記事公開日:2025.04.28
最終更新日:2025.05.08
中小製造業の未来モデル!有川製作所の自動化による企業変革コラム
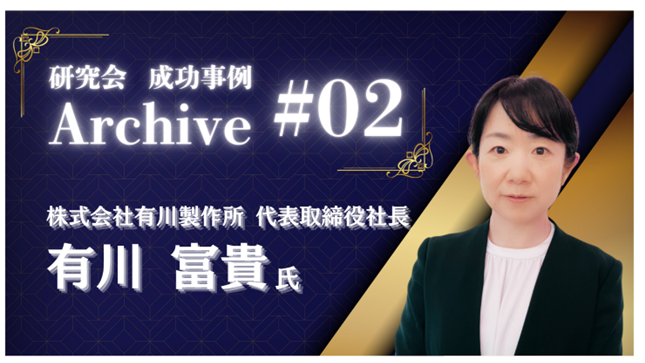
人手不足・小ロット多品種の壁を打ち破る!自動化で生産性と働きがいを両立し、DXへと進化を遂げた成功の秘訣を公開します。
このコラムをお勧めしたい経営者の皆様
- 深刻化する人手不足に対応し、持続的な成長を目指している経営者様
- 小ロット多品種生産における生産性向上に課題を感じている経営者様
- 従業員の働きがいを高め、魅力ある企業文化を醸成したい経営者様
- 自動化導入に踏み切れずにいる、あるいは導入効果に悩んでいる経営者様
- 自動化を起点としたDX(デジタルトランスフォーメーション)に関心のある経営者様
このコラムの内容の要約
本コラムは、石川県に拠点を置く中小製造業、株式会社有川製作所の自動化への挑戦とその成果を解説するものです。同社は、深刻化する人手不足や小ロット多品種生産という課題に対し、「小人の靴屋プロジェクト」と銘打った自動化に着手。協調ロボットの導入と内製化、そして徹底した人材育成により、プレス工程や検査工程の生産性を大幅に向上させました。その結果、2年連続の残業ゼロ達成、従業員の働きがい向上、若手・キャリア採用の成功といった、経営全般にわたる好循環を生み出しています。成功の背景には、スモールスタート、事前検証、外部連携、そして何よりも経営者の強いリーダーシップがありました。さらに同社は、自動化で得た知見を活かし、「巨人の肩プロジェクト」として3Dバーチャル技術やChatGPT活用といったDXにも挑戦。自動化を起点に企業価値を高め続ける同社の取り組みは、多くの中小製造業にとって未来への羅針盤となるでしょう。
このコラムを読むメリット
本コラムをお読みいただくことで、中小製造業が直面する普遍的な課題、特に人手不足や小ロット多品種生産への対応について、具体的な解決策のヒントを得ることができます。有川製作所の事例を通じて、協調ロボット導入や自動化システムの内製化といった、自動化を成功に導くための実践的なノウハウを学ぶことが可能です。また、自動化が単なる生産性向上に留まらず、従業員の働きがい向上、採用力の強化、ひいては企業文化の変革にまで繋がるプロセスを具体的に理解できます。投資対効果の考え方、スモールスタートや事前検証といった導入プロセスの要諦、そして外部リソースの活用法など、自社で自動化を検討・推進する上で不可欠な視点が得られるでしょう。さらに、アナログな自動化からデジタル技術を活用したDXへとステップアップしていく道筋を知ることで、自社の将来像を描き、具体的なアクションプランを構想する一助となります。
目次
第1章 なぜ今、自動化なのか? 中小製造業を取り巻く環境と有川製作所の挑戦
1. 中小製造業を取り巻く厳しい経営環境
現在、日本の製造業、特にその大多数を占める中小企業は、かつてない厳しい経営環境に直面しています。少子高齢化に伴う構造的な人手不足は深刻化の一途をたどり、多くの企業で受注機会の損失や既存従業員の負担増といった問題が顕在化しています。加えて、原材料価格の高騰やエネルギーコストの上昇は収益を圧迫し、価格転嫁も容易ではない状況です。
さらに、事業承継の問題も深刻です。経営者の高齢化が進む一方で、後継者が見つからない、あるいは事業の将来性への不安から承継を躊躇するケースも少なくありません。また、若い世代を中心に「働きがい」を重視する価値観が広がる中、旧態依然とした労働環境では優秀な人材の獲得・定着が困難になっています。
こうした状況を打開する鍵として期待されるのが、デジタルトランスフォーメーション(DX)です。しかし、多くの中小企業では、資金や人材、ノウハウの不足からDXへの取り組みが遅々として進んでいないのが実情です。「どこから手をつければ良いのか分からない」「導入効果が見えない」といった声も多く聞かれます。このままでは、企業間格差はますます拡大し、厳しい淘汰の時代を迎えることになりかねません。
2. 有川製作所の挑戦 – 危機感から生まれた変革への決意
このような厳しい事業環境は、石川県に拠点を置く株式会社有川製作所にとっても例外ではありませんでした。昭和15年創業、金型設計製作と金属プレス加工を主力とし、特に小ロット多品種生産において高い技術力を持つ同社もまた、人手不足という大きな課題に直面していました。熟練技術者の高齢化が進む一方で、若手人材の確保は難しく、増え続ける受注に対応しきれない場面も出始めていました。
「このままではジリ貧になる。会社を存続させ、さらに発展させていくためには、抜本的な変革が必要だ」
有川社長は強い危機感を抱いていました。現状維持は緩やかな衰退を意味します。変化に対応し、未来を切り拓くためには、従来のやり方にとらわれない新たな挑戦が不可欠でした。そこで着目したのが「自動化」です。
しかし、同社が目指したのは、単なる省人化やコスト削減ではありませんでした。自動化によって生産性を向上させることはもちろん、それ以上に、従業員が単純作業から解放され、より創造的で付加価値の高い仕事に取り組める環境を創り出すこと、そして、誰もが「この会社で働きたい」と思えるような、魅力あふれる企業へと変革することを目指したのです。
属人化していた作業を標準化し、若手でも活躍できる環境を整える。労働時間を短縮し、働きがいを高める。そして、変化に前向きな企業文化を醸成する。自動化は、これらの目標を実現するための重要な手段と位置づけられました。まさに、「モノづくりの未来を創る」という同社のビジョンを具現化するための挑戦の始まりでした。次章では、この変革への第一歩となった「小人の靴屋プロジェクト」の具体的な取り組みについて詳述します。
第2章 「小人の靴屋プロジェクト」始動 – 協調ロボット導入と内製化への道
1. プロジェクト発足 – 小ロット多品種の壁に挑む
有川製作所の自動化への挑戦は、「小人の靴屋プロジェクト」と名付けられました。これは、グリム童話『小人の靴屋』のように、「寝ている間に仕事が進んでいる」状態を目指すという想いが込められています。人手不足という課題に対し、自動化によって24時間稼働に近い体制を構築し、生産性を飛躍的に向上させようという意欲的な取り組みです。
プロジェクトの最初のターゲットとなったのは、プレス工程と検査工程でした。プレス工程は、まさに同社の主力事業でありながら、人手不足の影響を直接的に受けていました。一方、検査工程は、製品の品質を担保する重要な工程であるものの、人による作業のため負担が大きく、ボトルネックとなりやすい状況でした。これらの工程を自動化することが、生産性向上と従業員の負担軽減に直結すると判断されたのです。
しかし、有川製作所が得意とする小ロット多品種生産は、従来の産業用ロボットによる自動化には不向きとされてきました。品種ごとに段取り替えが必要となり、その手間とコストを考えると、自動化のメリットを享受しにくいと考えられていたためです。この「常識」を打ち破るために、同社が着目したのが「協調ロボット」でした。
2. 協調ロボットという選択肢
協調ロボットは、従来の産業用ロボットと比較して、いくつかの大きなメリットがあります。まず、安全柵なしで人と隣り合って作業できる安全性の高さです。これにより、限られたスペースでも導入しやすく、既存の生産ラインにも柔軟に組み込むことが可能です。また、プログラミングや操作が比較的容易であるため、専門のロボットエンジニアでなくても扱うことができる点も魅力でした。
さらに重要なのは、その柔軟性です。多様な製品に対応するためのハンド(ロボットの手先)交換や、品種ごとの動作プログラム変更が比較的容易に行えるため、小ロット多品種生産への適性が高いのです。有川製作所は、この協調ロボットの特性を活かせば、自社の生産体制に合った自動化が実現できると考えました。
もちろん、導入は決して平坦な道のりではありませんでした。最適なロボットや周辺機器の選定、効果的なシステム構成の検討、そして実際の導入と立ち上げには、多くの試行錯誤が必要でした。ここで大きな力となったのが、技術商社である山崎電機や、ロボットメーカーであるオムロンといった外部パートナーとの連携でした。彼らの専門的な知見やサポートを得ながら、一つひとつの課題を乗り越えていきました。
3. 内製化への挑戦 – 自動化を自社の力に
自動化システムを導入する上で、有川製作所が特に重視したのが「内製化」です。システムインテグレーター(SIer)に全てを任せるのではなく、可能な限り自社の従業員の手でシステム構築や改善を行える体制を目指したのです。
内製化には、いくつかの大きなメリットがあります。第一に、トラブル発生時の迅速な対応が可能になることです。外部業者に依頼すると時間もコストもかかりますが、社内に対応できる人材がいれば、ダウンタイムを最小限に抑えられます。第二に、生産品目の変更や改善要求に対して、柔軟かつスピーディーに対応できることです。自分たちでシステムを改変できれば、外部に頼ることなく、継続的な改善活動が可能になります。
そして第三に、最も重要なのが、ノウハウの蓄積と人材育成です。自動化システムの構築・運用を通じて、従業員はロボット技術やプログラミング、システム設計に関する知識・スキルを習得します。これは、単に自動化を進めるだけでなく、従業員の多能工化やスキルアップ、ひいては会社全体の技術力向上に繋がります。
有川製作所では、ポリテクセンター(石川職業能力開発促進センター)が提供する研修プログラムを積極的に活用したり、社内でのOJT(On-the-Job Training)を通じて、ゼロからロボットを扱える人材を育成しました。当初は「自分たちにできるだろうか」という不安もあったと言いますが、経営陣の強い後押しと、挑戦を奨励する風土の中で、従業員は着実にスキルを身につけていきました。この内製化への取り組みが、後に大きな成果を生む原動力となります。
第3章 自動化がもたらした変革 – 生産性向上、残業ゼロ、そして働きがい
1. 目に見える成果 – 生産性と品質の劇的向上
「小人の靴屋プロジェクト」による自動化の導入は、有川製作所に目覚ましい成果をもたらしました。まず、定量的な効果として、生産性が大幅に向上しました。プレス工程では、協調ロボットによる24時間稼働も視野に入れた自動化により、生産能力が従来比で9%向上。検査工程においても、ロボットと画像検査システムを組み合わせることで、検査能力が22%向上しました。これは、単に人手不足を補うだけでなく、企業の成長エンジンとなる生産能力の増強を実現したことを意味します。
さらに特筆すべきは、2年連続で「残業ゼロ」を達成したことです。自動化によって生まれた時間的な余裕は、従業員の負担軽減に直結しました。長時間労働が常態化しやすい製造業において、これは画期的な成果と言えるでしょう。
品質面でも大きな改善が見られました。自動化により作業のばらつきがなくなり、製品品質が安定しました。特に検査工程では、従来の人間の目による官能検査から、画像検査システムによる数値的なデータに基づいた検査へと移行したことで、検査精度が向上し、顧客からの信頼も高まりました。
2. 働く人に起きた変化 – 働きがいと成長実感
自動化のインパクトは、生産性や品質といった数値的な指標にとどまりません。むしろ、働く人々の意識や働き方にこそ、より大きな変化が表れたと言えます。
これまで単純作業や負担の大きな作業に従事していた従業員は、自動化によってそれらの業務から解放され、より付加価値の高い仕事、例えば、自動化設備の運用管理、改善活動、新たな技術の習得などに時間を割けるようになりました。これは、従業員のスキルアップと多能工化を促進し、「やらされ仕事」から「自ら考え、工夫する仕事」へと、仕事の質そのものを変えるきっかけとなりました。
こうした変化は、従業員の「働きがい」の向上に直結します。自分の仕事が会社の成長に貢献しているという実感、新しいスキルを習得する喜び、そして自らの手で職場をより良くしていく達成感。これらが、従業員のモチベーションを高め、組織全体の活性化に繋がっていきました。
さらに、自動化への先進的な取り組みや「残業ゼロ」といった魅力的な労働環境は、採用活動にも好影響を与えました。製造業、特に地方の中小企業では採用難が叫ばれる中、有川製作所には意欲ある若手人材やキャリア人材が集まるようになり、実際に6名の若手と2名のキャリア採用に成功しています。また、社内でゼロから育成したシステムエンジニア(SE)が2名誕生するなど、人材育成の面でも着実な成果を上げています。
3. 企業文化の変容 – 未来への期待感が醸成
自動化プロジェクトの成功体験は、有川製作所の企業文化にもポジティブな影響を与えました。「自分たちでもできる」「やれば変わる」という自信が社内に広がり、変化に対する前向きな姿勢、新しいことに挑戦しようという意欲が醸成されていったのです。
経営陣と従業員の間でのコミュニケーションも活発になり、一体感が高まりました。自動化という共通の目標に向かって協力し、困難を乗り越えた経験が、組織としての結束力を強めたと言えるでしょう。
社外からの評価も高まりました。先進的な取り組みはメディアにも取り上げられ、多くの企業から視察や講演の依頼が舞い込むようになりました。これは、従業員の誇りを高めるとともに、企業のブランドイメージ向上にも大きく貢献しています。
このように、有川製作所の自動化は、単なる設備投資ではなく、生産性、品質、コストといった経営指標の改善はもちろんのこと、従業員の働きがい、人材育成、採用力強化、そして企業文化の変革といった、組織全体の進化を促す起爆剤となったのです。
第4章 成功の秘訣 – スモールスタート、人材育成、そして経営者の覚悟
有川製作所の自動化プロジェクトが大きな成功を収めた背景には、いくつかの重要な成功要因が存在します。これらは、同様の課題を抱える多くの中小製造業にとって、貴重な示唆を与えてくれるものです。
1. 「まずやってみる」精神と徹底した事前検証
自動化導入には、不安がつきものです。「本当に効果があるのか」「投資に見合うのか」「自分たちに使いこなせるのか」。有川製作所も例外ではありませんでした。しかし、同社は「まずやってみる」という精神で、最初から大規模な投資に踏み切るのではなく、比較的小規模で実現可能性の高いところから着手する「スモールスタート」を選択しました。
具体的には、プレス工程と検査工程という、効果が見えやすく、かつ自社の技術で対応できそうな範囲から始めました。そして、導入前には徹底した事前検証を行いました。例えば、検査工程の自動化では、実際にカメラテストを繰り返し行い、要求される精度が出せるかを確認。また、ワーク(加工対象物)をロボットが確実に掴めるかどうかの「バラ積み検証」なども実施しました。これにより、導入後のリスクを最小限に抑え、「これならいける」という確信を持ってプロジェクトを進めることができたのです。
2. 多面的な視点での投資対効果判断
自動化への投資判断において、単純な「省人化効果=人件費削減効果」だけでROI(投資収益率)を計算してしまうと、多くの場合、「投資対効果が見合わない」という結論になりがちです。特に、協調ロボットなどは、従来の産業用ロボットほどの高速性を求められないケースもあり、単純なタクトタイム短縮効果だけでは投資回収が難しい場合があります。
しかし、有川製作所では、投資対効果をより多面的に捉えました。生産能力向上による売上増への貢献、品質安定化による不良率低減や顧客信頼向上、労働環境改善による従業員の定着率向上や採用コスト削減、そして何よりも、従業員の働きがい向上やスキルアップといった、数値化しにくい「見えない効果」も考慮に入れたのです。
もちろん、定量的な評価も重要です。プレス自動化の投資回収期間は当初6.1年と試算されましたが、補助金を活用することで4.0年に短縮できる見込みとなりました。このように、利用可能な制度を最大限活用しつつ、短期的なコスト削減効果だけでなく、中長期的な企業価値向上に繋がるかどうかという視点で投資判断を行うことが、自動化成功の鍵となります。
3. 内製化と外部連携の戦略的な使い分け
前述の通り、有川製作所は自動化システムの「内製化」に積極的に取り組みました。しかし、全てを自社だけで賄おうとしたわけではありません。自社の強み・弱みを冷静に分析し、コアとなる部分は内製化を目指しつつ、専門的な知識や技術が必要な部分、あるいは一時的にリソースが不足する部分については、外部パートナーとの連携を効果的に活用しました。
技術商社である山崎電機は、最新の技術動向や製品情報を提供し、最適なシステム構成の提案を支援。ロボットメーカーのオムロンは、技術的なサポートやトレーニングを提供。ポリテクセンターは、社員向けの研修プログラムを提供しました。こうした外部の知見やリソースを戦略的に活用することで、自社だけでは乗り越えられなかったであろう壁を突破し、プロジェクトを加速させることができたのです。
4. 人こそが主役 – 徹底した人材育成
自動化システムを導入しても、それを使いこなし、改善していくのは「人」です。有川製作所は、自動化プロジェクトの開始当初から、人材育成を最重要課題の一つと位置づけていました。
重要なのは、単に操作方法を教えるだけでなく、「なぜ自動化に取り組むのか」「自動化によって何を目指すのか」という目的意識を経営者自らが繰り返し伝え、従業員と共有することです。これにより、従業員は自動化を「自分ごと」として捉え、主体的に関わるようになります。
また、失敗を恐れずに挑戦できる環境づくりも不可欠です。トライ&エラーを奨励し、たとえ失敗しても、そこから学び、次に活かすことを評価する文化を醸成しました。外部研修への参加や資格取得支援など、学びの機会も積極的に提供しました。こうした地道な取り組みが、従業員のスキル向上とモチベーション維持に繋がり、結果として2名のSEを育成するという大きな成果を生み出したのです。
5. 経営者の覚悟とリーダーシップ
これら全ての成功要因の根底にあるのは、有川社長の強いリーダーシップと「会社を変える」という覚悟です。「モノづくりの未来を創る」という明確なビジョンを掲げ、自動化プロジェクトを自ら牽引し、その意義や進捗状況を社内外に積極的に発信し続けました。時には、導入に際して生じる不安や疑問に対して、粘り強く対話を重ね、従業員の理解と協力を得ていきました。
経営者が明確な方向性を示し、本気で取り組む姿勢を見せること。それが、従業員の意識を変え、組織全体を動かす原動力となるのです。有川製作所の事例は、自動化プロジェクトの成否は、技術や設備だけでなく、経営者の覚悟とリーダーシップに大きく左右されることを改めて示しています。
第5章 「巨人の肩プロジェクト」へ – 自動化からDXへ、未来を創る挑戦
1. 「小人の靴屋」から「巨人の肩」へ – 新たなステージへの進化
有川製作所の挑戦は、「小人の靴屋プロジェクト」によるアナログ工程の自動化だけにとどまりません。自動化によって得られた成果と自信を土台に、同社は次なるステージ、すなわちデジタルトランスフォーメーション(DX)による本格的なデジタルイノベーションへと歩みを進めています。その取り組みが「巨人の肩プロジェクト」です。
このプロジェクト名は、「先人(巨人)の知恵や実績(肩)の上に立つことで、より遠くまで見渡せる」という言葉に由来します。「小人の靴屋プロジェクト」で培った自動化技術やノウハウ、そして挑戦する企業文化という「肩」の上に立ち、AIや3D、IoTといった最先端のデジタル技術を活用することで、これまでにない新たな価値を創造し、モノづくりの未来を切り拓こうという意欲的な試みです。
なぜ、アナログの自動化の次にDXが必要なのでしょうか。それは、個別の工程を自動化するだけでは、その効果は限定的であり、企業全体の競争力を抜本的に高めるには限界があるからです。製造現場で生成される様々なデータを収集・分析・活用し、設計から生産、検査、さらには経営判断に至るまで、バリューチェーン全体をデジタルで繋ぎ、最適化していくこと。そして、デジタル技術を駆使して、従来にはなかった新しい製品やサービス、ビジネスモデルを生み出していくこと。これこそが、DXの本質であり、持続的な成長を実現するための鍵となります。
2. 企業間連携によるDXの加速 – 3DバーチャルとChatGPT活用
「巨人の肩プロジェクト」における具体的な取り組みとして、注目すべきは、外部企業との積極的な連携によるDXの推進です。自社だけのリソースに固執せず、優れた技術やアイデアを持つ他社と協業することで、よりスピーディーかつ効果的にDXを実現しようとしています。
その一つが、3Dバーチャル技術を活用した事業です。airoo合同会社とフォア株式会社との連携により、自社の工場やオフィスをリアルに再現した3Dバーチャル空間を構築しました。これにより、遠隔地にいる顧客や就職希望者に対して、臨場感あふれる工場見学や会社説明を提供することが可能になります。将来的には、この仮想空間を活用した研修や、製品のバーチャル展示、さらには新たなeコマース展開なども視野に入れています。これは、単なる技術導入に留まらず、マーケティングや人材採用、教育といった企業活動全般をデジタルで変革しようとする試みです。
もう一つの注目すべき取り組みが、ChatGPTとOffice365を連携させた業務改善アプリケーションの開発です。これは、DX支援プラットフォームを提供する株式会社INDUSTRIAL-X、DXコンサルティングを行うナカタケテック株式会社との共同プロジェクトとして進められています。従来は紙ベースで行われていた作業報告や日報作成などを、対話型AIであるChatGPTを活用してデジタル化・効率化することを目指しています。これにより、従業員の事務作業負担を軽減するとともに、蓄積されたデータを分析し、さらなる業務改善やノウハウの共有、技術伝承に繋げていくことが期待されます。
3. 自動化・DXが拓く「未来のモノづくり」
これらの先進的な取り組みは、有川製作所が目指す「未来のモノづくり」の姿を具体的に示しています。それは、単に効率化・省人化された工場ではなく、デジタル技術を駆使することで、人がより創造性を発揮し、新たな価値を生み出すことができる工場です。
自動化された生産ラインが効率的に製品を生み出す一方で、従業員はAIやデータの支援を受けながら、より高度な改善活動や新製品開発、顧客との価値共創といった業務に注力する。仮想空間と現実空間が融合し、時間や場所の制約を超えて、多様な人材が連携し、イノベーションを創出する。有川製作所の挑戦は、そのような未来のモノづくりへの確かな一歩と言えるでしょう。
重要なのは、これらの取り組みが、決して大企業だけのものではないということです。有川製作所は、従業員30名規模の中小企業でありながら、明確なビジョンと強い意志、そして柔軟な発想と実行力によって、自動化、そしてDXへの道を切り拓いています。その根底には、「小人の靴屋プロジェクト」を通じて培われた「自分たちで未来を創る」という自信と、内製化によって蓄積された技術力があります。
有川製作所の事例は、多くの中小製造業にとって、自動化・DXは決して遠い未来の話ではなく、今すぐ取り組むべき喫緊の課題であり、そして大きなチャンスでもあることを示唆しています。変化を恐れず、未来への一歩を踏み出すこと。その先にこそ、持続的な成長と発展の道が拓けているのです。
このコラムを読んだ後に取るべき行動
今回の有川製作所の事例は、自動化やDXが、単なる技術トレンドではなく、中小製造業が厳しい経営環境を乗り越え、持続的な成長を実現するための強力な武器となり得ることを示しています。この貴重な学びを自社の経営に活かしていただくために、コラムをお読み頂いた経営者の皆様に、ぜひ取っていただきたい行動を以下に提案いたします。
1. 自社の課題と自動化・DXの可能性を再認識する:
- まずは、自社が抱える本質的な課題(人手不足、生産性、品質、コスト、働きがい、採用、事業承継など)を改めて洗い出してください。
- その上で、有川製作所の事例を参考に、どの課題に対して自動化やデジタル技術が有効な解決策となり得るか、具体的な可能性を探ってみましょう。固定観念にとらわれず、柔軟な発想で検討することが重要です。
2. 情報収集を積極的に行う:
- 自動化やDXに関する情報は日々進化しています。関連するセミナーへの参加、展示会への視察、専門書籍の購読などを通じて、最新の技術動向や他社の成功事例、利用可能な支援策などについて、積極的に情報を収集してください。
3. スモールスタートできる領域を探す:
- 最初から大規模な投資や全社的な改革を目指す必要はありません。有川製作所のように、比較的小さな範囲、例えば特定の工程や業務から、低リスクで始められる自動化・デジタル化がないか検討してみましょう。「まずやってみる」ことが重要です。
4. 信頼できるパートナーを見つける:
- 自社だけですべてを解決しようとせず、外部の専門家の知見やサポートを積極的に活用しましょう。技術商社、SIer、ロボットメーカー、コンサルタントなど、自社の状況や目的に合った信頼できるパートナーを見つけることが、成功への近道です。
5. 経営者自身が変革の旗手となる:
- 自動化・DXは、単なる設備導入やシステム導入ではありません。企業文化や働き方そのものを変える、全社的な取り組みです。経営者自身が強いリーダーシップを発揮し、明確なビジョンを示し、変革への強い意志を持って社内を牽引していくことが不可欠です。従業員との対話を重ね、理解と協力を得ながら、一丸となって取り組む姿勢が求められます。
これらの行動を通じて、皆様の会社が、有川製作所のように、変化を乗り越え、魅力あふれる企業へと進化されることを、私ども船井総合研究所としても心より願っております。ご不明な点や具体的なご相談がございましたら、いつでもお気軽にお声がけください。
さいごに
本コラムを最後までご覧頂きありがとうございます。
最後までお読みいただいた皆様に朗報です。
2025年06月26日 (木)
船井総研が主催するものづくり経営研究会スマートファクトリー経営部会にて有川製作所様のご登壇が決定いたしました。
今回、一度限りではございますが、無料でお試し参加のご招待をさせて頂きます。
【詳細はこちらhttps://lpsec.funaisoken.co.jp/study/smart-factory/047708/】
※お試し参加は 経営研究会の入会をご検討いただく為に 経営者のみ・初回のみ 無料でご参加いただけます。当社の判断で申し込みをお断りする場合もありますので予めご了承ください。
※座席に限りがございますので、満席の場合は別の日をご案内させていただく事がございます。予めご了承ください。
【自動化のご相談はこちら】
船井総研が提供するスマートファクトリーコンサルティング【Funai-soken Smart Factory Connection】は、製造業の生産性向上・自動化を支援し、スマートファクトリー化を実現する総合支援サービスです。
現状分析に基づき、最適なソリューション(自動化、デジタル化、生産管理システム等)をご提案。豊富なネットワークと推進力で、計画策定から効果測定まで強力にサポートします。
https://www.funaisoken.co.jp/solution/maker_smartfactory_703_S045