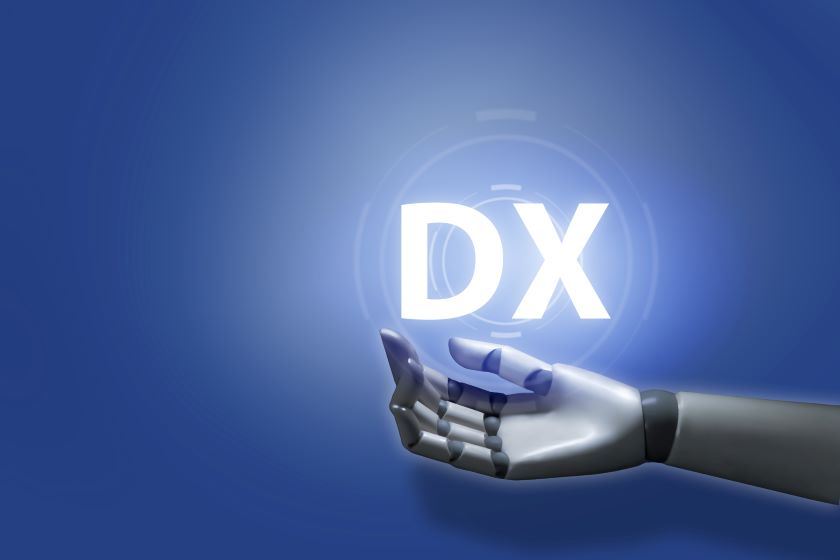
「また失敗か…」は、もう終わりに。コスト超過、現場の混乱、使われない新システム…その“失敗フラグ”、回避できます。
2025.09.01
「鳴り物入りで導入したはずの基幹システムが、いつの間にか誰も使わない“巨大なExcel”と化している…」
「『ウチの業務は特殊だから』という現場の声に押され、カスタマイズを繰り返した結果、莫大なコストと複雑怪奇なシステムだけが残った…」
「グローバル展開を見据えてシステムを統一したいが、どこから手をつければいいのか、想像もつかない…」
製造業の経営者、IT責任者の皆様。このような悩みに、一つでも心当たりはないでしょうか?
人手不足、サプライチェーンの複雑化、そして激化するグローバル競争。製造業を取り巻く環境が厳しさを増す中、的確な経営判断と現場の生産性向上を実現する「基幹システム」の重要性は、かつてないほど高まっています。
しかし、その重要性を理解していながらも、多くの企業が基幹システムの刷新プロジェクトで苦戦を強いられているのが現実です。時間とコストをかけたにも関わらず、ROI(投資対効果)が見えないばかりか、かえって現場の混乱を招いてしまうケースも少なくありません。
なぜ、これほどまでに基幹システムの導入は難しいのでしょうか?
なぜ、あなたの会社のプロジェクトは“失敗”という名の沼にハマるのか?
多くの失敗プロジェクトには、共通する「落とし穴」が存在します。
落とし穴1:「ベンダーに丸投げ」という幻想
「専門家にお願いすれば、うまくやってくれるだろう」。
これは非常に危険な考え方です。
自社の業務を最も理解しているのは、現場の皆さん自身です。
目的や要件が曖昧なままプロジェクトを進め、ベンダーの提案を鵜呑みにした結果、「こんなはずではなかった」というボタンの掛け違いが起こります。システムの完成間際になって、現場の業務に全くフィットしないことが発覚するのです。
落とし穴2:「ウチは特別」が招く、カスタマイズ地獄
「長年このやり方でやってきた」「この業務は特殊だから、システムを合わせるべきだ」。
現場からのこうした声は、尊重すべき部分もあります。
しかし、その声に無批判に従い、安易なカスタマイズを繰り返せばどうなるでしょうか。
追加コストは雪だるま式に膨れ上がり、システムの構造は複雑化。将来のアップデートにも対応できず、結果的に「塩漬け」システムを生み出す温床となります。
落とし穴3:完璧を目指す「ビッグバン・アプローチ」の罠
「せっかく刷新するのだから、全部門の課題を一度に解決する完璧なシステムを」。
この壮大な計画は、一見すると理想的に見えます。
しかし、大規模な一括導入(ビッグバン・アプローチ)は、要件定義の長期化、開発中の仕様変更の続出、そして導入時の現場の急激な変化に対する抵抗など、プロジェクトが頓挫するリスクをあらゆる側面に抱えています。一つの失敗が、プロジェクト全体の失敗に直結してしまうのです。
あなたの会社は、これらの落とし穴に向かって進んでいませんか?
もし、少しでも不安を感じたなら、ぜひ一度立ち止まって考えてみてください。失敗には必ず理由があり、そして成功には必ず法則があります。
失敗しないための「羅針盤」を手に入れる
では、どうすればこれらのリスクを回避し、プロジェクトを成功に導くことができるのでしょうか。その鍵は、闇雲に突き進むのではなく、明確な「羅針盤」を持って航海に出ることにあります。
1.「何のために」を突き詰める(システム化計画・RFPの重要性)
プロジェクトの成否は、最初の「計画策定」で9割決まります。
自社の課題を全社横断で洗い出し、「何のためにシステムを刷新するのか」という目的を明確にすること。
そして、その目的を達成するための要求を具体的に記した「提案依頼書(RFP)」を作成することが、ベンダーとの的確なコミュニケーション、そして自社に最適なパートナー選定の第一歩となります。
2.一歩ずつ、着実に進む「段階的導入」という賢い選択
一度に全てを変えようとするのではなく、業務インパクトが大きく、かつ成功しやすい領域からスモールスタートする。
そして、小さな成功体験を積み重ねながら、段階的に適用範囲を広げていく。この「マイクロリリース」と呼ばれるアプローチは、リスクを最小限に抑え、現場の納得感を得ながら、着実に成果を出すための極めて有効な戦略です。
この「マイクロリリース」という手法、具体的にどう計画し、どう進めていけば良いのか、その実践的なアプローチにご興味はありませんか?来るセミナーでは、この手法を活用してグローバルERPの短期導入に成功したリアルな事例を、ゲスト講師から直接お話しいただきます。
3.「業務を、標準に合わせる」勇気(Fit to Standard)
「システムに業務を合わせる」と聞くと、抵抗を感じる方も多いかもしれません。しかし、世界のベストプラクティスが凝縮されたERPの標準機能は、自社の業務プロセスを見直す絶好の機会を与えてくれます。不要なカスタマイズを徹底的に排除することで、コストを削減し、短期導入を実現する。
この「Fit to Standard」を成功させるためには、当初の目的がブレないようにするための具体的なポイントが存在します。
4.「IT部門任せ」からの脱却(部門横断の実行体制)
基幹システムは、IT部門だけのものではありません。実際にシステムを使うのは、現場の全部門です。プロジェクトの初期段階から、次世代を担う若手や中堅社員を各部門から巻き込み、当事者意識を持たせることが不可欠です。彼らが部門の壁を越えて連携することで、全社的なシステム活用が初めて実現するのです。
成功事例から学ぶ、次の一手
「理屈はわかるが、本当にそんなことが可能なのか?」
そう思われるかもしれません。
今回ご紹介するセミナーでは、机上の空論ではない、生々しい成功事例の数々をお届けします。
1度頓挫したERP刷新プロジェクトを立て直し、成功させた事例
グローバルERPを驚くべき短期間で導入に成功したプロジェクト事例
次世代メンバーが主導し、部門横断的な新基幹システム導入に成功した事例
など、あなたの会社が今まさに直面しているであろう課題を乗り越えた、先人たちの知恵と経験に触れることができます。
特に、第2講座にご登壇いただくNSW株式会社 谷口美奈子氏の講演は必見です。
実際にプロジェクトマネージャーとして、スコープを絞ったグローバルERPの短期導入を成功させた当事者から語られる「短期導入が達成できた5つのポイント」は、明日からのあなたの行動を変える、具体的なヒントに満ちています。
【セミナーのご案内】コストダウン!成功率UP!!失敗しない基幹システム導入の実践
もし、あなたが、
基幹システム導入の失敗リスクを、限りなくゼロに近づけたい
グローバルで戦える、統一的なシステム基盤を構築したい
現場が積極的に活用し、明確なROIを生み出すシステムを導入したい
次世代の人材を育てながら、全社一丸となってプロジェクトを推進したい
と本気でお考えなら、このセミナーはあなたのためのものです。
多くの企業がなぜ失敗し、成功企業は何を実践したのか。
その本質を理解し、自社の成功に向けた具体的なアクションプランを手に入れる、またとない機会です。
漠然とした不安を、成功への確信に変えませんか?
皆様のご参加を、心よりお待ちしております。
▼セミナー詳細・お申し込みはこちらから
https://www.funaisoken.co.jp/seminar/132595 「鳴り物入りで導入したはずの基幹システムが、いつの間にか誰も使わない“巨大なExcel”と化している…」
「『ウチの業務は特殊だから』という現場の声に押され、カスタマイズを繰り返した結果、莫大なコストと複雑怪奇なシステムだけが残った…」
「グローバル展開を見据えてシステムを統一したいが、どこから手をつければいいのか、想像もつかない…」
製造業の経営者、IT責任者の皆様。このような悩みに、一つでも心当たりはないでしょうか?
人手不足、サプライチェーンの複雑化、そして激化するグローバル競争。製造業を取り巻く環境が厳しさを増す中、的確な経営判断と現場の生産性向上を実現する「基幹システム」の重要性は、かつてないほど高まっています。
しかし、その重要性を理解していながらも、多くの企業が基幹システムの刷新プロジェクトで苦戦を強いられているのが現実です。時間とコストをかけたにも関わらず、ROI(投資対効果)が見えないばかりか、かえって現場の混乱を招いてしまうケースも少なくありません。
なぜ、これほどまでに基幹システムの導入は難しいのでしょうか?
なぜ、あなたの会社のプロジェクトは“失敗”という名の沼にハマるのか?
多くの失敗プロジェクトには、共通する「落とし穴」が存在します。
落とし穴1:「ベンダーに丸投げ」という幻想
「専門家にお願いすれば、うまくやってくれるだろう」。
これは非常に危険な考え方です。
自社の業務を最も理解しているのは、現場の皆さん自身です。
目的や要件が曖昧なままプロジェクトを進め、ベンダーの提案を鵜呑みにした結果、「こんなはずではなかった」というボタンの掛け違いが起こります。システムの完成間際になって、現場の業務に全くフィットしないことが発覚するのです。
落とし穴2:「ウチは特別」が招く、カスタマイズ地獄
「長年このやり方でやってきた」「この業務は特殊だから、システムを合わせるべきだ」。
現場からのこうした声は、尊重すべき部分もあります。
しかし、その声に無批判に従い、安易なカスタマイズを繰り返せばどうなるでしょうか。
追加コストは雪だるま式に膨れ上がり、システムの構造は複雑化。将来のアップデートにも対応できず、結果的に「塩漬け」システムを生み出す温床となります。
落とし穴3:完璧を目指す「ビッグバン・アプローチ」の罠
「せっかく刷新するのだから、全部門の課題を一度に解決する完璧なシステムを」。
この壮大な計画は、一見すると理想的に見えます。
しかし、大規模な一括導入(ビッグバン・アプローチ)は、要件定義の長期化、開発中の仕様変更の続出、そして導入時の現場の急激な変化に対する抵抗など、プロジェクトが頓挫するリスクをあらゆる側面に抱えています。一つの失敗が、プロジェクト全体の失敗に直結してしまうのです。
あなたの会社は、これらの落とし穴に向かって進んでいませんか?
もし、少しでも不安を感じたなら、ぜひ一度立ち止まって考えてみてください。失敗には必ず理由があり、そして成功には必ず法則があります。
失敗しないための「羅針盤」を手に入れる
では、どうすればこれらのリスクを回避し、プロジェクトを成功に導くことができるのでしょうか。その鍵は、闇雲に突き進むのではなく、明確な「羅針盤」を持って航海に出ることにあります。
1.「何のために」を突き詰める(システム化計画・RFPの重要性)
プロジェクトの成否は、最初の「計画策定」で9割決まります。
自社の課題を全社横断で洗い出し、「何のためにシステムを刷新するのか」という目的を明確にすること。
そして、その目的を達成するための要求を具体的に記した「提案依頼書(RFP)」を作成することが、ベンダーとの的確なコミュニケーション、そして自社に最適なパートナー選定の第一歩となります。
2.一歩ずつ、着実に進む「段階的導入」という賢い選択
一度に全てを変えようとするのではなく、業務インパクトが大きく、かつ成功しやすい領域からスモールスタートする。
そして、小さな成功体験を積み重ねながら、段階的に適用範囲を広げていく。この「マイクロリリース」と呼ばれるアプローチは、リスクを最小限に抑え、現場の納得感を得ながら、着実に成果を出すための極めて有効な戦略です。
この「マイクロリリース」という手法、具体的にどう計画し、どう進めていけば良いのか、その実践的なアプローチにご興味はありませんか?来るセミナーでは、この手法を活用してグローバルERPの短期導入に成功したリアルな事例を、ゲスト講師から直接お話しいただきます。
3.「業務を、標準に合わせる」勇気(Fit to Standard)
「システムに業務を合わせる」と聞くと、抵抗を感じる方も多いかもしれません。しかし、世界のベストプラクティスが凝縮されたERPの標準機能は、自社の業務プロセスを見直す絶好の機会を与えてくれます。不要なカスタマイズを徹底的に排除することで、コストを削減し、短期導入を実現する。
この「Fit to Standard」を成功させるためには、当初の目的がブレないようにするための具体的なポイントが存在します。
4.「IT部門任せ」からの脱却(部門横断の実行体制)
基幹システムは、IT部門だけのものではありません。実際にシステムを使うのは、現場の全部門です。プロジェクトの初期段階から、次世代を担う若手や中堅社員を各部門から巻き込み、当事者意識を持たせることが不可欠です。彼らが部門の壁を越えて連携することで、全社的なシステム活用が初めて実現するのです。
成功事例から学ぶ、次の一手
「理屈はわかるが、本当にそんなことが可能なのか?」
そう思われるかもしれません。
今回ご紹介するセミナーでは、机上の空論ではない、生々しい成功事例の数々をお届けします。
1度頓挫したERP刷新プロジェクトを立て直し、成功させた事例
グローバルERPを驚くべき短期間で導入に成功したプロジェクト事例
次世代メンバーが主導し、部門横断的な新基幹システム導入に成功した事例
など、あなたの会社が今まさに直面しているであろう課題を乗り越えた、先人たちの知恵と経験に触れることができます。
特に、第2講座にご登壇いただくNSW株式会社 谷口美奈子氏の講演は必見です。
実際にプロジェクトマネージャーとして、スコープを絞ったグローバルERPの短期導入を成功させた当事者から語られる「短期導入が達成できた5つのポイント」は、明日からのあなたの行動を変える、具体的なヒントに満ちています。
【セミナーのご案内】コストダウン!成功率UP!!失敗しない基幹システム導入の実践
もし、あなたが、
基幹システム導入の失敗リスクを、限りなくゼロに近づけたい
グローバルで戦える、統一的なシステム基盤を構築したい
現場が積極的に活用し、明確なROIを生み出すシステムを導入したい
次世代の人材を育てながら、全社一丸となってプロジェクトを推進したい
と本気でお考えなら、このセミナーはあなたのためのものです。
多くの企業がなぜ失敗し、成功企業は何を実践したのか。
その本質を理解し、自社の成功に向けた具体的なアクションプランを手に入れる、またとない機会です。
漠然とした不安を、成功への確信に変えませんか?
皆様のご参加を、心よりお待ちしております。
▼セミナー詳細・お申し込みはこちらから
https://www.funaisoken.co.jp/seminar/132595