記事公開日:2025.03.12
最終更新日:2025.03.19
生産性向上のための、工場レイアウト最適化の手法
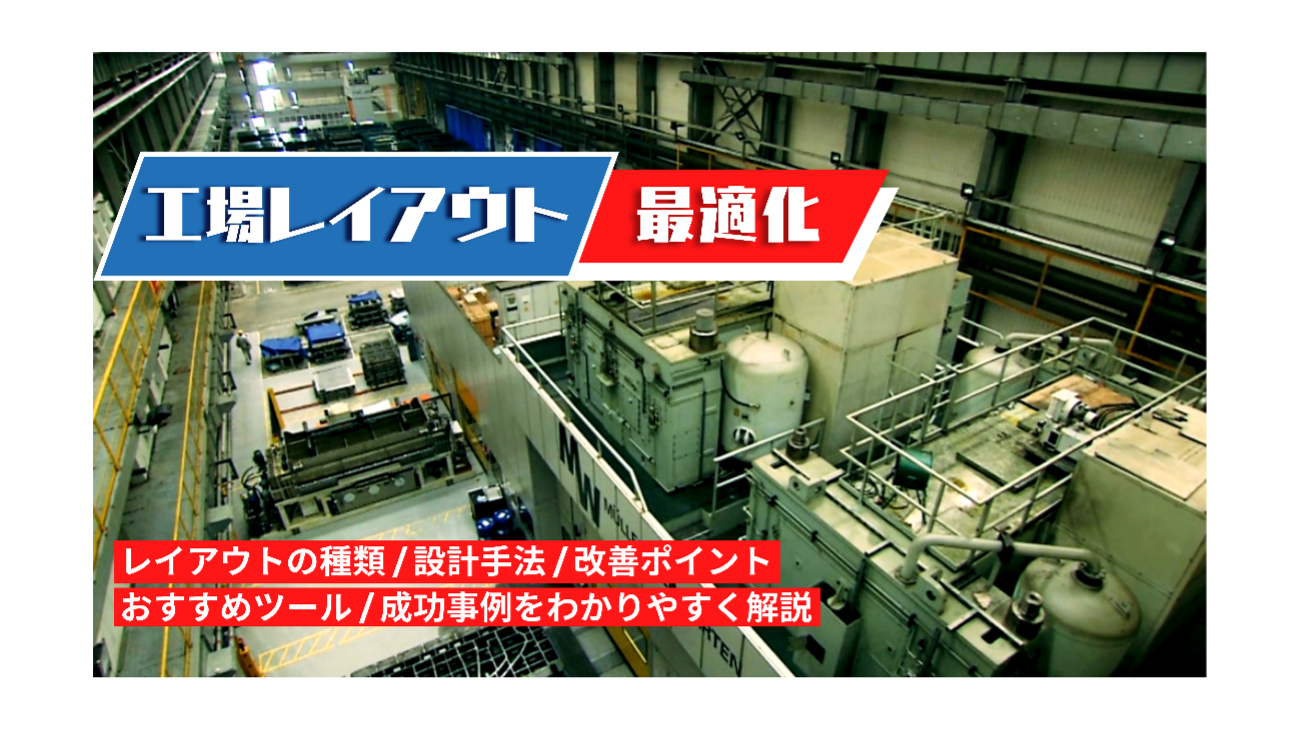
工場レイアウトは、単なる機械の配置ではありません。製品の品質、生産性、安全性、そして従業員の満足度にまで影響を与える、企業の根幹を支える重要な要素です。しかし、多くの企業が現状のレイアウトに課題を感じながらも、どのように改善すべきか悩んでいます。
本記事では、レイアウトの種類、設計手法、改善ポイント、おすすめツール、成功事例まで、わかりやすく解説します。この記事を読めば、あなたの工場も劇的に生まれ変わり、生産性向上と競争力強化へ一歩を踏み
出すことができるでしょう。
目次
1. 工場レイアウトとは?工場レイアウトの概要と重要性
工場レイアウトとは、工場内における人、機械、設備、資材などの配置計画のことです。効率的なレイアウトは、生産性の向上、コスト削減、品質向上、安全性の確保など、多岐にわたるメリットをもたらします。逆に、不適切なレイアウトは、作業効率の低下、人的ミスの増加、事故のリスク増大など、様々な問題を引き起こす可能性があります。
製造業を取り巻く環境が変化し、多品種少量生産や短納期への対応が求められる中で、工場レイアウトの重要性はますます高まっています。
2. 工場レイアウトの種類と特徴
工場レイアウトは、主に以下の3つの種類に分けられます。
工場レイアウトは、製品の生産方法や工場の規模、取り扱う製品の種類などによって最適なものが異なります。ここでは、代表的な3つのレイアウトタイプを、それぞれの特徴、メリット・デメリットを解説します。
・ジョブショップ型(機能別レイアウト)
ジョブショップ型レイアウトは、同じ機能を持つ設備や作業場を一つのエリアにまとめる方式です。例として、旋盤、フライス盤、研磨機などの工作機械をそれぞれ専用のエリアに配置する工場が挙げられます。
このレイアウトの最大のメリットは、多品種少量生産に柔軟に対応できることです。専門性の高い設備や作業者が集約されているため、様々な製品を効率的に製造できます。また、設備のメンテナンスや管理も容易です。一方、デメリットとしては、製品の製造工程が複雑になりやすく、搬送距離が長くなる傾向があります。これにより、リードタイムが長くなり、在庫管理も煩雑になる可能性があります。熟練した作業者の配置も必須です。
事例:多種多様な部品加工を行う機械工場、試作品製造を行う工場など。
・ライン型(工程別レイアウト)
ライン型レイアウトは、製品の製造工程順に設備や作業場を配置する方式です。自動車の組立ラインや食品の製造ラインなどが代表的な例です。
このレイアウトのメリットは、大量生産に特化しており、効率性と生産性が非常に高いことです。自動化が進めやすく、品質の安定化も図りやすいです。しかし、製品の種類変更や生産量の調整には柔軟に対応しにくいというデメリットがあります。また、一部の工程が停止すると、全体の生産ラインが停止してしまうリスクもあります。
事例:自動車の組立工場、家電製品の製造工場、食品の大量生産工場など。
・セル型(作業者中心レイアウト)
セル型レイアウトは、一人の作業者または少数の作業者グループが、製品の完成まで一貫して作業を行う方式です。多品種少量生産に対応しやすく、作業者の多能工化を促進します。
メリットとしては、作業者の責任感やモチベーションが高まりやすく、品質向上やリードタイム短縮につながることが挙げられます。また、柔軟な生産体制を構築できます。デメリットとしては、作業者の教育に時間がかかることや、レイアウト変更に柔軟な対応が求められることが挙げられます。
事例:電子機器の組み立て工場、精密機械の製造工場など。
3. 工場レイアウト最適化の重要性と効果
工場レイアウトを最適化することで、以下のような効果が期待できます。
- 生産性向上: 作業効率の向上、リードタイムの短縮、在庫削減など。
- コスト削減: 無駄なスペースや移動の削減、エネルギーコストの削減など。
- 品質向上: 作業の標準化、不良品発生の抑制など。
- 安全確保: 作業動線の確保、事故リスクの低減など。
- 従業員のモチベーション向上: 快適な作業環境の提供、作業負担の軽減など。
- 競争力強化: 生産効率の向上、顧客満足度の向上など。
関連記事:工場の自動化 (ファクトリーオートメーション) とは?成功事例5選やメリット、実現の流れを一挙解説!
4. 工場レイアウト設計の基本ステップ:SLPとは?
工場レイアウトの設計には、SLP(システマティック・レイアウト・プランニング)という体系的な手法が有効です。ここでは、工程レイアウト時に踏むべきステップについて解説します。
- Step1:P-Q分析(製品・数量分析)
▲P-Q分析サンプル図
P-Q分析は、製品の種類(Product)と生産量(Quantity)を分析し、最適なレイアウトタイプを選定するための基礎データを提供します。製品の種類や生産量に応じて、ジョブショップ型、ライン型、セル型などのレイアウトタイプを選択します。
具体的には、製品ごとの生産量や需要予測をグラフや表にまとめ、上位の製品を特定します。上位の製品は、ライン型レイアウトなど、大量生産に適した方式を選択する根拠となります。
- Step2:物・作業者の動線分析(動線分析)
▲作業者のスパゲティチャートサンプル
物の流れ分析は、原材料の入荷から製品の出荷までの全工程における物の動きを可視化し、最適な動線を設計するための分析です。また、作業者の動線分析とは、作業者の動きを可視化し、最適な動線を設計するための分析です。
フロム・ツーチャートやフローチャート、スパゲティチャート等を用いて、工程間の物/作業者の移動量や頻度、移動距離などを詳細に調査し、無駄な動きや非効率な流れを特定します。
この分析結果に基づいて、搬送距離の短縮、搬送時間の短縮、搬送回数の削減などを考慮したレイアウトを設計します。
- Step3:アクティビティ相互関係図表・ダイヤグラム作成
アクティビティ相互関係図表は、各作業区域や部門間の関係性を評価し、配置の優先順位を決定するためのツールです。
近接していることが望ましい区域や、逆に離れていることが望ましい区域を特定し、視覚的に理解しやすい形で表現します。
例えば、騒音の多い区域と静かな環境が必要な区域は離す必要があります。また、関連性の高い工程は近くに配置することで、作業効率を高めます。アクティビティ相互関係ダイヤグラムは、図表をもとに、各区域の位置関係を図式化したもので、関係の強さに応じて線の太さや本数を変えるなどして表現されます。
- Step4:スペース相互関係ダイヤグラム作成
スペース相互関係ダイヤグラムは、前段階で作成したアクティビティ相互関係ダイヤグラムに、各区域の必要面積を加味したものです。
機械設備のサイズ、作業スペース、通路幅などを考慮し、実際の工場の広さに合わせてスケールを調整します。
このステップにより、より現実的なレイアウトプランを作成することができます。
- Step5:レイアウト案の作成と評価
これまでの分析と検討をもとに、具体的なレイアウト案を複数作成し、効率性、柔軟性、拡張性、安全性などの観点から評価を行います。
各案について、シミュレーションソフトなどを用いて検証し、最適な案を選定します。
また、将来の生産計画や技術革新なども考慮に入れ、長期的な視点でレイアウトを決定することが重要です。
- Step6:レイアウト変更の実施
レイアウト案の評価結果を踏まえ、最終的なレイアウトを決定し、変更作業を実施します。機械設備の移動、配管・配線の変更、床面の整備など、事前に綿密な計画を立て、関係部署と連携してスムーズな変更作業を行います。また、安全対策を徹底し、作業中の事故防止にも努めます。
- Step7:レイアウト改善の効果検証・調整
レイアウト変更後、一定期間を経て、実際の生産状況や作業者の意見などを基に、レイアウト改善の効果を検証します。生産性、リードタイム、稼働率、作業者の動線などをデータで分析し、改善目標の達成度合いを確認します。もし、改善目標を達成できていない場合や、新たな課題が見つかった場合は、レイアウトの微調整や作業方法の変更などを行い、継続的な改善を図ります。
- Step8:レイアウトの定着化
レイアウト改善の効果を維持し、長期的に活用するためには、レイアウトを定着化させる必要があります。定期的な清掃や整理整頓、作業者の教育や訓練などを通じて、レイアウトの維持管理を徹底します。また、レイアウト変更の目的やメリットを従業員に周知し、理解と協力を得ることも重要です。レイアウトの定着化により、継続的な生産性向上と競争力強化を実現できます。
5. 工場レイアウト最適化のための7つのポイント
工場レイアウトを最適化するためには、以下の7つのポイントを考慮する必要があります。
- 動線: 作業者や物の移動距離を最小限に抑え、スムーズな流れを確保します。
- 作業効率: 作業スペースを最適化し、作業者の負担を軽減します。
- 保管場所: 在庫管理の効率化、搬入・搬出の円滑化を図ります。
- エリア分け: 作業内容や関連性に応じて、適切なエリア分けを行います。
- スペース: 設備の配置や作業スペースを考慮し、有効な空間利用を計画します。
- 設備: 最新の設備導入による作業効率の向上や安全性向上を考慮します。
- 従業員: 作業者の安全性や快適性を考慮し、モチベーション向上を目指します。
6. 工場レイアウト改善に役立つ最新ツール
工場レイアウトの改善に使えるツールとして、3Dシュミレーションツール (デジタルツインツール)が挙げられます。
実際にレイアウト変更をおこなう際は、上記に説明した通りのステップで進めることが重要ですが、どんなに検討をおこなったとしても、実際にレイアウトを変更した際には思ってもみなかったトラブルが発生することは往々にしてあります。そのトラブルを最小限にするためのツールが3Dシュミレーションツール (デジタルツインツール)です。デジタルツインとは、リアルタイムで取得したデータを仮想空間にて分析することで、改善・管理に活用することができる技術を指します。
自動車産業を中心に、以下のようなモニター画面を使った見える化・分析が進んでいます。
▲現場の稼働状況とAGVの位置をリアルタイムに可視化している様子
(引用:https://www.wingarc.com/solution/manufacturing/blog/digitaltwin.html)
デジタルツイン環境を構築することができれば、レイアウト変更時の生産能力/リードタイムなどを簡単に把握することができ、作業者の導線なども視覚的にわかりやすく把握することができます。
また、以下の画像のように、現状の設備に対して、追加設備の干渉がないかを確認することなどが可能です。
▲現状の設備と、設計中の設備との干渉をみている様子
(引用:https://monoist.itmedia.co.jp/mn/articles/2102/09/news002_2.html)
7. 工場レイアウト改善における課題と解決策
工場レイアウトの改善は、生産性向上や競争力強化に不可欠ですが、様々な課題が伴います。これらの課題を克服し、スムーズに改善を進めるためには、事前に課題を認識し、適切な解決策を講じることが重要です。
課題1:初期投資コスト
工場レイアウトの変更には、機械設備の移動や新規導入、内装工事など、多岐にわたる費用が発生します。特に、大規模なレイアウト変更や最新設備の導入には、多額の初期投資が必要です。中小企業や予算が限られている企業にとっては、大きな負担となる可能性があります。解決策として、国や地方自治体が提供する補助金・助成金の活用や、段階的なレイアウト変更をおこなうこと、リースや中古設備の活用が挙げられます。
課題2:レイアウト変更中の生産停止
レイアウト変更中は、機械設備の移動や設置、内装工事などのために、一時的に生産を停止する必要がある場合があります。生産停止期間が長引くと、納期遅延や売上減少につながる可能性があります。解決策として、休日や夜間を活用して作業することなどが挙げられます。
課題3:従業員の理解と協力
工場レイアウトの変更は、従業員の作業環境や作業方法に大きな影響を与えるため、従業員の理解と協力が不可欠です。従業員が変更に抵抗したり、協力的でなかったりすると、スムーズな改善が進まない可能性があります。事前にレイアウト変更の目的や内容、メリットなどを従業員に丁寧に説明し、意見交換の場を設けることが非常に重要です。
8. まとめ
工場レイアウトは、単なる設備の配置ではなく、企業の生産性、品質、安全性、従業員の満足度を左右する重要な要素です。この記事では、工場レイアウトの基礎から最適化手法、最新ツール、改善事例までを網羅的に解説しました。
工場レイアウトの最適化は、企業の持続的な成長と競争力強化に不可欠です。本記事が、貴社の工場レイアウトを見直し、生産性向上と効率化を実現する一助となれば幸いでございます。
船井総研では、レイアウト変更~工場新設コンサルティング、レイアウト変更~自動化コンサルティングを行っております。ご興味がございましたらお気軽に無料経営相談をご活用ください。