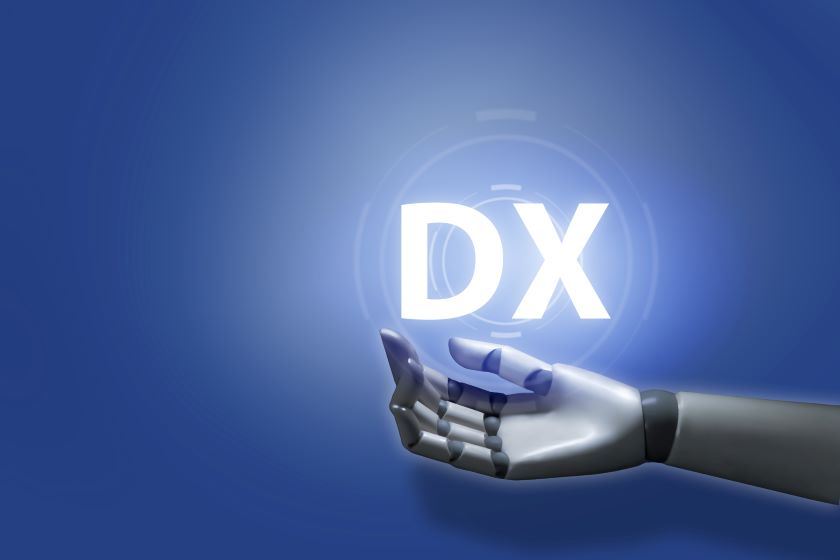
生産管理システムとは?導入で失敗しないための完全ガイド
2025.04.03
「生産管理システム」の導入を検討中の企業様必見!
本ガイドでは、システムの基本機能から選び方、導入ポイントまでを徹底解説。
製造業の業務効率化、コスト削減に貢献する生産管理システムの導入で失敗しないためのノウハウをご紹介します。
1.はじめに
製造業において、「生産管理」は企業の生命線とも言える重要な活動です。原材料の調達から製品の出荷に至るまで、生産活動全体を計画、実行、管理することで、効率的なものづくりを実現します。
しかし、現代の製造業は、多品種少量生産、短納期、顧客ニーズの多様化など、複雑な課題に直面しています。これらの課題に対応し、競争力を維持・向上させるためには、生産管理システムの導入が不可欠となっています。
私自身、全国各地の製造業のコンサルティングを行う中で、多くの企業が生産管理システムの導入に課題を感じている現状を目の当たりにしてきました。
「どのシステムを選べばいいのかわからない…」
「導入にどれくらいの費用や時間がかかるのかが不透明…」
「システムベンダーの選定も難しそう…」
「導入しても本当に効果があるのか疑問…」
このような悩みを抱えている企業様は少なくありません。
本ガイドでは、これらの疑問や不安を解消し、生産管理システムの導入を成功に導くための羅針盤となることを目指します。
2. 生産管理システムの基本
ヒヤリハットとは?理由と原因、ハインリッヒの法則
ヒヤリハットとは、労働災害に至らなかったものの、一歩間違えれば重大な事故につながりかねない事象を指します。その背景には、作業者の不注意や設備の不備、作業環境の悪さなど、様々な要因が考えられます。ハインリッヒの法則によれば、1件の重大事故の背後には29件の軽微な事故があり、さらに300件のヒヤリハットが存在するとされています。つまり、ヒヤリハットを放置することは、将来的に重大な労働災害を引き起こす可能性を高めることを示唆しています。
2.1 生産管理の定義と目的
生産管理とは、企業の生産活動全体を計画、実行、管理することです。具体的には、原材料の調達から製品の出荷に至るまでのプロセス全体を最適化し、効率的なものづくりを実現するための活動を指します。
生産管理の目的は、以下の3つの要素をバランス良く達成することです。
品質(Quality): 顧客の要求を満たす品質の製品を安定的に供給すること
コスト(Cost): 生産にかかるコストを最小限に抑え、利益を最大化すること
納期(Delivery): 顧客が求める納期に製品を確実に供給すること
これらの要素は、QCD(Quality、Cost、Delivery)と呼ばれ、生産管理における重要な指標となっています。生産管理は、企業の競争力を高めるための重要な活動であり、その目的は、QCDのバランスを最適化することにあります。
2.2 生産管理システムの機能
生産管理システムは、生産活動における様々な情報を一元的に管理し、最適化するためのツールです。ここでは、生産管理システムの主な機能について解説します。
2.2.1 生産計画
生産計画は、顧客からの受注や需要予測に基づいて、いつ、何を、どれだけ生産するかを決定する機能です。システム上では、受注情報、在庫情報、設備能力、人員配置などの様々な情報を考慮して、最適な生産計画を立案します。
2.2.2 工程管理
工程管理は、生産計画に基づいて、実際の生産活動を管理する機能です。システム上では、各工程の進捗状況をリアルタイムに把握し、遅延が発生している工程を特定したり、問題を早期に発見したりすることができます。
2.2.3 在庫管理
在庫管理は、原材料、仕掛品、製品などの在庫を適切に管理する機能です。システム上では、在庫の入出庫状況、在庫量をリアルタイムに把握し、過剰在庫や在庫不足を防ぎ、在庫コストを最適化します。
2.2.4 品質管理
品質管理は、製品の品質を維持・向上させるための機能です。システム上では、検査結果の記録、不良品の分析、品質改善のためのデータ分析などを行い、品質管理の効率化と品質向上に貢献します。
2.2.5 その他機能
生産管理システムには、上記以外にも、購買管理、販売管理、原価管理、設備管理など、様々な機能があります。必要な機能は、企業の業種や規模、生産形態などによって異なります。
2.3 生産管理システムの導入形態
生産管理システムは、その提供形態や機能によって、様々な種類があります。ここでは、代表的な生産管理システムの導入形態について解説します。
2.3.1 オンプレミス型
オンプレミス型は、自社のサーバーにソフトウェアをインストールして利用する形態です。従来はオンプレミス型が普及していましたが、近年ではクラウド技術の発展やセキュリティに対する考え方の変化などもあり、ケースバイケースではありますが、以前と比べるとオンプレミス型以外にクラウド型を選択肢に含める企業も増えてきています。
2.3.2 クラウド型
オンプレミス型に対し、クラウド型生産管理システムは、インターネット経由でサービスを利用する形態です。原則として、インターネットが繋がる環境であれば、場所を問わずに利用することができます。クラウド型は、初期費用を抑えることができ、メンテナンスやバージョンアップなどの手間がかからないというメリットがあります。
2.3.3 スクラッチ開発
スクラッチ開発とは、既存のパッケージソフトウェアを利用せずに、自社の業務に合わせてシステムを構築する形態です。スクラッチ開発は、自社の業務に完全に合致したシステムを構築できるというメリットがあります。しかし、その自由度の高さゆえにカスタマイズ・アドオン開発が増えやすく、結果として開発費用の高騰や開発期間の長期化を招くケースも多くあります。
2.3.4 パッケージ型
スクラッチ開発に対し、パッケージ型生産管理システムは、予め用意された既成のソフトウェアを導入する形態です。パッケージ型は、導入期間を比較的短く抑えることができるとともに、極力カスタマイズなしで導入する方針を踏襲することで、導入費用を低減することも可能です。
中堅・中小企業向けの生産管理システムは、パッケージ型で提供されることが多いです。例えば、「クラウド」「パッケージ」の条件をおさえたプロダクトとして、マイクロソフト社が提供する「Microsoft Dynamics 365 Business Central」があります。 「Microsoft Dynamics 365 Business Central」は、多品種少量生産に対応した柔軟性と拡張性を備えながら、中堅・中小企業にとって導入しやすい価格帯と操作性を実現しており、近年注目を集めています。
3. 生産管理システム導入のメリット
生産管理システムの導入は、企業の生産活動に様々なメリットをもたらします。ここでは、生産管理システム導入の主なメリットについて解説します。
3.1 業務効率化
生産管理システムは、生産活動における様々な情報を一元的に管理し、自動化することで、業務効率化に貢献します。例えば、生産計画の作成、工程の進捗管理、在庫管理などの業務を、システムが自動的に行うことで、従業員の負担を軽減し、より付加価値の高い業務に集中させることができます。
3.2 コスト削減
生産管理システムは、生産活動における無駄を排除し、最適化することで、コスト削減に貢献します。例えば、生産計画の精度向上により、過剰在庫を削減し、在庫コストを削減することができます。また、工程管理の最適化により、不良品の発生率を低下させ、品質コストを削減することができます。
3.3 リードタイム短縮
リードタイムとは、顧客からの受注~製品の出荷に至るまでの期間のことです。生産管理システムは、生産活動全体を最適化することで、リードタイム短縮に貢献します。例えば、生産計画の精度向上により、無駄な工程や必要以上のバッファを排除し、生産時間を短縮することができます。また、工程管理の最適化により、ボトルネックとなっている工程を特定し、改善策を講じることで、工程時間を短縮することができます。
3.4 品質向上
生産管理システムは、品質管理の効率化と品質向上に貢献します。例えば、検査結果の記録、不良品の分析、品質改善のためのデータ分析などを行い、品質管理の精度を高めることができます。品質向上は、リピート率向上にもつながります。
3.5 情報共有の促進
生産管理システムは、生産活動における様々な情報を一元的に管理することで、社内での情報共有を促進します。例えば、生産計画、工程の進捗状況、在庫情報、品質情報など、様々な情報を関係者間で共有することができます。
3.6 データ活用とDX推進
生産管理システムは、生産活動における様々なデータを収集・分析することで、データ活用とDX(デジタルトランスフォーメーション)推進に貢献します。例えば、生産計画、工程の進捗状況、在庫情報、品質情報など、様々なデータを分析することで、生産活動における課題を特定したり、改善策を検討したりすることができます。
4. 生産管理システムの選び方とポイント
生産管理システムの導入を成功させるためには、自社のニーズに合ったシステムを選ぶことが重要です。ここでは、生産管理システムの選び方について解説します。
4.1 導入目的の明確化
生産管理システムを選ぶ前に、まず、導入目的および解決したい課題を明確にすることが重要です。
なぜ、生産管理システムを導入するのか?
どのような課題を解決したいのか?
どのような効果を期待するのか?
これらの点を明確にすることで、自社に必要な機能や要件が見えてきます。
4.2 必要な機能の洗い出し
導入目的を明確にしたら、次に、必要な機能を洗い出します。
どのような機能が必要なのか?
どのような機能は不要なのか?
将来的に必要になる可能性のある機能はあるか?
これらの点を検討することで、自社に必要な機能を過不足なく備えたシステムを選ぶことができます。
4.3 システムの比較ポイント
必要な機能を洗い出したら、次に、複数の生産管理システムを比較検討します。比較検討する際には、以下のポイントを考慮することが重要です。
4.3.1 対応する生産形態
生産管理システムは、それぞれ対応する生産形態が異なります。自社の生産形態に対応したシステムを選ぶことが重要です。
多品種少量生産
大量生産
個別受注生産
見込生産
4.3.2 拡張性・柔軟性
生産管理システムは、導入後も、企業の成長や変化に合わせて、機能を追加したり、他のシステムと連携したりできることが重要です。
将来的に機能を追加できるか?
他のシステムと連携できるか?
4.3.3 使いやすさ・操作性
生産管理システムは、従業員が使いやすいことも重要です。
操作画面が見やすいか?
操作方法がわかりやすいか?
トレーニングを受けられるか?
4.3.4 サポート体制
生産管理システムは、導入後も、ベンダーからのサポートを受けることが重要です。
導入時のサポートは充実しているか?
運用開始後のサポートは受けられるか?
トラブル発生時の対応は迅速か?
4.3.5 費用対効果
生産管理システムは、導入費用だけでなく、運用コストも考慮する必要があります。
導入費用はいくらか?
運用費用はいくらか?
費用対効果は高いか?
4.4 導入形態の検討
生産管理システムには前述の通り、オンプレミス型、クラウド型、スクラッチ開発、パッケージ型など、様々な導入形態があります。自社のニーズに合わせて、最適な導入形態を選ぶことが重要です。
4.5 ベンダー選定のポイント
生産管理システムを選ぶ際には、ベンダー選定も重要です。
ベンダーの実績は豊富か?
ベンダーの技術力は高いか?
ベンダーのサポート体制は充実しているか?
5.まとめ
本ガイドでは、生産管理システムの基本から、選び方、導入ポイントまで、網羅的に解説しました。生産管理システムの導入は、企業の生産活動を効率化し、競争力を高めるための重要な手段です。
今後、生産管理システムは、AIやIoTなどの最新技術との連携が進み、より高度な機能が提供されるようになるでしょう。また、クラウド型のシステムが普及し、中堅・中小企業でもさらに導入しやすくなることが期待されます。また、生産管理システムの導入について、
「どのシステムを選べばいいのかわからない…」
「導入にどれくらいの費用や時間がかかるのかが不透明…」
「システムベンダーの選定も難しそう…」
「導入しても本当に効果があるのか疑問…」
などのお悩みをお持ちの方は、是非船井総研の「無料経営相談」をご利用ください。 「生産管理システム」の導入を検討中の企業様必見!
本ガイドでは、システムの基本機能から選び方、導入ポイントまでを徹底解説。
製造業の業務効率化、コスト削減に貢献する生産管理システムの導入で失敗しないためのノウハウをご紹介します。
1.はじめに
製造業において、「生産管理」は企業の生命線とも言える重要な活動です。原材料の調達から製品の出荷に至るまで、生産活動全体を計画、実行、管理することで、効率的なものづくりを実現します。
しかし、現代の製造業は、多品種少量生産、短納期、顧客ニーズの多様化など、複雑な課題に直面しています。これらの課題に対応し、競争力を維持・向上させるためには、生産管理システムの導入が不可欠となっています。
私自身、全国各地の製造業のコンサルティングを行う中で、多くの企業が生産管理システムの導入に課題を感じている現状を目の当たりにしてきました。
「どのシステムを選べばいいのかわからない…」
「導入にどれくらいの費用や時間がかかるのかが不透明…」
「システムベンダーの選定も難しそう…」
「導入しても本当に効果があるのか疑問…」
このような悩みを抱えている企業様は少なくありません。
本ガイドでは、これらの疑問や不安を解消し、生産管理システムの導入を成功に導くための羅針盤となることを目指します。
2. 生産管理システムの基本
ヒヤリハットとは?理由と原因、ハインリッヒの法則
ヒヤリハットとは、労働災害に至らなかったものの、一歩間違えれば重大な事故につながりかねない事象を指します。その背景には、作業者の不注意や設備の不備、作業環境の悪さなど、様々な要因が考えられます。ハインリッヒの法則によれば、1件の重大事故の背後には29件の軽微な事故があり、さらに300件のヒヤリハットが存在するとされています。つまり、ヒヤリハットを放置することは、将来的に重大な労働災害を引き起こす可能性を高めることを示唆しています。
2.1 生産管理の定義と目的
生産管理とは、企業の生産活動全体を計画、実行、管理することです。具体的には、原材料の調達から製品の出荷に至るまでのプロセス全体を最適化し、効率的なものづくりを実現するための活動を指します。
生産管理の目的は、以下の3つの要素をバランス良く達成することです。
品質(Quality): 顧客の要求を満たす品質の製品を安定的に供給すること
コスト(Cost): 生産にかかるコストを最小限に抑え、利益を最大化すること
納期(Delivery): 顧客が求める納期に製品を確実に供給すること
これらの要素は、QCD(Quality、Cost、Delivery)と呼ばれ、生産管理における重要な指標となっています。生産管理は、企業の競争力を高めるための重要な活動であり、その目的は、QCDのバランスを最適化することにあります。
2.2 生産管理システムの機能
生産管理システムは、生産活動における様々な情報を一元的に管理し、最適化するためのツールです。ここでは、生産管理システムの主な機能について解説します。
2.2.1 生産計画
生産計画は、顧客からの受注や需要予測に基づいて、いつ、何を、どれだけ生産するかを決定する機能です。システム上では、受注情報、在庫情報、設備能力、人員配置などの様々な情報を考慮して、最適な生産計画を立案します。
2.2.2 工程管理
工程管理は、生産計画に基づいて、実際の生産活動を管理する機能です。システム上では、各工程の進捗状況をリアルタイムに把握し、遅延が発生している工程を特定したり、問題を早期に発見したりすることができます。
2.2.3 在庫管理
在庫管理は、原材料、仕掛品、製品などの在庫を適切に管理する機能です。システム上では、在庫の入出庫状況、在庫量をリアルタイムに把握し、過剰在庫や在庫不足を防ぎ、在庫コストを最適化します。
2.2.4 品質管理
品質管理は、製品の品質を維持・向上させるための機能です。システム上では、検査結果の記録、不良品の分析、品質改善のためのデータ分析などを行い、品質管理の効率化と品質向上に貢献します。
2.2.5 その他機能
生産管理システムには、上記以外にも、購買管理、販売管理、原価管理、設備管理など、様々な機能があります。必要な機能は、企業の業種や規模、生産形態などによって異なります。
2.3 生産管理システムの導入形態
生産管理システムは、その提供形態や機能によって、様々な種類があります。ここでは、代表的な生産管理システムの導入形態について解説します。
2.3.1 オンプレミス型
オンプレミス型は、自社のサーバーにソフトウェアをインストールして利用する形態です。従来はオンプレミス型が普及していましたが、近年ではクラウド技術の発展やセキュリティに対する考え方の変化などもあり、ケースバイケースではありますが、以前と比べるとオンプレミス型以外にクラウド型を選択肢に含める企業も増えてきています。
2.3.2 クラウド型
オンプレミス型に対し、クラウド型生産管理システムは、インターネット経由でサービスを利用する形態です。原則として、インターネットが繋がる環境であれば、場所を問わずに利用することができます。クラウド型は、初期費用を抑えることができ、メンテナンスやバージョンアップなどの手間がかからないというメリットがあります。
2.3.3 スクラッチ開発
スクラッチ開発とは、既存のパッケージソフトウェアを利用せずに、自社の業務に合わせてシステムを構築する形態です。スクラッチ開発は、自社の業務に完全に合致したシステムを構築できるというメリットがあります。しかし、その自由度の高さゆえにカスタマイズ・アドオン開発が増えやすく、結果として開発費用の高騰や開発期間の長期化を招くケースも多くあります。
2.3.4 パッケージ型
スクラッチ開発に対し、パッケージ型生産管理システムは、予め用意された既成のソフトウェアを導入する形態です。パッケージ型は、導入期間を比較的短く抑えることができるとともに、極力カスタマイズなしで導入する方針を踏襲することで、導入費用を低減することも可能です。
中堅・中小企業向けの生産管理システムは、パッケージ型で提供されることが多いです。例えば、「クラウド」「パッケージ」の条件をおさえたプロダクトとして、マイクロソフト社が提供する「Microsoft Dynamics 365 Business Central」があります。 「Microsoft Dynamics 365 Business Central」は、多品種少量生産に対応した柔軟性と拡張性を備えながら、中堅・中小企業にとって導入しやすい価格帯と操作性を実現しており、近年注目を集めています。
3. 生産管理システム導入のメリット
生産管理システムの導入は、企業の生産活動に様々なメリットをもたらします。ここでは、生産管理システム導入の主なメリットについて解説します。
3.1 業務効率化
生産管理システムは、生産活動における様々な情報を一元的に管理し、自動化することで、業務効率化に貢献します。例えば、生産計画の作成、工程の進捗管理、在庫管理などの業務を、システムが自動的に行うことで、従業員の負担を軽減し、より付加価値の高い業務に集中させることができます。
3.2 コスト削減
生産管理システムは、生産活動における無駄を排除し、最適化することで、コスト削減に貢献します。例えば、生産計画の精度向上により、過剰在庫を削減し、在庫コストを削減することができます。また、工程管理の最適化により、不良品の発生率を低下させ、品質コストを削減することができます。
3.3 リードタイム短縮
リードタイムとは、顧客からの受注~製品の出荷に至るまでの期間のことです。生産管理システムは、生産活動全体を最適化することで、リードタイム短縮に貢献します。例えば、生産計画の精度向上により、無駄な工程や必要以上のバッファを排除し、生産時間を短縮することができます。また、工程管理の最適化により、ボトルネックとなっている工程を特定し、改善策を講じることで、工程時間を短縮することができます。
3.4 品質向上
生産管理システムは、品質管理の効率化と品質向上に貢献します。例えば、検査結果の記録、不良品の分析、品質改善のためのデータ分析などを行い、品質管理の精度を高めることができます。品質向上は、リピート率向上にもつながります。
3.5 情報共有の促進
生産管理システムは、生産活動における様々な情報を一元的に管理することで、社内での情報共有を促進します。例えば、生産計画、工程の進捗状況、在庫情報、品質情報など、様々な情報を関係者間で共有することができます。
3.6 データ活用とDX推進
生産管理システムは、生産活動における様々なデータを収集・分析することで、データ活用とDX(デジタルトランスフォーメーション)推進に貢献します。例えば、生産計画、工程の進捗状況、在庫情報、品質情報など、様々なデータを分析することで、生産活動における課題を特定したり、改善策を検討したりすることができます。
4. 生産管理システムの選び方とポイント
生産管理システムの導入を成功させるためには、自社のニーズに合ったシステムを選ぶことが重要です。ここでは、生産管理システムの選び方について解説します。
4.1 導入目的の明確化
生産管理システムを選ぶ前に、まず、導入目的および解決したい課題を明確にすることが重要です。
なぜ、生産管理システムを導入するのか?
どのような課題を解決したいのか?
どのような効果を期待するのか?
これらの点を明確にすることで、自社に必要な機能や要件が見えてきます。
4.2 必要な機能の洗い出し
導入目的を明確にしたら、次に、必要な機能を洗い出します。
どのような機能が必要なのか?
どのような機能は不要なのか?
将来的に必要になる可能性のある機能はあるか?
これらの点を検討することで、自社に必要な機能を過不足なく備えたシステムを選ぶことができます。
4.3 システムの比較ポイント
必要な機能を洗い出したら、次に、複数の生産管理システムを比較検討します。比較検討する際には、以下のポイントを考慮することが重要です。
4.3.1 対応する生産形態
生産管理システムは、それぞれ対応する生産形態が異なります。自社の生産形態に対応したシステムを選ぶことが重要です。
多品種少量生産
大量生産
個別受注生産
見込生産
4.3.2 拡張性・柔軟性
生産管理システムは、導入後も、企業の成長や変化に合わせて、機能を追加したり、他のシステムと連携したりできることが重要です。
将来的に機能を追加できるか?
他のシステムと連携できるか?
4.3.3 使いやすさ・操作性
生産管理システムは、従業員が使いやすいことも重要です。
操作画面が見やすいか?
操作方法がわかりやすいか?
トレーニングを受けられるか?
4.3.4 サポート体制
生産管理システムは、導入後も、ベンダーからのサポートを受けることが重要です。
導入時のサポートは充実しているか?
運用開始後のサポートは受けられるか?
トラブル発生時の対応は迅速か?
4.3.5 費用対効果
生産管理システムは、導入費用だけでなく、運用コストも考慮する必要があります。
導入費用はいくらか?
運用費用はいくらか?
費用対効果は高いか?
4.4 導入形態の検討
生産管理システムには前述の通り、オンプレミス型、クラウド型、スクラッチ開発、パッケージ型など、様々な導入形態があります。自社のニーズに合わせて、最適な導入形態を選ぶことが重要です。
4.5 ベンダー選定のポイント
生産管理システムを選ぶ際には、ベンダー選定も重要です。
ベンダーの実績は豊富か?
ベンダーの技術力は高いか?
ベンダーのサポート体制は充実しているか?
5.まとめ
本ガイドでは、生産管理システムの基本から、選び方、導入ポイントまで、網羅的に解説しました。生産管理システムの導入は、企業の生産活動を効率化し、競争力を高めるための重要な手段です。
今後、生産管理システムは、AIやIoTなどの最新技術との連携が進み、より高度な機能が提供されるようになるでしょう。また、クラウド型のシステムが普及し、中堅・中小企業でもさらに導入しやすくなることが期待されます。また、生産管理システムの導入について、
「どのシステムを選べばいいのかわからない…」
「導入にどれくらいの費用や時間がかかるのかが不透明…」
「システムベンダーの選定も難しそう…」
「導入しても本当に効果があるのか疑問…」
などのお悩みをお持ちの方は、是非船井総研の「無料経営相談」をご利用ください。