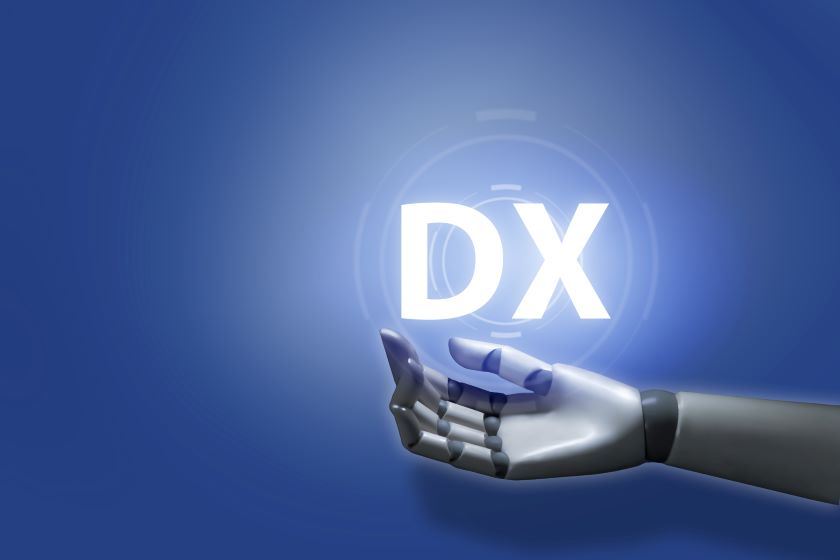
食品業界の未来を拓く!スマート化で乗り越える3つの課題
2025.08.21
はじめに:今、なぜ食品製造業はスマート化を急ぐべきなのか
日本の食品製造業は、消費者の多様なニーズに応える多品種少量生産へと急速にシフトしています。しかし、その一方で、業界全体が構造的な課題に直面しているのをご存知でしょうか。農林水産省の調査データ(令和2年度)によると、食品産業の労働生産性(1人当たり年間付加価値額)は、他産業と比べて低い水準にあります。さらに、食品製造業の欠員率は他の製造業と比べても高い値で推移しており、人員確保は依然として厳しい状況が続いています。
このような状況は、食品のデリケートな特性や多品種少量生産への対応が難しく、人手に頼らざるを得ない作業が多いことが主な原因です。しかし、この現状を「避けられない現実」として諦める必要はありません。今こそ、急速に進展するスマート技術(AI、ロボット、IoT)を戦略的に活用し、この課題を根本から解決すべき時です。
本コラムでは、農林水産省の最新データや国の施策を読み解きながら、食品業界が持続可能な成長を遂げるために、協働ロボットがどのように貢献できるのかを、そのメリット・デメリットを含めて解説します。
食品業界の現状と協働ロボットを導入すべき理由
日本の食品業界は以下の3つの主要な課題を抱えています。
1. 低い労働生産性と深刻な人手不足
食品製造業の労働生産性は、他産業と比べて低い状況にあります。これは、多くの作業が手作業に依存しているためであり、生産効率の向上が進みにくい構造的な問題です。さらに、欠員率が高いことからもわかるように、労働力不足は慢性化しており、採用難が深刻です。
【協働ロボットが解決できる理由】 協働ロボットは、この人手不足を補い、生産性を根本から向上させるための有効な手段です。ロボットは疲れることなく、24時間稼働が可能です。人が作業しない夜間や休日も稼働を続けることで、人手不足を補い、生産量を安定させることができます。これにより、労働力不足による生産機会の損失を防ぎ、企業の収益性を高めることができます。
2. 品質安定の難しさと事業継続リスク
手作業による工程では、作業者の熟練度や体調によって品質にバラつきが生じることがあります。また、特定の熟練作業者に依存する体制は、その人が欠けた場合に事業継続が困難になるというリスクをはらんでいます。
【協働ロボットが解決できる理由】 協働ロボットは、一度設定された作業を常に正確かつ均一に繰り返します。これにより、誰が作業しても安定した品質を保ち、製品の不良率を低減できます。また、作業のノウハウをロボットのプログラムとして記録することで、属人化を解消し、誰でも同じ品質を再現できる体制を構築できます。これは、事業継続リスクを低減する上で非常に重要な要素です。
3. 労働環境の改善と企業の魅力向上
食品製造の現場には、繰り返し行う作業や、重いものを持ち運ぶ作業が多く、従業員の身体的負担を増大させています。これは、若年層の入職を遠ざける大きな要因となっています。
【協働ロボットが解決できる理由】 協働ロボットは、これらの単純かつ重労働な作業を代行します。これにより、従業員は重い荷物から解放され、身体的な負担が大幅に軽減されます。労働環境が改善されることで、従業員の定着率が向上し、企業の魅力が高まります。これは、新たな人材確保を有利に進める上でも大きなメリットとなります。
協働ロボット導入のメリットとデメリット
協働ロボットの導入は、多くのメリットをもたらしますが、同時にデメリットも存在します。導入を成功させるためには、これらを両方とも正しく理解しておくことが不可欠です。
協働ロボット導入の5つのメリット
労働力不足の解消: ロボットが単純作業を代行することで、人手不足を補い、生産量を安定させることができます。
身体的負担の軽減: 重労働から従業員を解放し、腰痛や肩痛といった労災リスクを低減します。
品質の均一化: ロボットはプログラム通りに正確な作業を繰り返すため、製品の品質にバラつきがなくなります。
生産性向上: 休憩なしで24時間稼働が可能なため、機械の稼働率が向上し、生産量を増加させることができます。
技術継承の仕組み化: 熟練作業者のノウハウをロボットのプログラムとして記録することで、技術の属人化を防ぎ、次世代に継承できます。
協働ロボット導入の5つのデメリットと対策
初期投資費用: 協働ロボットは従来の産業用ロボットに比べて安価ですが、導入には初期費用がかかります。
◦対策: 国や自治体の補助金・助成金制度を積極的に活用することで、導入負担を軽減できます。また、導入前のROI(投資対効果)計算も重要です。
動作速度の限界: 人との安全な協働を前提としているため、産業用ロボットに比べて動作速度が遅い場合があります。
◦対策: ロボットの導入目的を「スピードアップ」ではなく、「稼働時間の延長」や「ライン全体のボトルネック解消」に設定することが重要です。
複雑な作業への対応の難しさ: 多様な製品や、毎回位置が異なるワークへの対応は、高度なティーチングやセンサー技術が必要となり、難易度が高くなります。
◦対策: 最初は単純な繰り返し作業から始め、導入ノウハウを蓄積する「スモールスタート」をお勧めします。
運用・保守に必要な人材: 導入後、ロボットのトラブル対応やプログラム修正、メンテナンスを行うための専門知識を持った人材が必要です。
◦対策: ロボットメーカーやSIer(システムインテグレーター)が提供する研修プログラムを積極的に活用し、社内で運用できる人材を育成することが不可欠です。
従業員の抵抗感: 新しい技術の導入は、「自分の仕事がなくなるのではないか」という従業員の不安を招くことがあります。
◦対策: 協働ロボットはあくまで「パートナー」であることを丁寧に説明し、従業員を導入プロセスに巻き込むことが重要です。ロボットが単純作業を代行することで、より付加価値の高い業務にシフトできることを具体的に伝えましょう。
今後の方向性:国が推進するスマート食品産業の未来
農林水産省は、食品製造業の労働生産性を2030年までに最低3割向上させるという目標を掲げ、スマート化を強力に推進しています。これは、企業の自主的な取り組みに任せるだけでなく、国全体でバックアップしていくという強い意志の表れです。
スマート技術の社会実装支援 「スマート食品産業実証事業」では、AIやロボット、IoTを活用した自動化・リモート化技術を実際の現場に導入し、その成果を横展開する取り組みを支援しています。
安全・衛生ガイドラインの策定 「スマート食品産業安全確保推進事業」では、人とロボットが安全に協働するためのガイドラインを作成し、食品製造現場へのスムーズな導入を後押ししています。これにより、企業は安心してロボットを導入でき、リスクを管理しながら生産性を高めることが可能になります。
フードテックと持続可能性 「みどりの食料システム戦略」や「フードテック官民協議会」といった取り組みからもわかるように、日本の食料システムは、環境負荷の低減や持続可能性を追求する大きな流れの中にあります。協働ロボットをはじめとするスマート技術の活用は、単なる生産性向上に留まらず、食品ロス削減やエネルギー効率化といった、より広範な社会課題の解決にも貢献するでしょう。
まとめ:協働ロボットが切り拓く、新たな時代の食品製造業
本コラムでは、日本の食品製造業が直面する課題と、協働ロボットがその解決に貢献できる理由、そして導入のメリット・デメリットについて解説しました。
協働ロボットは、人手不足を補い、品質を安定させ、従業員の労働環境を改善する「パートナー」です。デメリットを正しく理解し、国が提供する支援策を有効活用することで、中小企業でも十分に導入効果を享受できます。
人手不足を「時代のせい」と諦めるのではなく、協働ロボットを「未来を創るためのツール」として捉え、行動を起こすことが、貴社の競争力を高める第一歩です。
今こそ、私たちと共にその一歩を踏み出し、持続可能な成長を目指しませんか。 はじめに:今、なぜ食品製造業はスマート化を急ぐべきなのか
日本の食品製造業は、消費者の多様なニーズに応える多品種少量生産へと急速にシフトしています。しかし、その一方で、業界全体が構造的な課題に直面しているのをご存知でしょうか。農林水産省の調査データ(令和2年度)によると、食品産業の労働生産性(1人当たり年間付加価値額)は、他産業と比べて低い水準にあります。さらに、食品製造業の欠員率は他の製造業と比べても高い値で推移しており、人員確保は依然として厳しい状況が続いています。
このような状況は、食品のデリケートな特性や多品種少量生産への対応が難しく、人手に頼らざるを得ない作業が多いことが主な原因です。しかし、この現状を「避けられない現実」として諦める必要はありません。今こそ、急速に進展するスマート技術(AI、ロボット、IoT)を戦略的に活用し、この課題を根本から解決すべき時です。
本コラムでは、農林水産省の最新データや国の施策を読み解きながら、食品業界が持続可能な成長を遂げるために、協働ロボットがどのように貢献できるのかを、そのメリット・デメリットを含めて解説します。
食品業界の現状と協働ロボットを導入すべき理由
日本の食品業界は以下の3つの主要な課題を抱えています。
1. 低い労働生産性と深刻な人手不足
食品製造業の労働生産性は、他産業と比べて低い状況にあります。これは、多くの作業が手作業に依存しているためであり、生産効率の向上が進みにくい構造的な問題です。さらに、欠員率が高いことからもわかるように、労働力不足は慢性化しており、採用難が深刻です。
【協働ロボットが解決できる理由】 協働ロボットは、この人手不足を補い、生産性を根本から向上させるための有効な手段です。ロボットは疲れることなく、24時間稼働が可能です。人が作業しない夜間や休日も稼働を続けることで、人手不足を補い、生産量を安定させることができます。これにより、労働力不足による生産機会の損失を防ぎ、企業の収益性を高めることができます。
2. 品質安定の難しさと事業継続リスク
手作業による工程では、作業者の熟練度や体調によって品質にバラつきが生じることがあります。また、特定の熟練作業者に依存する体制は、その人が欠けた場合に事業継続が困難になるというリスクをはらんでいます。
【協働ロボットが解決できる理由】 協働ロボットは、一度設定された作業を常に正確かつ均一に繰り返します。これにより、誰が作業しても安定した品質を保ち、製品の不良率を低減できます。また、作業のノウハウをロボットのプログラムとして記録することで、属人化を解消し、誰でも同じ品質を再現できる体制を構築できます。これは、事業継続リスクを低減する上で非常に重要な要素です。
3. 労働環境の改善と企業の魅力向上
食品製造の現場には、繰り返し行う作業や、重いものを持ち運ぶ作業が多く、従業員の身体的負担を増大させています。これは、若年層の入職を遠ざける大きな要因となっています。
【協働ロボットが解決できる理由】 協働ロボットは、これらの単純かつ重労働な作業を代行します。これにより、従業員は重い荷物から解放され、身体的な負担が大幅に軽減されます。労働環境が改善されることで、従業員の定着率が向上し、企業の魅力が高まります。これは、新たな人材確保を有利に進める上でも大きなメリットとなります。
協働ロボット導入のメリットとデメリット
協働ロボットの導入は、多くのメリットをもたらしますが、同時にデメリットも存在します。導入を成功させるためには、これらを両方とも正しく理解しておくことが不可欠です。
協働ロボット導入の5つのメリット
労働力不足の解消: ロボットが単純作業を代行することで、人手不足を補い、生産量を安定させることができます。
身体的負担の軽減: 重労働から従業員を解放し、腰痛や肩痛といった労災リスクを低減します。
品質の均一化: ロボットはプログラム通りに正確な作業を繰り返すため、製品の品質にバラつきがなくなります。
生産性向上: 休憩なしで24時間稼働が可能なため、機械の稼働率が向上し、生産量を増加させることができます。
技術継承の仕組み化: 熟練作業者のノウハウをロボットのプログラムとして記録することで、技術の属人化を防ぎ、次世代に継承できます。
協働ロボット導入の5つのデメリットと対策
初期投資費用: 協働ロボットは従来の産業用ロボットに比べて安価ですが、導入には初期費用がかかります。
◦対策: 国や自治体の補助金・助成金制度を積極的に活用することで、導入負担を軽減できます。また、導入前のROI(投資対効果)計算も重要です。
動作速度の限界: 人との安全な協働を前提としているため、産業用ロボットに比べて動作速度が遅い場合があります。
◦対策: ロボットの導入目的を「スピードアップ」ではなく、「稼働時間の延長」や「ライン全体のボトルネック解消」に設定することが重要です。
複雑な作業への対応の難しさ: 多様な製品や、毎回位置が異なるワークへの対応は、高度なティーチングやセンサー技術が必要となり、難易度が高くなります。
◦対策: 最初は単純な繰り返し作業から始め、導入ノウハウを蓄積する「スモールスタート」をお勧めします。
運用・保守に必要な人材: 導入後、ロボットのトラブル対応やプログラム修正、メンテナンスを行うための専門知識を持った人材が必要です。
◦対策: ロボットメーカーやSIer(システムインテグレーター)が提供する研修プログラムを積極的に活用し、社内で運用できる人材を育成することが不可欠です。
従業員の抵抗感: 新しい技術の導入は、「自分の仕事がなくなるのではないか」という従業員の不安を招くことがあります。
◦対策: 協働ロボットはあくまで「パートナー」であることを丁寧に説明し、従業員を導入プロセスに巻き込むことが重要です。ロボットが単純作業を代行することで、より付加価値の高い業務にシフトできることを具体的に伝えましょう。
今後の方向性:国が推進するスマート食品産業の未来
農林水産省は、食品製造業の労働生産性を2030年までに最低3割向上させるという目標を掲げ、スマート化を強力に推進しています。これは、企業の自主的な取り組みに任せるだけでなく、国全体でバックアップしていくという強い意志の表れです。
スマート技術の社会実装支援 「スマート食品産業実証事業」では、AIやロボット、IoTを活用した自動化・リモート化技術を実際の現場に導入し、その成果を横展開する取り組みを支援しています。
安全・衛生ガイドラインの策定 「スマート食品産業安全確保推進事業」では、人とロボットが安全に協働するためのガイドラインを作成し、食品製造現場へのスムーズな導入を後押ししています。これにより、企業は安心してロボットを導入でき、リスクを管理しながら生産性を高めることが可能になります。
フードテックと持続可能性 「みどりの食料システム戦略」や「フードテック官民協議会」といった取り組みからもわかるように、日本の食料システムは、環境負荷の低減や持続可能性を追求する大きな流れの中にあります。協働ロボットをはじめとするスマート技術の活用は、単なる生産性向上に留まらず、食品ロス削減やエネルギー効率化といった、より広範な社会課題の解決にも貢献するでしょう。
まとめ:協働ロボットが切り拓く、新たな時代の食品製造業
本コラムでは、日本の食品製造業が直面する課題と、協働ロボットがその解決に貢献できる理由、そして導入のメリット・デメリットについて解説しました。
協働ロボットは、人手不足を補い、品質を安定させ、従業員の労働環境を改善する「パートナー」です。デメリットを正しく理解し、国が提供する支援策を有効活用することで、中小企業でも十分に導入効果を享受できます。
人手不足を「時代のせい」と諦めるのではなく、協働ロボットを「未来を創るためのツール」として捉え、行動を起こすことが、貴社の競争力を高める第一歩です。
今こそ、私たちと共にその一歩を踏み出し、持続可能な成長を目指しませんか。