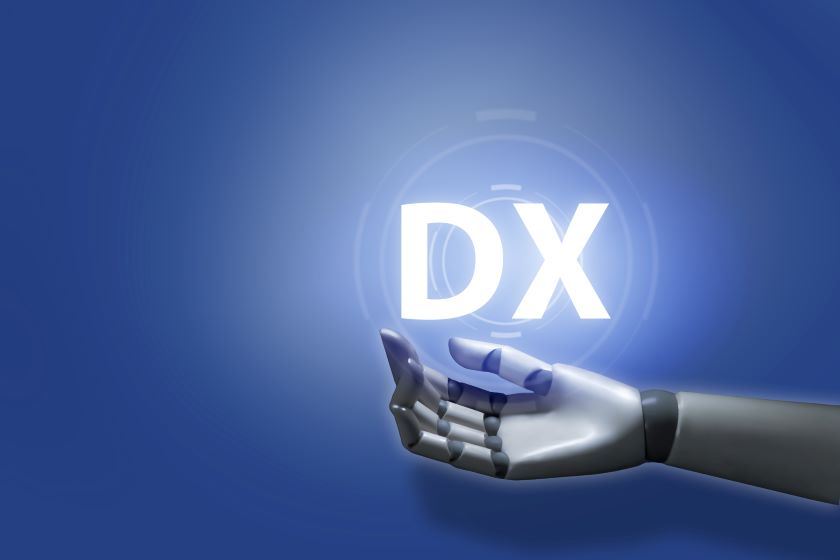
中小企業が導入すべきERPは?導入のメリットと製品選定のポイントを解説!
2025.04.02
~こんな方におすすめです~
データの蓄積や活用に悩まれている中小企業の経営者様
業務の非効率さに悩まれている中小企業の経営者様
中小企業でIT担当者やシステム管理者を務めている方
業務効率化を検討している部門責任者の方
ERP導入を検討している企業の決裁者の方
1.中小企業がERPを導入するメリット
まずはERP(基幹システム)を導入するメリットをご紹介したいと思います。
1-1) 業務の効率化
ERP(基幹システム)とは、企業内の様々な業務プロセスを統合するシステムを指します。
中小企業がERP(基幹システム)を導入することで、いままでばらばらだったデータの一元化が可能となり、重複業務の削減や手作業のミスを防ぐことができます。
1-2) データの可視化と分析力の向上
ERPシステムはリアルタイムでデータを収集・更新するため、経営者は即座に正確な情報を把握できます。これにより、経営判断の迅速化が図れ、市場の変化に柔軟に対応できるようになります。また、データ分析機能を活用することで、売上予測や在庫管理など、戦略的な意思決定が可能となります。
1-3) コスト削減
ERP導入により、在庫管理や受発注業務が効率化され、過剰在庫や欠品のリスクが低減します。
また、ペーパーレス化が進み、印刷コストや文書保管スペースの削減にも繋がります。
さらに、重複したシステムやソフトウェアの統合により、ITコストも抑えることができるようになります。
2.中小企業がERPを導入すべき理由
これは様々な理由が存在しますが、一番のポイントは競争力の向上です。
中小企業は大企業と比べてリソースが限られていますが、ERPの導入により、リソースを最適に活用することができます。販売業務、製造業務、会計業務…様々な業務がありますが、中小企業では今でも当たり前にデータの2重3重入力が行われています。
ERPの考え方として、リソースを最適化するというのはこういった業務を効率化するという事も含まれています。
更に、様々なシステムに分けてデータを入れている場合、各システムからデータを取り出し、加工し、ようやく業績情報が確認できるなどということは大企業であったとしても珍しいことではありません。
データを一元管理し、加工を容易にすることで月次業績資料が今より早く出てきたらどうでしょうか。
こういった取り組みにより、業務プロセスの標準化や効率化が図れ、大企業と対等に競争するための基盤が整います。
中小企業だからこそ、ERPの導入は必要なのです。
3.中小企業がERPを選定するときにおさえるべき3つのポイント
3-1) 自社の業務に適した機能性
ERPシステムの選定において最も重要なのは、自社の業務プロセスに適合した機能を持つシステムを選ぶことです。例えば、製造業であれば生産管理機能を含めたものが良いでしょう。また、業界特有のニーズに対応できるカスタマイズ性も重要です。
しっかりと現在の業務に必要なプロセスを抑え、かつ、改善したい要望をまとめておきましょう。
3-2.) 導入・運用コスト
ERPシステムの導入には初期費用やライセンス料がかかるため、総コストを慎重に評価する必要があります。導入後の運用コストやサポート費用も考慮し、自社にとって最適な形を選択する必要があります。
現在はクラウド型ERPも発表されており、かなり初期費用が抑えられ、運用コストも予測しやすい点で中小企業には適していると言えるでしょう。
3-3) 使いやすさとサポート体制
ERPシステムは日常業務で頻繁に使用するため、使いやすさも選定の重要なポイントです。ユーザーフレンドリーなインターフェースや、操作性の高さを重視しましょう。また、システム導入後のサポート体制が充実しているベンダーを選ぶことで、トラブル発生時にも迅速に対応できるようになります。
4.中小企業でERPを導入する際の注意点
4-1) 現場の意見を取り入れ、必要機能の取捨選択を行う
ERP導入は全社的なプロジェクトであり、現場の意見を無視すると、運用開始後にトラブルが発生する可能性があります。各部門の業務フローを詳細にヒアリングし、現場のニーズを反映したシステム設計を行いましょう。この際に全ての意見を丸のみにしてしまわないように要望の取捨選択を行う事も必要です。
4-2) 導入前の業務プロセス見直し
ERP導入を機に、現行の業務プロセスを見直し、無駄な手順や非効率な作業を洗い出すことが重要です。これにより、ERPの効果を最大限に引き出し、業務の標準化と効率化が実現します。これを行わないと、現在の無駄な業務をそのまま新しいシステムに変えて行うことになってしまいますので、特にこの点は注意が必要です。
4-3) スムーズな移行計画
ERP導入に伴うシステム移行は、従業員の負担を軽減し、業務の中断を最小限に抑えるために計画的に行う必要があります。段階的な移行やトレーニングプログラムの実施により、従業員が新システムに慣れるまでの期間をスムーズに乗り切りましょう。
5.最後に
いかがでしたでしょうか。
中小企業でERPを導入するメリットや注意点をご紹介しました。
最後に、特に重要で、一番難しいポイントをお伝えします。
それは、継続的な改善とサポートです。
ERP導入はゴールではなく、スタートに過ぎません。導入後も定期的にシステムの見直しを行い、業務の変化や新たなニーズに対応できるように改善を続けることが何よりも重要です。
中小企業はERPを導入することで、多くのメリットを享受でき、競争力を高めることができます。
しかし、導入には慎重な計画と選定、そして活用に結びつけるための働きかけが何よりも必要です。
もし、実際に基幹システムを導入し、業務改革を成功させた事例がお知りになりたければ、以下のDLレポートも是非お読みください。
基幹システム活用+在庫管理 解決策レポート
▼事例レポート無料ダウンロードお申し込みはこちら▼
収益に着目したDXを行う手順と成功事例をご紹介します。
データの一元管理を通した改善ポイントの明確化
各種在庫の最適化と収益改善の仕組み
在庫管理を通した改善業務手順のご紹介
在庫管理を行い、収益改善を実現した事例のご紹介
https://www.funaisoken.co.jp/dl-contents/smart-factory_smart-factory_02627_S045 ~こんな方におすすめです~
データの蓄積や活用に悩まれている中小企業の経営者様
業務の非効率さに悩まれている中小企業の経営者様
中小企業でIT担当者やシステム管理者を務めている方
業務効率化を検討している部門責任者の方
ERP導入を検討している企業の決裁者の方
1.中小企業がERPを導入するメリット
まずはERP(基幹システム)を導入するメリットをご紹介したいと思います。
1-1) 業務の効率化
ERP(基幹システム)とは、企業内の様々な業務プロセスを統合するシステムを指します。
中小企業がERP(基幹システム)を導入することで、いままでばらばらだったデータの一元化が可能となり、重複業務の削減や手作業のミスを防ぐことができます。
1-2) データの可視化と分析力の向上
ERPシステムはリアルタイムでデータを収集・更新するため、経営者は即座に正確な情報を把握できます。これにより、経営判断の迅速化が図れ、市場の変化に柔軟に対応できるようになります。また、データ分析機能を活用することで、売上予測や在庫管理など、戦略的な意思決定が可能となります。
1-3) コスト削減
ERP導入により、在庫管理や受発注業務が効率化され、過剰在庫や欠品のリスクが低減します。
また、ペーパーレス化が進み、印刷コストや文書保管スペースの削減にも繋がります。
さらに、重複したシステムやソフトウェアの統合により、ITコストも抑えることができるようになります。
2.中小企業がERPを導入すべき理由
これは様々な理由が存在しますが、一番のポイントは競争力の向上です。
中小企業は大企業と比べてリソースが限られていますが、ERPの導入により、リソースを最適に活用することができます。販売業務、製造業務、会計業務…様々な業務がありますが、中小企業では今でも当たり前にデータの2重3重入力が行われています。
ERPの考え方として、リソースを最適化するというのはこういった業務を効率化するという事も含まれています。
更に、様々なシステムに分けてデータを入れている場合、各システムからデータを取り出し、加工し、ようやく業績情報が確認できるなどということは大企業であったとしても珍しいことではありません。
データを一元管理し、加工を容易にすることで月次業績資料が今より早く出てきたらどうでしょうか。
こういった取り組みにより、業務プロセスの標準化や効率化が図れ、大企業と対等に競争するための基盤が整います。
中小企業だからこそ、ERPの導入は必要なのです。
3.中小企業がERPを選定するときにおさえるべき3つのポイント
3-1) 自社の業務に適した機能性
ERPシステムの選定において最も重要なのは、自社の業務プロセスに適合した機能を持つシステムを選ぶことです。例えば、製造業であれば生産管理機能を含めたものが良いでしょう。また、業界特有のニーズに対応できるカスタマイズ性も重要です。
しっかりと現在の業務に必要なプロセスを抑え、かつ、改善したい要望をまとめておきましょう。
3-2.) 導入・運用コスト
ERPシステムの導入には初期費用やライセンス料がかかるため、総コストを慎重に評価する必要があります。導入後の運用コストやサポート費用も考慮し、自社にとって最適な形を選択する必要があります。
現在はクラウド型ERPも発表されており、かなり初期費用が抑えられ、運用コストも予測しやすい点で中小企業には適していると言えるでしょう。
3-3) 使いやすさとサポート体制
ERPシステムは日常業務で頻繁に使用するため、使いやすさも選定の重要なポイントです。ユーザーフレンドリーなインターフェースや、操作性の高さを重視しましょう。また、システム導入後のサポート体制が充実しているベンダーを選ぶことで、トラブル発生時にも迅速に対応できるようになります。
4.中小企業でERPを導入する際の注意点
4-1) 現場の意見を取り入れ、必要機能の取捨選択を行う
ERP導入は全社的なプロジェクトであり、現場の意見を無視すると、運用開始後にトラブルが発生する可能性があります。各部門の業務フローを詳細にヒアリングし、現場のニーズを反映したシステム設計を行いましょう。この際に全ての意見を丸のみにしてしまわないように要望の取捨選択を行う事も必要です。
4-2) 導入前の業務プロセス見直し
ERP導入を機に、現行の業務プロセスを見直し、無駄な手順や非効率な作業を洗い出すことが重要です。これにより、ERPの効果を最大限に引き出し、業務の標準化と効率化が実現します。これを行わないと、現在の無駄な業務をそのまま新しいシステムに変えて行うことになってしまいますので、特にこの点は注意が必要です。
4-3) スムーズな移行計画
ERP導入に伴うシステム移行は、従業員の負担を軽減し、業務の中断を最小限に抑えるために計画的に行う必要があります。段階的な移行やトレーニングプログラムの実施により、従業員が新システムに慣れるまでの期間をスムーズに乗り切りましょう。
5.最後に
いかがでしたでしょうか。
中小企業でERPを導入するメリットや注意点をご紹介しました。
最後に、特に重要で、一番難しいポイントをお伝えします。
それは、継続的な改善とサポートです。
ERP導入はゴールではなく、スタートに過ぎません。導入後も定期的にシステムの見直しを行い、業務の変化や新たなニーズに対応できるように改善を続けることが何よりも重要です。
中小企業はERPを導入することで、多くのメリットを享受でき、競争力を高めることができます。
しかし、導入には慎重な計画と選定、そして活用に結びつけるための働きかけが何よりも必要です。
もし、実際に基幹システムを導入し、業務改革を成功させた事例がお知りになりたければ、以下のDLレポートも是非お読みください。
基幹システム活用+在庫管理 解決策レポート
▼事例レポート無料ダウンロードお申し込みはこちら▼
収益に着目したDXを行う手順と成功事例をご紹介します。
データの一元管理を通した改善ポイントの明確化
各種在庫の最適化と収益改善の仕組み
在庫管理を通した改善業務手順のご紹介
在庫管理を行い、収益改善を実現した事例のご紹介
https://www.funaisoken.co.jp/dl-contents/smart-factory_smart-factory_02627_S045