記事公開日:2025.03.04
最終更新日:2025.04.02
製造業の工程分析:多品種少量生産の課題解決と生産性向上のための 完全ガイド
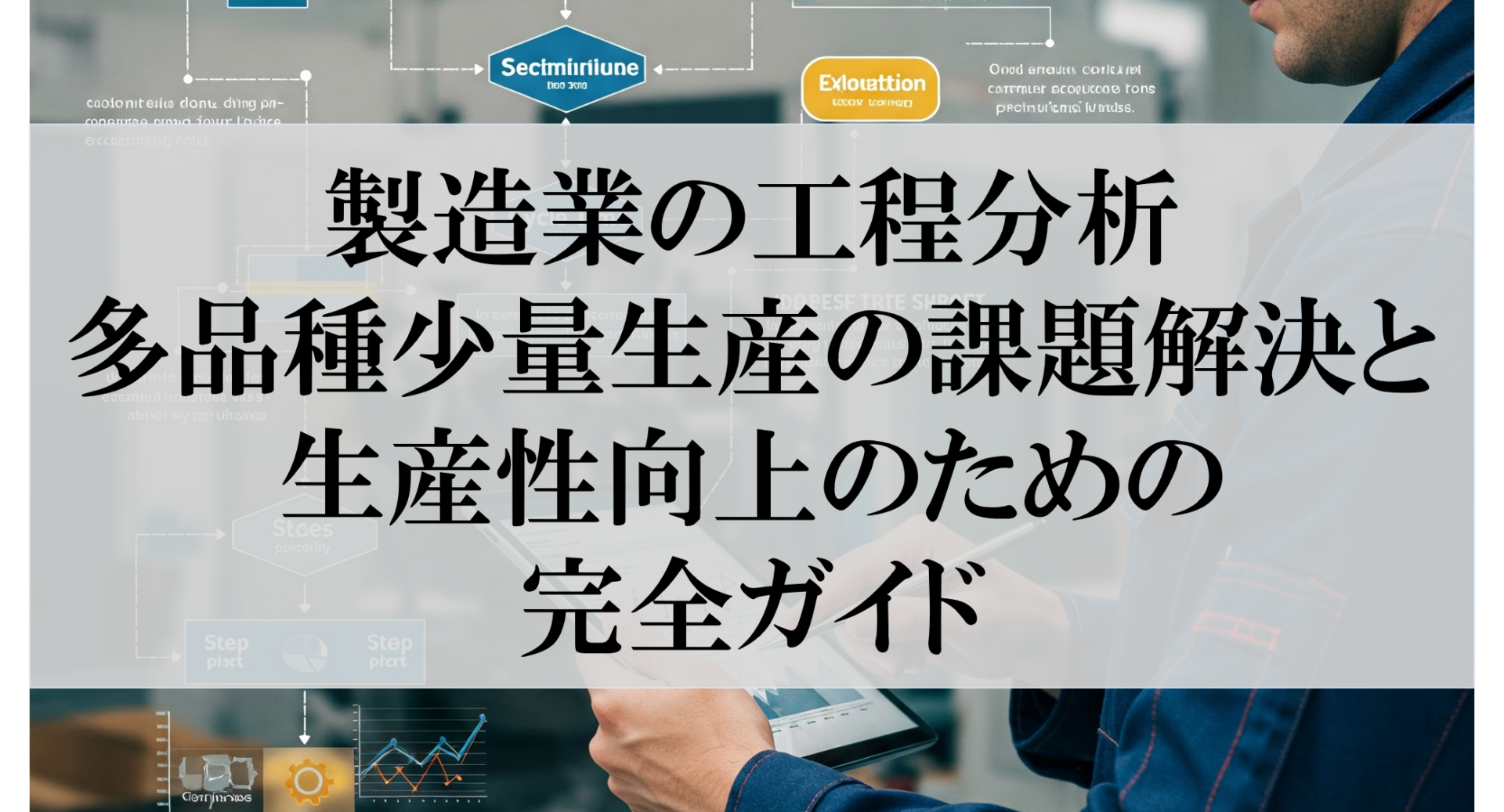
製造業の工程分析に悩む方必見!
多品種少量生産の生産性向上を実現する、工程分析の完全ガイド。
IE、SMED、TOC、IoTなど、現場で役立つ手法を網羅的に解説。
ムダの排除、段取り改善、生産計画の最適化、人材育成まで、多角的な視点から改善活動を支援します。
目次
はじめに:多品種少量生産の現場が抱える課題
現代の製造業、特に中小製造業において、多品種少量生産は避けて通れない現実です。顧客ニーズの多様化、製品ライフサイクルの短期化、そしてグローバル競争の激化といった要因が複雑に絡み合い、従来の大量生産方式では対応しきれない状況が生まれています。
多品種少量生産の現場では、品種ごとの仕様変更や段取り替えが頻繁に発生し、効率的な生産が困難になります。
「同じ設備、人員で、いかに生産性を上げるか?」
これは多くの中小企業経営者や工場長にとって、日々の切実な課題です。
本記事では、多品種少量生産に特化した工程分析の手法を詳細に解説します。現場の生産性向上に直結する具体的な施策を、理論から実践まで網羅的にご紹介します。
1. 多品種少量生産の特徴と生産性向上のカギ
1.1. 多品種少量生産の特徴:多様性と複雑性
多品種少量生産は、同じ設備や人員で多様な製品を少量ずつ生産する方式です。
その特徴は、単に「多品種少量」であるというだけでなく、以下のような複雑な要素を含んでいます。
- 頻繁な仕様変更と段取り替え
品種ごとに異なる仕様に対応するため、頻繁な段取り替えや設定変更が必要です。これにより、機械の稼働率が低下し、生産リードタイムが長くなる傾向があります。 - オーダーメイド要素の強さと標準化の困難性
顧客の個別ニーズに合わせたオーダーメイド的な要素が強く、生産プロセスの標準化が難しい場合があります。これにより、作業者の熟練度による品質のばらつきや、生産効率の低下が発生しやすくなります。 - 需要変動の大きさと計画的生産の難しさ
需要の変動が大きく、予測が困難なため、計画的な生産が難しい場合があります。過剰在庫や納期遅延のリスクが高まります。 - 在庫コスト抑制の必要性と過剰生産の制約
在庫コストを抑制するため、過剰生産ができないという制約があります。必要な時に必要な量だけを生産する、高度な生産管理が求められます。
1.2. 生産性向上のカギ:4つの視点
多品種少量生産における生産性向上は、単一の解決策では達成できません。多角的なアプローチが求められます。ここでは、生産性向上のための4つの重要な視点を紹介します。
① ムダの徹底排除(工程分析・作業研究)
IE(インダストリアル・エンジニアリング)などの手法を用い、工程全体のムダを徹底的に洗い出し、排除します。
② 段取り時間の短縮(SMED・段取り改善)
SMED(シングル段取り替え)などの手法を活用し、段取り時間を短縮することで、機械の稼働率を向上させます。
③ 生産計画の最適化(スケジューリング・TOC)
TOC(制約理論)などの手法を用いて、ボトルネック工程を解消し、生産計画を最適化します。
④ 現場の見える化と改善活動の継続(IoT・デジタル化)
IoTやMES(製造実行システム)などのデジタル技術を活用し、現場の状況をリアルタイムで把握し、継続的な改善活動を推進します。
以下、各ポイントについて具体的な手法を詳しく解説します。
2. 工程の可視化と分析:ムダを徹底排除する
まずは「何がムダなのか?」を明確にするため、工程分析を行います。
2.1. IE(インダストリアル・エンジニアリング)の活用
IE(インダストリアル・エンジニアリング)は、生産工程を科学的に分析し、効率化するための手法です。多品種少量生産の現場では、その有効性が特に高まります。
フローチャートによる工程の可視化
まず、工程全体の流れをフローチャートとして可視化し、どの部分にムダが発生しているのかを洗い出します。これにより、どの作業がボトルネックになっているかの把握や、無駄な手順が明確になります。
・フローチャート作成のポイント
- 作業の開始から完了まで、全ての工程を網羅する。
- 各工程の担当者、使用する設備、時間などの情報を記載する。
- フローチャート作成ソフトやツールを活用する。
作業区分VA/NVA(付加価値・非付加価値)分析
次に、各作業を「付加価値(VA)」と「非付加価値(NVA)」に分類します。
生産性向上のためには、非付加価値作業を削減することが重要です。例えば、部品を取りに行く移動や、待機時間などが非付加価値作業に該当します。これらを削減することで、全体の作業効率を高めることができます。
- VAとNVAの具体例
・VA:製品の加工、組み立て、検査など、顧客が価値を感じる作業。
・NVA:移動、待ち時間、手直しなど、顧客が価値を感じない作業。 - NVAを削減する際のポイント
・NVAの中でも、特に時間やコストがかかっている作業を優先的に改善する。
・現場の作業者から意見を聞き、改善アイデアを収集する。
動作分析と時間研究
動作分析では、作業者が行う各動作を細かく分析し、最適な動作を定義します。
さらに、時間研究を行い、作業標準を設定することで、無駄な時間を削減することが可能です。例えば、ある作業が5秒で行えるところを3秒に短縮することができれば、全体の生産性が大きく向上します。
- 動作分析の目的
・無駄な動作を排除し、作業者の負担を軽減する。
・作業者の熟練度に左右されない、標準的な作業方法を確立する。 - 時間研究の目的
・各作業の標準時間を設定し、生産計画の精度を高める。
・作業者の生産性を評価し、改善の余地を見つける。
2.2. ECRSの原則に基づいた改善:4つの視点
ECRSは、工程改善の基本的な考え方であり、以下の4つの原則に基づいています。
- E(Eliminate:排除):不要な作業をなくす
排除の検討ポイント
・本当に必要な作業か?
・他の作業で代替できないか?
・作業の目的は何か? - C(Combine:結合):一緒にできる作業をまとめる
結合の検討ポイント
・作業の順序を入れ替えることで、同時に行える作業はないか?
・同じ場所で行う作業をまとめることはできないか?
・使用する設備や工具を共通化できないか? - R(Rearrange:並べ替え):作業順序を最適化する
並べ替えの検討ポイント
・作業の順序を入れ替えることで、移動距離や待ち時間を減らせないか?
・流れ作業を導入できないか?
・作業者の動線を考慮したレイアウトに変更できないか? - S(Simplify:簡素化):作業をシンプルにする
簡素化の検討ポイント
・作業手順を減らすことはできないか?
・専用の治具や工具を導入できないか?
・チェックリストやマニュアルを作成できないか?
3. 段取り時間の短縮:SMEDを活用する
段取り替えの時間は、多品種少量生産の大きなボトルネックとなります。この段取り時間を短縮するために、SMED(Single Minute Exchange of Die)という手法を活用します。
3.1. SMEDの基本的な手法
SMEDは、段取り時間を10分以内に短縮することを目指す手法です。
内段取りと外段取りの分離
段取り作業を、機械停止中に行う内段取りと、機械稼働中に行う外段取りに分け、内段取りを可能な限り外段取りに移行します。
- 内段取りの具体例:金型交換、工具交換、設定変更など。
- 外段取りの具体例:材料や工具の準備、段取り手順の確認など。
内段取りの外段取り化
内段取り作業を、機械稼働中でも可能なように工夫します。
- 事前準備:材料や工具を事前に準備しておく。
- ワンタッチ化:治具や工具の取り付け・取り外しをワンタッチで行えるようにする。
- 並行作業:複数の作業者が同時に作業を行う。
段取り作業の改善
段取り作業自体を効率化します。
- 標準化:段取り手順を標準化し、誰でも同じ時間で作業できるようにする。
- 専用工具・治具の導入:段取り作業専用の工具や治具を導入し、作業時間を短縮する。
- チェックリストの活用:段取り作業の抜けや漏れを防ぐために、チェックリストを活用する。
3.2. 治工具や材料の標準化:効率化の基盤
多品種少量生産における段取り時間を短縮するためには、治工具や材料の標準化を進めることが重要です。特に、頻繁に使用される工具や部品に関しては、規格を統一し、準備作業を簡素化します。
治工具の標準化
- 汎用性の高い治工具を導入し、品種ごとの専用治工具を減らす。
- 治工具の取り付け・取り外し方法を標準化し、作業時間を短縮する。
- 治工具の保管場所を整理整頓し、探す時間を削減する。
材料の標準化
- 共通部品や材料の使用率を高め、品種ごとの専用部品や材料を減らす。
- 材料の形状やサイズを標準化し、加工や組み立ての効率を高める。
- 材料の保管方法を標準化し、取り出しやすくする。
3.3. 段取り手順のマニュアル化:知識と経験の共有
また、段取り手順をマニュアル化し、作業者に標準的な手順を教えることも有効です。
これにより、誰が作業をしても同じ効率で段取りを進めることができ、安定した生産性を確保できます。
マニュアル作成のポイント
- 図や写真、動画などを活用し、視覚的に分かりやすいマニュアルを作成する。
- 作業手順だけでなく、注意点やコツなども記載する。
- 定期的にマニュアルを見直し、改善する。
- 教育・訓練
・マニュアルを使用して作業者に対して教育・訓練を実施する。
・熟練作業者による技能伝承を行う。
4. 生産計画とスケジューリングの最適化
計画がうまく立てられなければ、いくら工程改善をしても生産効率は上がりません。
4.1. TOC(制約理論)の活用:ボトルネック解消
生産性向上に向けたもう一つの重要な手法が、TOC(制約理論)です。TOCは、ボトルネックとなる工程を特定し、その部分を改善することで、全体の生産性を向上させる理論です。
多品種少量生産の現場では、変動する需要や複雑な工程に対応するために、TOCの考え方が非常に有効です。
ボトルネックの特定
- 生産ライン全体の工程を分析し、最も生産性が低いボトルネック工程を特定します。
- ボトルネック工程は、生産ライン全体の生産能力を制限している箇所です。
- ボトルネックは常に一定とは限りません。生産する製品や状況によって変化します。
ボトルネック改善
- ボトルネック工程を重点的に改善し、その他の工程をそれに合わせて調整します。
- ボトルネック改善のポイント
・ボトルネック工程の稼働率を最大化する。
・ボトルネック工程の作業時間を短縮する。
・ボトルネック工程の品質を向上させる。
・ボトルネック工程の前工程にバッファを置く。
バッファ管理
- バッファ管理とは、生産ラインのどの部分に余裕を持たせるかを決めることで、ボトルネックに対して適切な対策を講じる手法です。
- 納期遅延を防ぐために、納期前バッファを置く。
- 品質不良が発生した場合に、手戻りを吸収するための、品質バッファを置く。
4.2. スケジューリングの最適化:納期遵守と生産性向上
深層学習アルゴリズムを応用した某化学メーカーの原価管理システムでは、原材料価格の変動や為替リスクを瞬時に反映した製品原価のシミュレーションが可能となっています。このシステムにより、受注段階で複数の調達シナリオに基づく利益率予測を比較検討できるようになり、為替ヘッジ戦略の精度が飛躍的に向上しました。
スケジューリングのポイント
- 需要予測に基づき、生産計画を立案する。
- 各工程の能力や段取り時間を考慮し、詳細なスケジュールを作成する。
- 納期や優先順位を考慮し、最適な生産順序を決定する。
- 進捗状況をリアルタイムで把握し、必要に応じてスケジュールを修正する。
- スケジューラーの活用
・生産スケジューラーを活用する事でより高度なスケジューリングが可能になる。
・過去のビックデータを活用する事で、より精度の高いスケジューリングを行う。
5. IT・デジタル技術の活用:現場の見える化と効率化
5.1. IoT・MES(製造実行システム)による現場の見える化:リアルタイムな情報共有
現場でのデータをリアルタイムで収集し、可視化することが、生産性向上には不可欠です。IoTセンサーを導入し、生産状況や機械の稼働状況を常に把握できるようにします。
リアルタイムモニタリング
- 各機械や作業員の状態をリアルタイムでモニタリングすることで、問題が発生した際にすぐに対処できます。
- 例えば、機械が故障した場合でも、早期に異常を検出し、ダウンタイムを最小限に抑えることが可能です。
- IoTセンサーを取り付ける事で、稼働率、温度、湿度、振動等の情報が自動的に収集され、モニタリングが容易となります。
MESの導入
- 製造実行システム(MES)は、生産ライン全体の情報を統合し、最適な生産計画を立てるために有効です。
- MESにより、スケジューリングや生産進捗の管理がリアルタイムで可能となり、計画通りの生産が実現します。
- MES導入のメリット
・トレーサビリティの確保
MESを導入する事で、原材料の入荷から製品の出荷までの製造履歴を追跡可能となる。
・品質管理の向上
MESは、検査結果や不良情報をリアルタイムで収集・分析することで、品質管理の向上を支援する。
・ペーパーレス化
MESは、作業指示書や検査記録などの紙ベースの情報をデジタル化することで、ペーパーレス化を促進する。
5.2. データ分析とAIの活用:高度な意思決定
収集したデータを分析し、AIを活用することで、より高度な意思決定が可能になります。
データ分析
- 生産データを分析し、傾向やパターンを把握することで、改善のヒントを見つけます。
- 例えば、不良率の高い工程や、稼働率の低い機械などを特定することができます。
- データ分析を行う事で、属人化されたノウハウを形式知化することが可能となります。
AIの活用
- AIを活用することで、需要予測や生産計画の精度を高めることができます。
- また、AIによる画像認識技術を活用することで、外観検査などを自動化することも可能です。
- AIを活用し、設備の故障予知を行う事で、突発的な停止を回避できます。
6. 改善活動を定着させるための人材育成と組織作り
6.1. 人材育成:改善マインドの醸成
改善活動を持続的に行うためには、現場の人材育成が不可欠です。作業者には、改善活動の重要性を理解してもらい、改善策を実践するためのスキルを身につけてもらう必要があります。
トレーニングと教育
トレーニングや教育を通じて、改善手法(SMED、TOC、IEなど)を習得させることが大切です。また、現場での意識改革を促進し、改善活動を継続的に実施できるようにします。
改善提案制度
作業者からの改善提案を積極的に受け入れ、評価する制度を導入します。
これにより、作業者の改善意識を高め、現場からの改善アイデアを収集することができます。
多能工化
複数の工程を担当できる多能工を育成する事で、急な欠員や、生産状況の変化にも柔軟に対応できるようになります。
6.2. 組織作り:継続的な改善サイクルの確立
組織としての仕組みも重要です。改善活動を支えるためのチームを作り、定期的なミーティングやPDCAサイクルを活用して改善活動を推進します。管理職やリーダーは、現場の声を反映させながら、改善策の進捗状況をチェックし、必要に応じて修正を加える役割を果たします。
改善チームの設立
改善活動を推進するための専門チームを設立し、定期的なミーティングやPDCAサイクルを活用して改善活動を推進します。
リーダーシップ
管理職やリーダーは、現場の声を反映させながら、改善策の進捗状況をチェックし、必要に応じて修正を加える役割を果たします。
評価制度
改善活動の成果を評価する制度を導入し、作業者のモチベーションを高めます。
情報の共有
改善事例や成功事例を共有することで、他の作業者の改善意欲を高め、改善活動の水平展開を促進します。
まとめ
多品種少量生産における生産性向上には、工程分析や段取り改善、IT技術の活用などさまざまな手法が必要です。これらを組み合わせて、ムダを排除し、効率的な生産体制を築くことが求められます。また、改善活動を定着させるためには、人材育成と組織作りも重要な要素となります。
改善手法を積極的に導入し、持続可能な生産性向上を実現するために、日々の努力と工夫を続けていきましょう。
今回では、多品種少量生産である工場における工程分析の重要性について説明をしてまいりました。
弊社が主催している下記セミナーでは、自社の生き残りをかけたDXの取組を、実際の事例をもとにお話ししています。
【このような社長におすすめ】
- 多品種少量生産の窯業・土石製品製造業の社長
- 長年の職人技術に依存した生産体制が続いており、データ化・データ活用ができていない。
- 標準原価で収益管理しているが、材料費高騰・賃上げに対応できていない。
- Excel運用が多く、社内での情報共有がリアルタイムにできない。
- 原価管理をどのように利益UPに結びつけるか具体的な方法を知りたい。
- 経営指標はもちろんだが、現場指標を設けて従業員に経営意識を持たせたい。
【本セミナーで学べるポイント】
- 実際原価管理・現場改善による利益率UPを実践した成功事例がわかる!
~実際原価管理がどのように経営に影響したのかを実際の資料をもとにお伝えします~ - 現場自らが動き出せる現場指標・経営意識を持つための原価管理方法がわかる!
~今すぐに取り組める現場指標管理方法をお教えします~ - 現場の実際工数を経営や現場が活用できるように分析する方法がわかる!
~経営陣だけでなく現場自らが動きだせるデータ分析方法がわかります~ - 多品種少量”だからこそ”今すぐ実践できる原価管理DX・利益UPまでの道筋が分かる!
~理論・理屈ではなく、自社の現場で実践できる具体的なDX経営手法が分かります~
https://www.funaisoken.co.jp/seminar/124761
https://www.funaisoken.co.jp/dl-contents/smart-factory_smart-factory_03729_S045