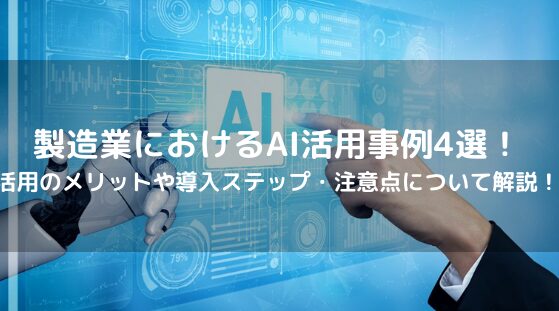
製造業におけるAI活用事例4選!活用のメリットや導入ステップ、注意点について解説!
2024.04.01
近年では、様々な分野でAI(人工知能)が活用され大きな効果を出しています。
当然ながら製造業でもAIの活用が注目されています。
製造業におけるAI活用は非常に大きな効果をもたらすことが期待されており、既に日本国内でも、AIを活用することでスマートファクトリー構想を実現している工場も存在している状態です。具体的には、AIによる需要予測、画像解析、異常検知・故障予知の分野において、成果を上げています。
現在では、様々なAIソリューションが散見されるため、
どのような業務においてAIが活用できるのかわからない!
結局自社に最適なAI活用法がわからない!
ディープラーニングやアルゴリズムなど、AIの知識が高度・専門的過ぎてよくわからない!
と感じる方も多いのではないでしょうか。
本記事では、製造業におけるAI活用を検討されてる方に向けて、「工場におけるAI活用法4選」「自社に最適なAIを選ぶときの基準」「AI導入の具体的なステップ」「AI活用の課題と注意点」等について記載しています。
情報収集のお役に立てば幸いです。
1.製造業におけるAIの現状
AI活用がバズワードとなり久しいですが、実際に様々な分野で、目に見えるところ/見えないところでAIが活用され大きな効果を出しています。
当然ながら製造業でもAIの活用が注目されています。
全業種おいて30%を占める製造業ですが、AI活用は実際どのようになっているのでしょうか。
少し古い資料にはなりますが、財務省の調査データによると、2018年時点で企業全体の10.9%が“AIを活用している“にとどまっており、製造業も11.6%とほぼ変わらない結果となっています。
資本力のある大企業で16.5%、中堅以下の会社では5.6%と、非常に限定的な活用状況と言わざるを得ないのが現状です。
ちなみに、ここでのAI活用は「AIチャットボット」がほとんどのようです。
2024年時点でも少しずつ進捗はしているものの、AI活用に関しては大きな改善はまだ見られないと感じています。
一方で昨今の生成AIの台頭もあり、今後AI活用は急激に飛躍するかもしれません。
⇒関連記事:AI導入で製造業の仕事はなくなるのか?2024年の展望
2.製造業におけるAI活用のメリット
AI活用のメリットを説明する前に、よく混同されがちなAI活用とRPA活用について説明します。
これらはよく混同されがちですが、以下のように違いがあります。
RPA=定型の反復作業の代替Excelの転記など
AI=属人的、ベテラン作業の代替
RPAはご存知の方も多いと思いますが、AI活用についてはいかがでしょうか。
AIもRPAも簡単な作業を代替するものだと思っていた方もいるのではないでしょうか。
AI活用とは、過去の大量データから最適解を提示することを指します。
この作業は、ベテラン(職人)の過去の経験から一番良い手を見つけ出すことに似ています。
ベテラン(職人)が凄いのは、過去の経験値をたくさん持っているということです。
AIはその知識(データ)を学習することで、与えられた条件での最適解を選択することができます。
AI活用はベテラン(職人)作業を代替することができるのです。
AIもRPAも有意義な技術ですが、これらを混同してはいけません。
RPAに難しいことをさせても良くありませんし(技術的なハードルがある)、AIに簡単な反復業務をさせてもいけません(費用対効果が合わない)。
それらを踏まえて、以下にAI活用のメリットを示します。
■労働力不足が解消する
少子高齢化による労働力不足や製造業を選択する若者の減少が問題になっており、製造業でも年々人手が足りなくなっています。
しかし、AIを導入することで、属人的業務、ベテラン業務の自動化や効率化を実現でき、限られた人員でも業務をスムーズにこなせるようになります。
■コスト削減・生産性が向上する
AIを活用することで業務判断が標準化され、ヒューマンエラーや部品ロスなどを減らすことができるため、コスト削減や生産性向上も期待できます。
すべてが数値化されるようになり、且つ課題の明確化や数値目標の設定もしやすくなるため、現場との合意も形成することができます。
■製造の品質や安全性が向上する
AIの有効活用により危険な作業を機械に任せられるため、事故の防止につながります。
ヒューマンエラーによる不良品の発生や異物の混入も避けることができます。
属人化した作業を自動化でき、製品品質も安定させられるでしょう。
3.工場におけるAI活用成功事例4選
次に、工場における、AI活用成功事例を4つ紹介いたします。
■見積業務におけるAI活用成功事例
【課題感】
複雑形状の試作(一品モノ)の受注が多く、過去の図面情報・製作情報の検索に多くの時間と労力がかかっていました。
見積り作業が属人化し、過去の情報も「わかる人にはわかる」状態となっており、ベテランでなければ精緻な見積は出来ず、新人などが出来るものではありませんでした。
【AI活用】
見積り業務に必要な過去案件の検索において、AIを活用して「いつでも」「だれでも」「簡単に」過去案件を検索・参照できる仕組みを構築しました。
これは、過去の図面データをAIに学習させることで、類似した図面をAIが検索します。
類似図面が見つかれば、その際に紐づけておいた営業情報、加工情報などを一緒に提示するようにしました。
【効果】
過去情報を探す時間は従来の1/4となり、これまでバラバラだった過去情報が一元管理され、「それを知っていたら簡単に見積を出せたのに・・」というムダな状況がなくなり業務が効率化されました。
また、この仕組みを生産計画部門でも利用しており、生産計画部門も業務の効率化に繋がりました。
このシステムは紐づける情報次第で、様々な部門で活用することが出来ます。
⇒関連記事:AI見積り導入の費用感やAI選定方法は?導入効果や進め方についても解説!
■生産計画業務におけるAI活用成功事例
【課題感】
生産計画(工程計画)には<設備条件><材料条件><担当者スキル><在庫条件><納期条件><生産状況>等が複雑に絡み合い、多面的な知識と豊富な経験が必要で作業立案はベテラン1名で担当していました。
経験の浅い作業員では、立案ミスをする可能性があり、トラブルや運転停止のリスクが高いため仕事を任せられない現状がありました。
【AI活用】
数理最適化を用いて生産計画を最適化するシステムを構築しました。
構築にあたり、担当者の考え方やロジックをドキュメントに落とし込み、システム上で最適化した計画を立案・ガントチャートにて表示しました。
システムの見た目は通常のスケジューラーと似ていますが、裏で計算できるロジックは、通常のスケジューラーでは出来ない条件を計算実施しています。
立案後に担当者が調整可能な機能も実装し、特急品やイレギュラー対応も可能なシステムとしています。
【効果】
属人化していた生産計画について「いつもで」「だれでも」「同じレベル(質)」で生産計画を立案出来るようになりました。
生産計画担当者は属人化しやすく、ノウハウが担当者のみに蓄積される為、後継者の育成に数年~数十年と非常に時間のかかるものでした。
システム化により、技術継承にも継承しました。生産計画をある程度誰でも立案出来るようになり、後継者の育成が難しい「計画立案者の後継者問題」から解放されました。
⇒関連記事:AIを活用した生産計画自動作成システムとは?
⇒関連記事:生産計画のAI活用を成功させるポイントとは
■外観検査業務におけるAI活用成功事例
【課題感】
外観検査領域においては、従来の画像処理カメラやセンサを用いて、できる限りの自動化をおこなっている企業は数多く存在します。
それでも、従来のカメラで判別できない場合は、やむを得ず目視検査を続けるしかありません。
ただ、目視検査は、担当者の感覚に頼っている場合が多く、担当者毎のばらつきがあり、担当者自身もその時の体調などで判断が変わってしまうことがあります。
もしくは、検査自体が熟練した担当者しかできない=属人化しているケースも多くあります。
担当者で判断が変わったり、熟練者しかできないという検査はモノづくりにおいて、かなり問題があることですが、「実際そのような状況に結果的になってしまっている」というケースが多くあります。
【AI活用】
従来の画像処理では、判断できなかった事象に対して、AIを搭載したカメラを用いることでうまく検査が出来るようになります。
例えば、透明なカップの外観や板地に模様がある中での傷の検査など、従来人の目でした判断がつかなかった事象についてもうまくとらえられるようになりました
【効果】
目視検査は人員を集めることも大変ですし、判断は標準化させることも難しい業務です。
その検査自体が、職人技なのであれば、さらに問題は複雑です。
AIカメラで代替させることで、品質基準は統一化され、365日24時間、同じ品筒基準で検査をしてくれるようになりました。
また、システム化により後継者の育成が難しい「外観検査の後継者問題」からも解放されました。
⇒関連記事:AI外観検査とは?従来の画像検査との違い、導入のメリットや注意点とは?
■在庫管理業務におけるAI活用成功事例
【課題感】
発注担当者は、在庫切れが起こらないよう日々在庫確認と発注作業が必要でした。
その一方で、確認作業や発注作業のタイミングは各担当者に一任されており、社内に統一された明確なルールはなく、発注タイミングは個人の感覚に任せられていました。
売上予測や発注業務が属人化しており勘や経験を必要とする業務となっていました。
【AI活用】
過去の商品/在庫/実績/仕入先データ+直近の売上/繁忙期/リードタイム等を機械学習により発注の予測モデルを構築しました。
予測モデルを構築するには、「何が発注に寄与するか」を担当者からヒアリングしながらデータ分析を行いました。
売上予測をもとに品目ごとに在庫切れのタイミングを特定することで、最適な発注タイミングをシステム上で提示します。
自動発注は行わず、最終確認は人間が行い発注をします。
【効果】
属人化していた発注タイミングを「いつもで」「だれでも」「同じレベル(質)」で判断が出来るようになりました。
感覚的(決まりがあるが決まっているものが感覚的な場合もあり)な発注は在庫の持ち過ぎ、持たな過ぎに直結します。
システム構築により、担当者毎の発注に対する質が標準化(凸凹がなくなり)され、在庫の過剰/不足が低減に繋がりました。
4.自社に最適なAIを選ぶときの基準
では、自社の状況に合ったAIはどのように選定していけば良いのでしょうか?以下の5つの基準を鑑みながら、選定していくことが重要です。
1. 目的とニーズの明確化
まずは、自社の目的とニーズを明確にすることが重要です。
AIを導入する目的や期待する効果、解決したい課題などを具体的に定義しましょう。
2. 機能と性能
AIの機能や性能が自社のニーズと一致しているかを確認しましょう。
具体的な要件や予算に基づいて、必要な機能や性能を評価します。
3. データの要件と適合性
自社のデータに合わせてAIが適切に動作するかを確認しましょう。
データの形式、量、品質などに対応できるかを評価します。
4. 解釈可能性と透明性
AIの結果を解釈できるかどうか、判断理由が明示されているかを確認しましょう。
特に、意思決定に影響を与える場合は、解釈可能性が求められます。
5. 可用性と拡張性
AIの実装および展開の容易さ、基幹システムの連携の可否、サポートやメンテナンスの提供、将来の拡張性などを評価しましょう。
自社の状況と予算に適合しているかを検討します。
これらの基準を元に、自社に最適なAIを選択することが重要です。
5.AI導入の具体的なステップ
AIを導入する際は、以下の5つのステップを踏み、着実にプロジェクトを進めていくことが重要です。
1. 目的とニーズの明確化
AIを導入する目的やニーズを明確に定義しましょう。
例えば、業務プロセスの効率化、顧客対応の向上、品質管理の強化、従業員の教育負担の軽減など、具体的な目標を設定します。
2. データの収集と前処理
AIはデータに基づいて学習し予測を行いますので、必要なデータを収集し、必要な前処理を行いましょう。
データの品質や量、形式にも注意を払いましょう。
3. AIモデルの選択
導入するAIの種類やモデルを選定します。
自然言語処理によるチャットボット、画像認識による品質管理システムなど、目的やニーズに合ったAIモデル・ツールを選びましょう。
4. モデルの学習と評価
選んだAIモデルをデータで学習させ、その性能を評価します。
学習方法やパラメータの調整によってモデルの精度を高めていきます。
5. 導入と運用
学習したAIモデルを実際の業務に導入し、運用します。
トライアル期間を設け、結果を評価しながら適切な調整や改善を行いましょう。
これらのステップを踏みながら、AIを導入することで効果的な活用ができるでしょう。
6.AI活用の課題と注意点
AI導入おけるもっと重要な箇所は、1番初めの「課題の抽出、目的とニーズの明確化」です。
<どこが課題>で<何を目的に導入するのか>をユーザー側は明確にする必要があります。
<目的>が曖昧だったり、ブレてしまうと、どういうAIを選定するか?を考える際に、AIが出来ることが優先され、結果的に導入されたもののさほど意味がない(当初の課題を解決してくれない)ものになってしまいます。
これを回避するには、課題抽出の時点からある程度のAIの知識(何が出来て何が出来ないか)を知っておく必要があります。
課題のすべてをAIが解決してくれるとは限らないのです。
AIベンダーはユーザーから与えられた要望に対して、自社製品を使って必死に知恵を絞り出します。
しかし、根本的に課題抽出から間違っている場合も多くあります。
「そもそもそれはAIで解決すべきではない」という結論です。
課題に対して、解決方法(アプローチ方法)はいくつかあります。
課題抽出の段階で、どの方法なら出来そうか?技術的なハードルを目途つけながらやっていくことが必要です。
全く考えないまま(知識がないまま)実施していくと、いわゆる「ベンダーの言いなり」となり、ベンダーが主導権を握り、自社ではハンドリングが出来なくなっていきます。
7.まとめ
船井総研では、上流の課題抽出からお客様と一緒に考え、取り上げられた課題は「今のAI技術で解決出来そうか」や、「技術的なハードルはどこか」を考慮しながらアドバイスを行っていきます。
AIプロジェクトだけではなく、様々なシステム開発に携わってきた観点からお客様の課題に対して「課題抽出→企画→要求取りまとめ→ベンダー選定→要件定義→システム開発→検証→ゴール(運用)」までお客様と共に伴走をしていきます。
工場内の課題に対して、「たくさん課題があるが何から手を付けるべきはわからない。」「AIを活用したいが、そもそもAIが必要なのか、どこに使えそうかわからない」という方はぜひ、船井総研までご相談下さい。
無料経営相談はこちら
無料ダウンロード!!
2024年AI活用時流予測レポート ~今後の業界動向・トレンドを予測~
▼事例レポート無料ダウンロードお申し込みはこちら▼
目次
1、製造業AI業界の現状
2、2023年製造業AI業界はこうなる!
3、2023年実践していただきたいこと
4、どの業務・工程でもAIは活用できる「業務別・工程別のAI活用」
5、国内中小製造業におけるAI導入事例
中小製造業のAI活用の最新事例と導入事例この1冊にまとめました。
AI活用術について「考え方」と「具体的な方法」を例を出して解説し、さらに導入事例を掲載することでAI活用の具体的な取り組み方が分かる資料になっております。
https://www.funaisoken.co.jp/dl-contents/jy-ai_S045 近年では、様々な分野でAI(人工知能)が活用され大きな効果を出しています。
当然ながら製造業でもAIの活用が注目されています。
製造業におけるAI活用は非常に大きな効果をもたらすことが期待されており、既に日本国内でも、AIを活用することでスマートファクトリー構想を実現している工場も存在している状態です。具体的には、AIによる需要予測、画像解析、異常検知・故障予知の分野において、成果を上げています。
現在では、様々なAIソリューションが散見されるため、
どのような業務においてAIが活用できるのかわからない!
結局自社に最適なAI活用法がわからない!
ディープラーニングやアルゴリズムなど、AIの知識が高度・専門的過ぎてよくわからない!
と感じる方も多いのではないでしょうか。
本記事では、製造業におけるAI活用を検討されてる方に向けて、「工場におけるAI活用法4選」「自社に最適なAIを選ぶときの基準」「AI導入の具体的なステップ」「AI活用の課題と注意点」等について記載しています。
情報収集のお役に立てば幸いです。
1.製造業におけるAIの現状
AI活用がバズワードとなり久しいですが、実際に様々な分野で、目に見えるところ/見えないところでAIが活用され大きな効果を出しています。
当然ながら製造業でもAIの活用が注目されています。
全業種おいて30%を占める製造業ですが、AI活用は実際どのようになっているのでしょうか。
少し古い資料にはなりますが、財務省の調査データによると、2018年時点で企業全体の10.9%が“AIを活用している“にとどまっており、製造業も11.6%とほぼ変わらない結果となっています。
資本力のある大企業で16.5%、中堅以下の会社では5.6%と、非常に限定的な活用状況と言わざるを得ないのが現状です。
ちなみに、ここでのAI活用は「AIチャットボット」がほとんどのようです。
2024年時点でも少しずつ進捗はしているものの、AI活用に関しては大きな改善はまだ見られないと感じています。
一方で昨今の生成AIの台頭もあり、今後AI活用は急激に飛躍するかもしれません。
⇒関連記事:AI導入で製造業の仕事はなくなるのか?2024年の展望
2.製造業におけるAI活用のメリット
AI活用のメリットを説明する前に、よく混同されがちなAI活用とRPA活用について説明します。
これらはよく混同されがちですが、以下のように違いがあります。
RPA=定型の反復作業の代替Excelの転記など
AI=属人的、ベテラン作業の代替
RPAはご存知の方も多いと思いますが、AI活用についてはいかがでしょうか。
AIもRPAも簡単な作業を代替するものだと思っていた方もいるのではないでしょうか。
AI活用とは、過去の大量データから最適解を提示することを指します。
この作業は、ベテラン(職人)の過去の経験から一番良い手を見つけ出すことに似ています。
ベテラン(職人)が凄いのは、過去の経験値をたくさん持っているということです。
AIはその知識(データ)を学習することで、与えられた条件での最適解を選択することができます。
AI活用はベテラン(職人)作業を代替することができるのです。
AIもRPAも有意義な技術ですが、これらを混同してはいけません。
RPAに難しいことをさせても良くありませんし(技術的なハードルがある)、AIに簡単な反復業務をさせてもいけません(費用対効果が合わない)。
それらを踏まえて、以下にAI活用のメリットを示します。
■労働力不足が解消する
少子高齢化による労働力不足や製造業を選択する若者の減少が問題になっており、製造業でも年々人手が足りなくなっています。
しかし、AIを導入することで、属人的業務、ベテラン業務の自動化や効率化を実現でき、限られた人員でも業務をスムーズにこなせるようになります。
■コスト削減・生産性が向上する
AIを活用することで業務判断が標準化され、ヒューマンエラーや部品ロスなどを減らすことができるため、コスト削減や生産性向上も期待できます。
すべてが数値化されるようになり、且つ課題の明確化や数値目標の設定もしやすくなるため、現場との合意も形成することができます。
■製造の品質や安全性が向上する
AIの有効活用により危険な作業を機械に任せられるため、事故の防止につながります。
ヒューマンエラーによる不良品の発生や異物の混入も避けることができます。
属人化した作業を自動化でき、製品品質も安定させられるでしょう。
3.工場におけるAI活用成功事例4選
次に、工場における、AI活用成功事例を4つ紹介いたします。
■見積業務におけるAI活用成功事例
【課題感】
複雑形状の試作(一品モノ)の受注が多く、過去の図面情報・製作情報の検索に多くの時間と労力がかかっていました。
見積り作業が属人化し、過去の情報も「わかる人にはわかる」状態となっており、ベテランでなければ精緻な見積は出来ず、新人などが出来るものではありませんでした。
【AI活用】
見積り業務に必要な過去案件の検索において、AIを活用して「いつでも」「だれでも」「簡単に」過去案件を検索・参照できる仕組みを構築しました。
これは、過去の図面データをAIに学習させることで、類似した図面をAIが検索します。
類似図面が見つかれば、その際に紐づけておいた営業情報、加工情報などを一緒に提示するようにしました。
【効果】
過去情報を探す時間は従来の1/4となり、これまでバラバラだった過去情報が一元管理され、「それを知っていたら簡単に見積を出せたのに・・」というムダな状況がなくなり業務が効率化されました。
また、この仕組みを生産計画部門でも利用しており、生産計画部門も業務の効率化に繋がりました。
このシステムは紐づける情報次第で、様々な部門で活用することが出来ます。
⇒関連記事:AI見積り導入の費用感やAI選定方法は?導入効果や進め方についても解説!
■生産計画業務におけるAI活用成功事例
【課題感】
生産計画(工程計画)には<設備条件><材料条件><担当者スキル><在庫条件><納期条件><生産状況>等が複雑に絡み合い、多面的な知識と豊富な経験が必要で作業立案はベテラン1名で担当していました。
経験の浅い作業員では、立案ミスをする可能性があり、トラブルや運転停止のリスクが高いため仕事を任せられない現状がありました。
【AI活用】
数理最適化を用いて生産計画を最適化するシステムを構築しました。
構築にあたり、担当者の考え方やロジックをドキュメントに落とし込み、システム上で最適化した計画を立案・ガントチャートにて表示しました。
システムの見た目は通常のスケジューラーと似ていますが、裏で計算できるロジックは、通常のスケジューラーでは出来ない条件を計算実施しています。
立案後に担当者が調整可能な機能も実装し、特急品やイレギュラー対応も可能なシステムとしています。
【効果】
属人化していた生産計画について「いつもで」「だれでも」「同じレベル(質)」で生産計画を立案出来るようになりました。
生産計画担当者は属人化しやすく、ノウハウが担当者のみに蓄積される為、後継者の育成に数年~数十年と非常に時間のかかるものでした。
システム化により、技術継承にも継承しました。生産計画をある程度誰でも立案出来るようになり、後継者の育成が難しい「計画立案者の後継者問題」から解放されました。
⇒関連記事:AIを活用した生産計画自動作成システムとは?
⇒関連記事:生産計画のAI活用を成功させるポイントとは
■外観検査業務におけるAI活用成功事例
【課題感】
外観検査領域においては、従来の画像処理カメラやセンサを用いて、できる限りの自動化をおこなっている企業は数多く存在します。
それでも、従来のカメラで判別できない場合は、やむを得ず目視検査を続けるしかありません。
ただ、目視検査は、担当者の感覚に頼っている場合が多く、担当者毎のばらつきがあり、担当者自身もその時の体調などで判断が変わってしまうことがあります。
もしくは、検査自体が熟練した担当者しかできない=属人化しているケースも多くあります。
担当者で判断が変わったり、熟練者しかできないという検査はモノづくりにおいて、かなり問題があることですが、「実際そのような状況に結果的になってしまっている」というケースが多くあります。
【AI活用】
従来の画像処理では、判断できなかった事象に対して、AIを搭載したカメラを用いることでうまく検査が出来るようになります。
例えば、透明なカップの外観や板地に模様がある中での傷の検査など、従来人の目でした判断がつかなかった事象についてもうまくとらえられるようになりました
【効果】
目視検査は人員を集めることも大変ですし、判断は標準化させることも難しい業務です。
その検査自体が、職人技なのであれば、さらに問題は複雑です。
AIカメラで代替させることで、品質基準は統一化され、365日24時間、同じ品筒基準で検査をしてくれるようになりました。
また、システム化により後継者の育成が難しい「外観検査の後継者問題」からも解放されました。
⇒関連記事:AI外観検査とは?従来の画像検査との違い、導入のメリットや注意点とは?
■在庫管理業務におけるAI活用成功事例
【課題感】
発注担当者は、在庫切れが起こらないよう日々在庫確認と発注作業が必要でした。
その一方で、確認作業や発注作業のタイミングは各担当者に一任されており、社内に統一された明確なルールはなく、発注タイミングは個人の感覚に任せられていました。
売上予測や発注業務が属人化しており勘や経験を必要とする業務となっていました。
【AI活用】
過去の商品/在庫/実績/仕入先データ+直近の売上/繁忙期/リードタイム等を機械学習により発注の予測モデルを構築しました。
予測モデルを構築するには、「何が発注に寄与するか」を担当者からヒアリングしながらデータ分析を行いました。
売上予測をもとに品目ごとに在庫切れのタイミングを特定することで、最適な発注タイミングをシステム上で提示します。
自動発注は行わず、最終確認は人間が行い発注をします。
【効果】
属人化していた発注タイミングを「いつもで」「だれでも」「同じレベル(質)」で判断が出来るようになりました。
感覚的(決まりがあるが決まっているものが感覚的な場合もあり)な発注は在庫の持ち過ぎ、持たな過ぎに直結します。
システム構築により、担当者毎の発注に対する質が標準化(凸凹がなくなり)され、在庫の過剰/不足が低減に繋がりました。
4.自社に最適なAIを選ぶときの基準
では、自社の状況に合ったAIはどのように選定していけば良いのでしょうか?以下の5つの基準を鑑みながら、選定していくことが重要です。
1. 目的とニーズの明確化
まずは、自社の目的とニーズを明確にすることが重要です。
AIを導入する目的や期待する効果、解決したい課題などを具体的に定義しましょう。
2. 機能と性能
AIの機能や性能が自社のニーズと一致しているかを確認しましょう。
具体的な要件や予算に基づいて、必要な機能や性能を評価します。
3. データの要件と適合性
自社のデータに合わせてAIが適切に動作するかを確認しましょう。
データの形式、量、品質などに対応できるかを評価します。
4. 解釈可能性と透明性
AIの結果を解釈できるかどうか、判断理由が明示されているかを確認しましょう。
特に、意思決定に影響を与える場合は、解釈可能性が求められます。
5. 可用性と拡張性
AIの実装および展開の容易さ、基幹システムの連携の可否、サポートやメンテナンスの提供、将来の拡張性などを評価しましょう。
自社の状況と予算に適合しているかを検討します。
これらの基準を元に、自社に最適なAIを選択することが重要です。
5.AI導入の具体的なステップ
AIを導入する際は、以下の5つのステップを踏み、着実にプロジェクトを進めていくことが重要です。
1. 目的とニーズの明確化
AIを導入する目的やニーズを明確に定義しましょう。
例えば、業務プロセスの効率化、顧客対応の向上、品質管理の強化、従業員の教育負担の軽減など、具体的な目標を設定します。
2. データの収集と前処理
AIはデータに基づいて学習し予測を行いますので、必要なデータを収集し、必要な前処理を行いましょう。
データの品質や量、形式にも注意を払いましょう。
3. AIモデルの選択
導入するAIの種類やモデルを選定します。
自然言語処理によるチャットボット、画像認識による品質管理システムなど、目的やニーズに合ったAIモデル・ツールを選びましょう。
4. モデルの学習と評価
選んだAIモデルをデータで学習させ、その性能を評価します。
学習方法やパラメータの調整によってモデルの精度を高めていきます。
5. 導入と運用
学習したAIモデルを実際の業務に導入し、運用します。
トライアル期間を設け、結果を評価しながら適切な調整や改善を行いましょう。
これらのステップを踏みながら、AIを導入することで効果的な活用ができるでしょう。
6.AI活用の課題と注意点
AI導入おけるもっと重要な箇所は、1番初めの「課題の抽出、目的とニーズの明確化」です。
<どこが課題>で<何を目的に導入するのか>をユーザー側は明確にする必要があります。
<目的>が曖昧だったり、ブレてしまうと、どういうAIを選定するか?を考える際に、AIが出来ることが優先され、結果的に導入されたもののさほど意味がない(当初の課題を解決してくれない)ものになってしまいます。
これを回避するには、課題抽出の時点からある程度のAIの知識(何が出来て何が出来ないか)を知っておく必要があります。
課題のすべてをAIが解決してくれるとは限らないのです。
AIベンダーはユーザーから与えられた要望に対して、自社製品を使って必死に知恵を絞り出します。
しかし、根本的に課題抽出から間違っている場合も多くあります。
「そもそもそれはAIで解決すべきではない」という結論です。
課題に対して、解決方法(アプローチ方法)はいくつかあります。
課題抽出の段階で、どの方法なら出来そうか?技術的なハードルを目途つけながらやっていくことが必要です。
全く考えないまま(知識がないまま)実施していくと、いわゆる「ベンダーの言いなり」となり、ベンダーが主導権を握り、自社ではハンドリングが出来なくなっていきます。
7.まとめ
船井総研では、上流の課題抽出からお客様と一緒に考え、取り上げられた課題は「今のAI技術で解決出来そうか」や、「技術的なハードルはどこか」を考慮しながらアドバイスを行っていきます。
AIプロジェクトだけではなく、様々なシステム開発に携わってきた観点からお客様の課題に対して「課題抽出→企画→要求取りまとめ→ベンダー選定→要件定義→システム開発→検証→ゴール(運用)」までお客様と共に伴走をしていきます。
工場内の課題に対して、「たくさん課題があるが何から手を付けるべきはわからない。」「AIを活用したいが、そもそもAIが必要なのか、どこに使えそうかわからない」という方はぜひ、船井総研までご相談下さい。
無料経営相談はこちら
無料ダウンロード!!
2024年AI活用時流予測レポート ~今後の業界動向・トレンドを予測~
▼事例レポート無料ダウンロードお申し込みはこちら▼
目次
1、製造業AI業界の現状
2、2023年製造業AI業界はこうなる!
3、2023年実践していただきたいこと
4、どの業務・工程でもAIは活用できる「業務別・工程別のAI活用」
5、国内中小製造業におけるAI導入事例
中小製造業のAI活用の最新事例と導入事例この1冊にまとめました。
AI活用術について「考え方」と「具体的な方法」を例を出して解説し、さらに導入事例を掲載することでAI活用の具体的な取り組み方が分かる資料になっております。
https://www.funaisoken.co.jp/dl-contents/jy-ai_S045