記事公開日:2025.05.27
最終更新日:2025.05.29
「迫る納期」「高まる要求品質」「消えゆく熟練の技」―― この三重苦から脱却し、金型づくりに革新をもたらす羅針盤
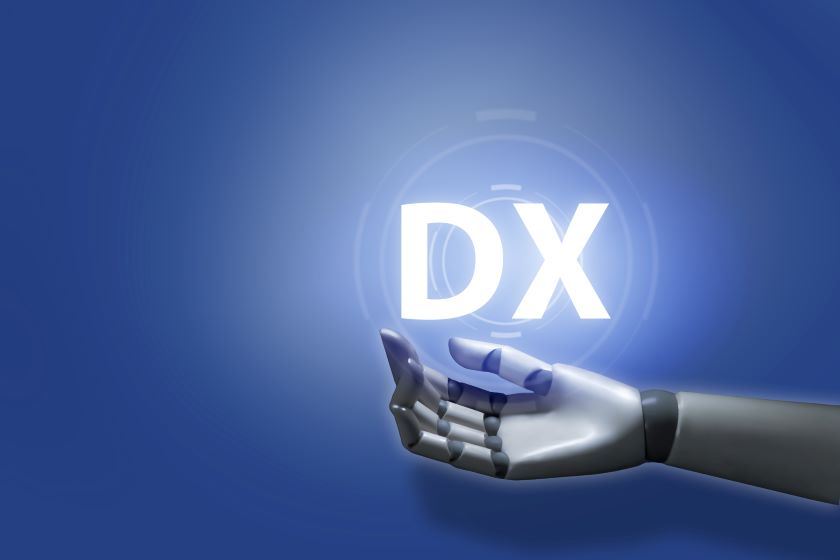
いつもコラムをご愛読いただきありがとうございます。船井総合研究所の熊谷です。
目次
「また取引先から無茶な納期短縮の連絡だ…」「この三次元曲面、ウチの山田さんじゃないと精度が出せないんだよな。でも、山田さんもあと数年で定年だ…」「若手はなかなか育たないし、かといって熟練の技は一朝一夕じゃ身につかない…」
金型製造の最前線に立つ皆様であれば、このような会話や悩みが日常茶飯事なのではないでしょうか。顧客からの要求は日に日に厳しさを増し、「より早く、より安く、そしてより高品質に」というプレッシャーは、まるで終わりのないマラソンのようです。特に、長年培われてきた熟練技術者の「匠の技」に支えられている工程が多い企業様ほど、その技術の継承や、万が一の事態を考えると、夜も眠れない日々をお過ごしかもしれません。
この、いわば「三重苦」とも言える状況を、ただ「仕方がないこと」として受け入れてしまうのでしょうか? それとも、これを変革の好機と捉え、新たな一歩を踏み出すのでしょうか?
その「日常の悩み」、放置すれば企業の存続に関わる大問題に発展しかねません
日々の業務に追われ、目の前の課題をこなすことで精一杯。それは重々承知しております。しかし、これらの課題を根本的に解決しないまま放置してしまうと、将来的には取り返しのつかない事態を招く可能性があります。
1. 「短納期対応」の限界と失注リスクの増大:
顧客の製品開発サイクルはますます短縮化され、金型への要求納期もそれに追随して厳しくなる一方です。熟練技術者の経験と勘に頼った場当たり的な対応では、いずれ限界が訪れます。突発的な仕様変更や、試作金型での予期せぬ不具合による手戻りは、貴重な時間を奪い、結果として納期遅延を引き起こします。一度失った信頼を取り戻すのは容易ではなく、最悪の場合、大切な顧客を失うことにも繋がりかねません。
2. 「品質のばらつき」が招くコスト増と信頼低下:
「ウチの品質は高い」と自負されていても、その品質が特定の熟練技術者に依存している場合、その方が不在の時や、作業者が変わった際に、微妙な品質のばらつきが生じることはありませんか? この小さなばらつきが、後工程である成形品の不良率増加に直結したり、納品後のクレームに繋がったりするのです。その対応には多大な時間とコストが費やされ、企業の収益を圧迫します。
3. 「技術伝承の断絶」という静かな時限爆弾:
金型製造の現場を支える熟練技術者の高齢化は、多くの企業が抱える深刻な問題です。彼らが持つ門外不出のノウハウや、言葉では伝えきれない「勘所」は、一朝一夕に若手に継承できるものではありません。「見て覚えろ」「技は盗め」といった旧来の育成方法では、変化の激しい現代において若手は育ちにくく、結果として貴重な技術が失われてしまう危機に瀕しています。これは、企業の競争力の源泉を失うことに他なりません。
4. 見えない「コスト競争力」の低下:
度重なる試作や修正、それに伴う材料費のロス、長時間の機械稼働によるエネルギーコストの増加、そして何よりも人的リソースの浪費…。これらは全て、最終的な金型コストに跳ね返ってきます。国内はもとより、海外の安価な金型メーカーとの競争が激化する中、このような見えないコストの積み重ねが、じわじわと貴社の競争力を削いでいるのです。
「守り」から「攻め」の経営へ。今こそ、デジタル技術を羅針盤に
「これまでも何とかやってこられたのだから」――そのお気持ちも理解できます。しかし、市場環境は刻一刻と変化しています。従来の延長線上ではない、新たなアプローチが求められているのです。その鍵を握るのが、デジタル技術の戦略的活用です。
それは、単に新しい機械を導入したり、ソフトウェアを買い揃えたりすることだけを意味するのではありません。設計から製造、検査に至るまでの全プロセスを見直し、情報を一元管理し、データを徹底的に活用することで、属人的なノウハウを形式知化し、生産性、品質、そして技術伝承のあり方を根本から変革することを目指すのです。
具体的には、以下のような取り組みが考えられます。
1.設計プロセスの革新:「バーチャル試作」で手戻りを撲滅
・3D CAD/CAMの高度連携: 単に図面を3D化するだけでなく、設計データを製造工程や検査工程でシームレスに活用できる体制を構築します。これにより、設計変更時の情報伝達ミスを防ぎ、加工プログラム作成の効率を飛躍的に向上させます。
・CAEシミュレーションの徹底活用: 経験と勘に頼っていた金型設計の妥当性検証を、コンピュータ上で事前に行います。樹脂流動解析によるウェルドラインやヒケの予測、反り変形解析による製品精度の事前確認、冷却解析による最適な冷却回路の設計など、試作金型を作る前に問題点を洗い出し、潰し込むことで、「一発OK」の金型製作を目指します。これにより、試作回数の劇的な削減、開発リードタイムの大幅短縮、そして材料費の削減が期待できます。
2.製造工程の変革:「見える化」と「標準化」で熟練の技を再現
・IoTを活用したリアルタイムな工程監視: 工作機械の稼働状況、工具の摩耗状態、加工中の温度変化といったデータをセンサーで収集し、リアルタイムに「見える化」します。これにより、異常の早期発見や予防保全が可能になるだけでなく、収集したデータを分析することで、最適な加工条件を導き出し、誰でも高品質な加工ができる「標準化」を推進できます。
・熟練技術のデジタル化と共有: 熟練技術者が持つ暗黙知を、動画マニュアルやデジタル作業手順書といった形で「形式知化」し、社内で共有します。タブレット端末などを活用し、若手技術者が作業現場で必要な情報をすぐに参照できるようにすることで、OJTの効果を高め、技術伝承を加速させます。
3.人材育成と働き方の変革:「スマートツール」で若手の即戦力化と多能工化を促進
・AIを活用した設計・加工支援システムの導入: 過去の膨大な設計データや加工実績をAIに学習させ、最適な設計パラメータの提案や、加工プログラムの自動生成などを支援するシステムを導入します。これにより、経験の浅い技術者でも、熟練者と同等レベルの業務を遂行できるようになり、早期の戦力化が期待できます。
・自動化・省人化技術の積極導入: ロボットによるワークの自動搬送・交換システムや、三次元測定器と連携した自動検査システムなどを導入することで、単純作業や繰り返し作業から人間を解放し、より付加価値の高い業務へシフトさせます。これにより、24時間稼働による生産性向上や、人手不足の解消にも繋がります。
これらの取り組みを進めた企業では、リードタイムが平均20%短縮された、不良率が半分以下に削減された、若手社員の定着率が向上し、新しい技術開発に挑戦する活気が出てきたといった声も聞かれます。これは、夢物語ではありません。正しい方向性を見据え、一歩ずつ着実に進めば、必ず実現できる未来です。
次回のセミナーでは、これらの課題解決に向けた具体的なソリューション、最新技術の動向、そして様々な企業の成功事例・失敗事例を交えながら、貴社が明日から取り組める「最初の一歩」を具体的に提示いたします。
まとめ
今回のコラムでは、金型製造業が抱える根深い課題と、その解決の方向性について、やや踏み込んでお話しさせていただきました。もし、少しでも「我が社のことだ」「何かを変えなければ」と感じていただけたのであれば、ぜひ一度、セミナー会場へ足をお運びください。そこには、貴社の未来を明るく照らすヒントが、必ずや見つかるはずです。
変革への第一歩を、私たちと一緒に踏み出しましょう。
金型製造&樹脂加工製造業向け生成AI活用セミナー
https://www.funaisoken.co.jp/seminar/129747
【第1講座 AI活用基礎:製造業がAI活用できる業務とは?】
・市場におけるAIの役割・AI動向
・中小企業だからこそ取り組むべきAI活用戦略
・AIを活用するためには、具体的に何をすれば良いのか?
・多品種少量生産製造業が実践すべきAI活用他社事例
・AI活用と原価管理の深い関係性
【第2講座 カワイ精工様登壇!従業員26名の社内DX・生成AI活用で年間1,100時間削減】
・DX取り組み前の当時のリアルな課題
・DX取り組み時の苦悩・乗り越え
・金型カルテ(実績のデジタル化)により、300時間/年削減
・IoT活用!在庫管理自動化により管理工数削減!在庫最適化を実現!
・その他IoT活用による業務改善事例
・RPA活用!部品発注作業を自動化!800時間/年削減
・製造業における生成AI活用事例
●生成AIシステム実演!
【第3講座 多品種少量生産製造業が知っておくべきAI・IoT活用戦略】
・自社データを基盤としたAI活用~”失敗しない”ためのDX経営~
・多品種少量生産の製造業が取り組むべきAI活用戦略
関連コラム
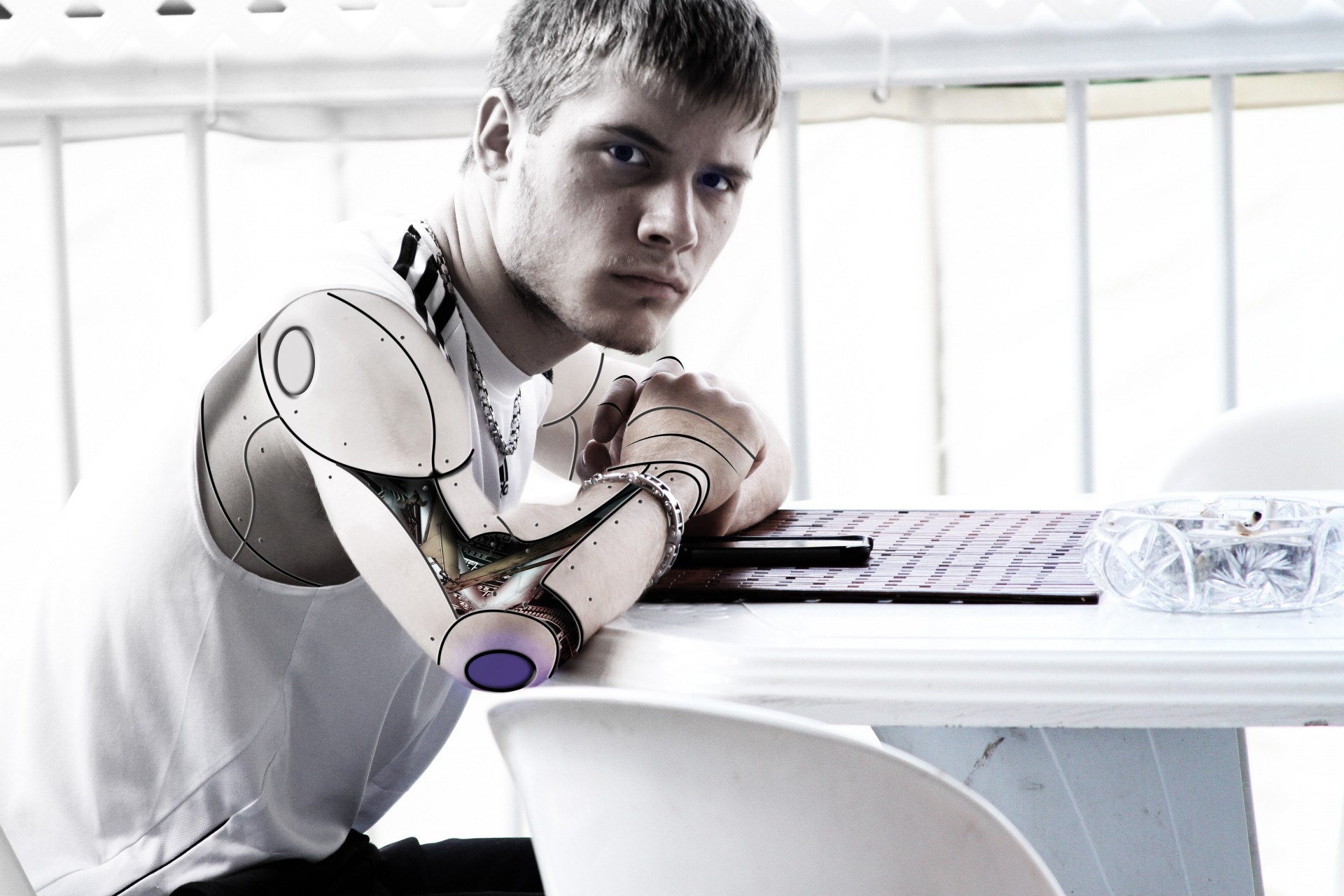
ロボットのティーチングとは?ティーチングの種類と概要を解説
2019.08.27
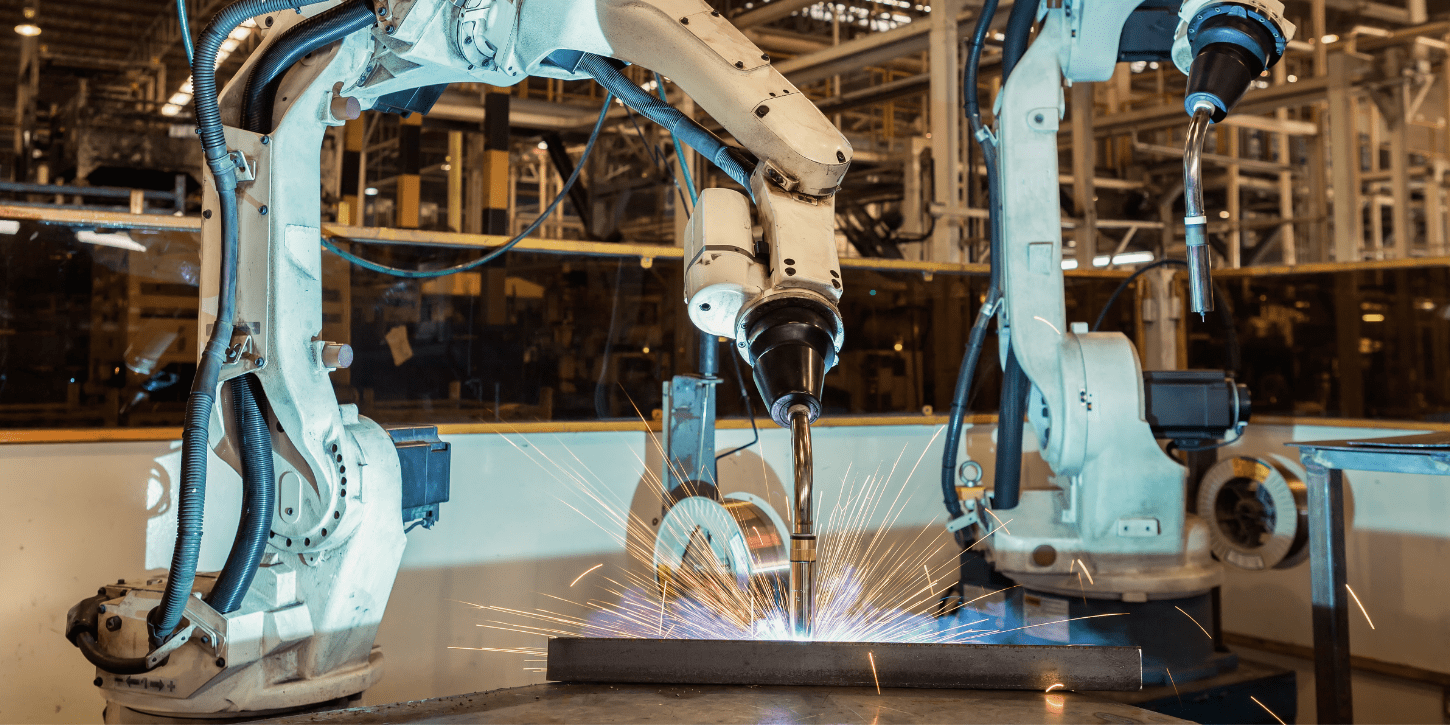
溶接ロボットで行う自動化の方法とは?
2019.08.29
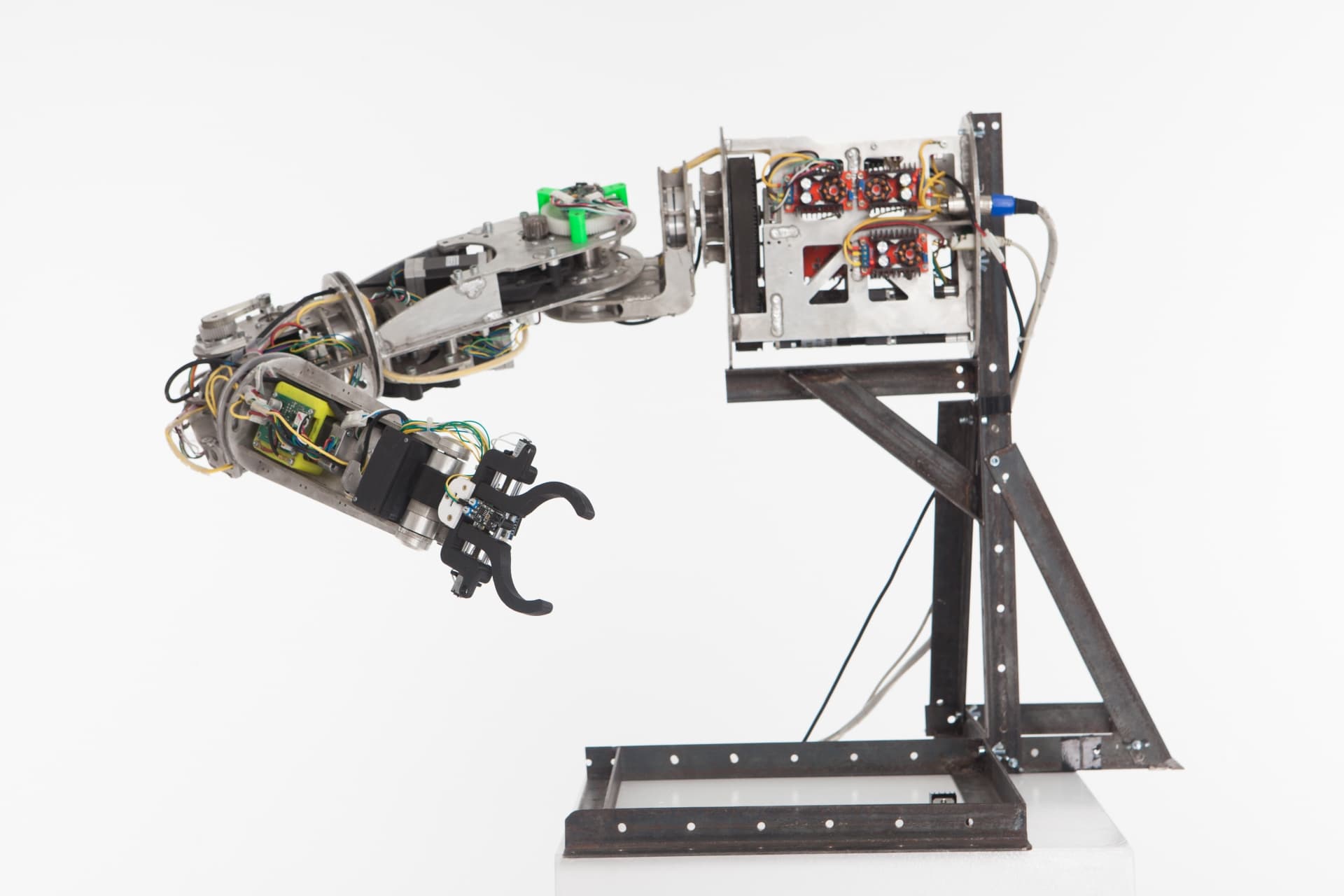
産業用ロボットとは?最新動向からロボットの違いを知る
2019.09.17