記事公開日:2025.02.04
最終更新日:2025.04.02
【工場のヒヤリハット事例を解説】原因と対策方法を紹介! 報告を活かして事故防止
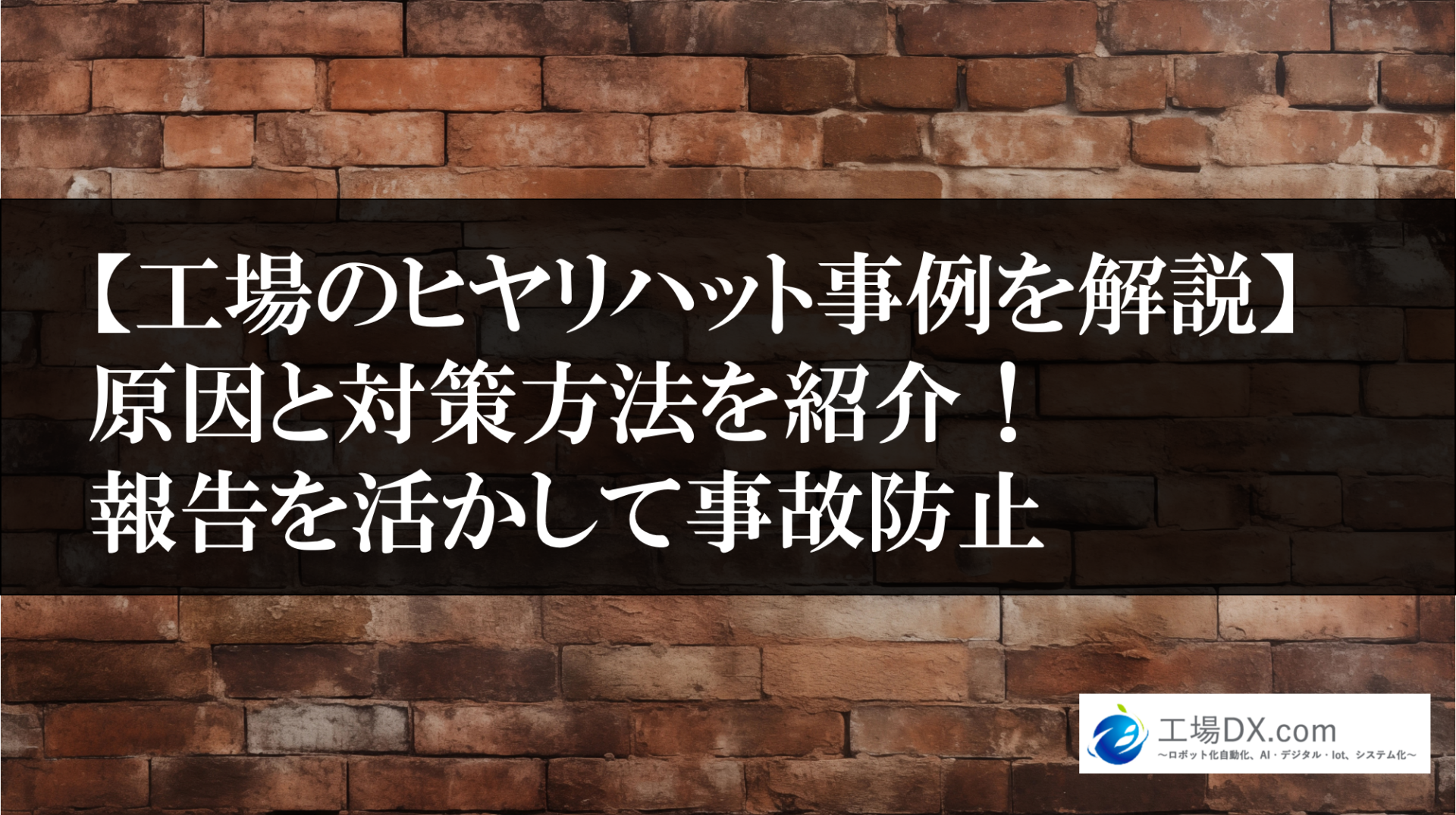
工場で起きるヒヤリハット、重大な事故につながる前に対策を講じましょう!
本記事では、工場でよくあるヒヤリハット事例を解説し、その原因と対策方法を紹介します。ヒヤリハット事例を参考に、作業現場の安全を見直し、報告書作成を通して事故防止に役立てましょう。
目次
1. 工場におけるヒヤリハットとは?
工場で働く方にとって、安全は最も重要な要素の一つです。しかし、どんなに注意していても、予期せぬ出来事が起こり、ヒヤリハットする経験をすることがあるかもしれません。
1.1. ヒヤリハットの定義と重要性
ヒヤリハットとは、「事故には至らなかったものの、ヒヤリとしたり、ハッとしたりするような危険な出来事」を指します。
例えば、作業中に工具を落としそうになったり、通路で人とぶつかりそうになったり、機械に手が触れそうになったりすることが挙げられます。
これらのヒヤリハットは、軽微な出来事のように思えるかもしれません。しかし、ヒヤリハットを放置すると、重大な事故につながる可能性があります。
なぜなら、ヒヤリハットは、作業環境や作業方法に潜む危険性を示すサインだからです。
ヒヤリハットを分析し、適切な対策を講じることで、事故を未然に防ぐことができます。
1.2. 労働災害とヒヤリハットの関係
厚生労働省の「職場のあんぜんサイト」によると、労働災害は、労働者が業務中に負傷、疾病、障害、死亡する事故を指します。
労働災害には、転倒、墜落、転落、挟まれ、巻き込まれ、切れ・こすれ、衝突など、さまざまな種類があります。
これらの労働災害の多くは、ヒヤリハットを放置した結果、発生していると考えられています。
ヒヤリハットは、労働災害の芽と言えるでしょう。
1.3. ヒヤリハット事例を報告する目的
ヒヤリハット事例を報告することは、工場の安全管理において非常に重要です。
報告することで、以下の目的を達成することができます。
- 事故の発生原因を分析し、再発防止策を検討する。
- 危険個所を特定し、改善を行う。
- 作業者全体の安全意識を高める。
- 安全な職場環境を構築する。
ヒヤリハット事例を共有することで、組織全体で安全に対する意識を高め、事故を未然に防ぐことができます。
1.4. ハインリッヒの法則
アメリカの安全技師、ハーバート・ウィリアム・ハインリッヒが提唱した「ハインリッヒの法則」は、労働災害における経験則の一つです。
この法則によると、1件の重大な事故の裏には、29件の軽微な事故があり、さらにその背後には300件のヒヤリハットが存在すると言われています。
つまり、重大な事故を防ぐためには、ヒヤリハットの段階で適切な対策を講じる必要があるということです。
2. 工場でよくあるヒヤリハット事例9選
工場では、さまざまな作業が行われており、それに伴い、ヒヤリハットも多岐にわたります。
ここでは、工場でよくあるヒヤリハット事例を、製造業における事例と職種別の事例に分けて紹介します。
2.1. 製造業におけるヒヤリハット事例
製造業では、機械の操作や材料の運搬など、危険を伴う作業が多く存在します。
ここでは、製造業でよくあるヒヤリハット事例を、作業中、設備、化学物質の3つの観点から紹介します。
2.1.1. 作業中の事例
- 事例1
機械の操作中に、誤ってボタンを押してしまい、機械が予期せぬ動作をした。幸い、作業者は怪我をしなかったが、重大な事故につながる可能性があった。 - 事例2
重量物を運搬中に、バランスを崩して転倒しそうになった。近くに人がいなかったため、衝突は避けられたが、転倒による怪我や、重量物の落下による事故が起こる可能性があった。 - 事例3
高所作業中に、足場が不安定で、転落しそうになった。安全帯を着用していたため、大事には至らなかったが、墜落による重傷を負う可能性があった。
2.1.2. 設備に関する事例
- 事例4
機械の点検中に、誤って電源が入り、機械が作動してしまった。作業者は機械から離れていたため、巻き込まれることはなかったが、接触していた場合は重大な怪我をする可能性があった。 - 事例5
設備の老朽化により、部品が落下した。落下地点に人がいなかったため、怪我人は出なかったが、直撃していた場合は、重傷を負う可能性があった。 - 事例6
フォークリフトの運転中に、視界が悪く、壁に衝突しそうになった。速度が遅かったため、衝突は避けられたが、高速で衝突していた場合は、フォークリフトの転倒や、壁の破損による二次災害が起こる可能性があった。
2.1.3. 化学物質に関する事例
- 事例7
化学物質の取り扱い中に、誤って容器を倒してしまい、液体がこぼれた。保護具を着用していたため、作業者は無事だったが、皮膚に付着していた場合は、炎症や中毒を起こす可能性があった。 - 事例8
化学物質の保管場所が適切でなく、容器が破損して内容物が漏洩した。換気が十分だったため、作業者への健康被害はなかったが、密閉された空間であれば、中毒や窒息を起こす可能性があった。 - 事例9
可燃性の化学物質を扱っている際に、静電気による火災が発生しそうになった。すぐに消火活動を行ったため、火災は発生しなかったが、初期消火に失敗していた場合は、大規模な火災に発展する可能性があった。
2.2. 職種別ヒヤリハット事例
職種によって、作業内容や作業環境が異なるため、ヒヤリハットの種類も異なります。
ここでは、電気工事士と倉庫作業員のヒヤリハット事例を紹介します。
2.2.1. 電気工事士のヒヤリハット事例
- 事例10
電気配線工事中に、誤って活線に触れてしまい、感電しそうになった。絶縁手袋を着用していたため、感電は免れたが、着用していなかった場合は、重度の感電事故を起こす可能性があった。 - 事例11
高所での作業中に、工具を落としてしまった。下に人がいなかったため、怪我人は出なかったが、人に当たっていた場合は、重大な怪我を負わせる可能性があった。 - 事例12
電気設備の点検中に、回路の誤認識により、予期せぬ電流が流れてしまった。保護装置が作動したため、事故には至らなかったが、保護装置が正常に作動しなかった場合は、感電や火災が起こる可能性があった。
2.2.2. 倉庫作業員のヒヤリハット事例
- 事例13
フォークリフトで荷物を運搬中に、積荷が崩れて落下しそうになった。すぐに停止し、積荷を固定し直したため、落下は防げたが、落下していた場合は、荷物の破損や、周囲の人への危害が生じる可能性があった。 - 事例14
高い棚から荷物を取ろうとして、バランスを崩して転倒しそうになった。近くに人がいなかったため、衝突は避けられたが、転倒による怪我や、落下物による事故が起こる可能性があった。 - 事例15
倉庫内での作業中、整理整頓が不十分で、通路に物が置かれていたため、つまずいて転倒しそうになった。幸い、怪我はなかったが、転倒による骨折などの怪我をする可能性があった。
3. ヒヤリハットの原因分析と対策方法
ヒヤリハットは、さまざまな原因で発生します。
ここでは、ヒヤリハットが起こる原因を分析し、工場における効果的な対策方法を紹介します。
3.1. ヒヤリハットが起こる原因5つ
ヒヤリハットが起こる原因は、大きく分けて以下の5つに分類できます。
- 人的要因: 作業者の不注意、知識不足、経験不足、体調不良、疲労など
- 設備的要因: 機械の老朽化、故障、不具合、安全装置の不備など
- 環境的要因: 照明不足、騒音、温度、湿度、整理整頓不良など
- 管理的要因: 安全教育の不足、作業標準の不備、リスクアセスメントの不足など
- その他の要因: 自然災害、予期せぬ出来事など
これらの要因が複合的に作用して、ヒヤリハットが発生することがあります。
3.2. 工場におけるヒヤリハット対策方法
ヒヤリハットを減らし、安全な職場環境を作るためには、原因に応じた対策を講じる必要があります。
ここでは、工場で実施できる具体的なヒヤリハット対策方法を紹介します。
3.2.1. 現場改善
- 5S活動の徹底: 整理、整頓、清掃、清潔、しつけの5S活動を徹底することで、作業環境を改善し、ヒヤリハットを減らすことができます。
- 通路の確保: 通路に物を置かないようにし、常に安全な通行を確保しましょう。
- 床面の滑り対策: 床材の選択や、滑り止めマットの設置などを行い、転倒事故を防止しましょう。
- 照明の改善: 明るい照明を設置することで、視界を確保し、作業ミスや転倒事故を防ぎましょう。
- 危険箇所の表示: 危険な場所には、注意喚起の標識や表示を設置することで、作業者の注意を促しましょう。
3.2.2. 安全教育の実施
- 新入社員教育: 新入社員に対しては、安全に関する基礎知識や作業手順などを丁寧に教育しましょう。
- 定期的な安全教育: 定期的に安全教育を実施することで、作業者の安全意識を維持・向上させましょう。
- KYT(危険予知トレーニング): KYTは、作業前に危険を予測し、対策を立てるトレーニングです。KYTを導入することで、作業者の危険予知能力を高め、ヒヤリハットを減らすことができます。
- OJT(On-the-Job Training): 経験豊富な作業者が、新入社員や若手作業者に、実務を通して安全作業を指導することで、技能と安全意識を向上させることができます。
- eラーニング: eラーニングを活用することで、時間や場所を選ばずに、効率的に安全教育を実施することができます。
3.2.3. リスクアセスメント
- リスクアセスメントの実施: 作業工程における危険要因を特定し、リスクのレベルを評価することで、適切な対策を講じることができます。
- リスクアセスメント結果の見直し: 作業内容の変更や、新たな設備の導入時には、リスクアセスメントを見直し、必要があれば対策を更新しましょう。
- リスクアセスメント結果の共有: リスクアセスメントの結果を作業者に共有することで、危険性に対する認識を共有し、安全意識の向上を図りましょう。
- リスクアセスメントツールの活用: リスクアセスメントツールを活用することで、効率的にリスクアセスメントを実施することができます。厚生労働省のサイトでは、無料のツールが公開されています。
3.2.4. 安全活動の推進
- 安全委員会の設置: 労働安全衛生法に基づき、事業場ごとに安全委員会を設置し、安全衛生に関する活動を推進しましょう。
- 安全パトロールの実施: 定期的に安全パトロールを実施し、作業環境の安全点検や、作業者の安全行動の確認を行いましょう。
- 安全標語の作成: 作業者の安全意識を高めるために、安全標語を作成し、職場に掲示しましょう。
- 安全大会の開催: 安全大会を開催し、安全に関する講演会や、ヒヤリハット事例の発表などを行い、作業者の安全意識向上を図りましょう。
- 改善提案制度の導入: 作業者からの改善提案を積極的に受け入れることで、現場の意見を反映し、より安全な職場環境を作ることができます。
3.2.5. ヒヤリハット報告書の活用
- ヒヤリハット報告書の提出: ヒヤリハットが発生した場合は、必ず報告書を提出させ、情報を収集しましょう。
- ヒヤリハット事例の分析: 収集したヒヤリハット事例を分析し、原因を究明することで、効果的な対策を立てることができます。
- ヒヤリハット事例の共有: 分析結果を作業者にフィードバックすることで、同様のヒヤリハットの再発防止につなげましょう。
- ヒヤリハットデータベースの構築: 過去のヒヤリハット事例をデータベース化することで、傾向を分析したり、対策を検討したりする際に役立ちます。
- ヒヤリハット報告書作成ツールの活用: ヒヤリハット報告書作成ツールを活用することで、報告書の作成を効率化することができます。
4. ヒヤリハット報告書の書き方
ヒヤリハット報告書は、単なる記録ではなく、事故を未然に防ぐための重要なツールです。
ここでは、ヒヤリハット報告書の書き方について、詳しく解説します。
4.1. ヒヤリハット報告書を作成する目的
ヒヤリハット報告書を作成する目的は、以下の3点です。
- 事実の記録: ヒヤリハットの内容を正確に記録し、後から振り返ることができるようにする。
- 原因の分析: ヒヤリハットが発生した原因を分析し、再発防止につなげる。
- 対策の検討: ヒヤリハットを防止するための対策を検討し、実行する。
4.2. 報告書に記載すべき内容
ヒヤリハット報告書には、以下の項目を記載する必要があります。
- 発生日時
- 発生場所
- ヒヤリハットの内容
- 作業内容
- 関係者
- 状況(発生状況、作業環境、設備の状態など)
- 原因
- 対策
これらの項目を具体的に記述することで、より詳細な分析が可能となり、効果的な対策を立てることができます。
4.3. 報告書の例文
以下は、ヒヤリハット報告書の例文です。
―――――――――――――――――――――――――――――――――――――――――――――――――
ヒヤリハット報告書
- 発生日時: 2024年1月23日 10時30分
- 発生場所: 工場A棟 組立ライン
- ヒヤリハットの内容: 作業中に工具を落としそうになった。
- 作業内容: 製品Aの組立作業
- 関係者: 作業員Aさん
- 状況: 高い位置にある部品を取り付ける際に、バランスを崩して工具を落としそうになった。
- 原因: 足場が不安定だった。
- 対策: 安定した足場を設置する。
―――――――――――――――――――――――――――――――――――――――――――――――――
4.4. 厚生労働省のヒヤリハット報告書
厚生労働省の「職場のあんぜんサイト」では、ヒヤリハット報告書のフォーマット(様式)が公開されています。
このフォーマットは、無料でダウンロードして使用することができます。
フォーマットには、上記の項目に加えて、以下の項目も含まれています。
- ヒヤリハットの種類(転倒、落下、衝突など)
- 危険の程度(軽微、重大など)
- 再発防止策
- 担当者
これらの項目を記入することで、より詳細な情報共有が可能となり、効果的な安全対策を講じることができます。
5. ヒヤリハット対策に役立つツールとサイト
ヒヤリハット対策には、さまざまなツールやサイトが役立ちます。
ここでは、ヒヤリハット報告書作成ツール、厚生労働省「職場のあんぜんサイト」、ヒヤリハット事例紹介サイトを紹介します。
5.1. ヒヤリハット報告書作成ツール
ヒヤリハット報告書作成ツールは、報告書の作成を効率化するためのツールです。
多くのツールは、入力フォームに必要事項を入力するだけで、簡単に報告書を作成することができます。
また、写真や動画を添付できるツールもあり、より詳細な情報共有が可能です。
5.2. 厚生労働省「職場のあんぜんサイト」
厚生労働省が運営する「職場のあんぜんサイト」は、労働安全衛生に関する情報提供サイトです。
サイト内では、ヒヤリハット事例集、リスクアセスメントツール、安全教育資料など、さまざまな情報が公開されています。
これらの情報は、無料でダウンロードして活用することができます。
5.3. ヒヤリハット事例紹介サイト
インターネット上には、さまざまな企業や団体が、ヒヤリハット事例を紹介するサイトを公開しています。
これらのサイトでは、業種別、作業内容別、原因別にヒヤリハット事例を検索することができます。
他の企業の事例を参考に、自社のヒヤリハット対策に役立てましょう。
6. ヒヤリハットを減らすためのポイント
ヒヤリハットを減らすためには、以下の3つのポイントを意識することが重要です。
6.1. 危険予知トレーニングの実施
危険予知トレーニング(KYT)は、作業前に危険を予測し、対策を立てるトレーニングです。
KYTを導入することで、作業者の危険予知能力を高め、ヒヤリハットを減らすことができます。
KYTには、以下の4つの段階があります。
- 状況の把握: 作業内容、作業環境、設備の状態などを把握する。
- 危険の予測: 作業中、作業環境、設備の状態から危険を予測する。
- 対策の検討: 危険を回避するための対策を検討する。
- 目標の設定: 対策を実行するための具体的な目標を設定する。
KYTは、グループで行うことで、さまざまな視点から危険を予測し、より効果的な対策を検討することができます。
6.2. 安全意識の向上
安全意識の向上は、ヒヤリハットを減らすための重要な要素です。
安全意識を高めるためには、以下の取り組みが有効です。
- 安全教育の充実: 定期的な安全教育やKYTなどを実施し、作業者の安全知識や危険予知能力を高める。
- 安全情報の共有: ヒヤリハット事例や事故情報を共有し、作業者全体の安全意識を高める。
- 安全目標の設定: 部署や個人ごとに安全目標を設定し、達成度を評価することで、安全意識向上を促進する。
- 安全キャンペーンの実施: 安全週間や安全大会などを開催し、安全に対する意識を高める。
- コミュニケーションの活性化: 作業者同士が積極的にコミュニケーションを取り、安全に関する情報交換や意見交換を行うことで、相互に安全意識を高め合うことができる。
6.3. 職場環境の整備
安全な職場環境を整備することも、ヒヤリハットを減らすために重要です。
職場環境の整備には、以下の取り組みが有効です。
- 5S活動の徹底: 整理、整頓、清掃、清潔、しつけの5S活動を徹底することで、作業スペースを確保し、転倒や落下などの事故を防止する。
- 設備の点検・整備: 設備の定期的な点検・整備を行い、故障や不具合を早期に発見し、事故を未然に防ぐ。
- 安全装置の設置: 機械には、安全カバーや非常停止ボタンなどの安全装置を設置し、事故発生時の被害を最小限に抑える。
- 通路の確保: 通路に物を置かないようにし、常に安全な通行を確保する。
- 照明の改善: 明るい照明を設置することで、視界を確保し、作業ミスや転倒事故を防ぐ。
7. DXで進化する工場のヒヤリハット対策
DXの進化により、工場のヒヤリハット対策は新たなステージへと進んでいます。
これまで、ヒヤリハットの記録や分析は、主に人手に頼るところが大きく、どうしても属人的な要素や時間的制約がありました。しかし、デジタル技術を活用することで、これらの課題を克服し、より効率的かつ効果的なヒヤリハット対策が可能になります。
例えば、ヒヤリハット報告をデジタル化し、クラウド上でデータを一元管理することで、以下のメリットが生まれます。
- データの蓄積と分析: 過去のヒヤリハット事例をビッグデータとして蓄積し、AIなどを活用して分析することで、事故発生のパターンや傾向を把握することができます。
- リスク予測: 過去の類似事例を参考に、AIが現在の状況を分析し、潜在的なリスクを予測することで、事故を未然に防ぐことができます。
- 最適な対策の提案: AIが過去の事例から最適な対策を提案することで、迅速かつ的確な対応が可能になります。
- リアルタイムな情報共有: 現場で発生したヒヤリハットをリアルタイムに共有することで、関係者全員が状況を把握し、迅速な対応を取ることができます。
さらに、蓄積されたデータは、安全教育にも活用することができます。
- VR/ARを活用したシミュレーション: 過去のヒヤリハット事例を基に、VR/AR技術を用いたリアルなシミュレーションを行うことで、作業者は危険を疑似体験し、安全意識を高めることができます。
- パーソナライズされた安全教育: 作業者の経験やスキルレベルに応じて、最適な安全教育コンテンツを提供することで、より効果的な学習を促進することができます。
このように、DXを活用することで、ヒヤリハット対策をより高度化し、安全な職場環境を実現することができます。
【具体例】
ある製造業の企業では、ヒヤリハット報告システムを導入し、AIによる分析を開始しました。
その結果、これまで見過ごされていた軽微なヒヤリハットが、実は重大な事故につながる可能性があることが判明しました。
AIの分析結果を基に、作業手順の見直しや安全教育を実施した結果、ヒヤリハットの発生件数を大幅に削減することに成功しました。
8. ヒヤリハット防止で労働災害ゼロを目指そう!
この記事では、工場におけるヒヤリハットの定義、事例、原因、対策方法、報告書の書き方などを解説しました。
ヒヤリハットは、重大な事故につながる可能性があるため、決して軽視してはいけません。
ヒヤリハットを一つひとつ分析し、適切な対策を講じることで、労働災害ゼロを目指しましょう。
9. 多品種少量生産を行う中小製造業の皆様へ
多品種少量生産では、作業内容が多岐にわたり、作業環境も変化しやすいため、ヒヤリハットのリスクが高まる可能性があります。
ぜひこの記事を参考に、ヒヤリハット対策を強化し、安全な職場環境を構築してください。
当コンサルティング会社では、多品種少量生産における安全管理に関するコンサルティングサービスも提供しています。
ヒヤリハット対策にお困りの際は、お気軽にお問い合わせください。
10. 参考文献
- 厚生労働省 職場のあんぜんサイト
https://anzeninfo.mhlw.go.jp/ - 中央労働災害防止協会
https://www.jisha.or.jp/ - 労働安全衛生法
https://www.mhlw.go.jp/stf/seisakunitsuite/bunya/koyou_roudou/roudoukijun/anzen/index.html
※注記
本記事は、2025年1月31日現在の情報に基づいて作成されています。
法令や統計データなどは、最新の情報をご確認ください。
本記事の内容は、一般的な情報提供を目的としたものであり、法的助言などを構成するものではありません。
11. 関連記事
- 【工場の改善事例100選】小さなアイデア&ネタで収益UP! 製造業の改善提案例を紹介
https://smart-factory.funaisoken.co.jp/250123-2/ - IoT導入による工場の見える化とは?成功事例と現場改革におけるメリット・注意点を紹介
https://smart-factory.funaisoken.co.jp/250108-2/ - 製造業の生産現場で活用するKPI設定:成功事例と必要なデータ活用法を解説
https://smart-factory.funaisoken.co.jp/241226-2/ - 【2025年時流予測】製造業のトレンドから見る未来展望・原価管理データ活用戦略
https://smart-factory.funaisoken.co.jp/241223-2/ - 【2025年年末年始に読みたい!】最新事例レポート一覧!
https://smart-factory.funaisoken.co.jp/241225-2/ - 製造業の人手不足の原因と効果的な対策法:人材不足解消のための実践的解説
https://smart-factory.funaisoken.co.jp/241219-3/
12. まとめ
この記事では、工場におけるヒヤリハット事例を原因別に詳しく解説し、具体的な対策方法を紹介しました。
読者の皆様が、この記事を参考にヒヤリハット対策に取り組み、安全な職場環境を実現できることを願っています。
最後に、もう一度、ヒヤリハット防止の重要性を強調しておきます。
ヒヤリハットは、重大な事故の芽です。
ヒヤリハットを軽視せず、積極的に報告し、対策を講じることで、労働災害を未然に防ぐことができます。
安全な職場環境は、従業員の健康と安全を守り、企業の生産性向上にもつながります。
自社のヒヤリハット事例をデータ化し、蓄積することにより、会社のノウハウとして蓄積・活用することが出来るようになります。
ぜひ、今日からヒヤリハット対策に取り組みましょう!
今回では、工場のヒヤリハット事例をもとに、DXとの関連性について説明をしてまいりました。
弊社が主催している下記セミナーでは、自社の生き残りをかけたDXの取組を、実際の事例をもとにお話ししています。
改めて、下記のような課題を抱えられている方はぜひご参加ください。
- 多品種少量生産の紡績・繊維業の社長
- 昨今の紡績業界の市場動向を鑑みて、自社はどのように生き残る戦略を立てるべきかを知りたい社長
- 紙日報による手書き運用が続いており、その後のデータ活用ができていない。
- 標準原価で収益管理しているが、材料費高騰・賃上げに対応できていない。
- Excel運用が多く、社内での情報共有がリアルタイムにできない。
- 原価管理をどのように利益UPに結びつけるか具体的な方法を知りたい。
- 経営指標はもちろんだが、現場指標を設けて従業員に経営意識を持たせたい。
https://www.funaisoken.co.jp/seminar/123657
https://www.funaisoken.co.jp/dl-contents/smart-factory_smart-factory_03729_S045