記事公開日:2024.04.22
最終更新日:2025.04.02
【生産管理システム導入の失敗例あるある】失敗しないためのコツ
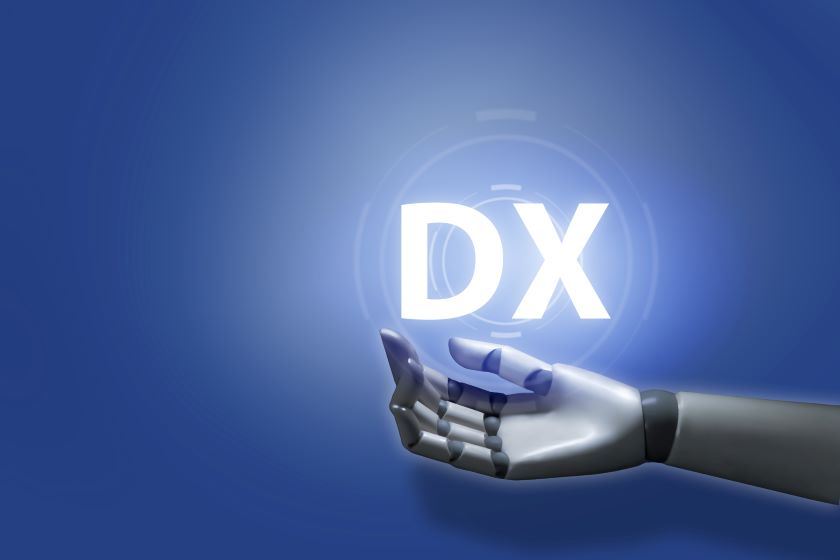
生産管理システムの導入に失敗したらどうしよう・・・ どうしたら失敗せずに生産管理システムを導入できるのだろうか、と言った不安は付き物です。
一般的には、組織のニーズと整合しないケースがあり、システムを活かしきれず無駄な時間とコストが発生することがあります。
また、ユーザーへの教育不足によりシステムの操作や活用が浸透されず導入効果を得られないことがあります。
本コラムでは、今まさに生産管理システムの導入を検討されている企業の方へ、生産管理システムの導入失敗例から
導入を失敗しないためのコツについてご紹介します。
1.生産管理システムの失敗例 3選
①業務の効率化を目的に導入したが、逆に工数が増えてしまった
よくあるケースとして、とりあえず生産管理システムを導入すれば業務の効率化が出来ると思って導入したが、自社の運用に合っていないシステムを選定してしまい、結果的に手間が増えてしまったと言う話を聞くことがあります。
その代表例として、
- 生産管理システムで生産計画がうまく立てられず、結局手作業での調整作業が増えてしまった
- 生産管理システムでは機能が賄えきれず、別で自作EXCELが増えてしまい運用が煩雑になった
結論として、合わない生産管理システムを選ぶと、想定していた機能が使えないことによる、本来しなくて良いはずの作業が生まれ、悪循環に陥る可能性も考えられます。
②高いスペックのシステムを導入したが、一部の機能しか使えていない
全ての業務を網羅できる多くの機能を持った生産管理システムを導入すれば、何でも実現できると思い込み実は自社の運用には適応していないことが判明したと言うケースがあります。
その代表例として、
- 生産計画機能
- 在庫管理機能
- 品質管理機能
そして、システムを使って対応できる業務を整理した結果、結局は一部の限られた機能しか使えないという状態に陥ります。
その結果、以下のような負荷も生じてくることがあります。
- その機能を補う別のシステムを構築する必要が生じる
- エクセルや紙帳票でのアナログな管理方法を残さざるを得なくなる
つまり、高機能だから汎用性があるとは限らず、自社にとっての高機能であるとは限りません。
やはりシステム導入以前の運用整理が重要ということになります。
③システムの操作が複雑で難しく、現場が使いこなせない
生産管理システムの操作がとても複雑で、システムに不慣れな特に現場担当者が使いこなすことが出来ず、結局は従来どおりのアナログな生産管理をしてしまうケースがあります。
その原因として実際、日常の業務が変化することで、下記の問題が起きることがあります。
- 一気にシステムで行う業務が増えることになり、操作手順を覚えられない。
- メニューやボタンがたくさんあり、それぞれの使い方を覚えられない。
- 膨大な分厚い操作マニュアルを読む気になれない。読んでも文章での説明が多く、理解ができない。
- パソコンで入力することが増えたが、そもそもパソコンに慣れていない高齢の方のストレスになった。
こういった問題の解決策のひとつに、「スモールスタート」をして徐々に慣れていくことで、新しく覚える作業も少なく、ストレス少なく浸透しやすいのが特徴です。
ここまで見てきたような失敗を起こさないためには「生産管理システムの導入を成功に導くコツ」があります。
続いて「生産管理システムの導入を成功に導くコツ」を解説します。
2.生産管理システムの導入を成功に導くコツ
①システム導入前に自社の問題点を把握する
生産管理システムの導入前に必ず、自社にどんな問題があり、どんな問題を解決したいのかのリストアップすることが重要です。
ただ、全ての問題に対応させようとすると、想定予算を大幅に上回る高額な費用が掛かる可能性があるため、必ず解決したい優先順位を決める必要があります。
②自社の運用にマッチした生産管理システムを調査し選定する
生産管理システムの機能は多種多様なため、どの生産管理システムを使えば、自社の問題を解決できるのかをしっかりと調査する必要があります。
また、1社だけで決めることはせず、自社にとって最適な生産管理システムだと確信できるまで調査をすることが重要です。
③最初の生産管理システム導入時にどの優先順位まで対応させるか決める
はじめに、解決したい問題のリストアップをして優先順位付けを行ったものを一つ一つ見直していき、実際にどの優先順位までの問題を解決できるようにするのかを決める必要があります。
なぜなら、すべてを同時に解決することができないわけではありませんが、もし全ての問題を解決できる生産管理システムを導入しようとすると、導入時のイニシャルコストが非常に高額になってしまう場合が多いためです。
また、自社の問題をすべて解決できるようになると信じていても、実際に生産管理システムを使い始めてみると不都合な部分が間違いなく出てくるため、追加のカスタマイズが必要になり、二重にコストがかかる可能性があります。
④ユーザー参加の促進と適切なトレーニングの実施
システム導入に伴うユーザーの不安や期待に耳を傾け、ユーザー参加型の導入プロセスを構築することで、ユーザーの理解を深め、意識を高めることができます。
また、導入後にはユーザーへの十分なトレーニングとサポートを行い、システムの適切な活用を支援することが重要です。ユーザーがシステムを活用するための環境を整えることが重要です。
⑤システム整合性の確保と継続的な改善実施
生産管理システムを他の業務システムやデータベースと適切に連携し、統合性を確保することで、情報の一元管理や効率的なデータ分析が可能となります。
導入後もユーザーからのフィードバックを受け入れ、システムや業務プロセスを改善するための仕組みを確立し、継続的な改善を図ることが重要です。
今回、ここでご紹介した5つのコツは、生産管理システムの導入に失敗するリスクを軽減するために、必ず行ったほうが良いことです。
何事も事前準備が大事だというように、生産管理システムも導入前準備が非常に重要です。
3.まとめ
最も重要なことは「導入テストをしっかりと行う」ことです。
生産管理システムを正しく導入できれば、工数削減や生産効率アップができ、結果的に売り上げ増加や利益率アップに繋がるので、経営という観点でも切っても切り離せない部分です。
今回ご紹介した、失敗例と同じようなことにならないためにも、事前に準備をシッカリと行っていただき、現場の声を吸い上げられる導入テストを行える生産管理システムをお選びください。
また、弊社では様々なノウハウをもとに生産管理システムの導入ご支援が可能となっておりますので、ご興味のある方はぜひご相談いただければと思います。
このコラムが皆様の工場にお役に立てれば幸いです。
最後までお読みいただきありがとうございました。
■関連するセミナーのご案内
「食品加工業の為の原価改善!」経営セミナー
セミナー詳細・申込はこちらから↓↓↓
https://www.funaisoken.co.jp/seminar/114264
従業員30~200名以下の食品加工業で生産管理&原価管理を徹底的に見直す為のシステム利用方法が分かる!
~社長の為の生産管理・原価管理システムで「見える化」する具体的な方法が分かります~
お申し込みはこちらから⇒
https://www.funaisoken.co.jp/seminar/114264
【製造業 2024年基幹システム活用時流予測レポート ~今後の見通し・業界動向・トレンド~】
国内製造業における現状とトレンド
現代の日本社会における国内製造業の特徴として、就業者数が下降傾向である一方、コロナに関係無く売上・利益ともに増加傾向を遂げていることとが挙げられます。また、2000年以降の本格的な海外展開により中堅中小企業も海外に進出していることから、今後の国内製造業において「グローバル経営」は必要不可欠となってくるでしょう。
しかし、現在の国内製造業の多くはグローバルビジネス展開に必要な真の経営ができていないことが推測できます。では、グローバルビジネス展開に必要な真の経営とはなんでしょう。企業がグローバル経営を進めるにあたって、国内外双方のデータの把握を徹底することは押さえておくべき要点となってきます。
国内製造業において高齢化・属人化・人手不足がネックとなる中、グローバル経営を進めるにはDX化による属人化・職人化の排除が不可欠です。基幹システム(ERP)の導入が有するメリットは大きく、その代表例として経営・現場データ可視化や海外拠点も含むデータ一元化などが挙げられます。国内製造業におけるDX化は利益向上につながると同時に、海外展開を進めるうえでも重要なカギとなってくるでしょう。
本レポートでは、国内製造業の現状と課題の解説に加え、DX化の現状や業務改善を伴うDX化成功のポイント、基幹システム導入の成功事例など、国内製造業を幅広く網羅しております。旧態依然とした企業経営から製造業における基幹システム(ERP)を構築・導入を試みたい、基幹システム(ERP)の活用成功事例を知りたい経営者様は是非お目通しください。
https://www.funaisoken.co.jp/dl-contents/jy-core-system_S045
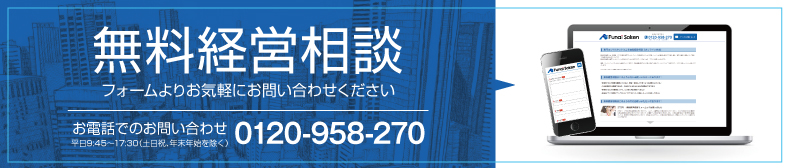
◾️この記事を書いたコンサルタント

株式会社船井総合研究所
DXコンサルティング部 リーダー
岩松 将史
全国各地の中堅・中小製造業における業務改革ならびに生産性向上支援に従事し、その実績は計30件以上。
支援先企業のDX実行計画の策定に加えて、生産工程やバックオフィス業務の調査&分析、生産性向上に向けたビジネスプロセスの抜本的な見直しを手掛ける。
また、AIやERP等のシステムベンダー選定やシステム導入に関するプロジェクトマネジメントも主導。
これまでに計20件以上のDX関連セミナー登壇実績あり。「製造業のDX」に特化した会員数50社以上の事例勉強会「船井総研 スマートファクトリー経営部会」の主宰でもある。
関連コラム
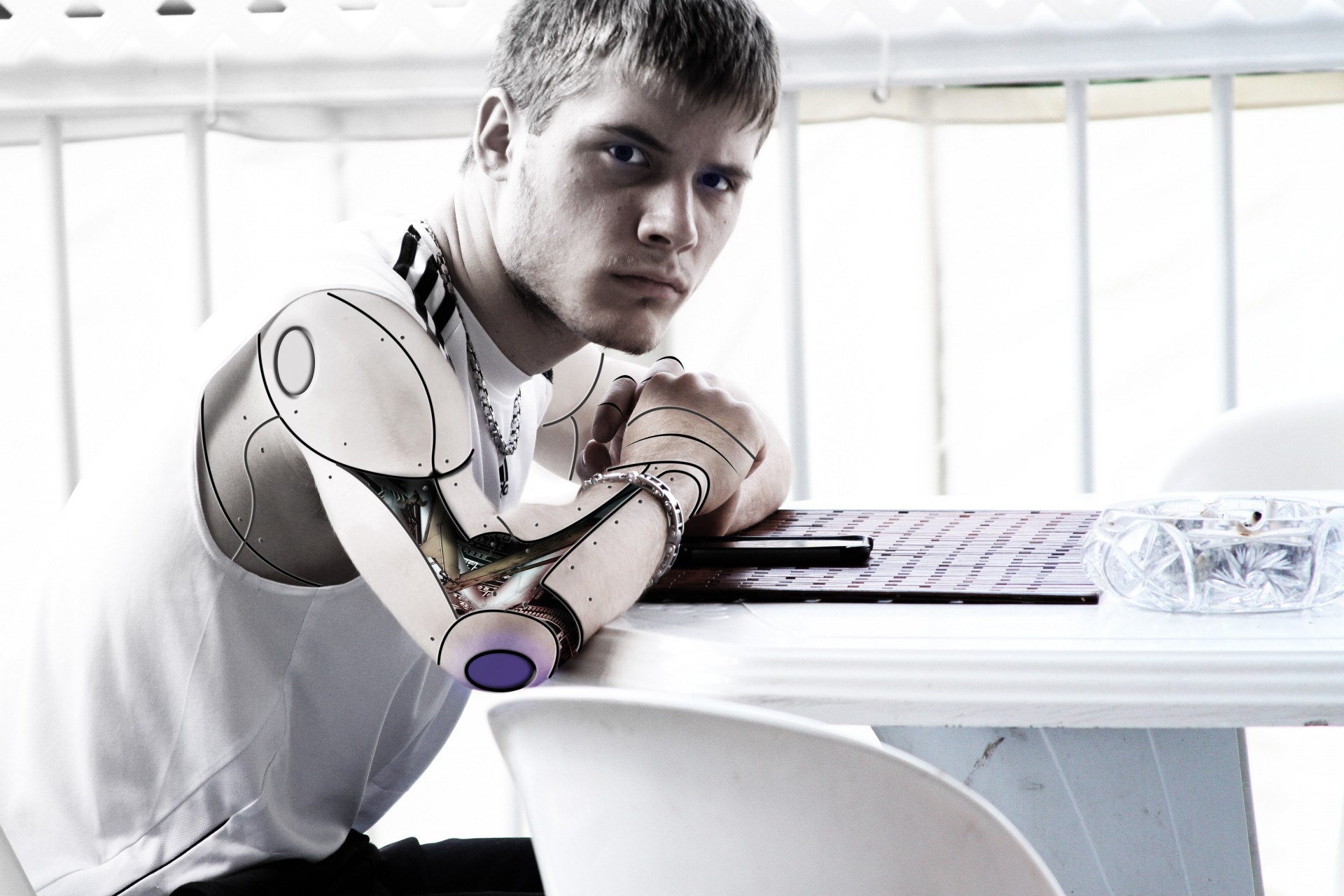
ロボットのティーチングとは?ティーチングの種類と概要を解説
2019.08.27
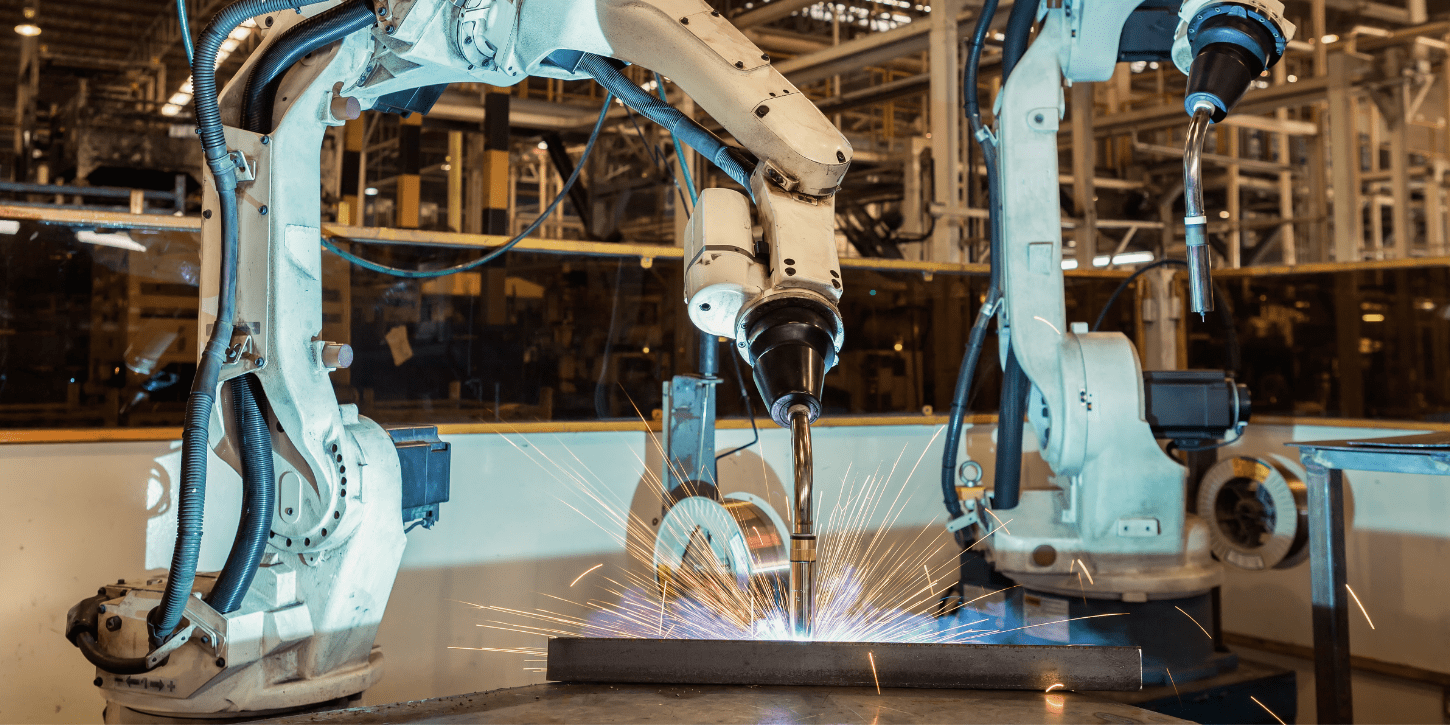
溶接ロボットで行う自動化の方法とは?
2019.08.29
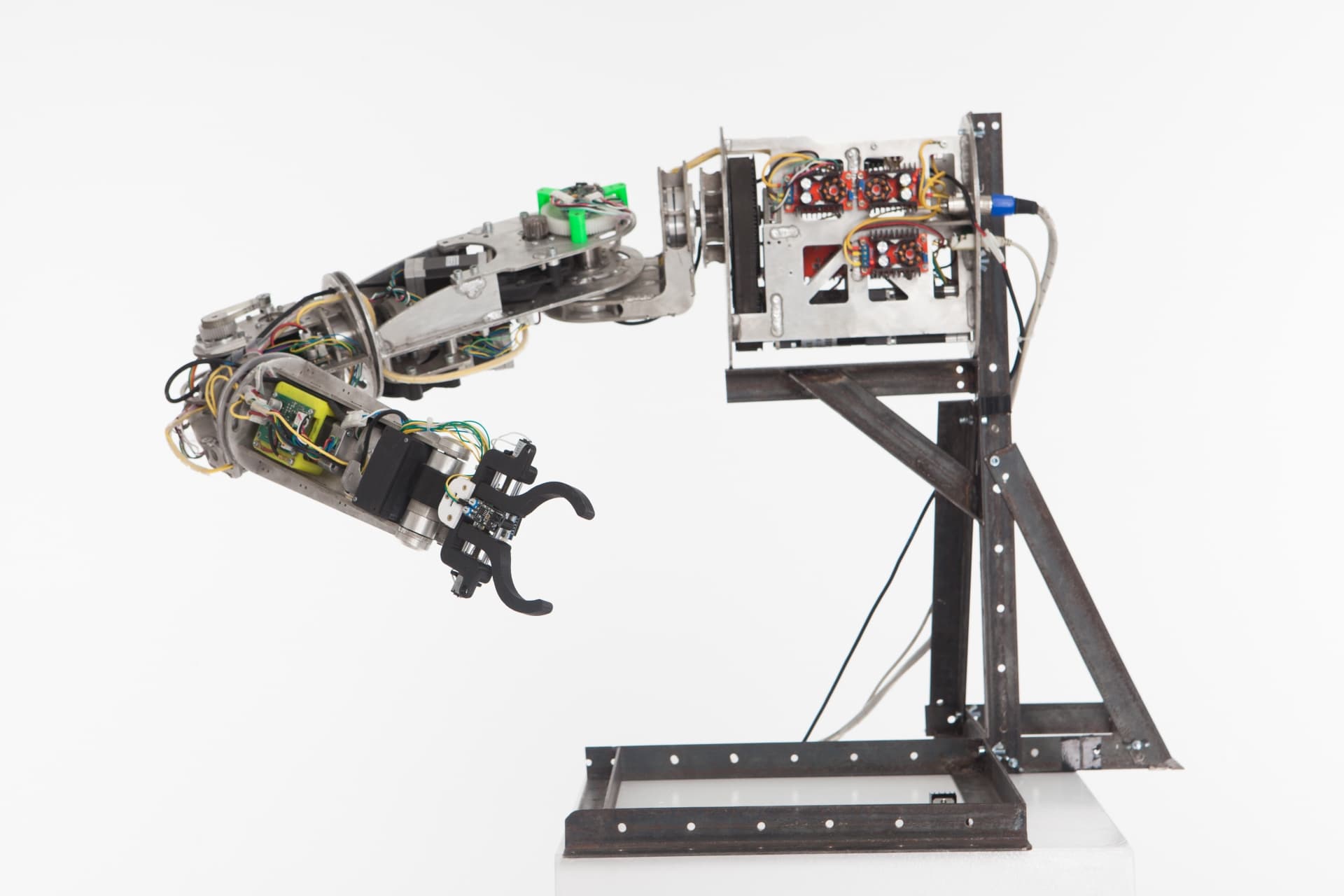
産業用ロボットとは?最新動向からロボットの違いを知る
2019.09.17