記事公開日:2024.11.21
最終更新日:2025.04.02
プラスチック射出成形の原価管理とコスト削減法:製造業の生産管理システム活用ガイド【基礎から実践まで】
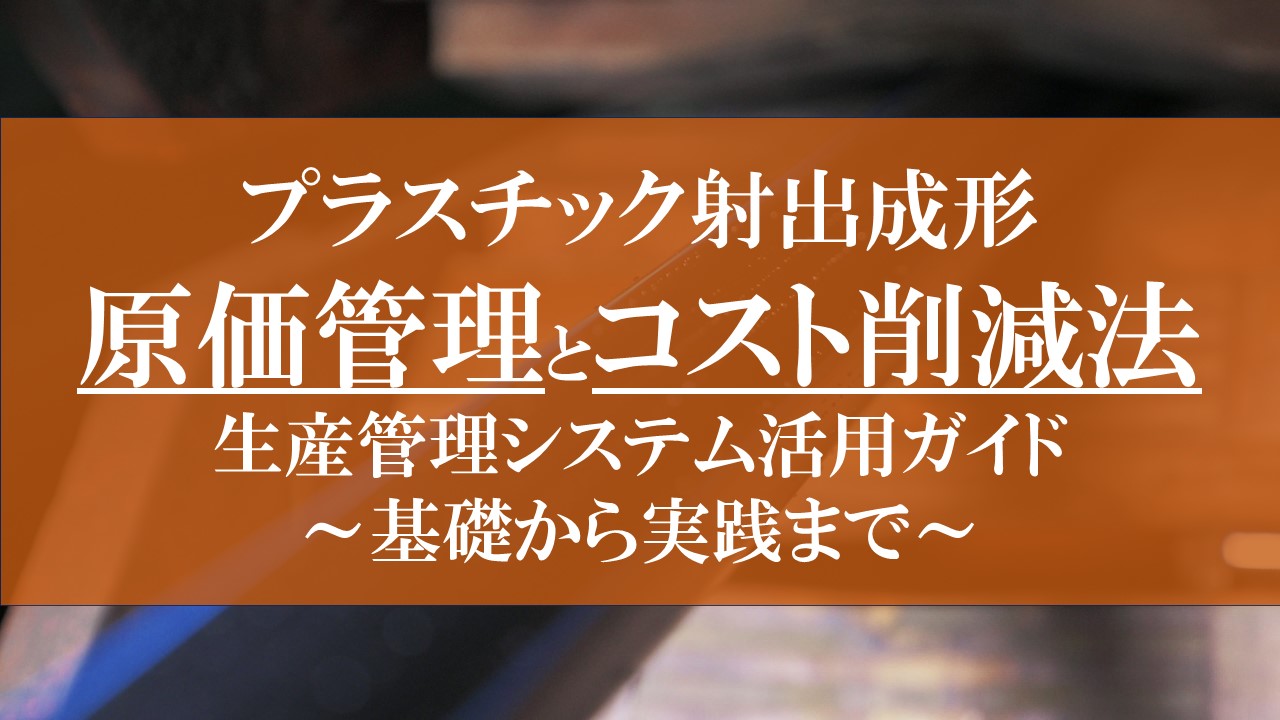
プラスチック射出成形は、製造業において広く使用されている生産技術であり、精密な製品を大量に生産することが可能です。しかし、その一方で、コスト管理の難しさが業界の課題として挙げられます。原材料費、加工費、設備費など、多くのコスト要因が絡み合い、適切な管理を怠ると、企業の利益を圧迫することになります。この記事では、プラスチック射出成形における原価管理の基本から、具体的なコスト削減方法、生産管理システムの活用方法、さらに実践的な事例を通じて、競争力を維持するための最適な原価管理手法を紹介します。
目次
1.はじめに:射出成形における原価管理の重要性とその背景
射出成形は、プラスチックや金属の加工において非常に重要な技術です。この技術を使用することで、複雑な形状や高精度な製品を短期間で生産することが可能になります。しかし、生産効率を最大化するためには、細かなコスト管理が必要不可欠です。
原材料費、加工費、設備維持費などが製造コストに影響を与えるため、それらのコストを的確に把握・管理を行い、データをもとにした原価改善を実施することが競争力維持に繋がります。
射出成形のプロセスは、多くの工程が絡むため、各工程で発生するコストを細かく分けて管理する必要があります。
例えば、原材料の仕入れから製品の完成までにかかる時間や人件費、そして生産設備の稼働率や保守管理費用が、全体的なコストにどのように影響するのかを理解することが重要です。
射出成形では、製品単価が低くなることが多いため、大量生産における効率化が求められます。そのため、製造原価を把握するためには、原価計算の手法を十分に理解し、適切な管理体制を築くことが必要です。
しかし近年の製品の多様化に伴って各社が製造する製品の品目数は多くなり、それぞれロット数も少なくなってきているのが現状です。
こういった多品種少量生産が求められる現在では、特に製品の製造に必要な準備時間(段取時間)をいかに効率的に最適化することができるかが原価低減における重要な視点となっていきます。
2.原価管理の目的:競争力向上と利益確保
射出成形は、プラスチックや金属の加工において非常に重要な技術です。この技術を使用することで、複雑な形状や高精度な製品を短期間で生産することが可能になります。しかし、生産効率を最大化するためには、細かなコスト管理が必要不可欠です。原材料費、加工費、設備維持費などが製造コストに影響を与えるため、それらのコストを的確に把握・管理を行い、データをもとにした原価改善を実施することが競争力維持に繋がります。
射出成形のプロセスは、多くの工程が絡むため、各工程で発生するコストを細かく分けて管理する必要があります。
例えば、原材料の仕入れから製品の完成までにかかる時間や人件費、そして生産設備の稼働率や保守管理費用が、全体的なコストにどのように影響するのかを理解することが重要です。
射出成形では、製品単価が低くなることが多いため、大量生産における効率化が求められます。そのため、製造原価を把握するためには、原価計算の手法を十分に理解し、適切な管理体制を築くことが必要です。
しかし近年の製品の多様化に伴って各社が製造する製品の品目数は多くなり、それぞれロット数も少なくなってきているのが現状です。
こういった多品種少量生産が求められる現在では、特に製品の製造に必要な準備時間(段取時間)をいかに効率的に最適化することができるかが原価低減における重要な視点となっていきます。
①実際工数のデータ化・一元化(データ取得)
こちらの画像をご覧ください。
こちらは弊社主催セミナーの資料の一部です。
画像に示されているように、多くの製造業では特に実際にかかった「労務費(工賃×工数)」と「光熱費」を正確に製品別工程別に取得することができていません。
実際にかかった労務費と光熱費が把握できないため、製造原価を把握することが出来ず、売価に対する利益を把握することが出来なくなってしまうのです。
実際原価を把握するためには、特に実際にかかった製造工数を現場でリアルタイムに取得していく必要があります。
光熱費においても、カーボンニュートラル等の観点から正確なデータ取得は必要ですが、光熱費を削減していく場合には新電力活用や設備投資等の投資による施策が挙げられることが多いため、現場改善・原価低減の観点で見る場合は、労務費をもとに按分するという進め方で取り急ぎは問題ないと考えられます。
皆さんの現場ではいかがでしょうか?
製造工数は正確に取れていますでしょうか?
また、そのデータを原価管理・現場改善へと活用することができていますか?
管理会計分野でも様々な分析・管理手法がありますが、それらもすべて「正確なデータが取得できていること」が前提です。
会社として、競争力を向上させるためには、特に正確な工数データを取得することが重要なのです。
②実際原価の可視化(集計)
製品別・工程別の実際にかかった原価を可視化することにより、どの製品・工程で無駄が発生しているかを特定できます。これにより、コスト削減の余地が明確になり、改善策を講じることができます。
多くの企業では、まだまだ標準原価計算によって原価管理されているのが実態です。
標準原価計算による製品別の原価を把握してしまうと、実際にかかった原価が見えなくなるため、生産計画・見積作成に影響を及ぼしてしまいます。
結果として、適切な経営判断を行うことが出来なくなってしまうのです。
データが集計されて可視化されてくれば、おのずと改善箇所が見えるようになっていきます。
製品別であれば、利益率のGood・Bad分析・製品分類別の利益率の推移・客先毎の利益率等が分析できるようになります。
工程別であれば、各ライン・設備における稼働時間の分析・製品別における製造ラインの特性等が統計的に分析できるようになります。
③利益の最大化(改善)
実際原価を可視化することによって得られる効果は、改善箇所が見えるようになることだけではなく、
改善後の結果が経営効果として数値化できるようになる
ことが挙げられます。
実際原価の可視化は実態を表すものであるため、改善の実施により過去と比較してどれだけ改善できたのかを数値で示すことができるようになるのです。
これにより、現場の方の改善活動に対するモチベーション向上につながることができ、会社として改善活動を活発化することができるようになります。
さらに、経営者・管理者としても、結果が数値で現れるようになるため根拠をもとに適切な評価ができるようになります。
現場の方からすると、やはり経営者・管理者からの適切な評価や適切な鼓舞はうれしいものであり、より改善活動を実施しようという考えを持ってくれるようになります。
そうすると、現場の方が率先して「データを見て気づきを得て」「改善ポイントを把握して」「自らが改善活動を実施する」ことができるようになるのです。
これにより、現場主導の経営改善・原価改善体制が出来上がります。
当たり前ですが、現場改善の気づきを得やすいのは現場の方々です。
日々作業をしているため、自部門の製造特性を熟知しているからです。
これを、「なんとなくやっている」「仕事だからやっている」といった意識で製造をする場合と、「この部分に改善ポイントがありそうだな」と考えながら製造をする場合では雲泥の差があることは明らかです。
こういった「原価意識を持った製造」意識を持たせるためにも、上記のような正確なデータ取得・可視化が重要となります。
生産性を向上させ、製造コストを抑えることができれば、同じ製品をより多くの利益を得ることができるようになります。利益率を改善するためには、原価計算と適切な価格設定が必要なのです。
現場主導の経営改善・原価改善体制を構築するためには、正確なデータ取得・可視化が重要なのです。
④競争力の向上(経営効果へと結びつける)
原価管理をすることは、社内の原価低減の為だけでなく、価格交渉や新規の見積による利益確保の材料ともなります。
価格交渉
自社の製品別工程別の原価を正しく把握することができれば、「どの製品が儲かっているか・儲かっていないか」「この製品のどの工程が儲かっているか・儲かっていないか」が詳細に分かるようになります。
さらに、近年の賃上げの状況を鑑みて、この工賃であればどの程度の利益を得ることができるのかが分かるようになります。
これにより、価格交渉しなければならない製品をピックアップすることができるようになります。
多くの企業では、材料費高騰に伴って、材料費の高騰分の価格交渉をすることはできていますが、賃上げに伴う価格交渉ができていないことが課題として挙げられます。
もちろん、客先との関係性などによりどうしても引き受けざるを得ない仕事もあるため、一筋縄で価格交渉をすることは難しいとは思いますが、データによる根拠が無い状態で行う価格交渉より、根拠のある価格交渉を行う方がより建設的な議論ができるようになることは間違いありません。
見積
新製品等の新規案件に対する見積作成の際には、過去の類似の案件・製品の見積情報を参考に作成することが少なからずあると思います。
原価管理が正しくできていなければ、その見積情報が実際に正しい見積であったのかどうかを判断できないため、仮に間違っていた場合は再び間違った見積を作成してしまうのです。
こういった際に、製品別工程別の原価を正しく把握することができていれば、過去の見積情報だけでなくその見積に対する実際原価を参考に作成することにより、新しい見積作成時には適切な価格で見積作成をすることができるようになるのです。
当たり前ですが、競争が激しい市場においてコスト管理を徹底することが、他社との差別化を図るための重要な要素となります。
⑤市場の変化に対応した柔軟な戦略(盤石な体制のもと、新たな経営判断へ)
原価管理を適切に行うことにより、急な市場の変化にも柔軟に対応で切るようになります。
近年の原材料費高騰や賃上げに伴う労務費の増加に対して迅速に対応するためには、リアルタイムでコスト情報を把握する必要があるのです。
また、データを蓄積しておくことにより、今後の予測を立てることも可能となります。
賃上げに伴い、最低賃金が上昇した場合、現在の加工時間では製品別でどれほど儲けを出すことができるのかが分かるようになります。
これは材料費も同様です。
シミュレーションを実施することにより、事前に対処をすることができるようになるのです。
3.直接費と間接費の分類と影響:材料費・加工費の詳細解説
原価管理の中で最も重要なのは、直接費(材料費や加工費)と間接費(管理費や設備費)を明確に区別し、それぞれに対する管理を行うことです。
直接費(材料費・加工費)
射出成形の原価において、直接費は非常に重要です。材料費は、使用するプラスチックの種類や量に依存し、製品の品質やコストに直結します。加工費は、成形機の稼働時間や人件費、エネルギーコストなどが含まれます。これらを適切に管理するためには、リアルタイムでコストを把握できるシステムが必要です。
特に多品種少量生産を実施している企業では、製造時間を段取時間と加工時間に区分けして管理することが重要です。
IoT等を活用して設備の稼働率を取得している企業もありますが、多品種少量生産では稼働率だけを現場の指標とするのは難しいため、段取時間の適正化を重要視する必要があるのです。
間接費(設備費・管理費)
設備費や管理費は、直接製品に関連しない費用ですが、企業の収益に大きな影響を与える要素です。例えば、成形機の維持管理費用や、工場の光熱費、スタッフの給与などがこれに該当します。これらの費用も管理し、効率化を図ることが利益向上に繋がります。
間接費においては、原価に占める割合が比較的少ないことが多いため、実際原価管理をしていくための優先順位は低くてもよいと考えられます。
しかし、間接費のうち特に光熱費においては、近年のカーボンニュートラルのトレンドを考慮して将来的には管理していく必要があります。
4.生産管理システムと原価管理の連携:費用効率の最適化
生産管理システムを導入することにより、原価管理と生産効率を最適化できます。ここでは、現代の生産管理システムを利用してどのようにコスト管理を行い、効率を向上させるかについて説明します。
①ERPシステム・生産管理システムの活用
ERP(統合基幹業務システム)を導入することで、財務、在庫管理、生産計画などの情報を一元化できます。これにより、製造工程における各コストをリアルタイムで監視し、必要な改善策を迅速に講じることが可能です。
ERP・生産管理システムに関しては、多くの企業で導入済であることが多いと考えています。
しかし、
- 実績入力が開始時間・終了時間で正確に入力ができていない。
- 工数をもとに実際原価計算ができるような機能になっていない。
といったシステム機能面での課題によって、実際原価管理を実現できていない企業も多いのではないでしょうか?
こういった課題に関しては、次項で説明するように実際工数取得に特化した別のツールとの連携を視野に入れながら検討するのが良いと考えられます。
②MES(製造実行システム)による生産管理の向上
MESを使用することで、製造工程の詳細なデータを収集し、コストを最適化することができます。生産ラインの稼働状況や材料の使用状況を可視化し、無駄を削減するためのデータを提供します。
いわゆるMESシステムを導入しようとすると、設備との連携等を考慮しなければならず、大がかりな投資になってしまいがちですが、自社にとって必要なMES機能は何か?を整理することによって、投資を必要最低限にまで最適化することができるようになります。
多くの企業にとって必要なMES機能は、あくまで製造実績データを取得する部分であることが多いのではないかと考えられます。
③データに基づく意思決定
正確なデータが取得できれば、集計された結果が正確なものになります。
そのため、現場で実践するコスト削減のアクションをリアルタイムで実行することができます。データドリブンで意思決定を行うことで、正確な予測と計画を立てることが可能となり、コストの無駄を減らすことができます。
さらに、コスト削減のアクションを実行した結果がリアルタイムに現れるようになるため、コスト削減実行者・管理者・経営者としても経営効果を共通認識化することができるようになるのです。
5.工数管理・不良品削減を通じた現場改善
射出成形における現場改善は、工数管理と不良品削減に大きく依存します。生産性を高め、品質を保ちながらコストを削減する方法を見ていきましょう。
①工数管理
製品別工程別で実際にかかった工数と標準工数の差を一目でわかるように集計することで、今回の製造時間が適切であるかどうかを判断することができるようになります。
またある企業では、日ごとの担当者別の標準工数との差を集計することにより、各担当者がその日どれだけ効率的に製造をすることができたかを現場にフィードバックする仕組みを構築し、現場に標準工数の意識を持たせる働きかけをしています。
現場で標準工数の意識を持つことにより、都度の製造において適切な工数で製造ができるようになり、結果として原価低減につながるのです。
②不良品削減
現場の評価軸として、工数管理だけでは品質がおろそかになってしまいがちです。
そのため、現場では「工数×品質」で評価軸を設けることが重要です。
前述した企業では、工数の他に不良品・手直し品の集計を実施することによって各現場で対策を議論するための場を設けています。
「なんとなくこの工程で不良が出やすい」「この製品は製造が難しい」といったベテランの主観による議論をするのでは無く、数値をもとに傾向をつかんで議論をすることにより、より建設的な議論ができるようになるのです。
品質管理を徹底し、不良品を減らすことで再加工や廃棄処分費用を削減できます。継続的な品質改善活動が、全体のコスト削減に繋がります。
6.分析ツールの活用とその効果:データに基づく意思決定
コスト管理におけるデータ分析は、現代の製造業において不可欠です。分析ツールを駆使して、データに基づく意思決定を行う方法について説明します。
①データ分析ツール
データ分析ツールを使用することで、製造工程のパフォーマンスをリアルタイムで監視し、問題点を特定できます。これにより、改善のための迅速なアクションを取ることができます。
多くの企業では、まだまだExcelによるデータ集計を実施されていることが多いのではないでしょうか?
画像にもある通り、現場改善のPDCAを回すにあたって多くの企業では、「現場のデータ化」「可視化・分析」に工数をかけすぎてしまっていると考えられます。
そのため、改善施策検討の議論に十分な工数を割くことが出来ず、結果として現場改善が進まないという状況が発生しているのではないでしょうか?
データの可視化・分析には、Excel等による集計ではなく、BIツールを使った自動集計を実施することが重要であると考えられます。
BIツールについては、こちらの記事をご確認ください。
製造業・工場が実践すべきBIツール活用とは?成功事例も紹介
②ROI(投資対効果)の分析
BIツールの活用によってリアルタイムにデータ集計ができるようになると、投資した・または投資する予定の設備やシステムがどれほどのコスト削減効果をもたらしているのかを分析することも可能です。ROI分析により、投資判断を適切に行うことができます。
「データに基づく意思決定」の項でも述べましたが、データ集計によって改善箇所が見えるようになると、その改善効果金額をシミュレーションできるようになります。
そうすることで、必要な投資金額が見えるようになり、できるだけ失敗する確率を下げた投資ができるようになるのです。
7.現場改善の成功事例
ここでは、実際の現場改善事例を取り上げ、どのようにコスト削減を実現したのかを見ていきます。また、改善活動での失敗例とその教訓も紹介します。
①成功事例
ペーパレス化により、10人分の工数を削減した事例
【社長特別インタビュー】製造業向け現場主導“完全ペーパレス化”で10人分の工数削減!
実際製造実績を取得し、実際原価管理を実現させた事例
【製造業向け】原価管理システムと補助金成功事例レポート
BI活用によるリアルタイムデータ集計成功事例
【製造業向け】BI活用によるデータ集計自動化事例
8.まとめ
プラスチック射出成形における原価管理は、製造業の競争力を維持し、利益を最大化するために非常に重要です。最新の技術やシステムを活用することで、より精度の高い原価計算と効率的な生産管理が可能になります。企業の規模やニーズに合ったシステムを導入し、日々の生産活動においてコスト削減に向けた取り組みを継続的に実施することが、長期的な成功に繋がります。
今回のコラムの内容は、セミナーの内容のほんの一部の抜粋となります。
より詳細な内容については、下記セミナーでお話ししておりますので是非ご参加ください。
▼セミナー詳細・申込はこちらから▼
https://www.funaisoken.co.jp/seminar/105866
お申し込みはこちらから⇒
https://www.funaisoken.co.jp/seminar/120968
https://www.funaisoken.co.jp/dl-contents/smart-factory_smart-factory_01906_S045