記事公開日:2025.03.04
最終更新日:2025.04.02
【製造業必見】構内物流改善!課題を解決する5つのステップ|自動化事例と導入のポイント
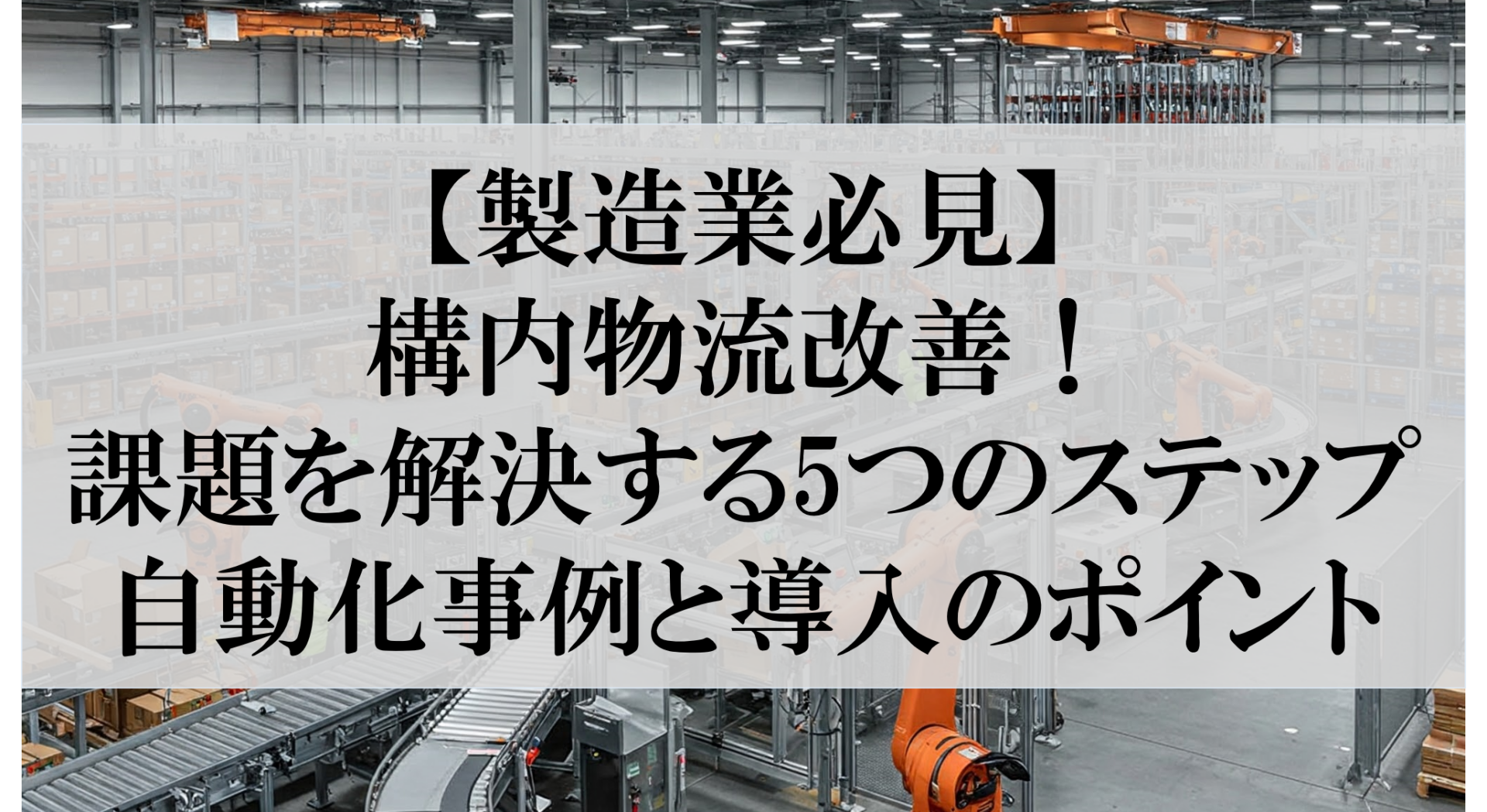
製造業における構内物流の課題を解決する5つのステップを解説した記事です。
工場内のモノの流れを効率化する構内物流は、生産性向上に重要です。
本記事では、物流の基礎知識から、倉庫・工程における課題、改善事例、自動化の導入ポイントまでご紹介します。
構内物流の効率化で、全体的な生産性向上を目指しましょう。
目次
1. 構内物流とは?その役割と重要性を解説
1.1. 構内物流の定義と種類
構内物流とは、工場や倉庫内におけるモノの流れを指します。具体的には、原材料の調達から製品の出荷まで、工場内で行われる一連の物流業務を指します。
工場によっては、物流が生産性向上に大きく影響する場合もあります。
構内物流は、大きく分けて以下の3つの種類があります。
- 調達物流: 原材料や部品を調達し、工場に搬入する物流
- 生産物流: 製造工程における資材や部品の搬送、保管など
- 販売物流: 完成品を倉庫に保管し、顧客に配送する物流
1.2. 製造業における構内物流の役割
製造業において、構内物流は生産活動を支える重要な役割を担っています。
- 必要な時に、必要な場所へ、必要な量の資材を供給する
- 製造工程におけるモノの移動を効率化し、生産性を向上させる
- 製品の品質を維持し、顧客満足度を高める
- 在庫管理を適切に行い、コストを削減する
1-3. 構内物流が重要な理由
構内物流が重要な理由は、以下の点が挙げられます。
- 生産性向上: 効率的な構内物流は、製造工程における無駄を排除し、生産性を向上させます。
- コスト削減: 適切な在庫管理や搬送の効率化は、物流コストを削減します。
- 品質向上: 適切な保管方法や搬送経路は、製品の品質を維持します。
- 顧客満足度向上: 迅速かつ正確な出荷は、顧客満足度を高めます。
2. 構内物流における課題と問題点
2.1. 倉庫における課題(在庫管理、スペース不足など)
倉庫における課題は、主に以下の点が挙げられます。
- 在庫管理の煩雑さ: 製品の種類が増えるほど、在庫管理が煩雑になり、誤出荷や在庫過剰が発生しやすくなります。
- スペース不足: 製品の保管スペースが不足すると、作業効率が低下し、製品の品質劣化を招く可能性があります。
- ピッキング作業の非効率: ピッキング作業は、倉庫内作業の中でも特に時間と手間がかかる作業です。
2.2. 工程における課題(搬送のムダ、作業のムラなど)
工程における課題は、主に以下の点が挙げられます。
- 搬送のムダ: 搬送距離が長かったり、搬送回数が多かったりすると、時間とエネルギーの無駄が発生します。
- 作業のムラ: 作業者のスキルや経験によって作業時間にバラつきが生じると、生産ライン全体の効率が低下します。
- ラインの停止: 部品や資材の供給が遅れると、生産ラインが停止し、生産計画に影響が出ます。
2.3. 人材に関する課題(人手不足、高齢化、教育不足など)
人材に関する課題は、主に以下の点が挙げられます。
- 人手不足: 物流業界は人手不足が深刻であり、必要な人員を確保することが難しい状況です。
- 高齢化: 物流現場では高齢化が進んでおり、若手人材の育成が急務となっています。
- 教育不足: 物流業務には専門的な知識やスキルが必要ですが、教育体制が整っていない企業が多くあります。
2.4. 情報管理の課題(可視化不足、情報共有不足など)
情報管理の課題は、主に以下の点が挙げられます。
- 可視化不足: 在庫情報や搬送状況などがリアルタイムに把握できないと、適切な判断ができません。
- 情報共有不足: 倉庫、工程、販売部門間で情報共有がスムーズに行われないと、連携がうまくいかず、非効率な作業が発生します。
- システム化の遅れ: 情報管理システムが導入されていないと、手作業での管理が多くなり、ミスが発生しやすくなります。
3. 構内物流を改善する5つのステップ
3.1. ステップ1:現状分析と課題の明確化
まずは、自社の構内物流の現状を分析し、課題を明確にすることが重要です。
- 現状把握: 倉庫のレイアウト、搬送経路、在庫管理方法、作業者のスキルなどを把握します。
- データ収集: 在庫データ、搬送時間データ、作業時間データなどを収集します。
- 課題分析: 収集したデータを分析し、課題を洗い出します。
3.2. ステップ2:改善目標の設定
次に、改善目標を設定します。
- 数値目標: 生産性向上率、コスト削減率、誤出荷率削減率など、具体的な数値目標を設定します。
- 達成時期: いつまでに目標を達成するか、具体的な時期を設定します。
3.3. ステップ3:具体的な改善策の検討
課題と目標を踏まえ、具体的な改善策を検討します。
- レイアウト改善: 搬送距離の短縮、保管スペースの確保などを検討します。
- 搬送効率化: 自動搬送機の導入、搬送ルートの最適化などを検討します。
- 在庫管理システム導入: WMSなどの在庫管理システム導入を検討します。
- 情報共有システム導入: 情報共有システム導入を検討します。
3.4. ステップ4:改善策の実施と効果測定
検討した改善策を実施し、効果測定を行います。
- テスト導入: まずは小規模でテスト導入し、効果を確認します。
- 本格導入: テスト導入で効果が確認できたら、本格導入します。
- 効果測定: 改善策実施後、目標達成状況を測定します。
3.5. ステップ5:継続的な改善活動
改善は一度行ったら終わりではありません。継続的な改善活動が重要です。
- 定期的な見直し: 定期的に現状を見直し、改善点を探します。
- PDCAサイクル: PDCAサイクルを回し、継続的に改善を行います。
4. 構内物流の改善事例
4.1. 倉庫のレイアウト改善で効率化を実現した事例
ある企業では、倉庫のレイアウトを見直すことで、ピッキング作業の効率化を実現しました。
- 改善前: 製品が種類別に保管されておらず、ピッキング作業者が倉庫内を歩き回る必要がありました。
- 改善後: 製品を種類別に保管し、ピッキングしやすい場所に配置しました。
- 結果: ピッキング作業時間が大幅に短縮されました。
4.2. AGV導入による搬送の自動化で省人化を実現した事例
ある企業では、AGV(無人搬送車)を導入することで、搬送作業の自動化を実現しました。
- 改善前: 作業者がフォークリフトで製品を搬送していました。
- 改善後: AGVが製品を自動で搬送するようになりました。
- 結果: 搬送作業の人員を削減し、人件費を削減しました。
4.3. 情報共有システム導入による在庫管理の精度向上を実現した事例
ある企業では、情報共有システムを導入することで、在庫管理の精度向上を実現しました。
- 改善前: 在庫情報が正確に把握できず、誤出荷や在庫過剰が発生していました。
- 改善後: 情報共有システムにより、リアルタイムに在庫情報を把握できるようになりました。
- 結果: 誤出荷が減少し、在庫管理コストが削減されました。
4.4. 3PL活用による物流業務のアウトソーシングでコスト削減を実現した事例
ある企業では、3PL(サードパーティーロジスティクス)を活用することで、物流業務のアウトソーシングを実現しました。
- 改善前: 自社で物流業務を行っていましたが、コストがかかっていました。
- 改善後: 3PL事業者に物流業務を委託しました。
- 結果: 物流コストが削減され、本業に集中できるようになりました。
5. 構内物流の自動化
5.1. 自動化のメリットとデメリット
構内物流の自動化には、以下のようなメリットとデメリットがあります。
メリット
- 省人化: 人手不足の解消、人件費削減
- 効率化: 搬送時間の短縮、作業効率向上
- 精度向上: 誤搬送の減少、品質向上
- 安全性向上: 作業者の負担軽減、事故防止
- 24時間稼働: 夜間や休日も稼働できる
デメリット
- 導入コスト: 設備投資が必要
- 運用コスト: メンテナンス費用、電気代など
- 柔軟性: レイアウト変更に時間がかかる場合がある
- システム依存: システムトラブル時に業務が停止する可能性がある
- 初期設定: 導入時の設定や調整が必要
5.2. 自動化に適した工程と作業
構内物流の自動化は、以下の工程や作業に適しています。
5.3. 自動化の導入手順とポイント
構内物流の自動化を導入する際は、以下の手順とポイントを押さえましょう。
- 現状分析: 課題を明確にし、自動化の必要性を検討する
- 目的設定: 自動化によって達成したい目標を設定する
- システム選定: 自社の課題や目的に合ったシステムを選定する
- 導入計画: 導入スケジュール、予算、体制などを計画する
- テスト導入: まずは小規模でテスト導入し、効果を確認する
- 本格導入: テスト導入で効果が確認できたら、本格導入する
- 効果測定: 導入後、目標達成状況を測定する
- 運用・改善: 運用状況を監視し、継続的に改善を行う
導入時のポイント
- 現場との連携: 現場の意見を聞き、協力体制を築く
- 段階的な導入: 最初から全てを自動化するのではなく、段階的に導入する
- 教育・研修: 作業者に自動化システムの操作方法などを教育する
- メンテナンス: 定期的なメンテナンスを行い、故障を防ぐ
5.4. AGV、AMR、RFIDなどの自動化技術を紹介
構内物流の自動化に活用される主な技術には、以下のものがあります。
- AGV (Automated Guided Vehicle):
・設定されたルートを走行する無人搬送車。
・磁気テープやレーザー誘導などで走行する。
・比較的安価で導入しやすいが、ルート変更に手間がかかる。 - AMR (Autonomous Mobile Robot):
・自律的に移動するロボット。
・地図作成機能や障害物回避機能などを搭載し、柔軟な搬送が可能。
・AGVに比べて高価だが、汎用性が高い。 - RFID (Radio Frequency Identification):
・ICタグを利用した情報管理システム。
・製品やパレットにICタグを取り付け、情報を読み取ることで、在庫管理や搬送管理を効率化する。 - WMS (Warehouse Management System):
・倉庫管理システム。
・入庫、出庫、在庫管理、ピッキング、梱包などの業務を管理する。
・RFIDと連携することで、より効率的な管理が可能になる。 - 自動倉庫:
・コンピューター制御によって、入庫、出庫、保管を行う倉庫。
・高密度な保管が可能で、スペース効率が良い。 - ピッキングロボット:
・ピッキング作業を自動化するロボット。
・画像認識機能やAIを活用し、様々な形状の製品をピッキングできる。
これらの技術を組み合わせることで、より効率的な構内物流を実現できます。
6. さらに構内物流を改善するためのポイント
6.1. 5S活動による現場環境の整備
5S活動(整理、整頓、清掃、清潔、躾)は、構内物流の改善に欠かせない活動です。
- 整理: 不要なものを処分し、必要なものを必要な場所に置く
- 整頓: ものの置き場所を決め、誰でもすぐに取り出せるようにする
- 清掃: 現場を清潔に保ち、安全な作業環境を作る
- 清潔: 整理、整頓、清掃を維持する
- 躾: 決められたことを守り、習慣化する
5S活動を徹底することで、無駄な動きや探す時間を減らし、作業効率を向上させることができます。
6.2. 標準化による業務の効率化
業務を標準化することで、作業のバラつきをなくし、効率化を図ることができます。
- 作業手順書の作成: 各作業の手順を明確に記載した作業手順書を作成する
- マニュアル作成: 作業に必要な知識やスキルをまとめたマニュアルを作成する
- 教育訓練: 作業者に標準化された手順を教育する
標準化により、作業時間の短縮、ミスの削減、品質の安定化を実現できます。
6.3. 人材育成によるスキルアップ
構内物流の改善には、人材育成も重要です。
- 研修: 物流に関する知識やスキルを習得する研修を実施する
- 資格取得支援: 物流関連の資格取得を支援する
- OJT: 実務を通してスキルを習得する機会を提供する
人材育成により、作業者のモチベーション向上、定着率向上、生産性向上を実現できます。
6.4. 最新技術の活用
最新技術を積極的に活用することで、構内物流をさらに効率化できます。
- AI (人工知能): 需要予測や在庫管理に活用する
- IoT (Internet of Things): センサーで取得したデータを活用する
- ビッグデータ: 収集したデータを分析し、改善に役立てる
- VR (仮想現実): 作業者の教育訓練に活用する
これらの技術を活用することで、より高度な自動化や効率化を実現できます。
まとめ|構内物流改善で生産性向上を実現
構内物流は、製造業の生産性を大きく左右する重要な要素です。課題を解決し、改善を進めることで、生産性向上、コスト削減、品質向上、顧客満足度向上など、様々なメリットが得られます。
この記事では、構内物流の基礎知識から、課題、改善ステップ、自動化事例、導入ポイントまで、網羅的に解説しました。ぜひ、この記事を参考に、自社の構内物流を見直し、改善に取り組んでみてください。
関連情報
【コンサルティング】品質管理に関する専門家相談
品質管理に関する専門家にご相談いただけます。お気軽にお問い合わせください。
今回では、工場における物流の重要性について事例をもとに説明をしてまいりました。
弊社が主催している下記セミナーでは、自社の生き残りをかけたDXの取組を、実際の事例をもとにお話ししています。
改めて、下記のような課題を抱えられている方はぜひご参加ください。
【このような社長におすすめ】
- 多品種少量生産の窯業・土石製品製造業の社長
- 長年の職人技術に依存した生産体制が続いており、データ化・データ活用ができていない。
- 標準原価で収益管理しているが、材料費高騰・賃上げに対応できていない。
- Excel運用が多く、社内での情報共有がリアルタイムにできない。
- 原価管理をどのように利益UPに結びつけるか具体的な方法を知りたい。
- 経営指標はもちろんだが、現場指標を設けて従業員に経営意識を持たせたい。
【本セミナーで学べるポイント】
- 実際原価管理・現場改善による利益率UPを実践した成功事例がわかる!
~実際原価管理がどのように経営に影響したのかを実際の資料をもとにお伝えします~ - 現場自らが動き出せる現場指標・経営意識を持つための原価管理方法がわかる!
~今すぐに取り組める現場指標管理方法をお教えします~ - 現場の実際工数を経営や現場が活用できるように分析する方法がわかる!
~経営陣だけでなく現場自らが動きだせるデータ分析方法がわかります~ - 多品種少量”だからこそ”今すぐ実践できる原価管理DX・利益UPまでの道筋が分かる!
~理論・理屈ではなく、自社の現場で実践できる具体的なDX経営手法が分かります~
https://www.funaisoken.co.jp/seminar/124761
https://www.funaisoken.co.jp/dl-contents/smart-factory_smart-factory_03729_S045