記事公開日:2022.07.14
最終更新日:2024.04.12
製造業必見! 6つのステップで解説!原価管理の取り組み方とは?
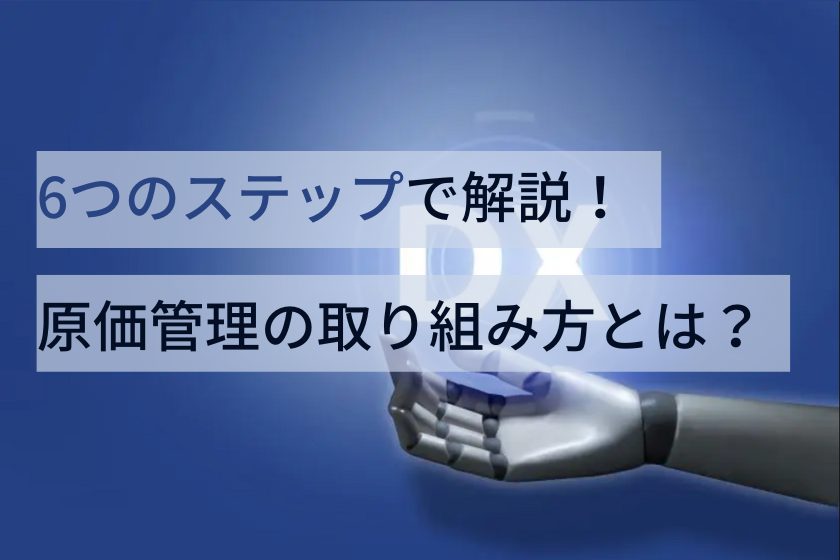
日々製造業の企業様とコミュニケーションをとる中で、ここ最近毎日のように話題に上がるのが「原材料の高騰」というキーワードです。
原材料費が高騰する中で、企業が自社だけで出来ることは適切な原価管理を通じた原価低減しかありません。
弊社のコラムでも何度も取り上げておりますが、今回は製造業が取り組むべき原価管理について、6つのステップで解説いたします。
ステップ0:原価管理の目的を明確にする
原価管理を進めるにあたって、最も重要なことは「何のために原価管理を行うのか」という目的を明確にすることです。
目的が不明確なままプロジェクトを開始しても、どんな情報を収集する必要があるかがぶれてしまい、原価管理を達成できなくなります。
よくある原価管理の目的としては、下記のような事項が挙げられます。
- 損益分岐点を明らかにして、現在の利益を把握するため
- 製品別個別原価を把握して注力商品を見つけやすくするため
- 直接原価計算といった原価分析を実施し、社内改善箇所を明確にするため
- 工程別設備別分析を行い、損失が出ている工程や設備を見つけて改善活動をするため
ステップ1:標準単価の設定
原価管理の目的を明確化したら、次は標準原価の設定を行います。
製造業の場合、3つの切り口で標準単価(=製造原価)を設定する必要があります。
①材料費:製造に必要となる部品の単価など
②労務費:製造に関連する従業員の賃金(チャージ)など
③経費:①・②以外で工場維持に必要な賃料、電気代など
標準単価を設定したら、実際のデータを取得するフェーズに移行します。
次に具体的な取得方法を解説します。
ステップ2:データの取得
先に示した通り、標準単価を設定したら、実際のデータを入力・取得するフェーズに移行します。
具体的には、ステップ1で設定した標準原価に対応する形で実績のデータを取得します。
それぞれの費用に対して必要になるデータ・情報としては下記が挙げられます。
①材料費:BOM(部品構成表)、材料の購買単価リスト
②労務費:時間チャージ、工程別製造実績時間
③経費:工場全体の賃料、機械毎稼働時間(機械単位で費用を按分するため)
製造業の場合に特に重要なのは、②労務費に関して「改善したい単位に工程を分けて実績を取得する」ということです。
段取りも含めてピッキング・抜き・曲げ・溶接・組立など工程ごとに実績を取得するのか、それとも工程をある程度まとめてしまって実績をとるかなど、自社の考え方に合わせてデータ取得をすると良いでしょう。
製造業という業種では、特に労務費の実際データ取得に苦労される企業が多いです。
各工程において、どのような実績データを取得するのが良いのか?どのように取得することが現場の負担にならないか?を議論して方法を決定する必要があります。
また、取得したデータを活用するためには、生産管理システムなどの他のシステムへデータ連携することが重要です。データ連携することにより、リアルタイムで実績データを取得することができるので後述する原価計算やデータ分析において即時対応できるといったメリットがあります。
ステップ3:原価計算
データの取得ができたら、標準原価と実績原価を計算します。
標準原価に関しては、ステップ1で設定した標準単価に対して実際に使用した数量や時間数を掛け合わせます。
一方で実績原価は、実際にかかった単価に対して実績数量や時間数を掛け合わせることで算出します。
ここでは、初めからすべてを細かく複雑に計算しようとするのではなく、まずは全製品分計算できる粒度で計算することが今後のステップに向けて重要となります。
ステップ4:差異分析
原価計算の結果を受けて標準原価と実績原価の比較、つまり「差異分析」を行います。
標準原価に対して実績原価が高い場合、なぜその差が生じたのかを分析します。
例えば材料費に関して実績原価が標準原価よりも高かった場合、その原因は標準で想定していたより数量が多かったからなのか、それとも仕入単価が高かったのか等、要素を細かく分けて分析を行います。
差異分析の際には、さまざまな軸で分析結果を出すことでより正確な議論ができるようになります。
しかし、差異分析は後述の改善活動のための手段であるため、できるだけ効率したい作業です。
さまざまな軸で分析することを得意とした分析ソフトや分析ツールを選定し、改善活動の為の工数を確保することが大切です。
ステップ5:改善活動
原価管理の最後のステップとしては、改善活動があります。
ステップ4で標準原価と実績原価になぜ差異が生じているかを分析した後は、その原因を解決するための改善活動を行います。
ステップ4の例で考えると、製造工程での加工ミスにより使用数量が標準より増えたことで実績原価が高くなっていたとします。
その場合、加工ミスを減らし歩留まり率を上げる必要があるため、治具の導入などにより歩留まり率を高めるための施策に取り組むなどの改善活動が考えられます。
以上のように、原価管理は大きく6つのステップで取り組むことが一般的です。
ただ、この工程の中でも特に難しいのは「ステップ2:データの取得」だと考えます。
日々の受注をこなすことで精一杯なのに実績取得のためのオペレーションを増やすことはできない、という企業様は非常に多いです。
弊社ではそのような企業様に対して、工数取得プログラムによる実績取得の効率化や原価計算・BIツールを用いたデータ分析自動化などの事例がございます。
ご興味のある方は下記レポートなどを参考にしていただけますと幸いです。
コラム|製造業必見!原価管理をエクセルで行う方法とそのメリット・デメリット
コラム|中小製造業こそ取り組むべき!個別原価管理のススメ
コラム|製造業・工場が実践すべきBIツール活用とは?成功事例も紹介
■無料ダウンロード
【製造業向け】補助金×原価管理システムの成功事例レポート
https://www.funaisoken.co.jp/dl-contents/smart-factory_smart-factory_01906_S045
目次
1、事例概要
2、当時の課題
3、取組内容
4、効果
5、補助金申請のポイント
レポートの内容
補助金を駆使した原価管理システム導入により、業務効率を向上させた製造業の事例です。
手書き日報や手動転記を排除し、リアルタイムなデータ分析を実現した今回の取組は、業務の革新と効率化を実現しました。
- どのような原価管理が良いのか?
- リアルタイムに把握するためにはどのような方法があるのか?
- 補助金はどのように活用するのが良いのか?
といった悩み事に対しての事例を一冊にまとめています。
■オンラインセミナー開催のお知らせ
「板金加工業の為の儲けの管理!」 社長セミナー
▼セミナーお申し込みはこちら▼
https://smart-factory.funaisoken.co.jp/event/
本セミナーで学べるポイント
-
従業員200名以下の板金加工・プレス・溶接加工業の社長が知っておくべき原価管理システムが分かる!
~社長の為の生産管理・原価管理システムで「見える化」する具体的な方法が分かります~ -
原価管理システムで製品別・取引先別・工程別データ化したものを経営や現場が活用できるように分析する方法がわかる!
~経営や現場が活用できるようにBIを活用してデータ分析をする方法がわかります~ -
職人・属人化している生産管理・個別原価管理業務を改善する為のシステムを導入する方法が分かる!
~一部の熟練者・職人に依存している業務にシステムを導入・活用する方法が分かります~ -
基礎知識や導入経験がない社長でも個別原価をデータ化してデータ経営する方法がわかります。
~生産・購買・在庫・原価をシステムで統合的する方法が良く分からない…そんな社長の為のセミナーです~ -
個別原価を可視化する事で何が儲かっているのか?儲かっていないのか?が明確になりその具体的な対策が分かる!
~理論・理屈ではなく、自社の現場で実践できるやり方が分かります~
開催は残り2回!オンライン開催となります。
2022/07/26 (火) 13:00~15:00
2022/07/28 (木) 13:00~15:00
お申し込みはこちらから⇒
このセミナーは終了しました。最新のセミナーはこちらから。
https://smart-factory.funaisoken.co.jp/event/