記事公開日:2022.01.19
最終更新日:2023.01.20
デジタル化・DXを推進するポイント
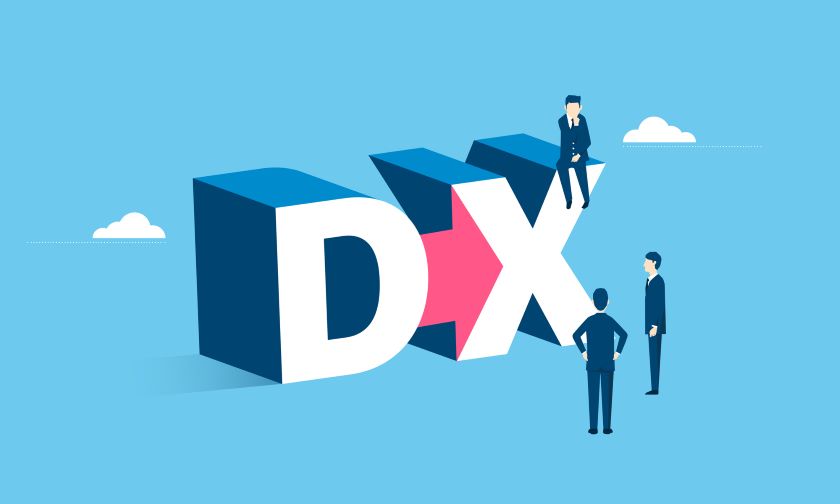
本コラムでは、ものづくり企業がデジタル化・DXを推進する際の越えなければならない壁の一つ、「導入した取り組みを現場に定着する」方法のポイントについて説明をさせていただきます。
本内容は、中小企業のみならず、どの企業規模の製造業事業者にでも適用できる内容になっています。
1はじめに
デジタル化・DXの目的は、「効率化、生産性改善」です。
紙を無くしてペーパーレス化すること、管理システムを導入することあくまで、“方法”でしかなく、“目的”ではありません。
これはデジタル化・DXを進めるマネージャー・リーダー各位がきちんと理解していなければいけないことです。
よくある事例として、最初は目的と方法をきちんと区別して理解しているのですが、目的達成のためにシステムを入れることが決まったタイミング以降、システムを入れることが目的となってしまうことです。
こうなると、現場はシステムを入れる意義が分からないまま、システムに対応することを要求された形となります。
そして、最終的にシステムを入れたけども、目的・意義が不明のままで、現場は使用することを要求されるので、言われたとおりに使うだけ、使い勝手が悪ければ使わなくなり、元の業務運用に戻ってしまい、投資活動が無駄になってしまうことになります。
マネージメント層が現場に期待することは、「導入した仕組・システムを活用して改善活動を自主的に行うこと」です。しかし、そうはなかなかなりません。なぜでしょうか?
以下の章で、原因について説明をします。
2.原因
現場がシステムを活用してくれない理由は、現場目線で考えると下記の3つに分けることが出来ます。
(1)システムを入れたけど、業務が改善されていない
(2)システムを入れたけど、業務量が増えただけ
(3)システムを入れたけど、恩恵を受けていない
上記の3点に共通していることは、デジタル化・DXの目的を現場が理解しておらず、現場目線でシステム導入が出来ていないことが原因ということです。一つずつ説明していきます。
まず、(1)システムを入れたけど業務が改善されていないについてです。
現場は、何かしらの改善(主に業務が楽になること)を期待していますが、実際は、記入する帳票が紙記入から、PC入力に変更になっただけの場合がこれにあたります。この場合は、システム設計・導入時に現場を巻き込めておらず、現場に適したシステム設計がされていないことが原因です。
続いて、(2)システムを入れたけど、業務量が増えただけについてです。
例としては、システム運用を開始したものの、不安があるから、しばらくは従来業務と併用し、そのまま、併用が当たり前になってしまった場合や、システムを使用すること自体がとても手間がかかり複雑な場合です。
この場合は、システム運用開始前に運用リスクを想定した操作テストを十分に評価しなかったこと、システムで把握したい項目、達成したいことが不明確であること、現場を巻き込めていないことが原因です。
最後に、(3)システムを入れたけど、恩恵を受けていないについてです。
前述した1.の現場業務改善も恩恵ですが、ここでの恩恵は、システムを活用することで会社全般の業務内容や取り組み活動の精度が向上し、業績・待遇が改善されることを指しています。例えば、現場が入力した製造工数(時間)と材料費から原価を算出し、各製品の利益率を出す。
そして、利益率が低いものは生産をやめ、利益率が高いものを多く製造販売するといった戦略に切り替えることで、現場は、段取り替えの回数が減り、より効率良く製造を行えるようになります。そうすると、残業時間が削減されるといった恩恵を受けることが出来ます。
3.対策
では、どうすれば前述した事態を防ぐことが出来るでしょうか。3つのポイントを下記します。
(1)デジタル化・DXの意義を繰り返し伝えて理解してもらうこと
(2)達成したい成果を明確に共有し、達成のために活動すること
(3)改善の成果をフィードバックすること
(1)は、言うのは簡単ですが、本当に理解しているのかを判定することが難しいです。
そのため、繰り返し伝えることで、刷り込んでいきましょう。そのためには、マネージャー・リーダー各位がデジタル化・DXのメリット・デメリットを理解して、具体例を用いながら現場と会話し、理解を深めてあげることが大切です。
(2)は、デジタル化・DXで何を達成しようとしているのかを明確にして、その成果を得るために改善が必要な業務を定め、成果を得られる仕組み・システムを構築する取り組みを行うということです。
システムは紙の帳票やエクセルと同じ手段の一つです。導入しただけでは、成果は得られません。
(3)は、システム導入後のポイントです。システムを使用することで、出てきた成果を現場と共有することで、取り組んだ成果を実感することが出来、意欲の向上につながります。
そしてその意欲が、次の改善活動の原動力になります。
目的を達成することからスコープをずらさず、成果が見える状態でプロジェクト運営をおこうことが出来れば、きっと導入したシステムは現場に定着し、改善を続けることができるでしょう。
4.対策
今回のコラムでは、デジタル化・DXを例として、実施した改善を現場に定着させ、更には現場が自主的に改善活動を行うようにするためのポイントについて説明させていただきました。本内容を自社の業務改善、成長発展のお役に立てていただきたいです。
また、上記内容の達成に支援が必要な場合は、弊社にお声がけいただければ幸いです。
最後までお読みいただきありがとうございました。
■オンラインセミナー開催のお知らせ
生産管理・基幹システム”革命セミナー”2022!
多品種小ロット生産板金・プレス加工業の為の生産管理・基幹システム”革命セミナー”2022!
属人化した生産・購買・在庫・原価のデータ化で「見える化」改革!
▼セミナーお申し込みはこちら▼
https://smart-factory.funaisoken.co.jp/event/
本セミナーで学べるポイント
- 従業員30名~200名以下の板金・プレス・溶接加工業の社長が知っておくべき生産管理・基幹システムが分かる!
- ~社長の為の生産管理・基幹システムで「見える化」する具体的な方法が分かります~
- 生産管理・基幹システムでデータ化したものを経営や現場が活用できるように分析する方法がわかる!
- ~経営や現場が活用できるようにBIを活用してデータ分析をする方法がわかります~
- 職人・属人化している生産管理・購買管理・原価管理業務を改善する為の生産管理・基幹システムを導入する方法が分かる!
- ~一部の熟練者・職人に依存している業務にシステムを導入・活用する方法が分かります~
- 基礎知識や導入経験がない社長でも生産・購買・在庫・原価のデータ化してデータ経営する方法がわかります。
- ~生産・購買・在庫・原価をシステムで統合的する方法が良く分からない…そんな社長の為のセミナーです~
- 自社のどの業務が改善されるのか具体的に分かる!
- ~理論・理屈ではなく、自社の現場で実践できるやり方が分かります~
お申し込みはこちらから⇒
このセミナーは終了しました。最新のセミナーはこちらから。
https://smart-factory.funaisoken.co.jp/event/
■オンラインセミナー開催のお知らせ
多品種少量生産機械加工業のAI&ロボット活用!社長セミナー
マシニングセンタ・NC旋盤・各種加工機等を保有している機械加工業を自動化・省力化・効率化!
▼セミナーお申し込みはこちら▼
https://smart-factory.funaisoken.co.jp/event/
本セミナーで学べるポイント
- マシニングセンタ・NC旋盤・各種加工機等を保有する機械加工業のAI&ロボットが分かる!
- ~少数精鋭主義の社長の為のAI&ロボット活用術が分かります~
- 従業員100名以下の多品種少量生産で出来るAI&ロボットが分かる!
- ~大量生産ではなく多品種少量生産に適したAI&ロボットの導入法が分かります~
- 熟練技術・職人的な業務にAI&ロボット導入する方法が分かる!
- ~一部の熟練者・職人に依存している業務にAI&ロボットを活用する方法が分かります~
- 基礎知識や導入経験がない社長でも多品種少量生産AI&ロボット導入法が分かる!
- ~多品種少量生産対応AI&ロボットは良く分からない…そんな社長の為のセミナーです~
- 自社でどんな工程・業務でAI&ロボットが活用できるかが具体的に分かる!
- ~理論・理屈ではなく、自社の現場で実践できるやり方が分かります~
お申し込みはこちらから⇒
このセミナーは終了しました。最新のセミナーはこちらから。
https://smart-factory.funaisoken.co.jp/event/
■工場AI・ロボット.comでは「無料オンライン診断サービス」を行っております
本コラム内容にご興味のある方はお気軽にお問い合わせください!
専門コンサルタントが無料でAI活用について診断致します!
無料お申し込みはこちら
https://lp.funaisoken.co.jp/mt/smart-factory/counsel.html
↓↓お申し込みはこちらから↓↓
https://lp.funaisoken.co.jp/mt/smart-factory/counsel.html