記事公開日:2025.04.11
最終更新日:2025.04.14
多品種少量生産の中小製造業必見!利益を生む「工場組織図」と「原価管理」の連携戦略
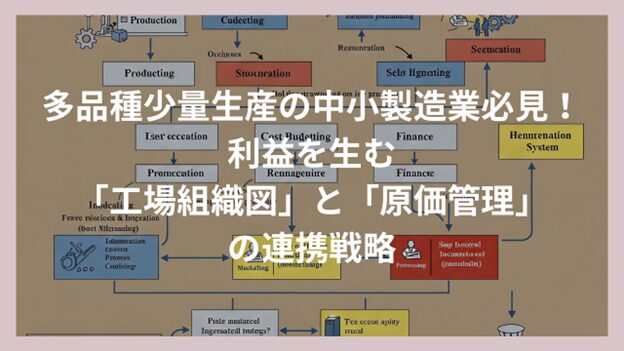
いつもコラムをご愛読いただきありがとうございます。
船井総合研究所の熊谷俊作です。
日々のコンサルティング活動の中で、「自社に合った工場の組織体制が分からない」「原価管理が上手くいかず、利益が伸び悩んでいる」「組織とコストの問題をどう連携させて解決すればいいのか」といった経営者様や工場長様の切実な悩みを数多くお聞きしてきました。
特に、顧客の多様なニーズに応える多品種少量生産の現場では、生産プロセスが複雑化しやすく、組織運営やコスト管理の難易度が高まる傾向にあります。従来の画一的な組織体制やどんぶり勘定のままでは、変化の激しい市場環境に対応し、持続的な成長を遂げることは困難です。
この記事では、多品種少量生産を行う中小製造業の皆様が抱える、「工場の組織図」と「原価管理」という二つの重要な経営課題に着目します。それぞれの基本的な考え方から、具体的な種類、作成・導入ステップ、そして両者をいかに連携させて利益最大化につなげるか、という実践的な戦略までを徹底的に解説します。
この記事を読むことで、あなたは以下のことを理解できます。
- 多品種少量生産において、なぜ適切な工場組織図が不可欠なのか
- 自社に適した工場組織図の種類と、そのメリット・デメリット
- 失敗しない工場組織図の具体的な作成ステップ
- 組織体制が原価管理の精度や効率にどう影響するのか
- 多品種少量生産に適した原価管理のポイントと進め方(6ステップ)
- 組織図と原価管理を連携させ、生産性向上とコスト削減を実現する方法
- 実際に組織改革と原価管理改善で成果を上げた企業の事例(実体験風)
この記事は、以下のような方に特におすすめです。
- 多品種少量生産を行っている中小製造業の経営者、役員の方
- 工場の生産性向上やコスト削減に取り組んでいる工場長、部門責任者の方
- 自社の組織体制や原価管理の方法に見直しを検討している方
- 部門間の連携不足や責任の所在の不明確さに課題を感じている方
- より効果的な工場運営と利益体質の強化を目指すすべての方
この記事を通して、皆様の工場がより強く、しなやかな組織へと進化し、厳しい競争環境の中でも着実に利益を生み出せる体制を構築するための一助となれば幸いです。それでは、具体的な内容に入っていきましょう。
目次
多品種少量生産の中小製造業こそ「工場の組織図」が重要な理由
工場の組織図と聞くと、「大企業が作るもの」「形式的なもので、実際の業務にはあまり関係ない」と感じる中小製造業の経営者様もいらっしゃるかもしれません。しかし、顧客の要求が多様化し、製品ライフサイクルが短縮化する現代において、特に多品種少量生産を手掛ける中小製造業にとって、戦略的に設計された工場の組織図は、企業の競争力を左右する極めて重要な経営ツールなのです。
その理由を詳しく見ていきましょう。
複雑化する生産プロセスと組織体制の課題
多品種少量生産の現場は、扱う製品の種類が多く、生産ロットが小さいという特徴があります。そのため、段取り替えが頻繁に発生し、生産計画は複雑になりがちです。また、製品ごとに異なる部品、工程、品質基準が求められるため、管理すべき情報量も膨大になります。このような状況下で、旧態依然とした組織体制のままでは、様々な問題が発生しやすくなります。
例えば、私が以前コンサルティングを担当したある金属加工メーカー(従業員約50名)では、社長がすべての指示を出し、各工程の職人が個々の判断で作業を進める、いわゆる「文鎮型」の組織でした。創業当初は少品種の量産が中心だったため、この体制でも問題なく運営できていました。しかし、時代の変化とともに多品種少量の受注が増えるにつれて、問題が顕在化し始めました。
具体的には、以下のような課題が発生していました。
- 情報伝達の遅延・錯綜: 社長を経由しないと情報が伝わらず、急な仕様変更や納期変更への対応が遅れる。
- 部門間の連携不足: 設計、加工、検査といった部門間の連携が悪く、手戻りや工程間の待ち時間が増加する。
- 責任の所在の不明確化: 問題が発生しても、どの部門・誰の責任なのかが曖昧になり、原因究明や再発防止が進まない。
- 若手人材の育成の遅れ: 特定のベテラン職人に業務が集中し、技術やノウハウの継承が進まない。
- 意思決定の遅延: すべての判断を社長に仰ぐため、現場レベルで迅速な意思決定ができない。
これらの課題は、結果として生産性の低下、納期の遅延、品質の不安定化、そしてコストの増加といった深刻な経営問題につながっていました。
この事例のように、生産形態の変化に合わせて組織体制を最適化しなければ、現場の混乱を招き、企業の成長を妨げる要因となってしまうのです。
組織図がもたらす「見える化」と意思決定の迅速化
適切に設計された工場の組織図は、単なる部門の配置図ではありません。
それは、企業の戦略を実現するための「設計図」であり、様々な効果をもたらします。特に重要なのが、「役割・責任・権限の見える化」と、それによる「意思決定の迅速化」です。
組織図を作成するプロセスを通じて、各部門や役職が「何をすべきか(役割)」「何に対して責任を持つのか(責任)」「どこまで自分で判断できるのか(権限)」が明確になります。
これにより、従業員一人ひとりが自分のミッションを理解し、責任感を持って業務に取り組むことができます。誰に報告し、誰から指示を受けるのか(指揮命令系統)が明確になることで、情報伝達がスムーズになり、混乱を防ぐことができます。
先ほどの金属加工メーカーの例で言えば、もし機能別に部門を分け、各部門に責任者を配置し、その責任者に一定の権限を委譲するような組織図があれば、状況は大きく改善されたはずです。
例えば、製造部門長は生産計画の変更に迅速に対応でき、品質管理部門長は検査基準の徹底を図ることができます。各部門長が責任を持って担当領域を管理し、部門間で必要な情報を適切に連携することで、現場レベルでの問題解決能力が向上し、社長はより重要な経営判断に集中できるようになります。
さらに、組織図は「誰に相談すればよいか」を明確にする効果もあります。多品種少量生産では、予期せぬトラブルやイレギュラーな要求が発生しがちです。そのような時に、組織図があれば、関連する部門や担当者をすぐに特定し、迅速に連携して対応することが可能になります。
これにより、問題解決までの時間が短縮され、顧客満足度の向上にもつながります。
このように、工場の組織図は、複雑化する多品種少量生産の現場において、業務の効率化、責任体制の明確化、迅速な意思決定を実現するための基盤となるのです。
それは、従業員のモチベーション向上や人材育成にも寄与し、ひいては企業全体の生産性向上と収益力強化に不可欠な要素と言えるでしょう。
多品種少量生産に適した工場の組織図の種類と選び方
工場の組織図には、いくつかの代表的な型があります。それぞれに特徴があり、メリット・デメリットも異なります。多品種少量生産を行う中小製造業が、自社の状況や目指す方向に合わせて最適な組織図を選ぶためには、まず各種類の特徴を理解することが重要です。ここでは、代表的な組織図の種類と、そのメリット・デメリット、そして多品種少量生産への適性について解説します。
機能別組織図:専門性は高いが、部門間の壁が課題に
機能別組織図は、製造、技術、品質管理、購買、生産管理など、業務の機能(ファンクション)ごとに部門を編成する、最も一般的で古典的な組織形態です。
例えば、「製造部」「技術部」「品質管理部」といった形で部門が構成されます。社長の下に各機能部門の責任者(部長など)が配置され、それぞれの部門内で専門的な業務を行います。
メリット:
- 専門性の向上: 各部門が特定の機能に特化するため、専門知識やスキルが蓄積されやすく、業務の効率化や高度化が期待できます。例えば、製造部は生産技術の改善に集中でき、技術部は新製品開発に専念できます。
- 資源の効率的な活用: 各機能に必要な設備や人材を部門内に集約できるため、重複投資を防ぎ、資源を効率的に活用できます。例えば、高価な測定機器を品質管理部に集約するなどです。
- 明確なキャリアパス: 各機能分野での専門性を高めていくキャリアパスが描きやすく、従業員のスキルアップやモチベーション向上につながりやすいです。
- 経営トップによる統制の容易さ: 各機能部門の責任者を通じて、組織全体を管理・統制しやすい構造です。
- 標準化の推進: 部門内で業務プロセスやルールを標準化しやすく、業務の安定化や品質維持に貢献します。
デメリット:
- 部門間の壁(セクショナリズム): 各部門が自部門の目標や利益を優先しがちになり、部門間の連携が悪くなる可能性があります。これが「サイロ化」と呼ばれる状態です。
- 意思決定の遅延: 部門をまたがる問題が発生した場合、部門間の調整に時間がかかり、意思決定が遅れることがあります。特に、多品種少量生産で求められる迅速な対応が難しくなる場合があります。
- 顧客ニーズへの対応力低下: 各部門が機能に特化するあまり、製品全体や顧客の視点が欠けやすくなる可能性があります。例えば、製造効率を優先するあまり、顧客が求める短い納期に対応できないなどです。
- ゼネラリスト人材の育成難: 部門内での専門性は高まりますが、組織全体を俯瞰できるような幅広い知識や経験を持つ人材(ゼネラリスト)が育ちにくい傾向があります。
- 環境変化への適応力: 市場環境や顧客ニーズが大きく変化した場合、組織構造の変更に時間がかかり、迅速に対応することが難しい場合があります。
多品種少量生産への適性:
機能別組織図は、比較的製品の種類が少なく、生産プロセスが安定している場合には有効です。専門性を活かして各工程の効率を高めることができます。しかし、多品種少量生産のように、製品の種類が多く、仕様変更や納期変更が頻繁に発生する場合には、部門間の連携不足や意思決定の遅延がボトルネックとなりやすい側面があります。特に、部門間の情報共有や協力体制が十分に構築されていないと、生産リードタイムの長期化や手戻りの増加を招く可能性があります。
製品別組織図:製品ごとの迅速な対応が可能だが、部門重複のコスト増も
参考記事で紹介されている原価管理の6つのステップを、多品種少量生産の現場でどのように応用できるのかを具体的に解説します。
多品種少量生産を行う中小製造業が原価管理に取り組む際には、参考記事で解説されている6つのステップを基本としつつ、自社の状況に合わせて応用していくことが重要です。
1. 現状把握: まず、自社の多品種少量生産におけるコストの現状を詳細に把握します。製品別、工程別はもちろんのこと、ロット別、顧客別など、様々な切り口でコストを分析することが重要です。例えば、特定の顧客からの受注製品のコストが高い場合、その原因を掘り下げて分析する必要があります。
2. 目標設定: 現状把握の結果を踏まえ、具体的なコスト削減目標を設定します。多品種少量生産では、製品ごとに利益率が異なる場合があるため、製品別の目標設定も有効です。例えば、「〇〇製品の製造コストを、次の四半期までに〇%削減する」といった具体的な目標を設定します。
3. 対策立案: 目標達成のために、具体的な対策を検討します。多品種少量生産においては、段取り時間の短縮、作業の標準化、不良の削減、共通部品の活用などが考えられます。現場の作業者からのアイデアも積極的に取り入れることが重要です。
4. 対策実行: 立案した対策を実行に移します。多品種少量生産では、多くの部門が連携する必要があるため、関係部署との情報共有を密に行い、計画的に実行していくことが重要です。
5. 効果測定: 対策の実施後、コスト削減効果を測定します。多品種少量生産では、対策によって特定の製品のコストは削減できたものの、他の製品の品質が低下してしまった、というような事態も起こりうるため、多角的な視点での評価が必要です。
6. 定着・改善: 効果のあった対策は標準化し、継続的に実施できるように定着させます。多品種少量生産の環境は常に変化しているため、定期的に原価管理の状況を見直し、継続的な改善に取り組む姿勢が重要です。
多品種少量生産における品質目標達成がコスト削減に貢献する理由
品質目標の達成は、不良品削減や歩留まり向上など、様々な側面からコスト削減に貢献します。具体的な理由を解説します。
不良品削減による材料費と再作業コストの低減
製品別組織図は、特定の製品群や事業ごとに、必要な機能(設計、製造、販売など)をまとめて一つの部門(事業部)として編成する組織形態です。
「A製品事業部」「B製品事業部」といった形で構成され、各事業部長がそれぞれの製品群に関する全責任と権限を持ちます。
事業部内は、さらに機能別に組織されることもあります。
メリット:
- 製品・市場への迅速な対応: 各事業部が特定の製品や市場に責任を持つため、顧客ニーズの変化や競合の動きに対して、迅速かつ柔軟に対応することが可能です。多品種少量生産においても、製品ごとの特性に合わせた機動的な運営が期待できます。
- 責任と成果の明確化: 事業部ごとに損益計算が行われることが多く、各事業部の責任と成果が明確になります。これにより、事業部長の経営者意識が高まり、収益性向上へのインセンティブが働きます。
- 意思決定の迅速化: 各事業部長に大幅な権限が委譲されるため、事業部内で完結する意思決定が迅速に行われます。これにより、製品開発や生産改善のスピードが向上します。
- 経営者人材の育成: 事業部長は、担当事業に関する広範な責任と権限を持つため、将来の経営幹部候補となる人材を育成する場として有効です。
- 部門間調整の負荷軽減: 製品に関する問題の多くが事業部内で解決されるため、機能別組織で見られるような部門間の複雑な調整業務が軽減されます。
デメリット:
- 機能部門の重複によるコスト増: 各事業部内に同様の機能(例えば、設計部門や購買部門)を持つことになるため、組織全体で見ると機能が重複し、管理コストや間接費が増加する可能性があります。
- 全社的な視点の欠如: 各事業部が自部門の利益を最優先するあまり、全社的な資源の最適配分や技術共有が進まなくなる可能性があります。例えば、ある事業部で開発された優れた技術が、他の事業部に展開されないなどです。
- 事業部間の壁: 機能別組織と同様に、事業部間で壁ができ、協力体制が築きにくくなることがあります。特に、共通の顧客を持つ場合などに問題となる可能性があります。
- 導入の難易度(中小企業の場合): 各事業部がある程度の規模と独立性を持つ必要があるため、比較的小規模な中小製造業では導入が難しい場合があります。人材や資源の制約から、事業部として独立採算で運営することが困難なケースもあります。
- 短期的な視点に陥る可能性: 事業部ごとの損益が重視されるあまり、短期的な成果を追求し、長期的な視点での研究開発や人材育成への投資が疎かになる可能性があります。
多品種少量生産への適性:
製品別組織図は、扱う製品群が明確に分かれており、それぞれの製品で市場特性や要求される技術が大きく異なる場合に有効です。製品ごとの専門性を高め、市場への対応力を強化できます。多品種少量生産の中でも、特定の顧客向けの専用ラインや、特殊な技術を要する製品群がある場合などは、この組織形態が適している可能性があります。ただし、中小製造業においては、機能の重複によるコスト増や、各事業部を運営できる人材の確保が課題となるでしょう。
マトリックス組織図:柔軟性は高いが、指揮系統の複雑化に注意
マトリックス組織図は、従業員が機能別部門(例:製造部、技術部)と、特定の製品やプロジェクトチームの両方に所属する組織形態です。
従業員は、機能部門の上司(ファンクショナルマネージャー)と、製品・プロジェクトの責任者(プロダクトマネージャー、プロジェクトマネージャー)の双方から指示を受ける(ワンマン・ツーボス)のが特徴です。
メリット:
- 柔軟性と適応力: プロジェクトや製品の状況に合わせて、必要な専門知識を持つ人材を機能部門から柔軟に集め、チームを編成できます。これにより、複雑な課題や新しい要求に迅速かつ効果的に対応することが可能です。多品種少量生産における急な仕様変更や短納期要求にも対応しやすい体制です。
- 専門知識の共有と活用: 機能部門の専門知識と、製品・プロジェクトごとの要求を結びつけることで、イノベーションが促進され、より高度な問題解決が可能になります。異なる専門分野のメンバーが協力することで、新たなアイデアが生まれやすくなります。
- 資源の効率的な活用: 機能部門に所属する専門家を、複数のプロジェクトや製品で共有できるため、限られた人材や設備といった経営資源を効率的に活用できます。
- 従業員のスキル向上と多能工化: 従業員は、専門分野の知識を深めると同時に、プロジェクトを通じて他の分野の知識や経験を得ることができます。これにより、多角的な視点を持つ人材(多能工)が育成されやすくなります。
- コミュニケーションの活性化: 縦(機能部門)と横(プロジェクト・製品)の連携が必須となるため、組織内のコミュニケーションが活性化され、情報共有が促進されます。
デメリット:
- 指揮命令系統の混乱(ワンマン・ツーボス問題): 従業員が二人の上司から指示を受けるため、指示の内容が矛盾したり、どちらの指示を優先すべきか混乱したりする可能性があります。これにより、従業員にストレスがかかり、意思決定が遅れることもあります。
- 権限と責任の不明確化: 機能マネージャーとプロジェクトマネージャーの間で、権限と責任の範囲が曖昧になりやすく、対立が生じる可能性があります。どちらが最終的な決定権を持つのかが不明確だと、問題解決が進まないことがあります。
- 調整コストの増加: マネージャー間の調整や、メンバー間の意見調整に多くの時間と労力がかかる場合があります。会議が増えたり、コンフリクト解決のためのコストが発生したりする可能性があります。
- ストレスとプレッシャー: 従業員は、複数の要求に応えなければならず、役割の重複や過剰な負荷によってストレスを感じやすくなる可能性があります。
- 導入と運用の難易度: 組織文化として、高度なコミュニケーション能力や協調性が求められます。明確なルール設定や、マネージャー間の良好な関係構築が不可欠であり、導入と運用には十分な準備とトレーニングが必要です。
多品種少量生産への適性:
マトリックス組織図は、技術的な要求が高く、部門間の緊密な連携が不可欠な製品やプロジェクトを多く抱える場合に有効です。特に、新製品開発が頻繁に行われる、あるいは顧客ごとのカスタマイズ要求が多い多品種少量生産には、その柔軟性と適応力が強みとなります。しかし、中小製造業で導入する際には、指揮命令系統の混乱を避けるための明確なルール作りと、マネージャー間の密なコミュニケーション体制の構築が成功の鍵となります。小規模な組織であれば、比較的導入しやすい側面もありますが、運用には注意が必要です。
中小製造業におすすめの組織図パターンと事例
多くの中小製造業、特に多品種少量生産を手掛ける企業にとって、純粋な機能別組織、製品別組織、マトリックス組織のいずれか一つだけを採用するのではなく、これらの要素を組み合わせたハイブリッド型の組織形態が現実的で効果的な場合が多いです。
例えば、基本は機能別組織としつつ、特定の重要製品や新規開発プロジェクトに対して、部門横断的なチーム(マトリックス組織の要素)を一時的または恒常的に設置するといった形です。これにより、日常業務の効率性と専門性を維持しつつ、特定の課題に対して柔軟に対応できる体制を構築できます。
中小製造業においては、自社の規模、製品特性、企業文化、そして目指す方向性を考慮し、既存の組織形態の良い点を活かしつつ、課題を解決するための要素を柔軟に取り入れることが、最適な組織図を見つけるための重要なアプローチとなります。
失敗しない!中小製造業のための工場組織図作成ステップ
効果的な工場の組織図は、ただ既存の体制を図に落とし込むだけでは生まれません。自社の現状を正確に把握し、目指すべき姿を明確にした上で、戦略的に設計していく必要があります。ここでは、中小製造業が失敗せずに、自社に最適な工場組織図を作成するための具体的なステップを解説します。
ステップ1:現状の組織課題と生産プロセスの徹底分析
組織図作成の第一歩は、「今、何が問題なのか」を徹底的に洗い出すことです。思い込みや感覚ではなく、客観的な事実に基づいて現状を分析することが重要です。
● 組織に関する課題の洗い出し:
- 部門間の連携はスムーズか?(情報共有、協力体制など)
- 指示命令系統は明確か?混乱は生じていないか?
- 各部門・役職の役割と責任は明確か?重複や抜け漏れはないか?
- 意思決定は適切なスピードで行われているか?ボトルネックはどこか?
- 従業員の業務負荷は偏っていないか?
- 人材育成は計画的に行われているか?技術継承は進んでいるか?
- 従業員のモチベーションはどうか?組織に対する不満はないか? (従業員アンケートやヒアリングを実施するのも有効です)
● 生産プロセスの分析:
- 受注から出荷までのリードタイムは?各工程の時間は?
- ボトルネックとなっている工程はどこか?
- 手戻りや不良品の発生状況は?原因は何か?
- 段取り替えの頻度と時間は?
- 在庫(原材料、仕掛品、完成品)は適正か?
- 生産計画と実績の乖離は?
- 各工程の生産性は? (バリューストリームマッピングなどの手法を用いて、モノと情報の流れを可視化すると効果的です)
このステップでは、現場の従業員の声を丁寧にヒアリングすることが欠かせません。実際に業務を行っているからこそ分かる問題点や改善のヒントが数多く隠されています。
私がコンサルティングに入る際も、必ず現場を歩き、様々な立場の従業員の方々と対話することから始めます。そこで得られる生の情報こそが、実効性のある組織改革の土台となるのです。
分析結果は、具体的な数値や事実を挙げて、客観的に整理しておくことが後のステップで役立ちます。
ステップ2:目指すべき姿と経営目標の明確化
現状の課題を把握したら、次に「将来、どのような工場・会社になりたいのか」という目指すべき姿(ビジョン)と、それを達成するための具体的な経営目標を明確にします。組織図は、このビジョンと目標を実現するための手段であるべきです。
● ビジョンの設定:
- 3年後、5年後、どのような工場になっていたいか?
- 顧客からどのような価値を提供できる工場でありたいか?
- 従業員がどのように働ける工場にしたいか?(働きがい、成長機会など)
- 地域社会に対してどのような貢献をしたいか?
● 経営目標の設定(具体的・測定可能に):
- 売上高、利益率の目標値
- 生産性向上の目標値(例:一人当たり生産性〇%向上)
- リードタイム短縮の目標値(例:平均リードタイム〇日短縮)
- 不良率削減の目標値(例:不良率〇%削減)
- 納期遵守率の目標値(例:納期遵守率99%以上)
- 新製品開発の目標(例:年間〇件の新製品上市)
- 従業員満足度向上の目標値
ここで重要なのは、経営層だけでなく、管理職や現場のリーダー層も巻き込んで議論することです。全員で目指す方向性を共有することで、組織改革への当事者意識が高まり、実行段階での協力が得られやすくなります。設定したビジョンと目標は、組織図を設計する上での「羅針盤」となります。どのような組織構造が、これらの目標達成に最も貢献できるかを判断する基準になるのです。
ステップ3:最適な部門構成と役割分担の設計
現状分析と目標設定を踏まえ、いよいよ具体的な組織構造、すなわち部門の構成と、各部門が担うべき役割(ミッション)を設計していきます。
● 部門構成の検討:
- 現状の部門構成は、設定した目標達成に適しているか?
- 機能別、製品別、マトリックス型、あるいはハイブリッド型など、どの組織形態が自社に最も合っているか?(前述の各組織形態のメリット・デメリットを参考に検討)
- 新しい機能(例:DX推進室、生産技術開発課など)を追加する必要はないか?
- 逆に、統合・廃止すべき部門はないか?
- 部門の階層(例:部-課-係)は適切か?フラット化は可能か?
● 各部門の役割(ミッション)の定義:
- 各部門が、会社のビジョン達成や経営目標達成のために、具体的に何をすべきか?
- 主要な業務内容は何か?
- どのような成果を出すことが期待されているか?(KPIの設定)
- 他の部門との連携において、どのような役割を果たすべきか?
例えば、「リードタイム短縮」という目標に対しては、生産管理部門の役割として「精度の高い生産計画立案と進捗管理」、製造部門の役割として「段取り時間短縮と多能工化推進」、購買部門の役割として「部品調達リードタイムの短縮」などが考えられます。このように、目標達成から逆算して、各部門に必要な機能と役割を割り当てていくことが重要です。部門の名称も、その役割が分かりやすいものにすると良いでしょう。
(例:「品質管理課」→「品質保証部」など、責任範囲を明確にする)
ステップ4:責任と権限の明確化による指示系統の確立
部門構成と役割が決まったら、次に各役職(部長、課長、係長、リーダーなど)の「責任」と「権限」を明確にし、誰が誰に指示を出し、誰に報告するのかという「指示命令系統(指揮命令系統)」を確立します。これが曖昧だと、組織はうまく機能しません。
● 責任の明確化:
- 各役職者は、どの業務範囲と成果に対して責任を負うのか?
- 部門目標の達成責任は誰にあるのか?
- 部下の指導・育成に対する責任は?
- コンプライアンス遵守や安全管理に関する責任は?
● 権限の明確化:
- 各役職者は、どこまでの範囲で意思決定できるのか?(予算執行、人事評価、業務指示など)
- どのレベルの承認が必要か?(稟議規程などとの整合性)
- 部下に対して、どのような指示・命令ができるのか?
● 指示命令系統の確立:
- 報告・連絡・相談(ホウレンソウ)のルートを明確にする。
- マトリックス組織を採用する場合は、機能マネージャーとプロジェクトマネージャーの指示系統のルールを明確にする。(例:業務の進め方は機能マネージャー、プロジェクトの納期や仕様はプロジェクトマネージャーが指示するなど)
責任と権限のバランスを取ることが重要です。責任だけ重くて権限がない、あるいは権限だけ大きくて責任が伴わない、といった状況は、組織の機能不全を招きます。特に中小企業では、社長や一部の役員に権限が集中しがちですが、現場に近い管理職へ適切に権限を委譲することで、意思決定の迅速化と、管理職の育成につながります。これらの内容は、「職務権限規程」などの文書に明記し、全従業員に周知することが望ましいです。
ステップ5:部門間連携を促進する仕組みづくり
多品種少量生産の工場運営を円滑に進めるためには、部門間のスムーズな連携が不可欠です。
組織図を作成するだけでなく、実際に部門間の壁を取り払い、協力体制を築くための「仕組み」を導入することが重要になります。
● 情報共有の仕組み:
- 部門横断的な定例会議(生産会議、開発会議など)の設定と、効果的な運営ルールの策定。
- 社内SNS、ビジネスチャットツール、グループウェアなどのITツールを活用したリアルタイムな情報共有。
- 生産管理システムやERPなどを導入し、各部門が必要な情報(生産計画、在庫状況、工程進捗など)をリアルタイムに参照できる環境の整備。
● 連携プロセスの明確化:
- 新製品開発プロセスにおける各部門の役割と連携手順のルール化。
- 設計変更や仕様変更が発生した場合の連絡・調整プロセスの明確化。
- 品質問題発生時の原因究明と対策における関連部門の協力体制の構築。
● 部門横断的な目標設定と評価:
- 部門ごとの目標だけでなく、工場全体や製品・プロジェクト単位での共通目標を設定し、部門間の協力を促す。
- 人事評価において、自部門の成果だけでなく、他部門への貢献度や連携姿勢も評価項目に加える。
● ジョブローテーションや部門交流:
- 定期的なジョブローテーションにより、従業員が他部門の業務や課題を理解する機会を作る。
- 部門合同の研修や懇親会などを実施し、部門間の相互理解と人間関係の構築を促進する。
これらの仕組みは、組織図という「ハード」面だけでなく、組織文化や従業員の意識といった「ソフト」面での改革も伴います。トップが率先して部門連携の重要性を説き、成功体験を積み重ねていくことが、連携を促進する文化を醸成する上で重要です。
ステップ6:定期的な見直しと改善サイクルの確立
工場の組織図は、一度作ったら終わりではありません。企業の成長段階、事業環境の変化、技術の進展、新たに出てきた課題などに対応して、定期的に見直し、改善していく必要があります。組織も生き物であり、常に変化に対応していくことが求められます。
● 効果測定と評価:
- 新しい組織体制が、当初設定した目標(生産性向上、リードタイム短縮など)に対して、どのような効果をもたらしたかを定期的に測定・評価する。
- 従業員アンケートやヒアリングを通じて、新しい組織体制に対する意見や課題を収集する。
● 定期的な見直し:
- 少なくとも年に1回程度、経営層や管理職が集まり、組織体制の有効性をレビューする機会を設ける。
- 市場環境や競合の動向、自社の経営戦略の変化などを踏まえ、組織体制が現状に適しているかを確認する。
● 改善の実行:
- 見直しによって明らかになった課題や改善点について、具体的な対策を検討し、実行に移す。
- 組織図の修正だけでなく、役割分担、権限、連携の仕組みなども必要に応じて見直す。
● PDCAサイクルの確立:
- 組織体制に関しても、Plan(計画:組織設計)→ Do(実行:新体制導入)→ Check(評価:効果測定)→ Act(改善:見直し・修正)のPDCAサイクルを回していく意識を持つ。
組織改革には、時間と労力がかかります。すぐに完璧な組織ができるわけではありません。大切なのは、常に「より良い組織とは何か」を問い続け、試行錯誤しながら改善を続けていく姿勢です。この継続的な改善プロセスこそが、変化に強く、持続的に成長できる組織を作り上げる鍵となります。
工場の組織体制が「原価管理」の成否を分ける!その理由とは?
ここまで、工場の組織図の種類や作成方法について解説してきました。適切な組織体制を構築することは、生産効率の向上や意思決定の迅速化に不可欠ですが、実は「原価管理」の精度と効果にも極めて大きな影響を与えるのです。
組織体制と原価管理は、いわば車の両輪であり、どちらか一方だけがうまく機能していても、企業の収益力を最大化することはできません。
ここでは、なぜ組織体制が原価管理の成否を分けるのか、その理由を掘り下げていきます。
組織構造が原価計算の精度に与える影響
原価管理の基礎となるのは、製品やサービスにかかるコストを正確に把握する「原価計算」です。
どこで、何に、どれだけのコストが発生しているのかを正確に把握できなければ、有効なコスト削減策を打つことはできません。そして、この原価計算の精度は、工場の組織構造に大きく左右されます。
例えば、機能別組織の場合、各部門(製造部、技術部、品質管理部など)で発生した費用(労務費、経費など)は比較的把握しやすいでしょう。しかし、ある特定の製品を作るために、これらの部門がどれだけ関与し、どれだけのコストが発生したのかを正確に把握するのは難しくなることがあります。特に、間接費(各部門に共通でかかる費用や、管理部門の費用など)を、どの製品に、どのような基準で配賦(割り振る)するかが課題となります。配賦基準が曖昧だったり、実態と乖離していたりすると、製品ごとの原価が不正確になり、正しい収益性分析や価格設定ができなくなります。
一方、製品別組織(事業部制)であれば、製品群ごとに費用が集計されるため、製品別の原価や収益性は把握しやすくなります。
しかし、各事業部で共通して利用する設備や間接部門のコストを、どのように各事業部に配賦するかが課題となる点は同様です。また、機能が重複している場合、組織全体で見た場合のコスト効率が悪化している可能性も考慮しなければなりません。
マトリックス組織の場合は、さらに複雑になります。従業員が複数のプロジェクトや製品に関与するため、特定の製品やプロジェクトにどれだけの工数(労務費)がかかったのかを正確に把握するための仕組み(工数管理システムなど)が不可欠です。これができていないと、プロジェクトごとの原価計算が非常に困難になります。
このように、どのような組織構造を採用するかによって、原価情報の収集単位や集計方法、間接費の配賦方法などが影響を受け、結果として原価計算の精度が変わってくるのです。したがって、原価管理を効果的に行うためには、自社の組織構造に合った、精度の高い原価計算ができる仕組みを構築することが大前提となります。組織図を設計する段階から、原価情報をどのように収集・集計するかを考慮に入れておくことが重要です。
部門間の連携不足が引き起こすコスト増のリスク
工場のコストは、単一の部門だけで発生するわけではありません。
設計、購買、製造、検査、出荷といった一連のプロセスに関わる複数の部門の活動が積み重なって、最終的な製品原価が構成されます。
そのため、部門間の連携が不足していると、様々な形で無駄なコストが発生するリスクが高まります。
例えば、以下のようなケースが考えられます。
- 設計部門と製造部門の連携不足: 設計部門が、製造現場の実情(設備能力、作業者のスキルなど)を考慮せずに、加工が難しい、あるいは特殊な部品が必要な設計をしてしまうと、製造工程での手戻り、不良品の発生、作業時間の増加などを招き、製造コストが増大します。
- 営業部門と生産管理部門の連携不足: 営業部門が、生産現場のキャパシティやリードタイムを考慮せずに無理な納期で受注してしまうと、生産計画の混乱、残業時間の増加、特急対応による追加コストなどが発生します。
- 製造部門と品質保証部門の連携不足: 製造工程での問題点や品質に関する情報が品質保証部門に迅速に伝わらないと、不良の早期発見や原因究明が遅れ、手直しコストや最悪の場合は市場でのクレーム対応コストが発生します。
- 購買部門と設計・製造部門の連携不足: 購買部門がコスト削減のみを追求し、安価だが品質の安定しない部品を調達してしまうと、製造工程での不良増加や、製品の信頼性低下につながる可能性があります。
これらの問題は、機能別組織における「部門間の壁」や、縦割り意識が強い組織で特に起こりやすいと言えます。各部門が自部門の効率や目標達成のみを追求し、工場全体の最適化という視点が欠けていると、部門間の情報共有や協力が滞り、結果として目に見えないコスト(機会損失を含む)が膨らんでしまうのです。
効果的な原価管理とは、単に各部門で発生したコストを集計するだけでなく、プロセス全体を俯瞰し、部門間の連携を通じてコスト削減の機会を見つけ出す活動でもあります。そのためには、組織図上での連携体制の構築はもちろん、部門間のコミュニケーションを促進する仕組みや文化の醸成が不可欠です。
責任の所在が不明確だと原価削減が進まない
コスト削減活動を継続的に進めていくためには、「誰が、どのコストに対して責任を持つのか」が明確になっている必要があります。
責任の所在が曖昧なままでは、コスト削減の目標設定や、具体的なアクションプランの実行、そしてその結果に対する評価が難しくなり、活動が形骸化してしまう可能性が高まります。
組織図において、各部門や役職の役割と責任が明確に定義されていることは、原価管理の観点からも非常に重要です。
例えば、
- 材料費の削減目標に対する責任は、購買部門長と設計部門長にあるのか?
- 労務費(作業時間)の削減目標に対する責任は、製造部門長にあるのか?
- 不良率削減によるコスト削減目標に対する責任は、品質保証部門長と製造部門長にあるのか?
- ●間接費(消耗品費、光熱費など)の削減目標は、各部門長が負うのか、それとも管理部門が一括して管理するのか?
このように、コスト項目ごとに、その発生をコントロールできる立場にある部門や役職者に、明確な責任と目標を与えることが重要です。そして、その目標達成度合いを定期的に評価し、フィードバックする仕組みが必要です。
私が支援したある中小製造業では、以前は工場全体のコスト削減目標を掲げるだけで、各部門の具体的な責任が曖昧でした。
そのため、「誰かがやってくれるだろう」「自分の部門だけ頑張っても仕方ない」といった意識が蔓延し、なかなかコスト削減が進みませんでした。
そこで、組織体制の見直しと同時に、部門別の原価計算を導入し、各部門長に担当コスト項目に関する明確な削減目標と責任を与えました。
さらに、月次の業績会議で各部門の目標達成状況を共有し、優れた取り組みを発表する場を設けたところ、部門長の当事者意識が高まり、現場を巻き込んだ具体的な改善活動が次々と生まれるようになりました。結果として、工場全体のコストが大幅に削減されたのです。
組織図は、単なる体制図ではなく、責任分担の明確化を通じて、原価管理を含む経営目標達成のための実行力を高めるためのツールでもあるのです。
多品種少量生産における「原価管理」の重要ポイント
多品種少量生産は、顧客の個別ニーズに対応できる柔軟性が強みですが、一方で製品の種類が多く、生産量が少ないため、原価管理が複雑になりがちです。
画一的な量産品とは異なり、製品ごとに材料費、加工時間、段取り時間などが大きく異なるため、どんぶり勘定では、どの製品が本当に儲かっているのか、どこにコスト削減の余地があるのかを見極めることが困難になります。ここでは、多品種少量生産の特性を踏まえた上で、原価管理を効果的に進めるための重要なポイントを解説します。
正確な変動費・固定費の把握が第一歩
原価管理の基本は、まずコストを「変動費」と「固定費」に正しく分類し、それぞれを正確に把握することから始まります。
- 変動費: 生産量や販売量の増減に比例して変動するコスト。多品種少量生産においては、主に直接材料費や、製品加工に直接関わる作業者の直接労務費、外注加工費などが該当します。製品の種類によって単価や使用量が異なるため、製品ごとに正確に集計することが重要です。
- 固定費: 生産量や販売量の増減に関わらず、一定期間、比較的一定額が発生するコスト。工場の減価償却費、機械のリース料、間接部門の人件費、地代家賃、水道光熱費などが該当します。多品種少量生産では、段取り替えの回数が多いため、段取り作業にかかる労務費も固定費的な性格を帯びることがあります(生産量に関わらず段取りは発生するため)。
なぜこの分類が重要かというと、損益分岐点分析や限界利益(売上高-変動費)の計算に不可欠だからです。限界利益は、固定費を回収し、利益を生み出す源泉となります。
多品種少量生産では、製品ごとに限界利益率が大きく異なることがよくあります。どの製品がより多くの限界利益を生み出しているかを把握することで、受注の優先順位付け、価格設定、 利益の出にくい製品の見直しといった戦略的な意思決定が可能になります。
例えば、売上高は高いけれど、変動費も高く、限界利益率が低い製品ばかりを受注していると、いくら忙しくても利益は増えません。
逆に、売上高はそれほど高くなくても、限界利益率が高い製品の比率を高めることで、全体の収益性を改善できます。
変動費と固定費を正確に把握するためには、勘定科目の設定を見直し、費用が発生した際に適切に仕訳できるルールを整備する必要があります。また、労務費については、直接作業時間と間接作業時間(段取り、準備、待ち時間など)を分けて記録するなど、より詳細なデータ収集が必要になる場合もあります。
個別原価計算など、生産形態に適した計算方法の選択
原価計算の方法には、大きく分けて「総合原価計算」と「個別原価計算」があります。
- 総合原価計算: 同じ仕様の製品を大量に連続生産する場合に適した方法。一定期間に発生した総製造費用を、その期間に生産した製品数量で割り、製品1単位あたりの平均原価を計算します。
- 個別原価計算: 顧客からの注文に応じて、仕様の異なる製品を個別に生産する場合に適した方法。特定の注文(製造指図書)ごとに、直接材料費、直接労務費、製造間接費を集計し、その注文にかかった原価を個別に計算します。
多品種少量生産においては、製品ごとに仕様や製造工程、コスト構造が異なるため、原則として「個別原価計算」が適しています。 個別原価計算を行うことで、製品ごと、あるいは受注ごとの正確な原価を把握でき、それぞれの採算性を評価することが可能になります。
個別原価計算を導入するためには、以下の準備が必要です。
-
1. 製造指図書の発行: 受注ごと、あるいは生産ロットごとに製造指図書を発行し、固有の番号を付与します。
- 直接材料費: 製造指図書に基づいて出庫された材料の費用を、その指図書に紐付けて集計します。
- 直接労務費: 各作業者が、どの製造指図書の作業に、どれだけの時間従事したかを記録し(作業時間報告書や工数管理システムなどを使用)、その時間に基づいて労務費を計算し、指図書に紐付けて集計します。
- 工場全体で発生した製造間接費(直接材料費・直接労務費以外の製造費用)を集計します。
- 製造間接費を各製造指図書に配賦するための適切な配賦基準(直接作業時間、機械稼働時間、直接材料費など)を設定します。
- 設定した配賦基準に基づいて計算した配賦率(例:1時間あたり〇円)を用いて、各製造指図書に製造間接費を配賦します。
2. 直接費の賦課:
3. 製造間接費の配賦:
製造間接費の配賦は、個別原価計算において最も難しく、かつ精度に影響を与える部分です。配賦基準の選択が不適切だと、製品原価が歪められてしまう可能性があります。
例えば、労働集約的な製品と設備集約的な製品が混在している場合に、一律に直接作業時間基準で配賦すると、設備を多く使う製品の原価が過小評価され、労働集約的な製品の原価が過大評価される、といったことが起こり得ます。
近年では、より精度の高い原価計算手法として「活動基準原価計算(ABC: Activity-Based Costing)」も注目されています。ABCは、コスト発生の原因となる「活動(アクティビティ)」に着目し、製品が各活動をどれだけ消費したかに基づいてコストを配賦する方法です。導入には手間がかかりますが、特に間接費の割合が大きい場合に、より実態に近い原価計算が可能になります。
自社の生産形態や製品特性、管理レベルに合わせて、最適な原価計算方法を選択し、運用していくことが重要です。
標準原価と実際原価の差異分析による問題点の特定
原価管理の目的は、単に発生したコスト(実際原価)を集計するだけではありません。目標とすべきコスト(標準原価)を設定し、実際原価との差異を分析することで、コスト管理上の問題点を発見し、改善につなげることが重要です。
- ● 標準原価: 製品を製造するために、科学的・統計的な調査に基づいて、目標として設定される原価。材料の標準使用量や標準単価、作業の標準時間、製造間接費の標準配賦率などから計算されます。効率的な作業が行われた場合の「あるべきコスト」を示します。
- ● 実際原価: 実際に製品製造にかかった原価。
- ● 原価差異: 標準原価と実際原価の差額。この差異を分析することで、コストが目標から乖離した原因を探ることができます。
原価差異は、主に以下の要素に分解して分析されます。
● 材料費差異:
- 価格差異: 材料の実際の購入単価が標準単価と異なったことによる差異。
- 数量差異: 材料の実際の使用量が標準使用量と異なったことによる差異。(歩留まりの悪化、仕損じなど)
● 労務費差異:
- 賃率差異: 実際の作業者の賃率が標準賃率と異なったことによる差異。
- 時間差異(能率差異): 実際の作業時間が標準作業時間と異なったことによる差異。(作業効率の低下、段取り時間の超過など)
● 製造間接費差異:
- 予算差異: 実際の製造間接費発生額が、予算額(標準配賦率×実際操業度)と異なったことによる差異。(経費の使いすぎなど)
- 能率差異: 実際の作業時間(または機械稼働時間)が、生産量に見合った標準時間と異なったことによる差異。(労務費の時間差異と同様の原因)
- 操業度差異: 実際の操業度(作業時間や生産量)が、予算策定時の基準操業度と異なったことによる差異。(設備の遊休、生産計画の未達など)
これらの差異を定期的に計算し、特にマイナス(不利差異)が大きい項目について、その原因を深掘りしていくことが、コスト削減の具体的なアクションにつながります。「なぜ材料を多く使ってしまったのか?」「なぜ作業時間が標準より長くなったのか?」といった問いを立て、現場の状況を確認し、真の原因を特定します。
例えば、材料費の数量差異が大きい場合、原因は「材料の品質が悪かった」「作業者のミスが多かった」「機械の調子が悪かった」など、様々考えられます。原因に応じて、購買部門、製造部門、設備保全部門などが連携して対策を講じる必要があります。
標準原価の設定は、現実的に達成可能なレベルにすることが重要です。高すぎる目標は現場のモチベーションを下げ、低すぎる目標は改善意欲を削ぎます。定期的に標準原価を見直し、現場の実態に合わせて更新していくことも大切です。
継続的な改善活動(PDCA)によるコスト削減
原価差異分析によって問題点が特定できたら、それを具体的な改善活動につなげ、継続的に取り組んでいくことが最も重要です。原価管理は、一度仕組みを作ったら終わりではなく、PDCAサイクル(Plan-Do-Check-Act)を回し続けることで、初めて効果を発揮します。
1. Plan(計画):
- 原価差異分析の結果に基づき、コスト削減の目標を設定する。
- 目標達成のための具体的な改善策を立案する。(作業手順の見直し、治具の導入、不良削減活動、仕入先との価格交渉など)
- 担当者、期限、実施方法などを明確にする。
2. Do(実行):
- 計画に基づいて改善策を実行する。
- 実行状況を記録し、関係者間で情報を共有する。
3. Check(評価):
- 改善策の実施後、コストが目標通りに削減されたか、原価差異が改善されたかを測定・評価する。
- 期待通りの効果が出なかった場合は、その原因を分析する。
4. Act(改善):
このPDCAサイクルを、工場全体、部門、あるいは個々の工程レベルで、継続的に回していくことが、持続的なコスト削減と収益性向上につながります。
特に多品種少量生産の現場では、変化が常態です。新しい製品、新しい材料、新しい工程が次々と導入される中で、常にコスト構造も変化します。
そのため、一度確立した標準原価や改善策が、いつまでも有効とは限りません。 定期的な見直しと、変化に対応した柔軟な改善活動が不可欠なのです。
原価管理は、経理部門だけの仕事ではありません。設計、購買、製造、品質保証、営業といった、製品に関わるすべての部門が、コスト意識を持って日々の業務に取り組み、改善活動に参加することが成功の鍵となります。そのためにも、各部門の役割と責任を明確にした組織体制と、部門間の円滑な連携が、ここでも重要になってくるのです。
組織体制を活かす!製造業における原価管理の進め方6ステップ
これまで見てきたように、工場の組織体制と原価管理は密接に関連しています。効果的な原価管理を進めるためには、組織体制を前提とし、それを活かす形でステップを踏んでいくことが重要です。ここでは、特に多品種少量生産を行う中小製造業を念頭に、組織体制と連携させながら原価管理を導入・推進するための具体的な6つのステップを、提供された記事の内容も踏まえながら解説します。
ステップ1:組織目標と連動した原価管理目標の設定
原価管理は、単にコストを把握・削減すること自体が目的ではありません。企業の経営目標や、各部門に与えられた組織目標を達成するための手段として位置づける必要があります。したがって、最初のステップは、全社的な経営戦略や、組織図で定められた各部門の役割・目標と連動する形で、原価管理の具体的な目標を設定することです。
● 全社目標との連動:
- 例えば、全社的な利益率向上目標がある場合、それを達成するために、工場全体でどれだけのコスト削減を目指すのか、具体的な目標値を設定します。(例:製造原価率を〇%削減する)
- リードタイム短縮が経営目標であれば、それに伴うコスト(仕掛在庫削減、特急対応費削減など)の目標も設定します。
● 部門目標との連動:
- 組織図で定められた各部門のミッションやKPIと連携させます。
- 製造部門:「生産性向上による労務費〇%削減」「不良率削減による材料費・手直し工数削減」
- 購買部門:「材料単価の〇%引き下げ」「サプライヤーとの連携による調達リードタイム短縮」
- 技術部門:「設計標準化による部品点数削減」「歩留まり改善につながる工程設計」
- 品質保証部門:「検査効率向上による検査工数削減」「市場クレーム削減による対応コスト削減」
● 目標の具体性・測定可能性:
- 目標は、「コスト意識を高める」といった曖昧なものではなく、「〇〇費を〇%削減する」「製品Aの原価を〇円引き下げる」など、**具体的で測定可能な指標(KPI)**で設定します。
- 達成期限も明確にします。(例:年度末までに、来期末までに)
このステップでは、経営層が明確な方針を示し、各部門長と目標を共有し、合意形成を図ることが重要です。組織全体で「何のために原価管理に取り組むのか」という目的意識を共有することで、後のステップへのモチベーションが高まります。設定した目標は、組織図上の各部門・役職の責任範囲と整合性が取れている必要があります。
ステップ2:各部門の役割に応じた原価情報の収集と現状把握
次に、設定した目標に対する現状を把握するために、必要な原価情報を収集・集計する仕組みを構築します。この際、組織図で定められた各部門の役割と責任範囲に応じて、どのような情報を、どの部門が、どのように収集・報告するのかを明確に定義することが重要です。
● 収集すべき原価情報の特定:
- 目標達成度を測るために必要なコスト項目は何か?(材料費、労務費、経費、外注費など)
- 製品別、部門別、工程別、あるいは製造指図書別など、どの単位で原価情報を把握する必要があるか?(多品種少量生産では、個別原価計算に基づき、製造指図書別の原価把握が基本)
- 変動費と固定費を区別して把握する必要があるか?
● データ収集方法と担当部門の明確化:
- 直接材料費: どの部門が、どの伝票(出庫伝票など)に基づいて、どの製造指図書に紐付けて集計するか?(購買部門、資材管理部門、製造部門など)
- 直接労務費: どの部門の作業者が、どのように作業時間を記録し(作業日報、工数管理システムなど)、どの部門が集計して製造指図書に紐付けるか?(製造部門、生産管理部門、経理部門など)
- 製造間接費: どの部門が発生させた経費を、どのように集計するか?(各部門、経理部門)
● 現状の原価構造の把握:
- 収集したデータに基づき、現状の製品別原価、部門別原価、費目別原価構成などを分析し、「見える化」します。
- どの製品の収益性が高い(低い)のか?
- どの部門、どの工程でコストが多く発生しているのか?
- コスト構造における問題点や課題は何か?
このステップでは、経理部門だけでなく、製造現場、生産管理、購買など、関連する全部門が協力する必要があります。特に、作業時間の記録や材料使用量の正確な報告などは、現場の協力なしには成り立ちません。なぜこれらの情報が必要なのか、目的を丁寧に説明し、理解を得ることが重要です。また、既存の生産管理システムや会計システムを活用したり、必要であれば新たなITツール(工数管理ツール、原価計算ソフトなど)の導入を検討したりすることも有効です。組織体制によっては、原価管理専任の担当者やチームを設置することも考えられます。
ステップ3:実現可能な標準原価(目標原価)の設定
現状の原価(実際原価)を把握したら、次に**目指すべきコスト水準である「標準原価」**を設定します。標準原価は、コスト削減活動のベンチマークとなり、差異分析を通じて改善点を見つけ出すための重要な指標です。
● 標準原価の設定方法:
- 科学的・工学的手法: 製品の設計図、部品表(BOM)、工程表(作業手順書)などに基づき、必要な材料の標準使用量、標準作業時間などを設定します。IE(インダストリアル・エンジニアリング)の手法を用いて、作業分析を行い、標準時間を設定することも有効です。
- 過去の実績データの分析: 過去の実際原価データの中から、効率的に生産できた時期の実績値や平均値などを参考に、目標値を設定します。
- 見積原価の活用: 受注時の見積原価を、目標とすべき原価として設定する方法もあります。
● 設定する項目:
- 直接材料費: 標準単価 × 標準使用量
- 直接労務費: 標準賃率 × 標準作業時間
- 製造間接費: 標準配賦率 × 標準操業度(標準作業時間など)
● 部門連携による設定:
- 標準原価の設定は、経理部門だけで行うのではなく、関連部門と協力して行うことが重要です。
- 標準使用量や標準作業時間の設定には、設計部門や製造部門、生産技術部門の知見が必要です。
- 標準単価の設定には、購買部門の協力が必要です。
- 製造間接費の標準配賦率の計算には、工場全体の予算や生産計画を考慮する必要があります。
● 実現可能性と目標達成意欲のバランス:
- 設定する標準原価は、現場の努力によって達成可能な、現実的なレベルであることが重要です。あまりに厳しい目標は、現場の士気を低下させます。
- 一方で、現状維持レベルの甘い目標では、改善意欲が湧きません。現状よりも少し高いレベルの、挑戦しがいのある目標を設定することが望ましいでしょう。
- 標準原価は固定的なものではなく、定期的に見直し、改善の進捗に合わせて更新していく必要があります。
標準原価を設定するプロセス自体が、各部門の担当者にコスト意識を持たせ、目標達成へのコミットメントを高める効果があります。組織図上の役割分担に基づき、各部門が責任を持って標準値の設定に関与することが重要です。
ステップ4:部門ごとの実際原価の正確な集計
標準原価が設定されたら、次は実際に発生したコスト(実際原価)を、標準原価と比較できる形で、正確に集計する仕組みを運用していきます。ステップ2で構築した原価情報収集の仕組みを、継続的に回していく段階です。
● 正確性の確保:
- 材料の出庫記録、作業時間の報告、経費の計上などが、正確かつタイムリーに行われているかを継続的にチェックします。入力ミスや報告漏れがあると、実際原価の信頼性が損なわれます。
- 現場の作業者に対して、正確なデータ入力の重要性を繰り返し伝え、教育することが必要です。ツールの使いやすさなども改善を検討します。
● 集計単位:
- 個別原価計算に基づき、製造指図書ごとに直接材料費、直接労務費、製造間接費を集計します。
- さらに、部門別、費目別にも集計し、多角的な分析ができるようにします。
● 集計タイミング:
- 月次など、定期的に実際原価を集計し、標準原価との比較を行えるようにします。問題の早期発見のためには、より短いサイクル(週次など)での集計が望ましい場合もあります。
● システム化の検討:
- 手作業での集計は、手間がかかり、ミスも発生しやすいため、生産管理システム、ERP、原価計算ソフトなどのITシステムを活用し、効率的かつ正確な集計プロセスを構築することが望ましいです。
- バーコードやRFIDなどを活用して、材料使用量や作業時間を自動的に記録する仕組みを導入することも有効です。
このステップでは、経理部門と現場部門(製造、生産管理など)の連携が特に重要になります。経理部門は、現場から上がってくるデータが正確かを確認し、現場部門は、日々の活動を正しく記録・報告する責任があります。組織として、正確な原価データを収集・集計する文化を醸成していくことが求められます。
ステップ5:組織全体で差異原因を分析し、課題を共有
実際原価が集計できたら、いよいよ標準原価と比較し、その差異(原価差異)を計算・分析します。そして、その分析結果を特定の部門だけでなく、組織全体で共有し、コストに関する課題認識を合わせることが重要です。
● 原価差異の計算:
- 材料費差異(価格差異、数量差異)、労務費差異(賃率差異、時間差異)、製造間接費差異(予算差異、能率差異、操業度差異)などを計算します。
- 製品別、部門別、原因別に差異を把握します。
● 差異原因の分析(深掘り):
- なぜ差異が発生したのか? その具体的な原因を特定します。単に「作業効率が悪かった」だけでなく、「なぜ効率が悪かったのか?(例:新人作業者が多かった、機械の故障が頻発した、指示が不明確だった)」まで掘り下げます。
- 分析には、現場へのヒアリングや、関連データ(生産実績、品質データ、設備稼働記録など)の確認が不可欠です。
- 責任部門の特定だけでなく、部門間の連携に起因する問題がないかも検討します。(例:設計変更の連絡遅れが、材料手配の遅れと高値購入につながった、など)
● 課題の共有:
- 分析結果と特定された課題を、定例の生産会議や業績会議などの場で、関連する全部門(経営層、管理職、現場リーダーなど)に共有します。
- グラフや表を用いて、**分かりやすく「見える化」**することが重要です。
- 単に結果を報告するだけでなく、課題に対する共通認識を持ち、解決に向けた当事者意識を醸成する場とします。
このステップは、原価管理を「管理会計」として機能させるための核心部分です。差異分析の結果は、単なる過去の記録ではなく、未来の改善活動につなげるための重要な情報源となります。組織全体で課題を共有することで、部門の壁を越えた協力体制が生まれやすくなります。組織図上の報告ラインを活用し、分析結果が経営層まで適切に報告され、意思決定に活かされる仕組みを確立することも重要です。
ステップ6:部門連携による具体的な改善策の立案と実行
最後のステップは、差異分析によって明らかになった課題に対して、具体的な改善策を立案し、実行に移すことです。そして、その実行にあたっては、原因が特定の部門にあったとしても、関連する部門が連携して取り組むことが、より効果的な成果につながります。
● 改善策の立案:
- 特定された差異原因に対して、具体的で実行可能な改善策を検討します。
- 短期的に実施できる対策(作業手順の見直し、5S活動の徹底など)と、中長期的に取り組むべき対策(設備投資、システム導入、人材育成計画など)を分けて考えます。
- 改善策の担当部門・担当者、実施期限、期待される効果(目標値)を明確にします。
● 部門連携による実行:
- 例えば、材料の数量差異(使いすぎ)が大きい場合、製造部門だけでなく、**設計部門(歩留まり改善設計)、購買部門(材料品質の安定化)、品質保証部門(不良原因の特定と対策)**などが連携して改善に取り組みます。
- 労務費の時間差異(作業効率低下)が大きい場合、製造部門だけでなく、**生産技術部門(工程改善、治具開発)、生産管理部門(生産計画の平準化)、人事部門(スキルアップ研修)**などが協力します。
● 改善活動の推進体制:
- 部門横断的な改善テーマについては、プロジェクトチームを組成することも有効です(マトリックス組織の考え方)。
- 改善活動の進捗状況を定期的にフォローアップし、必要に応じて計画を修正します。
- 成功事例は積極的に共有し、他の部門や製品にも展開(横展開)します。
● PDCAサイクルの継続:
- 改善策の実行後、その効果を測定・評価し(Check)、さらなる改善につなげる(Act)という、原価管理におけるPDCAサイクルを継続的に回していきます。
このステップを確実に実行し、継続していくためには、経営トップの強いリーダーシップと、改善活動を奨励する組織文化が不可欠です。失敗を恐れずに挑戦できる雰囲気や、改善提案を積極的に吸い上げる仕組み、成果を上げた部門や個人を適切に評価する制度なども、活動を後押しします。
このように、組織体制を活かし、部門間の連携を前提とした6つのステップを踏むことで、原価管理は単なるコスト集計にとどまらず、企業の収益力強化と持続的成長を実現するための強力な経営管理ツールとなるのです。
まとめ
本記事では、多品種少量生産を行う中小製造業の皆様に向けて、「工場の組織図」と「原価管理」という二つの重要なテーマについて、その重要性、種類、作成・導入方法、そして両者を連携させることの効果と具体的な進め方を、事例を交えながら詳しく解説してきました。
工場の組織図は、単なる形式的なものではなく、企業の戦略を実現し、複雑化する生産プロセスを効率的に運営するための「設計図」です。機能別、製品別、マトリックス型といった種類があり、それぞれにメリット・デメリットがありますが、中小製造業においては、自社の状況に合わせて要素を組み合わせたハイブリッド型の組織が有効な場合が多いことを説明しました。そして、効果的な組織図を作成するためには、現状分析、目標設定、部門設計、責任・権限の明確化、連携の仕組みづくり、定期的な見直しというステップを踏むことが重要です。
一方、原価管理は、企業の収益性を左右する重要な経営管理手法です。特に多品種少量生産においては、**変動費・固定費の正確な把握、個別原価計算などの適切な計算方法の選択、標準原価と実際原価の差異分析、そして継続的な改善活動(PDCA)**がポイントとなります。
そして、この記事で最も強調したかったのは、「組織体制」と「原価管理」は決して切り離して考えるべきではないということです。
- 組織構造は、原価計算の精度や情報収集のあり方に影響を与えます。
- 部門間の連携不足は、見えないコスト増を招きます。
- 責任の所在が不明確な組織では、コスト削減は進みません。
逆に言えば、適切に設計された組織体制は、効果的な原価管理の実行を強力に後押しします。 各部門の役割と責任が明確であれば、コスト削減目標の設定や実行がしやすくなります。部門間の連携がスムーズであれば、プロセス全体の視点から無駄を発見し、改善につなげることができます。
私たちは、組織体制を活かした原価管理の進め方として、以下の6つのステップを提案しました。
- 1. 組織目標と連動した原価管理目標の設定
- 2. 各部門の役割に応じた原価情報の収集と現状把握
- 3. 実現可能な標準原価(目標原価)の設定
- 4. 部門ごとの実際原価の正確な集計
- 5. 組織全体で差異原因を分析し、課題を共有
- 6. 部門連携による具体的な改善策の立案と実行
これらのステップを、自社の組織体制と連携させながら着実に実行していくことで、原価管理は単なるコスト把握にとどまらず、生産性の向上、リードタイムの短縮、品質の向上、そして最終的な利益の最大化に貢献する強力な武器となります。
ご紹介したB社の事例のように、組織改革と原価管理改善に同時に取り組み、V字回復を果たした企業は決して少なくありません。変化の激しい時代において、多品種少量生産という強みを活かし、持続的に成長していくためには、自社の足元を見つめ直し、戦略的な組織運営と、精緻な原価管理の両輪をしっかりと回していくことが不可欠です。
この記事が、皆様の会社の組織体制や原価管理のあり方を見直すきっかけとなり、より強く、収益性の高い工場づくりに向けた具体的なアクションにつながれば、これほど嬉しいことはありません。
もし、自社だけでの取り組みに難しさを感じていらっしゃる場合は、ぜひ私たちのような専門家の活用もご検討ください。皆様の状況に合わせた最適な組織設計と原価管理体制の構築を、全力でサポートさせていただきます。
関連記事
【最新版】工場の組織図を徹底解説!種類・作成方法・事例を紹介 (業種別・会社規模別)
https://smart-factory.funaisoken.co.jp/250210-2/
製造業必見! 6つのステップで解説!原価管理の取り組み方とは?
https://smart-factory.funaisoken.co.jp/220714/
原価企画とは?【徹底解説】初心者でもわかる目的・進め方・成功の秘訣集
https://smart-factory.funaisoken.co.jp/250324-4/