記事公開日:2024.03.08
最終更新日:2024.03.08
データ一元管理の成功事例
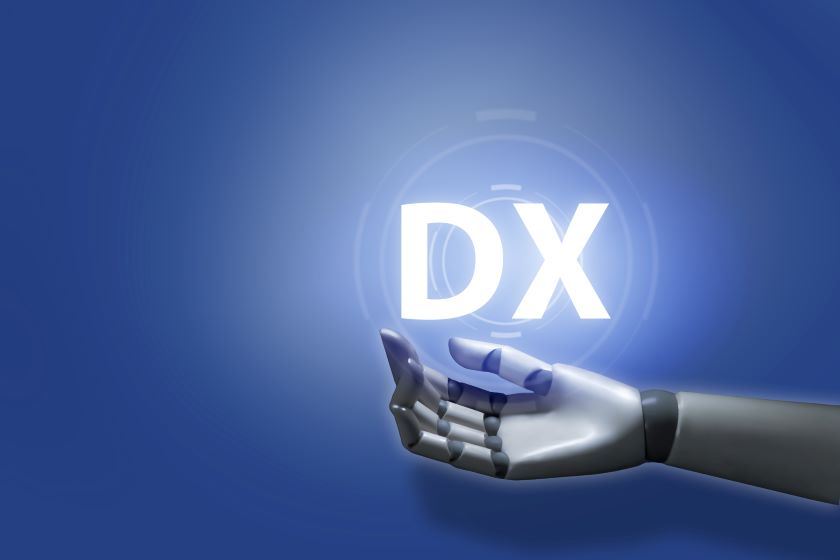
いつも当コラムをご愛読いただきありがとうございます。
1.Excel管理と紙伝票管理の課題
突然ですが、皆様の会社でこのようなお悩みはありませんか?
「社内にムダな業務やアナログな工程がたくさん残っている・・・」
「Excelや紙伝票が散在しており、二重三重業務が多い・・・」
「煩雑なExcel管理・紙伝票管理が常態化して現場が疲弊している…」
「このままでは時代の波に取り残されてしまう…」
「今の社内をもっと生産性の高い、働きやすい現場に変えていきたい・・・」
上記のようなお悩みは日々全国各地の中堅・中小製造業の企業様と接点を持つ中で実際に現場の実態としてよく聞こえてくるお声です。
日本全国には様々なタイプの製造業の企業様が存在していますが、その中でも非常に多くの中堅・中小製造業の企業様において、
「Excelや紙帳票・紙伝票に溢れた現場」
「二重・三重の業務オペレーション(二度手間な業務)」
「ヒトによる手入力や転記のオンパレード」
が当たり前のように残っていることが伺えます。
そのような中で、
“経営者”が先頭に立って自社の業務改革を進めていき、結果として、
- 元々は受注・販売・在庫・生産・会計等をバラバラの仕組みで管理していたが、全社一丸となり統合一元管理を実現した
- ERPシステム(業務の一元管理システム)の導入を通じて「脱・Excel管理」「脱・紙伝票管理」「全社でのデータ一元管理」を実現した
という成果をあげられた企業様がいらっしゃいます。
ここで、成功企業様の概要ならびに取り組みのBefore/Afterについて、簡単にご紹介したいと思います。
2.成功事例
成功企業様の概要
- 本社:大阪府大阪市
- 営業拠点:本社+全国に5か所
- 主な事業:包装機器の設計・製造・販売及びサービス
- 従業員数:30名(直近)
一元管理システム導入のBefore/After
【Before(システム導入前の状態と主な課題)】
- 各業務システムがバラバラに導入されており、各業務が一元管理されていない。
- kintoneや商奉行、Sansan等の管理システムが散在しており、二重三重入力が発生している。
- 以前に導入したシステムで見積や受注等に関する分析を試みているが、機能を十分に使いこなせていない。
- 見積と受注の連携を手作業でアナログに実施している。
- 現場担当者がそれぞれ異なるフォーマットのExcelや紙伝票を使用している。
- 製品に紐づく材料費・労務費・経費等の「製品別原価」が十分に管理できていない。
- 発注業務が属人的なExcel管理となっており、発注履歴の管理体制が不十分。
- 生産予定や出荷予定が一部の部門からしか見えず、他の部門担当者にとっては情報を把握するのに一苦労。
- 製品の故障履歴&修理履歴データが蓄積されていない。
- 顧客側の修理発生タイミングがわからない。
【After(システム導入後の主な効果)】
- 受注・購買・販売・在庫・生産等の管理業務を一元化!
- 各種データを一元化&二重三重入力を排除し業務を効率化!
- 製品別・担当者別等のさまざまな軸でスムーズに分析が可能に!
- 1つのシステム上で見積と受注がスムーズに連動!
- 新システム導入をきっかけに、既存のExcelや既存伝票の見直し・標準化・効率化を推進!
- 「製品別の個別原価管理」が可能に!
- 各部門共通のシステム上で発注管理履歴を可視化!発注漏れも防止!
- 一部の部門だけでなく他部門からもリアルタイムで生産予定や出荷予定が把握可能に!
- 故障履歴&修理履歴の管理が可能に!
- データによる故障予測を通じて、顧客への修理フォローのタイミングも最適化!
上記の取り組み全体を通して、
- 元々は受注・販売・在庫・生産・会計等をバラバラの仕組みで管理していたが、全社一丸となり統合一元管理を実現した
- ERPシステム(業務の一元管理システム)の導入を通じて「脱・Excel管理」「脱・紙伝票管理」「全社でのデータ一元管理」を実現した
という成果をあげることができました。
では、なぜこのような成果をあげることができたのでしょうか?
ここまでお読みいただいた皆様の中には、
- さらに詳しく話を聞いてみたい!
- 自社で上手くいっていない理由を探りたい!
- 当事者の生の声を直接聞きたい!
という方もいらっしゃるかと思います。
そのような皆様のお声にお応えするべく、
船井総研では今回新たにセミナーを企画させていただきました。
特別ゲスト講師として、当事者である“経営者様”に直接お話をしていただくセミナーです。
■関連するセミナーのご案内
~ERP・基幹システム導入を通じて「”脱”Excel管理」「”脱”紙伝票管理」を実現し生産性アップ!~
ERP導入を通じて「“脱”Excel管理」「“脱”紙伝票」を実現!セットメーカーにおける生産性アップの最新事例を大公開!
セミナー詳細・申込はこちらから
https://www.funaisoken.co.jp/seminar/111209
■開催日程
全てオンライン開催となります
以下の日程よりご都合の良い日程をお選び下さい
※内容は全て一緒です
- 2024/04/16 (火) 13:00~15:00
- 2024/04/23 (火) 13:00~15:00
- 2024/04/24 (水) 13:00~15:00
◆このような方におすすめです!
- 従業員数30~300名のセットメーカーの事業主の方
- 「Excelの手入力作業」や「二重三重の生産管理・原価管理業務」が多いセットメーカーの事業主の方
- Excelや紙伝票で溢れている現場を効率化し、生産性アップを目指していきたいセットメーカーの事業主の方
- 「ブラックボックス化・属人化」している自社の生産管理業務を「見える化・自動化・脱属人化」していきたいセットメーカーの事業主の方
- 自社で新たなERP・基幹システムの導入を検討しているセットメーカーの事業主の方
- 業務改革を伴うERP・基幹システム導入の具体的な実践事例やコストダウンの進め方についてご興味のあるセットメーカーの事業主の方
◆学べるポイントはこちら!
【Point01】従業員数30~300名のセットメーカーにおける「脱・エクセル」「脱・紙伝票」の手法がわかる!
~現場にExcelや紙伝票が散在しており、二重三重業務が常態化している・・・そんな現場の実態にお悩みのセットメーカー社長のためのセミナーです~
【Point02】従業員数30~300名のセットメーカーにおける生産性アップ&コストダウンの手法がわかる!
~自社の生産性アップやコストダウンの実現に向けて、どこから手を付けてよいかわからない・・・そんなセットメーカー社長のためのセミナーです~
【Point03】職人化・属人化している業務を改善するためのシステムを導入する方法がわかる!
~一部の熟練者・職人に依存している業務にシステムを導入・活用する方法がわかります~
【Point04】セットメーカーにおける実際のDX取り組み事例がわかる!
~理論・理屈ではなく、自社の現場で実践できる脱Excel&脱紙伝票の進め方がわかります~
本セミナーにご興味のある方は
是非「今すぐ!」以下のURLより詳細をご確認ください!
お申し込みはこちらから⇒
https://www.funaisoken.co.jp/seminar/111209
・セミナーの開催日(2024年4月16日、23日、24日)まで待てない!
・一刻も早く自社特有の課題について相談したい!
という方は、以下の「無料オンライン相談」を是非ご利用ください。
▼無料オンライン相談(お問い合わせはこちら)
https://lp.funaisoken.co.jp/mt/form01/inquiry-S045.html
基幹システム導入+業務改革事例レポート
レポートの内容
基幹システム導入・活用のポイントを丸ッとご紹介します!
- システム導入のポイント
- プロジェクト推進のポイント
- 導入、活用による効果事例紹介
「こうなりたい!」と思っている経営者様におすすめ
- 旧システムを刷新し、業務改革を実行したい経営者様
- 数々の業務効率化を図り、費用対効果の高いシステム導入を行いたい経営者様
- 紙だらけの業務をデジタル化したいと思っている経営者様
- 経験と勘に頼らないデータドリブン経営を実践したいと思っている経営者様
- スモールスタートからDXを始めたいと思っている経営者様
https://www.funaisoken.co.jp/dl-contents/smart-factory_smart-factory_02221_S045