記事公開日:2025.01.23
最終更新日:2025.08.26
【工場の改善事例100選】小さなアイデア&ネタで収益UP! 製造業の改善提案例を紹介
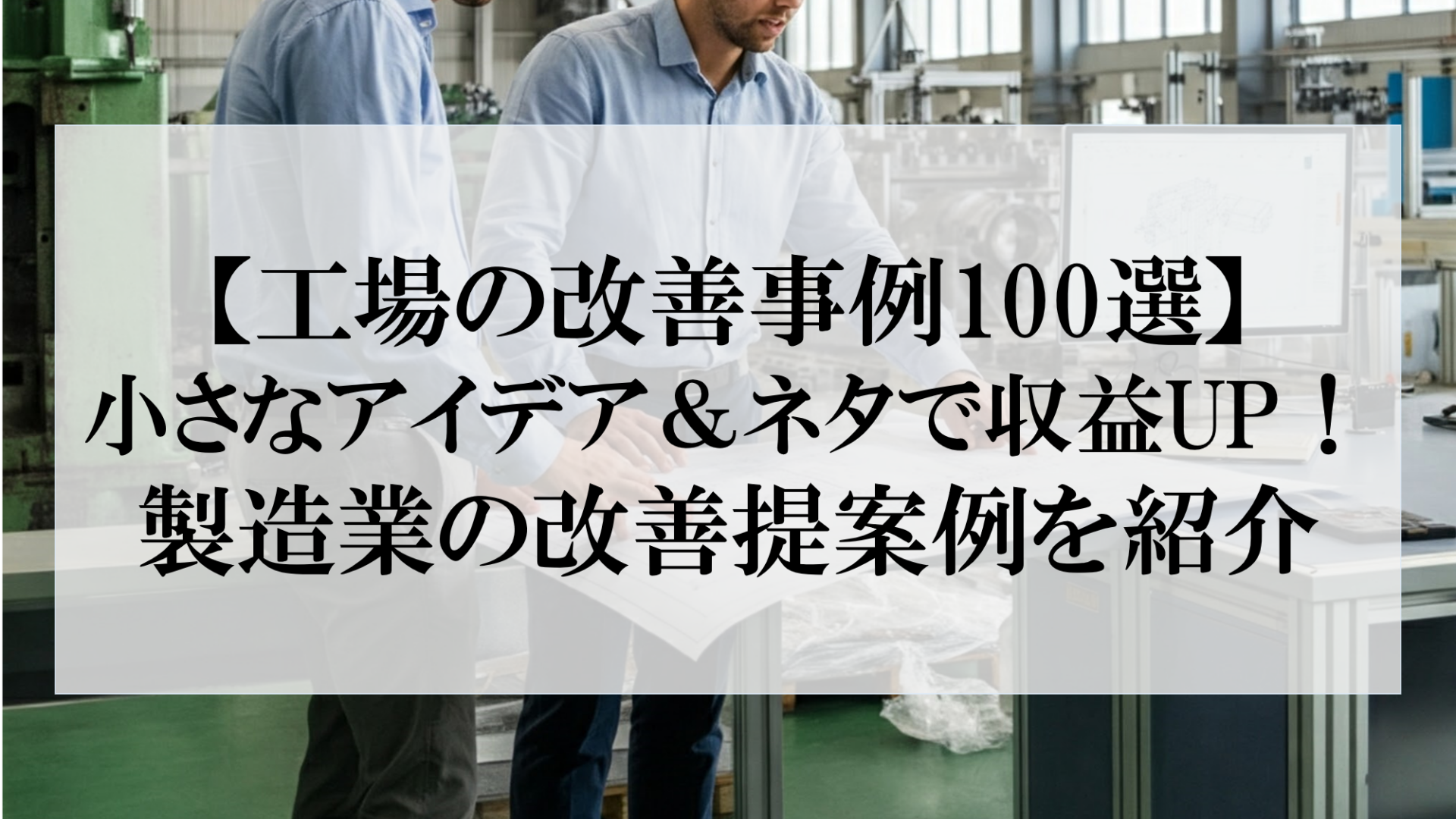
小さなアイデア&ネタで収益UP!製造業の現場で即効性のある改善事例を紹介。作業効率UP、コスト削減、品質向上など、収益UPに繋がる改善提案を多数掲載。改善活動のポイントを押さえ、業務効率化を実現しよう!企業の成功事例からヒントを得て、明日から使える改善ネタを見つけよう!
目次
- 1.はじめに:なぜ工場の改善が必要なのか?
- 2.改善の基本を理解しよう
- 3.すぐに取り組める!工場の小さな改善アイデア&ネタ集
- 3.1.5S活動で職場環境を改善
- 3.1.1. 整理整頓:不要なものをなくし、必要なものをすぐ取り出せるようにする
- 3.1.2.清掃:常に清潔な状態を保つ
- 3.1.3.清潔:汚れやゴミが出にくいように工夫する
- 3.1.4.しつけ:決められたルールを守り、整理整頓・清掃・清潔を維持する
- 3.1.5.習慣化:5S活動を習慣化し、継続的に実施する
- 3.1.6.5S活動の成功事例
- 3.2.ムダをなくして効率UP
- 3.2.1.動作のムダ:移動距離や作業動作を減らす
- 3.2.2.手待ちのムダ:待ち時間の発生原因を突き止め、解消する
- 3.2.3.不良品のムダ:不良品の発生原因を分析し、対策を講じる
- 3.2.4.在庫のムダ:適切な在庫管理を行い、過剰な在庫を抱えないようにする
- 3.2.5.過剰品質のムダ:必要以上の品質を求めない
- 3.2.6.ムダ削減の成功事例
- 3.3.作業効率を上げるアイデア
- 3.3.1. 作業標準化:標準作業手順書を作成し、作業のバラつきをなくす
- 3.3.2. 工程の改善:工程の順番やレイアウトを見直し、作業効率を上げる
- 3.3.3.ツールの改善:作業に適したツールを導入し、作業効率を上げる
- 3.3.4.設備の自動化:人手に頼っていた作業を自動化する
- 3.3.5.情報共有の促進:情報共有システムを導入し、情報伝達のロスタイム削減
- 3.3.6.作業効率向上事例
- 3.4.品質向上で顧客満足度UP
- 3.4.1.品質管理の徹底:品質管理基準を明確化し、検査体制を強化する
- 3.4.2.不良品発生時の迅速な対応:不良品が発生した場合の原因究明と再発防止策を迅速に行う
- 3.4.3.工程内検査の導入:各工程で検査を行い、不良品の流出を防ぐ
- 3.4.4.品質向上事例
- 3.5.安全性を高める改善
- 3.5.1.安全教育の徹底:従業員に対して定期的な安全教育を実施する
- 3.5.2.危険箇所の特定:工場内の危険箇所を特定し、対策を講じる
- 3.5.3.安全設備の導入:安全設備を導入し、事故を防止する
- 3.5.4.安全性向上事例
- 3.6.コスト削減で収益改善
- 3.6.1.電力使用量の削減:省エネ設備の導入や電力会社の見直し
- 3.6.2.廃棄物削減:廃棄物の分別を徹底し、リサイクルを推進
- 3.6.3.コスト削減事例
- 3.7.納期遵守で信頼獲得
- 3.7.1.生産計画の見直し:需要予測に基づいた生産計画の作成
- 3.7.2.工程管理の徹底:各工程の進捗状況を管理し、遅延を防止する
- 3.7.3.納期遵守事例
- 3.8.モラル・モチベーション向上で活力のある工場に
- 3.8.1. 従業員満足度調査の実施:従業員の意見を収集し、職場環境改善に繋げる
- 3.8.2.コミュニケーションの活性化:上司と部下、同僚同士のコミュニケーションを促進
- 3.8.3.モラル・モチベーション向上事例
- 4.改善をさらに進めるために
- 5.製造業の現場における具体的な改善事例
- 6.よくある質問
- 7.まとめ
- 8.参考資料・関連情報
- 9.付録:改善アイデアチェックリスト
1.はじめに:なぜ工場の改善が必要なのか?
皆さんは、「カイゼン」という言葉をご存知でしょうか?日本語の「改善」をローマ字表記したもので、トヨタ自動車が世界に広めた、業務をより良くするための活動のことです。
この「カイゼン」活動こそ、日本の製造業が世界で高い競争力を維持してきた秘訣の一つと言えるでしょう。
近年、製造業を取り巻く環境は、めまぐるしく変化しています。グローバル化の進展、技術革新の加速、顧客ニーズの多様化、人材不足など、企業は多くの課題に直面しています。
このような状況下において、工場の改善活動は、企業の成長と発展に不可欠な要素となっています。
1.1.時代の変化と工場改善の重要性
かつては、大量生産・大量消費の時代において、いかに多くの製品を効率的に生産するかが、工場の主な役割でした。しかし、現代社会では、顧客のニーズは多様化し、製品のライフサイクルは短くなっています。
そのため、企業は、多品種少量生産、短納期化、高品質化など、顧客のニーズに柔軟に対応できる生産体制を構築することが求められています。
このような変化に対応するためには、工場の改善活動を通して、生産プロセスの効率化、品質の向上、コストの削減などを実現していく必要があります。
特に、中小製造業においては、限られたリソースを有効活用し、大企業との競争に打ち勝っていくためには、日々の改善活動がより一層重要になってきます。
1.2.改善活動がもたらすメリット(収益UP、コスト削減、業務効率化など)
工場の改善活動は、企業にさまざまなメリットをもたらします。
- 収益UP
生産性の向上、品質の向上、納期の短縮などにより、売上増加や顧客満足度向上に繋がり、収益UPに貢献します。
例えば、ある工場では、作業プロセスの見直しによって、1日の生産量を10%向上させることに成功しました。
この結果、売上高は前年比15%増となり、大幅な収益UPに繋がりました。 - コスト削減
ムダの排除、電力量削減、資源の有効活用などにより、コスト削減を実現できます。
例えば、ある工場では、電力会社の見直しと省エネ設備の導入によって、年間の電気料金を20%削減することに成功しました。
また、廃棄物の分別を徹底し、リサイクルを推進することで、廃棄物処理費用を15%削減しました。 - 業務効率化
作業プロセスの見直し、情報共有の促進、ITツール導入などにより、業務効率化を図り、人材不足に対応できます。
例えば、ある工場では、生産管理システムを導入することで、在庫管理や納期管理を効率化し、担当者の業務負担を軽減しました。
また、情報共有システムを導入することで、コミュニケーションのロスタイムを削減し、業務のスピードアップを実現しました。 - 従業員満足度向上
働きやすい環境づくり、コミュニケーション活性化、人材育成などを通して、従業員のモチベーションと仕事の満足度を高め、人材の定着率向上に繋がります。
例えば、ある工場では、従業員満足度調査を実施し、その結果を基に職場環境の改善に取り組みました。
その結果、従業員のモチベーションが向上し、離職率が低下しました。 - 安全性向上
職場環境の改善、安全教育の徹底などにより、労働災害を防止し、安全な職場を実現できます。
例えば、ある工場では、工場内の危険箇所を特定し、安全対策を強化した結果、労働災害発生件数を前年比で30%削減することに成功しました。 - 企業イメージ向上
環境への配慮、品質管理への取り組み、コンプライアンス遵守などを通して、企業イメージ向上に繋がり、社会的な信頼を得られます。
例えば、ある工場では、環境管理システムを導入し、CO2排出量削減に取り組んでいます。
この取り組みが地域社会から高く評価され、企業イメージ向上に繋がっています。
1.3.本記事でわかること
本記事では、工場の改善活動の基本から、すぐに取り組める小さな改善アイデア、具体的な事例まで、幅広く解説します。
この記事を読むことで、以下のことがわかります。
- 工場における改善活動の重要性
- 改善活動の基本的な進め方
- 改善アイデアの見つけ方
- すぐに取り組める小さな改善アイデア&ネタ
- 具体的な改善事例
- 改善活動を成功させるためのポイント
本記事は、以下のような方々に読んでいただきたいと考えています。
- 中小企業の経営者
- 改善活動を推進するリーダー
- 生産管理、品質管理、製造部門の担当者
- 工場改善に興味のある方
- 工場勤務の方
2.改善の基本を理解しよう
改善活動とは、職場の問題点や課題を特定し、それを解決するための活動のことです。
工場における改善活動は、生産性の向上、品質の向上、コストの削減、納期の短縮、安全性の向上など、さまざまな目的で行われます。
改善活動は、一過性のものではなく、継続的に行うことが重要です。
PDCAサイクルを回し、小さな改善を積み重ねていくことで、大きな成果に繋がる可能性があります。
2.1. 改善活動とは?
改善活動とは、職場の問題点や課題を特定し、それを解決するための活動のことです。
工場における改善活動は、生産性の向上、品質の向上、コストの削減、納期の短縮、安全性の向上など、さまざまな目的で行われます。
改善活動は、一過性のものではなく、継続的に行うことが重要です。
PDCAサイクルを回し、小さな改善を積み重ねていくことで、大きな成果に繋がる可能性があります。
2.2.改善活動の進め方
改善活動を進めるには、以下の手順を踏むことが一般的です。
I.計画:改善の対象、目標、方法などを具体的に計画します。
II.実施:計画に基づいて、具体的な改善活動を実施します。
III.評価:改善活動による効果を測定し、評価します。
IV.改善:評価結果を踏まえ、改善点があれば、さらに改善活動を行います。
このサイクルを繰り返すことによって、継続的に改善を進めていくことができます。
2.2.1.改善活動の手順(計画→実施→評価→改善)
【計画】
まず、現状を把握し、問題点や課題を明確化します。
例えば、「ある工程で不良品が多く発生している」という問題があるとします。
この問題を解決するためには、まず、現状における不良品の発生率、発生原因、発生箇所などを把握する必要があります。
次に、改善の目標を設定します。目標は具体的で、測定可能なものにすることが重要です。
例えば、「不良品発生率を3ヶ月以内に5%削減する」といった具体的な目標を設定します。
そして、目標達成のための具体的な方法を検討します。
例えば、「作業手順書を見直し、作業ミスを減らす」「品質管理基準を見直し、検査体制を強化する」「設備のメンテナンスを徹底し、設備トラブルによる不良品発生を防止する」といった具体的な方法を検討します。
改善活動のスケジュール、担当者、必要な資源なども明確にしておきます。
例えば、「3ヶ月間を改善活動期間とし、Aさんを担当者とする」「改善活動に必要な費用は10万円とする」といったように、具体的に決めておきます。
【実施】
計画に基づいて、改善活動を実施します。
実施にあたっては、関係部署との連携、情報共有を密に行うことが重要です。
例えば、上記の不良品発生の問題を解決する場合、製造部門だけでなく、品質管理部門やエンジニアリング部門とも連携し、情報共有をしながら改善活動を進める必要があります。
また、従業員の意見を聞きながら、改善活動を進めることも大切です。
従業員は、日々の業務の中で、さまざまな問題点や改善点に気づいている可能性があります。
従業員の意見を積極的に聞き取り、改善活動に反映することで、より効果的な改善活動を行うことができます。
【評価】
改善活動による効果を測定し、評価します。
効果測定には、さまざまな指標が用いられます。例えば、生産性、品質、コスト、納期、安全性などです。
例えば、不良品発生率を改善目標としていた場合、改善活動後の不良品発生率を測定し、目標達成度を評価します。
評価結果を分析し、改善活動の成果と課題を明確化します。
例えば、「不良品発生率は3%削減できたが、目標の5%には達しなかった」という結果だった場合、その原因を分析し、次の改善活動に活かします。
【改善】
評価結果を踏まえ、改善点があれば、さらに改善活動を行います。
改善活動は、一度で終わるものではありません。
継続的に改善を繰り返すことによって、より大きな成果を得ることができます。
例えば、上記の不良品発生の問題では、目標達成度が低かった原因を分析し、新たな改善策を検討・実施します。
2.2.2.改善活動におけるフレームワーク活用
改善活動を進めるにあたり、さまざまなフレームワークを活用することができます。
フレームワークとは、問題解決や分析のための枠組みのことです。
フレームワークを活用することで、以下のメリットがあります。
- 問題点を整理しやすくなる。
- 分析がスムーズに行える。
- 解決策を見つけやすくなる。
- 関係者間で共通認識を持ちやすくなる。
代表的なフレームワークとしては、以下のものがあります。
-
PDCAサイクル
計画(Plan)、実施(Do)、評価(Check)、改善(Action)の4つのプロセスを繰り返すことによって、継続的に改善を進めるフレームワークです。
PDCAサイクルは、改善活動の基本となるフレームワークです。
計画を立て、実行し、評価し、改善するというサイクルを繰り返すことによって、継続的に業務を改善していくことができます。 -
Why-Why分析(なぜなぜ分析)
問題の根本原因を突き止めるための分析方法です。
問題に対して、「なぜ?」を繰り返すことによって、真の原因を突き止めます。
例えば、「なぜ不良品が発生したのか?」→「作業ミスがあったから」→「なぜ作業ミスがあったのか?」→「作業手順書が分かりにくかったから」→「なぜ作業手順書が分かりにくかったのか?」→・・・
このように、「なぜ?」を繰り返すことで、問題の根本原因を突き止め、効果的な対策を立てることができます。 -
5W1H
問題を明確化し、解決策を検討するためのフレームワークです。
When(いつ)、Where(どこで)、Who(誰が)、What(何を)、Why(なぜ)、How(どのように)の6つの要素を明確にすることで、問題を多角的に捉え、解決策を検討することができます。 -
SWOT分析
企業のstrengths(強み)、weaknesses(弱み)、opportunities(機会)、threats(脅威)を分析するフレームワークです。
企業の内部環境と外部環境を分析することで、現状を把握し、今後の戦略立案に役立てることができます。
2.2.3.改善活動を成功させるためのポイント
改善活動を成功させるためには、以下のポイントを押さえることが重要です。
-
トップのコミットメント
経営トップが改善活動にコミットメントし、積極的にサポートすることが重要です。
経営トップが率先して改善活動に取り組む姿勢を示すことで、従業員の意識改革を促進し、改善活動を全社的に展開することができます。 -
従業員の参加
従業員一人ひとりが改善活動に積極的に参加することが重要です。
従業員一人ひとりが「改善は自分事」という意識を持ち、積極的にアイデアを出し、改善活動に参加することで、より効果的な改善活動を行うことができます。
従業員の参加を促すためには、提案制度の導入、表彰制度の導入、コミュニケーションの活性化など、さまざまな取り組みが有効です。 -
目標の明確化
改善活動の目標を明確化し、共有することが重要です。
目標が曖昧だと、改善活動の方向性が定まらず、効果的な活動ができません。
目標は、従業員全員が理解し、共有できるものにする必要があります。
また、目標達成度を測るための指標を明確にしておくことも重要です。 -
効果測定
改善活動の効果を測定し、評価することが重要です。
効果測定を行うことで、改善活動の成果を客観的に評価することができます。
効果測定の結果は、次の改善活動に活かすことができます。
また、効果測定の結果を従業員にフィードバックすることで、モチベーション向上にも繋がります。 -
継続的な改善
改善活動を継続的に行うことが重要です。
改善活動は、一度実施すれば終わりではありません。
継続的に改善を繰り返すことによって、より大きな成果を得ることができます。
改善活動を継続するためには、PDCAサイクルを回し、定期的に改善活動を見直すことが重要です。 -
情報共有
改善活動に関する情報を共有することが重要です。
改善活動の進捗や成果を共有することで、従業員のモチベーション向上や、全社的な改善意識の向上に繋げることができます。
情報共有には、社内報、掲示板、ミーティングなど、さまざまなツールを活用することができます。 -
コミュニケーション
関係者間でコミュニケーションを密に行うことが重要です。
改善活動は、関係部署との連携が不可欠です。
コミュニケーションを密に行うことで、スムーズな連携体制を構築し、効果的な改善活動を行うことができます。
2.3.改善アイデアの見つけ方
改善活動を進めるためには、まず改善アイデアを見つける必要があります。
改善アイデアは、現場の観察、データ分析、ブレインストーミングなど、さまざまな方法で見つけることができます。
2.3.1.現場の課題発見
改善アイデアを見つけるためには、まず現場の課題を発見することが重要です。
現場の課題を発見するためには、以下の方法があります。
-
現場観察
実際に現場に行って、作業プロセスや職場環境を観察する。
現場観察を行う際には、以下の点に注意する必要があります。
作業者の邪魔にならないように、観察する。
作業者にインタビューを行い、意見や要望を聞く。
写真やビデオを撮影し、記録を残す。 -
従業員へのインタビュー
従業員にインタビューを行い、意見や要望を聞く。
インタビューを行う際には、以下の点に注意する必要があります。
従業員が自由に意見を言えるような雰囲気を作る。
具体的な質問をする。
従業員の意見を尊重する。 -
アンケート調査
アンケート調査を実施し、従業員の意見を収集する。
アンケート調査を実施する際には、以下の点に注意する必要があります。
質問項目を明確にする。
回答しやすいように、選択肢を設ける。
回答結果を分析し、改善に活かす。 -
データ分析
生産データや品質管理データなどを分析し、問題点を特定する。
データ分析を行う際には、以下の点に注意する必要があります。
適切なデータを収集する。
データを正確に分析する。
分析結果を分かりやすく可視化する。
2.3.2.改善ネタを見つけるコツ
改善ネタを見つけるコツとしては、以下のものがあります。
-
5S活動
整理整頓、清掃、清潔、しつけ、習慣化の5S活動を通して、職場環境を改善することで、さまざまな改善ネタが見つかることがあります。
5S活動は、職場環境を改善するための基本的な活動です。
5S活動を徹底することで、職場が綺麗になり、作業効率が向上するだけでなく、従業員のモチベーション向上や安全意識向上にも繋がります。 -
ムダの排除
動作のムダ、手待ちのムダ、不良品のムダ、在庫のムダ、過剰品質のムダなど、7つのムダを特定し、排除することで、改善ネタが見つかることがあります。
ムダをなくすことは、コスト削減や効率化に繋がるだけでなく、品質向上や納期遵守にも繋がります。 -
他社の事例
他社の改善事例を参考にすることで、自社の改善活動に役立つヒントが得られることがあります。
他社の事例を参考にする際には、自社の課題や状況に合わせて、参考にすべき点とそうでない点を見極めることが重要です。 -
ブレインストーミング
関係者でブレインストーミングを行い、自由にアイデアを出し合うことで、新たな改善ネタが見つかることがあります。
ブレインストーミングを行う際には、以下の点に注意する必要があります。
自由な発想を促す。
批判をしない。
アイデアを記録する。
2.3.3.改善提案を促す社内体制
従業員が積極的に改善提案を行うためには、以下の取り組みが有効です。]
-
提案制度の導入
従業員からの改善提案を募集し、評価・表彰する制度を導入する。
提案制度を導入することで、従業員の改善意識を高め、積極的に改善提案を促すことができます。
提案制度では、提案内容だけでなく、提案件数や実現件数なども評価することで、従業員のモチベーション向上を図ることができます。 -
提案しやすい雰囲気づくり
従業員が自由に意見やアイデアを出しやすい雰囲気づくりをする。
従業員が上司や同僚の目を気にせず、自由に意見やアイデアを出し合えるような職場環境を作ることが重要です。 -
改善教育
従業員に対して、改善活動に関する教育を実施する。
改善活動に関する知識やスキルを習得することで、従業員の改善意識を高め、より効果的な改善活動を行うことができます。 -
コミュニケーションの活性化
上司と部下、同僚同士のコミュニケーションを活性化し、情報共有を促進する。
コミュニケーションを活性化することで、従業員同士が互いに意見交換や情報共有を行いやすくなり、新たな改善アイデアが生まれる可能性が高まります。
2.4.改善事例から学ぶ
他社の改善事例を参考にすることは、自社の改善活動を進める上で非常に役立ちます。
成功事例だけでなく、失敗事例からも学ぶことで、より効果的な改善活動を行うことができます。
2.4.1.他社の成功事例紹介
ここでは、中小製造業における改善の成功事例をいくつかご紹介します。
【事例1】
ある部品加工会社では、5S活動を導入し、職場環境を改善した結果、作業効率が向上し、不良品発生率が減少しました。
この会社では、5S活動を導入する前は、職場が乱雑で、必要な工具や材料がすぐに見つからないという問題がありました。
5S活動を導入し、職場を整理整頓した結果、必要なものがすぐに見つかるようになり、作業効率が10%向上しました。
また、職場が綺麗になったことで、従業員のモチベーションが向上し、品質管理意識が高まりました。
その結果、不良品発生率は5%から2%に減少しました。
【事例2】
ある食品加工会社では、工程分析を実施し、ボトルネック工程を特定した上で、工程改善を行った結果、リードタイムを短縮し、納期遵守率を向上させました。
この会社では、以前は納期遅延が頻繁に発生しており、顧客からのクレームも増加していました。
工程分析を実施した結果、ある工程に作業が集中しており、ボトルネックになっていることが判明しました。
ボトルネック工程の作業プロセスを見直し、人員配置や設備配置を変更することで、リードタイムを20%短縮することに成功しました。
その結果、納期遵守率は80%から95%に向上し、顧客満足度も向上しました。
【事例3】
ある金属加工会社では、3Dプリンターを導入し、治具を内製化した結果、治具製作コストを削減し、納期を短縮しました。
この会社では、以前は治具を外注しており、治具製作コストが高く、納期もかかっていました。
3Dプリンターを導入し、治具を内製化した結果、治具製作コストを30%削減することに成功しました。
また、納期も1週間から3日に短縮することができ、生産リードタイムの短縮にも繋がりました。
2.4.2.成功事例から得られるヒント
成功事例から得られるヒントとしては、以下のものがあります。
- トップのコミットメント
経営トップが改善活動にコミットメントし、積極的にサポートしている。
従業員の参加:従業員一人ひとりが改善活動に積極的に参加している。 - 目標の明確化
改善活動の目標を明確化し、共有している。 - 効果測定
改善活動の効果を測定し、評価している。 - 継続的な改善
改善活動を継続的に行っている。
3.すぐに取り組める!工場の小さな改善アイデア&ネタ集
この章では、すぐに取り組める工場の小さな改善アイデア&ネタを100個ご紹介します。
これらのアイデアは、特別な設備や多大な投資を必要とせず、すぐにでも実践できるものばかりです。
3.1.5S活動で職場環境を改善
5S活動とは、「整理」「整頓」「清掃」「清潔」「しつけ」の5つの頭文字をとった言葉です。
5S活動を推進することで、職場環境を改善し、作業効率向上、品質管理、安全性の向上などに繋げることができます。
3.1.1. 整理整頓:不要なものをなくし、必要なものをすぐ取り出せるようにする
- 不要なものを特定し、処分する。
職場には、長年使われていない工具や材料、書類などが放置されていることがよくあります。
まずは、職場全体を点検し、不要なものを特定しましょう。
不要なものは、思い切って処分することで、職場のスペースを有効活用することができます。 - 必要なものを決められた場所に置く。
必要なものは、決められた場所に置くようにすることで、必要なときにすぐに見つけることができます。
置き場所を決める際には、使用頻度や作業動線を考慮することが重要です。
使用頻度の高いものは、取り出しやすい場所に置きましょう。 - 物の置き場所を分かりやすく表示する。
物の置き場所を分かりやすく表示することで、誰でも必要なものをすぐに見つけることができます。
表示方法としては、ラベルを貼ったり、棚に名前を付けたり、写真やイラストを使用したりするなど、さまざまな方法があります。 - 定期的に整理整頓を行う。
整理整頓は、一度行えば終わりではありません。
定期的に整理整頓を行うことで、職場を常に綺麗な状態に保つことができます。
整理整頓の頻度は、職場の状況や作業内容によって異なりますが、少なくとも月に1回は行うようにしましょう。
3.1.2.清掃:常に清潔な状態を保つ
- 職場を毎日清掃する。
職場を毎日清掃することで、チリやゴミをなくし、清潔な状態を保つことができます。
清掃は、作業開始前や作業終了後に行うようにしましょう。 - 機械や設備も定期的に清掃する。
機械や設備に付着したチリや汚れは、故障やトラブルの原因となります。
定期的に清掃することで、機械や設備の寿命を延ばし、安全性を高めることができます。 - 清掃ツールを整備する。
清掃ツールが不足していたり、壊れていたりすると、清掃効率が低下します。
必要な清掃ツールを揃え、常に使える状態にしておきましょう。 - 清掃責任を明確にする。
職場の清掃責任を明確にすることで、清掃が行き届かないという事態を防ぐことができます。
清掃責任は、担当者を決める、エリアごとに分担するなど、職場の状況に合わせて決めましょう。
3.1.3.清潔:汚れやゴミが出にくいように工夫する
- 汚れやゴミの原因を特定し、対策を講じる。
汚れやゴミが発生しやすい場所を特定し、その原因を突き止めましょう。
原因が分かれば、それに応じた対策を講じることで、汚れやゴミの発生を抑制することができます。 - 汚れにくい材料を使用する。
職場の床や壁、設備などに、汚れにくい材料を使用することで、清掃の手間を減らすことができます。 - ゴミ箱を設置する。
ゴミ箱を設置することで、ゴミを適切に処理することができます。
ゴミ箱は、作業しやすい場所に設置し、分別しやすいように種類分けしておきましょう。 - 覆いやカバーをする。
機械や設備、材料などに覆いやカバーをすることで、チリや汚れが付着するのを防ぐことができます。
3.1.4.しつけ:決められたルールを守り、整理整頓・清掃・清潔を維持する
- 5Sに関するルールを明確にする。
整理整頓、清掃、清潔に関するルールを明確にし、従業員に周知徹底しましょう。
ルールは、分かりやすく、実行しやすいものにすることが重要です。 - ルールを遵守する。
従業員一人ひとりがルールを遵守することで、5S活動を定着させることができます。
ルールを守らない従業員に対しては、注意や指導を行いましょう。 - 定期的に点検を行う。
5S活動が適切に行われているか、定期的に点検を行いましょう。
点検結果は、従業員にフィードバックし、改善を促しましょう。
3.1.5.習慣化:5S活動を習慣化し、継続的に実施する
- 5S活動をdaily業務に取り入れる。
5S活動をdaily業務に取り入れることで、習慣化することができます。
例えば、作業開始前や作業終了後に5S活動を行う時間を設ける、5S活動のチェックリストを作成するなど、工夫してみましょう。 - 5S活動を評価する。
5S活動の成果を評価することで、従業員のモチベーション向上を図ることができます。
評価は、点数をつける、ランキング形式にするなど、さまざまな方法があります。 - 5S活動を継続する。
5S活動は、一度実施すれば終わりではありません。
継続的に実施することで、職場環境を常に改善していくことができます。
3.1.6.5S活動の成功事例
【事例1】
ある工場では、5S活動を導入したことで、職場が綺麗になり、従業員のモチベーションが向上しました。
以前は、職場が乱雑で、従業員のモチベーションも低かったのですが、5S活動を導入したことで、職場が綺麗になり、従業員も気持ちよく働くことができるようになりました。
その結果、従業員のモチベーションが向上し、生産性も向上しました。
【事例2】
ある工場では、5S活動を導入したことで、不良品発生率が減少しました。
以前は、職場が乱雑で、必要なものがすぐに見つからないため、作業ミスが発生しやすく、不良品発生率も高かったのですが、5S活動を導入したことで、必要なものがすぐに見つかるようになり、作業ミスが減少しました。
その結果、不良品発生率も減少しました。
【事例3】
ある工場では、5S活動を導入したことで、安全性が向上しました。
以前は、職場に物が散乱しており、転倒や落下などの事故が発生しやすかったのですが、5S活動を導入したことで、職場が綺麗になり、事故発生件数が減少しました。
また、従業員の安全意識も高まり、安全な職場づくりに繋がりました。
3.2.ムダをなくして効率UP
ムダをなくすことは、コスト削減や効率化に繋がるだけでなく、品質向上や納期遵守にも繋がります。
工場には、さまざまなムダが潜んでいます。
代表的なムダとしては、以下の7つが挙げられます。
I. 動作のムダ
II. 手待ちのムダ
III. 不良品のムダ
IV. 在庫のムダ
V. 過剰品質のムダ
VI. 運搬のムダ
VII. 加工のムダ
これらのムダを特定し、排除することで、工場の効率化を図ることができます。
3.2.1.動作のムダ:移動距離や作業動作を減らす
- 作業動線を改善する。
作業動線を改善することで、移動距離を減らすことができます。
例えば、作業台や設備の配置を見直し、移動距離を減らす、搬送ルートを見直し、移動時間を減らすなど、工夫してみましょう。 - 作業動作を改善する。
作業動作を改善することで、作業時間を減らすことができます。
例えば、両手作業を導入する、ツールを改良する、人間工学的な作業姿勢を導入するなど、工夫してみましょう。
3.2.2.手待ちのムダ:待ち時間の発生原因を突き止め、解消する
- 待ち時間の発生原因を特定する。
待ち時間の発生原因を特定するためには、作業観察やデータ分析が有効です。
例えば、前工程の遅延、設備の故障、材料の不足などが原因で待ち時間が発生していることがあります。 - 待ち時間を解消する。
待ち時間の発生原因に応じて、適切な対策を講じましょう。
例えば、前工程の作業効率を改善する、設備の予防メンテナンスを徹底する、材料の在庫管理を徹底するなど、工夫してみましょう。
3.2.3.不良品のムダ:不良品の発生原因を分析し、対策を講じる
- 不良品の発生原因を分析する。
不良品の発生原因を分析するためには、品質管理データの分析や、不良品発生時の状況確認などが有効です。
例えば、作業ミス、設備の不具合、材料の不良などが原因で不良品が発生していることがあります。 - 不良品を減らすための対策を講じる。
不良品の発生原因に応じて、適切な対策を講じましょう。
例えば、作業手順書を見直し、作業ミスを減らす、設備のメンテナンスを徹底し、設備の不具合を防止する、材料の入荷検査を強化し、材料の不良を防止するなど、工夫してみましょう。
3.2.4.在庫のムダ:適切な在庫管理を行い、過剰な在庫を抱えないようにする
- 適切な在庫管理を行う。
必要なときに必要な量の材料があるように、適切な在庫管理を行うことが重要です。
在庫管理には、さまざまな方法がありますが、代表的なものとしては、発注点方式、定期発注方式、かんばん方式などがあります。
自社の状況に合わせて、適切な在庫管理方法を選びましょう。 - 需要予測を行う。
将来の需要を予測することで、過剰な在庫を抱えることを防ぐことができます。
需要予測には、過去の販売データや市場トレンドなどを参考にしましょう。 - 在庫の保管場所を改善する。
在庫の保管場所を改善することで、スペースの有効活用や、在庫管理の効率化を図ることができます。
例えば、棚やラックを導入する、保管場所を表示する、保管場所を整理整頓するなど、工夫してみましょう。 - 在庫の回転率を上げる。
在庫の回転率を上げることで、在庫の保管期間を短縮し、在庫費用を削減することができます。
回転率を上げるためには、需要予測の精度向上、発注量の適正化、生産リードタイムの短縮など、さまざまな取り組みが必要です。
3.2.5.過剰品質のムダ:必要以上の品質を求めない
- 必要とされる品質を明確にする。
製品やサービスに必要とされる品質を明確にすることで、過剰な品質を求めることを防ぐことができます。
必要とされる品質は、顧客の要求や業界基準などを参考にしましょう。 - 工程能力を評価する。
工程能力を評価することで、現状の品質レベルを把握し、必要とされる品質を満たしているかを確認することができます。
工程能力が不足している場合は、改善を行う。
工程能力が不足している場合は、工程改善を行うことで、必要とされる品質を満たすことができます。
3.2.6.ムダ削減の成功事例
【事例1】
ある工場では、5S活動を導入することで、職場のムダを削減し、作業効率を向上させました。
5S活動によって、職場が整理整頓され、必要なものがすぐに見つかるようになったことで、探し物の時間が減り、作業効率が向上しました。
【事例2】
ある工場では、かんばん方式を導入することで、在庫のムダを削減し、在庫費用を削減しました。
かんばん方式を導入することで、必要なときに必要な量の材料を調達することができるようになり、過剰な在庫を抱えることがなくなりました。
その結果、在庫費用を削減することができました。
【事例3】
ある工場では、工程分析を実施することで、工程のムダを特定し、工程改善を行いました。
工程分析の結果、ボトルネック工程を特定し、その工程の作業プロセスを見直すことで、リードタイムを短縮することができました。
3.3.作業効率を上げるアイデア
作業効率を上げることは、生産性の向上に繋がり、収益UPに貢献します。
作業効率を上げるためには、以下の取り組みが有効です。
3.3.1. 作業標準化:標準作業手順書を作成し、作業のバラつきをなくす
- 標準作業手順書を作成する。
標準作業手順書を作成することで、作業のバラつきをなくし、作業品質を安定させることができます。
標準作業手順書には、作業の手順、使用するツール、品質管理基準などを明確に記載しましょう。 - 作業手順書を遵守する。
作業者は、標準作業手順書を遵守することで、品質の高い作業を行うことができます。
作業手順書の内容を定期的に見直し、改善していくことも重要です。
3.3.2. 工程の改善:工程の順番やレイアウトを見直し、作業効率を上げる
- 工程分析を行う。
工程分析を行うことで、工程のムダを特定し、改善点を見つけることができます。
工程の順番を見直す。
工程の順番を見直すことで、作業効率を上げることができる場合があります。
例えば、並行作業を導入する、作業の順番を入れ替えるなど、工夫してみましょう。 - レイアウト変更を行う。
レイアウト変更を行うことで、作業動線を改善し、移動距離を減らすことができます。
また、設備の配置を見直すことで、作業効率を上げることができる場合があります。
3.3.3.ツールの改善:作業に適したツールを導入し、作業効率を上げる
- 作業に適したツールを導入する。
作業に適したツールを導入することで、作業効率を上げることができます。
例えば、人間工学的なツールを導入することで、作業者の負担を軽減し、作業効率を上げることができます。 - ツールを改良する。
既存のツールを改良することで、作業効率を上げることができる場合があります。
例えば、ツールに補助器具を取り付ける、ツールの形状を変えるなど、工夫してみましょう。
3.3.4.設備の自動化:人手に頼っていた作業を自動化する
- 自動化できる作業を特定する。
人手に頼っていた作業を特定し、自動化できるかどうかを検討しましょう。
例えば、搬送作業、組み立て作業、検査作業など、自動化できる作業は多くあります。 - 自動化設備を導入する。
自動化設備を導入することで、人手に頼っていた作業を自動化し、人材不足に対応することができます。
また、自動化設備を導入することで、作業品質の安定化や、人為的なミス削減にも繋がります。
3.3.5.情報共有の促進:情報共有システムを導入し、情報伝達のロスタイム削減
- 情報共有システムを導入する。
情報共有システムを導入することで、必要な情報を必要なときに共有することができ、情報伝達のロスタイムを削減することができます。
また、情報共有システムを導入することで、ペーパレス化を推進し、業務効率化を図ることもできます。 - 情報共有のルールを明確にする。
情報共有システムを導入する際には、情報共有のルールを明確にし、従業員に周知徹底することが重要です。
例えば、どの情報を共有するのか、どのタイミングで共有するのか、誰に共有するのかなどを明確にしておきましょう。
3.3.6.作業効率向上事例
【事例1】
ある工場では、標準作業手順書を作成し、作業者に教育を実施することで、作業品質のバラつきをなくし、作業効率を向上させました。
以前は、作業者によって作業方法が異なり、作業品質にバラつきがありました。
標準作業手順書を作成し、作業者に教育を実施することで、作業品質が安定し、作業効率が向上しました。
【事例2】
ある工場では、工程分析を実施し、ボトルネック工程を特定した上で、工程改善を行った結果、リードタイムを短縮し、納期遵守率を向上させました。
以前は、納期遅延が頻繁に発生していましたが、工程改善によってリードタイムを短縮することができ、納期遵守率が向上しました。
【事例3】
ある工場では、人間工学的なツールを導入することで、作業者の負担を軽減し、作業効率を向上させました。
以前は、作業者が重いツールを使用していたため、腰痛などの健康problemを抱える作業者が多くいました。
人間工学的なツールを導入することで、作業者の負担を軽減し、作業効率を向上させることができました。
3.4.品質向上で顧客満足度UP
品質向上は、顧客満足度向上に繋がり、企業の信頼獲得に繋がります。
品質向上のためには、以下の取り組みが有効です。
3.4.1.品質管理の徹底:品質管理基準を明確化し、検査体制を強化する
- 品質管理基準を明確化する。
製品やサービスの品質管理基準を明確化し、従業員に周知徹底することが重要です。
品質管理基準は、顧客の要求や業界基準などを参考にしましょう。 - 検査体制を強化する。
検査体制を強化することで、不良品の流出を防ぎ、品質向上を図ることができます。
検査項目を増やす、検査頻度を増やす、検査設備を導入するなど、さまざまな方法があります。
3.4.2.不良品発生時の迅速な対応:不良品が発生した場合の原因究明と再発防止策を迅速に行う
- 不良品が発生した場合の原因を究明する。
不良品が発生した場合は、原因を究明し、再発防止策を講じることが重要です。
原因究明には、5W1Hなどを活用すると良いでしょう。 - 再発防止策を講じる。
原因究明の結果を踏まえ、再発防止策を講じましょう。
再発防止策は、作業手順書の見直し、設備のメンテナンス、教育の実施など、さまざまなものがあります。
3.4.3.工程内検査の導入:各工程で検査を行い、不良品の流出を防ぐ
- 各工程で検査を行う。
各工程で検査を行うことで、不良品を早期に発見し、流出を防ぐことができます。
工程内検査は、全数検査、サンプリング検査など、さまざまな方法があります。 - 検査結果を記録する。
検査結果を記録することで、品質管理データを蓄積し、分析することができます。
検査結果の分析は、品質管理の改善に役立ちます。
3.4.4.品質向上事例
【事例1】
ある工場では、品質管理サークル活動を導入することで、従業員の品質管理意識を高め、品質向上を図りました。
品質管理サークル活動とは、従業員が自主的に品質管理に関する活動を行うことです。
品質管理サークル活動を導入することで、従業員が品質管理に積極的に取り組むようになり、品質向上に繋がりました。
【事例2】
ある工場では、データ分析を活用することで、不良品発生の原因を特定し、品質向上を図りました。
以前は、不良品発生の原因が特定できず、対策が遅れていましたが、データ分析を活用することで、不良品発生の原因を特定することができ、効果的な対策を講じることができました。
その結果、不良品発生率を大幅に削減することができました。
【事例3】
ある工場では、顧客からのフィードバックを積極的に収集し、製品開発に活かすことで、顧客満足度向上を図りました。
顧客からのフィードバックを収集することで、顧客のニーズを把握し、製品開発に活かすことができました。
その結果、顧客満足度が向上し、売上増加に繋がりました。
3.5.安全性を高める改善
安全な職場を実現することは、従業員の安全確保だけでなく、企業の信頼獲得にも繋がります。
安全性向上のためには、以下の取り組みが有効です。
3.5.1.安全教育の徹底:従業員に対して定期的な安全教育を実施する
- 新入社員教育
新入社員に対しては、入社時に安全教育を実施し、職場のルールや安全に関する知識を習得させましょう。 - 継続教育
継続教育を実施することで、従業員の安全意識を維持し、高めることができます。
継続教育は、定期的に実施しましょう。 - 職種別教育
職種別に必要な安全知識やスキルは異なります。
職種別に教育を実施することで、より効果的な安全教育を行うことができます。
3.5.2.危険箇所の特定:工場内の危険箇所を特定し、対策を講じる
- 危険箇所を特定する。
工場内を点検し、危険箇所を特定しましょう。
危険箇所としては、転倒しやすい場所、物が落下しやすい場所、機械に巻き込まれやすい場所などがあります。 - 対策を講じる。
危険箇所を特定したら、対策を講じましょう。
対策としては、注意喚起の表示をする、安全策を設置する、設備を導入するなどがあります。
3.5.3.安全設備の導入:安全設備を導入し、事故を防止する
- 安全設備を導入する。
安全設備を導入することで、事故を防止することができます。
安全設備としては、ヘルメット、安全帯、安全靴、保護メガネなどがあります。 - 安全設備の使用方法を教育する。
安全設備を導入する際には、使用方法を従業員に教育することが重要です。
正しい使用方法を習得することで、安全設備を効果的に使用することができます。
3.5.4.安全性向上事例
【事例1】
ある工場では、ヒヤリハット活動を通して、従業員の安全意識を高め、事故発生件数を減少させました。
ヒヤリハット活動とは、従業員がヒヤリとしたり、ハッとしたりしたことを報告し、共有することで、事故を未然に防ぐ活動です。
ヒヤリハット活動を通して、従業員が安全について考える機会を増やし、安全意識を高めることができました。
【事例2】
ある工場では、リスクアセスメントを導入することで、危険箇所を特定し、対策を講じました。
リスクアセスメントとは、作業プロセスにおける危険特定し、リスクを評価することで、事故を未然に防ぐ活動です。
リスクアセスメントを導入することで、危険箇所を特定し、適切な対策を講じることができました。
【事例3】
ある工場では、安全設備を導入することで、事故発生件数を減少させました。
以前は、安全設備が不足しており、事故が発生していましたが、安全設備を導入することで、事故発生件数を減少させることができました。
3.6.コスト削減で収益改善
コスト削減は、企業の収益改善に直結する重要な取り組みです。
コスト削減のためには、以下の取り組みが有効です。
3.6.1.電力使用量の削減:省エネ設備の導入や電力会社の見直し
- 省エネ設備を導入する。
省エネ設備を導入することで、電力使用量を削減することができます。
省エネ設備としては、LED照明、エアコン、高効率ボイラーなどがあります。 - 電力会社の見直しを行う。
電力会社の見直しを行うことで、電気料金を削減することができます。
電力会社によっては、企業向けの割引プランを提供している場合があります。 - 材料費の削減:材料の調達先の見直しや共同購入
材料の調達先を見直す。
材料の調達先を見直すことで、材料費を削減することができます。
複数の調達先から見積もりを取り、価格を比較検討しましょう。 - 共同購入を行う。
他の企業と共同で購入することで、大量購入による割引を受けることができます。
3.6.2.廃棄物削減:廃棄物の分別を徹底し、リサイクルを推進
- 廃棄物の分別を徹底する。
廃棄物の分別を徹底することで、リサイクルできるものを増やし、廃棄物処理費用を削減することができます。 - リサイクルを推進する。
リサイクルできるものは、積極的にリサイクルしましょう。
リサイクル業者に依頼することで、リサイクルすることができます。
3.6.3.コスト削減事例
【事例1】
ある工場では、LED照明を導入することで、電力使用量を削減し、電気料金を削減しました。
以前は、蛍光灯を使用していましたが、LED照明を導入することで、電力使用量を50%削減することができました。
【事例2】
ある工場では、材料の調達先を見直し、共同購入を行うことで、材料費を削減しました。
以前は、1つの調達先から材料を調達していましたが、複数の調達先から見積もりを取り、価格を比較検討した結果、より安い調達先を見つけることができました。
また、他の企業と共同で購入することで、大量購入による割引を受けることができました。
【事例3】
ある工場では、廃棄物の分別を徹底し、リサイクルを推進することで、廃棄物処理費用を削減しました。
以前は、廃棄物を分別せずに処理していましたが、廃棄物の分別を徹底することで、リサイクルできるものを増やし、廃棄物処理費用を削減することができました。
3.7.納期遵守で信頼獲得
納期遵守は、顧客との信頼関係を築く上で非常に重要です。
納期を守るためには、以下の取り組みが有効です。
3.7.1.生産計画の見直し:需要予測に基づいた生産計画の作成
- 需要予測を行う。
需要予測を行うことで、将来の需要を予測し、適切な生産計画を作成することができます。
需要予測には、過去の販売データや市場トレンドなどを参考にしましょう。 - 生産計画を作成する。
需要予測に基づいて、生産計画を作成しましょう。
生産計画には、生産量、生産時期、必要なリソースなどを明確に記載しましょう。
3.7.2.工程管理の徹底:各工程の進捗状況を管理し、遅延を防止する
- 各工程の進捗状況を管理する。
各工程の進捗状況を管理することで、遅延が発生している工程を早期に発見することができます。
進捗状況の管理には、かんばん方式や生産管理システムなどを活用すると良いでしょう。 - 遅延を防止する。
遅延が発生している工程に対しては、原因を究明し、対策を講じましょう。
対策としては、人員の増員、設備の増設、作業プロセスの見直しなどがあります。
3.7.3.納期遵守事例
【事例1】
ある工場では、生産管理システムを導入することで、各工程の進捗状況をリアルタイムで把握し、納期遵守率を向上させました。
以前は、各工程の進捗状況を把握することが難しく、納期遅延が発生していましたが、生産管理システムを導入することで、各工程の進捗状況をリアルタイムで把握できるようになり、納期遅延を防止することができました。
【事例2】
ある工場では、ボトルネック工程を特定し、改善することで、リードタイムを短縮し、納期遵守率を向上させました。
ボトルネック工程とは、工程全体の流れを遅くしている工程のことです。
ボトルネック工程を特定し、改善することで、リードタイムを短縮することができ、納期遵守率を向上させることができました。
【事例3】
ある工場では、外注管理を徹底することで、外注先からの納期遅延を防止することができました。
以前は、外注先とのコミュニケーションが不足しており、納期遅延が発生していましたが、外注管理を徹底することで、外注先とのコミュニケーションが円滑になり、納期遅延を防止することができました。
3.8.モラル・モチベーション向上で活力のある工場に
従業員のモラル・モチベーションは、工場の生産性や品質に大きく影響します。
モラル・モチベーション向上のためには、以下の取り組みが有効です。
3.8.1. 従業員満足度調査の実施:従業員の意見を収集し、職場環境改善に繋げる
- 従業員満足度調査を実施する。
従業員満足度調査を実施することで、従業員の意見や要望を収集することができます。
アンケートは、無記名式にすることで、従業員が自由に意見を書きやすいようにしましょう。 - 業員の意見を分析する。
従業員満足度調査の結果を分析し、職場環境の改善に繋げましょう。
例えば、「職場が暗い」という意見が多ければ、照明を改善する、「休憩スペースが狭い」という意見が多ければ、休憩スペースを拡張するなどの対策を講じることができます。
3.8.2.コミュニケーションの活性化:上司と部下、同僚同士のコミュニケーションを促進
- コミュニケーションの機会を増やす。
朝礼や終礼、ミーティングなど、コミュニケーションの機会を増やすことで、従業員同士のコミュニケーションを促進することができます。 - コミュニケーションツールを導入する。
コミュニケーションツールを導入することで、コミュニケーションを活性化することができます。
コミュニケーションツールとしては、chatツール、ビデオ会議システムなどがあります。 - イベントを開催する。
懇親会やレクリエーションなどのイベントを開催することで、従業員同士の交流を深めることができます。
3.8.3.モラル・モチベーション向上事例
【事例1】
ある工場では、従業員満足度調査の結果を基に、職場環境を改善したことで、従業員のモチベーションが向上しました。
従業員満足度調査の結果、「職場が暗い」という意見が多かったため、LED照明を導入し、職場を明るくしました。
その結果、従業員のモチベーションが向上し、生産性も向上しました。
【事例2】
ある工場では、コミュニケーションツールを導入することで、従業員同士のコミュニケーションが活性化し、チームワークが向上しました。
以前は、従業員同士のコミュニケーションが不足していましたが、コミュニケーションツールを導入することで、コミュニケーションが活性化し、チームワークが向上しました。
【事例3】
ある工場では、表彰制度を導入することで、従業員のモチベーション向上を図りました。
表彰制度を導入することで、従業員の頑張りを認め、評価することで、従業員のモチベーション向上を図ることができました。
4.改善をさらに進めるために
4.1.改善効果の測定方法
改善活動の効果を測定するためには、適切な指標を設定することが重要です。
指標は、改善活動の目的や内容によって異なりますが、代表的なものとしては、以下のものがあります。
- 生産性
- 品質
- コスト
- 納期
- 安全性
- 従業員満足度
4.2.改善活動の継続
改善活動は、一度実施すれば終わりではありません。
継続的に改善活動を行うことで、より大きな成果を得ることができます。
改善活動を継続するためには、以下のポイントを押さえましょう。
- PDCAサイクルを回し、定期的に改善活動を見直す。
- 従業員のモチベーションを維持する。
- 改善活動を評価し、改善していく。
4.3.改善事例共有の重要性
改善事例を共有することで、以下のメリットがあります。
- 他の部署や工場の参考になる。
- 従業員のモチベーション向上になる。
- 企業全体の改善意識が高まる。
改善事例を共有するためには、以下の方法があります。
- 社内報に掲載する。
- 掲示板に掲示する。
- ミーティングで発表する。
- 社内イントラネットに掲載する。
4.4.ITツール活用による改善
ITツールを活用することで、改善活動を効率化することができます。
4.4.1.DX推進
DX(デジタルトランスフォーメーション)とは、データとデジタル技術を活用して、企業の業務プロセスや製品、サービス、ビジネスモデルを変革することです。
工場におけるDX推進は、生産性向上、品質管理、コスト削減、人材不足解消など、さまざまな課題解決に役立ちます。
4.4.2.生産管理システム導入
生産管理システムを導入することで、生産計画の立案、工程管理、在庫管理、品質管理などを効率化することができます。
また、データ分析機能を活用することで、問題点の発見や改善策の検討にも役立ちます。
4.4.3.データ分析による効率化
生産データや品質管理データなどを分析することで、問題点の発見や改善策の検討に役立てることができます。
データ分析には、BIツールやデータマイニングツールなどを活用すると良いでしょう。
5.製造業の現場における具体的な改善事例
5.1.工具管理の改善
工具管理を改善することで、工具の紛失や破損を防ぎ、作業効率を向上させることができます。
5.1.1.工具の整理整頓、保管方法の改善
- 工具を整理整頓する。
工具箱や棚に工具を整理整頓することで、必要な工具をすぐに見つけることができます。
工具の種類ごとに整理整頓することで、さらに見つけやすくなります。 - 工具の保管方法を改善する。
工具の保管方法を改善することで、工具の破損や紛失を防ぐことができます。
例えば、工具をシャドウボードに保管することで、工具の置き場所を明確にし、紛失を防ぐことができます。
5.1.2.工具の紛失防止対策
- 工具にラベルを貼る。
工具にラベルを貼ることで、工具の特定を明確にし、紛失を防ぐことができます。 - 工具管理システムを導入する。
工具管理システムを導入することで、工具の貸出・返却状況を管理し、紛失を防ぐことができます。
5.1.3.工具の寿命を延ばすメンテナンス
- 工具のメンテナンスを行う。
工具のメンテナンスを行うことで、工具の寿命を延ばすことができます。
メンテナンス方法は、工具の種類によって異なりますが、定期的に清掃したり、オイルを注したりするなど、簡単なメンテナンスを行うだけでも効果があります。
5.2.作業環境の改善
作業環境を改善することで、作業効率向上、品質管理、安全性の向上などに繋げることができます。
5.2.1.照明の改善
- 照明を明るくする。
照明を明るくすることで、作業者の視認性を高め、作業ミスを減らすことができます。 - 照明の種類を変える。
照明の種類を変えることで、作業環境を改善することができます。
例えば、LED照明は、蛍光灯に比べて電力量削減効果が高く、寿命も長いため、コスト削減にも繋がります。
5.2.2.温度・湿度の管理
- 温度・湿度を適切に管理する。
温度・湿度を適切に管理することで、作業者の健康を守り、快適な作業環境を作ることができます。
温度・湿度の管理には、エアコンや加湿器などを活用しましょう。
5.2.3.騒音・振動対策
- 騒音・振動を低減する。
騒音・振動を低減することで、作業者の集中力を高め、作業ミスを減らすことができます。
騒音・振動対策としては、防音壁や防振ゴムなどを設置する、設備の配置を見直すなどがあります。
5.3.工程改善
工程改善を行うことで、リードタイムの短縮、品質向上、コスト削減などを実現することができます。
5.3.1.工程の標準化
- 工程の標準化を行う。
工程の標準化を行うことで、作業のバラつきをなくし、品質を安定させることができます。
工程の標準化には、標準作業手順書の作成、作業者への教育などが必要です。
5.3.2.ボトルネック工程の改善
- ボトルネック工程を特定する。
ボトルネック工程とは、工程全体の流れを遅くしている工程のことです。
ボトルネック工程を特定するためには、工程分析を行う必要があります。 - ボトルネック工程を改善する。
ボトルネック工程を改善することで、リードタイムを短縮することができます。
ボトルネック工程の改善方法としては、人員の増員、設備の増設、作業プロセスの見直しなどがあります。
5.3.3.レイアウト変更による効率化
- レイアウト変更を行う。
レイアウト変更を行うことで、作業動線を改善し、移動距離を減らすことができます。
また、設備の配置を見直すことで、作業効率を上げることができる場合があります。
5.4.3Dプリンター活用
3Dプリンターを活用することで、試作品製作や治具製作を効率化することができます。
5.4.1.治具製作
- 治具を内製化する。
3Dプリンターで治具を内製化することで、治具製作費用を削減することができます。
また、必要なときに必要な治具を製作することができるため、リードタイムの短縮にも繋がります。
5.4.2.試作品製作
- 試作品を製作する。
3Dプリンターで試作品を製作することで、製品開発を効率化することができます。
3Dプリンターで製作した試作品は、デザイン確認や機能確認などに使用することができます。
5.4.3.3Dプリンター導入事例
【事例1】
ある工場では、3Dプリンターを導入することで、治具製作費用を30%削減することに成功しました。
【事例2】
ある工場では、3Dプリンターを導入することで、試作品製作リードタイムを50%短縮することに成功しました。
5.5.ITツール導入事例
ITツールを導入することで、業務効率化、品質管理、コスト削減などを実現することができます。
▼【製造業向け】原価管理システムと補助金成功事例レポート
https://www.funaisoken.co.jp/dl-contents/smart-factory_smart-factory_01906_S045
▼【製造業向け】BI活用によるデータ集計自動化事例
https://www.funaisoken.co.jp/dl-contents/smart-factory_smart-factory_02476_S045
▼【製造業向け】IoT活用による差別化製品開発解説レポート
https://www.funaisoken.co.jp/dl-contents/smart-factory_smart-factory_02477_S045
6.よくある質問
6.1.改善活動がうまくいかないときは?
改善活動がうまくいかないときは、以下の点を確認してみましょう。
- 改善活動の目的が明確になっているか?
- 従業員が改善活動に積極的に参加しているか?
- 改善活動の効果を測定しているか?
- 改善活動を継続的に行っているか?
6.2.改善アイデアが思いつかないときは?
改善アイデアが思いつかないときは、以下の方法を試してみましょう。
- 現場観察を行う。
- 従業員にインタビューを行う。
- 他社の事例を参考にする。
- ブレインストーミングを行う。
6.3.改善の効果が見えないときは?
改善の効果が見えないときは、以下の点を確認してみましょう。
- 適切な指標を設定しているか?
- 改善活動前後のデータを比較しているか?
- 改善活動を継続的に行っているか?
7.まとめ
本記事では、工場の改善活動について、基本から具体的な事例まで、幅広く解説しました。
工場の改善活動は、企業の成長と発展に不可欠な要素です。
小さな改善を積み重ねていくことで、大きな成果に繋がる可能性があります。
ぜひ、本記事を参考に、工場の改善活動に取り組んでみてください。
8.参考資料・関連情報
- IoT導入による工場の見える化とは?成功事例と現場改革におけるメリット・注意点を紹介
https://smart-factory.funaisoken.co.jp/250108-2/ - 製造業の生産現場で活用するKPI設定:成功事例と必要なデータ活用法を解説
https://smart-factory.funaisoken.co.jp/241226-2/ - 製造現場のデータ可視化:利益向上を実現する最新事例と未来展望
https://smart-factory.funaisoken.co.jp/241206-2/ - 中小製造業の業務改善を通した働き方改革事例と製造プロセスの改善方法
https://smart-factory.funaisoken.co.jp/241007-2/ - 【製造業向け】現場を巻き込んだ業務改善で外せない重要なポイントとは
https://www.funaisoken.co.jp/dl-contents/smart-factory_smart-factory_03657_S045 - 【製造業 原価管理】時流予測レポート2025 (今後の見通し・業界動向・トレンド)
https://www.funaisoken.co.jp/dl-contents/jy-cost_S045 - 【製造業 基幹システム導入・活用】時流予測レポート2025 (今後の見通し・業界動向・トレンド)
https://www.funaisoken.co.jp/dl-contents/jy-core-system_S045 - 【製造業向け】リアルタイム現場データ可視化事例20選
https://www.funaisoken.co.jp/dl-contents/smart-factory_smart-factory_03546_S045 - 【社長特別インタビュー】製造業向け現場主導“完全ペーパレス化”で10人分の工数削減!
https://www.funaisoken.co.jp/dl-contents/smart-factory_smart-factory_03271_S045 - 【製造業向け】データ分析と個別原価取得解説レポート
https://www.funaisoken.co.jp/dl-contents/smart-factory_smart-factory_02507_S045
9.付録:改善アイデアチェックリスト
1.5S活動
1.整理整頓:不要な物を処分し、必要な物を決められた場所に置くようにする
2.清掃:作業場を毎日清掃し、常に清潔な状態を保つ
3.清潔:汚れやゴミが出にくいように工夫する
4.しつけ:決められたルールを守り、整理整頓・清掃・清潔を維持する
5.習慣化:5S活動を習慣化し、継続的に実施する
6.ラベル表示:物の置き場所を分かりやすく表示する
7.工具の整理整頓:工具箱の中を整理整頓し、必要な工具をすぐに取り出せるようにする
8.作業台の清掃:作業台の上を整理整頓し、清掃する
9.床の清掃:床にゴミや油などが落ちていないか確認し、清掃する
10.照明の清掃:照明器具を定期的に清掃し、明るさを確保する
2.ムダの削減
11.動作のムダ:移動距離や作業動作を減らす
12.手待ちのムダ:待ち時間の発生原因を突き止め、解消する
13.不良品のムダ:不良品の発生原因を分析し、対策を講じる
14.在庫のムダ:適切な在庫管理を行い、過剰な在庫を抱えないようにする
15.過剰品質のムダ:必要以上の品質を求めない
16.運搬のムダ:搬送距離や回数を減らす
17.加工のムダ:工程や作業の順番を見直し、無駄な加工を省く
18.設備のムダ:稼働率の低い設備を見直し、必要最低限の設備で運用する
19.エネルギーのムダ:電力やガスの使用量を削減する
20.情報のムダ:情報共有をスムーズに行い、無駄な情報収集や報告を減らす
3.作業効率の向上
21.作業標準化:標準作業手順書を作成し、作業のバラつきをなくす
22.工程の改善:工程の順番やレイアウトを見直し、作業効率を上げる
23.ツールの改善:作業に適したツールを導入し、作業効率を上げる
24.設備の自動化:人手に頼っていた作業を自動化する
25.情報共有の促進:情報共有システムを導入し、情報伝達のロスタイム削減
26.作業環境の改善:照明や温度、湿度などを適切に管理し、快適な作業環境を作る
27.作業姿勢の改善:人間工学的な作業姿勢を導入し、疲労を軽減する
28.多能工化:従業員のスキルアップを図り、複数の作業をこなせるようにする
29.チームワークの向上:チームで協力し、効率的に作業を進める
30.モチベーション向上:従業員のモチベーションを高め、作業効率を上げる
4.品質向上
31.品質管理の徹底:品質管理基準を明確化し、検査体制を強化する
32.不良品発生時の迅速な対応:不良品が発生した場合の原因究明と再発防止策を迅速に行う
33.工程内検査の導入:各工程で検査を行い、不良品の流出を防ぐ
34.材料の品質管理:材料の入荷検査を強化し、品質の安定化を図る
35.設備のメンテナンス:設備の定期的なメンテナンスを行い、故障による不良品発生を防止する
36.作業者の教育:作業者に対する品質管理教育を実施し、品質意識の向上を図る
37.データ分析による品質改善:品質データを分析し、改善に繋げる
38.QCサークル活動:従業員が自主的に品質管理活動に参加する
39.外注先の品質管理:外注先に対しても品質管理基準を設け、品質管理を徹底する
40.クレーム対応の改善:顧客からのクレームに対して迅速かつ丁寧に対応する
5.安全性の向上
41.安全教育の徹底:従業員に対して定期的な安全教育を実施する
42.危険箇所のidentification:工場内の危険箇所を特定し、対策を講じる
43.安全設備の導入:安全設備を導入し、事故を防止する
44.設備の安全点検:設備の定期的な安全点検を実施する
45.作業手順の見直し:安全性を考慮した作業手順を作成する
46.ヒヤリハット活動:ヒヤリハット事例を収集し、分析することで事故を未然に防ぐ
47.安全標語の掲示:安全標語を掲示し、従業員の安全意識を高める
48.安全パトロールの実施:定期的に安全パトロールを実施し、安全状態を確認する
49.緊急時の対応訓練:emergency時の対応訓練を実施する
50.安全目標の設定:安全目標を設定し、達成に向けて取り組む
6.コスト削減
51.電力使用量の削減:省エネ設備の導入や電力会社の見直し
52.燃料費の削減:燃料の種類や燃焼efficiencyの見直し
53.材料費の削減:材料の調達先の見直しや共同購入
54.廃棄物削減:廃棄物の分別を徹底し、リサイクルを推進
55.水道使用量の削減:節水設備の導入や水漏れ防止
56.事務用品費の削減:事務用品の使用量を削減
57.通信費の削減:通信会社やプランの見直し
58.修繕費の削減:予防メンテナンスを徹底し、設備の長寿命化
59.外注費の削減:内製化や外注先の選定
60.人件費の削減:業務効率化による残業時間の削減
7.納期遵守
61.生産計画の見直し:需要予測に基づいた生産計画の作成
62.工程管理の徹底:各工程の進捗状況を管理し、遅延を防止する
63.設備の稼働率向上:設備の故障やトラブルを未然に防ぎ、稼働率を向上させる
64.外注管理の徹底:外注先との連携を強化し、納期遅れを防止する
65.情報共有の促進:生産状況に関する情報をリアルタイムで共有
66.在庫管理の改善:適切な在庫管理を行い、欠品による納期遅れを防止する
67.運搬ルートの改善:搬送ルートの見直しによる搬送時間の短縮
68.作業手順の標準化:標準作業手順書を作成し、作業のバラつきをなくす
69.ボトルネック工程の改善:ボトルネック工程を特定し、改善することで全体のリードタイムを短縮
70.納期遅延防止のための会議:定期的に納期遅延防止のための会議を実施
8.モラル・モチベーション向上
71.従業員satisfactionsurveyの実施:従業員の意見を収集し、職場環境改善に繋げる
72.コミュニケーションの活性化:上司と部下、同僚同士のコミュニケーションを促進
73.表彰制度の導入:従業員の功績を表彰し、モチベーション向上
74.教育研修制度の充実:従業員のスキルアップを支援
75.福利厚生の充実:従業員のwork-lifebalanceを支援
76.イベントの実施:懇親会やレクリエーションなど、従業員同士の交流を深めるイベントを実施
77.提案制度の活用:従業員からの改善提案を積極的に採用
78.目標管理制度の導入:従業員一人ひとりに目標を設定し、達成度を評価
79.ワークライフバランスの推進:flexibleな勤務制度や休暇制度を導入
80.働き方改革:長時間労働の削減や休暇取得の促進
9.環境への配慮
81.省エネ活動の推進:省エネ設備の導入や電力使用量の削減
82.廃棄物削減:廃棄物の分別を徹底し、リサイクルを推進
83.リサイクル活動の推進:資源の有効活用
84.CO2排出量削減:環境負荷の少ない燃料や設備の導入
85.水質汚染防止:排水処理設備の導入や排水管理の徹底
86.大気汚染防止:排気ガス処理設備の導入や排出ガス規制の遵守
87.土壌汚染防止:化学物質の適正管理
88.騒音対策:防音設備の導入や作業時間の調整
89.振動対策:防振設備の導入
90.緑化推進:工場敷地内に緑地を設ける
10.その他
91.3Dプリンターの活用:試作品製作や治具製作に3Dプリンターを活用
92.IoTの活用:センサーなどを活用し、設備の稼働状況や環境データを収集・分析
93.AIの活用:画像分析や需要予測などにAIを活用
94.ドローン活用:工場の検査やsurveillanceにドローンを活用
95.事務部門の効率化:業務プロセスの見直しやITツール導入
96.レイアウト変更:作業スペースの有効活用
97.情報セキュリティ対策:情報漏洩防止対策
98.コンプライアンス遵守:法令遵守
99.防犯対策:theftやvandalism対策
100.地域貢献:地域貢献活動への参加
下記セミナーでは、自社の生き残りをかけたDXの取組を、実際の事例をもとにお話ししています。
改めて、下記のような課題を抱えられている方はぜひご参加ください。
- 多品種少量生産の紡績・繊維業の社長
- 昨今の紡績業界の市場動向を鑑みて、自社はどのように生き残る戦略を立てるべきかを知りたい社長
- 紙日報による手書き運用が続いており、その後のデータ活用ができていない。
- 標準原価で収益管理しているが、材料費高騰・賃上げに対応できていない。
- Excel運用が多く、社内での情報共有がリアルタイムにできない。
- 原価管理をどのように利益UPに結びつけるか具体的な方法を知りたい。
- 経営指標はもちろんだが、現場指標を設けて従業員に経営意識を持たせたい。
https://www.funaisoken.co.jp/seminar/123657
https://www.funaisoken.co.jp/dl-contents/jy-cost_S045