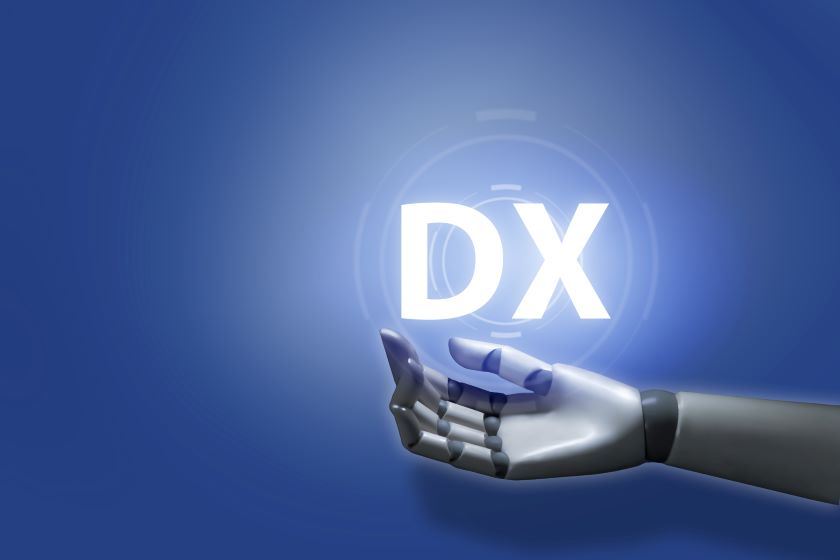
実話ベース|年商8000万の町工場が、データ分析で利益率を10%改善した物語
2025.08.28
※この物語は実話をもとにしたフィクションです。
「仕事はあるのに、なぜか月末になると手元に金が残らない…」
埼玉県にある、従業員5名の製本会社「鈴木製本」。 二代目社長の鈴木さん(55歳)は、毎月資金繰りのことで頭を悩ませていました。先代から受け継いだ会社は、地域の顧客にも恵まれ、仕事が途切れることはありません。しかし、利益はなぜか増えていかない。
これは、そんな崖っぷちの町工場が、たった一つのExcelファイルをきっかけに、会社を劇的に変えた物語です。
迫りくる赤字とベテランのプライド
「社長、A社の案件、また値引きですか…」
現場を取り仕切るベテラン職人の田中さん(62歳)が、苦い顔で社長に尋ねます。A社は売上の3割を占める大口顧客。しかし、その要求は年々厳しくなっていました。
「仕方ないだろう。A社を切ったらうちの経営は成り立たない」
社長の答えはいつも同じ。長年の付き合いと、「大口顧客を失う恐怖」が、正常な判断を鈍らせていました。ベテランの「勘」だけが頼りの経営は、とっくに限界を迎えていたのです。
若手社員・佐藤の挑戦
そんな空気を変えたのが、入社3年目の若手社員・佐藤くん(25歳)でした。彼は前職の営業事務で、Excelを使ったデータ集計の経験があったのです。
「社長、一度、この1年間の受注データを全部Excelに入力してみませんか?何か分かるかもしれません」
最初は「そんな暇なことやってられるか!」と一喝した社長。しかし、藁にもすがる思いで、佐藤くんに任せてみることにしました。ベテラン職人たちからは「そんな数字遊びで何が分かるんだ」と冷ややかな視線を浴びながらも、佐藤くんは黙々と作業を続けました。
たった一つのExcelファイルが示した「真実」
一週間後。佐藤くんが社長の前に一枚の集計表を差し出しました。 それは、顧客ごとの「年間利益額」と「案件ごとの利益率」をランキングにしたものでした。
そこに示された「真実」に、社長は言葉を失います。
売上1位のA社は、利益額ランキングでは15位。利益率はわずか3%。
一方、売上10位のBデザイン事務所は、利益額ランキングではなんと2位。小ロット・短納期の案件が多いが、利益率は30%を超えていました。
いつも無理難題を言うA社より、たまにWebサイト経由で依頼してくるBデザイン事務所の方が、よっぽど会社に貢献してくれていたのです。
会社が変わった日
「我々は、とんでもない勘違いをしていた…」
社長はすぐに行動を起こしました。 まず、Bデザイン事務所のような「小ロット・短納期・高利益率」の案件に特化する方針を打ち出しました。Webサイトを改修し、その強みを前面にアピール。営業リソースも、そのターゲット層に集中させました。
A社に対しては、勇気を出して価格交渉を実施。結果的に取引は縮小しましたが、高利益率の新規顧客が増えたことで、売上は少し落ちたものの、会社全体の利益率は10%以上も改善したのです。
データがもたらした、利益以上の「財産」
利益が増えたことだけが成果ではありませんでした。 一番の変化は、社内の雰囲気でした。データという「共通言語」ができたことで、ベテラン職人も若手社員も、対等に議論できるようになったのです。
「この案件は利益率が良いから、もっと効率化できないか?」 「このデータを見ると、次はこういう客層を狙うべきじゃないですか?」
かつて社長のワンマン経営だった会社は、今や全社員で会社の未来を考える組織に生まれ変わりました。データがもたらしたのは、利益以上に価値のある「組織の成長」という財産だったのです。
この物語は、あなたの会社の未来かもしれない
鈴木製本の話は、特別な成功体験ではありません。 どの会社にも、社内には必ず「宝の山」が眠っています。それに気づき、最初の一歩を踏み出すかどうか。違いは、ただそれだけです。
あなたの会社も、必ず変われます。
もし、自社のデータ活用について「何から始めればいいか分からない」「プロに相談してみたい」と思われたら、お気軽にご連絡ください。私たちが、あなたの会社の物語が始まる「最初の一歩」を、全力でサポートします。
データ活用による経営改善の無料相談はこちらから
https://formslp.funaisoken.co.jp/form01/lp/post/inquiry-S045.html?siteno=S045 ※この物語は実話をもとにしたフィクションです。
「仕事はあるのに、なぜか月末になると手元に金が残らない…」
埼玉県にある、従業員5名の製本会社「鈴木製本」。 二代目社長の鈴木さん(55歳)は、毎月資金繰りのことで頭を悩ませていました。先代から受け継いだ会社は、地域の顧客にも恵まれ、仕事が途切れることはありません。しかし、利益はなぜか増えていかない。
これは、そんな崖っぷちの町工場が、たった一つのExcelファイルをきっかけに、会社を劇的に変えた物語です。
迫りくる赤字とベテランのプライド
「社長、A社の案件、また値引きですか…」
現場を取り仕切るベテラン職人の田中さん(62歳)が、苦い顔で社長に尋ねます。A社は売上の3割を占める大口顧客。しかし、その要求は年々厳しくなっていました。
「仕方ないだろう。A社を切ったらうちの経営は成り立たない」
社長の答えはいつも同じ。長年の付き合いと、「大口顧客を失う恐怖」が、正常な判断を鈍らせていました。ベテランの「勘」だけが頼りの経営は、とっくに限界を迎えていたのです。
若手社員・佐藤の挑戦
そんな空気を変えたのが、入社3年目の若手社員・佐藤くん(25歳)でした。彼は前職の営業事務で、Excelを使ったデータ集計の経験があったのです。
「社長、一度、この1年間の受注データを全部Excelに入力してみませんか?何か分かるかもしれません」
最初は「そんな暇なことやってられるか!」と一喝した社長。しかし、藁にもすがる思いで、佐藤くんに任せてみることにしました。ベテラン職人たちからは「そんな数字遊びで何が分かるんだ」と冷ややかな視線を浴びながらも、佐藤くんは黙々と作業を続けました。
たった一つのExcelファイルが示した「真実」
一週間後。佐藤くんが社長の前に一枚の集計表を差し出しました。 それは、顧客ごとの「年間利益額」と「案件ごとの利益率」をランキングにしたものでした。
そこに示された「真実」に、社長は言葉を失います。
売上1位のA社は、利益額ランキングでは15位。利益率はわずか3%。
一方、売上10位のBデザイン事務所は、利益額ランキングではなんと2位。小ロット・短納期の案件が多いが、利益率は30%を超えていました。
いつも無理難題を言うA社より、たまにWebサイト経由で依頼してくるBデザイン事務所の方が、よっぽど会社に貢献してくれていたのです。
会社が変わった日
「我々は、とんでもない勘違いをしていた…」
社長はすぐに行動を起こしました。 まず、Bデザイン事務所のような「小ロット・短納期・高利益率」の案件に特化する方針を打ち出しました。Webサイトを改修し、その強みを前面にアピール。営業リソースも、そのターゲット層に集中させました。
A社に対しては、勇気を出して価格交渉を実施。結果的に取引は縮小しましたが、高利益率の新規顧客が増えたことで、売上は少し落ちたものの、会社全体の利益率は10%以上も改善したのです。
データがもたらした、利益以上の「財産」
利益が増えたことだけが成果ではありませんでした。 一番の変化は、社内の雰囲気でした。データという「共通言語」ができたことで、ベテラン職人も若手社員も、対等に議論できるようになったのです。
「この案件は利益率が良いから、もっと効率化できないか?」 「このデータを見ると、次はこういう客層を狙うべきじゃないですか?」
かつて社長のワンマン経営だった会社は、今や全社員で会社の未来を考える組織に生まれ変わりました。データがもたらしたのは、利益以上に価値のある「組織の成長」という財産だったのです。
この物語は、あなたの会社の未来かもしれない
鈴木製本の話は、特別な成功体験ではありません。 どの会社にも、社内には必ず「宝の山」が眠っています。それに気づき、最初の一歩を踏み出すかどうか。違いは、ただそれだけです。
あなたの会社も、必ず変われます。
もし、自社のデータ活用について「何から始めればいいか分からない」「プロに相談してみたい」と思われたら、お気軽にご連絡ください。私たちが、あなたの会社の物語が始まる「最初の一歩」を、全力でサポートします。
データ活用による経営改善の無料相談はこちらから
https://formslp.funaisoken.co.jp/form01/lp/post/inquiry-S045.html?siteno=S045