記事公開日:2025.02.05
最終更新日:2025.02.10
製造業の生産性向上とは?:メリット、成功事例、具体的な手法を徹底解説
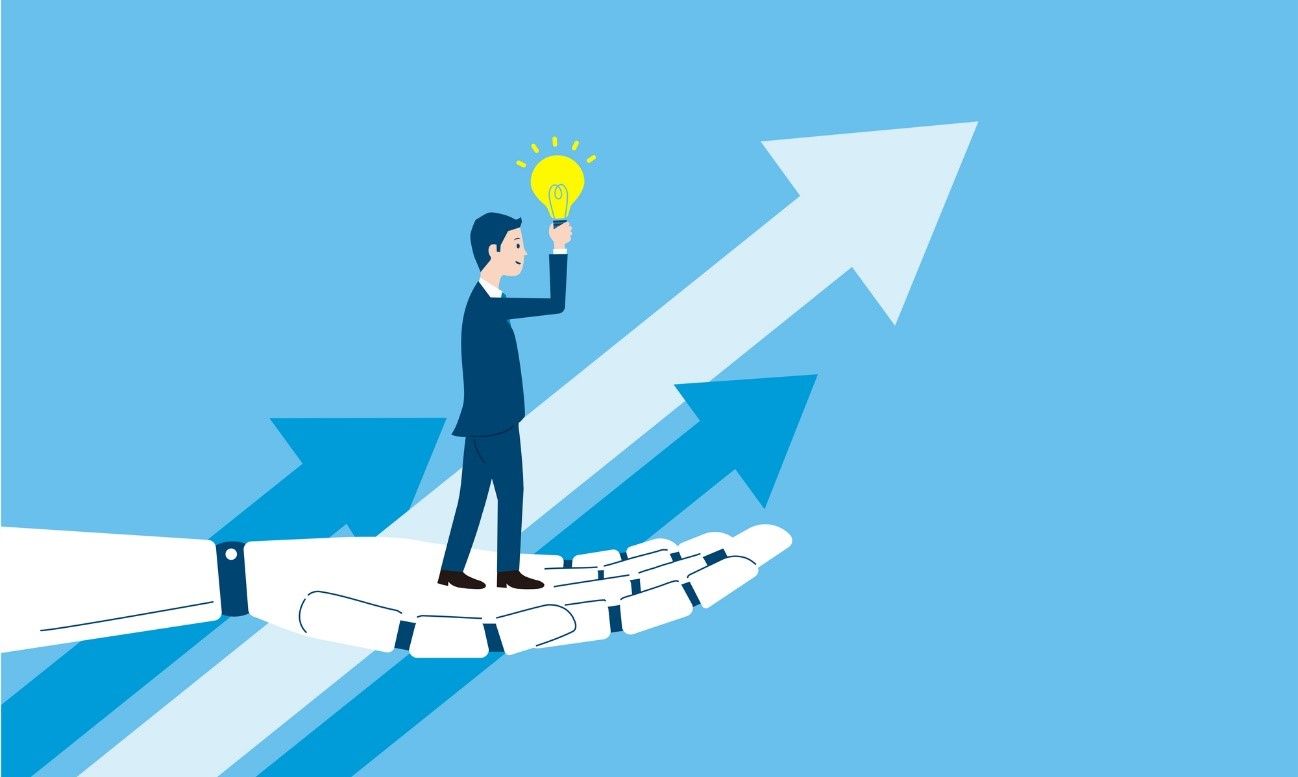
1. 生産性の定義と重要性
生産性とは
生産性とは、投入した生産要素をどれだけ有効に活用できたかを示す指標であり、インプット(投入)に対するアウトプット(産出)の割合で表されます。生産要素には、機械設備、土地、建物、エネルギー、原材料、そしてそれらを操作する人間などが含まれます。
生産性の向上は、企業の成長と発展に不可欠であり、特に労働人口の減少や国際競争の激化が進む現代において重要です。生産性向上とは、投入した資源に対し、より多くの成果や付加価値を生み出すことを意味します。
生産性の計算式は一般的に以下の通りです。
生産性 = アウトプット(生産量や付加価値) ÷ インプット(投入する人数や設備、時間)
生産性の種類
生産性には、物的生産性と付加価値生産性の2種類があり、それぞれ異なる側面から生産性を捉えます。
要約すると、
- 物的生産性: 生産物の物理的な量を基準に測定し、生産現場の効率を評価するのに適した指標です。
- 付加価値生産性: 企業が生み出した付加価値を基準に測定し、企業の経済的な価値創造能力を評価するのに適した指標です。
物的生産性は、生産物の大きさ、重さ、個数などの物量を単位として測定する生産性です。この指標は、生産現場における純粋な生産効率を測る際に特に有効です。なぜなら、生産物の価格は物価変動や技術進歩によって変動するため、物量を単位とすることで、価格変動の影響を受けずに生産効率を評価できるからです。例えば、生産能力や生産効率の時系列的な推移を知りたい場合などに、物的生産性が利用されます。
一方、付加価値生産性は、企業が新たに生み出した金額ベースの価値、つまり付加価値を単位とする生産性です。付加価値とは、売上高から原材料費、外注加工費、機械の修繕費、動力費など外部から購入した費用を差し引いたものです。企業は外部から購入したものを加工し販売しますが、その際に様々な形で手を加えることによって新たに付け加えた価値を金額で表したものが付加価値となります。付加価値は、人件費として労働に分配されたり、利益や配当などとして資本にも分配されます。したがって、生産性向上の成果をどのように分配するかという問題を考える上で、付加価値労働生産性は重要な指標となります。
これらの2種類の生産性は、生産性の向上を測る上で異なる視点を提供します。物的生産性は生産現場の効率を直接的に評価するのに役立ち、付加価値生産性は企業の経済的な価値創造能力を評価するのに役立ちます。
さらに、ここからさらに細分化された指標がこちらです。自社の状況を踏まえて、どの生産性指標を追いかけるか、検討する必要があります。
(公益財団法人 日本生産性本部「生産性とは」より
引用:https://www.jpc-net.jp/movement/productivity.html)
2. 生産性向上が求められる背景
まず人件費の高騰です。製造業の人件費は上昇を続けており、自動化による省人化が、人件費削減のカギとなります。
例えば 2024 年の春闘における、組合員数 300 名以下の中小企業 (2123 社)の賃上げ率は、4.75%と、過去最高の賃上げ率を記録しています。(2024 年 4 月 18 日時点)
引用:https://jp.reuters.com/markets/japan/funds/QCKCLLTJ6ZNWZOSLFMNJ5VP7FE-2024-04-18/
また、日系企業の海外拠点においても、平均賃金の上昇傾向が見られます。
図 A は、2020 年 1 月~2022 年 11 月における、在アメリカ日系製造業の平均時給の推移を示しています。
図 B では 2013 年~2023 年における、アジア各国の製造業の基本月給を比較しています。
図 A:2020 年 1 月~2022 年 11 月における、在米日系製造業の平均時給の推移
引用:https://www.jetro.go.jp/biz/areareports/2023/ab437b35a1ad87e0.html
図 B:2013 年~2023 年における、アジア各国の製造業の基本月給の比較
引用:https://www.jetro.go.jp/biz/areareports/2024/37977922f57e157a.html
これらの内容を鑑みると、海外拠点においても人件費の高騰が見られることがわかります。
次に労働人口の減少と人手不足の課題があります。生産年齢人口の減少が深刻化する中、作業員の確保が困難になっており、足りない人手を自動化で補う必要があります。
日本の人口は、2005 年をピークに減少傾向にあります。総務省が出しているデータによると、2005 年~2050 年の間で、総人口は 3,300 万人減少、若年人口 (15 歳未満の者の人口)は約 900 万人減少、生産年齢人口は約 3,500 万人減少、高齢人口(65 歳以上の者の人口)は約 1,200 万人増加すると見込まれています。
図 日本における総人口の推移と予測
引用:https://www.mhlw.go.jp/stf/newpage_21481.html
製造業においても、同様に人口減少の影響を受けています。総務省の労働力調査によると、2000 年~2019 年間において、若年層の就業者数割合が減少し、高齢者層の就業者数割合が増加しています。
現状でも人手不足を感じている企業様は多いかと思いますが、これからさらに人手不足が加速していくことが懸念されています。
図 就業者に占める若年者・高齢者の割合の推移
引用:総務省「労働力調査」
このように、工場の自動化は企業の根幹を左右する重要な経営課題となっているため、自動化を計画的に進めていく必要があります。
3. 生産性が低下する要因
生産性が低下する要因として、以下の6つのことがらが挙げられます。
1つ目は、コミュニケーション不足です。部門間の連携不足や情報共有の遅れは、手戻りやミスの増加を招き、作業効率を低下させます。 例えば、設計部門からの情報伝達が遅れたために、製造現場で手戻りが発生し、納期遅延につながることなどが挙げられます。
2つ目は、人材や時間の不足です。慢性的な労働力不足は、従業員一人当たりの業務負担を増やし、残業時間の増加や疲労蓄積を招き、生産性向上への取り組みを妨げます。例えば、人手不足により従業員が長時間労働を強いられ、疲労から作業ミスが増加し、生産性が低下することがあります。
3つ目は、業務の標準化不足です。作業手順や品質基準が標準化されていないと、従業員の経験やスキルによって品質にばらつきが生じ、ミスや不良品の発生につながります。例えば、熟練作業員しかできない作業があり、担当者が不在の場合に生産ラインが停止することがあります。
4つ目は、作業ミスです。作業手順の誤り、確認不足、不注意などによるミスは、手戻りや修正作業を発生させ、生産性を低下させます。例えば、組み立て工程で部品を間違えて取り付けてしまい、修正のために時間がかかることがあります。
5つ目は、デジタル化の遅れです。ITツールやシステムの導入が遅れていると、業務の効率化が進まず、人手による作業に頼ることが多くなり、生産性が低下します。例えば、紙ベースでの情報管理や手作業でのデータ入力が多く、非効率な業務が残っている場合があります。
6つ目は、管理不足です。需要予測や在庫管理が適切に行われていないと、過剰な在庫や材料不足が発生し、生産計画の遅延やコストの増加につながり、生産性を低下させます。例えば、需要予測が不正確で、過剰に製品を製造してしまい、在庫が増え、保管コストがかさむことがあります。
これらの課題は複合的に絡み合っており、中には単独部署では対応しきれない問題もあります。では、どのようにこれらの課題を解決し、生産性を向上していけばよいのでしょうか。
4. 生産性向上のための具体的な手法
次に、10個の生産性向上手法について、紹介します。製造業に長年従事した方にとっては釈迦に説法となりますが、お付き合いください。
1つ目は、課題の明確化です。まず、現状の生産プロセスにおける課題を洗い出し、改善すべき点を明確にすることが重要です。まず、業務の見える化をおこなうことが重要です。作業時間、品質、設備稼働状況などのデータを収集・分析し、ボトルネックとなっている工程を特定します。 例えば、生産ラインの各工程にかかる時間を計測し、最も時間がかかっている工程を特定することなどがこれにあたります。次に、従業員へのヒアリングを行いましょう。現場で働く従業員から意見やアイデアを聞き、問題点を把握します。
2つ目は、業務の標準化です。作業手順を標準化し、誰でも同じ品質で効率よく作業できるようにします。 まず、SOP(標準作業手順書)の作成・改善を行いましょう。作業手順、注意事項、品質基準などを文書化し、従業員が参照できるようにします。SOPには、文章だけでなく、画像や動画を活用して視覚的に分かりやすく説明することも効果的です。また、作業マニュアルの整備をおこなうことも重要です。作業手順を詳細に記述したマニュアルを作成し、従業員の教育や訓練に活用します。
3つ目は、生産管理の見直しです。生産計画、人員配置、資材調達などを最適化し、無駄を削減します。生産管理システムを導入することができれば、AIを活用したシステムも導入され、より効率的な生産管理が可能になっています。
- 設備・装置の改善:設備の機能性や効率を改善し、作業効率を高めます。
o 設備のレイアウト見直し:作業動線を考慮し、効率的な配置に変更します。
o 最新設備の導入:新型の工作機械や自動化設備を導入し、生産能力を高めます。 - IoT(Internet of Things)の導入・活用:生産設備や機器にセンサーを取り付け、データを収集・分析することで、生産状況をリアルタイムで可視化し、問題点の早期発見や改善に役立てます。
o 例:設備の稼働状況をリアルタイムで監視し、故障を未然に防ぐ。
o IoTを活用することで、従業員の負担を軽減したり、トラブルの発生を未然に防ぐこともできます。 - デジタル技術の活用:AI、ロボット、マシンビジョンシステムなどのデジタル技術を導入し、作業の自動化・省人化を進めます。
o 例:産業用ロボットを導入し、単純作業を自動化する。
o 例:AIによる画像処理を活用し、外観検査を自動化する。 - 5Sの徹底:「整理・整頓・清掃・清潔・しつけ」を徹底し、作業環境を改善し、無駄な動きをなくします。
o 例:工具や部品を所定の位置に保管し、探す時間を削減する。 - 多能工化:従業員が複数の業務をこなせるように育成し、人材不足や急な欠勤に対応できるようにします。
o 多能工化には、SOP(標準作業手順書)の整備が効果的です。 - 適切なコミュニケーション:部門間の情報共有や連携を密にし、スムーズな業務遂行を促します。
o コミュニケーションツール(チャット、ビデオ会議など)を活用し、情報共有を効率化します。 - ITツールの導入:業務効率化や人的ミスの防止のために、適切なITツールを導入します。
o RPA(ロボティック・プロセス・オートメーション):定型業務を自動化し、業務効率を向上させます。
o MES(製造実行システム):製造現場の情報を収集・分析し、生産状況の把握や改善に役立てます。
o ERP(基幹業務システム): 企業全体の情報を統合管理し、業務効率化や経営判断の迅速化を支援します。
5. 製造業における生産性向上成功事例5選
続いて、製造業において生産性向上を実現した事例について、5つ紹介します。
生産性向上 成功事例①:株式会社アスザック 自動バリ取りロボット
株式会社アスザックではロボットを使うことによって、工数がかかっていたバリ取り作業の自動化に成功しました。業種と自動化効果、投資金額は以下のようになっています。
業種 | セラミック製品製造 |
---|---|
自動化効果 | 年間工数 1019 時間削減・生産性 167%増 |
投資金額 | 1800 万円+6 軸ロボット費用 |
アスザックの成功事例の特徴は、画像認識によりバリ取りパスを自動で生成している点です。自動生成されたパスに沿ってロボットが動作するため、品種ごとにティーチングプログラムを作成する必要がなく、超多品種少量生産に対応することができます。
本来ロボットを稼働させる際は、ティーチングと呼ばれるロボットのプログラムを人が作成する必要があります。そのためロボットでさまざまな製品の加工をおこなおうとすると、その数だけティーチングをおこなう必要があります。
アスザックでは、画像認識による自動プログラム作成を採用しているため、作業員が治具に製品を置けば、ロボットが自動でバリ取りをおこなってくれます。
生産性向上 成功事例②:S社 協働ロボット
S 社では、協働ロボットを使うことによって、加工機へのワーク投入作業の自動化に成功しました。
業種 | 樹脂切削加工品製造 |
---|---|
自動化効果 | 年間工数1200時間削減 |
投資金額 | 500万円 |
S社の成功事例の特徴は、SIer なしでロボット導入を行った点です。ロボット導入のネックになりがちな費用として、SIer 費用があげられます。 (S社でロボット導入を検討した際は、ロボット本体代金のほかに SIer 費用が 1000 万円近く見積もられていました。)
S社では、自社で内製化することで、SIer 費用を押さえながらロボット活用を行うことに成功しました。
内製化の利点は、自動化品種の追加や、製造ラインの変更に比較的容易に対応できることです。ロボット立ち上げ時に、技術的な開発部分を SIer に任せてしまうと、新たに品種追加を行う際はさらに SIer に費用を払わなくてはなりません。内製化は時間も工数もかかりますが、中長期的に見れば経営効果は高いでしょう。
また、この会社様は従業員数 10 名以下の会社様のため、1 日数時間だけ単純作業を自動化するだけでも、高い自動化効果を発揮することができます。従業員数が少なくなればなるほど捻出される時間の価値が高まるため、ロボット活用は事業規模が小さい会社様ほど効果を発揮できるといえます。
⇒関連記事:日本&海外の協働ロボットメーカー16社の特徴を紹介!
⇒関連記事:協働ロボットの特徴と導入事例
生産性向上 成功事例③:C 社溶接ロボット・研磨ロボット
C社では、高い品質が求められる製品において、溶接工程と研磨工程の自動化に成功しました。
業種 | 鈑金溶接品製造 |
---|---|
自動化効果 | 溶接・研磨の熟練技術の継承に成功 |
投資金額 | 7700万円(うち4000万円は補助金) |
C社の成功事例の特徴は、非常に難易度の高い薄板ステンレスの TIG 溶接と鏡面研磨を最新技術を活用して自動化した点です。さらに投資金額 7700 万円のうち 4000 万円は事業再構築補助金を活用することにより投資コストを抑えています。
薄板の TIG 溶接は非常に熟練度が要求される作業であり、早い人でも製品として出荷できるレベルに達するまでには 5 年はかかる職人技術と言われています。また、C社の製品における研磨工程は鏡面仕上げとなっており相当の工数がかかっている状態でした。
これら難易度の高い職人技術を 6 軸力覚、加速度、位置センサー、アクティブ・コンプライアンス制御技術を用いて自動化に成功しました。
生産性向上 成功事例④:S社 AI 外観検査
S社では、樹脂成形製品の目視検査をAI外観検査で自動化に成功しました。
業種 | 樹脂成型品製造 |
---|---|
自動化効果 | 検査人員 2 名削減・1400 万円/年のコスト削減 |
投資金額 | 2400 万円 |
S社の成功事例の特徴は、製品自体を回転させながら撮像をおこない、AIに不良品判定を行わせている点です。
S社では、通常では検査が難しい透明の円筒形製品検査の自動化に取り組みました。製品自体を回転させ、且つ撮像した製品画像をAIで処理することで、不良品判定の自動化を成功させました。
明確な金額は記載しませんが、S社も補助金を活用することで投資費用を抑えています。
⇒関連記事:AI外観検査とは?従来の画像検査との違い、導入のメリットや注意点とは?
生産性向上 成功事例⑤:A社 協働ロボット
A社では、100 台の協働ロボットを導入し、ワーク投入やエアブロー、検査などの自動化に成功しました。
業種 | 金属部品加工 |
---|---|
自動化効果 | 人員 60名削減・2.5億/年のコスト削減 |
投資金額 | 協働ロボット 100台分 |
A社の成功事例の特徴は、S社と同様SIerレスで自動化に成功した点です。PLCが扱える人材を採用し、徹底してロボット活用の社内教育を行うことで、コストを抑えた圧倒的な自動化を実現しました。
総額では大きい投資となっていますが、それに見合うだけの費用対効果を実現しています。
6.まとめ
生産性とは、投入資源に対する産出の効率性を測る指標です。生産性低下の要因は、コミュニケーション不足、人材不足、標準化不足、作業ミス、デジタル化の遅れ、管理不足など多岐に渡ります。
これらの課題を解決し、生産性を向上させるために、上記に記載の手法が有効です。
是非、貴社の生産性向上にお役立てください。