記事公開日:2020.05.22
最終更新日:2022.12.14
【成功事例に学ぶ】産業用ロボット活用による小物部品出庫(ピッキング)の自動化
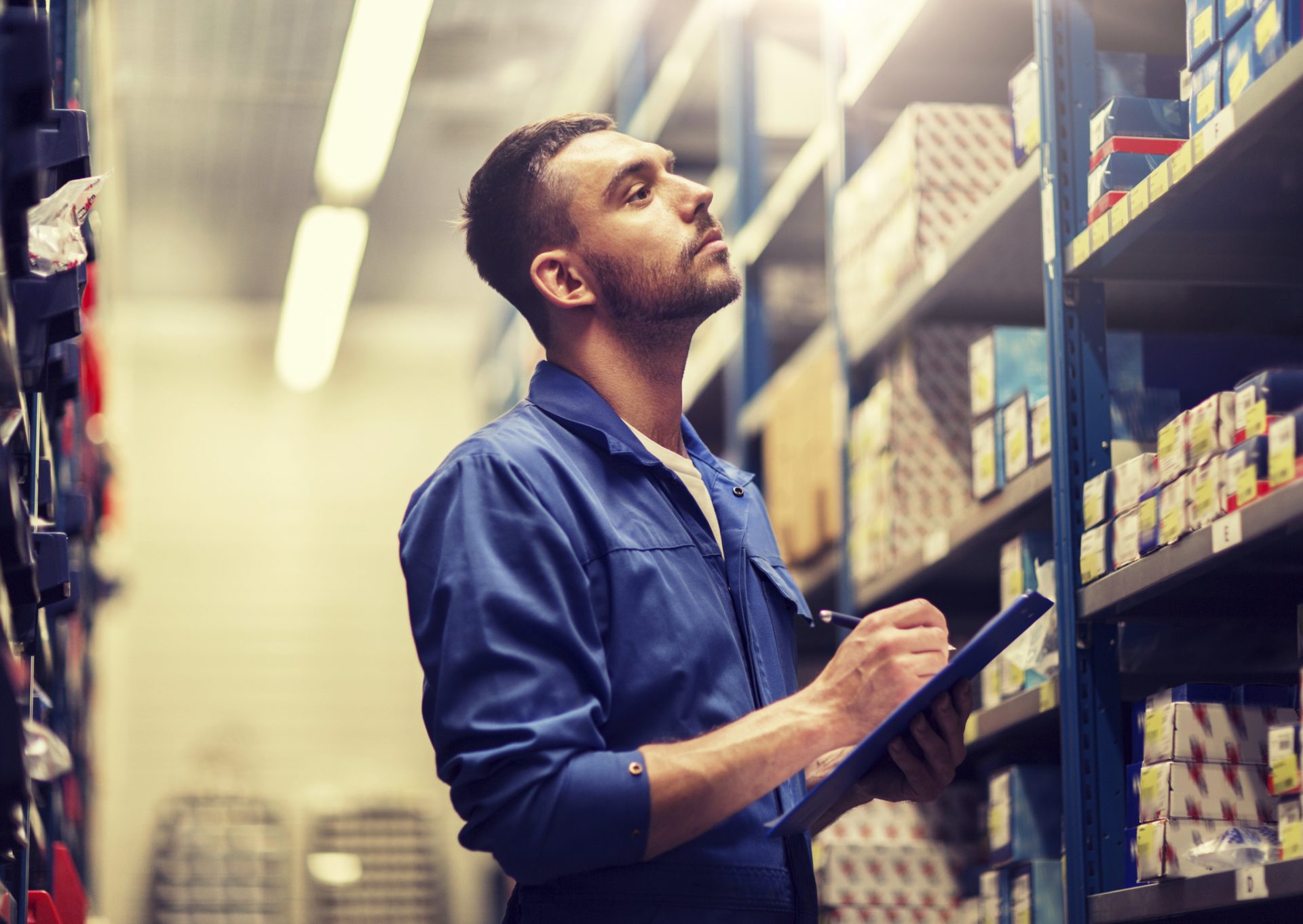
※以下導入事例は一般社団法人 日本ロボット工業会(JARA)「ロボット導入実証事業:事例紹介ハンドブック2017 」より抜粋
企業情報
業種:金属部品製造業
従業員規模:500名
エリア:関西
投資金額 66,000千円
直接効果・・省人効果4名省人(労働生産性3倍)
間接効果・・ミスピッキングの抑制、労働環境改善
この事例におけるロボット化によるメリット
□ 人手に頼っていた部品の入出庫作業(使用先別の仕分け)のロボット化を実現。
□ 入庫時の衝撃や部品の接触による傷、破損を防止するハンドリング。
□ 4名分の工数を省人化
課題
こちらの企業様では、毎日の生産に合わせて自動機を製作する為に必要な部品をピッキングする作業を6名で実施されていました。ピッキング作業は従来の部品棚に並んでいるコンテナから一つ一つリストと照合しながら歩いて部品を探す為に部品間違いやピッキングの時間に多くの工数を費やしていました。歩行量が多く時間もかかる作業である点とピッキングが完了しないと生産が開始できないという点、6名もの作業者が必要という点、一人当たりの労働生産性を向上させる為に自動化を取り組む必要がありました。
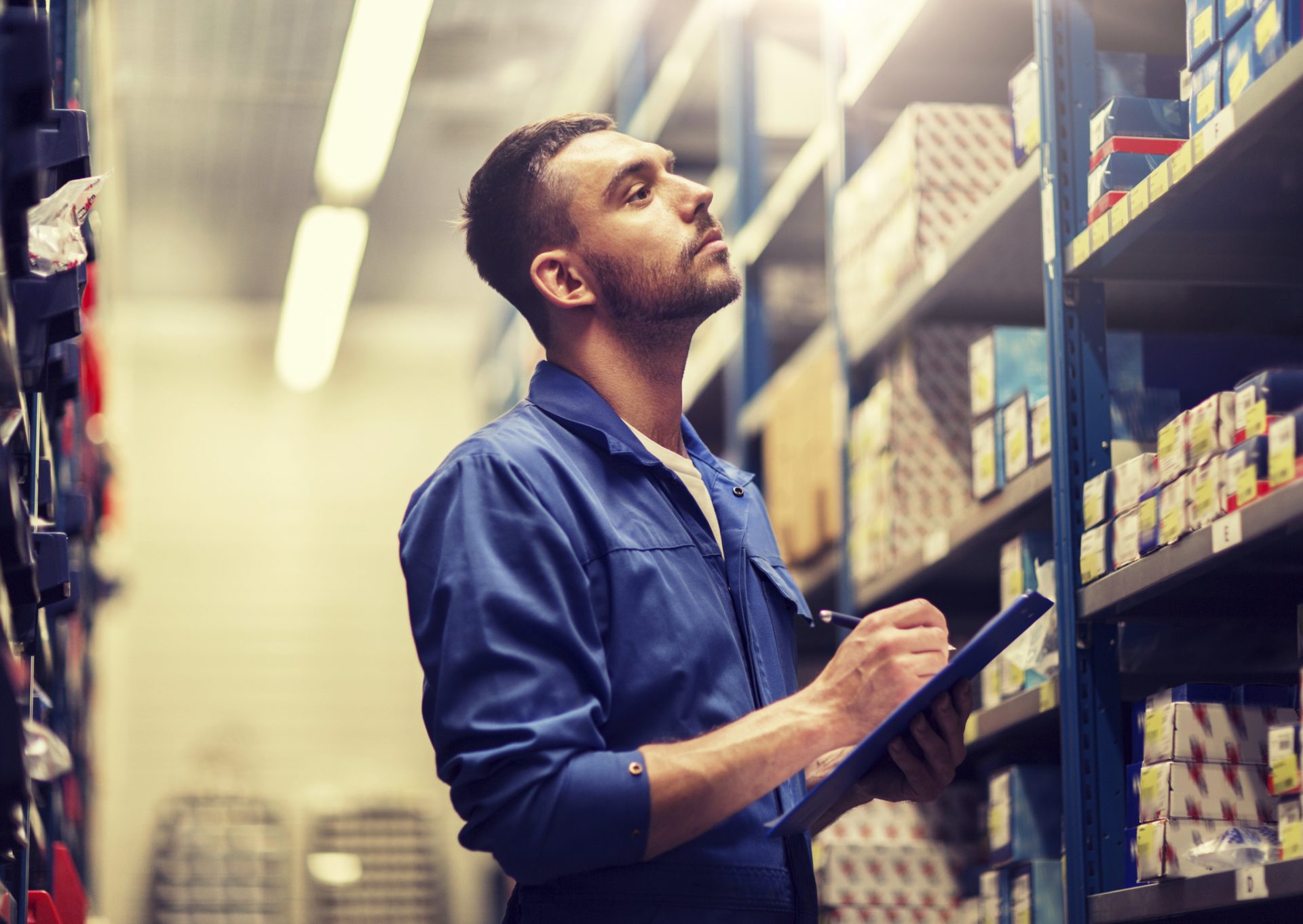
ロボットを導入した工程
大小様々な形状で3000品目ある自動機組立用部品のピッキング作業
ポイント
貨幣処理機、自動サービス機器の組立用に納品された部品を、各組立ラインの工程別に用意された部品箱に入庫(振り分け)する。部品は、材質、大きさ、重量、形状がそれぞれ異なり、1日に3,000品目が入荷している。
この作業を、可動式の垂直多関節ロボット2台を使用し自動化を実施した。作業者が伝票のバーコードを読み取り、部品をコンベア上のトレーに入れると、バーコードの情報をもとに専用アプリケーションが必要な情報をICタグに書き込み、これを利用してロボットが行き先別の部品箱に部品を投入するシステムである。
ハンドリング方法の検討により、重量2,000gまでの部品の傷つかない形での投入を実現した。作業者に占める高齢者や女性の比率が高いため、これらの自動化をはかることで、作業者を身体および神経疲労から開放するとともに、4名分の工数が削減できた。
コンサルタントの視点
今回の事例の様に、製造業のうち特に組立を行う業態では、部品のピッキングが必要不可欠です。ピッキングを自動化する為には色々な方法がありますがこちらの企業様の様に汎用の多関節ロボットを用いて投資額を抑制しつつ自社で使いやすい様にカスタマイズする方法もあります。
産業用ロボットとQRコードなどによるデジタル機器との併用による部品管理は直近では多くのメーカーが開発設計を行っており、部品の入出庫を全自動で行う自動倉庫がコンパクトサイズで販売されるようになりました。ロボットとQR、ICタグ等のデジタル機器を用いた自動化システムの開発は今後更に加速していく事でしょう。
またアプリケーションについても改良が加えられロボットに対して知見が無い人でも操作できる様に更に使いやすくなっていく事でしょう。このような自動ピッキングシステムは大規模の倉庫だけではなく、小規模で多品種少量生産方式の採用している企業に導入してこそ真価を発揮すると考えています。
日本の働き手の減少の問題は深刻であり、すでにこのような倉庫でのピッキングシステムを導入し自動化されている企業様も多いです。まだ自動化に取り組まれていない企業様は要チェックですね。
ーーーーーーーーーーーーーーーーーーーーーーーーーーーーーーーーーー
自動化・ロボット化事例集 vol.2
本事例集は、全国の先進的な工場が取り組む「自動化・ロボット化」の事例をまとめたものとなります。
これから自動化・ロボット化に取組もうと考える皆さまに、
「工場にロボット・IoTを導入する」ための具体的なノウハウを、
事例を通して知っていただくことを目的に作成しました。
※こちらの事例集は、導入を検討している工場の担当者様限定となっております。
同業他社、メーカーや商社、SI事業者の方にはご送付をお断わりさせていただいております。
ーーーーーーーーーーーーーーーーーーーーーーーーーーーーーーーーーー
https://smart-factory.funaisoken.co.jp/download/automation-robotization-examples-02/
関連コラム
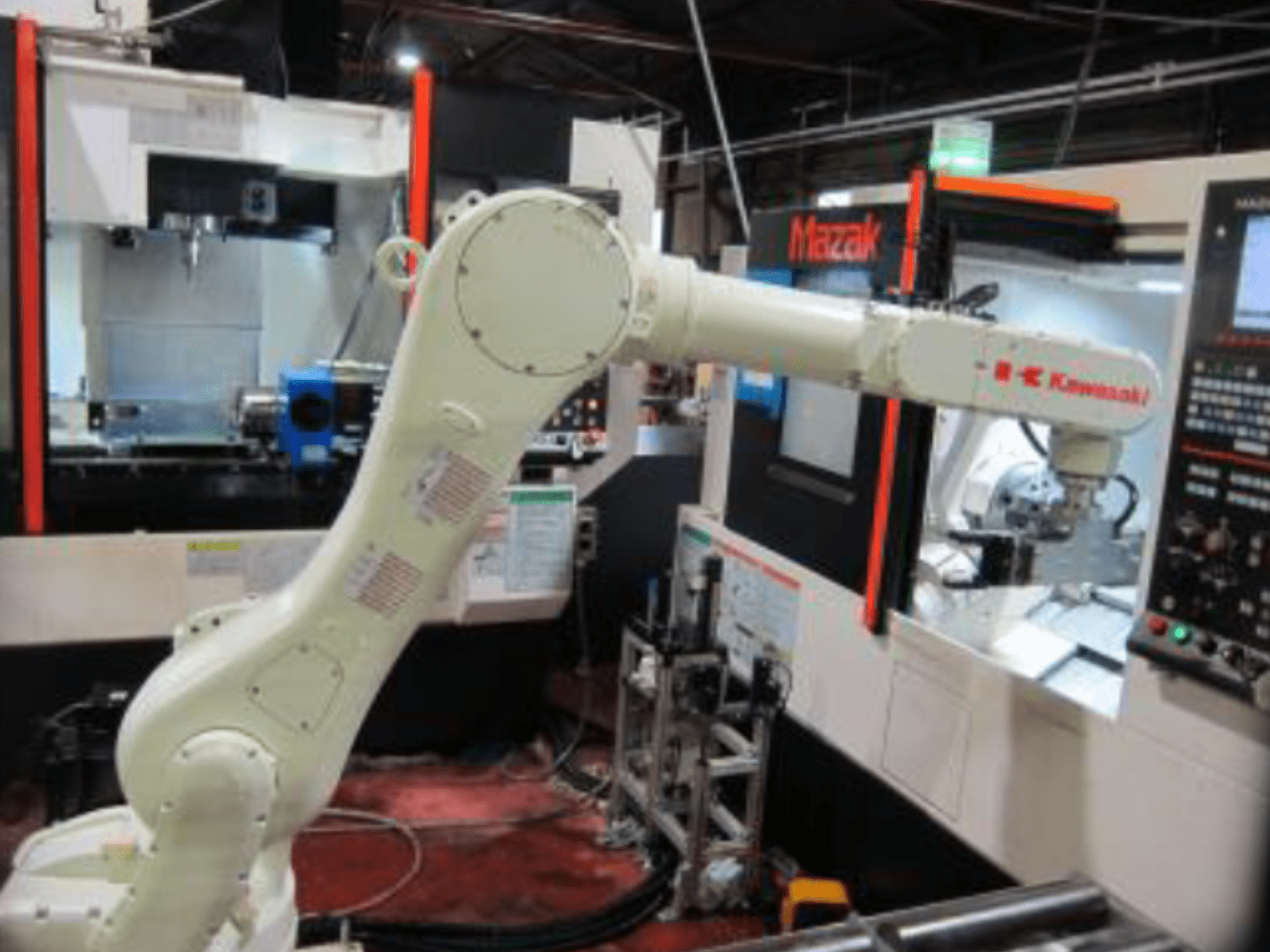
地場産業の素材加工工程にロボット導入
2019.06.19
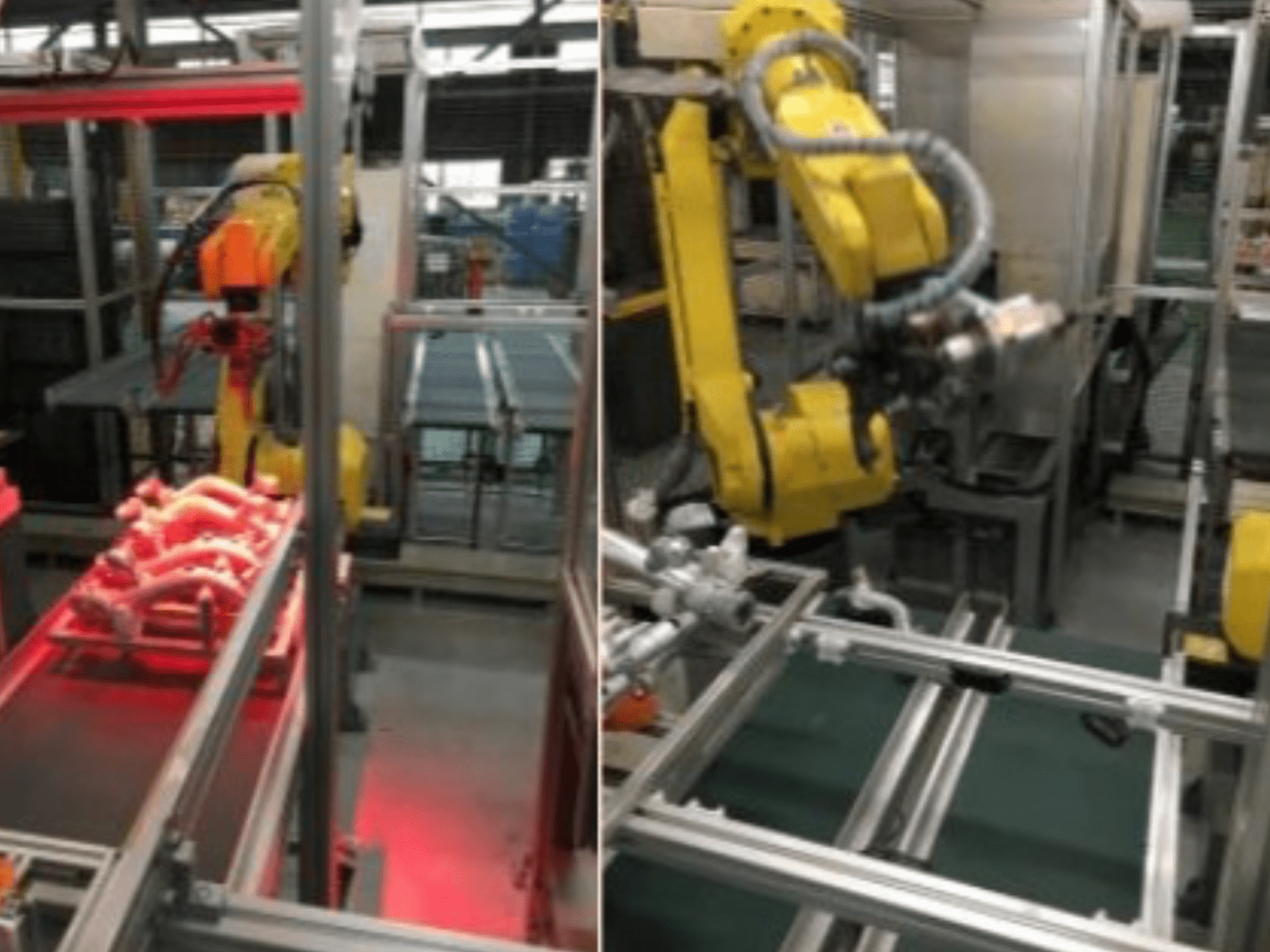
アルミ鋳造ラインの仕上げ作業にロボットを導入
2019.06.25
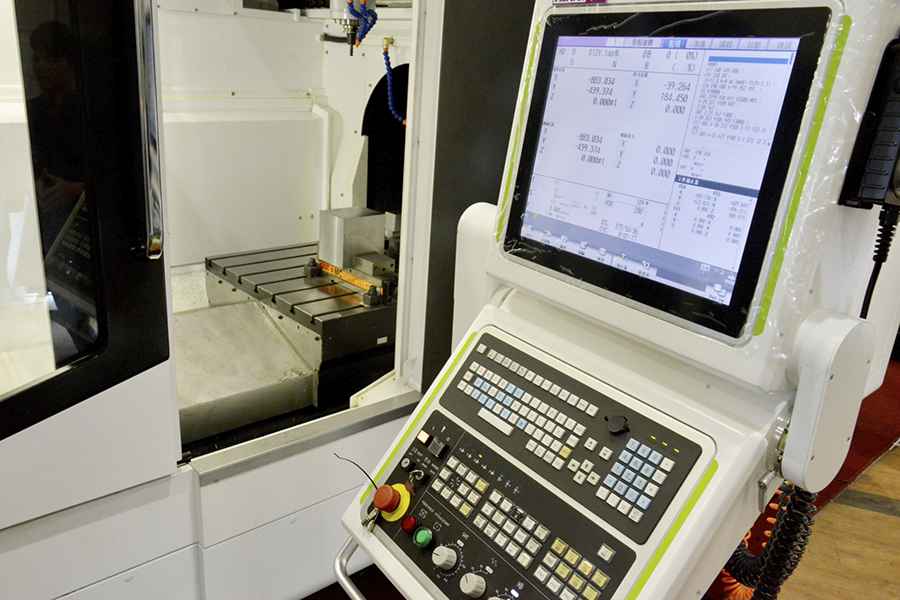
【成功事例に学ぶ】ロボットによる肉盛り溶接とオフラインティーチングで脱職人化
2020.04.09